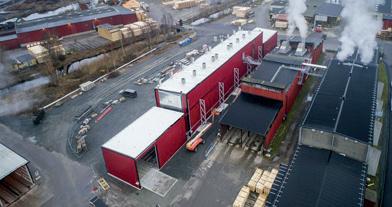
5 minute read
SETRA GROUP
Just under two years ago, Setra Hasselfors became the first sawmill within the Setra Group to invest in Valutec TC drying technology. Now they are investing in new TC wood drying kilns for both Hasselfors and the sawmill in Heby, both located in Sweden
Advertisement
Jan-Erik Johansson Vik, Site Manager, Setra Heby
Setra Group invests in TC kilns from Valutec to two Swedish sawmills
The properties of the TC continuous kiln fit well into the Setra Greenness philosophy. They offer the precision of the batch kiln in combination with high capacity and efficient heat recovery. Another bonus with it is that we don’t get tied to one batch size if we’d like to switch to larger ones in the future to reduce handling and further increase drying capacity,” says Jonas Fintling, Site Manager at Setra Hasselfors.
Setra Hasselfors in Sweden is a respected spruce sawmill established in 1908. In 2021, it produced approximately 345,000 m3 and the products are delivered to customers in Europe, the USA and Australia. The investment will increase the sawmill’s drying capacity by approximately 150,000 m3, which enables a planned production increase to approximately 500,000 m3. It will also be the first sawmill in Scandinavia with two TC kilns in one and the same sawmill.
The swedish sawmill Setra Heby was established in 1915 and 260,000 m3 was sawn in 2020. A large part of the production goes to Setra’s CLT and glulam factory in Långshyttan but the sawmill also exports dried-down goods mainly to France and Germany. The investment in a TC continuous kiln with a capacity of approximately 145,000 m3 is being made partly to replace older kilns and partly to increase drying capacity. With the new dryer in place, Setra Heby will have a drying capacity of approximately 320,000 m3 .
“We looked at different types of kilns and the TC kiln was best suited for the flow we have in Heby. It’s also good from a sustainability perspective, as with the same energy consumption, we will increase our drying capacity”, says Jan-Erik Johansson Vik, Site Manager at Setra Heby. He adds:
“The price is important when making an investment but you mustn’t fixate on it. With Valutec, we are getting a secure and developing partner who offers good service and delivery security.”
The kiln in Heby will begin assembly during the summer and in Hasselfors, assembly will begin in February next year. Jon Lindberg, Sales Manager at Valutec is looking forward to delivery:
“We already cooperate well with Setra and I look forward to us continuing to develop their drying capacity together.”
The TC kilns are delivered with Valutec Valmatics 4.0 control system, which enables the TC kiln functions to be utilised fully. Valmatics 4.0 is the only control system that combines simulator technology with adaptive control and which enables optimisation of capacity, quality and energy consumption simultaneously.
With these investments, Setra Group is following a clear trend in the world of sawmills. The new generation of Valutec TC kilns has been sold worldwide in recent years, opening up new markets for the company.
“What lies behind this technological leap is thousands of hours of development where
The properties of the TC continuous kiln fit well into the Setra Greenness philosophy. They offer the precision of the batch kiln in combination with high capacity and efficient heat recovery. Another bonus with it is that we don’t get tied to one batch size if we’d like to switch to larger ones in the future to reduce handling and further increase drying capacity
Jonas Fintling, Site Manager, Setra
we studied, evaluated, tested and invented new things in all parts of a sort of lumber kiln that, in its first form, was used as early as 1927”, says Robert Larsson, CEO of Valutec.
The big improvement is in the way to control temperature and airspeed individually in different zones using integrated simulator technology. Thanks to its development, the sawmill can choose with a high degree of freedom the dimensions of the lumber to be dried, something that has not previously been possible in a continuous kiln.
TC is the abbreviation of the Swedish for “cross circulation”. The principle is based on the lumber package being fed lengthways through zones in which the air circulates laterally across the drying channel. This enables the separate regulation of the climate in different zones according to a schedule that comes very close to the ideal schedule of a batch kiln.

Bois Daaquam, located in Saint Just De Bretenieres, Que., is investing in a new USNR end-dog carriage line. The new system replaces a dated Forano carriage that has provided good service over many years, and now makes way for new technology that will improve both recovery and throughput.
Bois Daaquam invests in new USNR end-dog carriage line
This new line is scheduled to be installed in 2023.
The end-dog carriage is an extremely versatile machine, capable of horizontal and vertical skewing, and 360-degree log rotation.
This fully automated system makes use of USNR’s proprietary Lasar2 sensors. The Lasar2 scanning system combines dense 3D scan data, and together with USNR’s powerful optimization
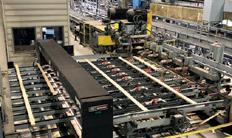
Parton Lumber in Rutherfordton, NC is investing to update its edger optimization system to vision-based scanning with BioLuma 2900LV sensors. This new system will be installed later in 2022.
Parton Lumber upgrades to USNR Edger vision scanning
The mill’s edger optimization system was installed with BioLuma 2900L laser profile sensors in 2015. With BioVision and Deep Learning AI technologies coming mainstream with proven benefits, Parton Lumber decided it was ready to take advantage of these technologies. Along with an advanced scanning system, the optimization platform will be updated to the latest Windows release, offering stability and longevity.
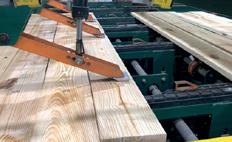
Nix Forest Industries is replacing their planermill stacker system on the heels of a new Transverse High Grader (THG) installation and other upgrades at their Timpson, TX mill. Investing in the new lowprofile stacker will increase overall throughput and uptime while reducing maintenance. This project is scheduled for start-up during the first part of 2023.
The Low-Profile Stacker features a compact, all-electric design and offers gentle handling of valuable product. Efficient and reliable in any environment, the energy-efficient design delivers precise actuation. engine, it is proven to maximize grade recovery in carriage lines around the globe.