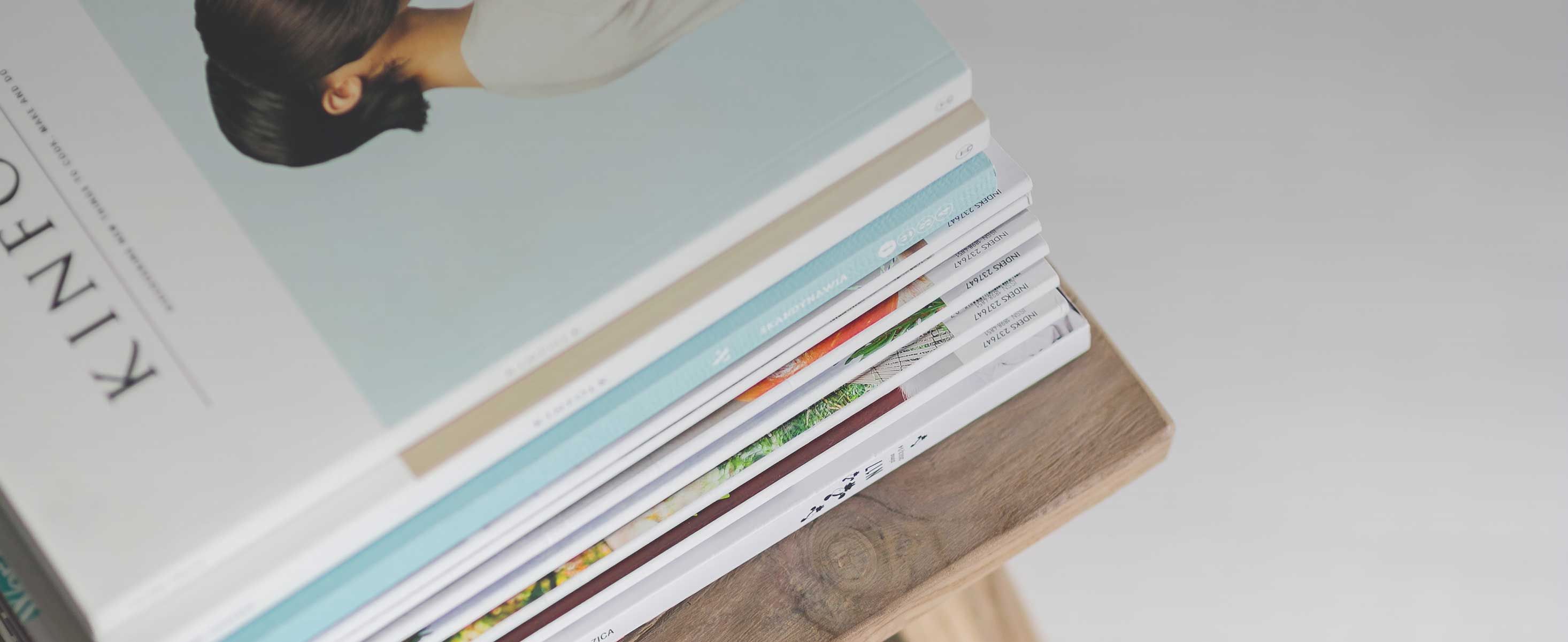
2 minute read
Kurtz Low-Pressure Casting Machine for Heunisch Site Krásná
INDUSTRY NEWS / 行业新闻 Kurtz Low-Pressure Casting Machine for Heunisch Site Krásná Heunisch Krásná公司安装新Kurtz低压铸造机
As a traditional family business with more than 40 years of foundry experience, Heunisch decided to invest in a new Kurtz casting line at the aluminum site in the Czech Republic in order to be best prepared for the future.
Advertisement
This decision for a system supplier was well-considered and based on a detailed evaluation process in advance. Heunisch was already using older Kurtz low-pressure casting machines, which, however, were no longer state of the art.
With the new casting line concept including the integrated furnace management system and shuttle, the company with headquarters in Bad Windsheim and further locations in Steinach (Thuringia), Krásná and Brno (both Czech Republic) has laid the foundation for good castings. The complete concept of the casting line with high flexibility, fastest furnace change and best melt quality as well as easy expansion of the production capacity convinced Heunisch. Long casting without changing the furnace again
The large crucible furnace with a capacity of 2.8 t allows both: long continuous casting without changing the furnace again and extremely high flexibility for positioning the riser tubes at the same time. Whether multiple cavities or large structural components - the large furnace allows the riser tubes to be positioned exactly where they are needed.
The concept with the shuttle also allows the downtime of the machine to be reduced to a minimum, which benefits OEE. The furnace is prepared outside the machine with the best melt quality, and the actual changeover is realized in the machine´s off-time - true to the motto "the machine has to run to make money".
To further increase efficiency, the casting machine has two mould change systems so that a new mould can be prepared on one and the old one dismantled in parallel on the other. The cooling system is connected via multi-couplings, which saves time and also means error-proofing when connecting the numerous cooling systems. Complete casting solution from a single source
In combination with the latest machine innovations, such as the cooling technology developed in-house by Kurtz, the best mechanical properties are achieved and the cycle time is significantly reduced. Thanks to the highly precise pressure control, low-turbulence mould filling is implemented, producing castings of the highest quality standards. Heunisch wanted much more than just the best machine technology - the company wanted a complete solution from melt preparation to handling and casting from a single source. In the end, the entire Kurtz know-how with the complete solution for the new casting line and the years of good cooperation convinced Heunisch all along the line. ■
作为一家拥有40多年历史的传统家族企业, Heunisch公司决定在捷克的铸铝厂安装一条新的Kurtz铸 造生产线,为未来做最好的准备。
选择系统供应商的决定经过了充分考虑,并事先进行 了详细评估。Heunisch公司已经安装过Kurtz低压铸造机, 但这些机器已不再是最先进的。
Kurtz公司总部位于德国巴特温茨海姆,另外还有位于 德国图林根州施泰纳克、捷克的Krásná和布尔诺的工厂, 凭借包括综合熔炉管理系统和运输系统在内的新铸造生产 理念,为生产优质铸件奠定了基础。Kurtz铸造生产线的完 整概念具有高度的灵活性、最快的换炉速度和最佳的熔体质 量,以及易于扩大的生产能力。
长时间浇铸,无需更换熔炉
容量为2.8t的大型坩埚炉既可以实现长时间的连续铸 造,又无需再次更换熔炉,同时具有极高的灵活性,可以定 位升液管。无论是多个腔体还是大型结构部件,大型熔炉都 可以将升液管准确定位。 运输系统的工作原理还允许将机器的停机时间减少到 最小,有利于提高设备综合效率(OEE)。炉子在机器外部, 具有最佳的熔体质量,实际的转换是在机器的停机时间完成 的——这符合“机器必须运转才能赚钱”的格言。 为了进一步提高效率,浇注设备有两个更换铸型的系 统,以便在一个换型设备上准备新铸型,同时在另一个换 型设备上换下原来的铸型。冷却系统通过多个耦合器连接, 节省了时间,也意味着在连接多个冷却系统时可以防止出现 错误。
单一来源的完整铸造解决方案
结合最新的机器创新,如Kurtz开发的内部冷却技术, 可获得最佳机械性能,并能显著缩短循环时间。由于高度精 确的压力控制,可进行低湍流充型,从而生产出最高质量标 准的铸件。Heunisch公司需要的不仅是最好的机器设备, 还想要从单一来源获得从熔体准备到熔炼和铸造的完整解 决方案。基于与Kurtz公司多年的良好合作,Heunisch公 司始终坚信Kurtz公司的专有技术与全新铸造生产线的完 整解决方案。■