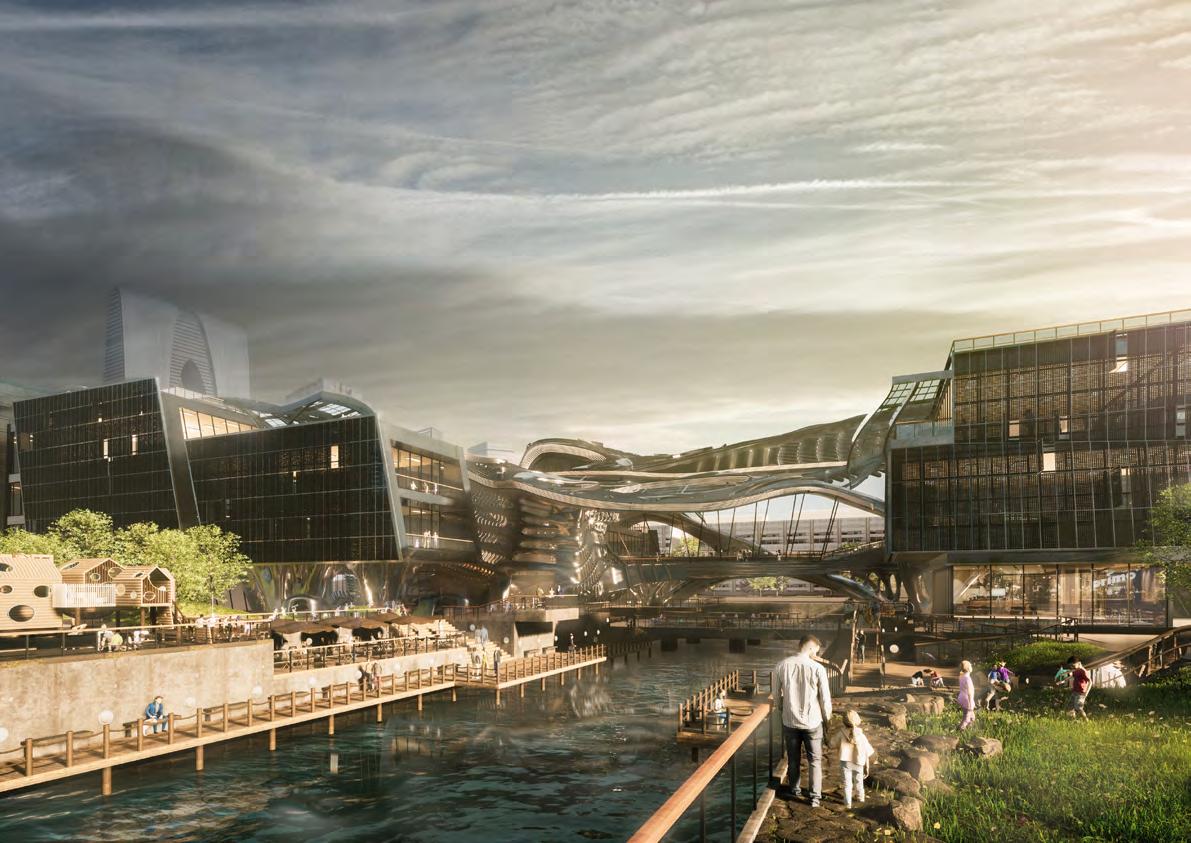
5 minute read
Xincheng Community Centre
Child-centered community & Multi-agent system
Suzhou, China
Advertisement
2021
Shuo Feng, Guosheng Chen
Individual Work
The design proposal centers around the construction of a community center, aimed at providing a secure and engaging environment for individuals, with a specific focus on children. In this unique setting, children aren't merely observers but active participants, present everywhere, interacting, and learning within their environment.
A multi-agent system is leveraged to simulate their movement patterns, thereby shaping the design volumes according to the trails within the existing buildings. Within these structures, children have the freedom to walk, run, slide, climb, and even construct their own secret base. The essence of this design is to foster active engagement and interaction in a safe, supportive space.
Axon View
In this child-centered community center, children are observers and participants. They should be present everywhere, which allows them to interact with different environments.
Using the multi-agent system aims to simulate their trails and figure out an organic way to interact with the built environment.
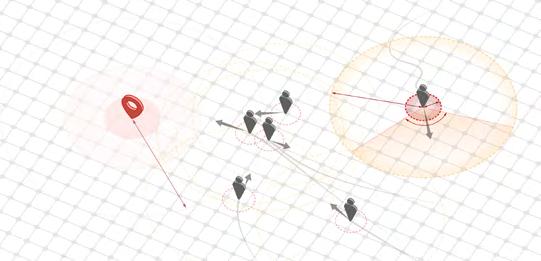

Agent Settings (Boid)
Attraction
Agents will be attracted to the targets scattered in the buildings.
Velocity Matching
Agents attempt to match velocity with nearby flockmates
Attraction Strength
Wandering Wandering is a type of random steering which has some long term order.
Trail Searching Radius
Repulsion Radius
Searching Angle
Attracting Radius
Flock centering
Each agent attempts to stay close to nearby flockmates;
Collision Avoidance
Each agent avoids collisions with nearby flockmates
Direction
Stigmergy Agents will chase other agents' trails.
Based on the multi-agent system's simulation, volumes are generated according to the trails. These volumes provide children with a place to hold various activities and allow them to interact closely with the real world while still under proper protection.
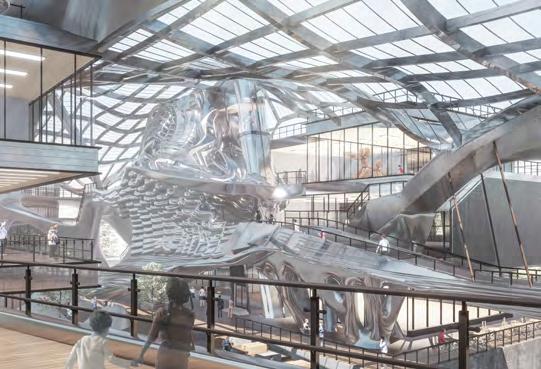
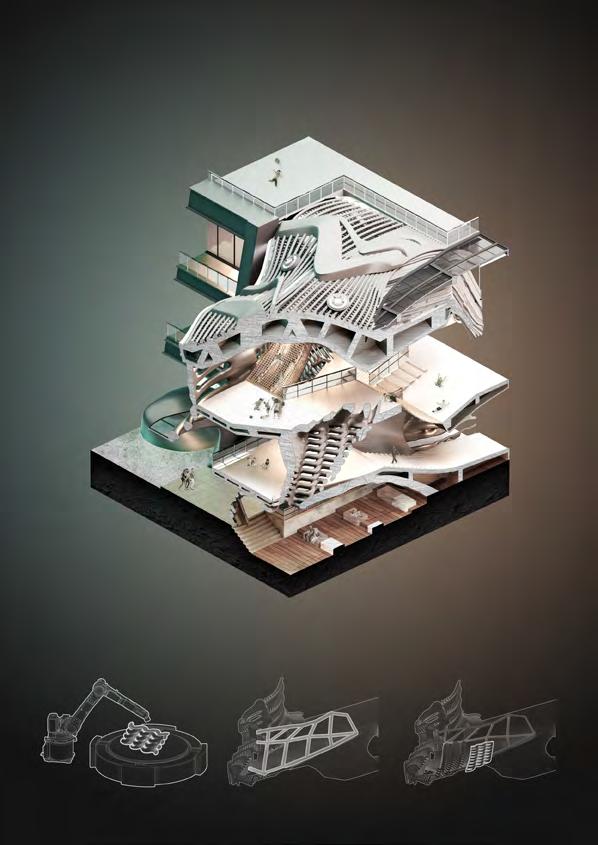
Rendering
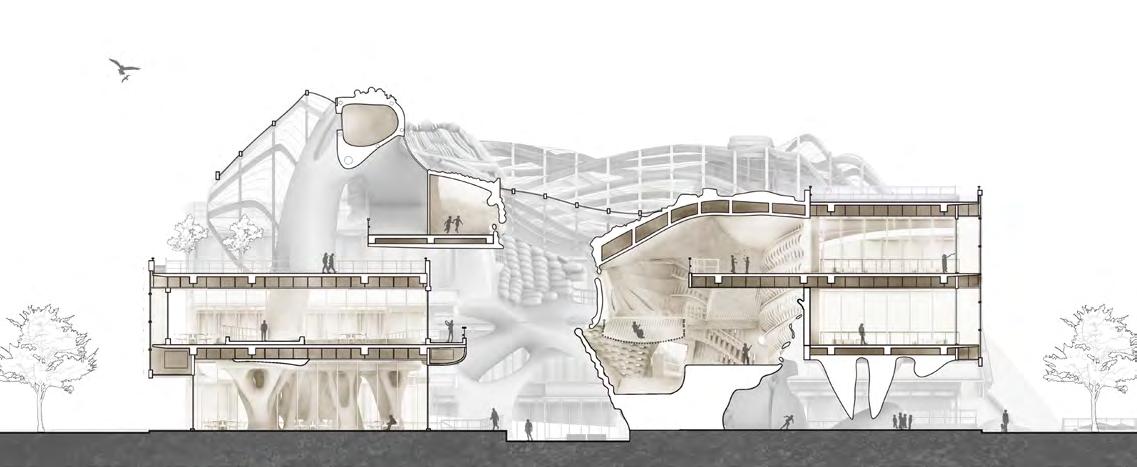

Location:
Year:
Instructor:
Description:
Dynamic Slip Casting
An Efficient Robotic Approach to Geometrically Variable Ceramic Part Production
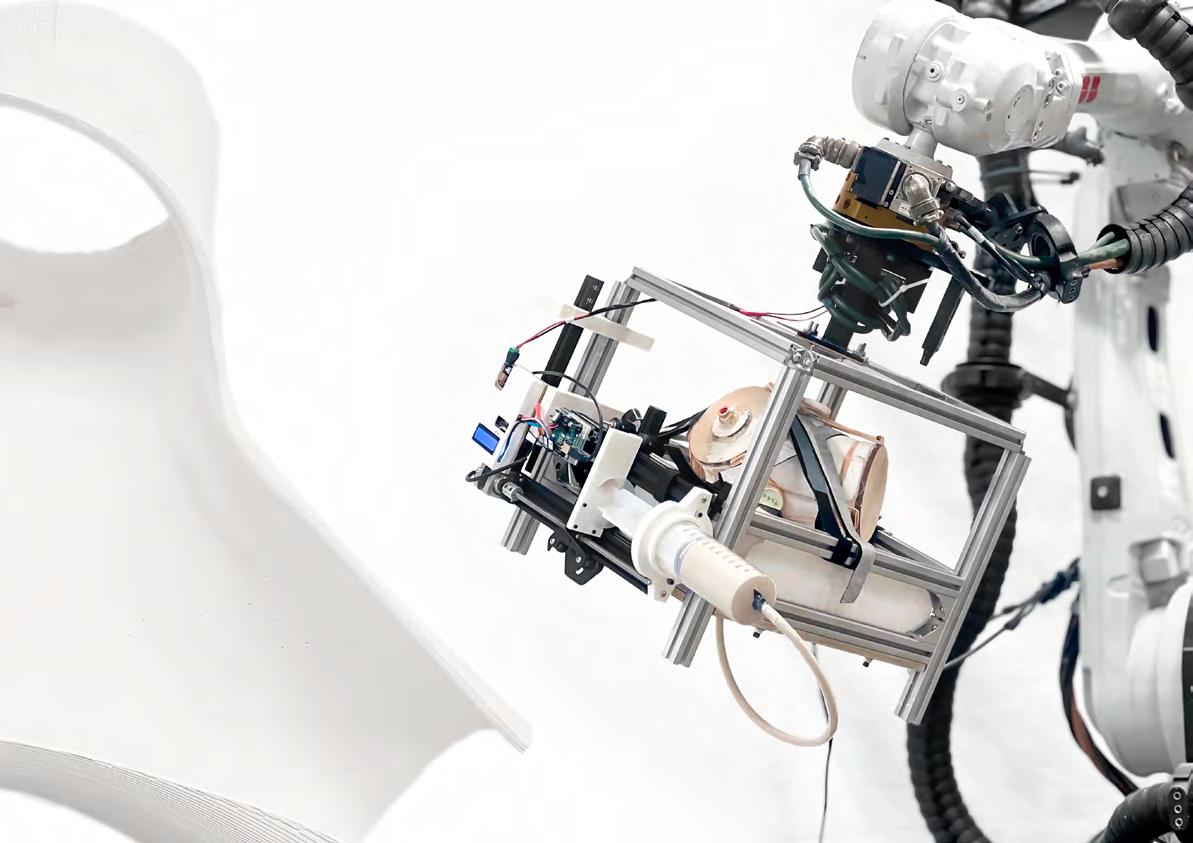
Philadelphia, Pennsylvania, United States 2023
Clay slip’s unique phase-changing properties make it an ideal material for crafting intricate, precisely-shaped components needed in industries such as fine porcelain and sanitary ware. However, its limitations in producing variable components without new molds present challenges for integration into architectural practices.
This research introduces an innovative slip casting approach that allows for the production of diverse clay forms using a single mold by employing a 6-axis robot that simultaneously rotates the mold during the solidification process. A key innovation in our research is the development of a simulation program specifically designed for the dynamic slip casting process. This breaks away from the traditional notion of slip casting as a “black box” process, where what happens inside the mold remains hidden. By providing insights into the mold’s interior, our simulation program adds significant value to the field and enhances our understanding of the process.
The simulation program predicts the solidified slip’s shape in real-time, and a customized end effector attaches the mold to a robotic arm and injects additional slip for precise edge control. The proposed method combines traditional slip casting with industrial robotics, offering greater control over geometric qualities without increasing mold demands. By overcoming conventional limitations, we hope that this unique ceramic workflow can be used in architecture and art, and inspire other fields of study.
Traditional Slip Casting Process
Our research revolved around process of Slip Casting. Slip casting, or slipcasting, is a ceramic forming technique, and is widely used for shapes that can not easily be formed by other techniques. The technique involves a clay body slip (which is the liquid clay), usually prepared in a blunger, being poured into plaster molds and allowed to form a layer, the cast, on the internal walls of the mold.
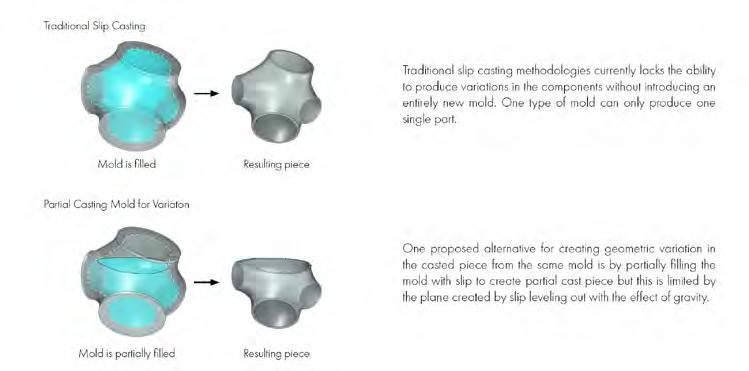
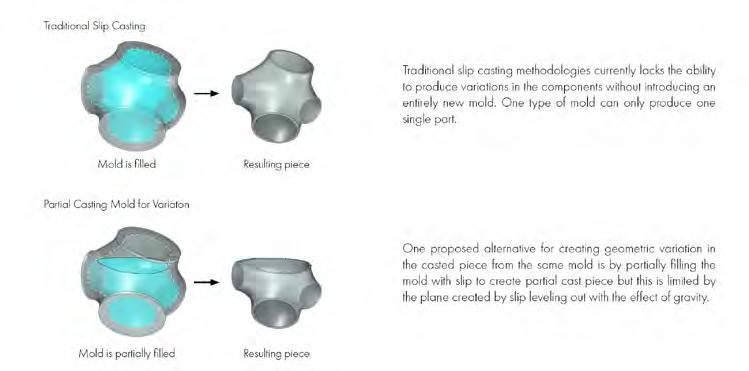
It is suited for the consistent and precise shaping of complex shapes. It is the standard shaping technique for sanitary ware, such as toilets and basins, and is commonly used for smaller pieces like figurines and teapots.
Research Aim
Our research aims to create diverse cast shapes to produce geometric variations by integrating robotic motion and simulation into the slip casting process for enhanced flexibility, precision and efficiency.
The proposed workflow involves the following components of Digital environment & physical environment. In this workflow, a slip casting simulation software to estimates the resulting cake’s shape and thickness distribution following robotic movements was developed to address the unpredictability of this process. Robotic motion is employed to effectively produce variations in cast pieces.
Traditional Slip Casting
Proposed Partial Slip Casting
Our
Typical Slip Casting Process
Comparison between
Traditional
Traditional Slip Casting Process
Casting Process
The proposed workflow involves the following components of Digital environment & physical environment. In this workflow, a slip casting simulation software to estimates the resulting cake’s shape and thickness distribution following robotic movements was developed to address the unpredictability of this process. Robotic motion is employed to effectively produce variations in cast pieces.
Traditional Slip Casting Process
Traditional Slip Casting Process
Traditional Slip Casting Process
Mold Creation
The mold is the negative space into which the slip is poured. Molds can be made from plaster, silicone, or other materials.
Slip-Pouring
The slip is poured into the mold slowly and carefully to prevent air bubbles from forming. The mold should be filled to the top.
Mold Creation Slip-Pouring
the top.
Drain Excess Slurry Remove the Cast
Drain Excess Slurry
Remove the Cast
Drain Excess Slurry Remove the Cast
Once the desired thickness is achieved, the excess slip is poured out of the mold. This can be reused for future slip castings.
Once the desired thickness is achieved, the excess slip is poured out of the mold. This can be reused for future slip castings.
Cake Growth
Left slip to sit for a period of time, to allow the clay to thicken and settle, called the cake growth.
Cake Growth
Left slip to sit for a period of time, to allow the clay to thicken and settle, called the cake growth.
Our proposed alternative tries to create variation in the casted piece from the same through partially filling and tilting the mold partial cast piece.
Comparison between different casting methods
Once the clay has set, the mold is removed and the cast is allowed to dry.
Once the clay has set, mold is removed and the cast is allowed to dry.
Finish the Cast
Finish the Cast
Once the cast is dry, it can be trimmed, sanded, and smoothed to remove any imperfections or excess clay.
Once the cast is dry, it can be trimmed, sanded, and smoothed to any imperfections or excess clay.
Digital simulation of the dynamic slip casting process. The red dots indicate the thickness of cake.
To address the challenge of unpredictability of slip behavior inside the mold and advance the field of slip casting, we introduce a novel approach: robot dynamic casting. In this method, the mold is continuously rotated during the casting process, allowing for the creation of more intricate and precise geometries. However, implementing dynamic casting effectively requires a deep understanding of the underlying physics and an ability to predict the outcomes of the process. This is where our simulation program comes into play.
Validation and Testing
While our simulation program has proven effective in predicting the shape of dynamic slip casting results, it currently does not account for shrinkage during the solidification and drying processes. This limitation may lead to discrepancies between the simulation predictions and the actual outcomes. Future improvements to the program should include incorporating shrinkage calculations to enhance the accuracy of the final shape predictions.
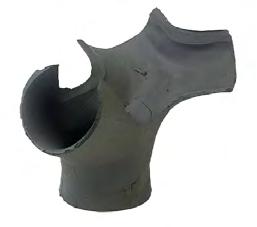
The choice to determine the thickness of the solidified slip (cake) based on the coverage time for each mesh vertex is grounded in previous research findings. Studies have shown that during the casting process, the cake thickness grows with the increased amount of time.
By tracking the coverage time for each vertex, we can estimate the thickness distribution of the solidified slip in the cast part, which is essential for optimizing the dynamic casting process.
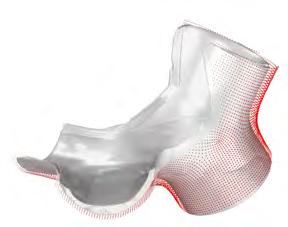
Program Screenshot
Although the final piece was smaller due to part shrinkage, a comparison between the simulation results and the 3D scan of the model demonstrated the simulation’s effectiveness in reverse engineering and generating the robot’s trajectory based on the desired design geometry. However, this process also highlighted challenges related to the edge condition of the resulting piece.

Similarly as each robotic motion was repeated to build up thickness, we discovered that the amount of slip inside the mold decreases resulting in a brittle edge condition. Reduction of slip inside the mold occurs as robotic motion is repeated and development of method for adding additional slip inside the mold was necessary.