
5 minute read
Problem analysis: water absorption, diagram
Movable slip volume is calculated to get a better understanding of the rate off decrease of slip as each robotic movement was repeated.
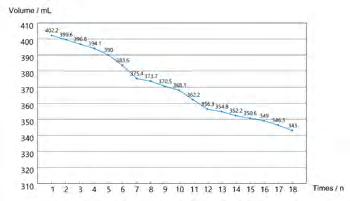
Advertisement
Development of Slip Injector for Reducing Slip Inside the Mold
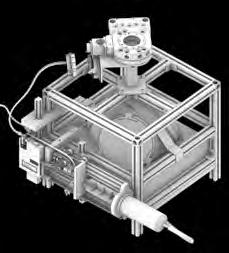
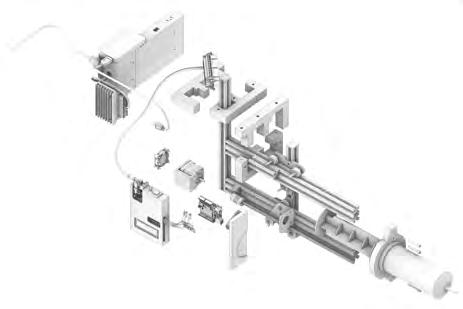
To address the decreasing slip inside the mold, we’ve designed a unique Arduino controlled slip injector that adds more slip as needed as each cycle of robotic routine is repeated. This helps maintain balance and ensure a smooth casting process while reducing the thin brittle edge condition. The design integrates an stepper motor that is controlled by robot’s i/o that actuates a syringe for precise slip volume injection and a LCD screen with a button system for easy adjustment of slip amount for different robotic routine.
Slip Injector
End-effector Mold Holder & Robotic Attachment
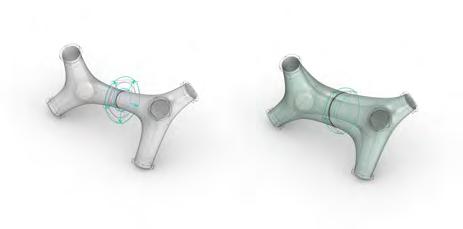
To further fine tune our workflow, we designed and fabricated a larger mold and a custom end-effector with aluminum extrusions. The design integrates a series of CNC foam inserts that would hold various types of mold in different initial starting orientation while also allowing for ease of interchanging of the molds for different robotic routines.
Gird System & Full Scale Mock - up
To further explore our workflow for creating geometric variations and to potentially informing future research into architectural applications such as facade screen assemblages, series of grid system studies has been done for nodebased geometry and workflow has been tested to fabricate a full scale mock-up. Node-based geometry is a versatile tool for producing intricate shapes and patterns. By adjusting the size of individual nodes, we can generate even more variation in our designs. Manipulating node size allows us to refine the overall scale and visual appeal of our design. Whether we’re aiming for dense, tightly packed grids or more open and airy structures, the spacing between nodes is also a crucial factor in achieving our desired effect. Furthermore, there are various node types and configurations to choose from, each offering distinct visual possibilities.
END-EFFECTOR: MOLD

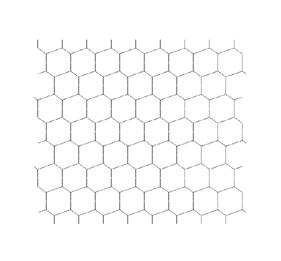
1 type of component with same node size, 5 types of component with two types of node size.

Prototype for fabrication
Prototype was designed for fabrication to fully test our extended research. The prototype consists of 28 pieces based on a tetrahedral grid system for it’s symmetrical nature and 4 mold variations for fabrication feasibility.
Larger Plaster Mold Production
The plaster mold was fabricated using a 3D printed shell which liquid plaster was poured and got melted away with a heat gun after the mold has cured. The plaster mold is an 4-part mold with interchangeable lid at each node that allows for selection of injection point depending on the desired casted piece and initial starting position of the robotic routine.
The prototype consists of 28 parts with 4 different component variations with different radius at the node with different partial cast piece to fully explore the capabilities of the proposed workflow.
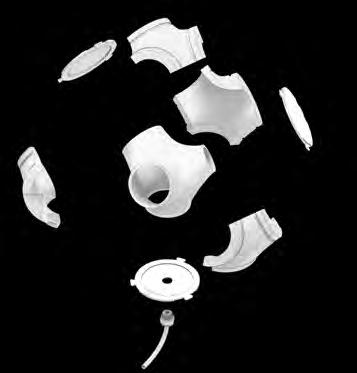
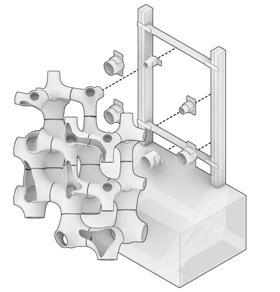
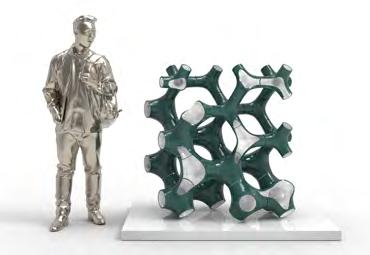
Production Process
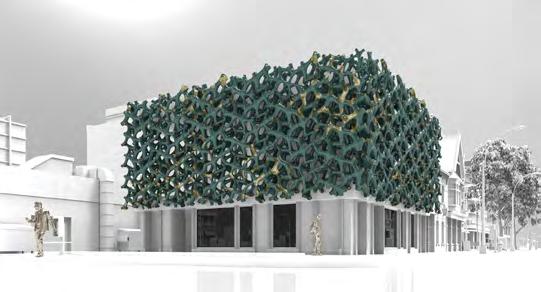
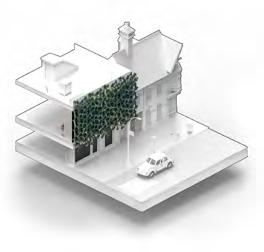
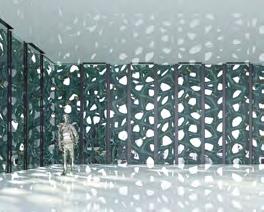
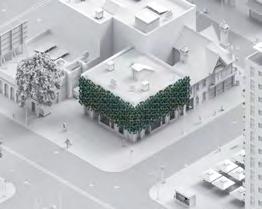
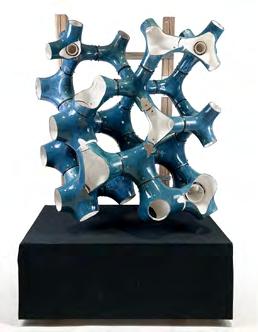

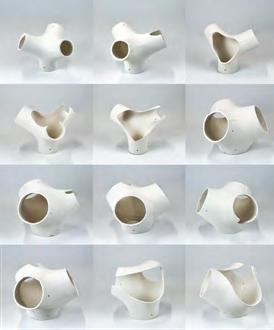
Location:
Year:
Instructor:
Ceiling Part Prototype
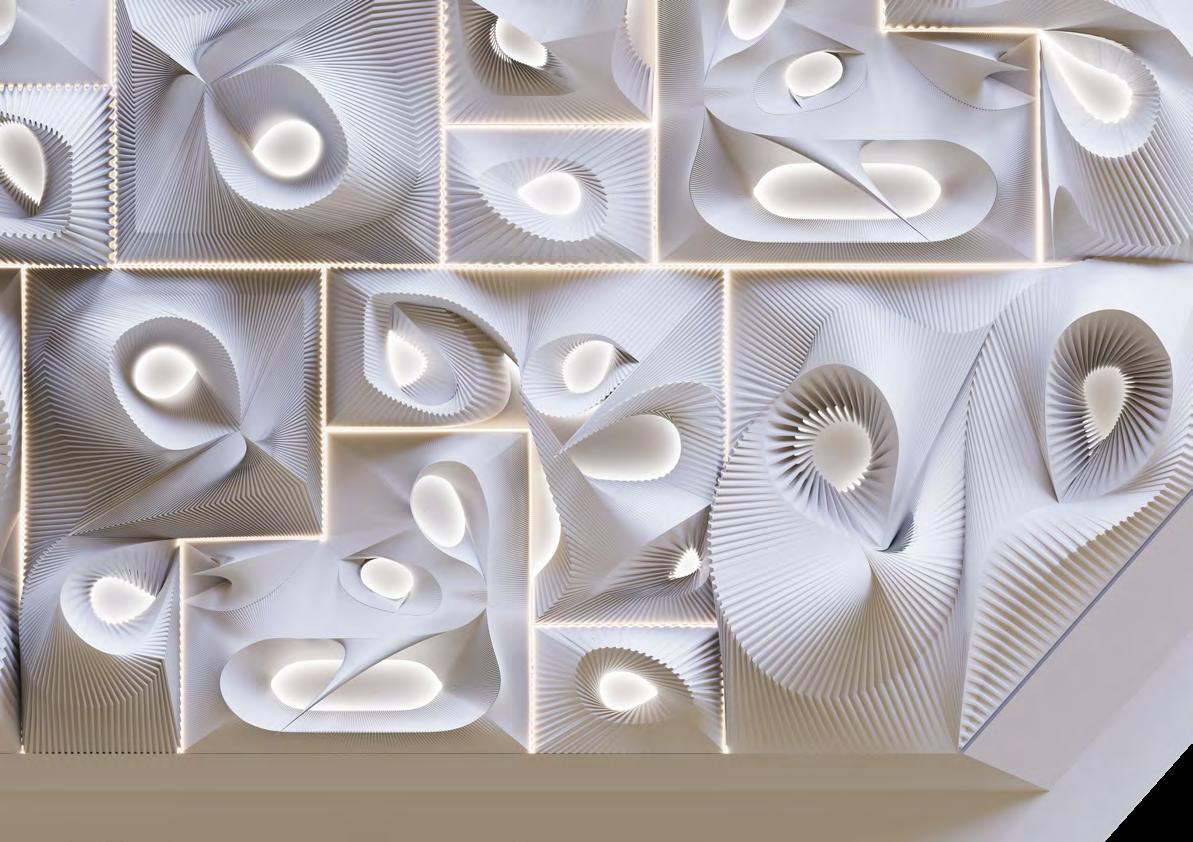
Robot hot-wire cut EPS foam ceiling prototype
Philadelphia, Pennsylvania, United States 2022
Andrew Saunders, Riley Studebaker, Claire Moriarty
Partner: Shunta Moriuchi, Jingyu Luo, Renhu Wu, Shuoxuan Su
Description:
We proposed a 900 square feet speculative ceiling for the Upper Gallery of Meyerson Hall. The ceiling scape deploys a series of hierarchical variations. The variations in the depths of the lilies and the peaks form different zones under the ceiling that resembles an infinite mushroom forest. Peaks stick out like vines and low plants, and lilies bump up to create circular spots on the ground. Like getting lost in the woods, the ceiling scape stimulates the wanderlust and Deja vu feeling of the person below.
Linear Construction in Space
We chose to study the Linear Construction in Space No. 4 by Gabo in which he created ruled surfaces using bronze wires strung between curved steel rails and Pevsner’s Construction of developable Surface which used bronze, oxidized brass, and a black marble base to construct developable surfaces.
Through a careful analysis of both sculptures, we digitally reproduced the ruled surface forms through which we were able to extract and digitally model specific geometric qualities.We transposed those ruled surfaces into volumetric implications of rulings in space to deconstruct the geometric moves made by the sculptures and to depict the geometry in light and shadow for input into neural networks.
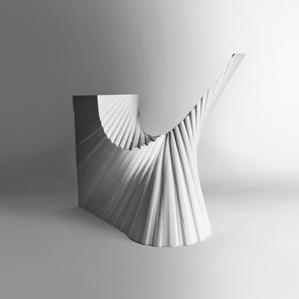
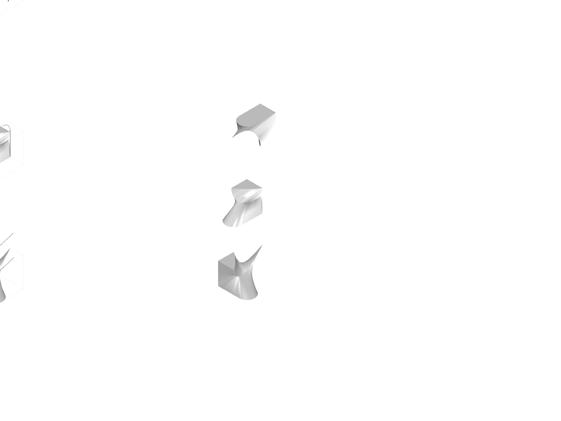
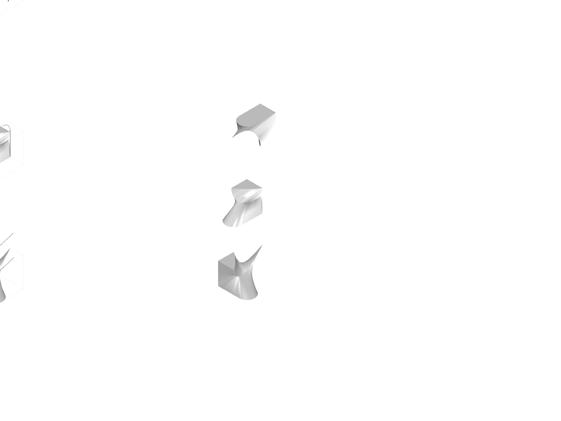
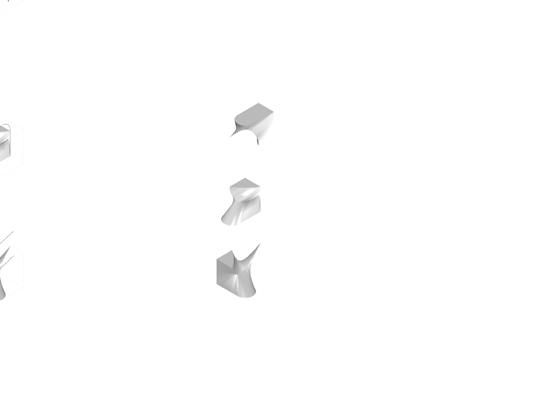
Robot Hot-wire Cut Foam Prototype
CNN (Convolutional Neural Network) Generative Design
We fed the images of these new distinct but identifiable and reproducible elements from our sculptures into the Convolutional Neural Network. Through this process, we were able to generate an outline for us to extract the threedimensional unprecedented geometric ceiling arrangements.
From Image To Production


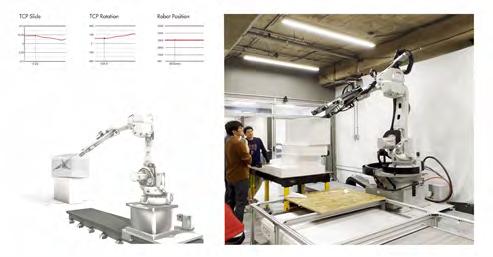
Although CNN excels at creating two-dimensional novel designs from learned arrangements of embedded information, it lacks the knowledge and struggles to produce perfect 3D outcomes that can be built. To overcome these limitations, we modeled explicitly CNN outcome images of the selected geometry to choreographed paths for multi-axis robotic hotwire cutting routines to be prototyped, using our in-depth understanding of distinct identifiable elements and the geometric hierarchy according to shape, brightness, and stacking relationship.

Ceiling Design

We proposed a 900 square feet speculative ceiling for the Upper Gallery of Meyerson Hall. The ceiling scape deploys a series of hierarchical variations. The variations in the depths of the lilies and the peaks form different zones under the ceiling that resembles an infinite mushroom forest. Peaks stick out like vines and low plants, and lilies bump up to create circular spots on the ground. Like getting lost in the woods, the ceiling scape stimulates the wanderlust and Deja vu feeling of the person below.
Ceiling Plan
South Elevation
Location:
Year:
Instructor:
Home of the Stepwell
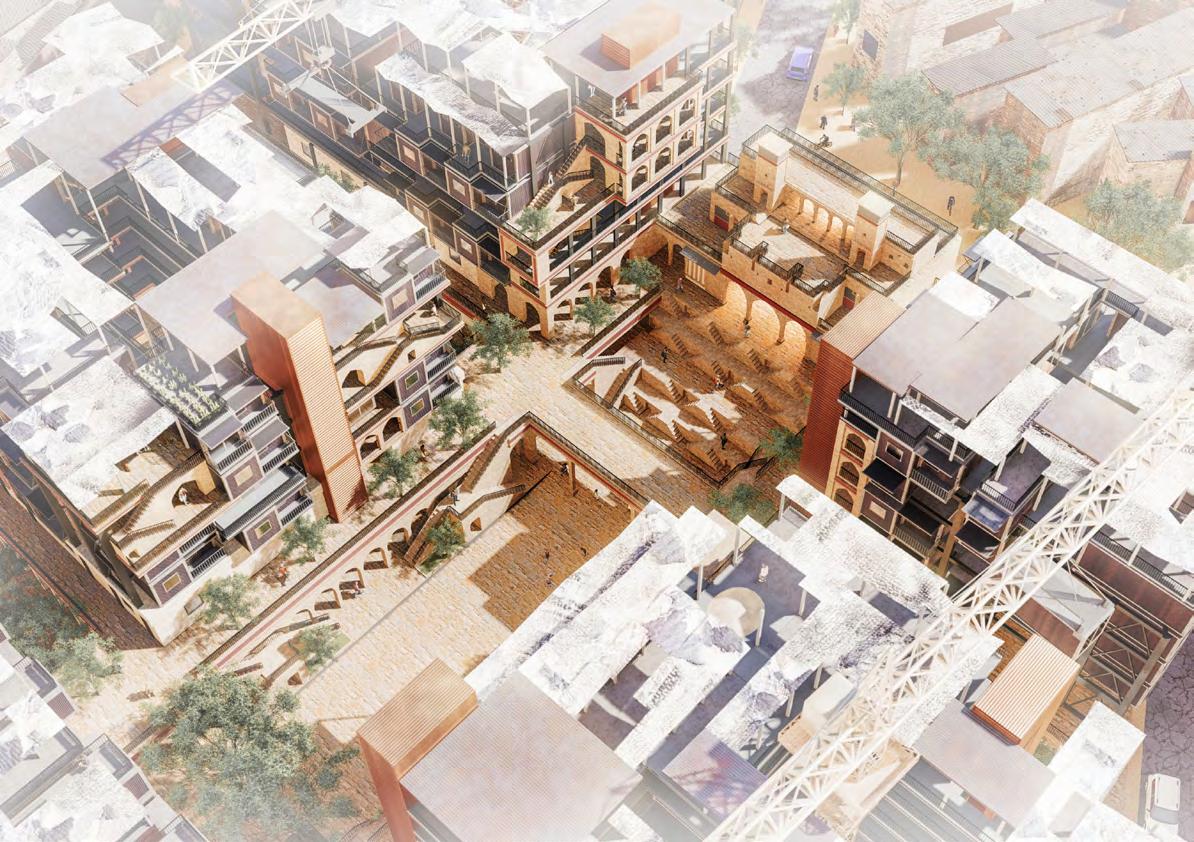
Religion, life, and epidemic
Dharavi, Mumbai, India
2020
Zhengwei Xia, Hengliang Tang
Partner: Haoxian Wang
Description:
Popularly known as Asia’s largest slum, Dharavi has active economic activities but poor living conditions. Such a problem is even more evident during the epidemic. People here lack proper medical treatment and a clean housing environment because they cannot protect their interests by speaking with a common voice. Therefore, many of them lost their jobs and struggled to live.
Besides, most residents here have their religious beliefs. Unfortunately they cannot fulfill their rituals because large assemblies are forbidden during the epidemic.
Concept
Based on the local features and slums dwellers' material and spiritual needs, the goal of this design is to improve their current life, maintain their rituals and make the community adaptive to the epidemic.
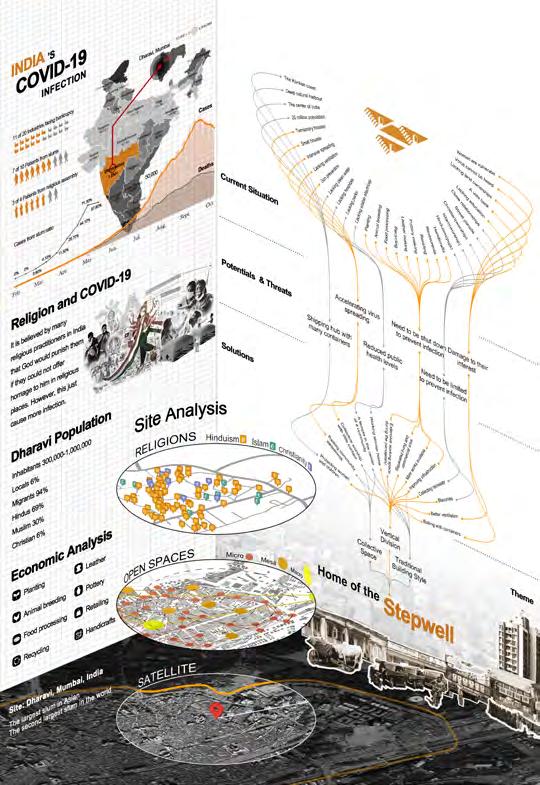
Lifestyle Analysis
Religious behavior sequence
Pious
Dwellers in Dharavi
Life production
Low shanty towns
Recite Scriptures
Individual Public Group
Private
Large-scale cultural events
Group praying
Living Scaffolding
Playground
Holi Festival
Roof
Commercial Industry
Stepwell: Adaptation Space Transformation
The stepwell is considered an essential monumental structure beyond its functional purpose of the source of water supply.
Besides, people can use it during the dry or rainy season, which shows adaptability due to its vertical stratification.
Space Strategy
Set the center of "stepwell". Split the site by traffic flow. The courtyards. Rectraction for public space. Connections and Platforms. Vertical transportation.
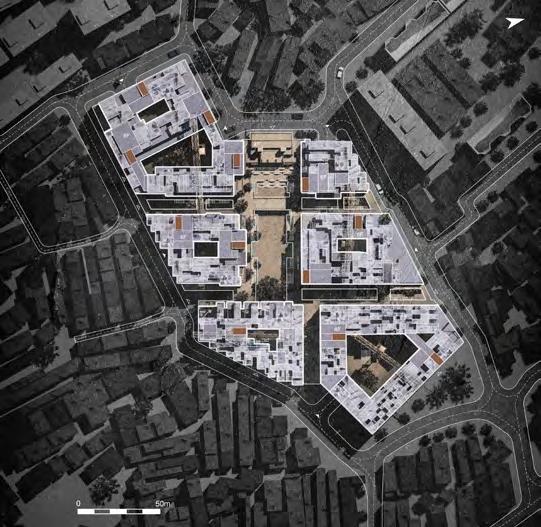
Site Plan
Activity Analysis
Religious Living Community Commercial Production Anti-epidemic
Religious Living Community Commercial Production Anti-epidemic
Behaviors type
Behaviors type
Use time Policies during the pandemic
The basement floor is used for production and storage activities, serving for the stores on the ground floor.
Religious Living Community Commercial Production Anti-epidemic
Behaviors type
Use time Policies during the pandemic
Public Space
People in Dharavi use to stay outside their home and communicate with neighbours or do some work in front of their homes.
New dwellers can buy a container home. Their homes can be installed on the structure by using the tower cranes.
Dewellers can plant vegetables, dry clothes, play, and do some manual work here.
Explosive View
In this design, the central plaza is the buttom of the "stepwell". It shares similar spatial sequence with the traditional indian stepwell, arousing residents' emotional resonance.
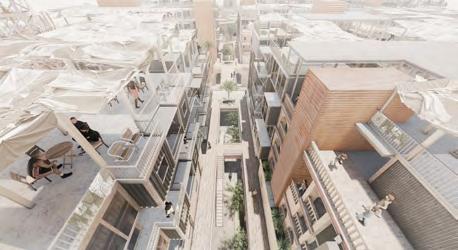
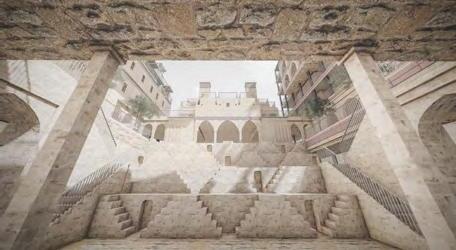
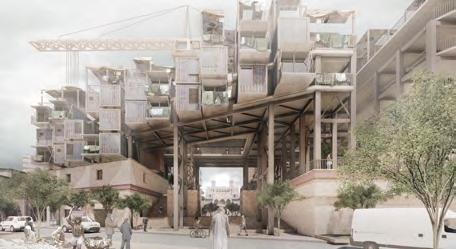

Roof
Canopy
Fixed roof
Above
Stairs
The 'temple'
Container home
First Floor
The 'temple'
Stairs
School
Ground Floor
The 'temple'
Courtyard
Playground
Retail store
Container Home
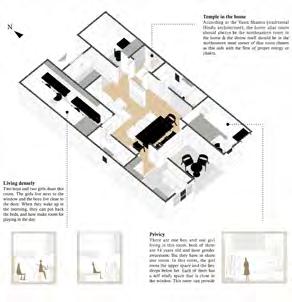


Family members: one pair of parents, three children
Containers used: 6m*2.1m*2.7m*2
Decoration elements
Originated from Hinduism
Family members: one pair of parents, two teenagers, four children
Containers used: 6m*2.1m*2.7m*1, 12m*2.1m*2.7m*2 Center
Section A-A
Location:
Year:
Instructor:
Partners:
Description: