
3 minute read
INTERMODAL
from Issue 27
stacks, new intermodal rail terminals are increasingly relying on RMGs to perform intermodal operations over a series of train tracks, often with some below crane space for track-side stacking. Several RMG models can swivel, allowing for perpendicu- lar crane side loading and unloading. An RMG used solely for stacking can accommodate densities above 1000 TEU per hectare (four full or five empty containers).
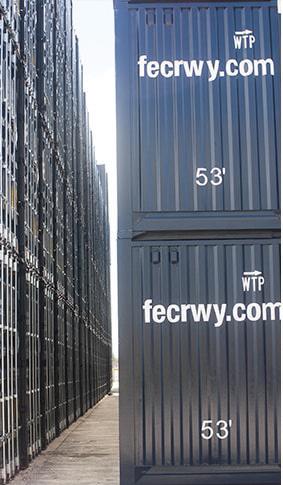
Advertisement
When carried by rail, containers may be carried on flatcars or well cars. The latter are specially designed for container transport and can accommodate double-stacked containers. However, the loading gauge of a rail system will restrict the modes and types of container shipment. The smaller loading gauges often found in European railroads will only accommodate single-stacked containers. In some countries, such as the United Kingdom, there are sections of the rail network through which high-cube containers cannot pass, or can pass through only on well cars. On the other hand, Indian Railways runs double-stacked containers on flatcars under 25 kV overhead electrical wires. The wires must be at least 7.45 metres (24 ft 5 in) above the track. China Railway also runs double-stacked containers under overhead wires, but must use well cars to do so, since the wires are only 6.6 metres (21 ft 8 in) above the track.
Double-stack rail transport is a form of intermodal freight transport in which railway cars carry two layers of intermodal containers. Invented in the United States in 1984, it is now being used for nearly 70% of United States intermodal shipments. Using double stack technology, a freight train of a given length can carry roughly twice as many containers, sharply reducing transport costs per container. On United States railroads special well cars are used for double-stack shipment to reduce the needed vertical clearance and to lower the centre of gravity of a loaded car. In addition, the well car design reduces damage in transit and provides greater cargo security by cradling the lower containers so their doors cannot be opened. A succession of larger container sizes have been introduced to further increase ship- ping productivity in the United States.
Southern Pacific Railroad (SP), and American Car Foundry, devised the double-stack intermodal car in 1977. The double-stack idea was originally proposed by Don Orris. He would devise the idea while working at the Denver Rio Grande & Western. SP then designed the first car with ACF Industries that same year. At first it was slow to become an industry standard, then in 1984 American President Lines, started working with the Union Pacific Railroad and that same year, the first all double-stack train left Los Angeles, California for South Kearny, New Jersey, under the name of "Stacktrain" rail service. Along the way the train transferred from the UP to the Chicago and North Western Railway and then to Conrail.
Stacking containers
Forty-foot containers are the standard unit length and load bearing points are at the ends of such containers. Longer containers, such as 45, 48 and 53 feet long, still have the load bearing points 40 feet apart, with the excess protruding equally outside this length. Therefore, 40-foot containers, or larger, can be stacked on 20-foot containers if there are two 20-foot containers in a row; however, 20-foot containers cannot be stacked on top of 40-foot or longer containers.
The possible double-stacking patterns are: two 20 ft in lower and one 40 ft (or longer) in upper stack (allowed in India, China); one 40 ft in lower and another 40 ft (or longer) in upper stack (allowed in India); two 20 ft in lower and another set of two 20 ft in upper stack (possible in well-type cars, in the USA).
The container coupling holes are all female and double male twistlocks are required to securely mate container stacks together.
Intermodal containers shipped by rail within North America are primarily 53 feet (16.15 m) long, with trailer-on-flat-car (TOFC) units used as well. The 53-foot length reflects a common maximum length for highway semi-trailers, which varies by state. Major domestic US intermodal carriers include: J. B. Hunt; Swift; Schneider National; and, Hub Group.
Containers shipped between North America and other continents consist of mostly 40-foot (12.19 m) and some 45-foot (13.72 m) and 20-foot (6.10 m) containers. Container ships only take 40's, 20's and also 45's above deck: 90% of the containers that these ships carry are 40-footers and 90% of the world's freight moves on container ships; so 81% of the world's freight moves by 40-foot containers. Most of these 40-foot containers are owned by non-US companies like Maersk, MSC, and CMA CGM. The only US 40-foot container companies are leasing companies like Textainer, Triton International and CAI Leasing.
Intermodal traffic
Intermodal volumes show no sign of an inflection point into positive territory and are unlikely to show one for the foreseeable future, predicts FTR Transportation Intelligence. Intermodal will be in a negative competitive position through most of 2023 and 2024 before edging up as competing trucking capacity tightens up.
Import slowdowns and shifting have added to intermodal’s malaise by making truck more competitive as length of haul lessens relative to the 2000-mile lengths of haul that are common for imports from the US west coast.
Domestic volumes are expected to fare worse in 2023 than their international counterparts because of the lack of transloading infrastructure at non-US