The future is now

The best and brightest in the fresh produce business are set to tap into cu ing-edge technologies to boost efficiency and profitability
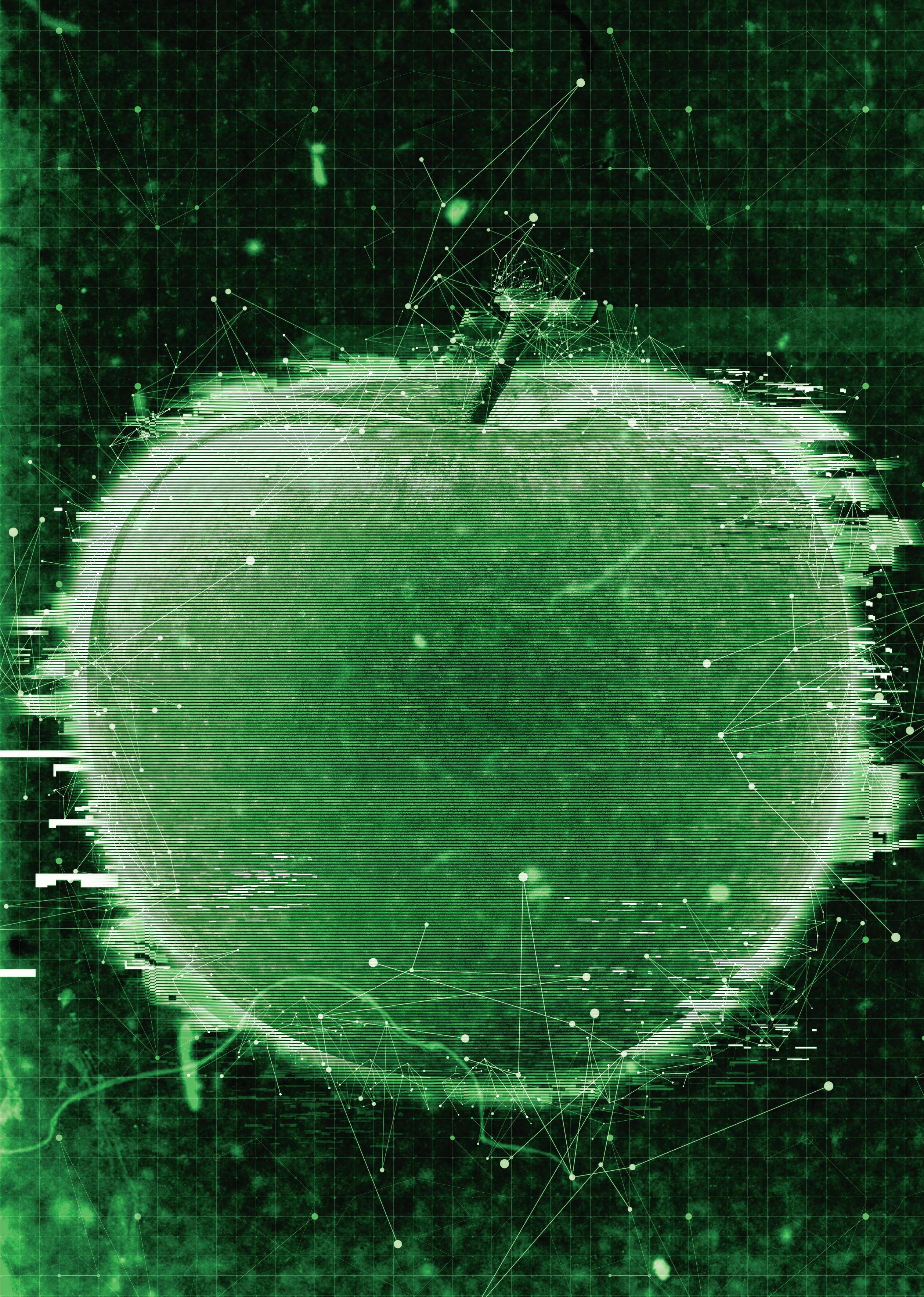
AI INTERVIEWS
PACKAGING
LABELLING
ROBOTICS
PALLETS
RETAIL VERTICAL FARMING

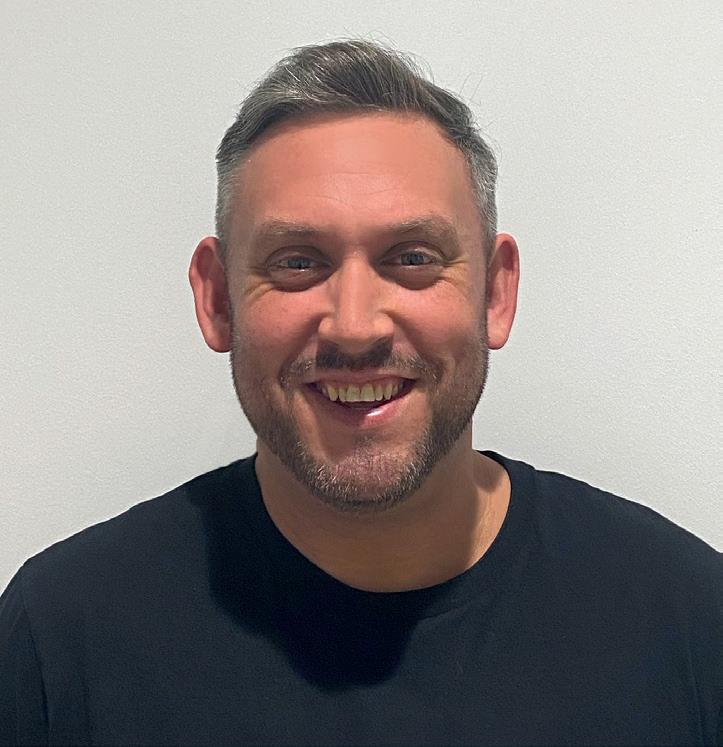
The best and brightest in the fresh produce business are set to tap into cu ing-edge technologies to boost efficiency and profitability
AI INTERVIEWS
PACKAGING
LABELLING
ROBOTICS
PALLETS
RETAIL VERTICAL FARMING
The long-running animated show South Park came up trumps again in March 2023 with its ChatGPTthemed episode ‘Deep learning’. As is so often the case with the on-the-ball sitcom, it offered a sideways look at one of the biggest news stories of the year – in this case, the rise of the generative pre-trained transformer chatbot. The cautionary tale warned of the doubleedged sword that is AI, and even ended with a tongue-in-cheek credit that ChatGPT had written that week’s programme along with creator Trey Parker. Clearly the episode and its underlying message failed to reach the offices of German publication Die Aktuelle, which in April ran what was billed as an ‘exclusive interview’ with legendary Formula 1 driver Michael Schumacher, who has been out of the public eye completely since a skiing accident in December 2013. It transpired that the “world sensation” interview had been completely generated by AI, despite being billed – on the surface at least – as Schumacher’s first since the accident. The disclaimer in the article that AI had been utilised to create the quotes (“it sounds deceptively real”, the cover claimed) was not enough to prevent condemnation; indeed, Die Aktuelle’s editor of 14 years was fired. And therein lies the lesson that I suspect South Park was trying to teach us in its own, irreverent way. That AI, like all powerful tools, has limitless potential but must be wielded with caution and responsibility.
Despite public fears over its impact, many believe we have still only caught a glimpse of artificial intelligence’s full potential in the fresh produce business.by Carl Collen, Mike Knowles and Maura Maxwell
@carlfruitnet @mikefruitnet @maurafruitnet
While the topic of artificial intelligence (AI) has shot back to the forefront of the world’s collective consciousness in recent months, it is an area that the fresh produce industry has looked to embrace for some time. The arrival of ChatGPT and
Bard in particular has reinvigorated the mainstream discussion around the opportunities – and potential pitfalls – of the power of AI, but many in the fruit and vegetable business already espouse the benefits in areas such as robotics, crop monitoring, machinery, and communications.
At this year’s Global Tomato Congress, which
took place in Rotterdam on 16 May, agtech startup Source.ag’s co-founder and CEO Rien Kamman spoke enthusiastically about the benefits of AI and downplayed some of the fears that exist over its adoption.
“AI has the potential to empower growers, who wield tremendous power, have an enormous responsibility and do a complex job,” said Kamman. AI was being utilised in a number of key areas in the fruit and vegetable supply chain, he outlined, including smart monitoring for full, real-time visibility (remotely or in person), assessing sales, planning labour, monitoring strategy and risk, and
OPPOSITE—An AI-generated fresh produce display –the topic of AI and its use has been mainstream news in the past year
ABOVE—Rien Kamman of Source.ag speaks at the Global Tomato Congress
LEFT—Itamar Zisling from robotics developer Metomotion
executing plans autonomously.
“Growers are three-dimensional chess players,” he continued. “You need to find the right strategy across these multiple dimensions – pruning, costs, irrigation and more – and every day you are presented with new information. This is where AI plays a massive supporting role.”
Kamman said Source.ag’s early adopters completed “hundreds” of simulations every week as new information came in and altered their strategies accordingly.
“You need a good digital representation of what is
happening in the greenhouse, a virtual overview,” he said. “The AI can simulate the actual biology of crops, to see how different strategies can affect the outcome. If you do this virtually, you can do it in seconds without any risk to the actual operation. We simulate strategies, simulate the biology, the production. You can model how good a strategy is from a financial point of view too, how much revenue will it bring in, how much profit.”
Kamman was also keen to point out that, while he understood the concerns surrounding the rapid development of AI and the perception it could usurp some in the supply chain, this was not the end goal.
“AI is a partner to help growers, not replace them, it is designed to help find the best solutions to help the business,” he explained. “It will reduce risk and help produce more food through expanded and more efficient production.
“There is uncertainty about the future when we speak to growers about AI, but there are so many jobs that they undertake that it is about benefiting them, making their life easier,” he added. “There is also an education aspect to this – a lot of the narrative around AI is driven by the media and it is important that the facts and nuances are made clear, as AI and its use is not so black and white.”
The advantages offered by AI are also championed by Itamar Zisling, business development and pilots manager at robotics developer Metomotion, who pointed to the numerous challenges being faced by those producing in greenhouses.
“Labour price and availability, energy crisis uncertainty and the market itself with people wanting more for less with better quality and variety are all considerations,” Zisling told the Global Tomato Congress. “Robots are here and they will help tackle not only the widespread labour issues but the others mentioned with advanced AI and technology.
The mechanical arms of Metomotion’s Greenhouse Robotic Tomato Harvester can detect, approach and harvest vines. They promise potential labour cost savings of 50 per cent, with an overall labour reduction of 80 per cent, and therefore offer a glimpse of a more efficient and cost-effective process.
“What does the future look like?” Zisling asked. “The technology of AI is already available and it allows us to go to the next level - not replacing people in the greenhouse but adding to them. AI offers new ways of working and new insights.”
For David Meszaros, founder and CEO of Dutch company Smartkas, which builds climate-neutral fruit and vegetable production centres that embrace a
wide range of new technologies, AI will be more useful in some situations, less so in others.
“I would say that AI can have far more radical and extreme applications in open-field farming, less in greenhouses, and almost nothing in vertical farms,” he outlines. “That’s because the level of control increases in greenhouses and even more so in vertical farms, therefore the variables narrow down.
If there are no variables, he says, all of the parameters are known exactly. “Like the PPFD [photosynthetic photon flux density] of the light, or
the co2 ppm [parts per million]. So what is there for the AI to think about?”
Out in a more natural environment, however, Meszaros believes there is huge potential. “AI can thrive in open field, where there are insects, birds, rain, and so on,” he suggests. “There, with a predictive algorithm, it can start modelling, because everything changes all the time.”
In practice, this would be achieved through the installation of systems like low-frequency ground sensors, GPS-controlled tractors and other automated units, and drones. “But I’m not talking drones for irrigation and pest control,” he explains. “Drones can help create something called an orthomosaic, a stitched-together array of 4K images. This is almost true AI, which creates an accurate
LEFT—Robotics is an area that holds serious potential for the industry BELOW—AI could benefit areas such as data analysis, forecasting, sustainability, sales strategy and more
BOTTOM—David Meszaros of Smartkas
live map of your farm. It can use all kinds of inputs to create a model that shows where your farm is most fertile, where it has a hotspot for bees, for flies, for birds, for whatever. And then you don’t have to spend millions on pesticides and all kinds of preventive measures.”
Ultimately, the question remains: how will AI benefit the industry in the long-term? Juan González Pita, chief operating officer at Argentinean group Salix Fruits, feels that it is going to have a huge impact on how fresh produce companies operate day-to-day.
“AI such as ChatGPT is helping us to refine the way we communicate with our stakeholders, either via the press or even with our social media,” Pita tells Fresh Focus Packaging and Technology. “Our language now is more consistent with the way we want to say things. AI-powered solutions can definitely help to reduce a company’s environmental impact and increase sustainability, but it needs still a lot of data input from the industry and also watchdogs to audit results.
“I don’t see ethical concerns per se, but I do know this is going to affect how each and all of us work on a daily basis,” he continues. “It reminds me of 20 years ago when the internet boomed and all of a sudden communications were faster than ever, and this left a lot of people behind. This feels pretty much the same. That is why I try to understand, to some extent, what the heck this AI thing is, and how it can affect our business.”
Radical improvement in food safety
The hygienic washing that the Citrocide® AVO System achieves represents a radical improvement in food safety, by eliminating surface contamination of the fruit. The washing machine becomes a Critical Control Point, avoiding cross contamination. This system drastically reduces the incidence of Peduncle mold, even after 40 days, allowing shipping to distant destinations without postharvest losses.
The PlantSeal® Tropicals coating doubles the shelf life of the fruit avoiding internal necrosis of the pulp caused by chilling injury that may otherwise become manifest during transport and cold storage. It mitigates weight loss, maintains rmness and does not interfere with the natural color change of the fruit during ripening.
PlantSeal® Tropicals is a coating certi ed for Organic use which is also suitable for vegan consumption.
Weight loss control and maintains firmness Stem-end mold controlTrends in fresh produce processing change constantly, mainly because there are so many factors that drive innovation and new product development: consumer demand, market conditions, technological advances, and many more. However, certain longer-term patterns and trends remain.
Sustainability is one of
these. Very often, the issue is not translated into concrete actions and solutions. Brands will be measured on how sustainable they are, as the industry continues to achieve sustainability targets. We all need to move beyond sterile greenwashing. We must offer innovative and pragmatic solutions. Companies that do not put sustainability at the forefront in 2023 will be left behind.
Verdant Technologies, a subsidiary of our group Gulftech International, has patented a system called HarvestHold that makes it possible, in a completely natural way, to regulate the degree of ripeness of many fruits and vegetables. Broccoli and tomatoes, for example, can arrive on supermarket counters at the right level of ripeness, minimising waste and guaranteeing consumers’ first-rate produce.
ABOVE—The fresh produce business is poised to enter a new digital age
OPPOSITE—Robotic automation is one area where the industry can take a big step forward
Another key trend is automation, but is this the answer to labour shortages? I agree that designing machinery and processes that require less human intervention is the best solution. However, to address this challenge in the right way requires a multidisciplinary approach and an innovative mindset.
What does this mean?
Well, first, select equipment and design layouts that are easier to clean and maintain.
“AI can discover undiscovered correlations and patterns where there are too many variables to handle”
Second, reduce human error by automating repetitive work. The relationship between automation and food safety is clear: no human intervention considerably reduces the chances of contamination.
At the same time, we must bridge the digital divide between untrained operators and those
sophisticated, automated processing line technologies. The increased use of intuitive operational interfaces will certainly help, as will convincing a new generation of digital natives to regard this industry as worth joining.
I also predict an increased use of robotics in processing lines, whereas until now this has been used mainly in receiving and packaging areas.
Artificial intelligence and digitalisation is already helping the industry in different areas, from food safety to automation. For the produce industry, freshness and quality are top priorities, which explains why applications so far have been directed mostly at sorting, grading and inspecting fruit and vegetables.
But AI can discover previously undiscovered correlations and patterns, especially where there are too many variables for the mind to handle. For instance, equipment could reduce energy consumption and food waste without human intervention.
Alessandro Turatti is director of business development at Gulftech International. He has worked for several decades in various sectors of the produce industry in the fields of processing, automation, and digitalisation. The fifth generation of an Italian family that founded the eponymous company in 1869, Turatti has lived for many years near Salinas in California, where he incorporated and directed the group’s North American branch (now owned by two Italian private equity funds). His present position at Gulftech International, a diversified holding group and global leader in the food and packaging sectors, offers him a well-rounded view of topics ranging from the agricultural sector to packaging, with a focus on processing
Also, it is possible to increase yields and working time through preventive maintenance. A programme to continuously monitor equipment and profile its performance could flag when a component or a part requires attention.
In 2023, traceability remains a major focus for the produce industry. The pandemic, ongoing outbreaks of foodborne illness, and regulatory requirements such as the US Bioterrorism Act all make it important to incorporate the most advanced technologies.
Even from a consumer perspective, concern about the origin of food and the way it is processed has never been so high. For example, virtual labels with blockchain technology are already used in the wine industry to enable transparency right along the supply chain.
As for the fresh-cut produce industry, there is undoubtedly a need to reduce costs and increase productivity. Other companies in our group, like ABL and Atlas Pacific, are world leaders in fruit processing. We have new solutions that reduce waste and the consumption of water and energy considerably. Some of these cutting-edge solutions can also be applied to the processing of vegetables and leafy products.
What is clear to me is that categories can be redefined with the inclusion of new processing models. We see this in so-called controlled environment agriculture or vertical farming.
In addition, systems to reduce or eliminate the use of plastic will reshape the fresh produce offer. Another Gulftech company, Sinclair, recently launched a series of compostable labels, which underlines the importance of environmental protection in this business.
Paul
Slupecki,CEO of Tomra Fresh Food, says the company’s new generation of sorters and graders can harness the power of artificial intelligence to improve traceability and connectivity.
by Maura Maxwell @maurafruitnetTwo years ago, Tomra Food split its fresh and processed business into two separate business areas. What have been the main benefits of this new structure and how has it enabled you to accelerate the expansion of your fresh fruit business?
Paul Slupecki: Tomra Fresh is made up of two world-leading New Zealand-based companies that were acquired by Tomra Food – Compac and BBC Technologies. Bringing them together under the Tomra Food umbrella has enabled us to harness their synergies in terms of innovation and technology. What I’ve found really exciting is how well the different mindsets of each innovation team can work together and really move things forward. Their combined expertise has not only strengthened our position with regard to product development, but also our global footprint.
What is it that sets your sorting and grading technology apart from the competition?
PS: That’s a great question. Going back to what I was just saying, I would say a big part is being able
to combine the know-how of BBC Technologies and Compac, having different views about how to do things.
If you look more widely at the whole of Tomra Group, we not only work in food, but also in collection and recycling, where the core technology is similar, albeit used in a different way. We are able to tap into things that are being worked on in one division and use them in another part of the business, sharing the core technologies across the group. The speed and amount of engineering power we have really does set us apart from everyone else.
Tomra has a number of new products coming through the innovation pipeline. What are the next technological barriers that are there to be broken when it comes to sorting technology?
PS: If you look anywhere, whether it’s the food industry or the automotive industry, artificial intelligence is the big buzzword. We’ve been working in this space for quite some time, particularly in the blueberry space with our LUCAi Vision Systems. That is something that is absolutely at the forefront of what we’re doing.
We have some very exciting things coming out in the near future. AI is something that will really
drive improvements – not only the speed of sorting, but also the ability to provide a lot more information in quick time back to our customers so they can make the right decisions.
We are entering a new era of digitalisation and interconnectedness. How is this
shaping the ability for you to link up with other parts of the supply chain in order to enhance your provision to fresh produce customers?
PS: Connectivity traceability is a big thing in the food industry, allowing the consumer to trace a piece of fruit all the way back to the farm, or even the tree that it has come from. We are investing a lot of money in this area, not just in our food division but across all our divisions, connecting every bit of equipment that’s coming out of our innovation and manufacturing pipeline.
“We’re investing a lot of money into R&D so there’s plenty more to come in the next few years – watch this space”
We have developed Tomra Insight, a cloud-based solution offering customers one secure, near real-time monitoring platform for all their sorting lines. Tomra Insight is probably one of the most connectable systems. It provides a wealth of information at different data points, which it then feeds back to the grower so they know exactly what they’ve done right on the farm to produce a particular apple, for example.
Does that connectivity mean there is less need for Tomra to have a local presence in each market as you can service your machines remotely?
PS: Yes and no. In some cases it means we are able to quickly inform the customer of what’s going on and what needs to be done, so the down time can potentially be reduced. It also means we can ensure we have the right components and people available in each region or market.
But it’s equally important to maintain that face-to-face contact
with the customer when a machine requires a major fix or adjustment. We continue to invest in our regional hubs so we can be a lot closer to the customer. Having that connectivity enables us to predict potential issues earlier – perhaps something is starting to wear out, or the fruit is coming out at the wrong speed, suggesting a blockage which would eventually create a problem. That information is fed through to our
are, and if there is a big requirement that needs to be prioritised, we are absolutely in a position to do that very quickly. I would say yes, we are definitely looking at not only the actual packhouse itself but at other areas, working very closely with our customers.
In terms of expansion into new markets, where do you see the best opportunities for growth?
PS: We’re continually looking at where and how the population is consuming fruit and vegetables. The biggest growth area is that middle income bracket, be in
centralised system and back into our service department which means we can react a lot quicker.
Tomra Fresh Food specialises in sorting and grading solutions for fruit and vegetable packhouses. Is there also potential for the development and use of sorting equipment at different stages in the supply chain?
PS: Right now we are focused on the packhouse but as we start to look further up the supply chain closer to the farm, there is definitely the potential to create pre-sorting solutions that could increase the speed at which the fruit moves through the packhouse. This is an area that’s very interesting for us. At the end of the day we want to identify what our customers need
all regions. This is what is driving demand for safe, highquality produce globally. At the same time we have to keep up with new trends. During Covid, for example, we saw a huge increase in citrus consumption because of its high Vitamin C content.
So what can we expect to see from Tomra Fresh in the coming months and years?
PS: We are going to see a lot more interconnectivity between the different regions in which we operate. We want to make sure we are a closer to our customers, not only in terms of manufacturing, but also in sharing expertise across different categories. If we look at innovation, the beauty of Tomra overall is that we have those three pillars of collection, recycling and food where innovation feeds through to the different business areas and fast-tracks the development of new solutions.
At Tomra Food we’re investing a lot of money into R&D and innovation so there is plenty more to come in the next few years. Watch this space!
Real-Time Cold Chain and Logistics Visibility
Cat-M1 for 4G/5G networks
Multimodal support—including air
Non-lithium battery options
Tracking temperature, location, humidity, light
Orders fulfilled within 48 hours globally
FOR MORE INFORMATION PLEASE CALL
+31 (0) 252 211 108 or visit our website
sensitech.com
Experts from Tunley Engineering have released a white paper entitled ‘Sustainable Packaging: Material Selection, Carbon Reduction, and the Role of Legislation in Facilitating a Circular Economy’.
TDR AARON YEARDLEY
Senior carbon reduction scientist
Tunley Engineering
NATHAN WOOD
Carbon reduction scientist
Tunley Engineering
he growing emphasis on sustainability in nearly all sectors has placed the packaging industry under scrutiny. As a critical component of the global economy, the packaging sector holds significant environmental implications. In the pursuit of sustainable packaging, a holistic approach is necessary, encompassing aspects such as material selection, carbon footprint reduction, and the development and implementation of government policies that foster a circular economy.
The three main elements of environmentally sustainable packaging are resource planning, carbon reduction and waste reduction. Resource planning aims to cut waste by encouraging reusability through material choices which facilitate reuse and efficient recycling. Carbon Reduction strives to lower the impact of greenhouse gas emissions by considering the entire carbon lifecycle of packaging, from manufacturing to consumer behaviour. Grasping an understanding of the stages in the lifecycle with the largest carbon emissions enables those areas to be addressed through the initiation of programmes such as utilising renewable energy for production or enhancing transportability through alterations in packaging dimensions or form.
Waste Reduction aims to lower waste volume through strategies like waste prevention, reuse, recycling, and composting. This can be achieved through material minimisation, recyclable or compostable designs, and reusable packaging systems. Using alternative packaging materials, such as recycled paper, biodegradable polymers, and plant-based options, can also decrease the carbon footprint of packaging.
NATALIE BAVIS
Carbon reduction scientist
Tunley Engineering
DR TORILL BIGG
Chief carbon reduction engineer
Tunley Engineering
One method to advance sustainable packaging solutions is through the establishment of regulations and policies that inform decision-making among businesses. Making the environmental impact of a diverse array of materials and products transparent can encourage manufacturers to choose more sustainable options. Environmental Product Declarations (EPDs), for instance, can provide valuable data for comparisons. Nevertheless, the current EPD system contains technical documentation that is difficult to evaluate, whilst there is a shortage of available EPDs. To tackle this problem, it is critical to make these evaluations more accessible to the general public. There is also a need for more sophisticated guidance in evaluating the emissions associated with different disposal techniques. Presently, the emission factors
ABOVE—The issue of plastic packaging remains high on the agenda »
provided by the UK Department for Business, Energy & Industrial Strategy inadvertently provide incentive for organisations to prefer landfill disposal of plastic rather than recycling.
To address this issue, an effective strategy should focus on pinpointing opportunities to decrease carbon emissions specifically from recycling processes themselves. This may encompass investments in cuttingedge recycling technologies, enhancement of sorting and separation procedures, and the investigation of pioneering recycling methodologies for a diverse array of materials.
Besides transparency on the environmental impact of materials, incentives and regulatory measures play a vital role in promoting sustainability. The UK, for example, has taken a leading role in implementing environmental policies such as the ban on plastic microbeads and limitations on single-use plastic items. These policies are important in addressing both the impact on resource use and environmental plastic pollution. The implementation of policies encourages consumers and businesses to adopt sustainable alternatives.
Despite efforts to manage plastic waste recycling, a notable gap persists in the UK between recycling rates of paper/cardboard (71 per cent) and plastic packaging (44.1 per cent). To address this, the UK government introduced a tax in 2022 targeting plastic packaging with less than 30 per cent recycled content. This strategic tax measure is designed to provide businesses with an economic incentive to incorporate recycled plastic materials into their packaging, thereby fostering increased waste plastic recycling and collection rates, and ultimately reducing waste
destined for landfill or incineration. The tax is projected to increase recycled plastic utilisation by 40 per cent and result in carbon savings of nearly 200,000 tonnes during 20222023.
Furthermore, in light of the pressing demand for enhancing the recyclability of packaging materials, the UK government has introduced the concept of ‘Extended Producer Responsibility’ (EPR). As of January 2023, businesses have been mandated to collate data pertaining to their packaging to comply with EPR regulations, with a registration deadline of 2024, at which point fees shall become payable to the environmental regulator. By holding packaging manufacturers responsible for non-recyclable materials, EPR is anticipated to lead to a shift towards reusable or recyclable materials, thus fostering a circular economy.
It is imperative to create informed and balanced policies in order to circumvent potential pitfalls while meeting sustainability objectives and goals. Certain measures may inadvertently encourage bad behaviours, such as an increase in
landfill disposal to reduce the measured carbon footprint of companies who conduct yearly carbon assessments. Policymakers must carefully evaluate the potential consequences of their actions to ensure that they do not result in counterproductive outcomes. Another challenge is the potential for ‘greenwashing’ or the practice of making misleading claims about the environmental benefits of a product or service. Policymakers and industries must remain vigilant against greenwashing and promote transparency.
ABOVE—Packaging policies are important in addressing both the impact on resource use and environmental plastic pollution
Proposed EU regulation, which would outlaw all fruit and vegetable packaging in the EU, needs a major rethink, according to Italian apple suppliers.
by Mike Knowles @mikefruitnetAban on packaging that would require all fruit and vegetables to be sold loose in the EU –except for sales units bigger than 1.5kg – is “discriminatory” and “disproportionate”. That’s according to Assomela, the Italian association of apple producers, which has called on the European Commission to reconsider a draft regulation for its proposed Packaging and Packaging Waste Directive (PPWD).
The regulation would affect all types of packaging, including cardboard, across all sectors. But
Italy’s apple association is among a number of groups in the fresh produce industry that believe it goes too far, and focuses too much on reuse rather than recycling.
A spokesperson for Assomela said the Italian apple sector had made significant efforts in recent years to find and use innovative packaging solutions that are environmentally friendly and safe for consumers.
“Although the Commission’s goals on packaging are generally commendable in the context of a transition towards sustainable packaging solutions, apple producers are primarily concerned about the discriminatory approach used in the proposed regulation for the fruit and vegetable sector and the Commission’s shi of
focus from recycling to reuse,” it said. “According to apple producers, the demands on the sector and [this] specific product category are disproportionate to the overall objective.”
Assomela wants European institutions to reconsider the ban. It also says it wants more transparency and dialogue with stakeholders to determine a reasonable timeline that considers the effects of such a ban.
“It seems the Commission did not consider packaging’s numerous functions in the fruit and vegetable sector,” it added. “Packaging serves to transport and protect the product during transportation and logistics operations; and it is needed to extend shelf-life, prevent food waste, and to avoid microbial contamination.
“What’s more, packaging serves to communicate mandatory information to consumers (such as variety, traceability, origin), and to speak to the consumer about innovations that differentiate the product –in the case of apples, the example of new varieties is obvious.”
The proposed regulation would also mean that all stickers placed on fruit had to be industrially compostable, which means they must be able to break down within 180 days at an industrial composting facility. The term ‘home compostable’, in contrast, means they have to break down within 12 months in the ambient environment.
Duncan Jones, senior marketing manager at Sinclair, looks at navigating the complexities of sustainable fruit stickers.
by Carl Collen @carlfruitnetManufacturing PLU fruit stickers with a compostable construction – adhesive, face stock and inks – to meet food safety standards, certification requirements and performance requirements has been quite the undertaking, according to Duncan Jones of Sinclair.
It requires materials that will compost easily in ambient temperatures but also stay on fruit all the way through to the consumers’ fruit bowl. The label must withstand application in demanding packhouse environments, survive its journey through the entire supply chain –which can last weeks – arrive on a retail shelf, and then be disposed of in a home compost or a composting facility. The characteristics that make a sticker compostable
“Sustainable PLU sticker development gained momentum as more suitable ecofriendly materials became available”
can easily detract from the characteristics needed to survive this challenging process.
“Identifying, manufacturing and testing eco-friendly materials is challenging but continues apace as we work to meet industry needs globally,” Jones tells Fresh Focus Packaging and Technology. “Sustainable PLU sticker development has
gained momentum as more suitable eco-friendly materials become available. This allows for faster development, but with testing taking up to six months for industrial compostable products and 12 months for home compostable PLU stickers, time is a significant factor in achieving OK compost (industrial or home) certification or legislative and regulatory requirements.”
When a material does not pass testing requirements, then o en it is a case of ‘back to the drawing board’ to develop and manufacture a new material for meeting OK compost certification and market requirement deadlines – in France, for example.
A key challenge is the need for a standardised approach, either regionally or globally. The current approach is fragmented with different regulatory, legislative, or voluntary requirements issued differently in multiple markets. Jones explains that, although it is all with the best intentions, this presents challenges for development, customers, the supply chain and costs.
Recently the CPMA released its guidance document for the fresh produce industry entitled ‘Rational and Guidance for Migrating to Certified Industrial Compostable PLU Stickers’. This document is only a guideline based on industry input and collaboration. There are no regulatory requirements at this time, but Jones says the CPMA is taking the initiative for positive change. As well as supporting the CPMA, Sinclair is actively working with organisations and customers in Europe and New Zealand to facilitate change and find practical solutions to the challenges.
“Being at the forefront of all key industry milestones, our team understands the pressures on our customers and the industry,” he adds. “Standard(s) harmonisation allows a more focused development of sustainable products as well as time to develop effective supporting infrastructure like composting facilities where needed. It also allows sustainable PLU stickers to be more widely available, satisfying consumer demand and allowing the industry to realise the benefits of a minimal packing solution –traceability, identification, origin, brand and more.”
GGN is a consumer label that stands for certified, responsible farming and transparency and is available across a range of fresh produce.
by Carl Collen @carlfruitnetAeon has revealed that it has rolled out the first products with the crosscategory GGN label across a range of supermarkets in the Kantō and Kinki regions of Japan. The retailer noted that products now available with the GGN label included tomatoes, aubergines, spinach, asparagus, cucumbers, and Japanese mustard spinach, with more to be added and the range of locations to be extended.
The GGN label is a consumer label that stands for certified, responsible farming and
transparency. Found in stores on both packed and loose fruit and vegetables, farmed seafood, flowers, and plants, the label offers shoppers a quick, consistent way to recognise products that align with their values on the topics of animal welfare and social and environmental responsibility.
Aeon became the first retailer in Asia, and, with Spinneys in the UAE, was one of the very few select retailers worldwide to adopt the original green GGN label on fresh fruits and vegetables in a pilot programme in 2018.
Following the successful conclusion of the pilot programme, the GGN label is being reintroduced a er being rebranded as a single cross-category label for use on fruits and vegetables, farmed seafood, and flowers and plants.
GlobalGAP managing director Kristian Moeller
Abel & Cole is claiming a UK first by becoming the first retailer to introduce eco labelling across its entire fruit and veg range.
The box scheme specialist has begun using Foundation Earth ecoimpact labelling, with products scored on impacts such as CO2 emissions and water pollution.
Foundation Earth is an independent non-profit organisation that brings together scientists and leading industry figures, and aims to unite the food industry behind a single eco-labelling system by working with Life Cycle Assessment experts to gather data and map supply chains..
expressed his appreciation for Aeon’s partnership over the years that had led to the release of the GGN label in stores in Japan.
“We applaud Aeon’s move to introduce our new consumer label,” he said. “Their strong commitment during the successful pilot phase has allowed GlobalGAP to develop today’s growing acceptance in Japan.”
In addition to signalling compliance with GlobalGAP’s Integrated Farm Assurance (IFA) standard, the yellow GGN label includes additional assurance of responsible labour practices through the GlobalGAP Risk Assessment on Social Practice (GRASP) add-on, making it the only label of its kind in Japan to include assurance of good social practices.
The GGN label additionally assures the use of a GlobalGAP recognised residue monitoring system and Chain of Custody (CoC) farm-to-shelf segregation of products with the GGN label.
The GGN label is owned by FoodPLUS GmbH in Cologne, Germany.
Polish foodtech company says its Vidre+ stickers can help save more than 9m tonnes of fresh produce each year.
by Carl Collen @carlfruitnetBELOW—Fresh Inset CEO Andrzej Wolan and the Vidre+ stickers that extend the shelf-life of fresh produce
value and remains fit for the market,” says Andrzej Wolan, co-founder and CEO of Fresh Inset. “All you need is a simple sticker placed on the packaging or the product itself, that’s it.
“The technology can be easily applied on-site directly a er harvest,” he explains. “Growers and packers can turn ordinary packaging that they use anyway into a smart tool that prevents loss of weight, quality, or nutritional value of the product. This gives the food business an incredible competitive advantage. It works with pears, apples, avocados, blueberries, mushrooms, tomatoes, and many more crops. Even freshly cut flowers can be treated.”
“We are talking about an extra few to several dozen days when freshly harvested produce keeps its quality and nutritional value”
Fresh Inset is championing its patented Vidre+ technology for extending the freshness of fresh fruit, vegetables, and flowers. According to the Polish group, the stickers are a “revolutionary solution” that could save over 9m tonnes of fresh produce annually.
The second-generation 1-MCP technology exponentially expands the benefits of produce preservation by mitigating the effects of ethylene. Fresh Inset says that research conducted across five continents proved that the technology works on various crops and varieties from avocados
to grapes, limes, pears, tomatoes, peppers, and many more. The stickers bring a timed and gradual release mechanism that allows produce to be treated by 1-MCP directly in packaging, eliminating the need for a 24-hour application in a sealed storage room or airtight containers.
Fresh Inset is backed by investors including Rubicon Partners, Montis Capital, Infinii and Business Angels, and its international team from the US, Brazil, Argentina, Peru,and Poland includes scientists, senior managers and experts with decades of experience in the post-harvest, international food business. Vidre+ is currently available in Argentina, while the technology has already been patented in 52 countries.
“We are talking about an extra few to even several dozen days when freshly harvested produce keeps its quality and nutritional
“We estimate that our technology can save up to 9.46m tonnes of fruits and vegetables annually,” notes Krzystosz Czaplicki, co-founder and COO of Fresh Inset. “That is equivalent to the weight of more than 612 Brooklyn Bridges in New York City. On top of that, the extended shelf-life provided by Vidre+ can redesign the current global logistics routes.
“By adding additional time for fresh produce in delivery, new more economical trade routes become available for growers, providing an increase in sales, profits and higher customer satisfaction,” he adds.
Fruit Logistica, which took place in Berlin on 8-10 February, saw the most innovative machinery and technology in the fresh produce business on display.
by Carl CollenItalian group marked a half-century in business at this year’s Macfrut in Rimini.
by Carl Collen @carlfruitnetSorma Group, a specialist in automated packing, grading and sorting machinery for fresh fruit and vegetables, has celebrated 50 years in business. Founded by Nevio Lotti in 1973, the Cesenabased company marked the anniversary at this year’s Macfrut in Rimini.
“On this occasion, our thanks go to our founder and everyone who has made Sorma what it is today,” said Andrea Mercadini, CEO of Sorma Group. “It’s easy
to use the word group, but we really are one, and have been for 50 years. From employees who have now retired, who built the company, trained colleagues and installed machines in dozens of countries, to current staff , some of whom have been working for us for more than 35 years, and from suppliers to customers, people are our real added value, because what we do would be impossible without them.”
Sorma has designed and marketed more than 200
machine models and created more than 60 models of packaging, protected by 60 industrial patents developed by its various R&D centres, and it has production sites and dealers all over the world.
In 2022 the group opened a location in Lima, Peru, which is Sorma Iberica’s second subsidiary in South America. “The South American market is growing strongly, and we already have a large number of customers there,” stated Mario Mercadini, marketing manager of Sorma Group, “so opening another subsidiary was the obvious choice. In fact, our automatic packaging lines with optical grading are perfect for the most important local products, such as mangoes and avocados, for which we actually have a specifi c sorter machine.”
System developed by B-hive Innovations and its partners holds huge promise for ground sensing in potatoes.
by Michael Barker @michaelbarkerGround-sensing technology
TuberScan is entering its final phase of testing both overseas and in the UK following the start of this year’s weatherdelayed potato growing season. In its current iteration, the TuberScan system comprises of a bespoke ground penetrating radar (GPR) system, GPS units and in-field and remote sensors, backed up by computer vision and AI, which provide detailed information on potato crop growth characteristics and performance.
The system, which has been developed by agri-tech business B-hive Innovations and partners, also detects where each potato has been planted, to go beyond traditional sampling methods conducted by growers.
The four-year research and development project for TuberScan has been funded by
Innovate UK across two different research programmes. B-hive has collaborated with potato supplier Branston, the University of Manchester and Harper Adams University to create demonstration units.
Effie Warwick-John, project manager on TuberScan at B-hive Innovations, said the project is on track for a successful final season, which has commenced with field trials in Mallorca and Lincolnshire.
“It’s exciting to see how modern methods of monitoring root crop performance could become the norm”
“We are looking to collect as many findings as possible into crop performance by September, addressing the lack of clarity that growers currently contend with when trying to predict growth of their crops underground,” she explained. “The trials in Spain enable us to check that our equipment is working accurately, with enough hardware stocked ahead of the UK growing season to allow for damage to prototypes during testing. It allows us to determine which hardware choices are best suited to the start or end of the season as conditions change and foliage develops.”
Working with Mateu Exports in Mallorca, the project team has been able to take advantage of the earlier growing season in Mallorca, acquiring data across three fields on the performance of
the system, as well as doing trial digs, to compare machine learning accuracy against real world data.
“The Mallorca trials give us a fantastic headstart to be best prepared for the UK growing season,” Warwick-John outlined. ”Acquiring images of plants and stems has helped us to test our image processing pipeline, since we don’t have much time in the
season to check this. We are experimenting with groundpenetrating radar systems (GPR) that can operate to a high accuracy despite having a relatively large air gap between the sensor and the soil, providing a great balance
between ease of mounting and quality of data.”
In the UK, TuberScan has also been trialling in three fields owned by David Armstrong Farms in Lincolnshire to collect additional testing data. Armstrong said: “As a grower, I would like to learn the most about my produce as possible. Ensuring its quality, variety and yield size is crucial to help me make informed decisions around the growing process and understand the marketable yield.
“It’s exciting to see how modern methods of monitoring root crop performance could soon become the norm and it’s imperative that we keep waste to a minimum,” he noted. “From first-hand experience we believe that TuberScan can be a key component to achieving this.”
To conduct further assessment of the technology, B-hive has also installed a polytunnel space to support with TuberScan and other projects, allowing testing to continue when outdoor conditions are too wet. It has also enabled the team to test TuberScan with different potato varieties as well as lighter and darker soils, from which the machine learning technology can be trained to detect the plants.
“The system is continually evolving and beyond September we aim to be in a position to explore the commercial viability of a ground sensing product,” Wawick-John added. “We’ve had great interest to date and hope that TuberScan continues to make a major contribution to eliminating food waste and addressing supply chain issues for the future.”
■
■
■
“RFID technology will allow us to augment the existing benefits of these protected pallets for customers”
Traceability technology for pallets promises to raise sustainability and lower costs.
by Dominic WeaverWhile good traceability has always been important in fresh produce, customer demands for more sustainable supply chains and lower costs have pushed this even higher up the agenda – and suppliers are looking for applications that can help them enhance their performance in this area.
Packaging tracking is one of the most promising solutions currently being trialled. The price of RFID (radio frequency identification) tagging technology has dropped significantly since its first use more than 20 years ago and is now becoming a viable method for tracing FMCG and other goods; while keeping pallets and other packaging in circulation, increasing reuse opportunities, and reducing costs.
This is one of the developments currently being put to test by Upall pallets, a joint venture headed by one of the UK’s largest suppliers of wooden pallets, James Jones & Sons (Pallets and Packaging) Ltd.
Upall extends the average lifespan of the FSC-accredited wooden ‘Euro’ pallets already used in supply chains from FMCG to pharmaceutical products by more than three times, according to testing at Virginia Tech and Napier University, Edinburgh. Robust guards fitted at the points of entry for forklifts or pallet trucks, protect the most frequently damaged areas of the pallet, including blocks and base boards, and make them highly resistant to impact.
Following the academic testing, products are now being trialled in
real-world situations by businesses keen to reduce downtime during the lifespan of their pallets and increase the number of times they can be used before they are recycled.
In addition, and in response to customer requests, planning is underway to fit RFID tags on the Upall pallets, allowing firms to add product traceability and boost the benefits of the new pallets in the process.
The new ‘passive’ RFID tags are scanned once the pallets arrive at their destinations, allowing users to know their location as they move around the site. The tag is scanned at each touch point on site – including dispatch, return and repair. This gives users sight of where their pallets are in their supply chain and dramatically reduces the likelihood of the products and their pallets from going missing in transit. This is also important for these enhanced pallets because their longer lifespan, cost savings, and sustainability benefits increases their value.
“RFID technology will allow us to augment the existing benefits of these protected pallets for customers, increasing the reliability, sustainability, and economy of any supply chains that use wooden Euro pallets,” said James Jones & Sons (Pallets and Packaging) managing director Peter McKenzie. “We are working with our existing pallet clients to test these in real-world situations and are looking forward to reporting back on the results we achieve.”
Initially known just as a small, tasty fruit, blueberries have become a ‘superfood’ demanded by consumers all yearround, and they have become a globalised product available on the table of health-conscious consumers wherever they may be.
High consumer expectations in terms of quality, taste and availability – 365 days per year on a global scale – require a meticulous selection process, based on the ideal nutritional profile desired by the target market, and based on the capability of the fruit to handle long-distance journeys.
The blueberry sector is in constant development and the trend is driven by growing consumer awareness of its nutraceutical properties and the many uses of these small fruits. To get consumption to rise along with a rise in production, it is necessary to have reliable, patented technologies, which are the key to responding to market demands.
In 2013, Unitec designed and developed the first technological innovation for blueberries –Blueberry Vision, subsequently updated further to the Blueberry Vision 3 system – for nondamaging sorting of external qualities (shape defects, soft fruit, in addition to optical size and colour), capable of sorting up to 45 fruits per second per lane with maximum reliability, precision and efficiency on top of using gentle handling technology for small fruit.
Thanks in particular to the Blueberry Vision 3 system, which is included on the Unical 222 Berry
labelling and the use of robots for palletisation, to make work processes more efficient.
sorter, packing houses are able to inspect the entire surface of each blueberry, using sophisticated high-resolution cameras, to sort the fruit according to external quality parameters, like colour and shape – in addition to optical size, for example.
The UNIQ Blueberry system – a highly reliable solution for sorting internal qualities without damaging the fruit – completes the offer for blueberry quality sorting.
Lastly, Unitec works to automate a greater number of processes in the warehouse, in response to labour issues – the shortage of workers, alleviating repetitive and stressful tasks – by integrating technological solutions for
Unitec is closely connected to the market in which it operates, thanks to its 20 branches spread across five continents, thus able to handle the challenges of the sector, by offering technological solutions capable of sorting by the qualitative parameters of the small fruits.
Technology can support the industry, explained Nour Abdrabbo, sales director of Unitec Group, at the International Blueberry Days held during Macfrut in Rimini on 4 May: “In these past few years, blueberries have gone from being a ’superfood’ to a ‘tasty superfood’: in addition to being good for your health they must also be good enough to satisfy the palate.”
He added: “Thanks to the technological development of UNIQ Blueberry, entirely designed and built internally at Unitec, we meet the challenge to select fruit based on its internal quality, to guarantee an excellent palate experience in any market in the world. Innovation has been part of our DNA for the past 100 years and the process of technological development continues, staying connected to the market and to our clients, according to our mission in Unitec.”
Unitec, we work for your results.
Recent growth in the Spanish retailer’s physical and online network means investment in greater automation and renewable energy are essential.
by Mike Knowles @mikefruitnetMore efficiency through automation, and improved sustainability thanks to greater use of renewable energy, are at the heart pf Spanish supermarket chain Mercadona’s plan to invest over €60m to develop and modernise its fresh produce logistics facility in Riba-roja del Túria, in Valencia.
The project, which started earlier in 2023, aims to improve processes and infrastructure at the site. The expansion will increase the size of the facility from 23,000m2 to 40,000m2, and the company says it will boost efficiency and production capacity.
In addition, Mercadona will introduce an automated preparation system called Picking Puente Grúa to reduce physical strain on workers. And, as part of its commitment to the environment, it will install 7,500 solar panels. These will meet 15 per
Mercadona will introduce an automated system called Picking Puente Grúa to reduce the strain on workers
cent of the facility’s annual energy requirement.
Throughout the extensive two-year renovation, products currently handled at Mercadona’s warehouse in nearby Paterna will
be temporarily relocated. Another logistics facility in Parc Sagunt will assume temporary responsibility for the operations of both the Riba-roja del Túria and Paterna warehouses.
Mercadona’s logistics network currently spans over 1.4m square metres. In that respect, making sure that its resources achieve greater productivity and protect the environment are key priorities.
“Through responsible protocols, innovation, and advanced technology, Mercadona aims to minimise its footprint in the communities it serves,” the company notes.
With 16 operational logistics blocks, two satellite warehouses, and two regulatory warehouses, Mercadona’s entire logistics operation supports a network of more than 1,600 supermarkets in Spain and Portugal.
ABOVE—The Ribaroja del Túria facility, near Valenca
BELOW—One of the group’s latest store openings in Portugal
60 million euros to be spent on retailer’s facility revamp
100%
WRAP-TRAY Adaptable to sizes
THE USE OF CARDBOARD LID ON TRAY BRINGS UP TO 15% COST SAVINGS .
FLAT®-TRAY Free fillable
PACKAGING OF ALL FRUIT SIZES AND SHAPES
COST SAVINGS THROUGH OPTIMAL PRODUCTION AND LOGISTICS
THE SOLUTION: JOLLYPACK & BLITZMATIC+ EFFICIENT CARTON PACKAGING LINE
LINE INTEGRATION: FILL AND CLOSE
Vertical farming is increasingly being regarded as one of the solutions to the problems faced by global food production systems. Measurement and control technology will be key to the success of this rapidly growing sector.
Outdoor agriculture occupies around half of the planet’s habitable land, and so-called modern agricultural practices have enabled the production of increased food volumes at relatively low prices.
According to the World Bank, agricultural development is one of the most powerful tools to end extreme poverty, boost shared prosperity, and feed a projected 9.7bn people by 2050.
However, it has been estimated that around 768m people were hungry in 2021. Furthermore, agriculture, forestry, and land use change are responsible for about 25 per cent of the greenhouse gas emissions that are driving global warming, and agriculture uses about 70 per cent of fresh water supplies. These challenges are of course exacerbated by climate change.
In recent decades, growth in agricultural production has come with a heavy price; causing unsustainable harm to the environment and biodiversity. Increasingly large areas of mono-cropped fields have reduced biodiversity and are frequently treated with fertiliser and agrochemicals that inflict environmental damage. There are also increasing concerns about the effects of agriculture on soil health. Agriculture is extremely sensitive to the effects of climate change, with higher temperatures, drought, flooding and extreme weather all presenting greater risks for farmers. The sector is therefore seeking to lower climate risk in its supply chains. This includes analysis of the carbon footprint of products, creating a requirement to reduce ‘food miles’ and encourage
the consumption of locally sourced food. Dwindling water resources are also driving the need for the assessment of water footprints.
Bringing agricultural production indoors resolves many of the challenges outlined above. For example, crops can be provided with ideal growing conditions, whatever the season, whilst being protected from variations in the weather. Water can be recycled, and pesticides are almost completely unnecessary. With no soil or pesticide contamination, water efficiency is further enhanced by the absence of a requirement for washing.
Traditionally, greenhouses and hydroponics have offered solutions to many agricultural problems, but with urbanisation, and the high cost and low availability of land in urban areas, it is difficult to resolve the food miles challenge.
Vertical farming dramatically reduces the physical footprint of food production, but given the high cost of energy, it is vitally important for the financial sustainability of vertical farming that it operates as efficiently as possible. For this reason, sensors perform a critical role, which is why Vaisala sensors have been deployed in the UK by the Jones Food Company (JFC) in their existing vertical farms, and in the enormous new facility in Lydney (JFC2) that is likely to become one of the largest vertical farms in the world.
JFC was established in 2016 to exploit the advantages of vertical farming to provide fresh local produce all year round.
The company’s first commercial vertical farm (JFC1) started production in 2018 with 5,000m2 of growing space and the capacity to produce 150 tonnes per year of fresh produce. JFC2 will be much larger with a growing area of 15,000m2 and a growing capacity of 1,000 tonnes per year.
JFC’s Innovation Centre in Bristol has the capacity to trial ten different crops under different conditions, concurrently. “This is fundamentally important to the success of the business,” explains Justin Au, operational grower at JFC. “When a customer approaches us looking for a specific crop, we are able to rapidly conduct trials to determine the optimal growing conditions for
that crop, and at every stage of its development. The monitoring and control system allows us to change both the intensity and spectra of light from the LEDs, as well as the nutrients in the irrigation water, and the temperature, humidity and carbon dioxide levels in the growing rooms.
“Once the optimal conditions have been established for a specific crop, we can be confident that we will be able to grow it at scale, and fulfil the customer’s requirements. Our objective is to drive efficiency so that we can compete with existing on-shelf products but with the substantial sustainability advantages that vertical farming delivers.
“Currently, we are growing herbs such as basil, dill, parsley, coriander, mint and chives; salads such as lettuce, rocket, pak choi, spinach, chard, kale and watercress, as well as other crops such as strawberries. Inevitably, the range of crops that we can grow commercially with vertical farming will continue to expand.”
“Once the optimal conditions have been established for a specific crop, we can be confident that we will grow it at scale”
Water is constantly recycled at all of the JFC facilities with continuous measurements of pH and conductivity helping to ensure the regulation of plant nutrients with dissolved fertilisers. The Vaisala sensors measure temperature, humidity and carbon dioxide; all of which have significant impacts on the growth of plants.
The first harvest for JFC2 is due in the summer of 2023, and with 15 layers, every acre becomes 15 times more productive. The roof of the new facility is entirely covered with solar panels, and 100 per cent of the energy will come from renewable sources. Rainwater will be harvested and filtered, and almost 95 per cent of the water will be recycled.
In order to maximise the efficiency of growing conditions in JFC2, the entire facility will be monitored by a network of Vaisala sensors, including 46 RH/Temp sensors; 12 CO2 sensors; ten Temp/RH/CO2 sensors; two atmospheric pressure sensors, and a Vaisala WXT 530 series multiparameter weather station.
The accuracy and reliability of these sensors will be crucial to the efficiency of the ongoing demandcontrolled management of plant growth conditions because accurate measurements help maximise production while avoiding waste and minimising costs.