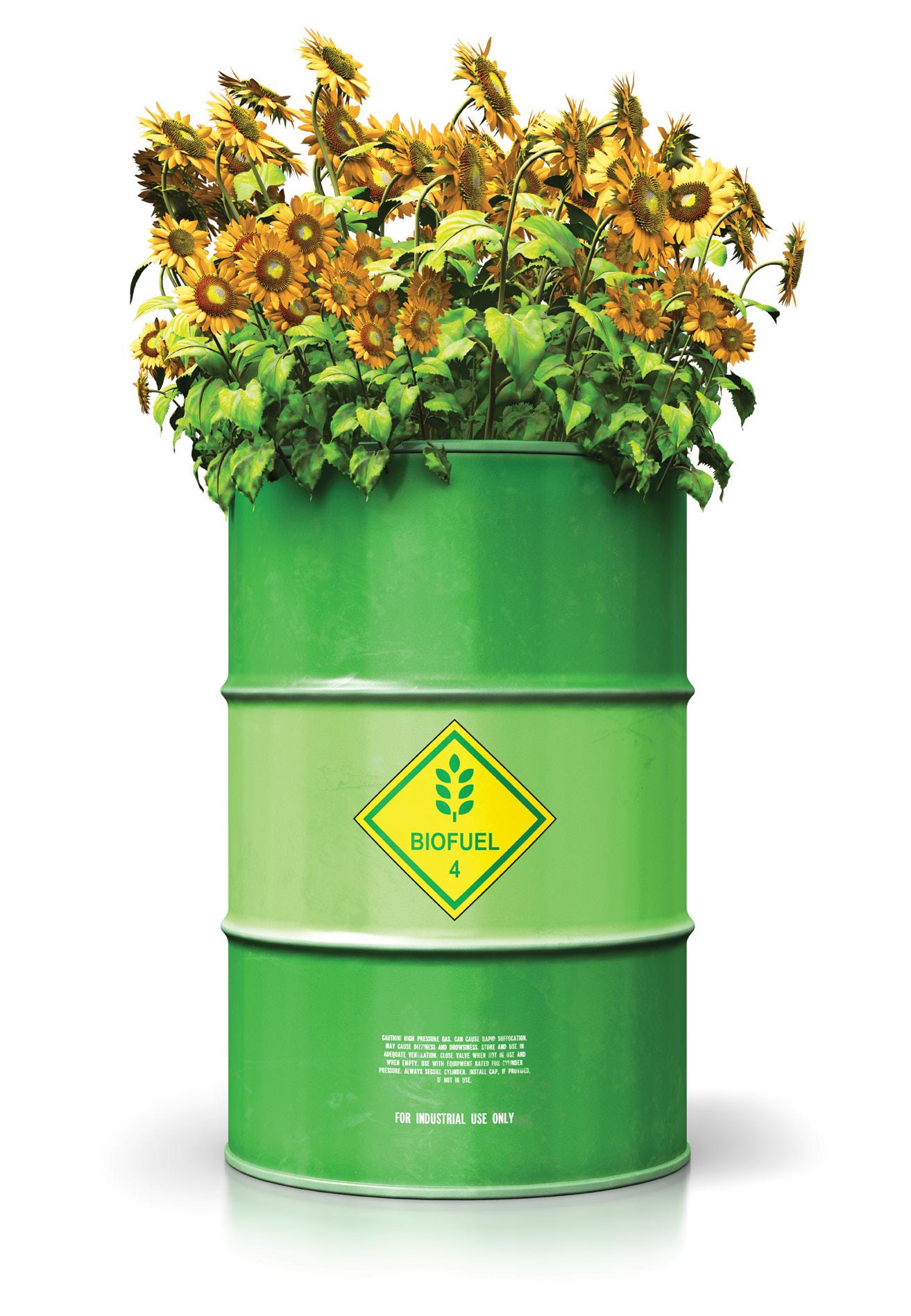
11 minute read
BIOFUELS
How easy is it to bring biofuel storage into a bulk plant or terminal operation?
By Keith Reid
Five years ago, Robert Brown had the opportunity to acquire a small fuel terminal to support his growing heating oil delivery operation, Broco Oil. “It was a small terminal, but I always saw the benefit of having some bulk oil on hand to take advantage of market swings,” said Brown.
Brown, along with his wife Angela, began building Broco Oil with a single delivery truck in 2007, after he left the Navy Seabees. It was about this time that heating oil dealers realized that a move to a more environmentally acceptable fuel was inevitable.
In the prime heating oil markets of the Northeast—where Broco Oil is based—and the Northwest, there is a strong environmental focus among both legislators and customers. While some operations began to explore propane, the heating oil side began its move to Bioheat. A common goal among heating oil marketers is to reach a 50% blend of biodiesel and heating oil by 2030 and net-zero carbon footprint by 2050. There is a similar push for low-carbon motor fuels among their fleet customers.
“We wanted to do biodiesel back in 2017, but I was afraid to kick it off because I didn’t want to do it incorrectly,” Brown said. He was particularly concerned with splash blending and wanted to have greater control through a blending system at the terminal. However, trucking in biodiesel for blending had been problematic. That problem shortly resolved itself.
“Having rail access was kind of an unforeseen thing. When we first bought the terminal there was a rail line behind the property,” Brown said. “Then a couple months later, after we’ve been watching the freight go by, my wife went to the Registry of Deeds and said, you know, the previous owners were deeded. And that’s how everything started rolling.”
Incorporating Biofuels Into Your Storage Facilities
Carbon reduction has become a more front-line issue today, and nationally fuel marketers are considering adding biodiesel blends, renewable diesel and enhanced ethanol products, among others, to their conventional fuel mix. While they can purchase pre-blended product, many like to be the blender of record and take advantage of RIN opportunities. However, setting up a storage and blending operation can be quite expensive and may not be worthwhile for smaller operations.
“A lot of the smaller guys know if you want to survive long term, you have to get into alternative fuel somehow,” said Mark Savage, owner of Savage Associates. The firm has been a leader in providing liquid and gas transfer equipment and systems to the petroleum, chemical and industrial markets since 1948. “And you have operators with very limited racks, where you just have a pump. Unless you want to spend a lot of money, the best option would be to bring in a tank and pre-blended product. Don’t do it at your rack.”
A key cost includes modernizing an older system (it’s not uncommon for many plants to have gone decades without significant upgrades) and making sure they are fit for the new fuels. Biofuels can require specific materials. For example, the seals used in a range of equipment, such as pumps, need to be compatible, and pumps might need replacing. Blending at the rack requires modern meters and software. New storage is often required for the new fuels, and that comes with significant add-ons to manage product in colder climates.
Savage noted that his firm worked on a plant to bring in biodiesel blending where age was a factor. “I said, ‘The meters you’ve been using are very, very old. Parts are no longer made for them.’ The site owner responded with, ‘They’ve been working for us for the past 30 years, and maybe they will workout for us now.’”
The instillation proceeded with biodiesel ratio blending. However, during the test the meters started to see a different pressure flow rate, became unreliable and had to be replaced.
Storage Tanks
For Brown, the upgrade process was extraordinary. The Broco Oil location went from eight 10,000-gallon heating oil tanks with two load positions to 250,000 gallons of heating oil storage, 50,000 gallons of on-road fuel storage and 150,000 gallons of separated biodiesel storage and associated piping. All feature offloading equipment on the rail side. “If I showed you a before and after of the terminal you wouldn’t think it was the same site,” Brown said.
Adding storage is a significant cost factor, with the cost dictated by the available space, layout and local regulations. Through a combination of luck and experience, Broco managed to minimize its expenditures.
The first set of biodiesel tanks that were installed were a demolition from a decommissioned site in Connecticut. “There were six oil tanks, and we were basically told we could have the tanks if we broke them down and transported them off-site,” Brown said. “The whole growth of the terminal has been self-performed by us—excavating, pouring the concrete pad, the containment, setting the tanks. We cleaned out all our tanks and made way for the new biodiesel feedstock.”
His many years of experience as a Seabee performing similar projects, assistance from his peers and an unrestricted builder’s license made this possible. Those lacking such a background are strongly encouraged to contact industry engineering consultants and experienced contractors for the work required.
If the operator is converting an existing tank to biofuels, a thorough cleaning is recommended. These new fuels tend to be very aggressive cleaning agents in their own right, leading to potential fouling issues downstream of the tanks as built-up contaminants are scoured off and enter the system.
Another consideration with biodiesel (but not ethanol) is its increased sensitivity to the cold relative to cloud and pour points. While regular diesel has similar concerns, biodiesel is more sensitive, although these issues are certainly manageable.
“B100 is a little different because everything has to be heated and insulated,” said Tony Cooper, vice president of construction at Acterra Group, which has provided equipment, manufacturing, consulting and specialized construction services to the fuel, renewable energy, government and fleet industries since 1958. “Your product, pipes, pumps, meters, you get into an awful lot of expense when you get to that. People aren’t aware of the expense of getting into all that. And then there’s a lot of maintenance with that. Having to maintain all your valves and that kind of stuff once they’re insulated isn’t the easiest thing either.”
Savage noted a circulation system should be installed in the tank if the throughput is limited, and temperatures should be maintained in the range of 40 to 50 degrees.
For Broco, all five 30,000-gallon biodiesel tanks are maintained at a constant 70 degrees. Introducing warm product to an already warm tank requires less energy to keep it heated. The heating is provided by three commercial-size boilers using B100.
“We’ve been able to save money because the system runs clean on the B100. Our costs have gone down every year since we’ve been using that. And this year we’re hoping to see a 25% reduction in heating costs to keep that product at temperature.”
Fuel Blending
Product blending is one of the core capabilities marketers pursue when adding biodiesel to their bulk storage facility. It provides both better quality control and solid recordkeeping for RIN opportunities. Quality control can be particularly important in colder climates where splash blending can face challenges. Among several similar stories Savage recounted was the following.
“We had an account that would go over to a facility and load up maybe a hundred gallons of B100, then drive down the road in the dead of winter to the bulk terminal, where they buy their
No. 2 oil and load the compartment,” he said. “And what had happened was the B100 started to solidify before they reached the other rack because it got colder than 30 degrees inside the compartment.”
As noted previously, blending will likely require modern meters and a blending system. Software can also facilitate the RIN management process.
“When you’re blending at the rack, that’s all done electronically,” Savage said. “You have two valves and two meters that work together. It’s all done electronically—recorded electronically— and you’ll see any issues, errors or deviations within the electronics. So, it’s just a matter of getting the electronics programmed properly. And once it is, it’s almost a set and forget. Then teaching the operator how to handle any alarm that comes up.”
Savage noted there are some significant blending considerations with ethanol compared to biodiesel. “You have the coefficient of expansion within ethanol,” he said. “Ratio blending is typical for biodiesel, where you have the two meters coming in at the same time. Pretty much they blend in a coordinated fashion. With sidestream blending, you want the ethanol to come in before the product meter. All the expansion happens theoretically before your final meter and your customer’s truck or tank.”
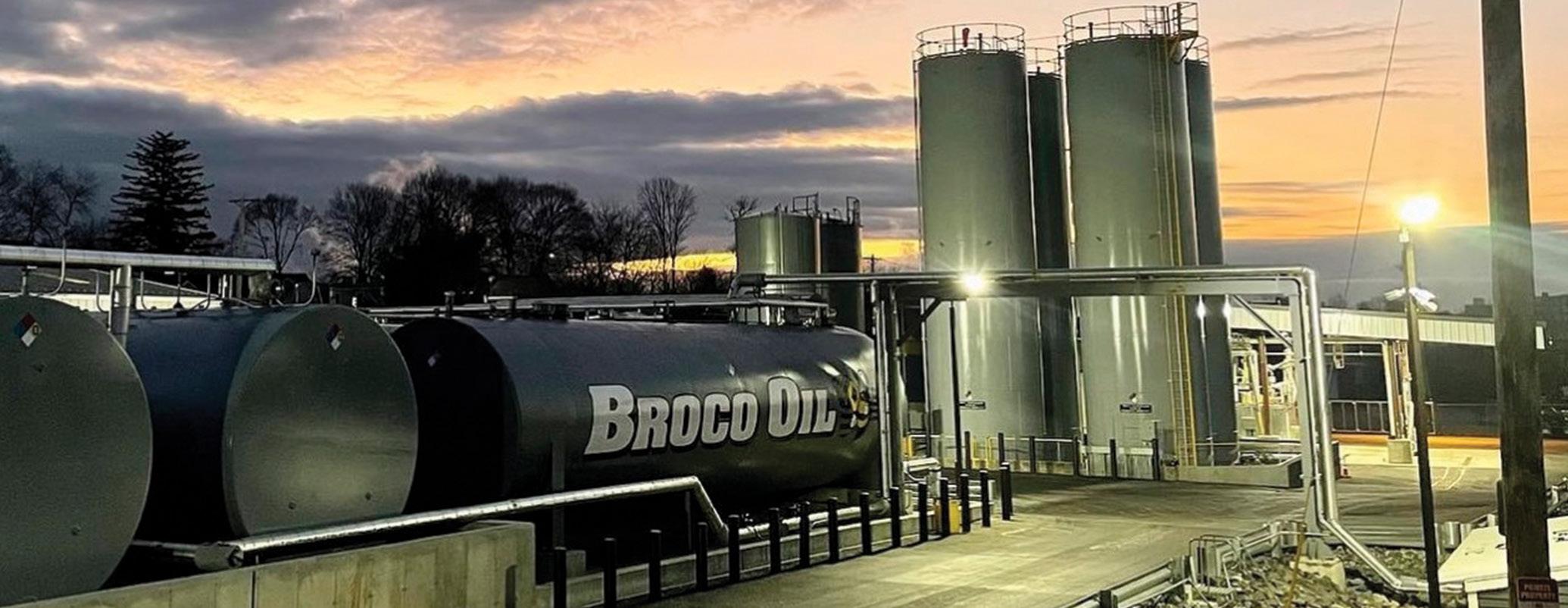
Additive blending also becomes automated and easier, but as with everything at a cost.
Operational Issues
Much of the operational maintenance is similar to maintenance when using conventional products—looking for leaks and such. However, there are differences.
Insulated tanks and piping must be inspected. Temperature needs to be monitored and the systems maintained.
Perhaps most noteworthy is the increased need to keep water out of the system. Water leads to biological growth, which generates acids that cause corrosion within fueling systems. It also creates phase separation issues with ethanol. Savage noted that any horizontal tank Savage Associates installs is pitched, and at that low end there is a drain valve.
Today’s terminal automation software is also useful for a range of operational monitoring.
“We have software with Toptech Systems,” Brown said. “It gives you daily reports on inventory levels. It gives you temperature readouts through our probes that we have installed in each tank. It gives you water levels if there is water detected so you can drain it off the bottom. It’s one of the key components that we use for our quality control daily. Those printouts give that visibility to us and to REG/Chevron because they will send wholesale customers through our terminal.”
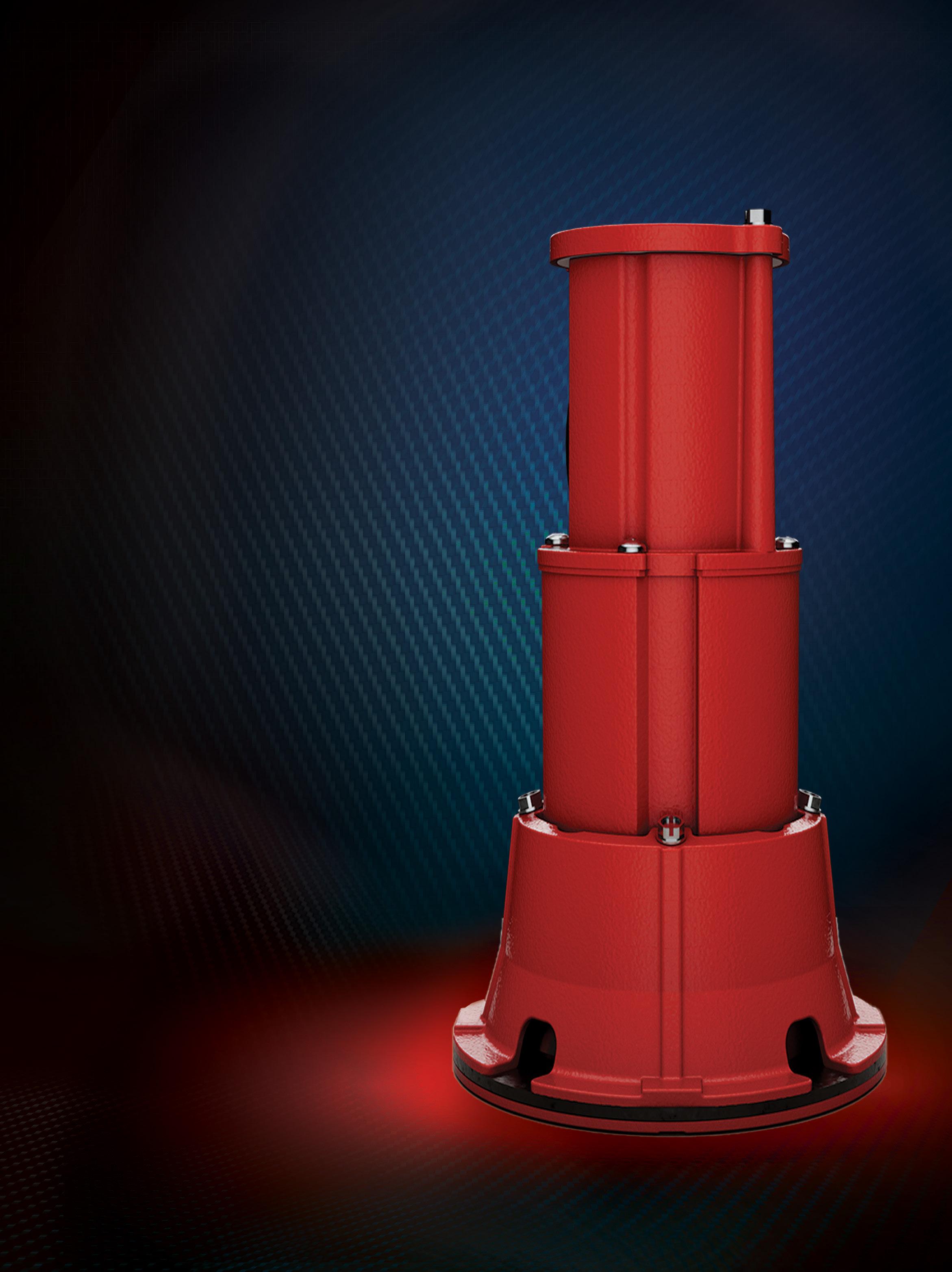
Biofuels Open Doors
For all the cost and complications, biofuels open doors and present opportunities.
Broco has used its blending capabilities to meet the needs of both heating oil customers and municipal biodiesel customers.
Broco’s heating oil customers in Massachusetts, New Hampshire and Maine are receiving a B50 blend. The company has reached this level by going up 10% each year since the blended fuel program began. The goal is to get the blend up to B80 by 2025. “I think we’ll be able to achieve that,” Brown said. “But we have to do it slowly because a lot of these customers have systems that are old and it’s such a clean agent, we’ve found that it’s scaling off a lot of the sludge built up in these older tanks and trying to push it through the lines.”
Broco also does business with local and state entities working to lower the carbon in their fleet operations.
“We get a lot of support from the Massachusetts Bay Transportation Authority,” Brown said. “We do a lot of work with them anyways, providing their fuels. And now we’re in talks with them to start working them up to going solely on renewable diesel in the next five years.” The company has numerous similar opportunities throughout the region.
Broco also leverages its terminal on the wholesale side. “We can sell anywhere from a B5 to B90. And sometimes people would like to pick up just straight B99,” Brown said. “So, we opened our terminal for other companies, some that would be our competition. But having this be a regional incentive, that’s the whole reason why we opened it up, not to hoard it for ourselves, but to make us an industry leader in the biodiesel world.”
Keith Reid is editor-in-chief of Fuels Market News. He can be reached at kreid@fmnweb. com
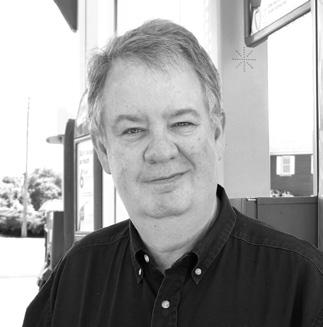


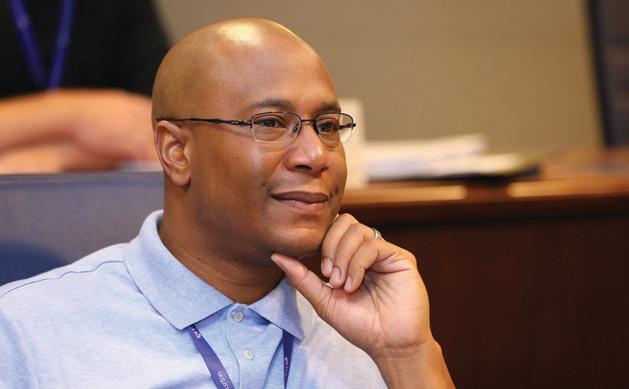
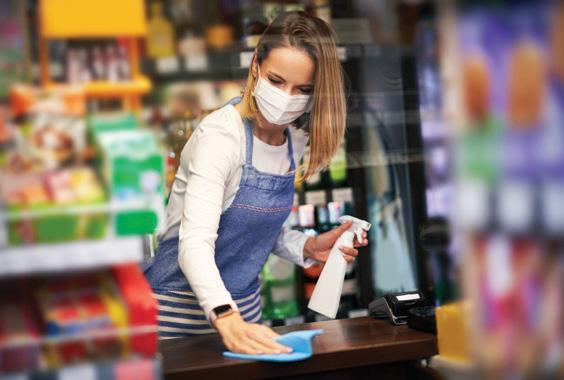
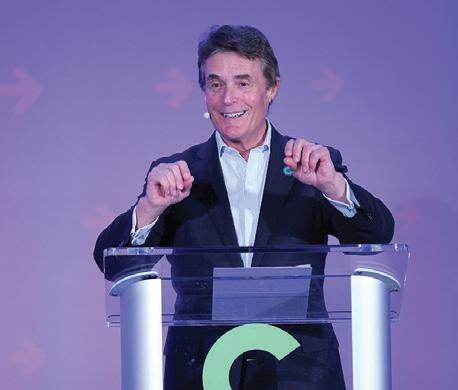
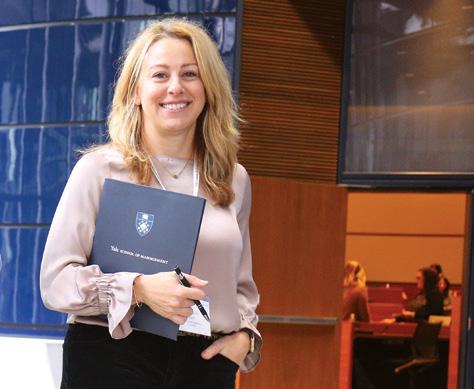

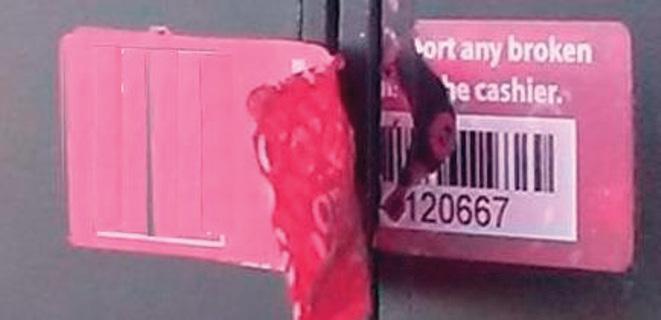
Add Systems Celebrates 50th Anniversary
ADD Systems (Advanced Digital Data, Inc.) has announced its 50th anniversary. In 1973, ADD Systems strived to improve the way energy distributors operate. Today, ADD Systems is happy to carry on that same goal in the energy distribution, HVAC and c-store industries. ADD Systems started with the single vision of its founder, Bruce Alan Bott. ADD Systems now has over 150 employees, United States and Canadian offices, and many clients throughout North America. Since the beginning, ADD Systems has led with these three principles: “Be honest, be fair, and treat others as you would expect to be treated.”
Spatco Energy Solutions Acquires Petro Supply
SPATCO Energy Solutions completed the acquisition of Petro Supply, a leading distributor of petroleum equipment in the Mid-Atlantic region, with offices in Elkridge, Md. and Richmond, Va. The addition of Petro Supply to the SPATCO family strengthens its position in the petroleum industry. SPATCO now has over 750 employees with 400+ technicians in 26 branches across 13 states in the Southeast and Mid-Atlantic region. It has over 88 years of experience as the go-to provider for petroleum fueling, installation, maintenance, environmental service and electric vehicle infrastructure solutions. In this ever-changing market, SPATCO continues to execute an ever-growing pipeline of infrastructure to support the needs of its customers.
Opw Retail Fueling Announces The Tse Tank Sump
The TSE Tank Sump is the latest addition to OPW’s E-Series Containment Sump product family. TSE sumps are part of the industry’s first composite containment system built using the advanced fiberglass sheet-molded compound (SMC) manufacturing process, which results in a high-quality sump that increases peace of mind for fuel-site operators. The SMC manufacturing process also gives the TSE sumps the shortest delivery lead times in the industry, consistent wall thickness and smoothness for a watertight seal and a value price when compared to competitive fiberglass tank sumps.
Pdi Technologies Acquires Blue Cow Software
PDI Technologies, a global leader delivering solutions and insights that serve as the backbone of the convenience retail and petroleum wholesale ecosystem, has acquired Blue Cow Software LLC, a fuel oil and propane management software business. With this acquisition, Blue Cow Software will divest from Repay Holdings Corporation, a leading provider of vertically integrated payment solutions. Blue Cow Software is an industry leader among heating oil and propane dealers. The robust capabilities it offers include fuel and service ordering, delivery route optimization and wireless communication with field teams, fuel oil- and propane-specific analytics, and customer relationship management and accounting, among other innovations.
D&H UNITED ACQUIRES DOUBLE CHECK
D&H United, a portfolio company of Wind Point Partners and a leading provider of mission-critical maintenance, testing and inspection services for fueling stations and electric vehicle charging infrastructure, is pleased to announce the acquisition of Double Check Company. Headquartered in Kansas City, Mo., Double Check Company is a turnkey provider of maintenance, distribution and installation services for retail fueling systems and car wash stations. The acquisition of Double Check Company marks D&H’s entry into the Missouri and Kansas markets and extends its service footprint across the Midwest. The combination will further increase D&H’s service focus and will expand on its growing capabilities in the carwash and automotive maintenance services.
WESTMOR ACQUIRES METZLER BROS. TANK, TRUCK AND TRAILER
Westmor Industries LLC, one of North America’s most comprehensive energy storage, transportation and dispensing equipment manufacturers and suppliers, announced its acquisition of Metzler Bros. Tank, Truck and Trailer. The new location has been rebranded as Westmor Industries and expands Westmor’s ability to sell and service refined fuel and propane transportation products in the mid-Eastern U.S. Westmor’s Eastern customers will now have access to an extended network that includes a location in Duncansville, Pa. Metzler Bros. Tank, Truck and Trailer’s customers will get the same great people and service they’ve always worked with plus access to numerous other locations, products and services.
Corrigan Oil Selects Irely For New Erp System
iRely LLC, an innovative partner providing enterprise software for petroleum distributors and convenience stores, announced Corrigan Oil selected iRely as its partner of choice for its comprehensive ERP and operational software solution. Founded in 1958, Corrigan Oil is a family business in its third generation, owned by Mike and Tim
Corrigan. Corrigan is a distributor of fuel, lubes and propane, headquartered in Michigan. With offices in Michigan, Ohio and Indiana, it distributes in more than 20 states and Canada. iRely will be replacing its current back-office system while also becoming its single logistics solution.
CITGO RAISES OVER $2.3 MILLION FOR MDA
CITGO Petroleum Corporation concluded another successful fundraising year with more than $2.3 million raised for families living with muscular dystrophy, ALS and related neuromuscular diseases. Funds raised will be used to help accelerate research, advance care and advocate for the neuromuscular community. CITGO employees, marketers, retailers, vendors and contractors held several fundraisers throughout the year. Golf events in Lake Charles, La., Lemont, Ill., and Corpus Christi, Texas, each had record-breaking results, raising more than $400,000 each, while a Houston golf event raised more than $880,000. A bowling event in Lemont raised more than $110,000.
Bestpass And Comdata Announce Partnership
Bestpass Inc., a comprehensive payment platform provider and leader in toll management solutions