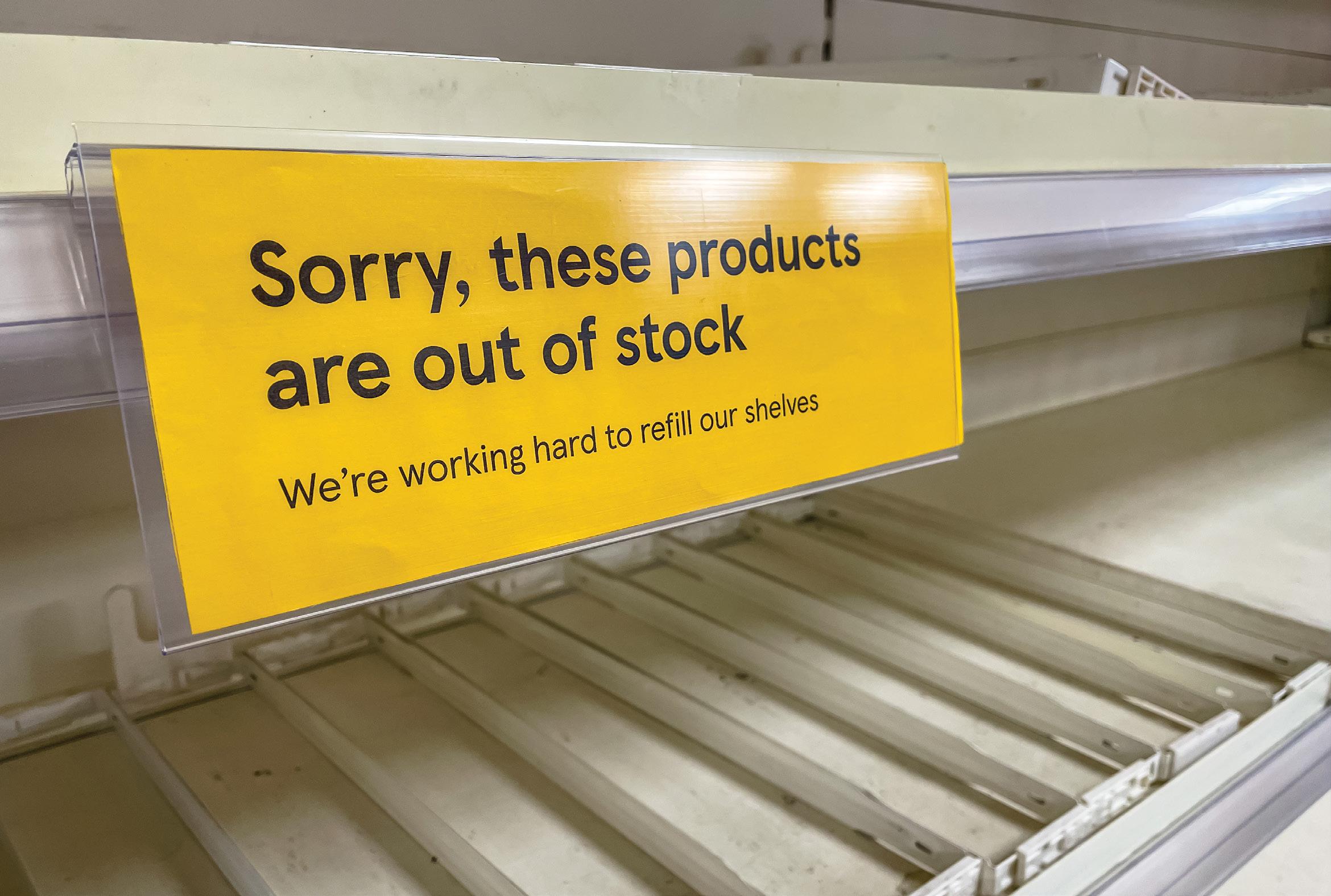
5 minute read
Empty Shelves and Trucks
Eight tips for dealing with out-of-stocks and other supply chain issues.
BY ROY STRASBURGER
“Oh, dearest father. If my heart’s greatest desire is not fulfilled by Christmastide, surely I will perish from this earth and my ghostly remains will wander these lands for the rest of eternity.”
This, or something like it, is what my then six-year-old daughter told me many years ago when she was informed that the hottest Christmas toy on the market was sold out everywhere in our fair city. The fact that there was a supply issue did not ease her pain or lessen the consumer demand element of the market economics that ran through our house. However, through heroic efforts I was able to save Christmas for her that year. (By the way, the toy was never seen after the second week of January.)
This was the memory I recalled when I heard that the product shortages and supply issues that we have been facing may extend through the holiday season and affect Christmas shopping.
In one form or another, we have been dealing with product issues in almost all our stores. They range from not being able to get items because of actual product shortages (drink cups) to products not being delivered because of the lack of truck drivers (soft drinks and groceries).
No one wants empty shelves in their store. It obviously directly impacts sales because the items that you don’t have can’t be sold. But it also indirectly affects your sales since it gives your customer the impression that you are going out of business and the items that are left on the shelf may be old or unsalable.
I thought it might be helpful to share some of the approaches that we have taken to deal with our supply issues.
Communicate. The first thing you should do is talk to your supplier to find out the issues they are facing. It is in your supplier’s best interest to get items delivered to you—that is how they make their money—and they should be willing to work with you to come up with creative solutions. Understanding the problems they are facing will help you determine your response.
Plan. If the supplier is having issues with transportation, plan your ordering to anticipate delivery delays. If you can only get a delivery once every two weeks rather than weekly, you need
to double up on your orders to have enough product on hand until the next delivery. This may affect your cash flow as your cost per order will increase, and you may need to find additional storage space since you will have more stock on hand. You may also be able to arrange with the supplier to pick up your products at their warehouse.
Substitute. If the supplier is having a supply issue, meaning that they can’t get the product into their warehouse, talk with them to see if they have something in stock that can act as a substitute. Having a different brand of the same type of product is better than not having the product at all. Most customers will accept a short-term alternative for their favorite brand if they understand the problems you are facing. The same is true with foodservice supply items— what does your supplier have that can be a reasonable substitute but performs the function safely? Is it time to reevaluate how you are currently packaging your foodservice products and change to more cost efficient or sustainable packaging?
Change. If your supplier can’t help you, start sourcing alternatives. There may be other distributors that can provide you with some, or all, of the items you need. There may also be vendors that will provide you with only what you are missing—such as a specialty cup supplier.
Shop. The wholesale clubs can be a good source of products. I don’t usually recommend this alternative as it takes your time away from the store, causes your product selection to be inconsistent because you can only buy what the big stores have in stock, and may also have an impact on your cash flow. But desperate times can call for desperate measures.
Share. Be creative and ask your customers to help you out. I was recently in a store where they were running short of coffee cups and the operator was offering customers a 50-cent discount if they brought in their own cup. In this case, the customer and retailer were sharing the burden to meet the customer’s need.
Reset. If you know you are going to be out of stock of an item for a while and you don’t have a suitable replacement, do a reset of your shelves to cover the gaps. You can expand to three or four facings of a product to take up more shelf space. This makes your shelves look fuller and gives the image of you being in stock. Also, make sure all your shelves are fronted—everything is pulled up to the front of the shelf edge.
Communicate, again. If you notice that customers cannot find what they are looking for, be sure to tell them that the product has been ordered, your supplier is out of stock, when you are expecting to receive the next delivery and that you are sorry for the inconvenience. You can also put pictures of the missing items on the shelf with a message that you are currently out of stock. This will let customers know that you are still carrying their favorite items, and they are temporarily unavailable.
Your customers will be understanding, and once you have explained the situation to them, will be sympathetic. But you won’t escape the look of disappointment in their eyes—like that of a six-year-old girl.
Roy Strasburger is CEO of StrasGlobal. For 35+ years StrasGlobal has been the choice of global oil brands, distressed assets managers, real estate lenders and private investors seeking a complete, turnkey retail management solution.