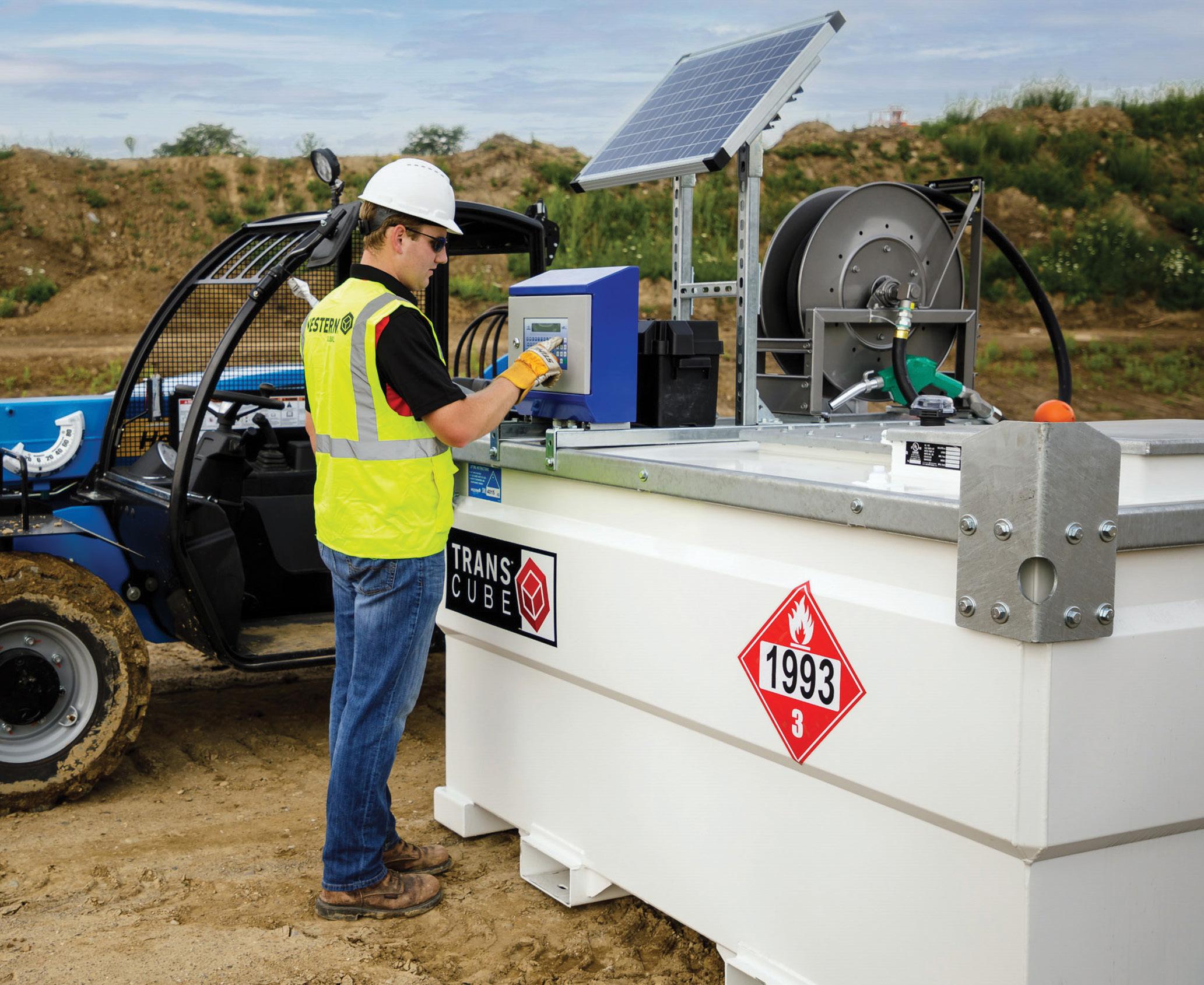
3 minute read
Technology Solutions for Fuel Efficiency
How companies can tackle jobsite fuel storage issues to prevent losses and mitigate costs.
BY JEFF LOWE
When it comes to running a business, everything points to profitability. Staff management, equipment efficiency and even something as simple as fueling can have a huge impact on the bottom line. In the scope of any project or job, the cost of fuel often accounts for one of the most significant expenses. When considering additional factors affected by fuel availability and quality, the stakes are even higher.
From the cost of lost fuel to theft, to engine issues associated with contaminants in the fuel, to lost productivity due to lack of fuel; the storage, transportation and distribution of jobsite fuel has the potential to significantly affect the bottom line. However, changing technology in fuel storage is helping companies tackle those issues and mitigate costs.
REMOTE TANK MONITORS
The most fundamental concern with fuel tanks is making sure there are always adequate fuel levels to power the productivity of the jobsite. Without fuel, both time and money are lost. New technology in fuel storage tanks includes remote tank monitoring systems, which allow operators to track inventory levels and location at any time, helping users take control of fuel supplies and avoid downtime associated with a depleted fuel supply.
The data is transmitted to a browser or phone app, where users can generate specific reports to enable efficient, accurate and timely refill orders. The
systems also help flag abnormal level changes due to theft or leaks and reduce the risk of overfill. Knowing exactly how much fuel is on hand (and the remaining capacity) also helps operators to capitalize on low prices when they appear. Personalized alerts sent as emails or texts are available for situations like above-average consumption rates, overfill incidents and more.
On a large jobsite, tank monitors use GPS to help operators precisely locate their fuel tanks. Fuel delivery trucks quickly and easily locate the truck or trailer carrying the tank, saving them the time of driving around looking for the tanks to fill.
CARD-LOCKED DISPENSE CONTROLS
Loss of fuel, or fuel that goes unaccounted for, is a sometimes-overlooked expense. Losing upward of $500 a month on misplaced fuel and chalking it up to “the cost of the job” happens more than one might expect. In fact, fuel theft is nearly a $133 billion issue that includes stolen, adulterated and defrauded product. But here’s the good news: Fuel loss can be prevented, and the bottom line can be protected.
Card-locking control technology combats the potential of fuel theft by only allowing authorized individuals to access fuel. With card-locking technology offered by some manufacturers, drivers use a phone-based app to enter their driver number, vehicle number and what type of fuel they need. Only after they’ve answered the required information does the fuel pump dispenser turn on and distribute fuel. This not only prevents loss but also helps determine which operator and equipment is using the bulk of the fuel. This valuable information can help determine overall efficiency or even cost/price structures. In the rare event of technical difficulties, administrators simply bypass the app with a key to allow for fueling, ensuring minimal downtime.
FUEL FILTRATION UPGRADES
While fuel availability and loss prevention are no-brainers in terms of impacting the bottom line, fuel filtration and quality are often overlooked. Some may find it surprising that most diesel is delivered with a fairly “dirty” ISO rating. This has led more and more users to realize the benefits of dispense filtration. A system using contaminated fuel can damage the engine, resulting in unwanted downtime and repairs.
Engineers design new engines to meet changing environmental standards, and fuel tank manufacturers are designing filtration systems to keep up with those standards. Clean, contaminant-free fuel means higher usage time and fewer issues when it comes to dispensing.
When fuel can account for up to 50% of a job’s total operating costs, it’s important to do everything possible to protect fuel assets. Pinpointing issues—and utilizing the latest technology—is an effective way to support the bottom line. Clean, readily available fuel means project movement, and project movement means profit.
Jeff Lowe is the director of product management for Western Global, an international designer and manufacturer of tanks and equipment for fuel and fluid handling. Building on a legacy that spans five decades, Western Global offers a wide range of solutions for the safe transportation and storage of fuel, diesel exhaust fluid, lubricants and more.