
4 minute read
Let’s Talk Safety: Job Hazard Analysis Identify and Reduce Hazards
This column addresses safety issues of interest to water and wastewater personnel, and will appear monthly in the magazine. The Journal is also interested in receiving any articles on the subject of safety that it can share with readers in the “Spotlight on Safety” column.
Job Hazard Analysis: Identify and Reduce Hazards
Advertisement
Ajob hazard analysis (JHA) is a safety evaluation process. Many companies, both large and small, have successfully used a JHA to identify potential dangers of specific tasks in order to reduce the risk of injury to workers. It takes a little time to do a proper JHA, but it’s time well spent. Be sure to involve employees in the process—they perform the work and often can easily identify the risks and know the best ways to work more safely.
How to Conduct a Job Hazard Analysis
Here are some things to consider when doing an analysis: S Start by talking to your employees. Tell them what you are doing and why. Explain that you are studying the safety of the work tasks they perform and not their work performance. S Review your company’s accident/injury/ illness/near-miss history to determine which jobs pose the highest risk. S Identify the Occupational Safety and Health
Administration (OSHA) standards that apply to your jobs, and incorporate the
OSHA requirements into the JHA. S Evaluate jobs where you have identified violations of OSHA standards and/or violations of company safety procedures.
List the jobs having the greatest potential to cause serious injuries or illness, even if there is no history of such problems. S Make a note of the jobs in which a simple mistake could lead to severe injury. S Evaluate jobs that are new or have been changed and those jobs that are so complex they require written instructions. Watch each worker perform his or her job in a routine manner. List each step of each task in the order in which it takes place. Begin each step with a verb; for example: “Turn on the saw.” Do not make the steps too broad or too detailed
While you are making a record of the job, you may want to photograph or videotape each step for further analysis. Review the steps with all the workers who do the same job to make sure nothing is been left out.
Identify the hazards of each step and ask: S What can go wrong? S What are the consequences if something does go wrong? S How could an accident happen? S Are there other contributing factors?
The weather, seasonal workload, or new construction are examples. S How likely is it that an accident will occur?
Review the List of Hazards With Employees
Your employees can provide a tremendous amount of information. Take the time to talk to them—and be sure to listen. Asking for their honest input will engage them in the process and lead to a higher level of safety awareness and compliance. You will likely hear several practical ways they believe the job hazards and job processes affecting them can be eliminated or at least reduced.
Eliminate or Reduce the Safety Hazards
You’ve evaluated the findings in your analysis and concluded there’s a safer way to do the job. Now your work begins. In your JHA you’ll need to: S Make any changes to the equipment, tools, or engineering controls to eliminate a
Let’s Talk Safety is available from AWWA; visit www.awwa.org or call 800.926.7337. Get 40 percent off the list price or 10 percent off the member price by using promo code SAFETY20. The code is good for the Let’s Talk Safety book, dual disc set, and book + CD set.
hazard. Such changes might include adding machine guards, improving lighting, or having better ventilation. S Change the work processes. S Change the administrative controls or make changes in how the task is done if engineering controls aren’t possible.
Perhaps you could rotate jobs, change the steps in the process, or provide additional training. S When engineering and administrative controls aren’t possible or don’t adequately protect the workers, make additions and changes in the required personal protective equipment as needed.
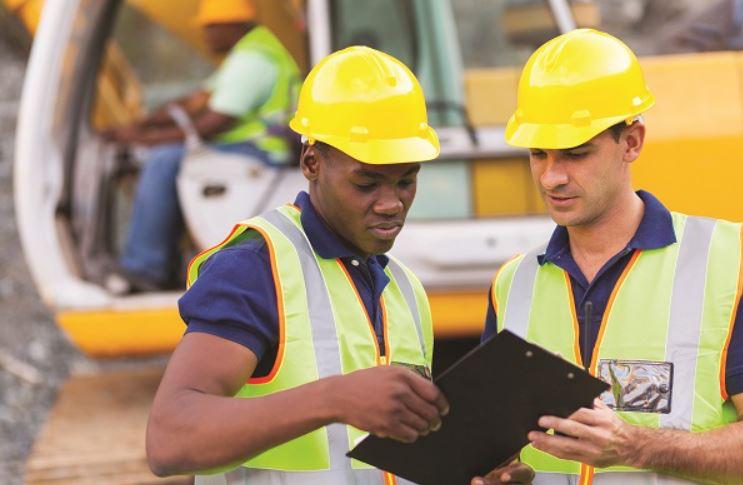

Implement Your Changes
To complete the JHA, you’ll need to correct all unsafe conditions and processes. The resulting changes may require additional training for your employees. Make sure they understand the changes and the reasons behind those changes. Periodically review the JHA; you may find hazards you missed before. Update and review the document when the task or process changes or when injuries or a close call occur when performing the recommended task.
You’ll find your JHA to be a valuable tool. Not only will it help to reduce worker injuries, but it’s a document you can use for training purposes. It can also serve as a reference tool in the event of an accident investigation.
Resources
For additional information read the OSHA booklet on job hazard analysis: www.osha.gov/ Publications/osha3071.pdf, or see American Water Works Association (AWWA) Manual M3, Safety Management for Utilities. S
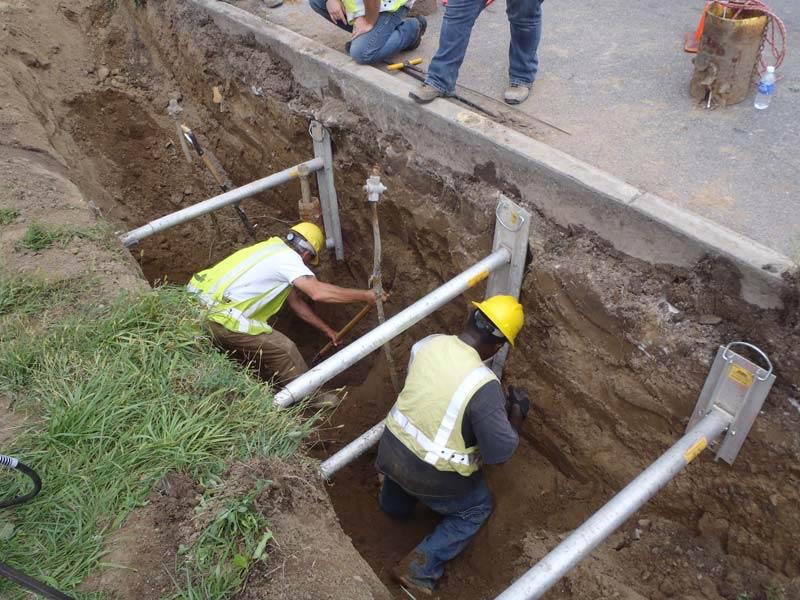
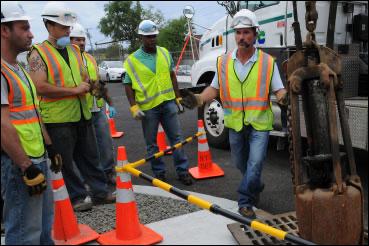