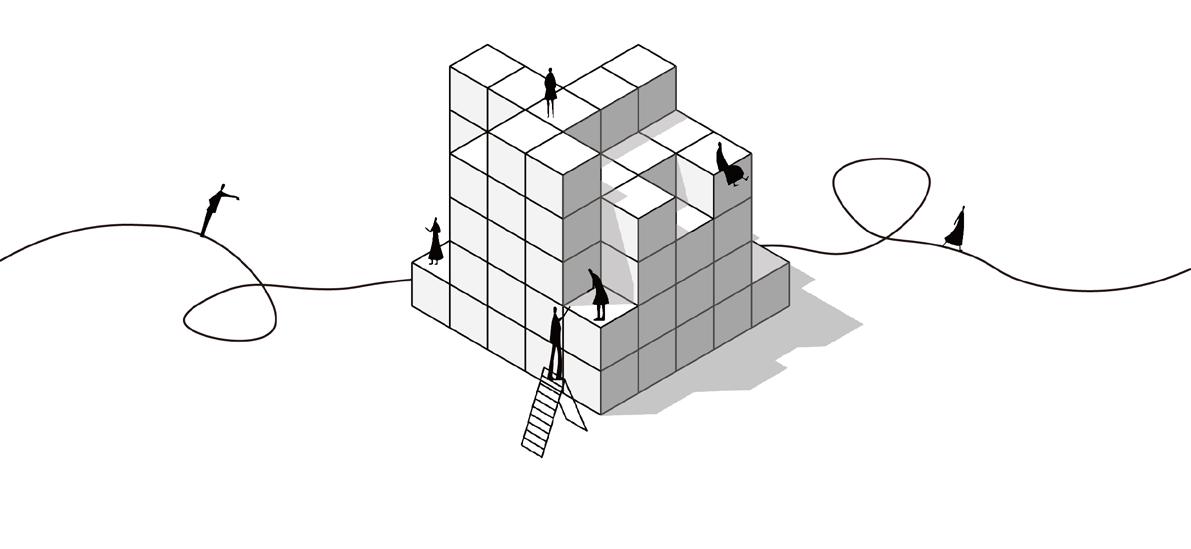
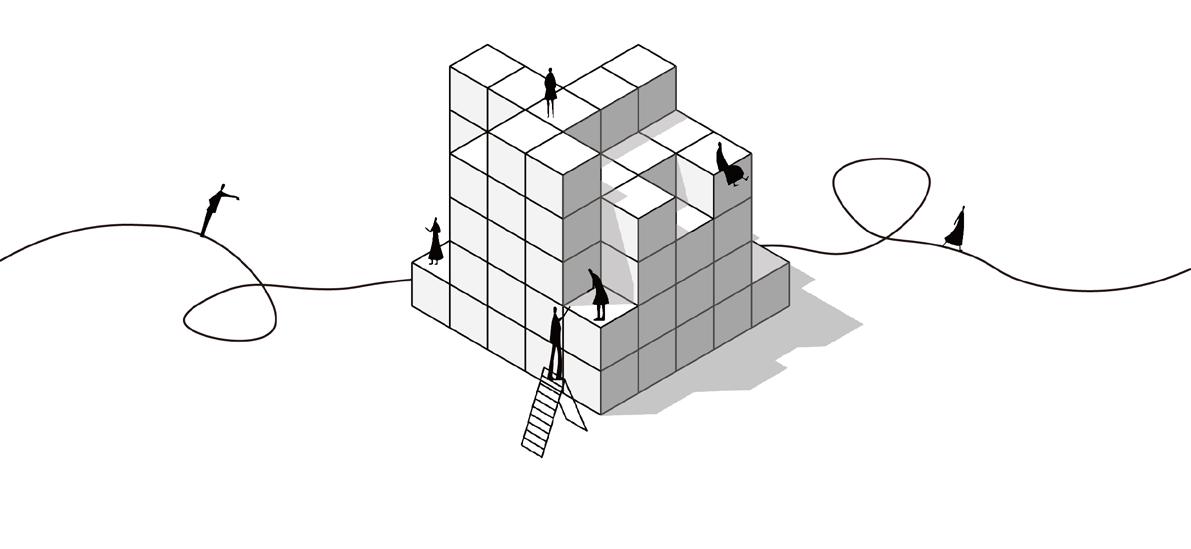
YUSHI GAN
ARCITECTURAL PORTFOLIO
Selected works from B.ARCH in Southeast University 2020-2025
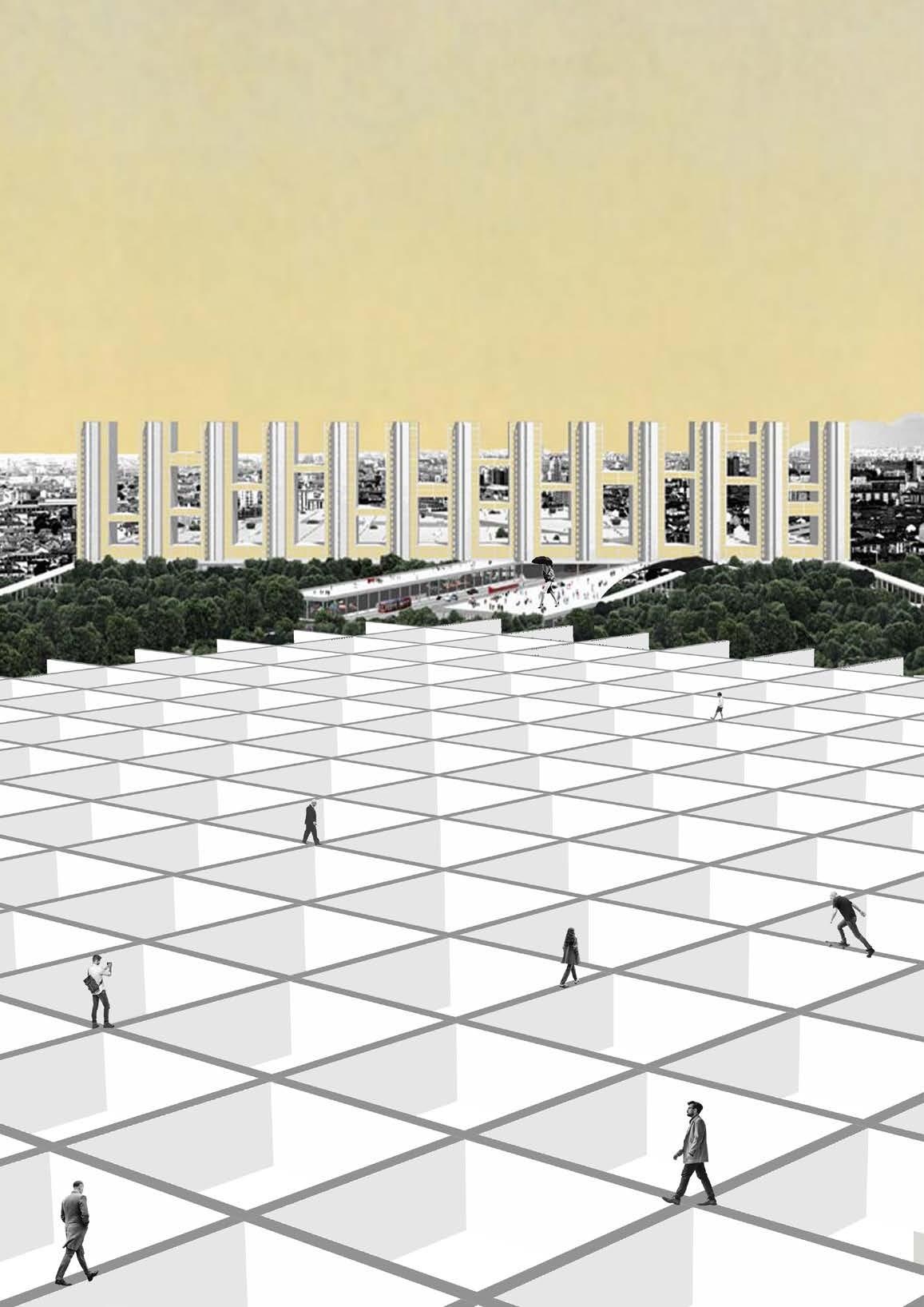
“The grid is, above all, a conceptual speculation…in its indifference to topography, to what exists, it claims the superiority of mental construction over reality”
——Rem Koolhaas
In the ever-evolving field of architecture, the pursuit of order and meaning within space remains a timeless quest. The grid is a tool for both order and chaos which provides a framework within which we can understand space, but it also allows for the unexpected. The 4 projects in my portfolio where completed during different periods of my undergraduate study which show my gradual understanding and mastery of architecture being a tool for both order and chaos. These projects strive to demonstrate how the grid can orchestrate spatial narratives, transforming abstract concepts into tangible realities. The interplay between rigid structures and fluid forms echoes my belief in the grid’s capacity to accommodate both predictability and surprise.
Content
01 Sewing up
Nature and City
Music Hall in North Ancient Yu Garden
02 Co-living, Co-working
Courtyard Design for 4 Youngsters
03 Pilgrimage Trio
Adaptive Reuse and Restoration of St. Peter’s Church in Tuscania
04 Woven Butterfly A Bamboo Pavilion of Physical Construction 05 Voronoi Collision
Digital Manufacturing based on Concrete 3D printing
Other Works
Internship Project at TM Studio
Art and Media Practice
Surveying & Mapping

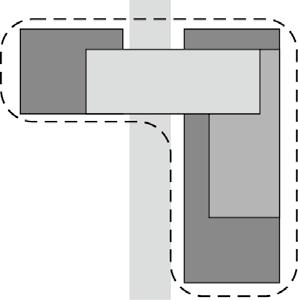
Sewing up Nature & City
Arts Centre in North Ancient Yu Garden
Y3 Semester2 Studio Project | Individual Work
Revised in 2024 Summer
Site: City Downtown, Nanjing, China
Site Area: 9416m² Project area: 7500m²
Instructor: Liu Jie
This project is located in the old central town in Nanjing which boasts rich historical and cultural features. In recent years public resources such as Xiaoshu Museum and private art galleries have been developed around the site. Yet there hasn’t been a formal acting space where intangible cultural heritage can be carried out.
The intricate context generated the central questions underpinning the design: How to break the detachments between the natural Chinese garden and chaotic city? How to extend the beautiful garden landscape while inviting the city toursists in? How to clarify the building organization while adapting to the small-scale Chinese Garden?
Rather than creating an iconic imposition, a music hall with comprehensive use is composed, sewing up nature and city as an extension of all three simultaneously. The new building will serve as a place accomodating all kinds of performing activities from tourists and citizens, creating a vivd scene where old city history collides with modern activities.
Issue: Detachment between city and nature The site is now a parking lot which cause a waste for such location and lanscape. The WAGUAN Temple has been damaged since 1908. Rare people would come to this deserted area.
Garden, a traditional Chinese garden built in late Qing Dynasty


Site Context: Detachment between City and Garden
The base lies between the outer Qinhuai River and the inner Qinhuai River which boasts rich history heritage. In a smaller scale it overlooks a traditional Chinese Garden in the south with and a city express road spreads in the north. The music hall aims to break the detachments between the natural garden and chaotic city, extending the beautiful garden landscape while inviting the city toursists in.

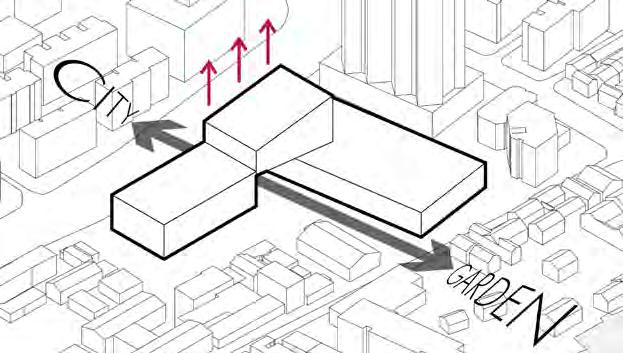
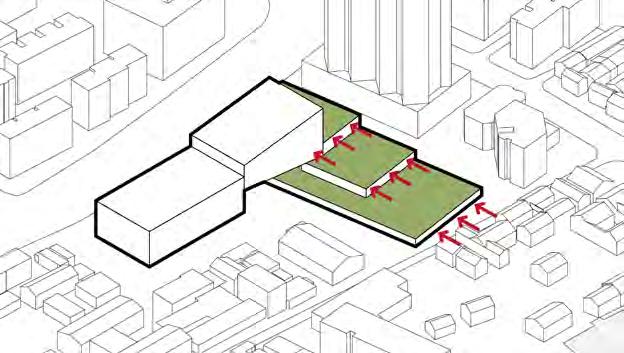
Extension

Circulation Connect 2 volumns with another volumn to complete the full circulation


Massing Strategies
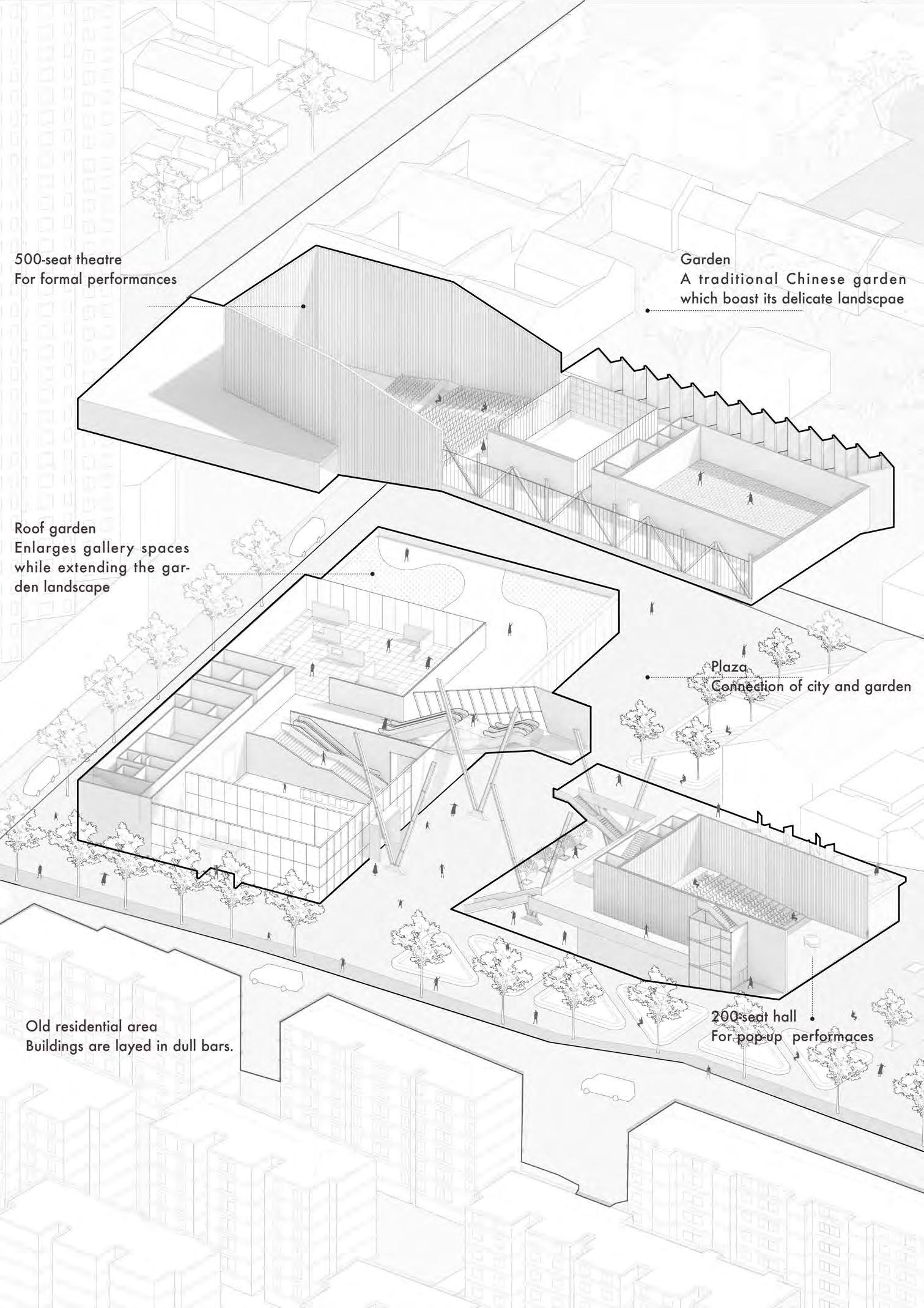
Axonometric View
The whole building has 4 huge steel “V” shape column to raise the lounge volumn up, thus creating a route to break the detachment from city to nature in a very welcoming and inviting gesture
Activity Research
Observation of potential activities in the surrounding area: The whole downtown area lacks exhibition places for Chinese traditional culture. Old and dull residential area lacks spaces for daily exercises. And events like outdoor concert have nowhere to carry out.

A Complex of Mixes Use


I consider the visitors of 3 type and make the function proposal according to their needs. With Hall and Gallery as the main function, the other spaces are planned carefully accordingly.
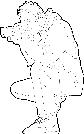

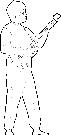
Underfolded Section Diagram
The 2 main functions are joint together by an upper level and created a path on the ground floor.
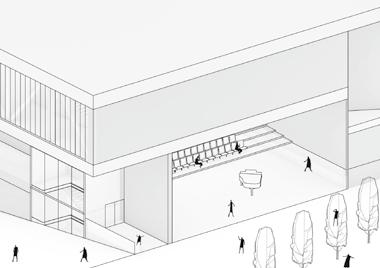
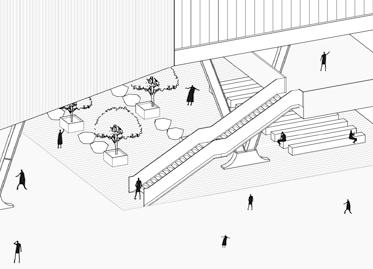
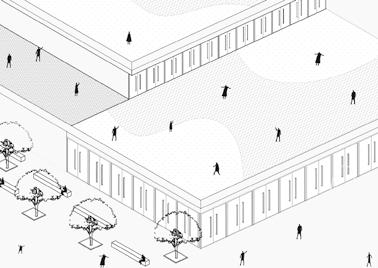
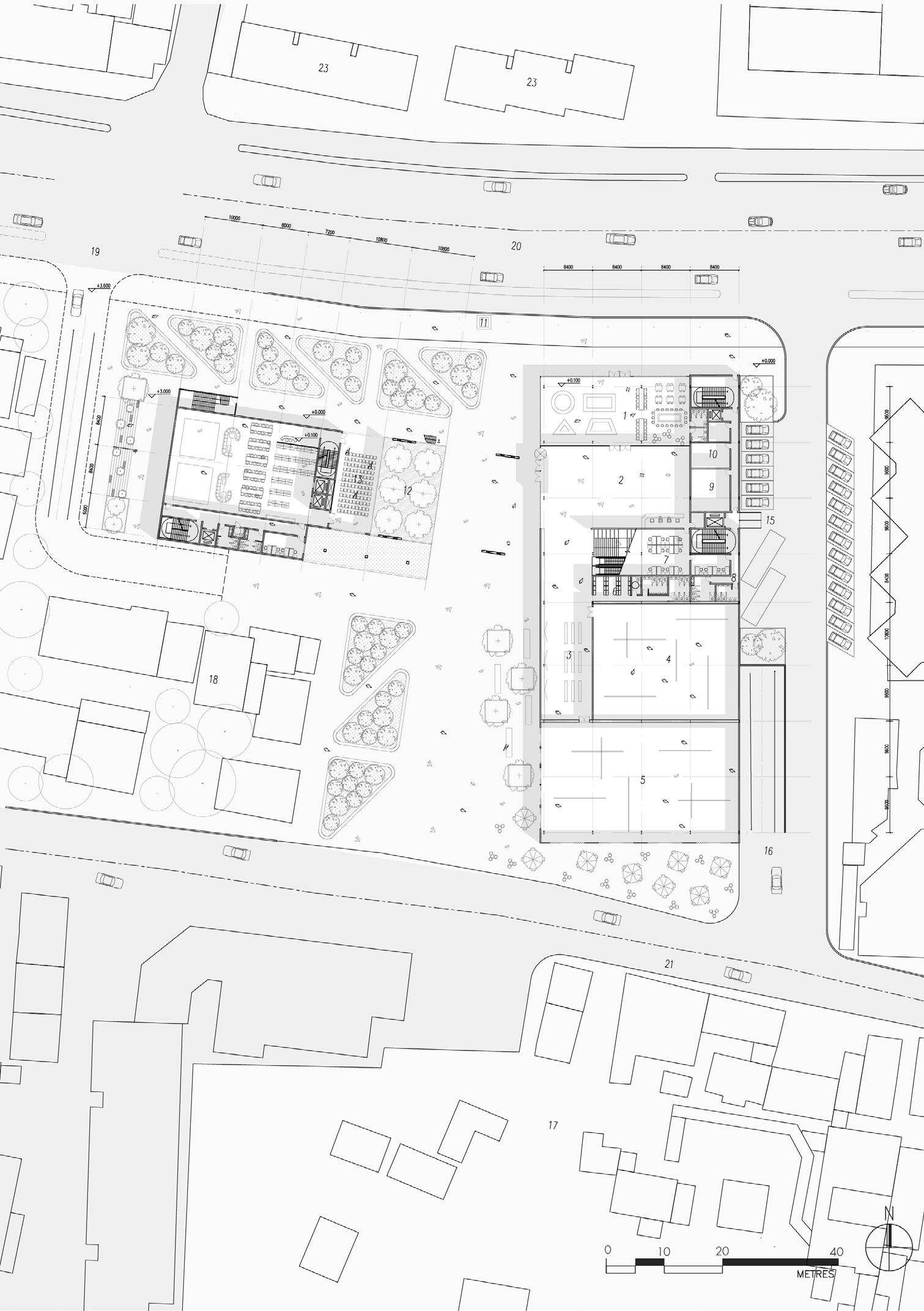



1 Preparation Room
2 Rehersal
3 Gallery
4 Atrium
5 Roof Garden
3rd Floor Plan
Juxtaposition of 2 theatres: The atrium connects 500-seat Grand Theatre and 200-seat Hall

Decreasing Volumns
The decreasing volumns lead to roof gardens as the extension of green space
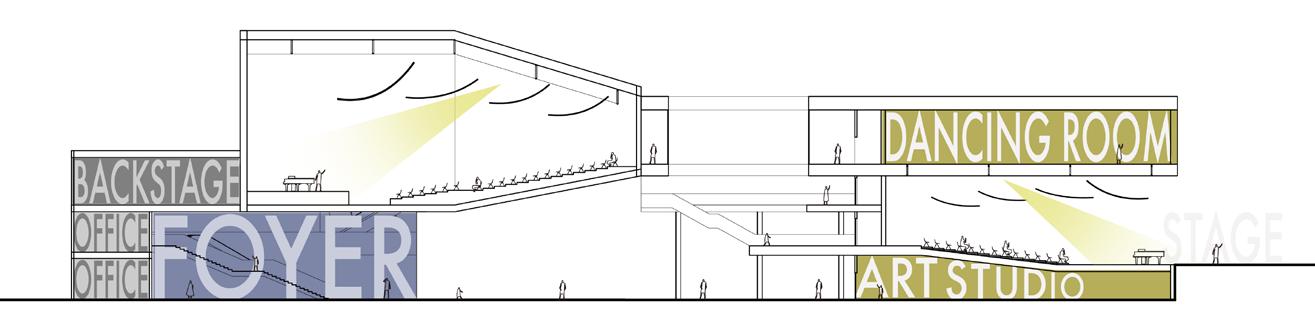
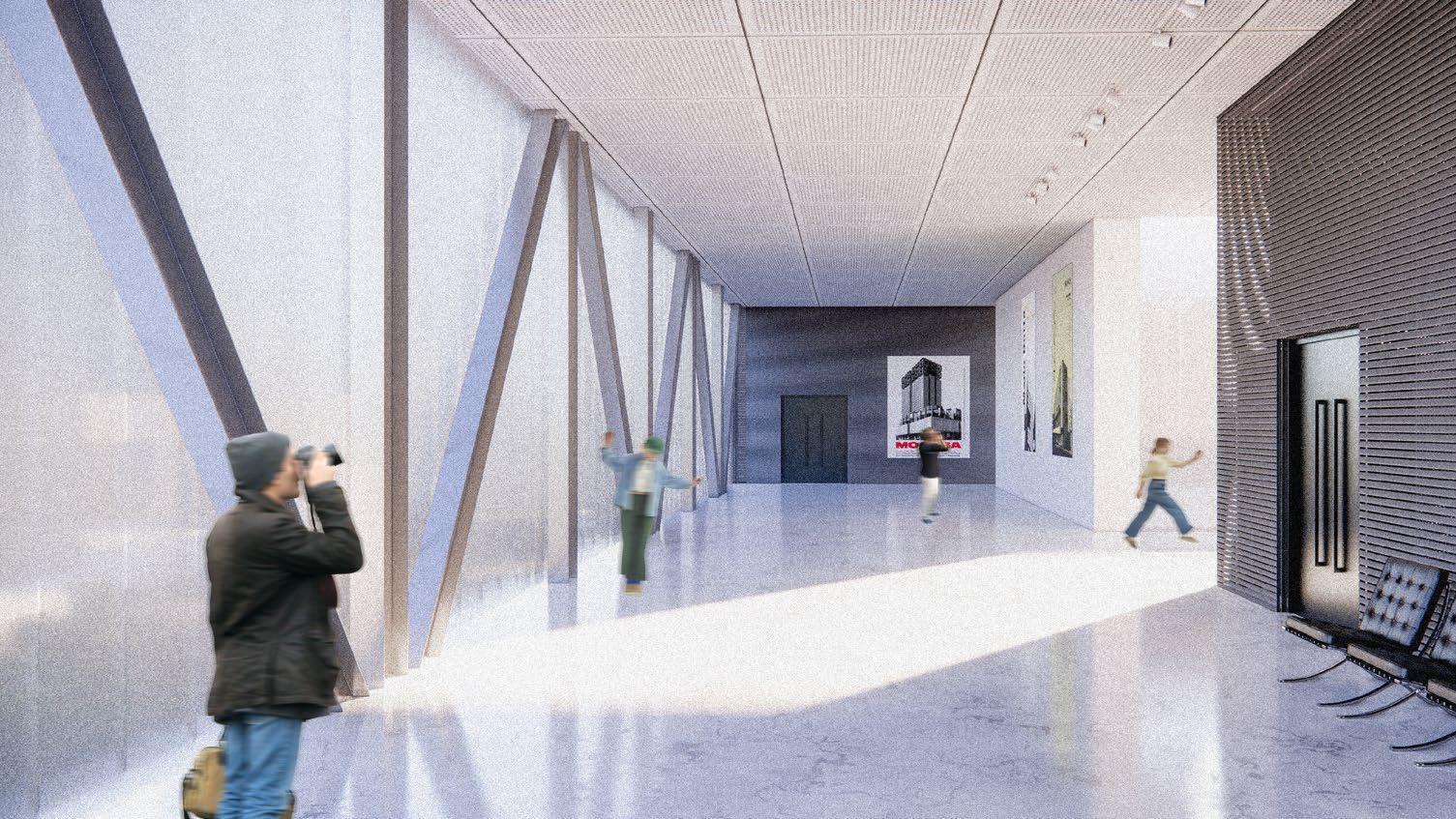
A very transparent and high space as the entry of the gallery volumn
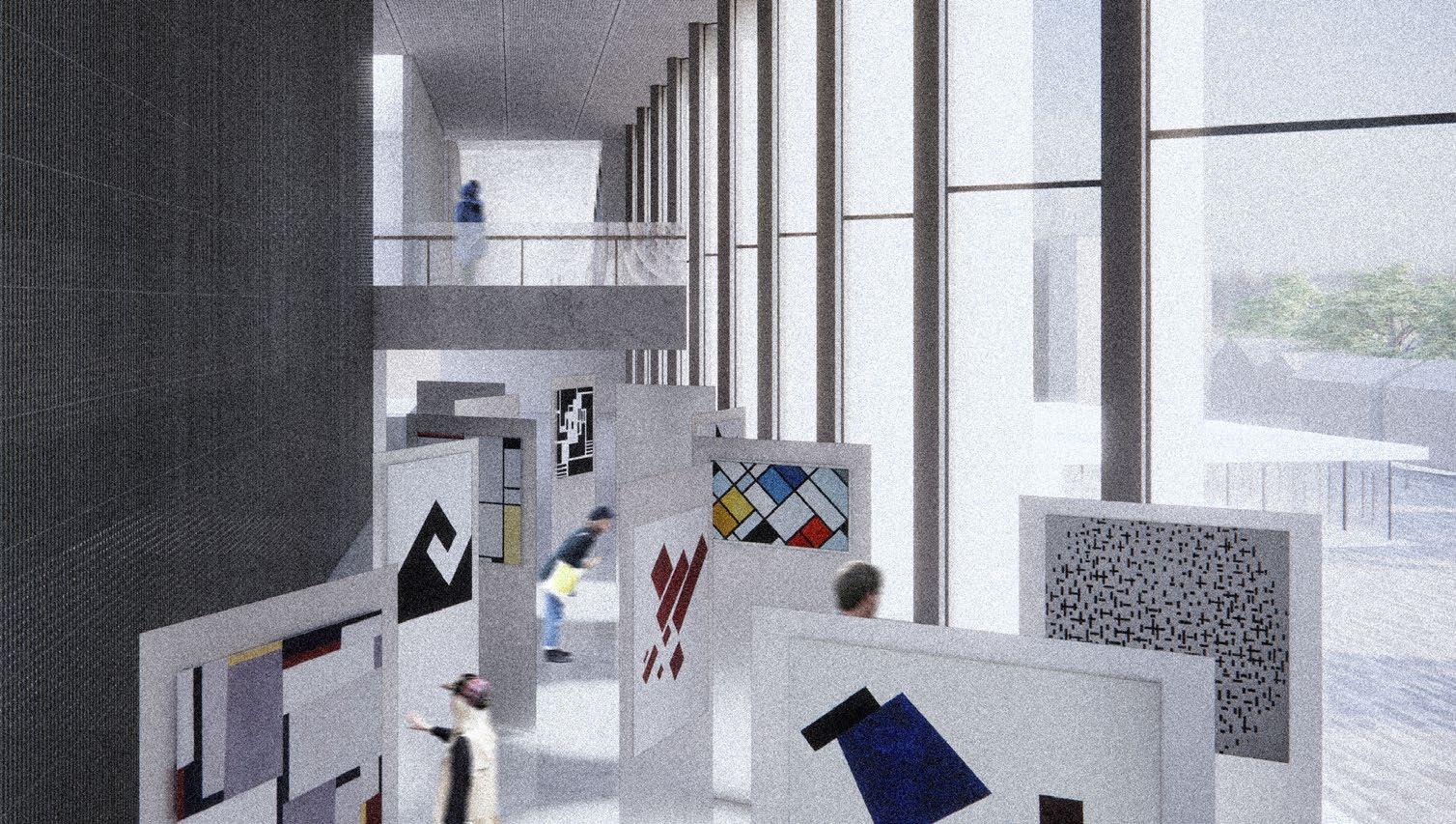
A narrow and high space which amplifies the garden landscape
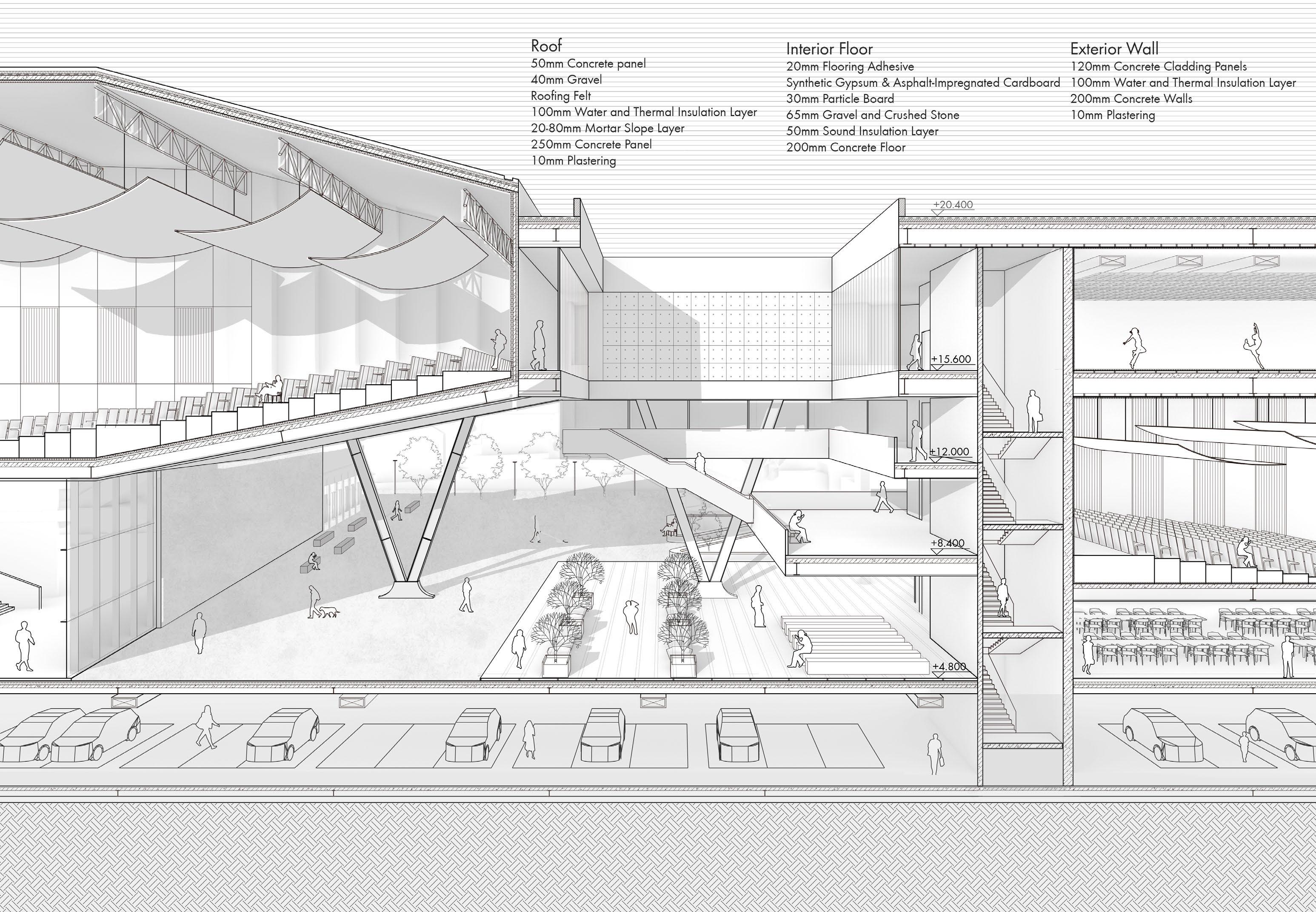
Section Detail
The atrium connect the platform which contains rich activities of residents. Spatial relationship between 2 halls and other relative rooms are clearly illustrated, as well as details of construction including material and structure.
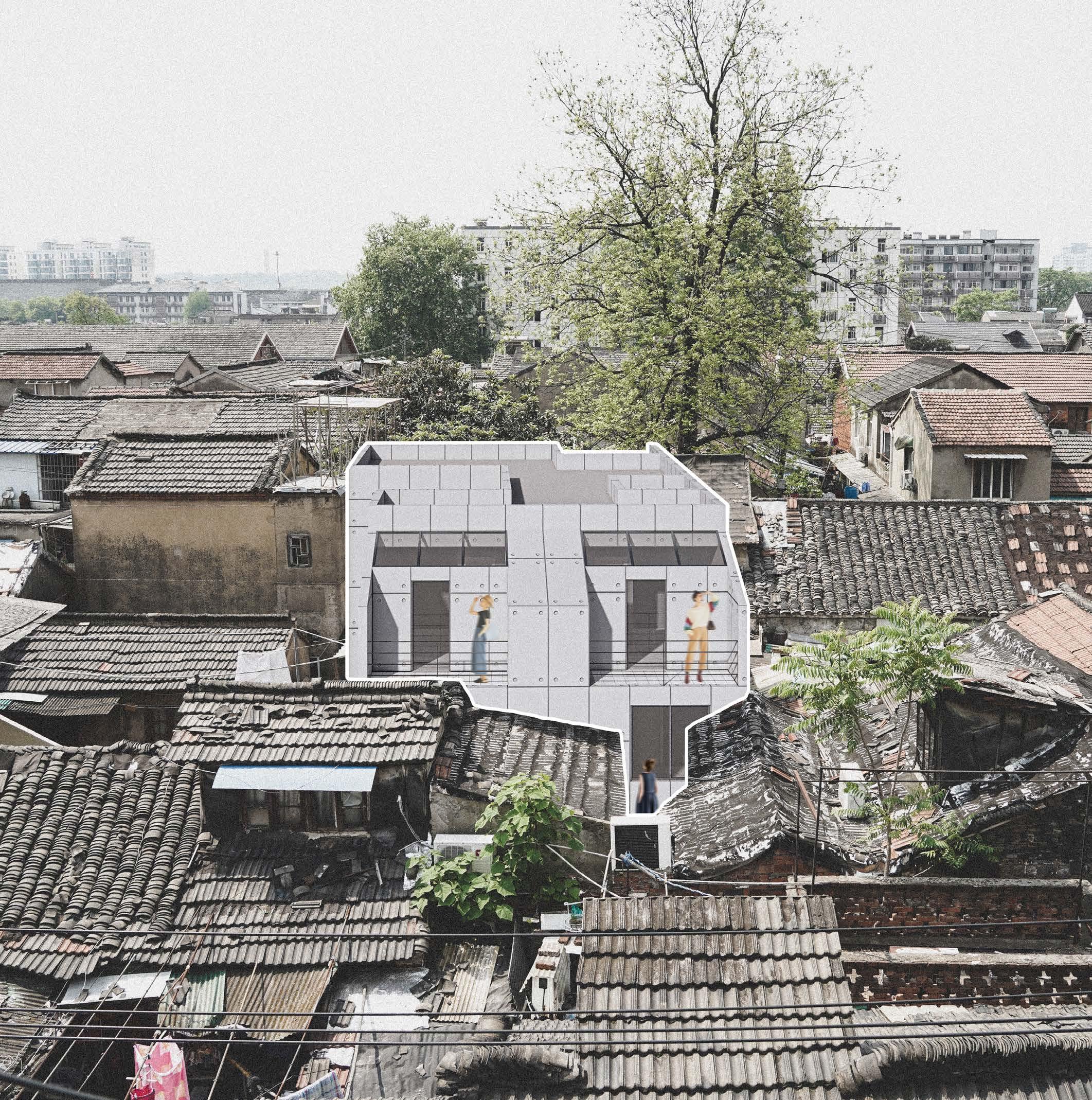
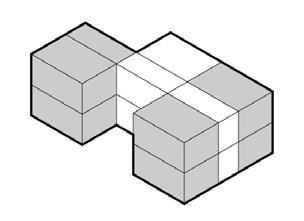
Co-living, Co-working Courtyard House for 4 Youngsters
Y2 Semester2 Studio Project | Individual Work Site: Hehuatang Historical Area, Nanjing, China
Study Area: 2000m² Building Area: 180m² Instructor: Chen Qiuguang
Residence is the foundation of urban life, the community is the gathering place of social relations, and the source of urban vitality. Courtyard house is both a typical living mode and spatial prototype. To some extent it reflects traditional Chinese philosophy towards human and nature. People can feel he repeating change of day and night, seasons and years from this inner-faced “window”.
The Hehuatang area is the only existing historical block of residential use in Nanjing. Once in history the area was lived by big families. Yet as time goes by, the bad living condition lead to a huge loss of residents Now the area are mainly lived by lower class residents, which forms the most basic component unit of the courtyard space of the city residence.
By observing and interviewing some residents on site, and with plenty of research of past historical activities, social issues and spatial typology of courtyard house and public spaces in this area, I conceived of “co-working” and “co-living” of 4 youngsters. I use the 9-grid sysmtem and duplicated walls to reform the traditional pattern of a courtyard house, yet in a modern construction material and living mode.
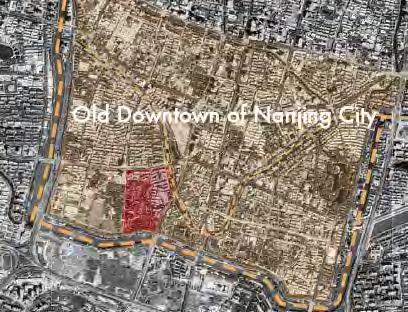
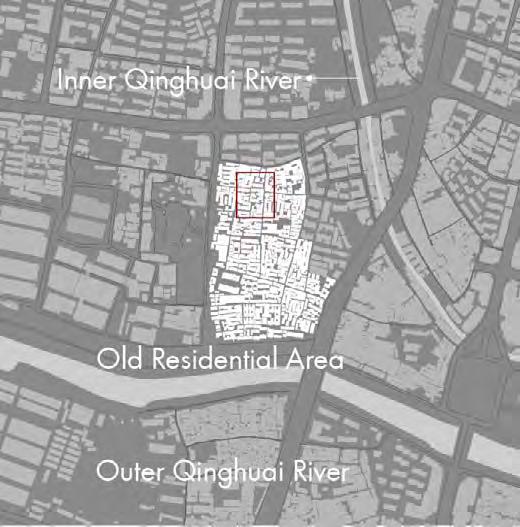
The Hehuatang area is the only existing historical block of residential use in Nanjing. With many low-rise dwellings, narrow streets and small residential plots, this kind of spatial sequence carries the memories of the courtyard life of the people from the old era.
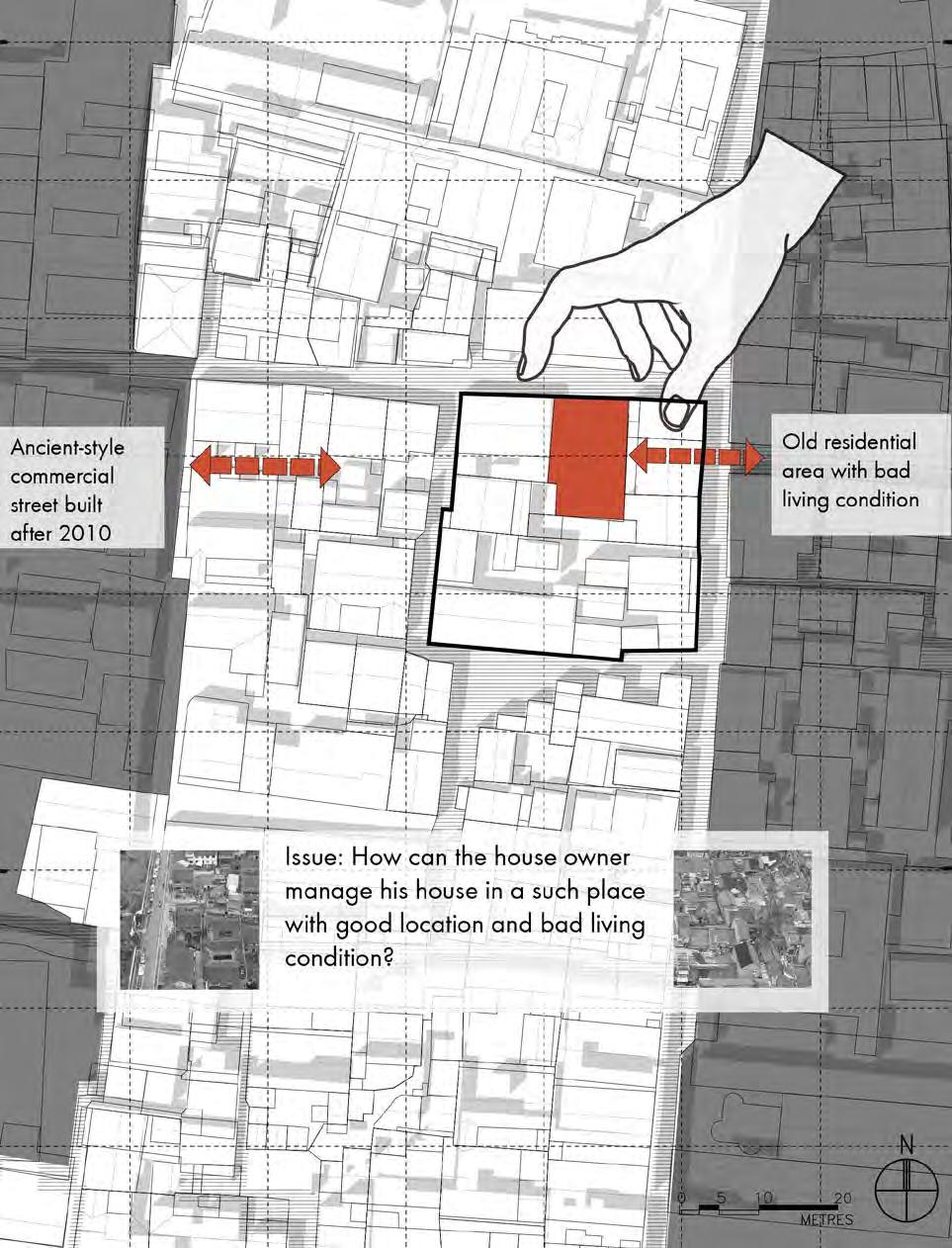
Site Context of Hehuatang
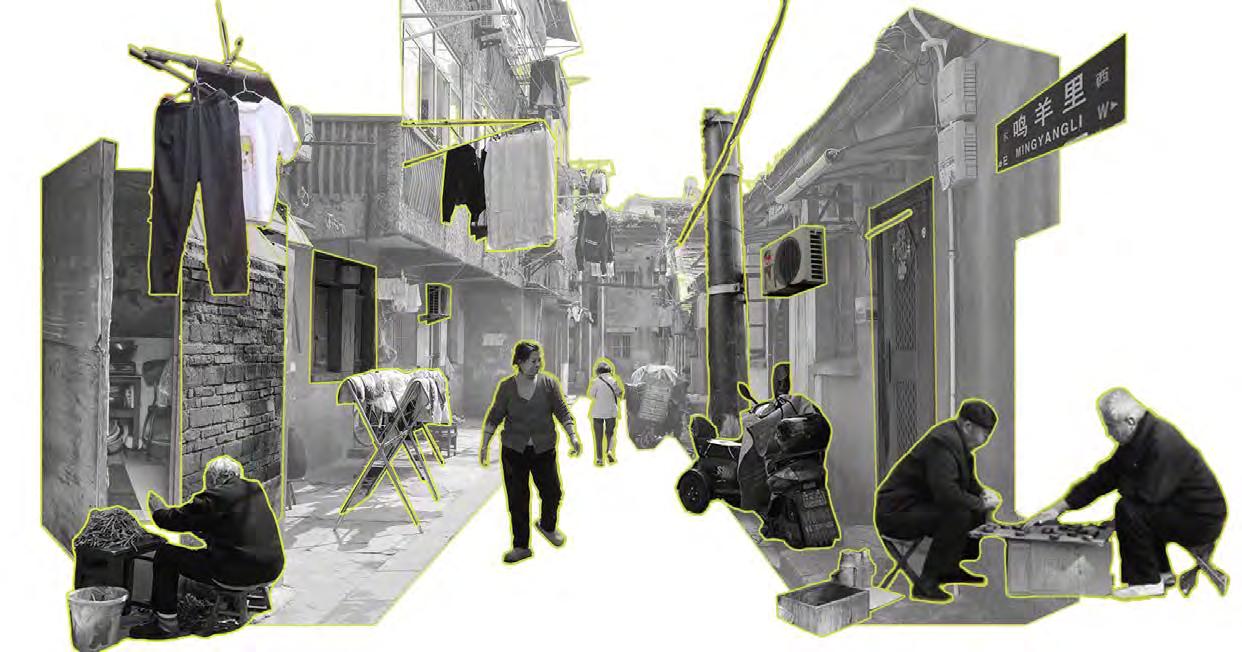
Spatial Prototype Analysis of Relationship of Yards and House
The study of courtyard house typology is a process of understanding living mode of this area. This spatial prototype under the accumulation of time has also undergone a special time translation. Throughout this process, the spatial prototype has also absorbed the influences of the inhabitants who have contributed to the mixing, repurposing, and reorganization of various types of spaces such as “rooms,” “corners,” “streets,” and “courtyards.” This ongoing transformation stems from the constantly changing needs of daily life, allowing us to view certain spatial “chaos” and “unexpectedness” from a more individual and multi-dimensional perspective, thereby revealing its particular prototype significance.
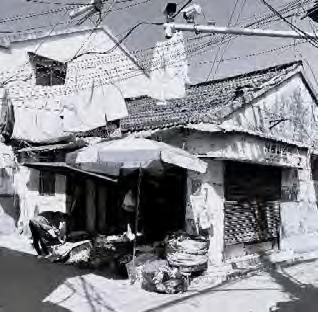
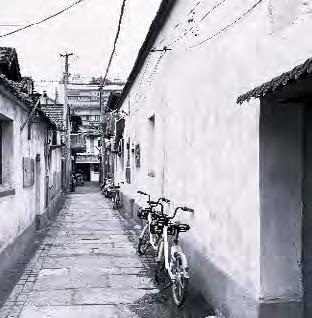
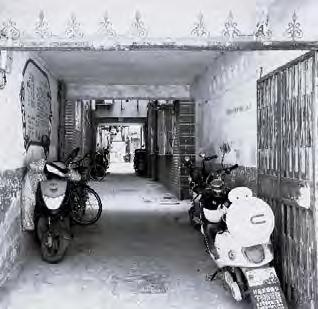
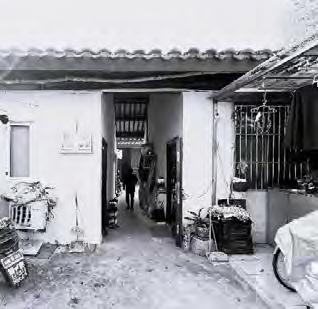
The Area is now Desolated as Residents Move Out due to Bad Living Condition
Observation of “Room” “Corner” “Couryard” and “Lane”
Social Issues brought by Land Price Rise
The traditional residential area now has aging problem due to loss of young residents. At the same time, with land price rising , young people tend to share accomodation for lower rents. The new mode of co-living and co-working can provide a better choice for youngsters.

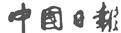
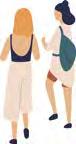
Leaving Big Cities of High Rent, Young people return to Hometown
A New Living Mode triggered by Research and Interview
The site I choose to rebuild is now lived by an old couple. With compressed living space and messy spatial order, I conceived of the couple renting his house to 4 college graduate who want to continue their career in Nanjing.
“Our children has moved out since 2010, we have more rooms and spaces and we’d love to rent them, and I want to do something new like open a studio after retirement”
House owner
Massing Process and Concpet

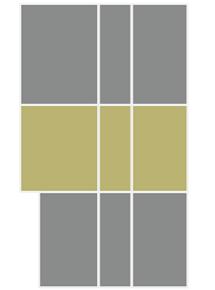
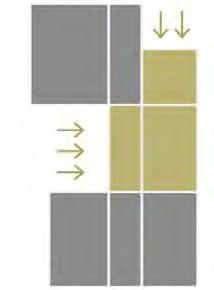


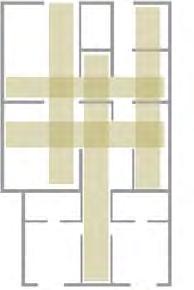
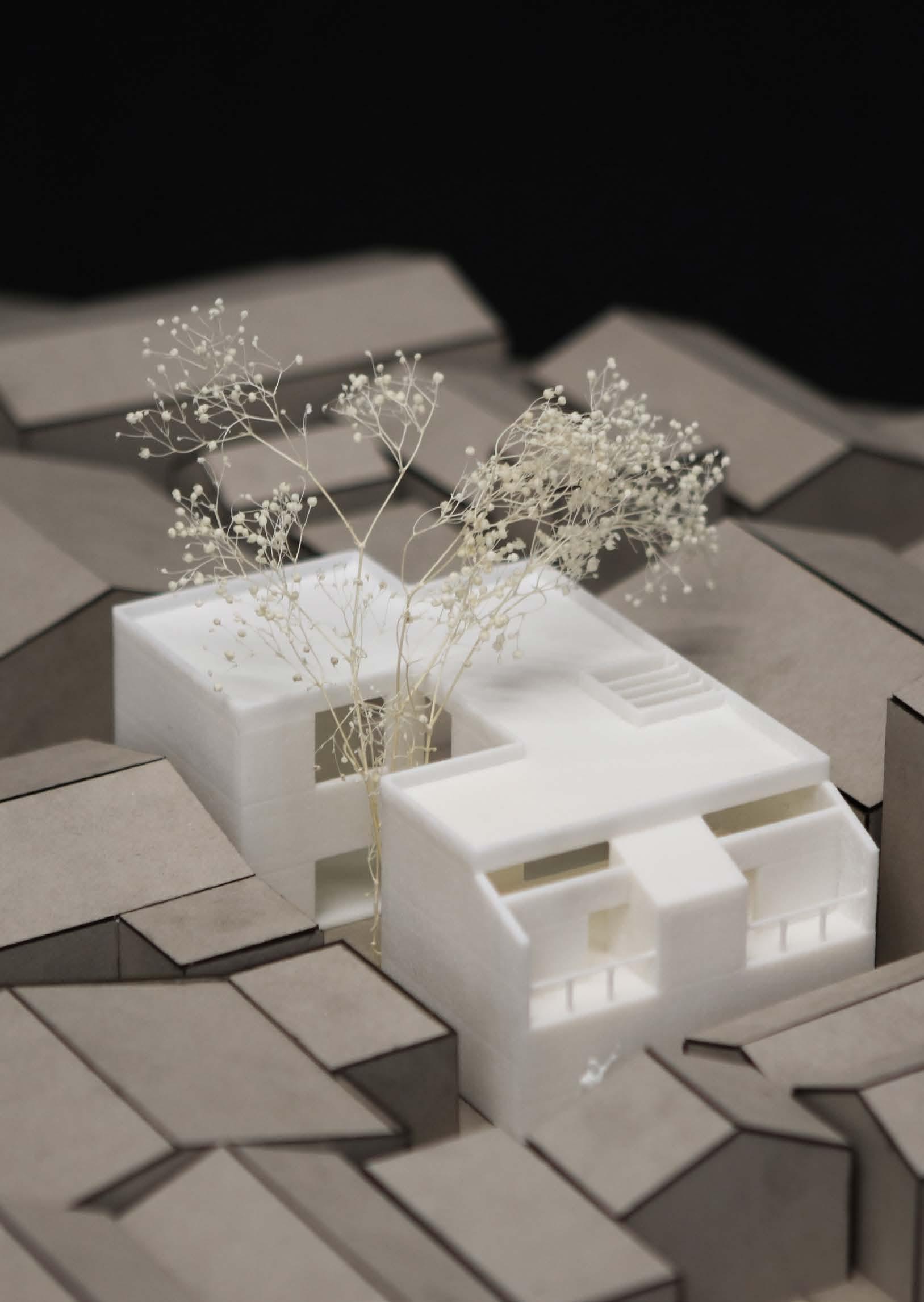
Located in the area with many Sloped-Roof, Low-rise dwellings built by bricks, the house constructed by concrete stands for the new living mode and bring
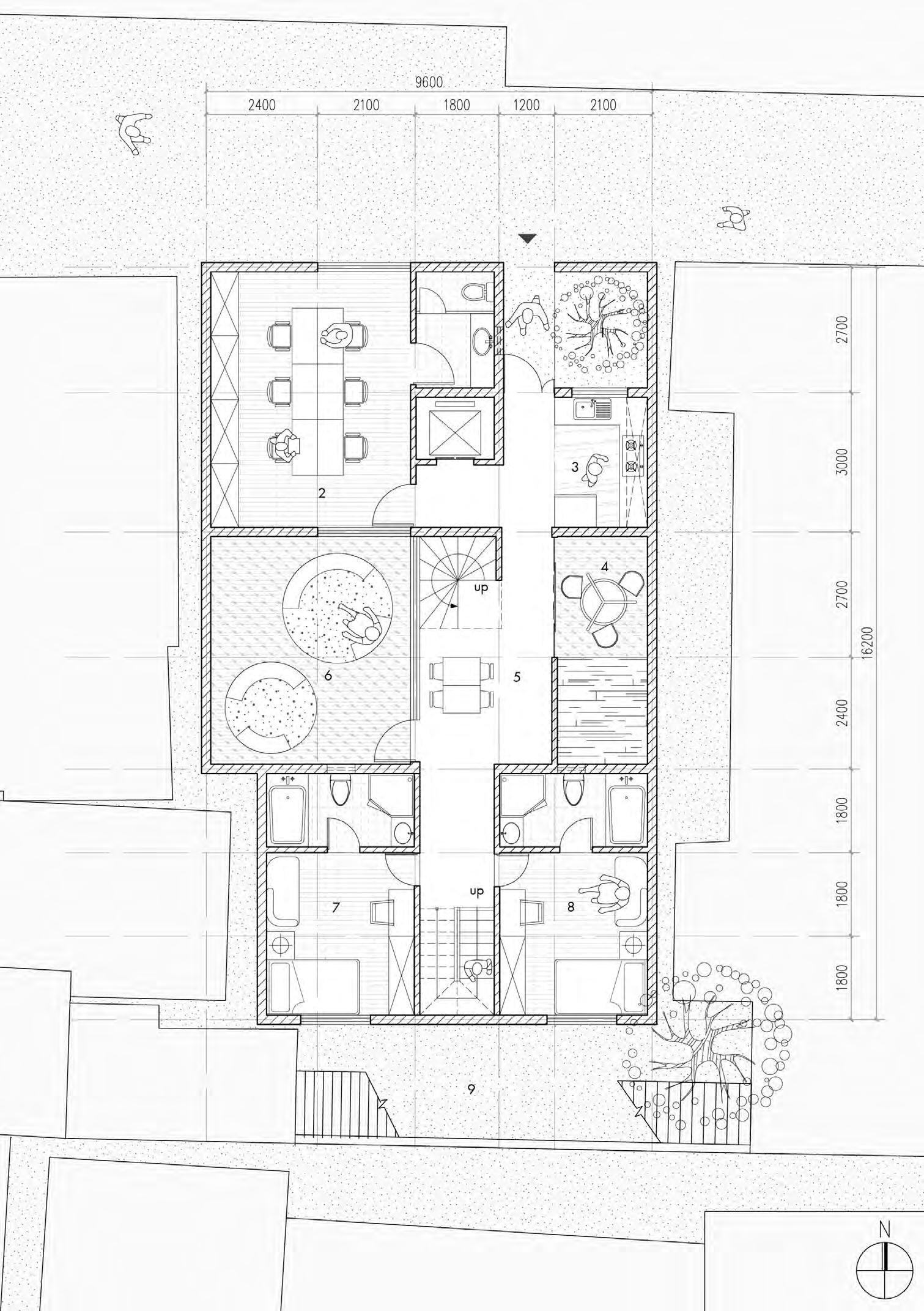
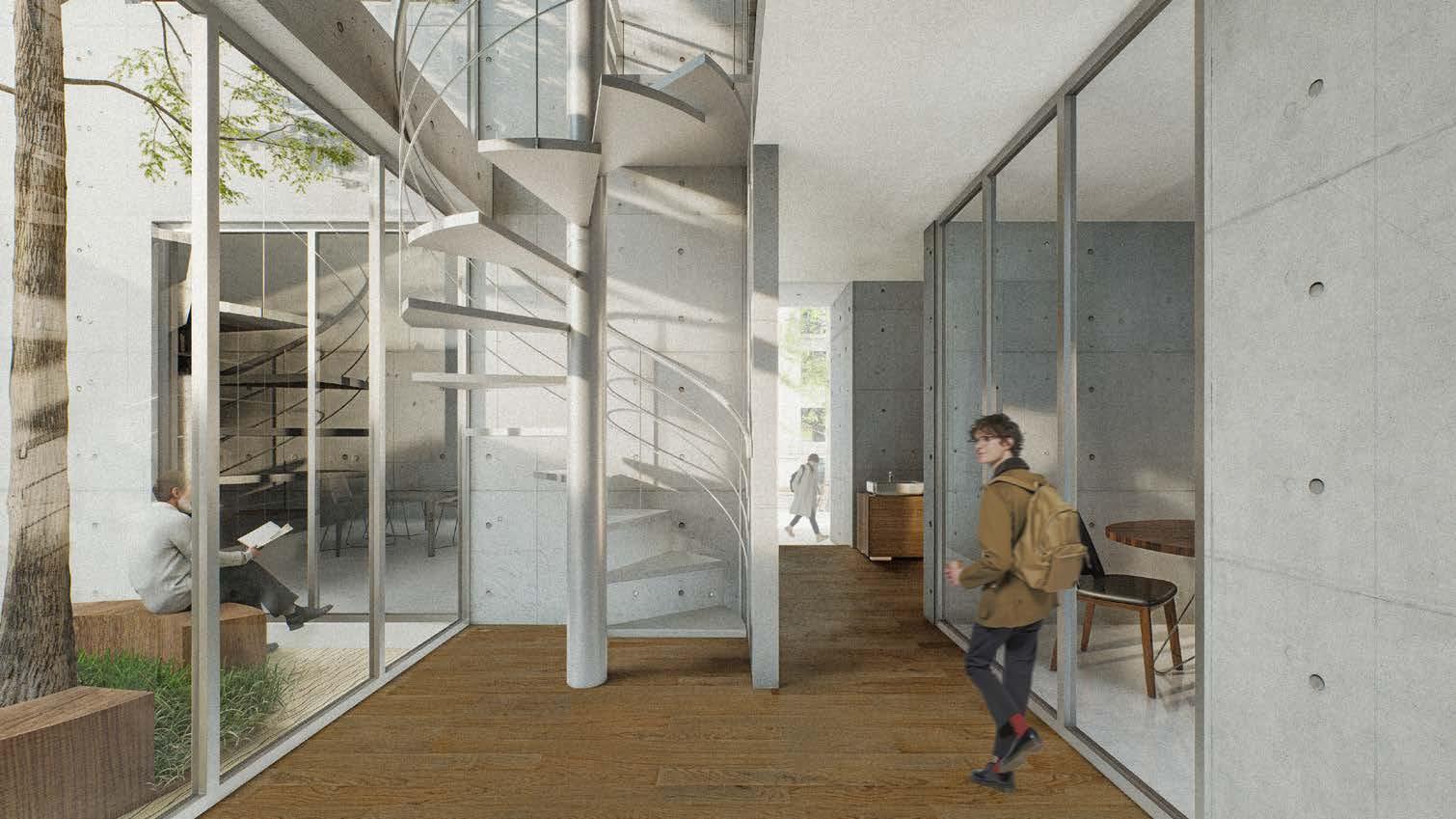
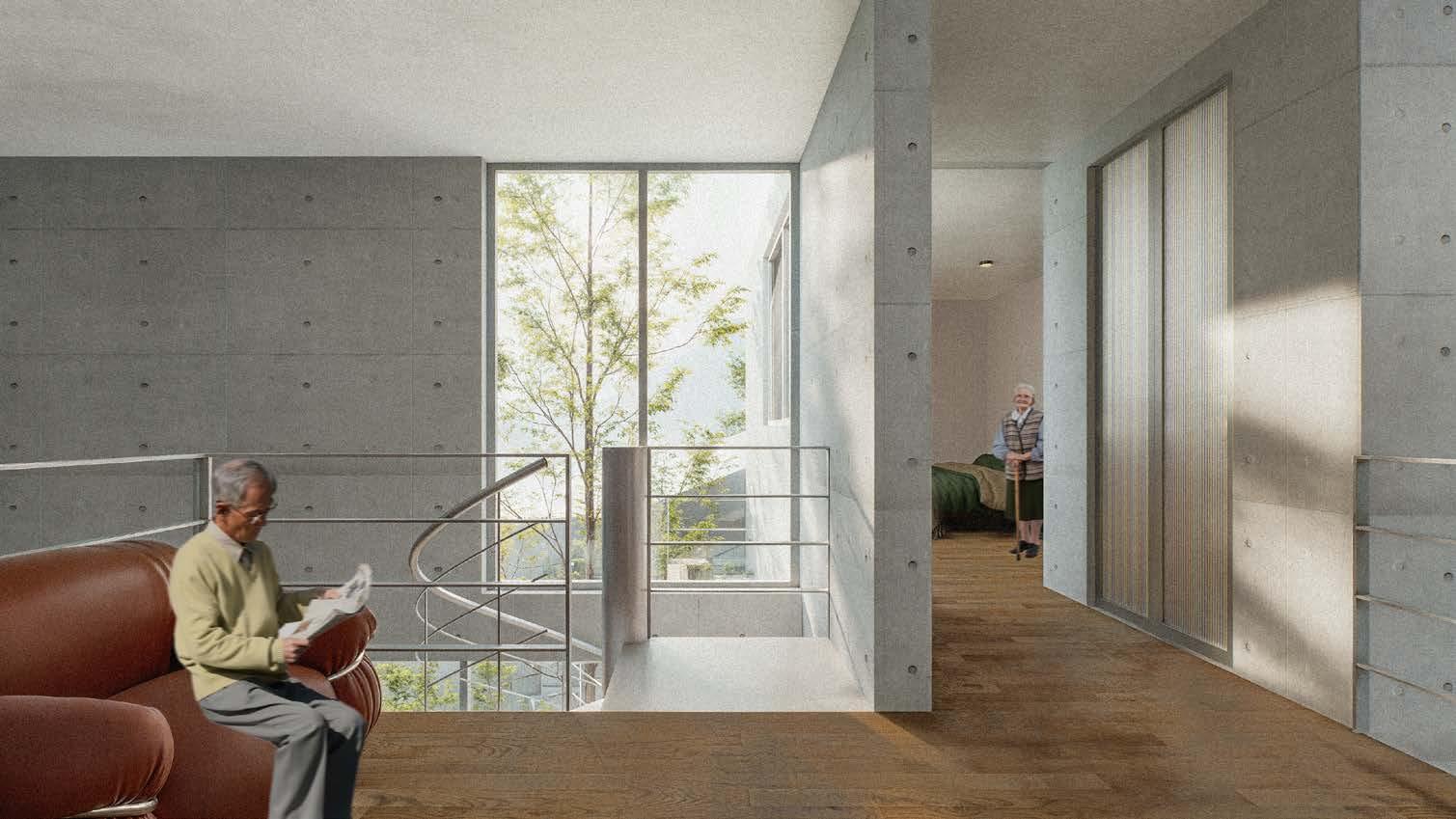
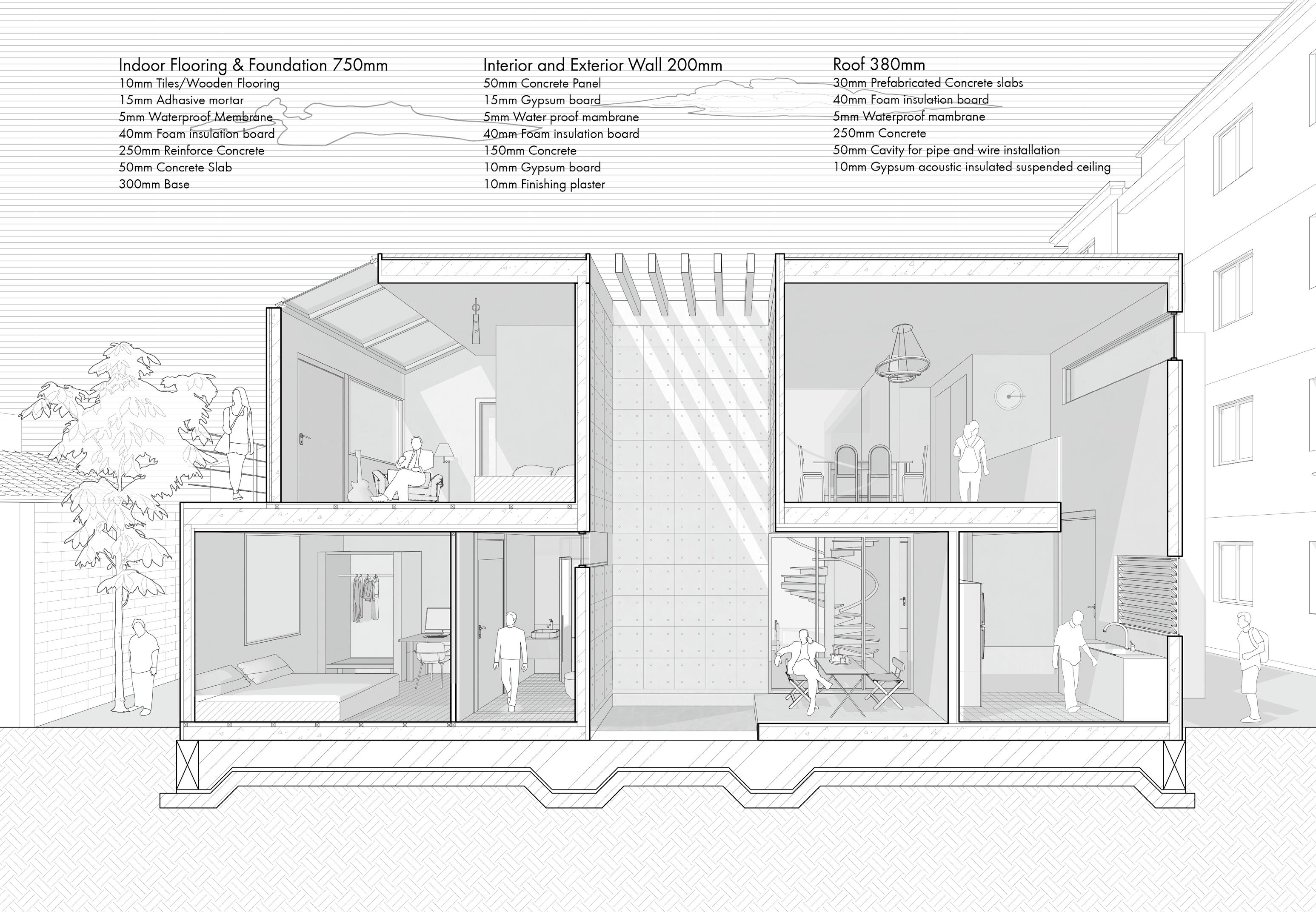
Section Detail
The Courtyard House is built by concrete with panel outwalls, residents enjoyed themselves in seperate parts
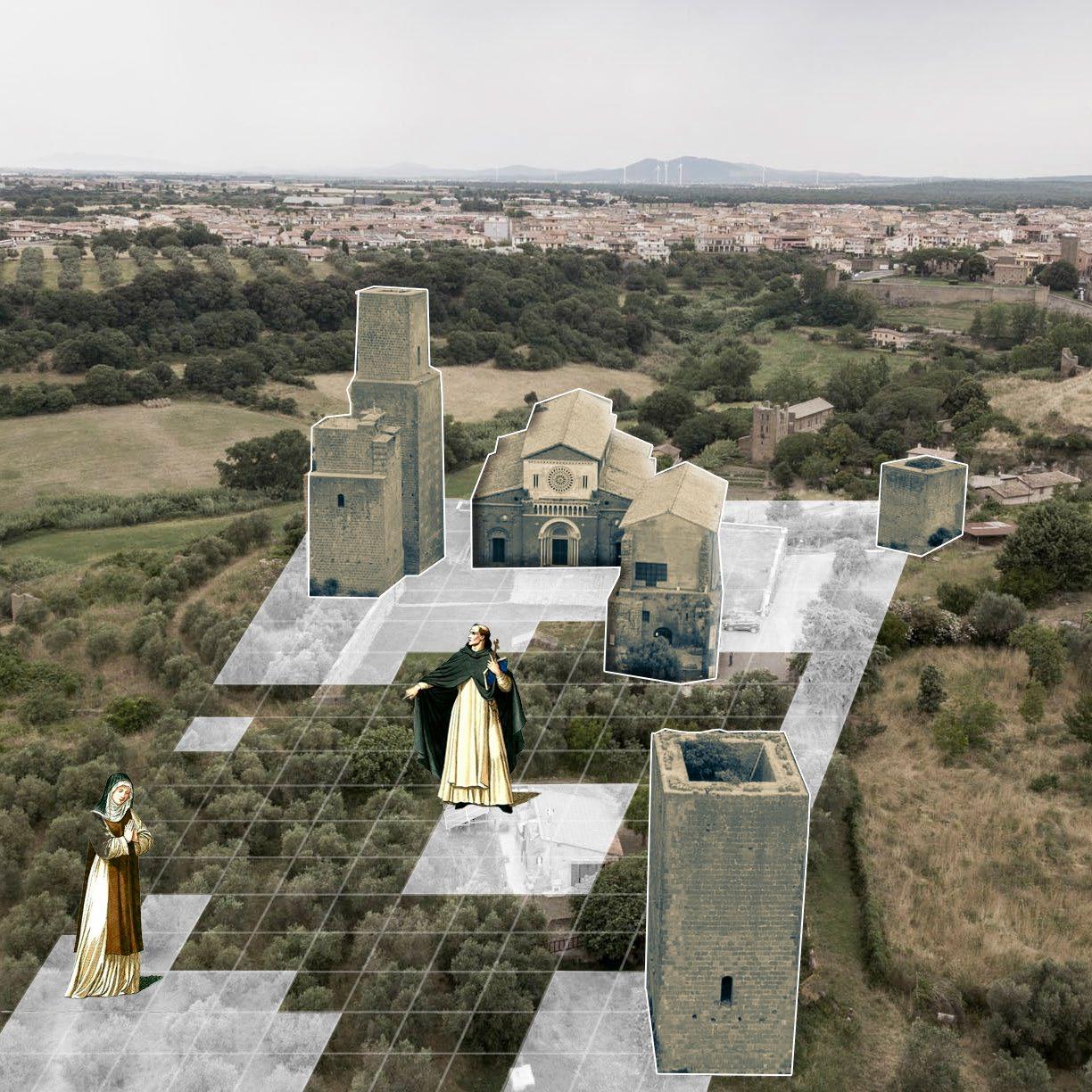
Pilgrimage Trio
Adaptive Reuse and Restoration of St. Peter’s Church
YAC Competetion 2024
Individual Work
Site:Tuscania,Italy
Site area: 2360m² Project area:850m²
As years gone by, the connection between God and Human has faded in St. Peter’s Church. Many of pilgrims will flock not only to the established routes but also to more off-the-beaten-track itineraries resulting from distant traditions and precious silences.The church is a place where time seems to stand still, and ancient stones tell of distant times, pilgrimages, and devotion. On the occasion of the Holy Year, St. Peter’s Church will need new spaces, where to exchange stories and experience moments of meditation, find a comfortable place to rest and live the experience of pilgrimage. It aims at generating spaces that are functional, but also a source of reflection, harmony and beauty by enhancing once again one of the oldest and purest purposes of architecture: giving shape to intangible and spiritual elements.
I inserted the grid system to cope with the connection between new and old. The new addition strictly follows the original order with no intervene to old one and bring new life to the church. Whereas, tourists can see the religious events, experience the history of this place and maybe have further thoughts after their journrey.
The church is situated at the top of the Saint Peter’s hill. The monumental complex consists of the Romanesque church, former bishop’s palace, outdoor area and three medieval towers.
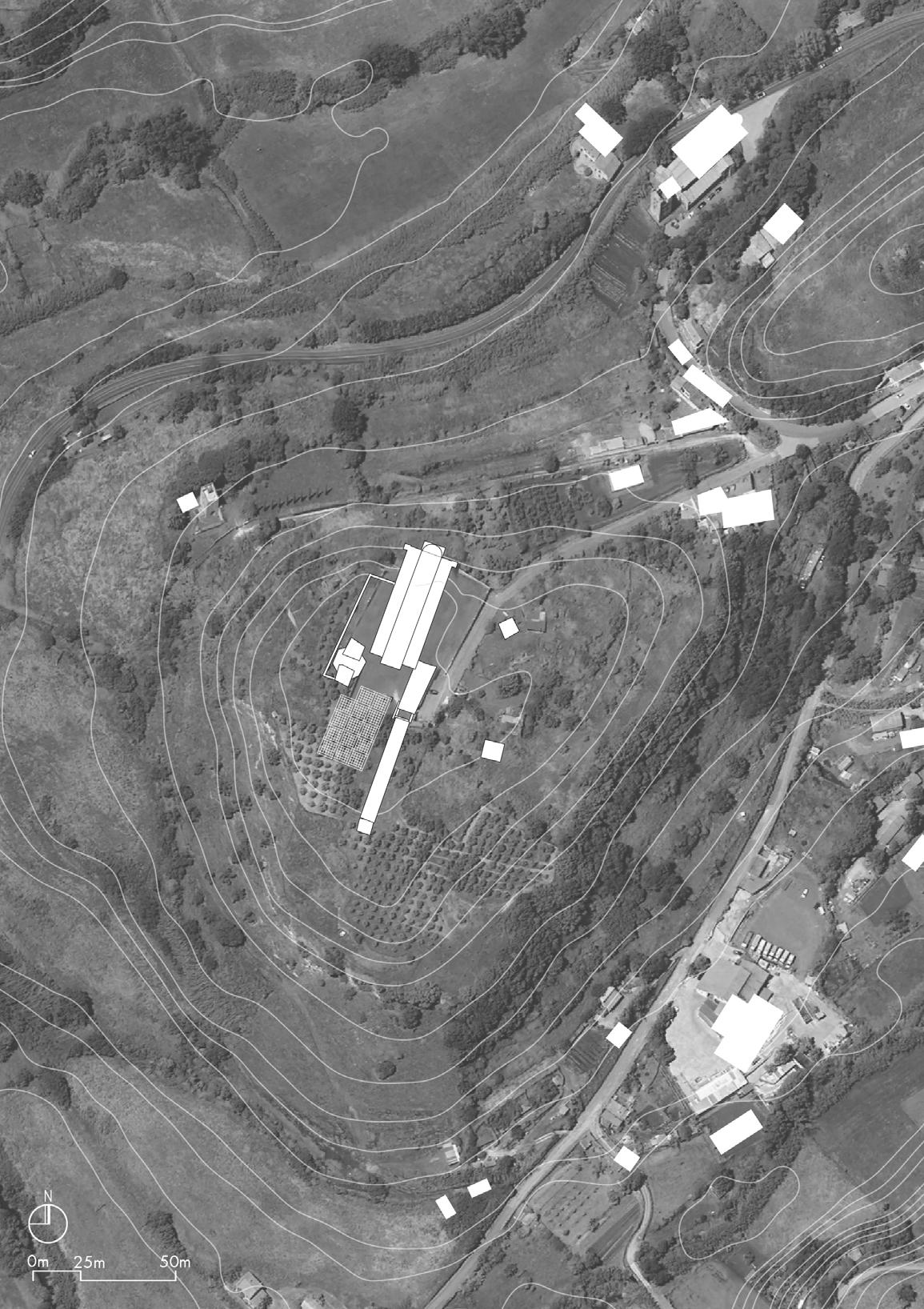
Church: a Tool to Shape Realities between Human and God
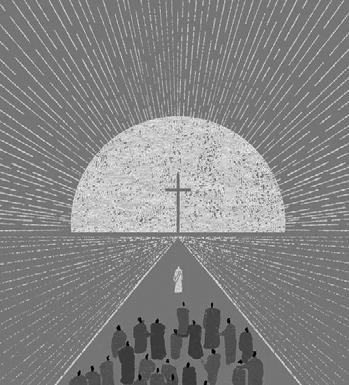
Human beings are peculiar creatures, a tangle of desires and questions greater than themselves. They are finite beings with infinite nostalgia, fleeting creatures with claims of eternity.Whatever its nature, the human root is intermingled with immanence and transcendence, the tangible and intangible. In this, architecture has always been and still is one of the main tools to shape abstract realities. For almost a millennium, one of the milestones of the Western spirituality has been the celebration of the Jubilee. This is a Hebrew heritage and a special occasion where the Human and Divine meet. In the 2025 Holy year, there would be pilgrimmers starting their route from Romea Germanica, and finally to Via Francigenna. The church of Saint Peter happens to be a spot to hold religious activities
The extent to which religion has influence human beings
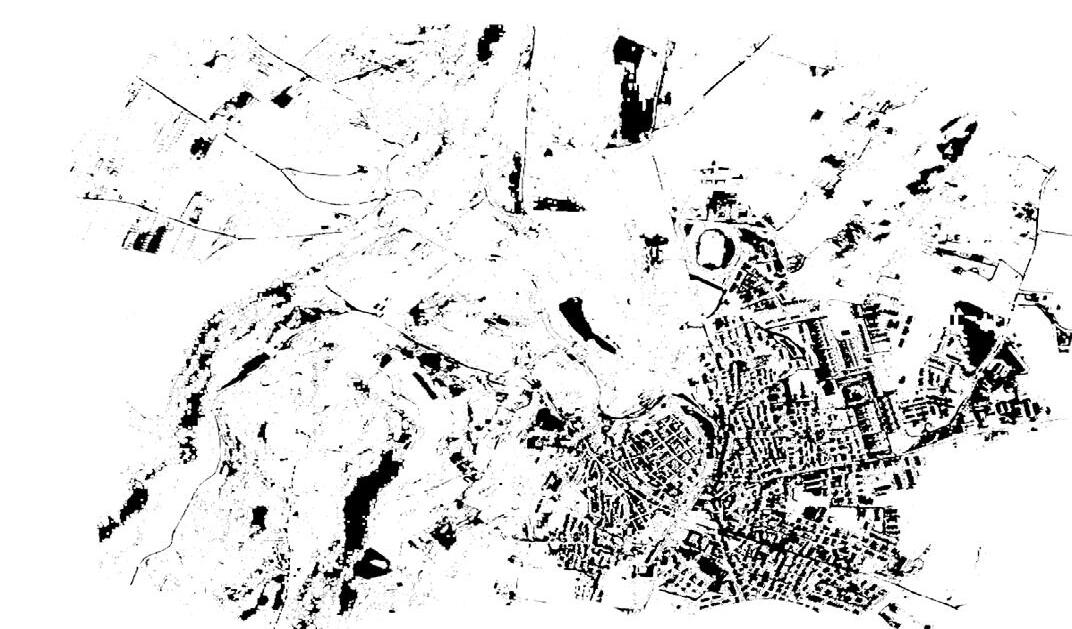
The hill started construction due to an acropolis.
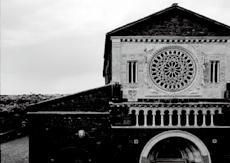
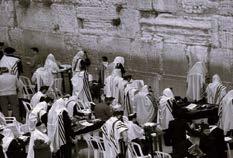

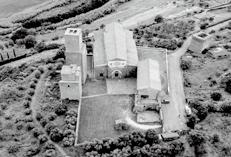
1222
St. Francis of Assisi visited Tuscania
Connection
has
A religious event resulted in huge construction of monasteries and buildings
Sacking by Charles VIII’s French army.
Present: Barely any believers would come to this place
faded in St. Peter’s Church in Tuscania
As years gone by, the connection between God and Human has faded in St. Peter’s Church. In mid-centry this kind of connection has reached a peak yet falled due to a series of historical events. However due to a series of events now the place has become a deserted place.

The New Activates The Old to Revive such Connection
Jubilees indeed strengthen one’s faith but also promote the culture of pilgrimage, reinvigorating ancient routes and traditions. These events have a significant economic and tourism impact. They increase visits to sacred, often remote sites, ensuring that they are accessible and maintained properly. In this project I consider the New as a kind of Addition to Activate and revive the Old Church. The Church itself as a core place and other old spaces are joint together by new buildings, which forms a complete circulation raising the emotion of the pilgrimmers at the end of the route. In this way, the new activates the old to revived the old system
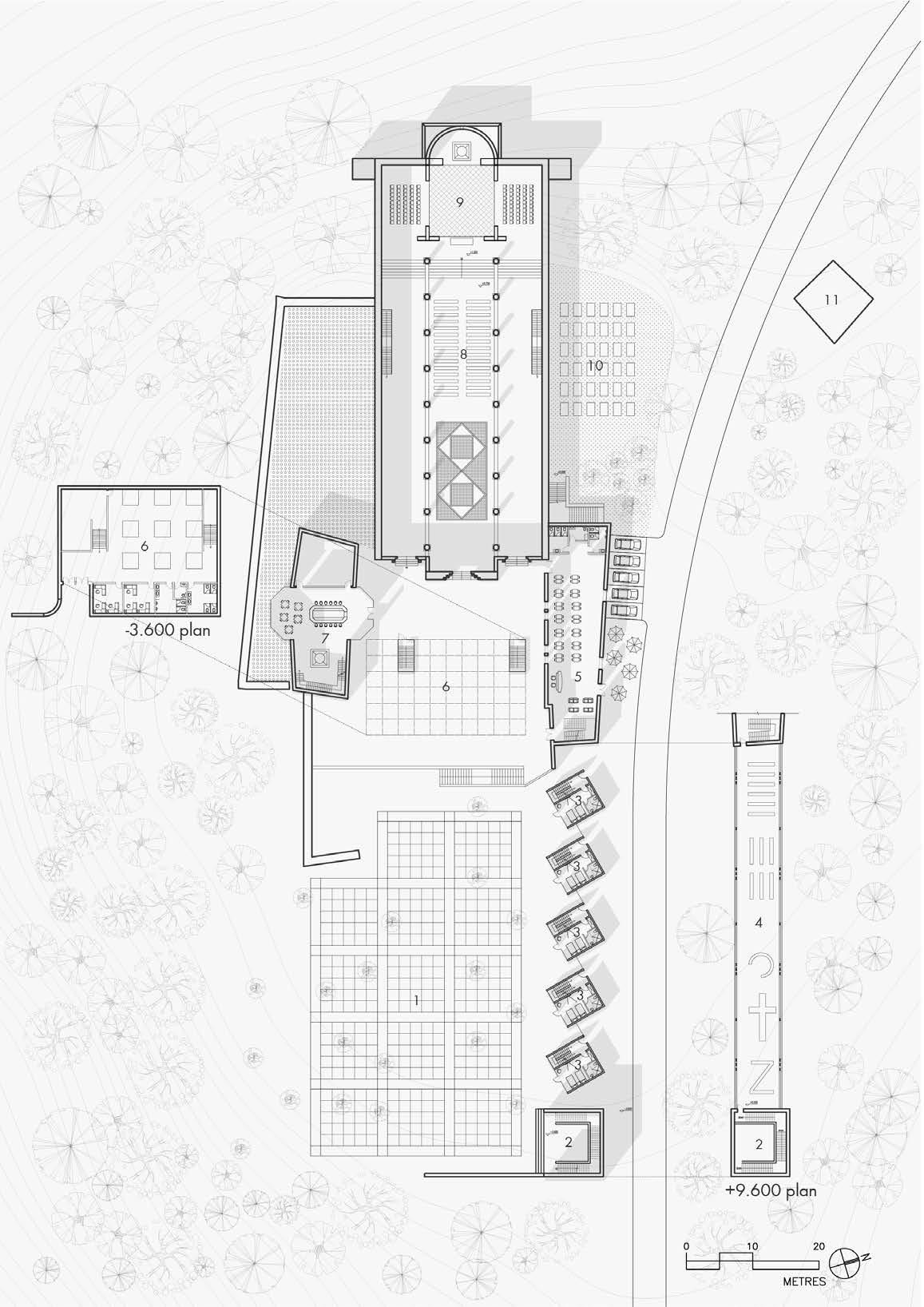
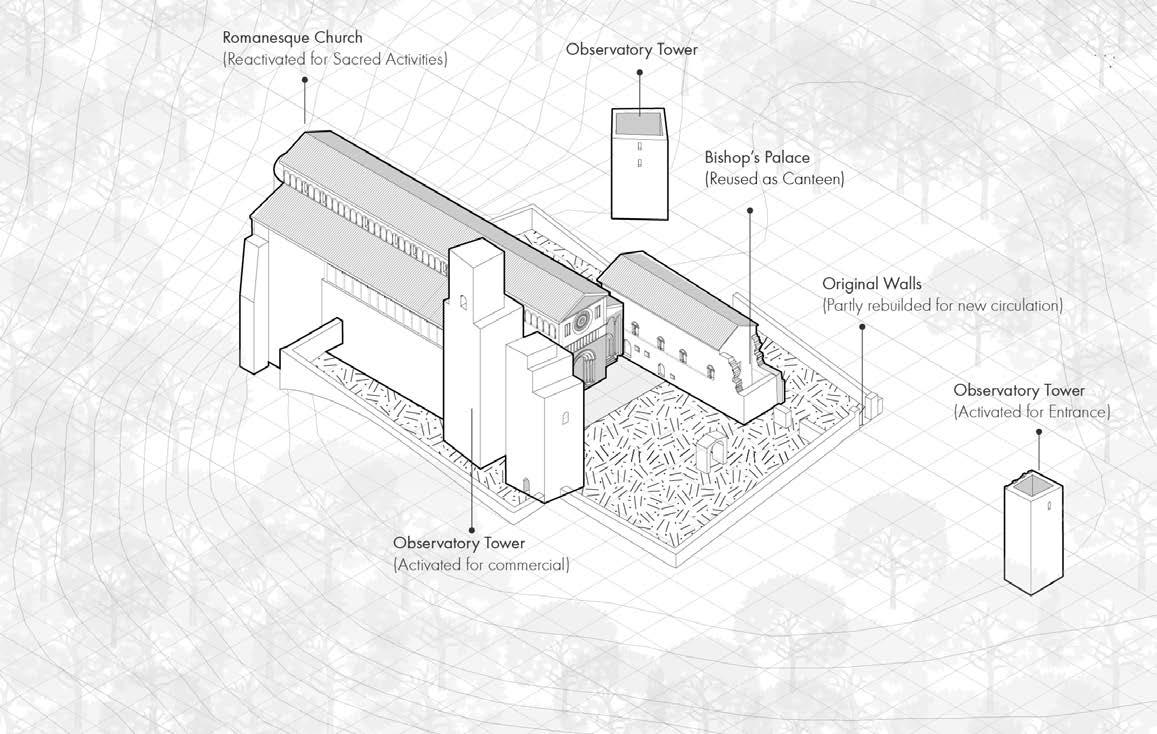
The Old Buildings seperated from each other
The old buildings have no circulations
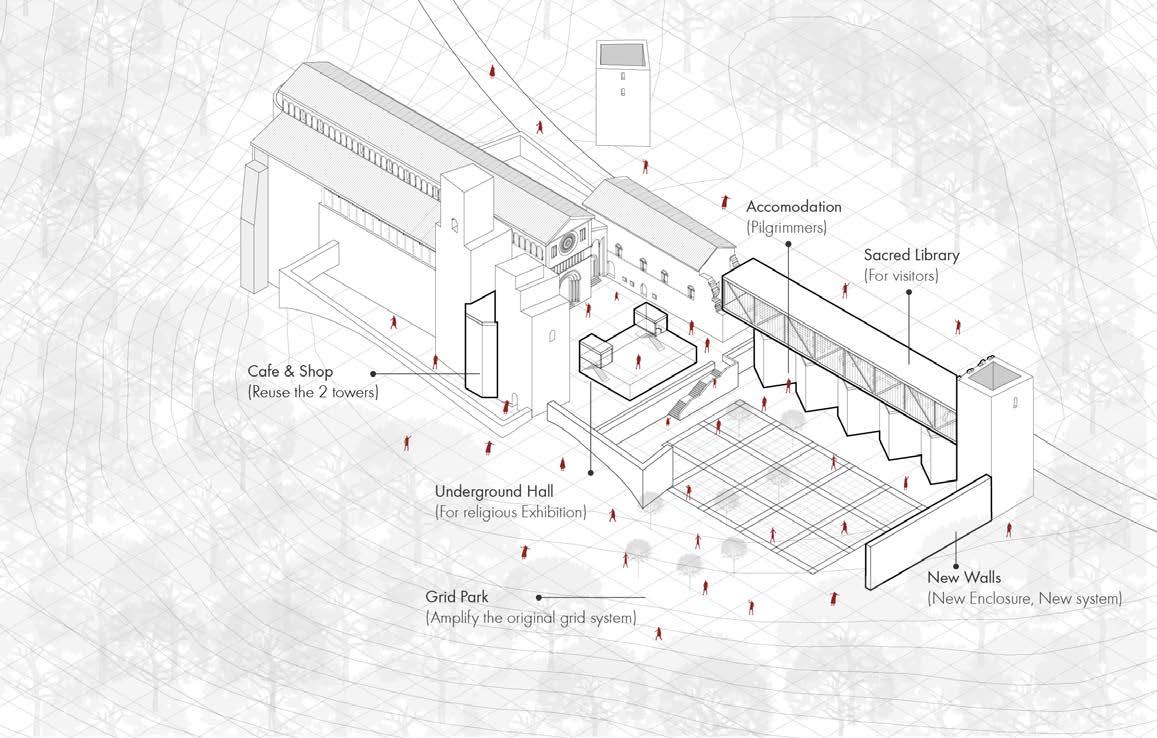
The New Addition Activates the Old Buildings
The new addition connect the old buildings and created a new circulation
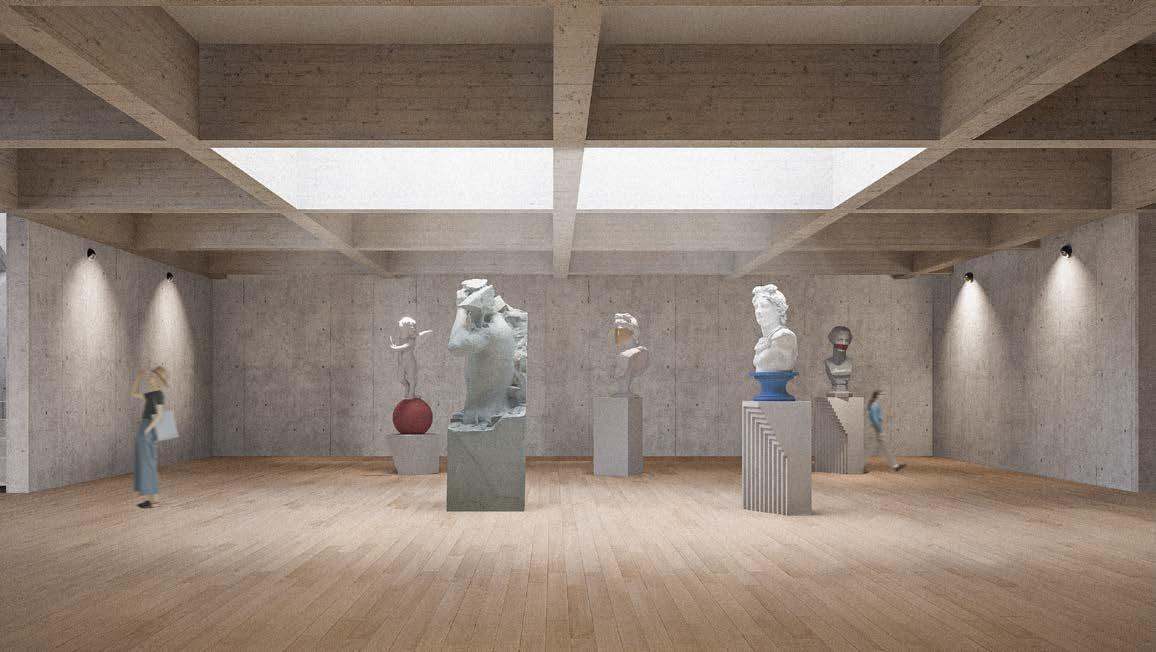
Underground Hall
Used to exhibit religious sculptures, the ceiling with grillage beam
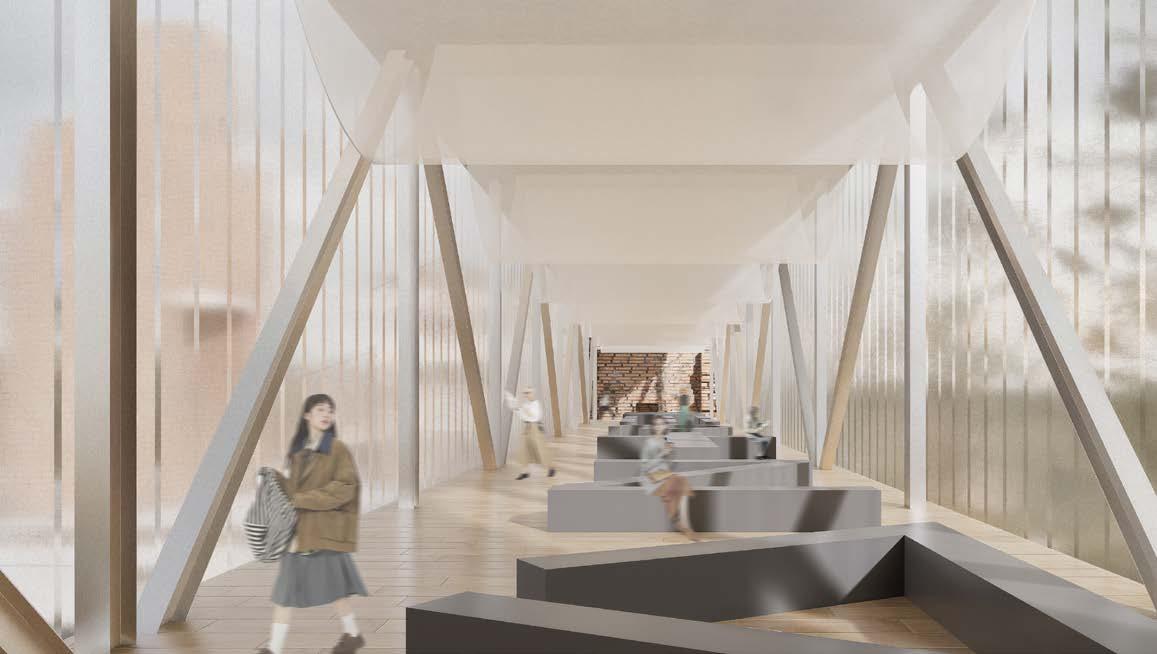
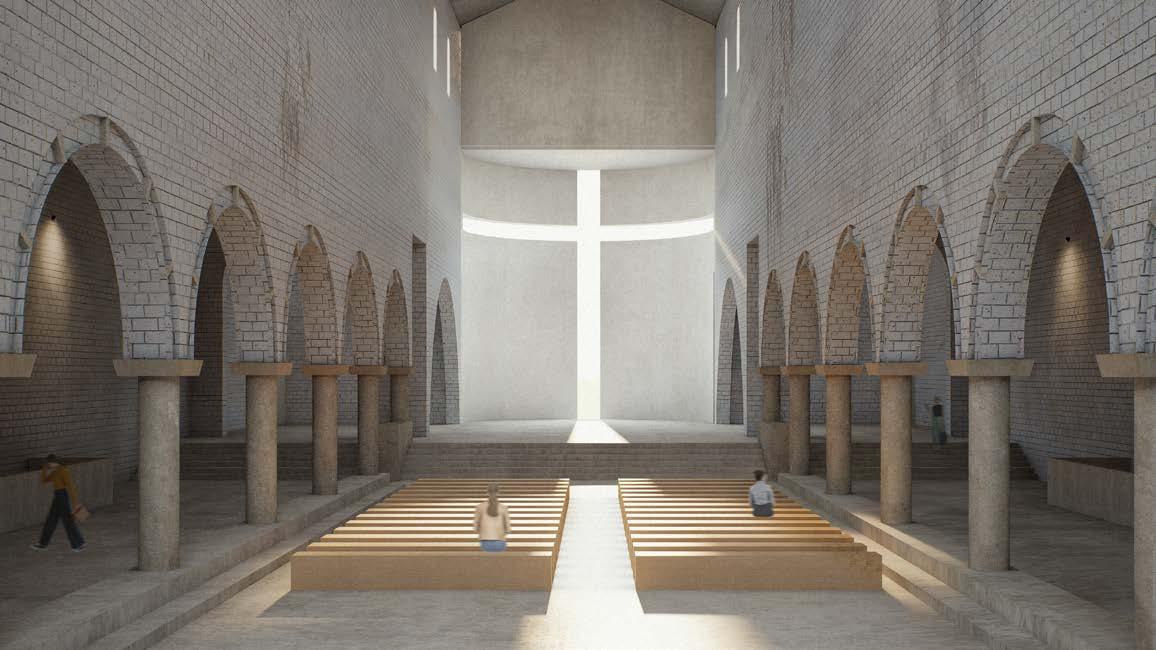
Church
Old Palace reused for Pilgrimmers Praying
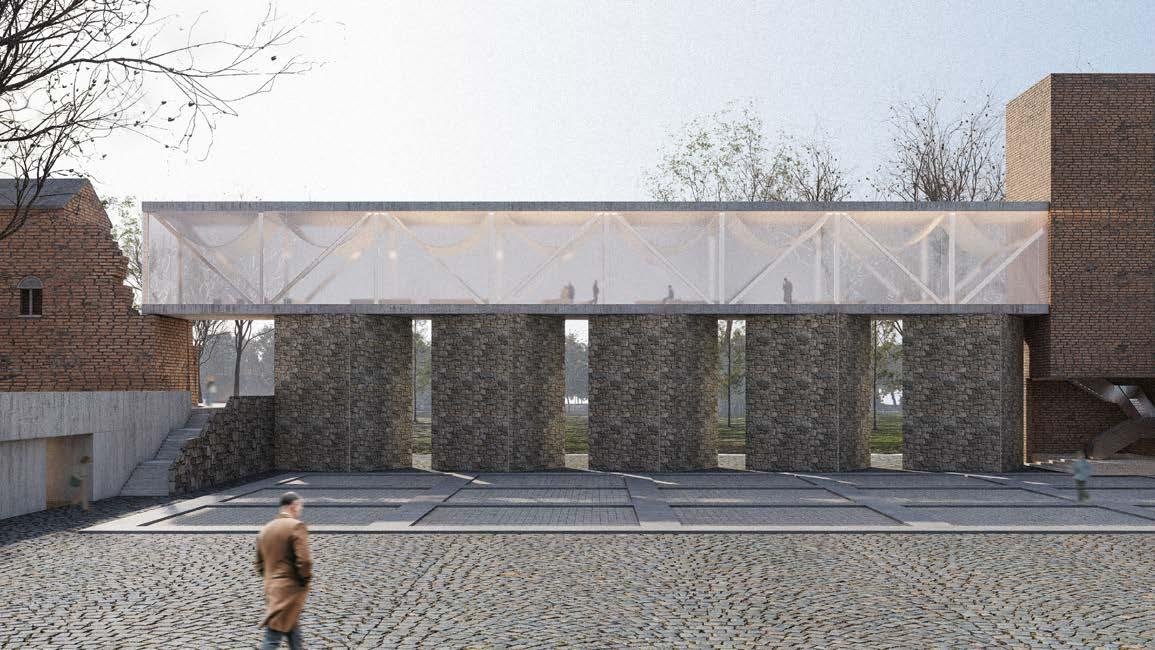
Grid Park
The library enclosed by glasses and the cabins with stone exterior walls fully respect the original brick structure of the Tower
Library
Place where pilgrims dedicated to God’s forgiveness, reconciliation and solidarity
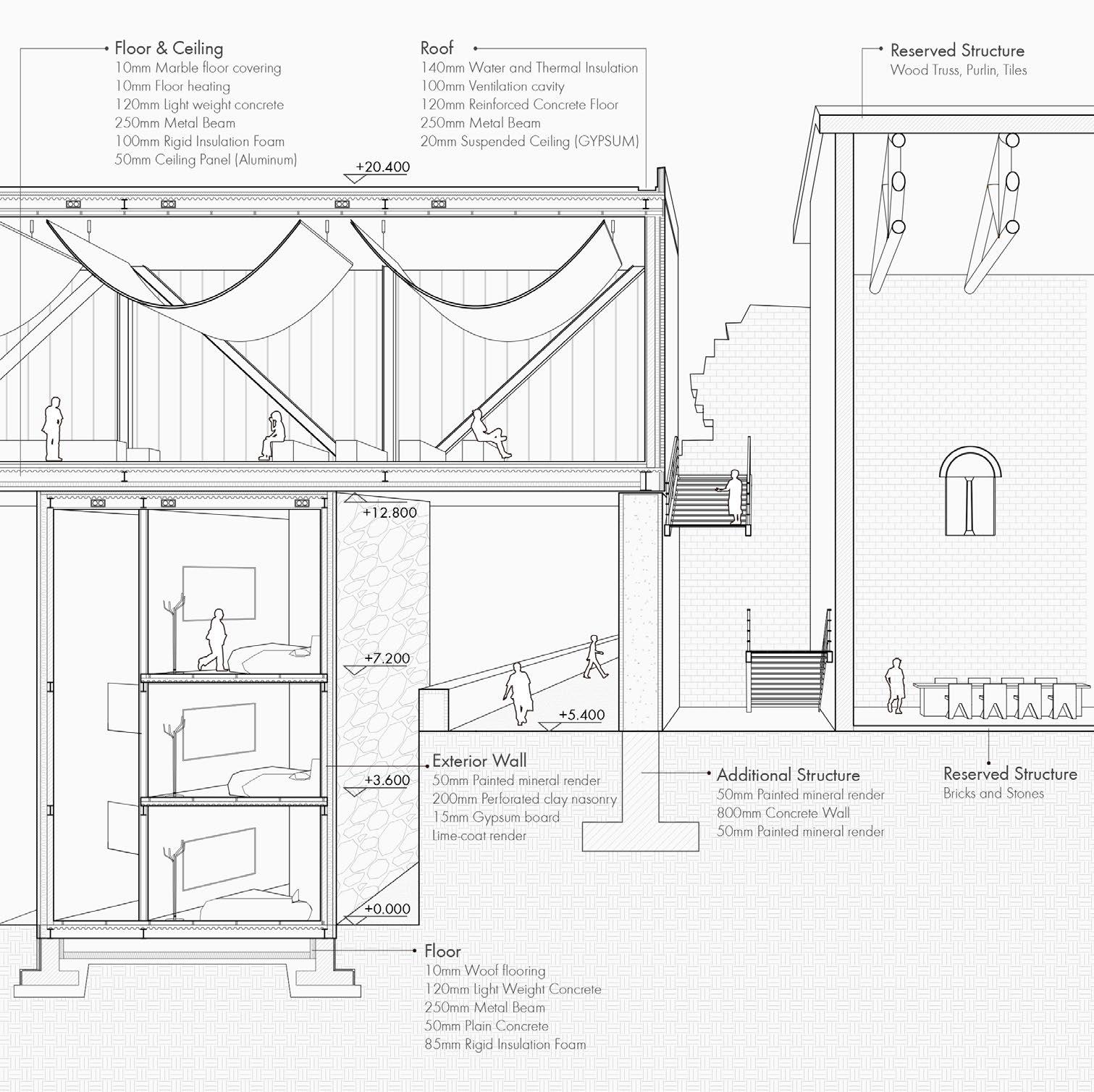
detail: How the new structure join the old one

Section: 3 Ascending level
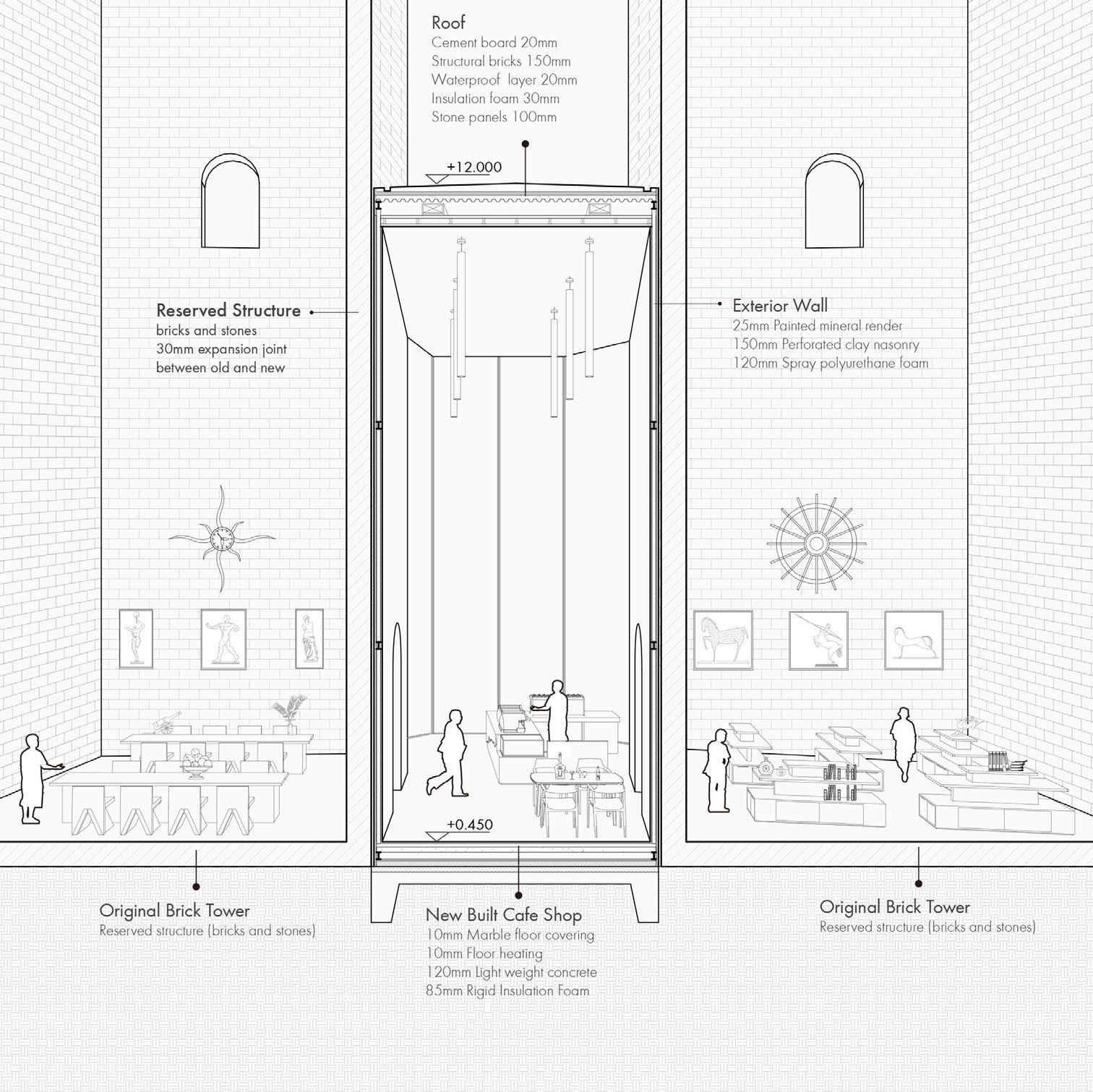
detail: How the new structure join the old one

Section: The new addition respects the original structure
Section
Section
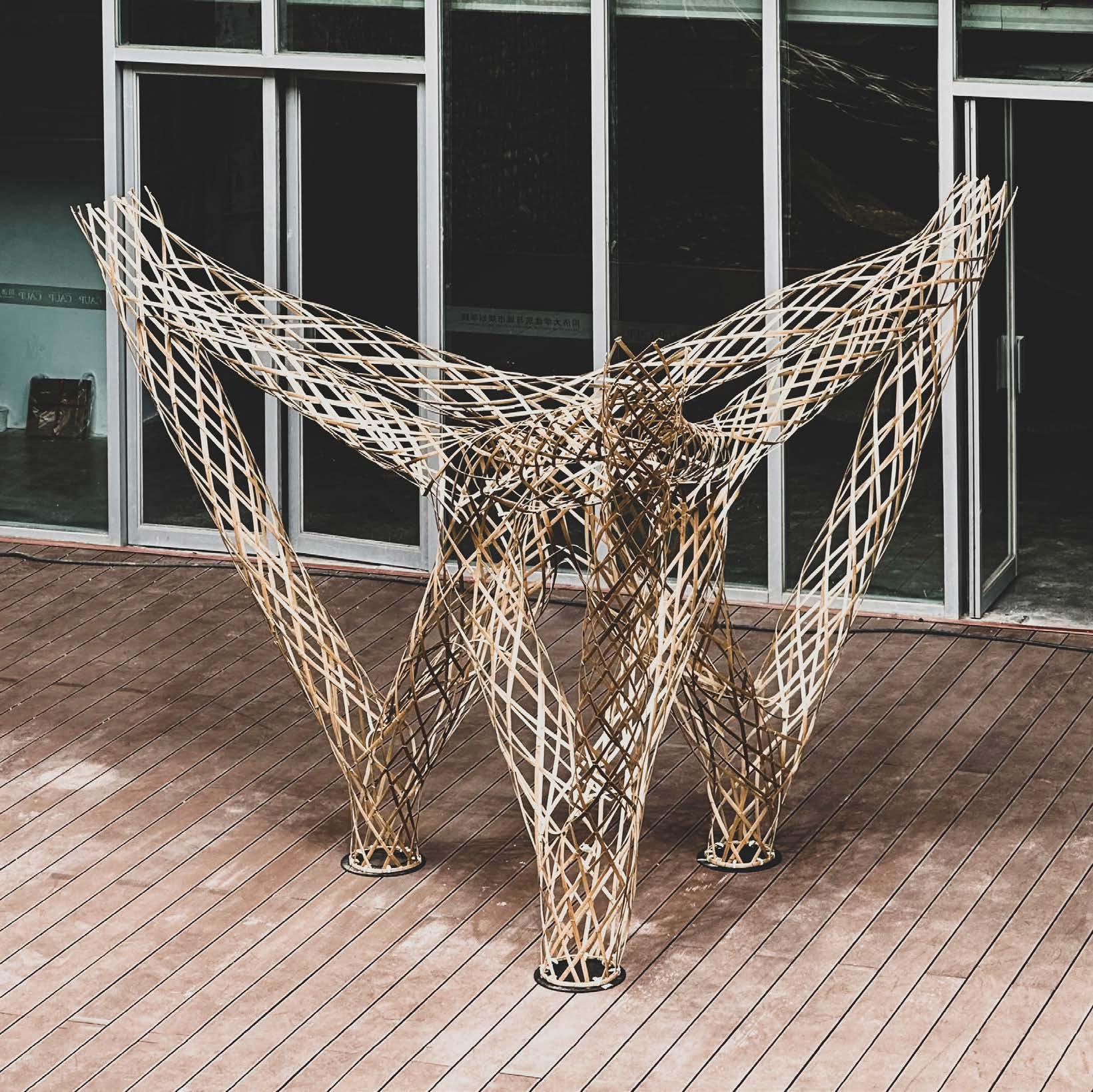
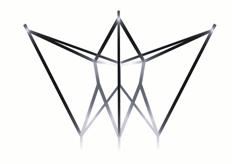
WOVEN BUTTERFLY
Bamboo Pavilion in Physical Construction
Y4 Semester2| Group Work with Su Yixiao
Paramatic Deisign and Physical Construction Studio
Exhibited in 2024 DigitalFUTURES “Transformative Bamboo Structure” Workshop
Instructor:Yige Liu,Biao Li
Construct Team: Lijia Liu,Jingyi Xiao,Shihan Li,Sijiu Yang,Ziyi Zheng,Kaiming Xie
As bamboo is one of the most rapid growing natural materials and is capable of absorbing vast amounts of carbon in the process of growth, it seemed to us to be a very natural material to begin exploring. Also, bamboo was highly pliable and flexible. The project “Woven Butterfly” is an exploration of the inherent material behaviors of bamboo and inspired by the craft-based practice of weaving
The shape was initialed by Soviet Sculpture and by using AI tools (midjourney and Stable Diffusion), and by extracting and simplifying the picture into we got a linear shape. Grasshopper was used for transforming a simple linear shape into a detailed “woven butterfly”. Then we made some experiments on the bamboo strip to test the material strength and repeatedly adapting our digital fabrication plan
The first trial turned out to be a failure for immature construction plan caused by limited working period. And due to budget reasons we weren’t able to be carried out the initiated base, But finally after the revision of the scale and detail we were able to finish the pavilion in the 7-day exhibition time.
Line Shape Extraction

Prompts
A popup pavilion made of light structure, wooden beams for frame, large wings, symmetrical as much as possible, clear structure of rods, high quality

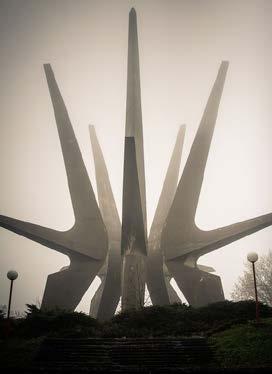
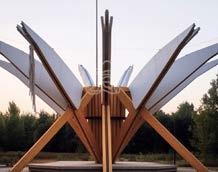
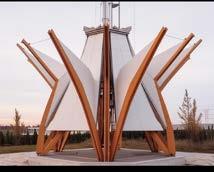
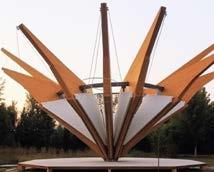

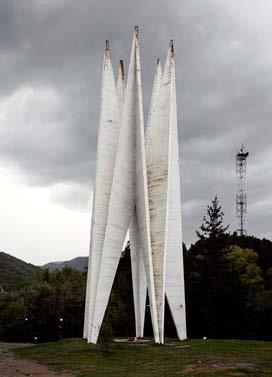

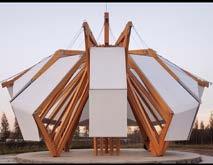
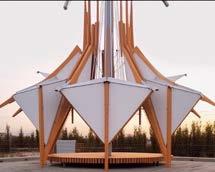

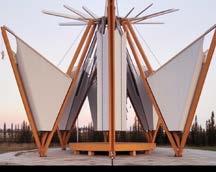

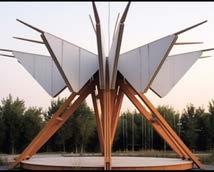
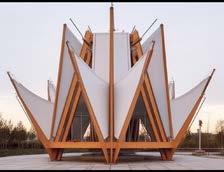
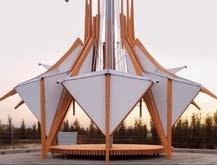
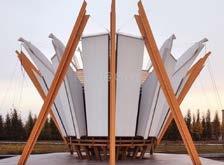
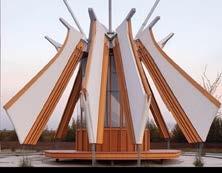
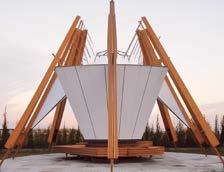
The Shape inspired by Brutalist Architecture
In the very first beginning we were told that the pavilion would finally lies in semi-outdoor space in CAUP (Shanghai) for exhibition, yet the seperate part should be produced in SEU (Nanjing) by the studio members So in the very first beginning I had a vague intention of “duplicated and symmetrical”. We were asked to got an inspiration using AI tools. I combined Brutalist Architecture in Russia and a pavilion composed of rods. Finally I got some seemingly “Irrational” pictures to choose from.
The shapes are extracted from those “irrational” AI pictures, and to make it more feasible, I simplify the line shape to make it as rational as possible. As this part is conducted with the case studies of some previous weaving related structures, I come up with making the line shape into a weaving texture on the surface, which is likely feasible and a little bit breakthrough over the case I learn.
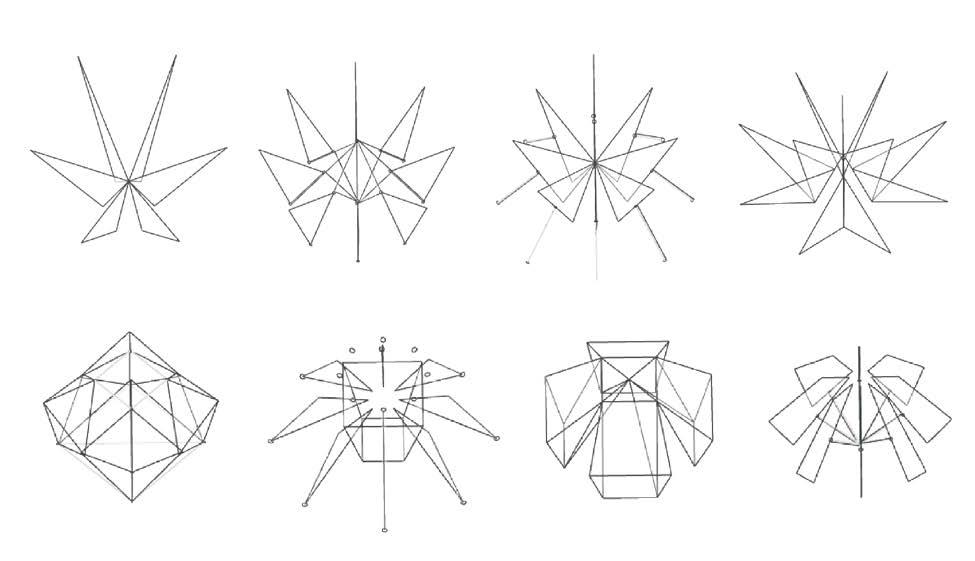
Computational framework
The design, modeling, and simulatlon of segmented shells modules is considerably complex. The kinematlcs of deployable components and the overall structural behavlor of the shell are signifcantly affected by geometric and topologic features at different scales. It’s also necessary to incorporate materlallzaton princlples at conceptual design stages to ensure the viabllity of the deslgn. A consistent digital approach was formulated, combining design process with computational models that vary in detail.
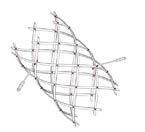
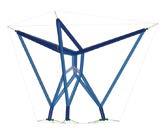
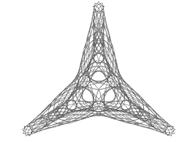
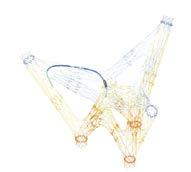
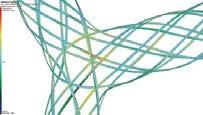

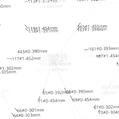
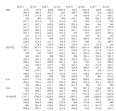

Picture of a real Pavilion
The symmetrical property has intensified
Option1: Monument of Red Star
Option 2: Russian Center for Robotics Combine the 2 Pictures in Stable Diffusion Midjourney

Step 1: The linear shape
We got several types of linear shape but choose the one with cantilever to make the fabrication more challenging.
Step 2: Volumn
“Multipie” in grasshopper to get a curved SubD volumn of 24 cylinder.
Step 3: Division
The cylinders are divided into segmented surfaces.
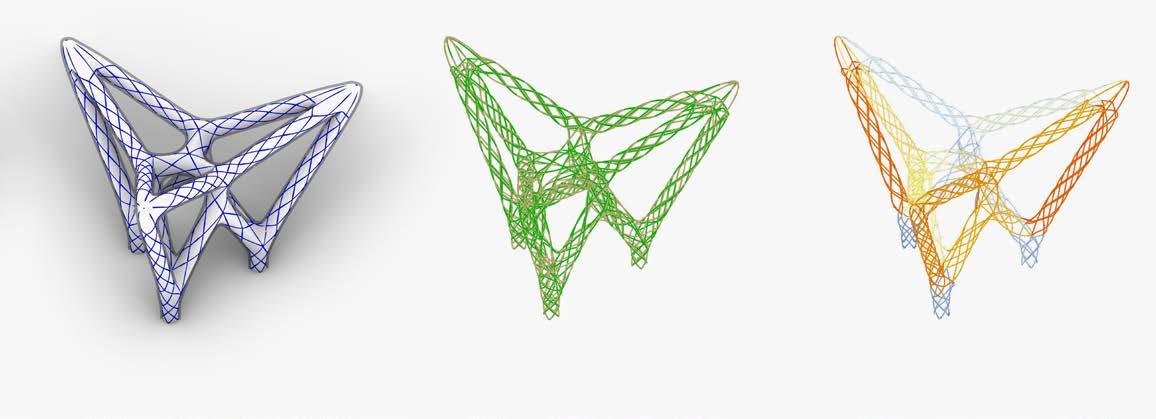
Step 4: Connection of weaving
The surfaces are connected diagonally
Step 5: Optimize the Curvation
The trip can be twisted and bended within a maximum angle (tested through experiment)
5 Flexible Parameters to Control the Result of the Pavilion
Step 6: Digital Construction
Label each cylinder, export the segemented length of each strip to excel
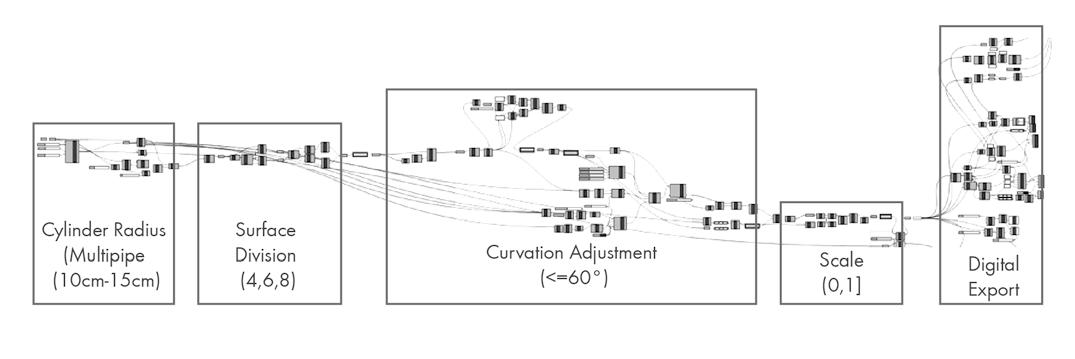
Digital Fabrication Layout
We inserted several flexible parameters listed above. The number of turns a curve takes around the edge determines the number of crossings along the cylinder and, ultimately, its deployment. The diameter of the cylinder directly impacts the structural performance of the overall shell. According to the experiment test of the bamboo strip we got, we continuously change the parameters and exported a detailed construction form with the of the segment length of the 24 bamboo cylinder.
Segmented shells Modeling
Segmented shells are a different type of discrete shell offering a simpler construction process than elastic gridshells. The fundamental principle is to connect prefabricated components in a step-by-step process to create a unified shell structure. The connection between components is crucial since any compromise in material continuity can reduce the structure’s stiffness.
The connection is geometrically modeled by extending one of the curves using tangent directions and incorporating an overlap between connected curves. Materialization constraints based on the dimensions of the available bamboo rods are enforced at this point to restrict the maximum length achievable by those curves. Consequently, a tessellation containing triangular tiles is generated on the surface of the node through the connection of spiral curves.
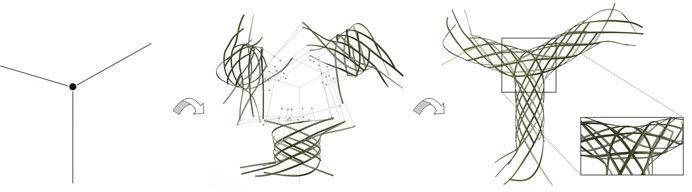
Structural Analysis
Structural analysis is integrated into the framework at different stages. An important consideration for developing the research demonstrator was the utilization of raw bamboo slats. Up-scaling a structure built out of raw bamboo requires a calculation process that considers the material properties derived from test results. This is because raw bamboo has substantially varying mechanical properties and cross-section dimension along the axis, unlike more standardized and graded building materials such as steel or concrete. Hence, integrating structural information into the design loop requires the characterization and evaluation of the acquired batch of material. Multi-scale calibration on the material, component and global levels provides an understanding of the range of scalability the structure can achieve.
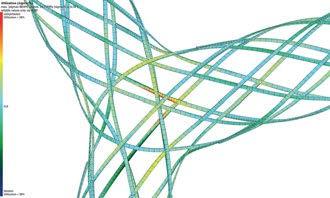
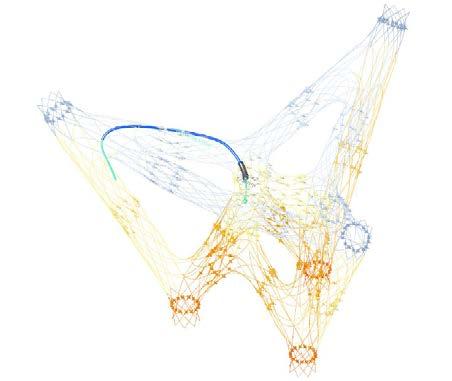
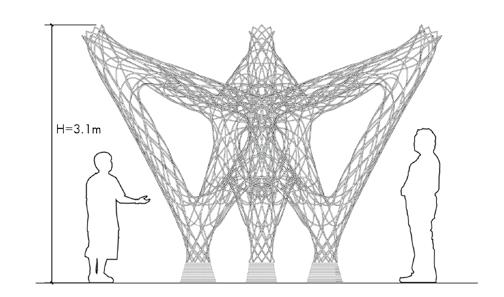
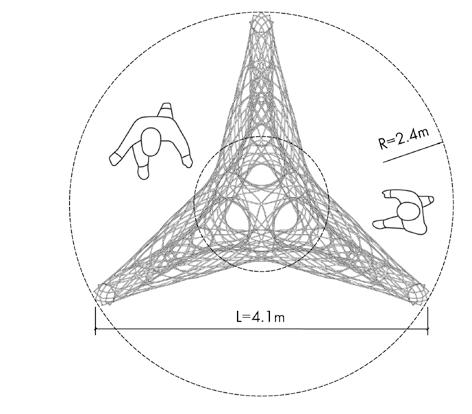
Cylinder1 Cylinder2
Cylinder3
Base Assembly Details
To make the pavilion as stable (The bamboo strip is too light) and for aesthetic consideration , we made a flower-liked, cut in pieced wooden base in the first version. Iron components to join the base and bamboo strip.
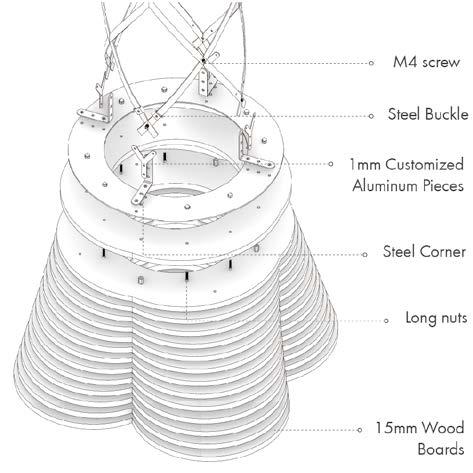
Bamboo Cylinder Joint Details

We customized aluminum panels of hexagon for each joint, and use steel buckle to join the end of the strip with the aluminum panel.
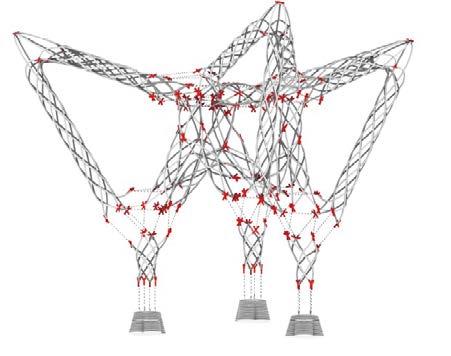

Assembly Components
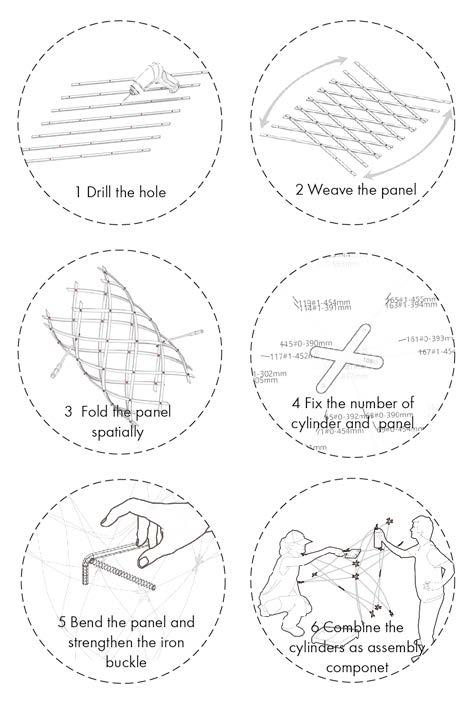
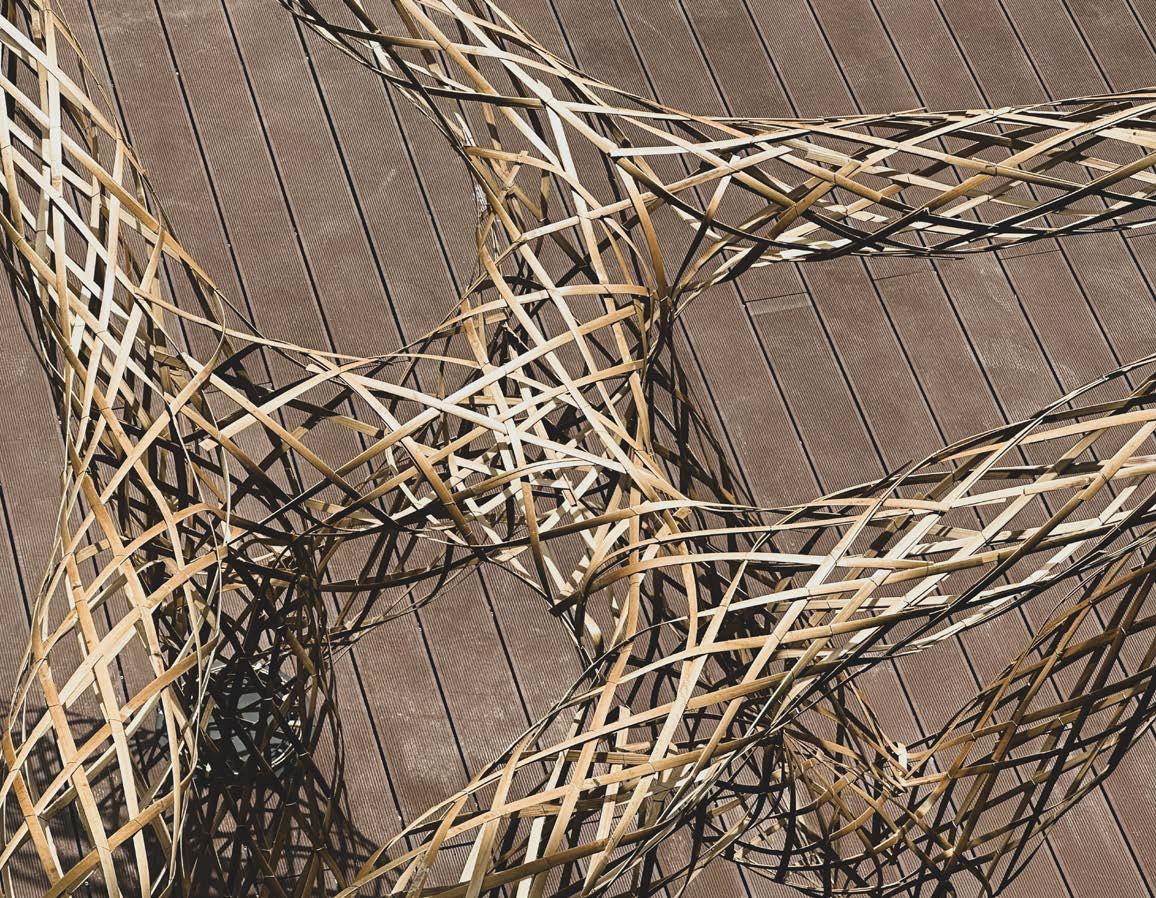

Construction Plan

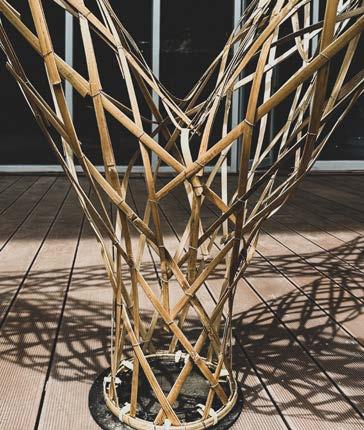
During pre-fabrication, a peer review system was instituted to ensure that manual measurement of the joints and label information precisely aligned with the data of the digital model. A custom-designed labeling system was adopted to include, in each bamboo slat, the required weaving information for assembly. Holes are then manually drilled and slats are cut to length with a hand saw. Finally, slats are connected with screws to create the cylindrical components, which were stored in their compact state. For budget reasons the base weren’t carried out in the first version. (As the second version scaled 0.6 and the foundation doesn’t fit anymore)
Aluminum Panel Position
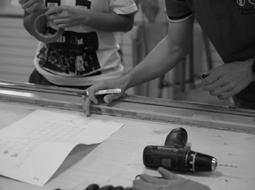
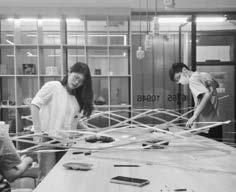
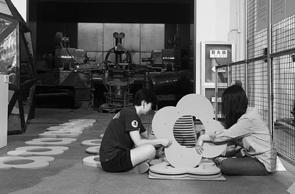
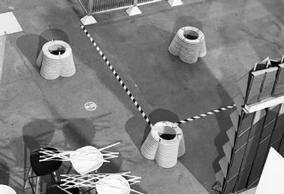
Transport to the site once the pre-fabrication was done On-site Assembly Preparation
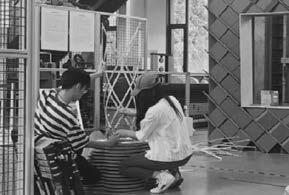
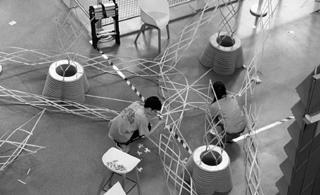
Q: How to reach the highest point at 6m???
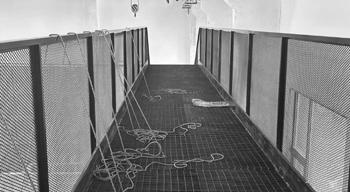
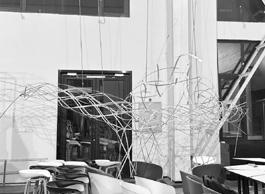
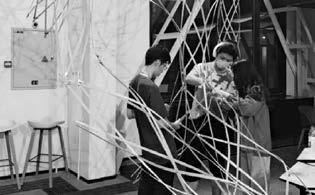

Transfer the stress from up to down

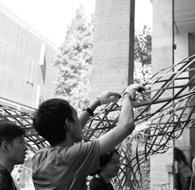
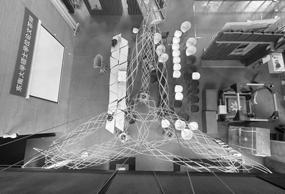
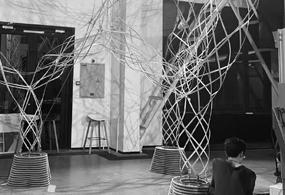
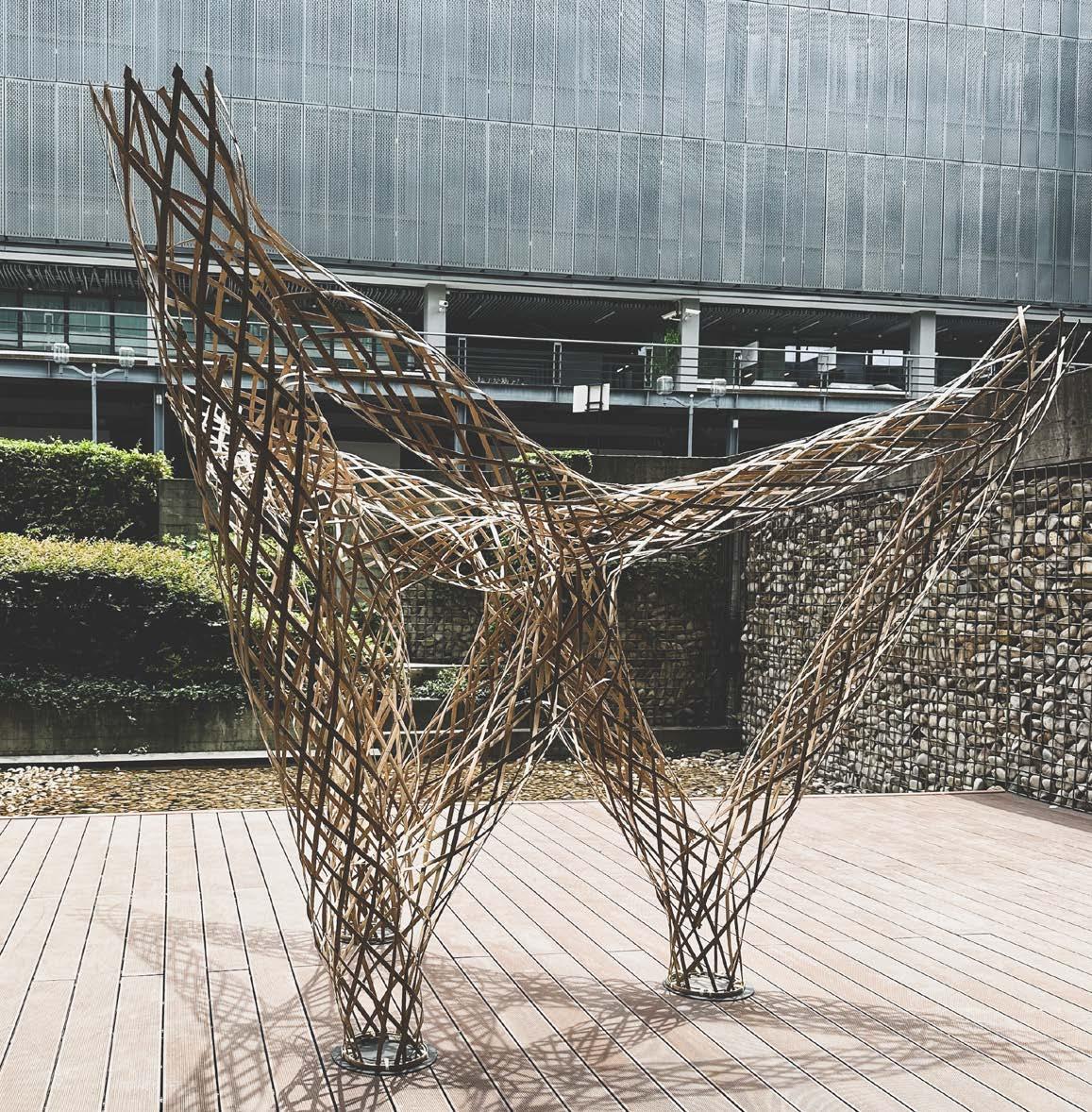
The assembly sequence of the entire structure was carefully planned by taking into account the maneuverability of cylinders and the site context. A top-to-bottom strategy was adopted, which involved assembling the upper part on the ground and then lifting it up using tension cables. This enabled adding the remaining parts of the structure and joining the nodes always at the floor level. The structure was raised gradually as cylinders were added. The next row of woven nodes was created by adding the remaining two cylinders per node, which also served to close the first level of pentagons and hexagons. The third row of woven nodes was completed after adding the cylinders in contact with the floor. The structure was then carefully released from the tension lines with the end cylinders attached to the base, thereby becoming load-bearing. The first trial were not that successful as it’s too large and weak so we scale the pavilion to 0.6 in the revised version. The second time carried out in CAUP were much more successful. And also it’s much more stable and stronger.
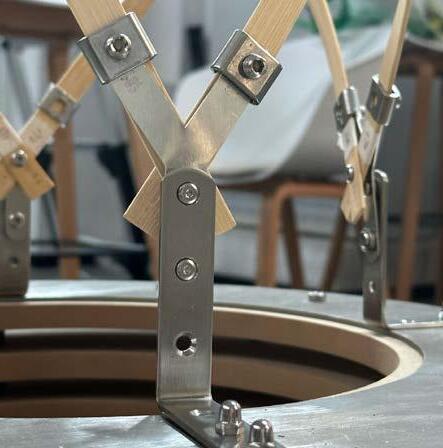
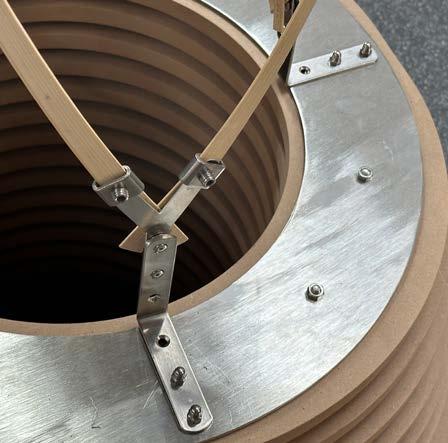
Weave the Cylinder P1
Drill the strip P1 Base Assembly P1
Raise the rope once a layer is completed
Locate the base in right position P1
Lower part fixed to the base
P2
Upper part assembled on ground P2 Release
Upper
Redo in Smaller Scale
Assembly Flow
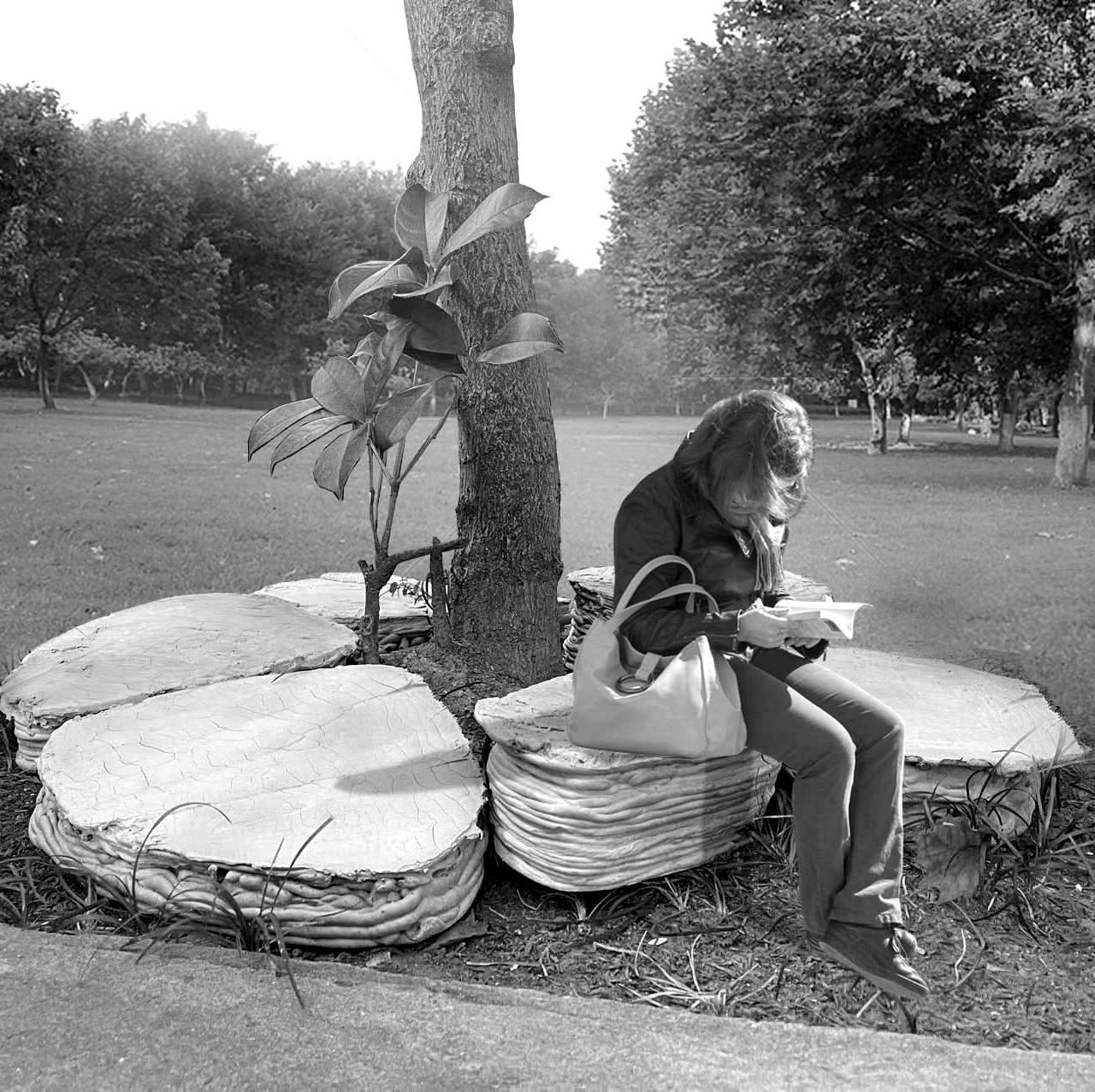
Voronoi Collision
Digital Manufacturing based on Concrete 3D printing
Collaborative Work with Li Yi, Tian Ye in 2023.12
Instructor: Li Li
Students’ Research Training Project
Writing Sample Revised Individually in 2024.12
As the largest and most widely used building material in the current construction industry, concrete has made irreplaceable contributions to the progress of human society. However, the high energy consumption and high pollution of concrete waste have gradually emerged. Since digital construction has become a trend in construction field in the 21st century, 3D printing concrete technology will surely become a promising construction method for customized architectural components
The project studied the form suitable for 3D printing, and designed a tree pool in random Thiessen polygon shape. Since the shape of the tree pool can be changed accordingly and different from each other, the advantages of 3D printing technology are showcased. The selected tree pool is composed of six units with different shapes and heights. The units are inverted and printed and then turned over. The tree pool can be used as a seat and are suitable for parks or kindergartens. Compared with traditional technology, the amount of concrete required is only one-fifth of the traditional pouring method, and it is more time-saving and labor-saving.
The essay fully recorded how we origins from case studies to final printing experiments. The printing gone through 6 times of experiments, each of which was optimized based on the previous trial.
Research Background
1.1 Origin of Concrete Printing Technology
Concrete remains one of the most commonly used building materials in China today due to its durability, abundant raw materials, and ease of preparation . The current construction methods mainly include pre-fabrication and cast-in-place. The pre-fabrication method has limitations such as fixed models, limited sizes which have resulted in small, monotonous spaces in residential buildings, while the cast-in-place method has addressed some of these issues, it still requires framework for shaping. The use of molds restricts the form and surface texture of concrete components. Since digital construction has become a trend in construction field in the 21st century, 3D printing concrete technology will surely become a promising construction method for customized architectural components.
1.2 Current construction Usage
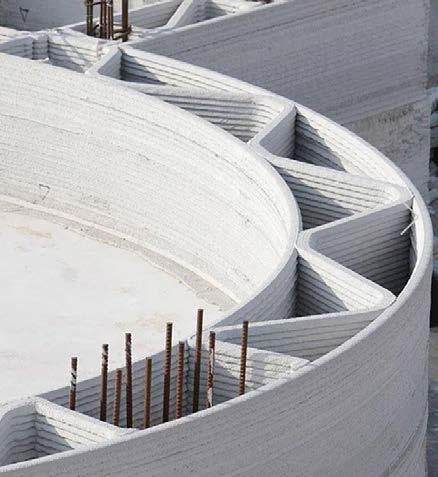
Currently, there are 3 main 3D printing technologies are applied in the construction field: D-shape, contour crafting, and concrete printing. In 2019,ETH has unveiled details of "Concrete Choreography". The installation presents the first robotically 3D printed concrete stage, consisting of columns fabricated without formwork, and printed to their full height in 2.5 hours. The process is expected to greatly improve the efficiency of concrete construction while achieving the fabrication of complex components.In 2022 a ceiling that uses a 3D printed mold called "HiRes Concrete Slab" was conducted by ETH. This ceiling is installed in the NEST research building. The ceiling surface has multiple curved lines that simulate the structure of leaves which is a rather complex design. Materials are saved by about 70% compared to traditional construction method.
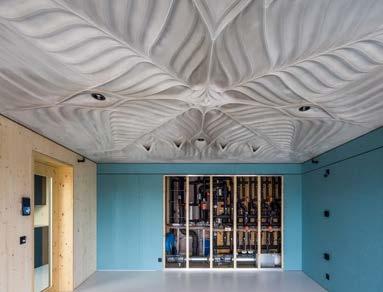

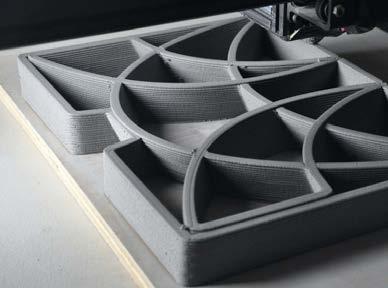
1.3 Technical Route and Research Methods
This experiment is based on the project of printing small-scale flower pots in the same way in 2022. We hope to explore and design components that can better reflect the advantages of concrete printing based on its property, enlarge the scale and apply the printing results to other practical uses.
The technic routes are shaped below. After the complex 3D shape is generated by Grasshopper, the 3D shape is sliced and converted into print head tracks. The track assembly is used to build a concrete 3D printer, and the mixing and preparation of concrete materials are studied, and finally the 3D shape is printed.
Ⅱ.
Printing Object Design
2.1 Object Type
the Experiment
Traditional concrete construction methods rely heavily on standardized molds . Concrete 3D printing, utilizing the principles of numerically controlled machinery, directly construct entities based on 3D models, free from the constraints of molds. This construction method demonstrates high precision and freedom in forming complex geometric shapes Municipal landscape facilities, on the other hand, are more suitable for concrete 3D printing due to their flexible scale and diverse forms. These projects typically have lower structural performance requirements, making them ideal for the quick, direct shaping capabilities of concrete 3D printing.
2.2 Shape Design
The morphological generation algorithm of random point generation Thiessen polygons is incorporated. The shape of Thiessen polygons is controlled by the position of random points in the area, and each of them is given a random height to achieve the purpose of controllable random morphology.The design also proposed a feasible technical solution for each unit: start printing from the bottom, and after completion, turn it upside down, and use a grid structure support in the middle to form a seat surface. The 3D printing method can print the model into a bottomless and hollow shell, and the amount of concrete used is only one-fifth of the traditional casting method. The weight of the unit is also greatly reduced making it easy to carry.
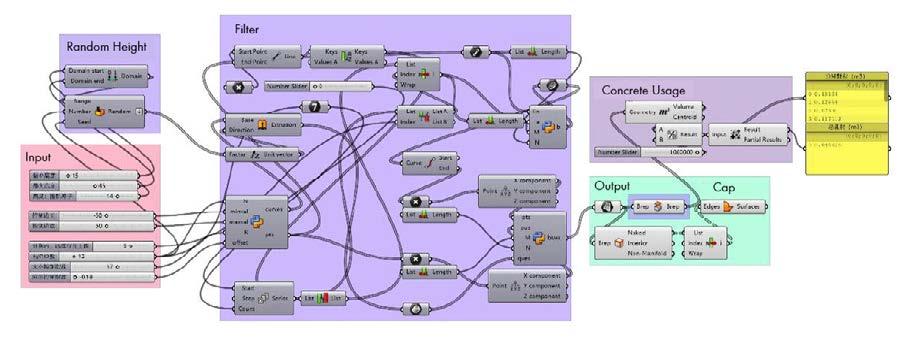
Modern Concrete Printing Projects of Different Scale and Usage
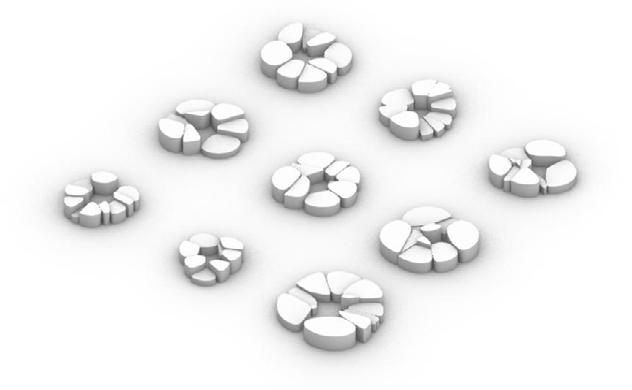
Random Pattern Developed by Grasshopper
2.3 Computation Design Process
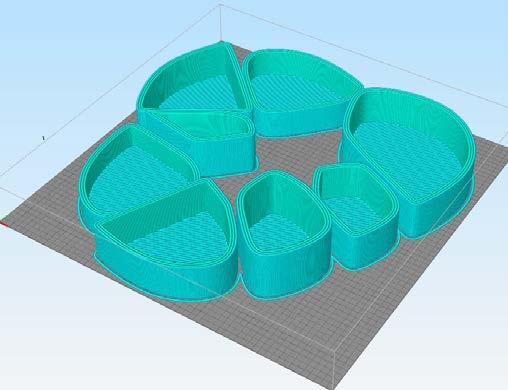
Slicing and Printing Route Planning
The parameter N controls the number of cells, minval and maxval control the length and width of the generated range respectively, R controls the relative size of the Thiessen polygons , and offset is used to control the spacing range between monomers. Combined with highly random seeds and screening algorithms, we can get tree pools of various shapes by changing the parameteres. Concrete 3D printing makes this kind of multi-shaped shape possible due to its strong degree of freedom and algorithm compatibility of additive manufacturing.
2.4 Model Slicing
Model slicing is the key to the process from 3D model to control and drive 3D printer. After slicing, the layer should be path planned. In this project, model slicing and path planning are completed using Simplified 3D software.
3.2 Parameters Set
The parameters that affect the molding accuracy and quality of the printed model in response to different concrete mixes and model differences mainly include:
1.Printing nozzle travel speed
2.Discharge speed
3.Printing layer thickness
4.Printing line overlap width.
Printing Facility and Material
3.1 Machine Assembly
This project uses a truss-type 3D printer structure. The nozzle moves along the planned path under the action of the conveyor belt. A vibration motor and stirring rod are added to the feed port to continuously stir the concrete to prevent it from solidifying at the feed port.
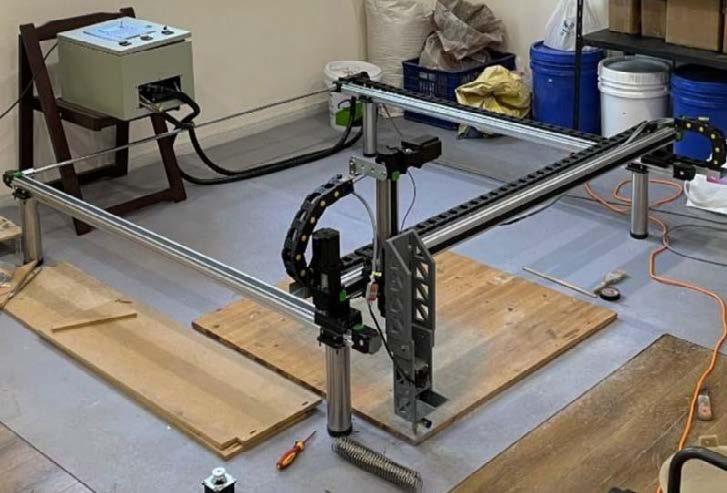
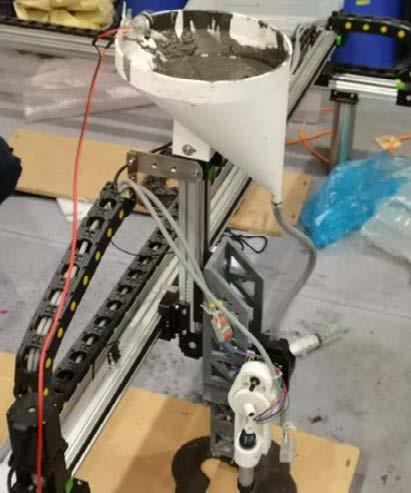
After a set of experiments of the machine, finally the parameters of the printer are set as follows
3.3 Printing Nozzle Optimization
Due to the pumping action of the rollers, the printed lines will have a pulsating texture, affecting the final finished product. The new print head has a spiral structure. The concrete is pumped into the print head cavity through a roller pump. After being stirred by the spiral rod, it counteracts the pulse texture of the pump
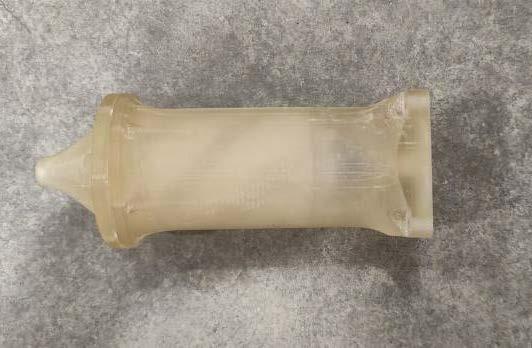

3.4 Material ratio Studies and Experiments
According to previous researchs, Concrete materials suitable for 3D printing should have such properties:
1. Moderate fluidity
Too Fluid------the components will deform or even collapse
Too Solid------cannot be smoothly squeezed which may cause blockage or intermittent output
2. Short solidate time
The use of sulphoaluminate cement can obtain a shorter solidate time, or add a suitable proportion of quick-setting agent during printing.
3. Higher mechanical properties
The layered layer stacking structure formed by 3D printing has a lower density, and the structural strength of the printed components is lower than that of traditional methods and prefabricated components.
After several experiments we configure the materials according to the following proportions.
Cement Powder 2000g
Water 600g
Thixoropic agent 6
Accelerating agent 50
Expanding agent 6


The customized new nozzle by Plastic 3D printing
Printing Experiments
We arranged four printing experiments from mid-Sep to mid-Oct.

The Assembly of the Truss Printer
1st trial 9/17
Experiment Purpose:
1. To verify whether the materials and proportions can be smoothly printed
2. To verify whether the designed shape is suitable.
2st trial 9/29
Experiment Purpose:
1. Verify that the selected concrete material has good strength after printing
2. Reprint the No. 1 part, and the new No.6
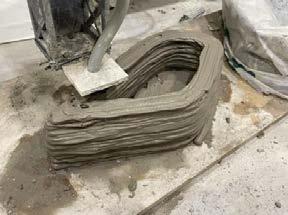
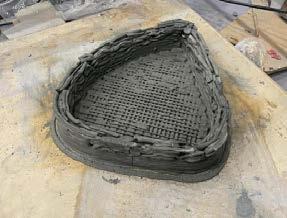
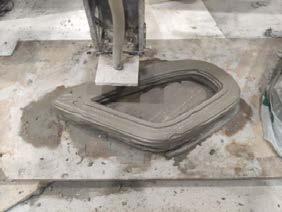
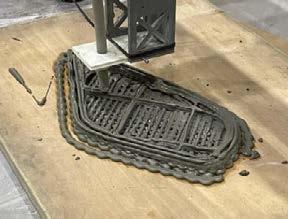
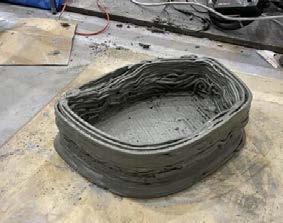
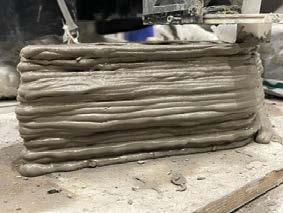
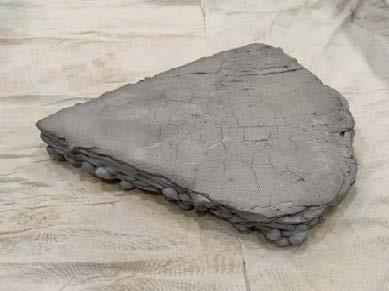
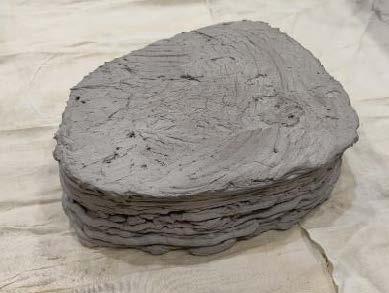

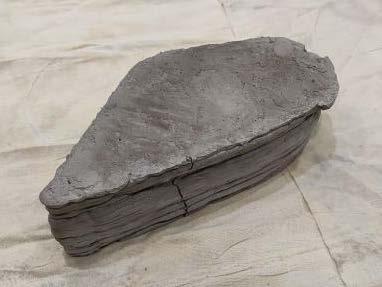


Conclusion and Future Studies
This project conducted four phases of concrete printing experiments. It can be clearly seen that the printing effect has improved. Eventually we got 6 printed seatts and by the last two units, the printing results were relatively perfect.
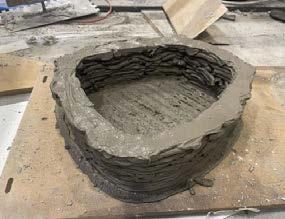
3st trial 10/10
Experiment Purpose:
1. Beautify the printed product after flipping
5.1 Conclusion and Summary
1. The material currently used in the experiment is glass fiber reinforced concrete. Other materials include silicate cement, nanoclay cement, foamed concrete, lightweight aggregate concrete and alkali-activated concrete. Considering the availability of materials, we can continue to try selectively in future experiments and obtain the appropriate component ratio through accumulated experience.
2. The truss-type printing equipment currently used is subject to many restrictions in terms of printing height, accuracy and flexibility. In the future, it is possible to consider adding a height adjustment device, or converting the robotic arm into a 3D printing robot, and using a printing nozzle with adjustable extrusion diameter to further achieve refined control of concrete printing.
5.2 Future Studies
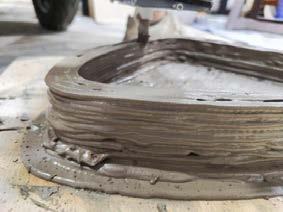
2. Print the rest components This project conducted four phases of concrete printing experiments. It can be clearly seen that the printing effect has improved. Eventually we got 6 printed seatts and by the last two units, the printing results were relatively perfect.
Domestic universities started research in this area relatively late. There is still a big gap from the actual application in building construction. It can be truly industrialized until the technology and process mature and the cost of mechanical materials is effectively controlled.
References
[1]Yuan Feng. From digital programming to digital construction[J]Times Architecture 2012
[2]Zhang Dawang, Wang Dongmin. Progress in 3D printing concrete materials and concrete construction technology[J] Silicate Bulletin, 2015
[3]Wang Ziming, Liu Wei, 3D printing technology and its application in the field of architecture. [J] Concrete World, 2015
[4]Yuan Feng, Ge Lifeng, Han Li, From Digital Construction to the New Material Era[T, Urban Architecture, 2011
Nozzle
Other works-Urban Renewal in Zen Lane, Nanjing
Internship at TM Studio
Date: Jul/2024
Instructor: Tong Ming, Ren Guang
Work: Render, Case Studies and Construction Drawings


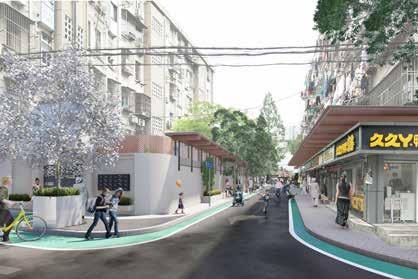
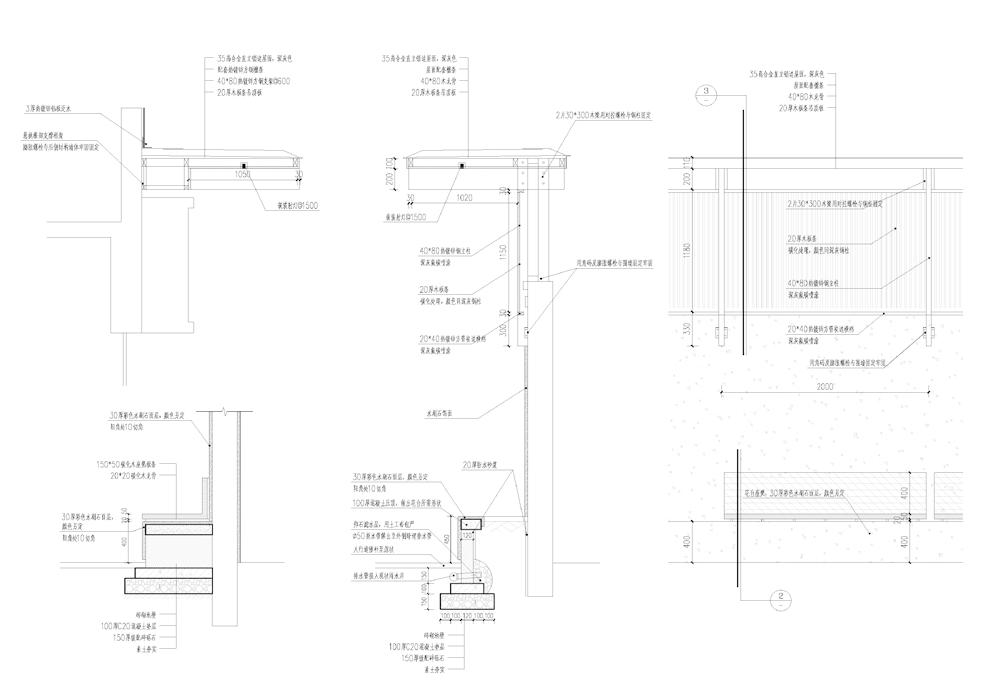
Other works-Renovation of Resident of Chuin Tung, Nanjing
Internship at TM Studio Date: Jul/2024
Instructor: Tong Ming, Ren Guang
Work: Render, Plan Drawings
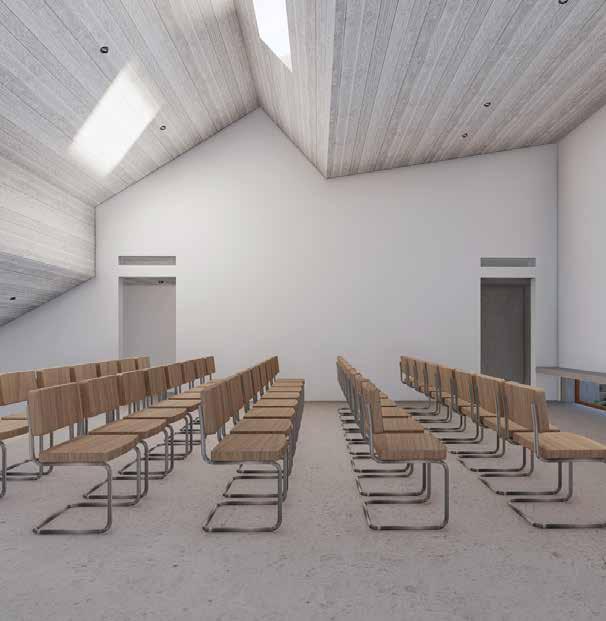
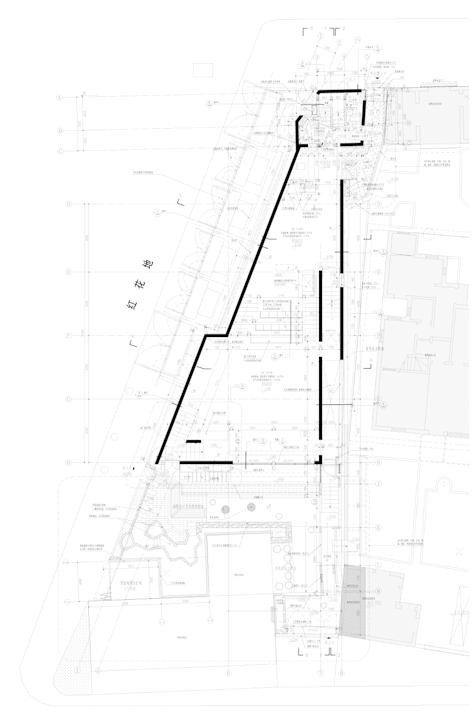
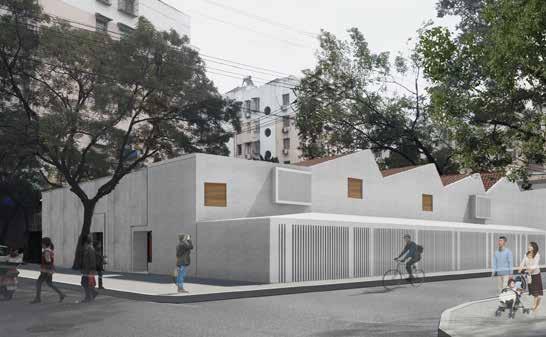
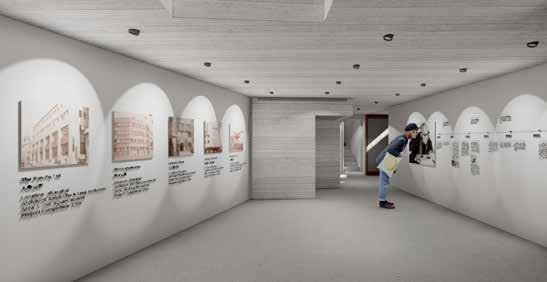
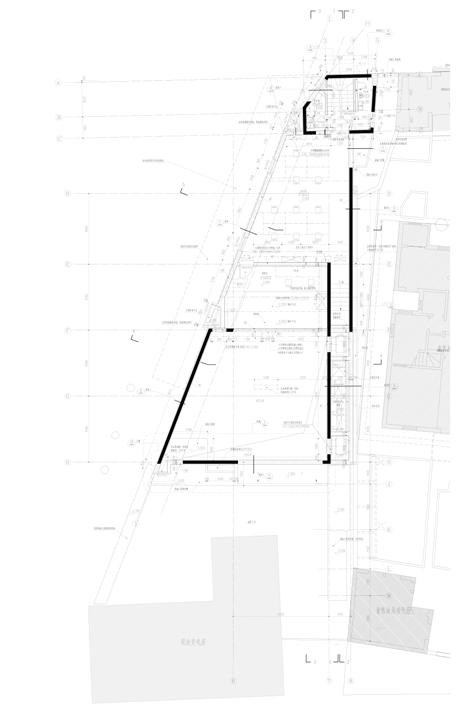
Art & Media-Photography & Spatial Cogition by Gesso 2022 summer school|individual work
Instructor: Zhang Lei
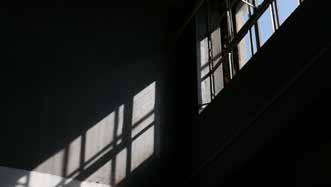
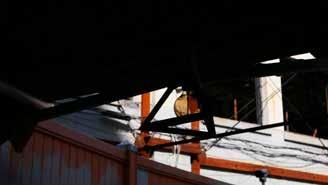
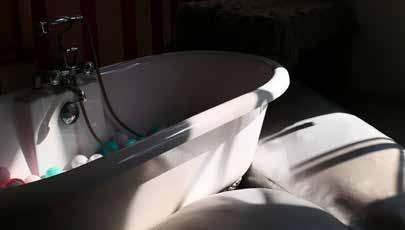
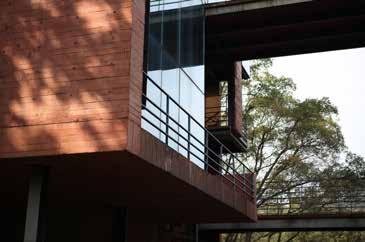
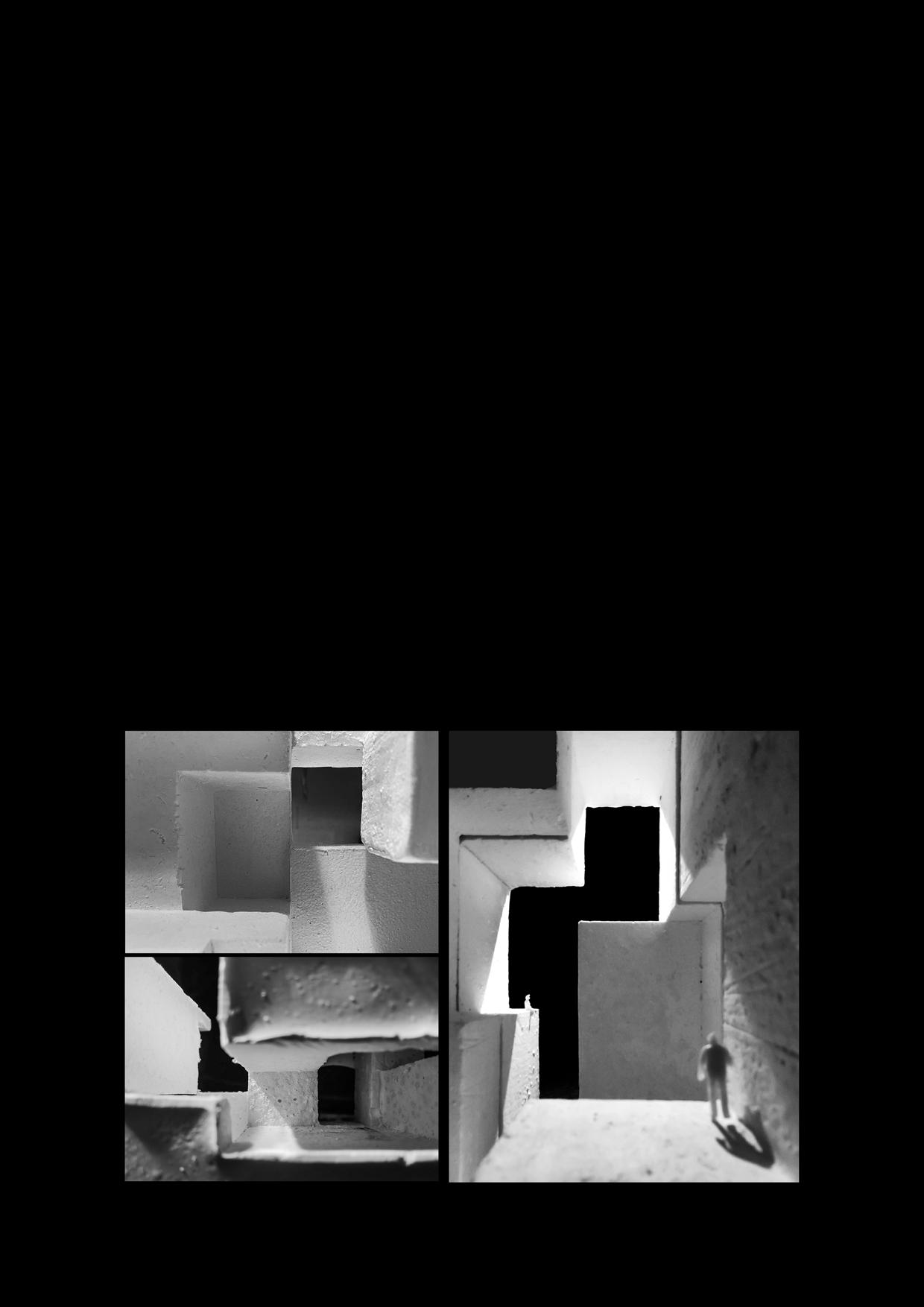
Other works-Surveying & Mapping
& Mapping
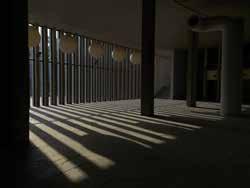
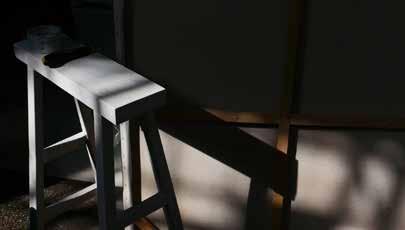
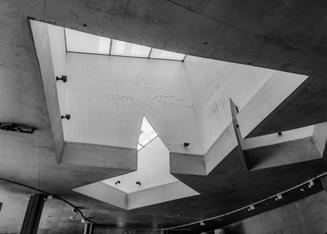
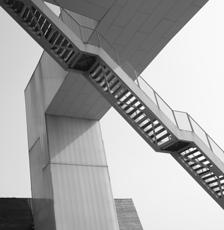

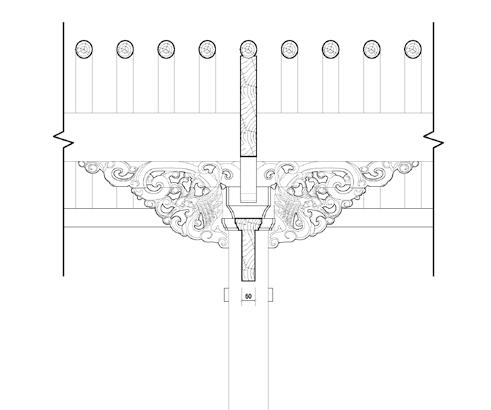
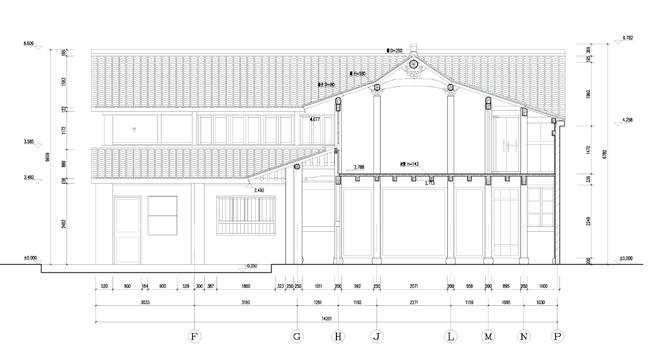
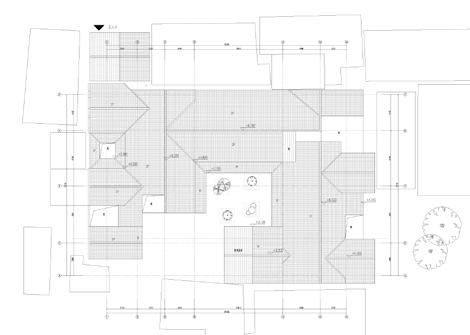
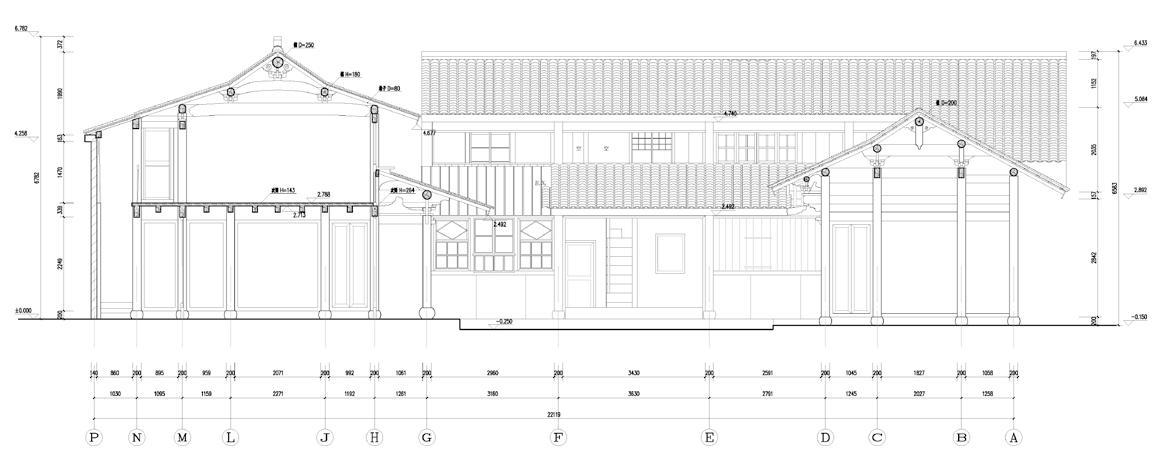
Surveying
of Chinese Traditional Courtyard House in Tiantaishan, ZheJiang Province
Group work with Wu Yangxiao, Yang Jianmin Instrucror: Shi Fei