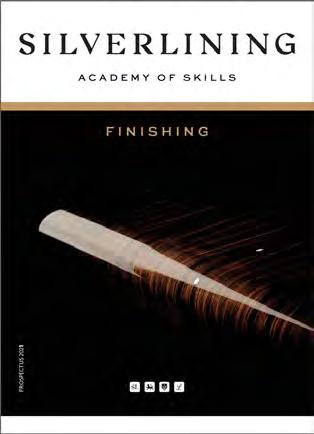
17 minute read
News
Silverlining launches Academy of Skills
Distinguished Wrexham-based furnituremaker Sliverlining has launched its own Academy of Skills, a high-level training programme teaching craftsmanship techniques in furnituremaking.
“We are now recruiting the first cohort to join the Finishing programme, starting in the autumn of 2021,” says Silverlining founder, Mark Boddington. “The course includes learning about traditional and modern wood finishes, preparation of wood and metals, application of
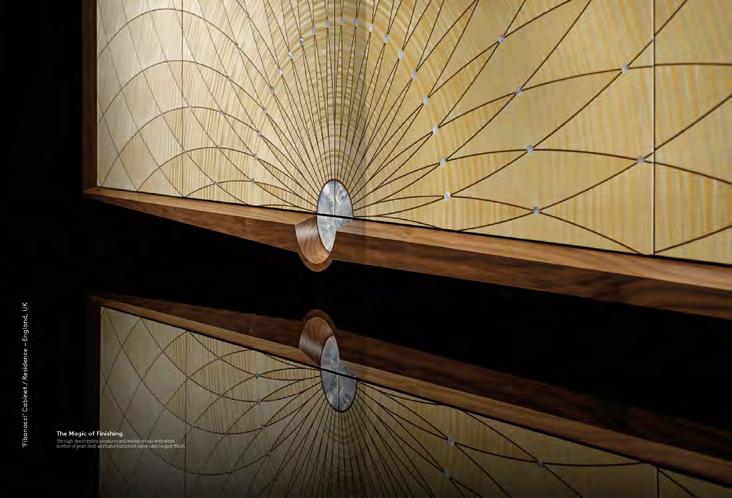
metallised, clear and coloured lacquers, polishing lacquers and metals, dyeing and staining woods and applying oils and waxes.
“The training is suitable for anyone who has an interest in designing or practical skills, is good with their hands or has creative flair,” says Mark, “and is open to school leavers, graduates and career changers, regardless of background, education, or experience.”
Candidates can view the prospectus, register interest or apply online at https:// silverliningfurniture.com/careers/academyfinishing. In addition, the business has an array of additional roles which it is currently advertising due to growth.
www.silverliningfurniture.com/careers
New zone at Bed Show to feature bed and mattress components
Join hundreds of bed buyers and specifiers for two days of beds as online registration opens for the 2021 Bed Show, which returns following a year’s break to Telford International Centre on 21st-22nd September 2021.
Organised by the industry trade association, the National Bed Federation (NBF), the only bed-specific exhibition in the UK promises to be another insightful outing for visitors, with all the big bed brand names in the industry exhibiting – including Airsprung, Breasley, Harrison Spinks, Hypnos, Relyon, Sealy, Silentnight and Sleepeezee – plus many smaller, niche members. New for 2021, the Bed Show’s Supplier Innovation Zone will feature well-known names in bed and mattress components such as Apropa, CPS Group, Enkev, John Cotton, Handy, Leggett & Platt, Maes Mattress Ticking, The Vita Group and Wolf Components.
Around 1500 people are expected to visit the show, and once again there will be complimentary refreshment vouchers courtesy of Airsprung, Bekaert Deslee, John Cotton and Silentnight. The organiser is hopeful the Gala Dinner and 2021 Bed Industry Awards ceremony, sponsored by The Vita Group, will go ahead on the night of the first day of the show.
NBF executive director Jessica Alexander says: “The Bed Show is the only place to see so many UK and Irish bed manufacturers all under one roof, with visitors coming to source new products, see the latest innovations and build new relationships. We really look forward to being able to come together again in celebration with everyone in the bed sector.”
www.bedshow.co.uk
Gowercroft wins top award
High-end timber window and door specialist Gowercroft Joinery has won the Family Business of the Year category of the 2021 Midlands Business Awards. Marking its 15th year, the award celebrates the entrepreneurship, innovation and business growth of the region’s most dynamic and successful businesses across a range of industries and sectors. As part of its ambitious plans for the future, Gowercroft Joinery is now moving to the next stage of its growth strategy by actively seeking new partners to grow its network of regional dealers.
Survey says UK REACH is threat to UK manufacturing
The latest survey of British Coatings Federation (BCF) members reveals that UK coatings manufacturers are increasingly concerned about the effects of the new UK chemical regulations. Almost 80% of respondents believe UK REACH will impact negatively on their businesses, with the fear that there will be a significant reduction in the portfolio of available chemical substances in the UK compared to the EU, and 67% of respondents fear higher costs in the future as suppliers pass on the costs of complying with UK REACH.
Strong half-year results
Howdens achieved a strong first-half performance, ahead of expectations, with group revenue of almost £785m (2020 – £465.0m, and 2019 – £652.6m). Howden Joinery UK depot revenue increased to approximately £764m, up +19.8%, compared to the first half of 2019. Despite competition and economic uncertainties, Howdens says it remains cautiously optimistic for the second-half period, and that it remains confident in its business model for the future. Accordingly, it is currently expecting pre-tax profits of around £300m for 2021 as a whole.
Online boosts sales
Manufacturer and online retailer Funky Chunky Furniture has doubled its workforce and turnover, as it celebrates its most successful year to date. It now employs 48 people at its workshop, across roles ranging from production, dispatch and customer services to design, marketing and administration. Its leadership team is now looking to the future and ways to capitalise on the ongoing growth. The business plans to expand its workshop and team further, enabling it to introduce new furniture lines as well as increase the volume of production for its shelving and mantels.
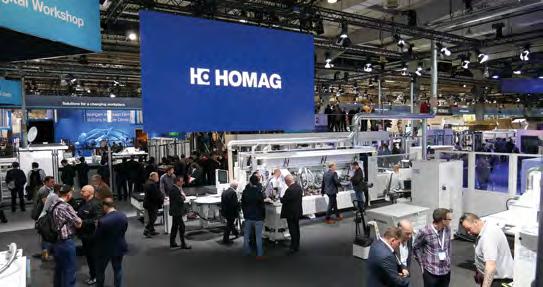
Working with one of the world’s premier woodworking technology companies surely represents a tremendous opportunity to many working across the furniture, joinery and woodworking industry, states Homag, which has a number of positions it is seeking to fill with the right candidates.
Widely recognised as setting impressive standards of technical innovation and well as being as an outstanding and progressive employer, Homag’s technologies drive many world markets, including those of furniture, joinery and woodworking.
With an open mind and the courage for new ideas, Homag
Opportunities to join the Homag team BFM MD to step down The MD of the British Furniture Manufacturers (BFM), Nick Garratt, has announced his intention to step down from the role at the end of the year. Nick informed the national trade body’s management board of his decision in June. As colleagues paid tribute to the “enormous impact” Nick has had on the BFM during his tenure, the search has now begun for the right candidate to take his place. BFM chairman Brian Ahern says: “As we look ahead to a postpandemic world, the BFM is in a strong position – and Nick has had consistently develops new a huge part to play in navigating the association through these difficult approaches – including numerous times. Nick will be a very hard act world-first solutions – enabling its to follow. The board and members customers to be more efficient in of BFM all wish Nick well for the their manufacturing processes. future.” Current open positions at Homag include project manager, field Nick adds: “It has been a privilege to be part of BFM and to serve the association as MD over the last service technicians, and hotline three years. I am very proud that support. “Take advantage of the BFM is in a strong position as I opportunity to enhance your prepare to step back from day-topersonal career and create with day operations and enjoy more time with my family.” Brian Ahern adds: Homag – the closing date is 30th “We are very keen to hear from August,” states the business. potential candidates for the role of Apply by emailing a CV to info-uk@homag.com. MD at BFM. We will be drawing up a job description, and welcome initial expressions of interest for this role.”
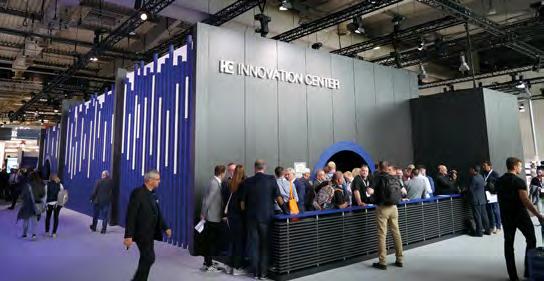
BWF launches 2021 awards
The British Woodworking Federation (BWF) is calling for entries for its prestigious BWF Awards, celebrating outstanding achievement, skills and talent from across the woodworking and joinery sector. This year marks the 13th anniversary of the annual awards, and both companies and individuals are encouraged to enter. There are six categories to choose from, including Woodworking Project of the Year, Product Design in Wood and Rising Star of the Year. “We’re delighted to be bringing the woodworking sector together once again to place a spotlight on the technical innovation, creativity and efficiency that make ours such an exciting field to work in,” says Helen Hewitt, chief executive of the BWF. The categories for this year’s awards, which are free to enter, are: Woodworking Project of the Year Award – sponsored by W Exhibition & The FIT Show; Product Design in Wood Award – sponsored by Teknos; Woodworking Apprentice of the Year Award – sponsored by CITB; Rising Star Award – sponsored by Dixon International Group; Health & Safety Hero Award – sponsored by Arnold Laver; and the Process Efficiency Award – sponsored by PIB Insurance Brokers.
www.bwf.org.uk/awards-2021
Weinig UK declares first Connect event a success
Weinig UK’s new hybrid in-house event series kicked off in July with The Potential of Powermat. The three-day, Covid-secure event, which took place at Weinig UK’s state-of-the-art showroom in Abingdon, offered new and existing customers an opportunity to see a wide range of moulders being demonstrated, and experience the latest technology first hand.
Upon attending the event, a representative from Carr Portable Buildings said: “We’ve truly valued the opportunity to have one-onone time with Weinig’s specialists. We were able to see a range of different models up close, giving us a better understanding of the technology available to us, and we had demonstrators to showcase the running of the machines, the tooling and special features. It was certainly time well spent, and it was great to be able to see so many fully accessible machines under one roof. We really had Weinig’s dream team looking after us.”
Malcolm Cuthbertson, MD of Weinig UK, adds: “Weinig UK’s first Connect event has proven to be a great success, with many businesses – some new to Weinig – attending the event. Many visitors came for a specific purpose, some to explore the Powermat range for the first time and others to add to their existing fleet.
“Each visit was tailored to suit the company’s needs, and each demonstration was carried out to specifically highlight the purpose of the visit. Feedback suggests this tailored approach really has added true value to our Connect series, and we’ve really enjoyed connecting with industry once again.
“We’re now looking ahead to our second event, Laser vs Glue, in September, where visitors can explore our Holz-Her edgebander range and our unique Glu Jet system with our experts.”
Weinig UK will hold its second in-house event, Laser vs Glue, from 14-16th September 2021. To confirm a place, register at www.holzher.co.uk.
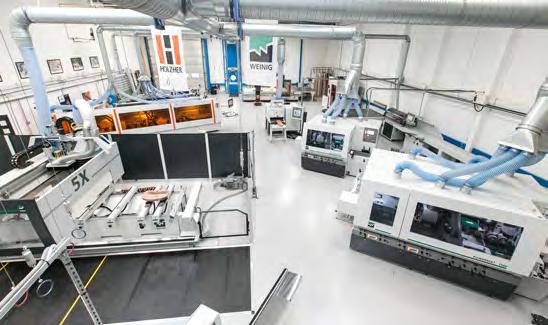
Growth at Advanced Machinery Services fuels recruitment drive
Advanced Machinery Services (AMS) has over 13 years’ experience in providing machinery and spare parts for production facilities and operations of all sizes. The Skeffington-based company promises that no matter what size or type of production facility is being operated, it can find exactly what its customers need – every step of the way.
Over the last decade, Advanced Machinery Services has forged a strong reputation for providing machinery and spare parts for production facilities and operations of all sizes, from small workshops to major manufacturing operations.
Today, the business enjoys positive relationships with manufacturers of worldrenowned machinery, helping to support them with both the supply of woodworking machines and equipment, high-quality spare machinery parts as well as servicing and rebuilding of ageing machinery.
With a high demand for its highly-thought services, the company is currently looking to recruit electrical and mechanical engineers based throughout the UK. The wide-ranging role includes supporting the company’s skilled and experienced staff with the service, maintenance and repairing of woodwork machinery. The work will be primarily based from home, with co-ordination from its offices in Skeffington – the successful applicant will join the AMS field team working across the whole UK, and possibly overseas.
For further details of the opportunities with AMS, visit https://www.advancedmachinery. co.uk/info/index.asp?page=vacancies-231

Combilift’s 60,000th truck delivered
Irish manufacturer Combilift recently marked a further milestone when its 60,000th unit came off the production lines at the company’s HQ in Monaghan and was shipped to the other side of the world. The customer taking delivery of this special forklift is Metroll, a leading Australian manufacturer and supplier of steel building products including roofing, cladding, rainwater, structural and fencing.
Metroll has branches across the country, and the new Combi-CB3000 will be a further addition to its fleet of 13 Combilifts that are operating throughout the Metroll Group, with another 10 already on order. These range from 3t multidirectional units to a customised 10t model.
Combilift number 60,000 will be working at the site in Toowoomba and has been fitted with features such as a 4.9m triplex mast with a 3050mm spreader to safely and easily manage the long loads that are typically handled by Metroll.
According to Metroll’s operations manager Vic Josephs: “Like most businesses we are very busy and we’re also growing at a significant rate, so space has become a premium resource. With this unit we can utilise our space more efficiently whilst at the same time operating safely. Safety is of paramount importance. This forklift allows our machinery to get into tighter spaces and for us to space our racks more closely together to maximise factory floor space.”
Combilift CEO and co-founder Martin McVicar comments: “This is a great achievement for Combilift, particularly as almost every truck we manufacture is a one-off, designed for specific and individual requirements. There are very few other companies, if any, that can offer this level of customisation whilst manufacturing in such volume.
“The first half of this year has been by far the best in our 23-year history for the number of orders we have received – not just for Combi-CB models but across our complete product range.”
Chris Littlewood, country manager of Combilift Australia, says: “The Combi-CB 3t model is the most popular unit in the Australian market and accounted for 50% of the machines we sold in the year ending March 2021. So, we are particularly pleased that it is one of our customers in this country that has been able to receive this landmark machine.”
Following the successful collaboration with Metroll in Australia, Combilift now also supplies its trucks to the company’s California-based operations, too. “We have often found that a recommendation from one country leads to sites elsewhere adopting the same materialhandling processes with our products,” says Martin McVicar. “So we’d like to congratulate Metroll on taking delivery of our 60,000th truck, and thank them for their continued support over the years.”
www.combilift.com/60000
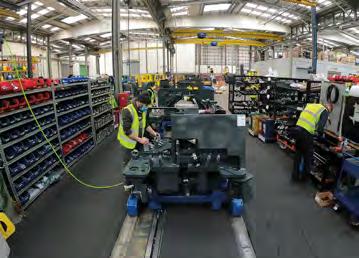
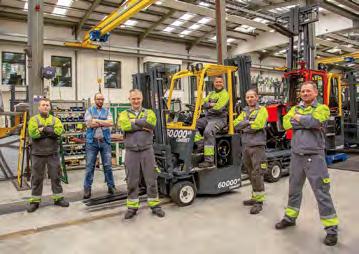
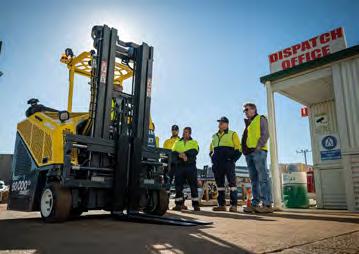
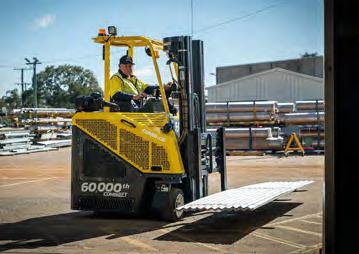
Blum records €2.37b turnover YE June 2021
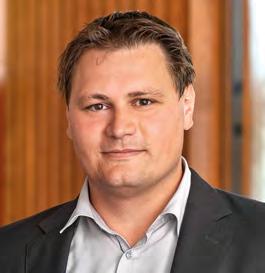
The family-owned business, based in Hoechst, Austria, has posted €2,376.75m in group turnover for the 2020/21 financial year (ended 30th June 2021), representing a growth in turnover of €470m (+24.7%) on the previous year.
The fittings specialist was able to achieve these positive results thanks to strong demand for topquality kitchens and furniture from consumers wanting to spruce up their homes. However, shortages in raw materials, especially in steel, have put severe pressure on supply chains.
The unforeseeable surge in demand for furniture caused by the pandemic has led to an above-average increase in turnover for the fittings manufacturer from Vorarlberg. “The crisis has prompted people all over the world to attach more importance to their homes. At the same time there has been a shift in private consumption – away from traditional leisure time activities to investments in home improvements, for example in kitchens and furniture,” says Philipp Blum, MD of Blum, explaining the development.

Development of international markets
Although furniture stores had to close their doors for long periods of time during the lockdowns, the demand for furniture and interior refurbishments increased dramatically all over the world. Western Europe recorded strong growth, particularly in Italy, France, the UK and Germany. Major increases were also posted in Eastern Europe, for example in Poland, Russia, the Czech Republic and Turkey. Business also went well in North America. Sales figures also rose in Asia and Oceania, with China again contributing significantly to the business’ results. Furthermore, last year proved a positive one for Blum in Africa, South America and the Near and Middle East.
The fittings specialist delivers to customers in more than 120 countries. With the foundation of Blum Indonesia in this spring, the company has 33 subsidiaries and representative offices worldwide. Philipp is convinced that the company’s international orientation and policy of having local
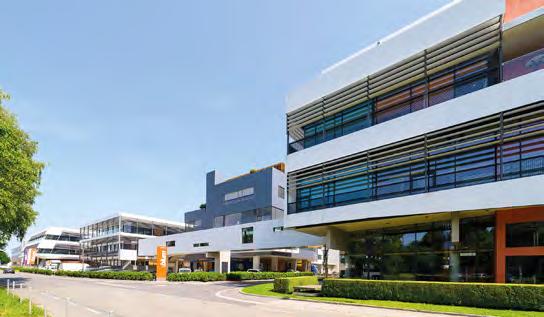
Philipp Blum
organisations and sales teams on site close to customers was very important during the pandemic.
The distribution of Blum’s turnover by region remained the same as in the previous year. “We still achieve most of our turnover, that is to say 44%, in our domestic market, the EU,” comments Philipp.
With a share of 13%, the US is the company’s largest single market – other markets worldwide account for 43% of total turnover.
Plant 2 in Hoechst, head office of the Blum Group
Employees are key success factor
“We’re delighted with the demand for kitchens, furniture and, consequently, Blum products, but it poses extreme challenges, especially in the field of production,” points out MD Martin Blum. The reliable and timely supply of its products to customers is a top priority for the long-established company from Vorarlberg. “We owe our thanks to our employees. It’s thanks to their commitment and flexibility that we’ve been able to deal with this extraordinary year,” underlines Martin.
At year-end, Blum employed 8778 people worldwide, 6551 of which were based in Vorarlberg. 371 new employees were recruited in Vorarlberg last year, and 429 worldwide.
Martin Blum
Blum continues to attach great importance to its apprenticeship programme (training young people to become specialists). The goal is to counteract the shortage of skilled professionals and be well equipped for the future.
A total of 93 new apprentices will start their vocational training with Blum in Vorarlberg on 1st September, eight new trainees will join Blum USA, and two Blum Poland.
The impact of strong demand
The high market demand in the kitchen and furniture industry, as well as in other industries, has led to shortages in raw materials such as steel. “Unfortunately, our customers are currently also having to wait longer for our products,” points out Martin. “Only by adjusting some delivery times have we been able to meet the rapid growth in market demand,” he adds.
“The price of steel has almost doubled, while plastic, packaging, zinc and aluminium have also been subject to enormous price hikes. We see a similar situation in the field of transportation. The whole international supply chain is under pressure. In some cases, overland and ocean freight costs have increased dramatically.
“The current situation is very challenging, but we’ve managed to create a certain level of stability thanks to our longstanding partnerships with our suppliers,” says Martin with conviction.
Innovations safeguard the future
Despite the turbulence of the last financial year, Blum is firmly convinced that continuous innovation in products and services will safeguard its future. The family-owned business used digital technologies to stage Blum CONNECTS, a hybrid event to mark interzum. The manufacturer presented its innovations to customers all over the world using a combination of local events held at market organisations and virtual experiences.
The first customers are now using Revego, a pocket system for closing off areas with large doors. It offers individualised design solutions for small and large spaces. Minimalist design can also be implemented with ease with Aventos HKi, a fitting that is hardly visible, even when the wall cabinet is open. Furthermore, Blum has also responded to the trend towards dark and metallic surface finishes. “We want to enable our customers’ design ideas and help them meet the demand for more individuality in kitchens and furniture by providing suitable fittings solutions,” reports Philipp.
Looking ahead
The managing directors believe that international supply chains and the supply of raw materials will remain severely impacted for some time. “We hope that the high vaccination rate will avert the need for further lockdowns,” says Philipp.
How long the home improvement trend and shift in private consumption will last is not clear. But one thing is certain for Philipp: “We’ve benefited from the experiences that we as a company have gained over the last one-anda-half years. Digital technologies offer many opportunities, but they’ve also shown us that you cannot replace face-to-face conversations and an exchange of ideas.” For the company as a whole, it is crucial to remain a trusted partner to its customers worldwide.