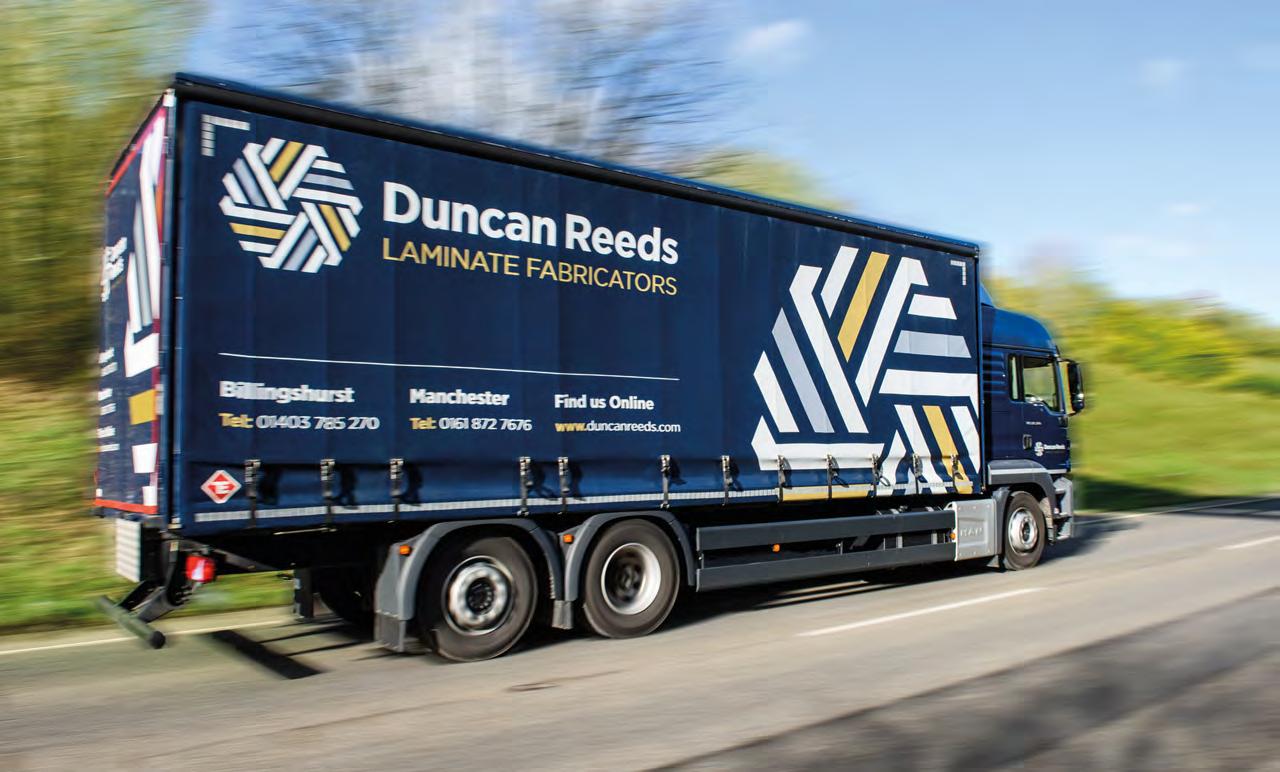
13 minute read
Installations
Duncan Reeds continues to opt for Homag quality and service
One of the UK’s leading fabricators of bespoke laminated products, Duncan Reeds, has selected Homag once again as its preferred supplier of a new range of wood processing machinery.
The family business was established in 1989 and has since grown into a dynamic operation. It has two production facilities located in West Sussex and Manchester, with production and storage space of just over 70,000ft2. As part of expansion plans, the company is about to open a third production facility in Kidderminster.
Duncan Reeds produces a vast array of custom-made products for a diverse variety of businesses in the UK and overseas. Among other products, it is currently manufacturing tabletops, toilet and washroom cubicles, wall liners and protective hygiene screens for safeguarding people during the Covid-19 pandemic.
Before investing in the new range of machinery, Homag invited Duncan Reeds’ company directors to visit its headquarters in Germany to see the machines in operation. During their visit, the Homag sales team helped the directors to select the most appropriate machinery for their specific requirements and budget.
Commenting on the Homag investment, director Dean Harkess-Cowlyn says: “Investing in our plant is a vital part of our success. Our commitment to Homag ensures that we have the most up-to-date, leading-edge machinery to service the diverse requirements and demands of our customers. This helps us to maintain our position as one of Europe’s leading decorative panel suppliers, with the capacity to deliver superior-quality products and services.
“Quality and service are essential to our success – consequently, these two attributes are the most important factors we look for in our machinery suppliers.”
Ongoing investment in Homag Machinery
Remarking on the company’s continual investment in Homag equipment, Dean went on to say: “We first invested in Homag machinery in 2002, when we bought a top-end Brandt edgebander. Since then we have added over 20 more Homag machines including saws, CNC processing centres, throughfeed post formers and PU edgebanders.
“Our continuous investment in the most advanced and state-of-the-art manufacturing machinery demonstrates our level of commitment to both our customers and employees. It allows us to offer the highestquality product at the most competitive rates.
“For us, the reliability of the Homag machinery is due to its world-class German engineering. Along with their productivity features, we have found the impressive array of safety features on their machinery has continually improved.
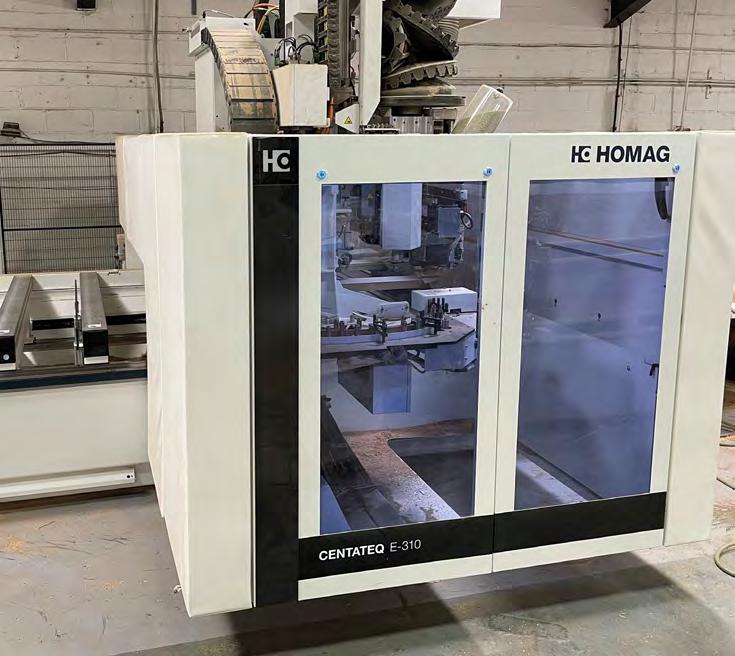
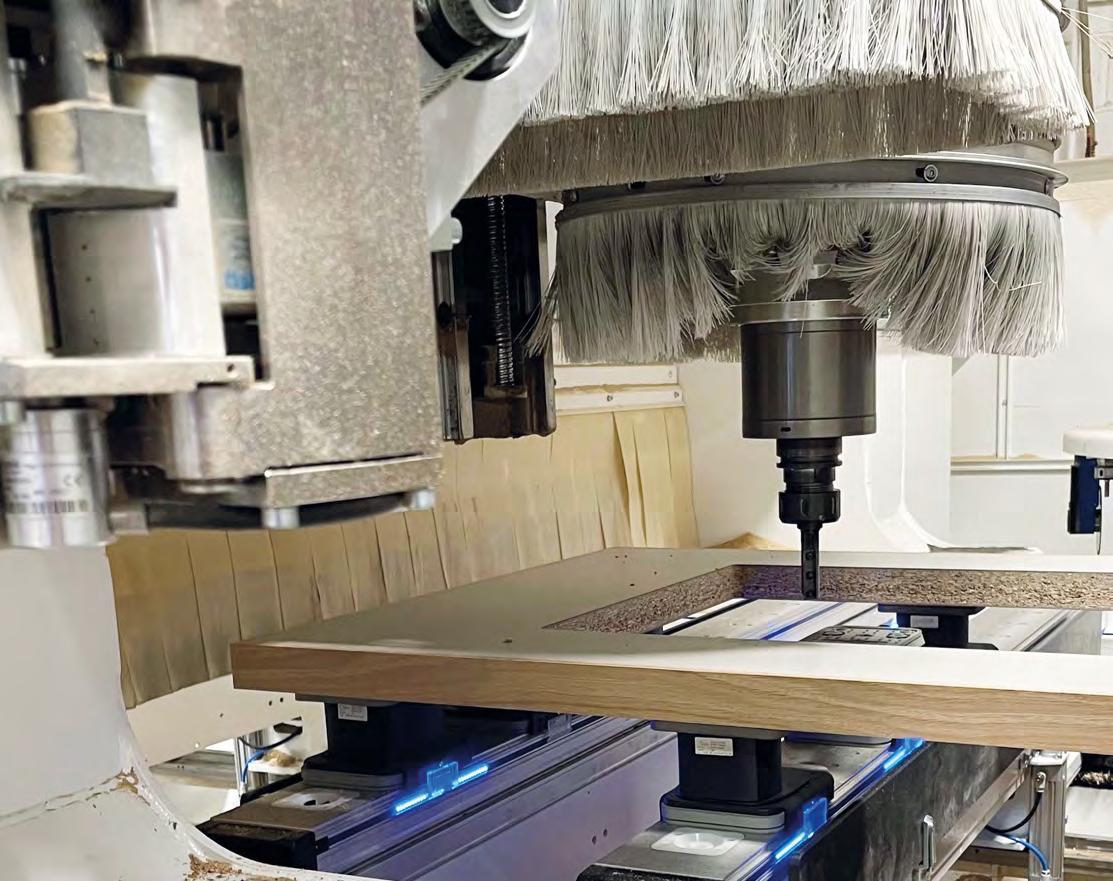
We now get fewer breakdowns, and the risk of accidents is minimal. What’s more, we have extended capacity to produce a very wide range of products more efficiently.
“Our most recent Homag equipment investments were for our head office in Billingshurst, West Sussex. These comprised of two Homag CNC processing centres – a fouraxis CENTATEQ P-110 and a CENTATEQ E-310. The latter machine was purchased to replace an old Homag BAZ 322, which was commissioned back in 2008. “With its airTec, zero-joint technology edgebanding unit, the CENTATEQ E-310 enables us to manufacture ABS-edged shaped panels seamlessly, with ease and efficiency. This helps to keep us at the forefront of modern panelprocessing supply. “Homag machinery gives us the ability to efficiently manufacture a diverse range of products using an extensive array of materials. This investment has facilitated YoY growth for the business, even in the middle of a global pandemic.
“Finally, we are delighted to say that our third factory will be opening in Kidderminster in the third quarter of this year. This facility will be equipped with five new Homag machines, which total nearly half a million pounds of investment,” concludes Dean. For more information on Homag’s machinery or software, contact Adele Hunt at Homag UK on 01332 856424.
www.homag.com
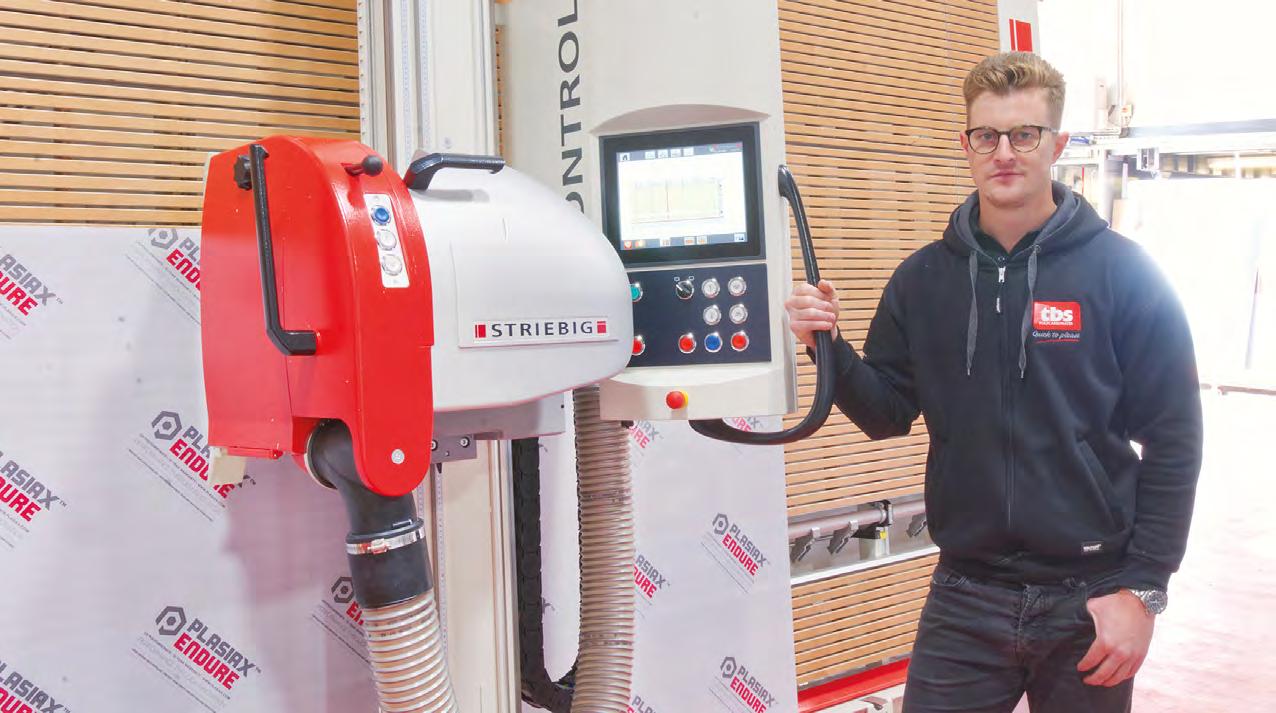
Cutting in Covid
The last 18 months have been a roller coaster for many businesses, with the industry having to adapt quickly during a time of economic uncertainty. For many, this has resulted in temporary or even permanent business closures but for TBS Poly, it’s been its busiest on record, as it’s continued to supply and fabricate plastic sheet materials to hospitals, prisons, large merchants and contractors throughout the pandemic. It’s this demand that has resulted in the family-run business investing in four new machines, including a new Striebig Control vertical panel saw from Leicester-based TM Machinery.
“Our previous Striebig vertical panel saw was 15 years old and, pre-Covid, it was running up to 12 hours a day, five days a week,” explains William Gresswell, Business Development at TBS Poly. “It’s safe to say it was the most-used piece of kit in our workshop, cutting on average three tonnes of sheet material each day – including Polycarbonate, Acrylic and Trespa, PTG, PVC, GLP, aluminium composite and laminate board – and up to 20 sheets at a time.”
But, when the country went into its first lockdown in March 2020, business was impacted immediately. “As our competitors shut down and the threat of material shortages turned into a reality, we decided to buy as much stock as we possibly could from our suppliers and stockists and ended up importing a continuous stream of material from over five countries,” reflects William. “I’m sure people thought we were mad but our gamble paid off. Demands meant that we were processing sheet material faster than we were able to offload it from our lorries. Demand for plastic safety panels, segregation screens and dividers skyrocketed. We went from cutting three tonnes of plastic sheet material a day to over 10 tonnes a day, 7 days a week on one 15-year old Striebig and it never let us down once. We were working it around the clock, only stopping for material change overs, and breaking material output records in the process. It was a true workhorse and it did us proud but it also made us reassess our business model.”
Whilst William admits orders for cut-to-size sheet materials have started to ease since the beginning of lockdown (but still remain considerably higher than previous years) ongoing plans to expand the company’s Hertfordshire-based facilities in order for it to hold up to three month’s-worth of sheet material at one time and house three newly-purchased three-axis CNC machines, are well underway and the need to invest in new technology is more necessary than ever.
William says, “Covid taught us vividly that with demand, comes supply. We needed a saw that could increase our throughput, streamline our
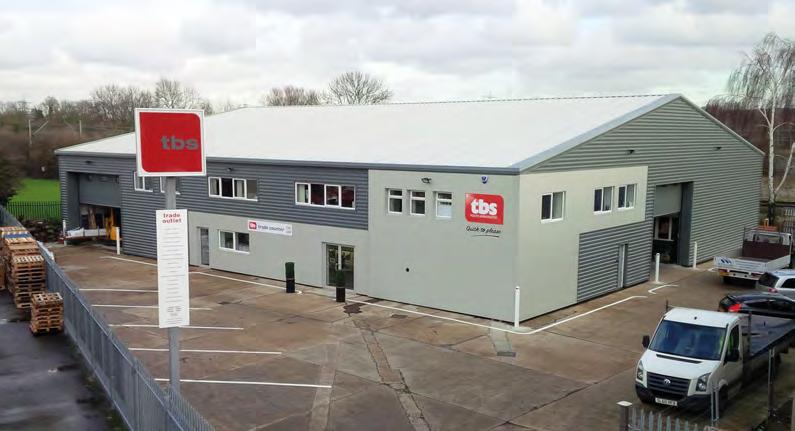
production and be more efficient in terms of material yield. We simply didn’t have the room to buy a second saw but we were in a position to upgrade to a newer, automated model. We didn’t need to look around. We’ve had a good relationship with TM Machinery for over 20 years – they service our machines every year and we trust them. We also know what we’re getting with a Striebig vertical panel saw: a robust machine that offers pin-point accuracy, guaranteed.”
The automated Striebig Control offered TBS Poly the perfect solution and, with no delays in shipments during the pandemic, TM Machinery were able to dismantle the old saw and install the new one in just eight weeks.
Thanks to its wealth of automated features – including fully automated cut cycle, automatic beam and saw head positioning for horizontal cuts and a new 12” touch screen computer, it has made TBS Poly’s cutting operation around 25% faster.
“As well as its handy standard features, like its laser indicator for horizontal cuts and digital measuring system, we also opted for automatic length stops (Electronic Positioning System). These really are worth the extra cost,” says William. “Once you’ve programmed the size of the panel, the stops automatically move into position. There’s no manual adjustment needed. It also lets you know if the stop has been knocked at any time during the handling process, saving you valuable time and material waste if something were to move accidently. Strip cuts have also been made easier and faster because of the strip cutting gauge and, with the saw’s computer able to save jobs and common cut sizes, repeating regular work has become much simpler, reducing set-up times by approximately 35%. The new Control also works efficiently with our Maxcut V2 cutting programme, which creates cutting lists designed around our stock sheets and off-cuts.”
William adds, “The new Control has definitely lived up to expectations and offers precise, accurate cuts. Features aside, confidence in the machine and its after-sales team always has a huge part to play in any purchase we make – it’s a big intangible benefit and one that we cannot afford to overlook. We have every confidence in our saw’s capabilities and that reflects in our level of customer service. Going forward, we want to be known as the go-to supplier of polycarbonates in the UK, increasing our stock levels and variety of polycarbonate that can be cut, shaped, edged and drilled before being shipped direct to manufactures and end-users. This will only be achievable with the best machinery in place and this is exactly why we’re continuing to invest in Striebig.”
www.tmmachinery.co.uk
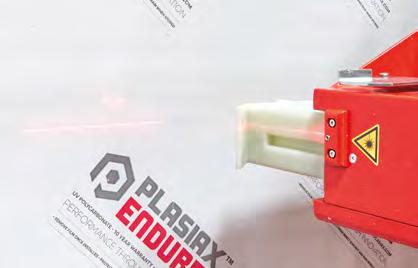
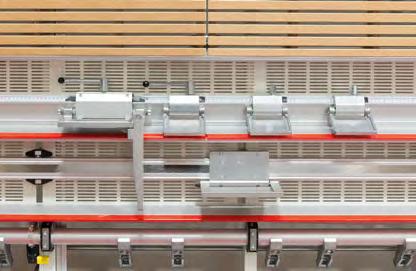

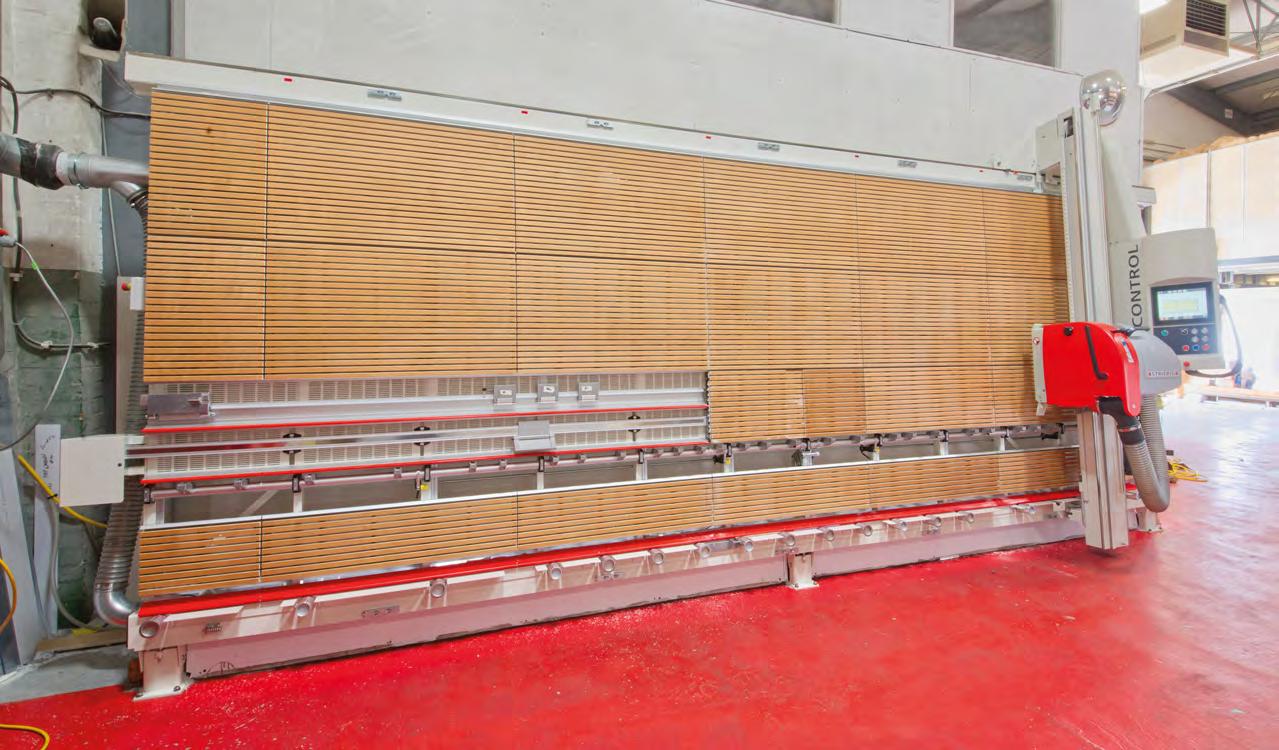
Multiple Salvador crosscuts for DWB
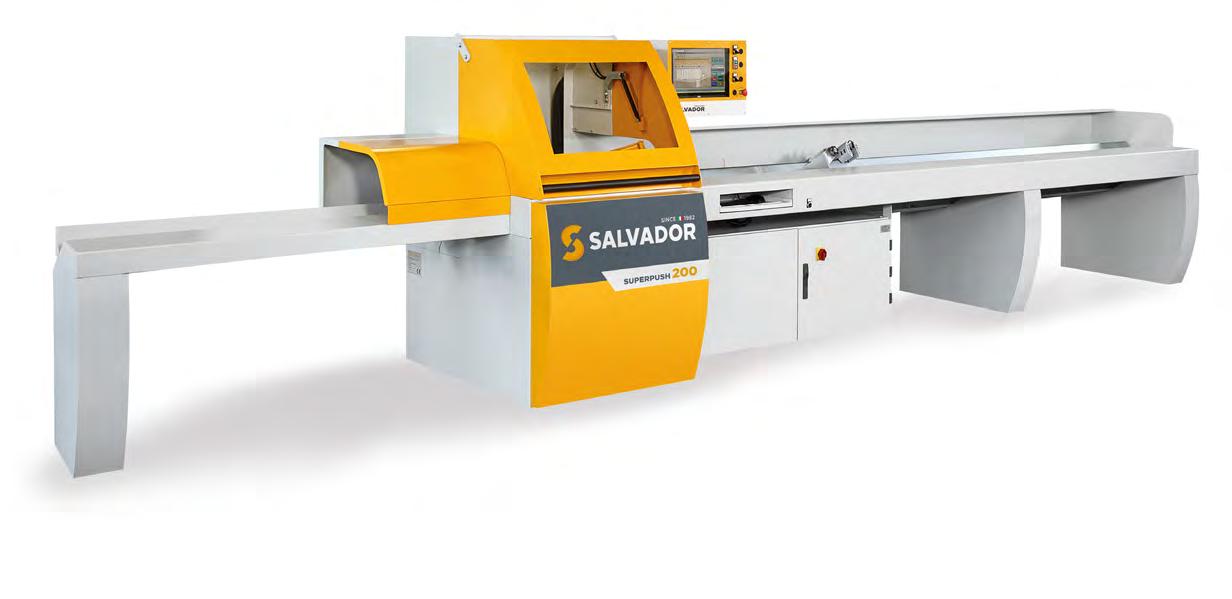
DWB Timber Engineering is a national group with facilities across the UK, including designated design and fabrication plants. Founded in 1986, the company has built an enviable reputation for high-quality roof trusses. F&JP visited Phil Daniels and his team in East Yorkshire, a year on from investing in a Salvador SuperPush 200 automatic crosscut saw from sole UK supplier Daltons Wadkin …
Many businesses in the construction and industrial sectors have adapted to keep up with the unprecedented demand brought on by the pandemic. Timber Trade Federation UK reported a 13-year high for timber imports in November 2020, reaching a volume of 1.08 million m3 . DWB had already highlighted the need to replace slow and aged machinery with a cutting-edge ‘smart’ machine to streamline its production, and machinery expert Daltons Wadkin was able to offer Covid-safe demonstrations and advice.
Speed, accuracy, safety, and saving waste were top of the list when looking for a new saw. Luke Laybourne, seasoned crosscut operator of 17 years at DWB, explains that the old saw was just too slow: “David Bell and Phil Daniels went down to an existing Salvador customer, and they said straight away, ‘that’s the saw for us’.”
Speed and accuracy of the Salvador SuperPush 200 is ensured with a heavy-duty infeed table, angled at 30° to keep the working material continually squared against the rear fence. The high-speed pusher can operate at up to 60m/min and can be regulated within each cutting list.
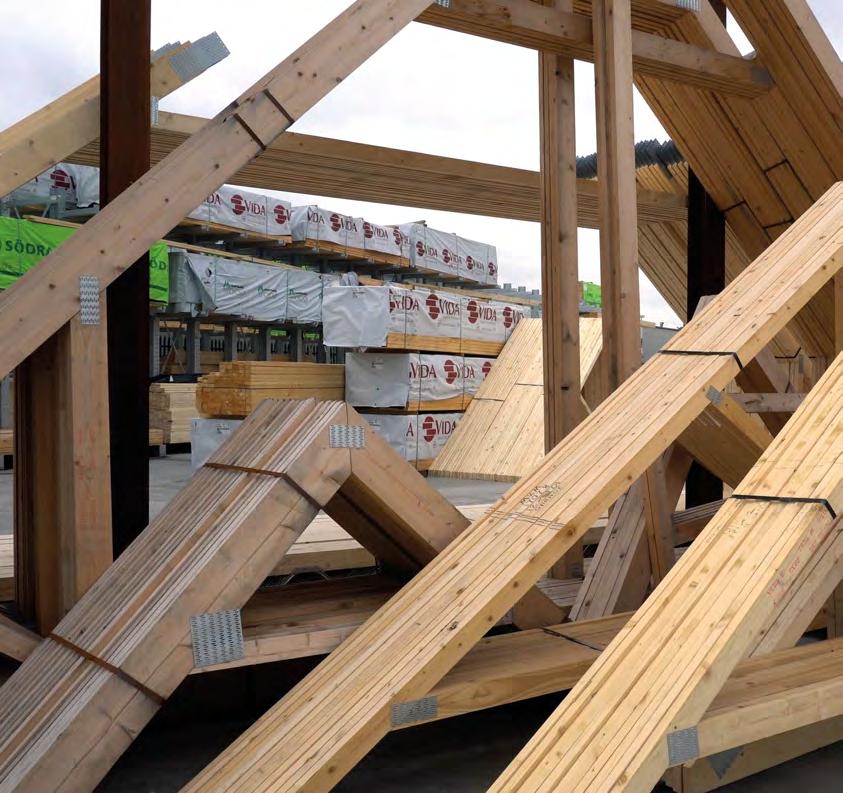
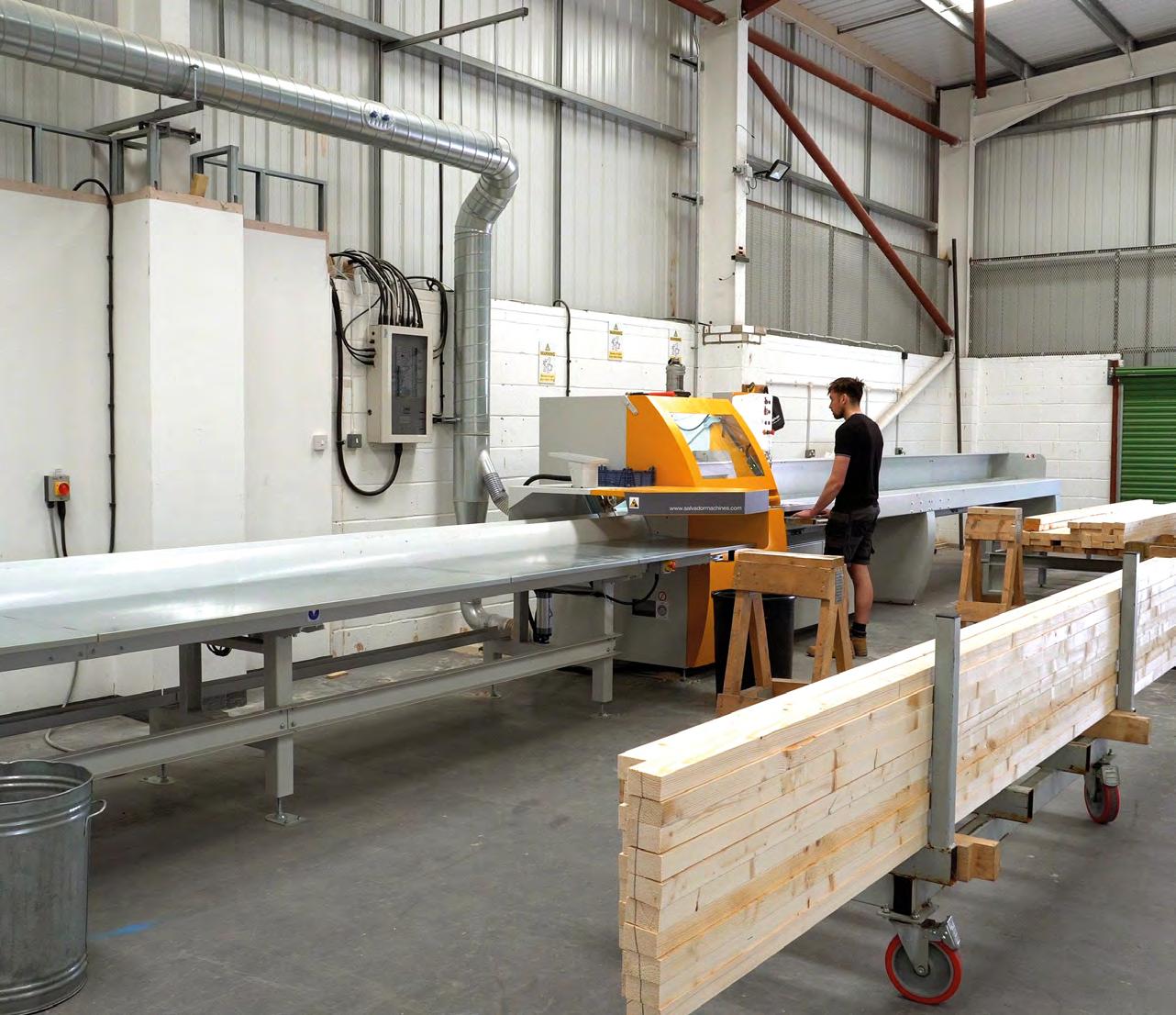
Luke enthuses: “Where a job used to take four days, we can do it in two. I’d say we’re cutting over +100% more.” The entire saw and pusher infeed are one single piece, resulting in an impressive accuracy of up to +/- 0.1mm.
Luke explains how the Salvador’s optimising algorithm “makes the job a lot easier” by working out the best yield from the timber, resulting in minimum wastage. The Salvador has reduced waste from 800mm per block to just 50mm for DWB: “We’ve got someone who comes in for firewood and he’s said ‘now you’ve got that new saw I’m not getting any waste’ – we always make a joke about it.”
Perhaps the most noticeable aspect of the saw for Luke was the safety, and ease of use for the operator. “Your hands are nowhere near the blade – not once have I ever felt unsafe,” he explains.
DWB is already looking ahead to streamline its other plants, starting with its Anglia branch, representatives from which visited Luke for a demonstration on the Salvador. “They felt like they picked it up straight away with just me explaining it. I just gave them my honest opinion of the saw – the answer was ‘yes’.”
The future for DWB looks exciting, and its forward-thinking approach has proved successful, with a +100% increase in production.
Daltons Wadkin looks forward to continuing to work with DWB Timber Engineering, as the company continues to innovate its nationwide facilities with smart machinery. For further information on automatic machinery, including the Salvador range, visit the supplier’s website.
0115 986 5201 info@daltonswadkin.com www.daltonswadkin.com
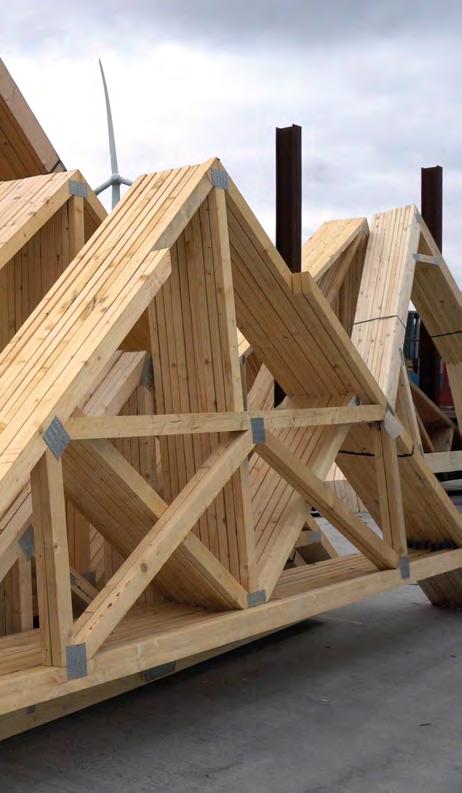
ZM 40 shredder in the Lerom production halls
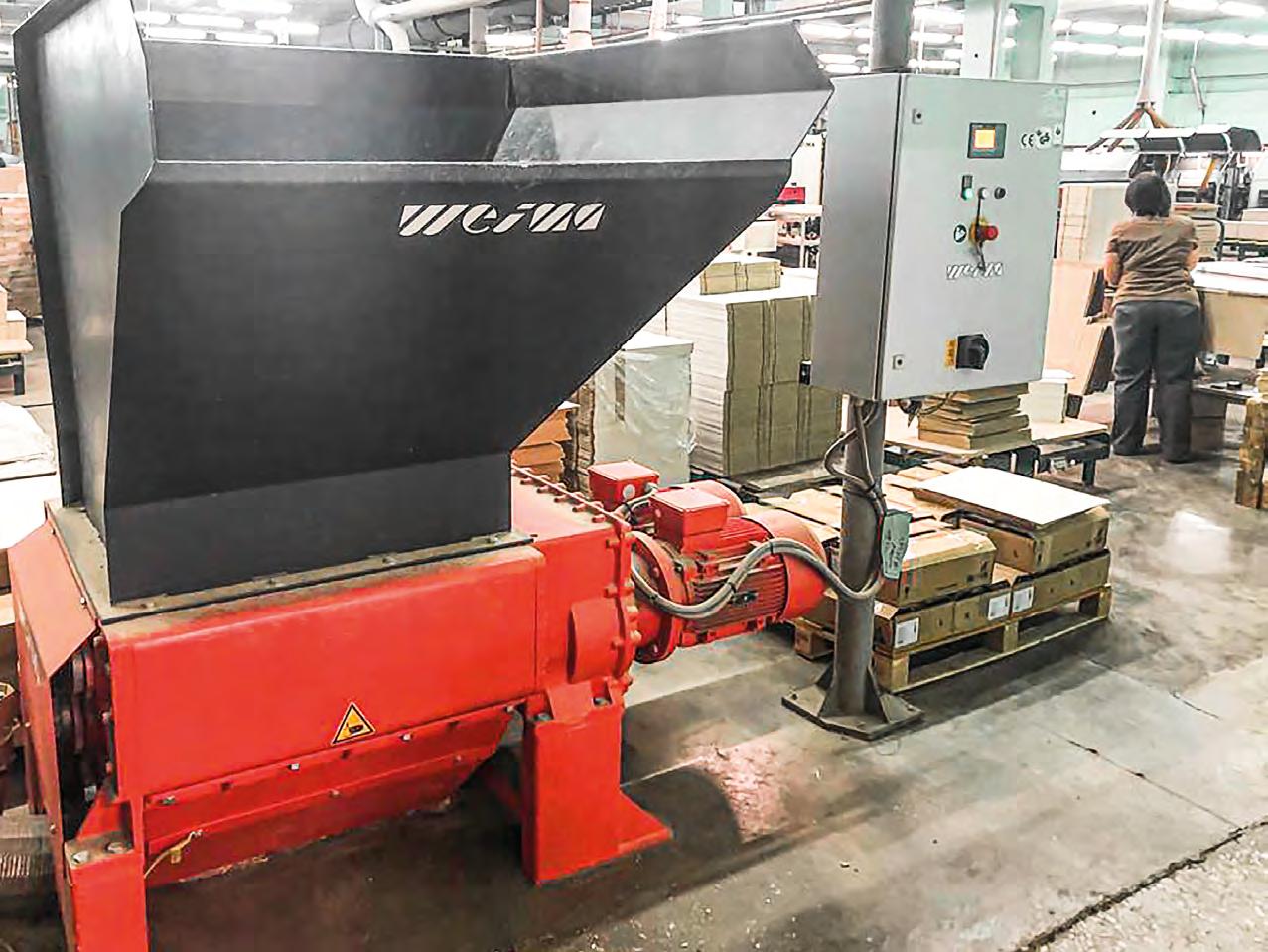
Long wood scrap for long winters
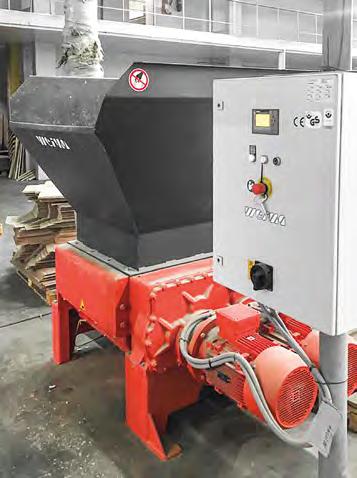
Russian furniture giant Lerom relies on a Weima ZM 40 four-shaft shredder to process more than 20m3 of woodwaste from production every day.
In 1997, the first piece of furniture was sold under the Lerom brand. Over the past 20 years, the furniture factory has grown to become one of the largest Russian furniture manufacturers. Across more than 100,000m2, 1100 employees design, plan, build and package the high-quality furniture pieces in Sarechny. The product range includes modular furniture for living rooms, bedrooms and children’s rooms. The quality brand is known not only in all regions of Russia, but also in surrounding countries.
20m3 of woodwaste per day
Every day, Lerom produces more than 20m3 of woodwaste. Not only does this take up valuable storage space, it also poses a fire safety risk and is extremely costly to dispose of. Together with its Russian partner SWEMA, Weima was able to offer an efficient, space-saving solution.
In 2020, a Weima ZM 40 four-shaft shredder was added to the furniture factory’s machinery. The shredder is used in three-shift operation almost around the clock, and shreds more than 7m3 of woodwaste per shift, including long and bulky sections of particleboard, MDF and fibreboard, but also solid wood scraps.
Weima ZM 40 – efficient shredding of bulky materials
The material is fed by hand via the generously sized material feed hopper. The woodwaste is shredded between the two cutting shafts and pushed through the cutting gap by two clearing shafts. The screen placed underneath defines the grain size of the shredded material.
Two powerful electric motors drive the four shafts. Due to the slow speed of approximately 25rpm, an extremely high torque is developed.
This enables a high throughput rate with low power consumption. The furniture company is particularly enthusiastic about the simple operation via Siemens PLC control, the high reliability of the shredder, and the high throughput.
Saving heating costs with woodwaste
The woodchips are then transported to the central chip bunker via an exhaust system. During the long, cold months, the shredded woodwaste serves as fuel for a woodchip heating system that heats the production rooms. The new recycling system enables significant cost savings – not only in waste disposal but also in heating the premises.
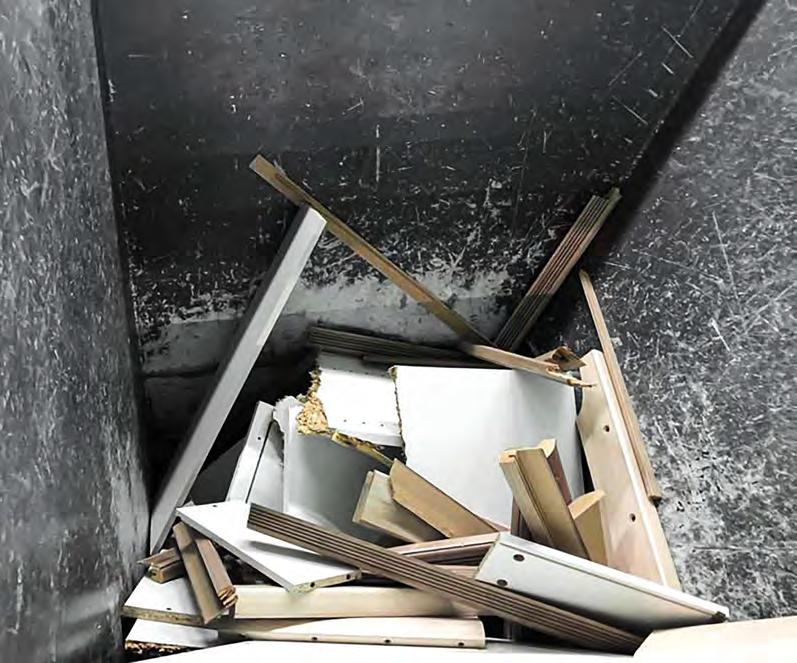
Weima has been manufacturing robust shredders, briquetting and drainage presses for the disposal and processing of all types of waste for more than four decades. Its machines include single-shaft shredders, fourshaft shredders, cutting mills, briquette presses, packaging and draining presses. The popular blood orange machines are used in the wood, plastics, paper, packaging, metal and waste-toenergy industries.
www.weima.com
Long and bulky wood scraps from particleboard, MDF and fibreboard, as well as solid wood cuttings, end up in the hopper of the ZM 40 shredder
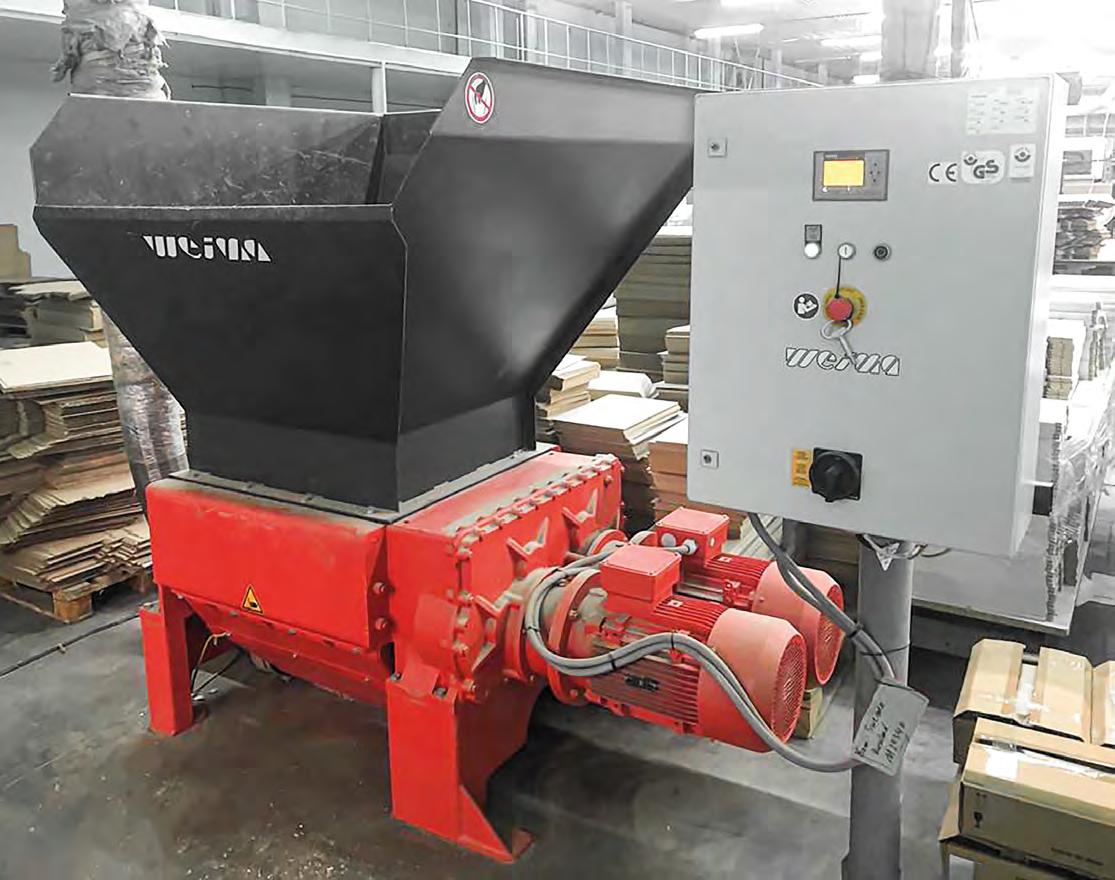