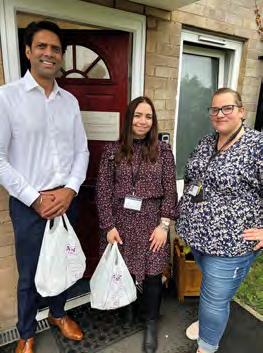
19 minute read
News
AJB Group continues its charity with local initiative
Residents at the Corby Homeless Project were treated to some Indian savouries, as part of a charitable initiative by the team at AJB Group to give back to the community.
AJB Group’s CEO, Amarjit Binji, provided finely-wrapped packages, each containing a selection of samosas and pakoras. He was greeted by Lucy Brooks and Susie Skelham, pictured, Resident Engagement & Project Lead and Homeless Pathway Co-ordinator, respectively, who gave a guided tour of the building.
Jo Burns, CEO of Encompass charity which runs Corby Homeless Project, said: “We would like to thank Amarjit and his team from AJB Group for their kind and generous foodbank donation. With an ever-increasing rise in the cost of living and the likely impact of this on homelessness, even stronger partnerships are going to be vital. Whilst Encompass continues to go over and beyond its call of duty, it’s organisations such as AJB Group that can help add even greater value to all that we do.”
The latest quarterly Chain figures found just under 3000 people sleeping rough in London between April and June 2022. This represents an alarming 10% rise on the 2714 people recorded in the previous three months.
As it stands, nearly seven million people are said to be going hungry in the UK, including two million children. That’s an increase of two million since the pandemic. By next month, almost half of all children will be living in families who’ll be unable to meet the cost of some basic necessities, research suggests. AJB Group is a manufacturer of world-class joinery products. Its client list includes The Shard, BBC TV Centre, Centre Point and Battersea Power Station. Corby Homeless Project is a partnership with North Northamptonshire Council, aimed at helping those who are homeless, both immediately and longer term.
As well as supporting with accommodation, residents are supported to learn to cook and clean, access their benefits, budget and plan for the future, complete training courses, education or be work ready and access other agencies such as health services, drug and alcohol support, the job centre and domestic abuse services. www.encs.org.uk www.ajb-group.co.uk
Egger boosts recycled content through £15m investment
Wood-based material manufacturer, Egger UK Limited, has invested over £15 million into recycling operations at its site in Hexham.
The investment reinforces the company’s commitment to make More From Wood, by improving the quality of recycled wood used to make Egger’s chipboard panels.
Employing the latest technology, the new recycling plant will segregate, clean, and chip waste wood that would otherwise be burnt or sent to landfill. Recycled material maintains the carbon stored in the wood and benefits the environment.
Thanks to the new, state-ofthe-art processing facilities and the high quality recycled material processed, Egger is able to increase the amount of recycled wood in each chipboard panel it produces.
By improving its recycling processes to get a better quality raw material, Egger can guarantee that the quality of the panel is not compromised.
Alex West, product manager at Egger UK, said, “Increasing our recycled content answers the demand from the interior design, furniture, and housebuilding industries for more environmentally conscious products. We are a major supplier to these industries, so it’s important that we lead the way when it comes to sustainable product innovation.”
Alex continues, “Not only does this investment strengthen our closed loop production cycle, but it also demonstrates the importance and commitment the company places on a sustainable supply of raw materials.”
Plans for the project started in 2019, with breaking ground taking place in October 2020. Led by Andrew Shepherd with Egger’s dedicated UK project team, installation was supported by the wider Egger Group, Cubby Construction, Mibex Ltd, Garwen Enterprises, and Parkgate.
The team has collectively spent over 130,000 hours on this project and navigated many external challenges during the build, including COVID-19, skill shortages, and material availability. After commencing commissioning in August, chipboard production with increased recycled content is underway. www.egger.com
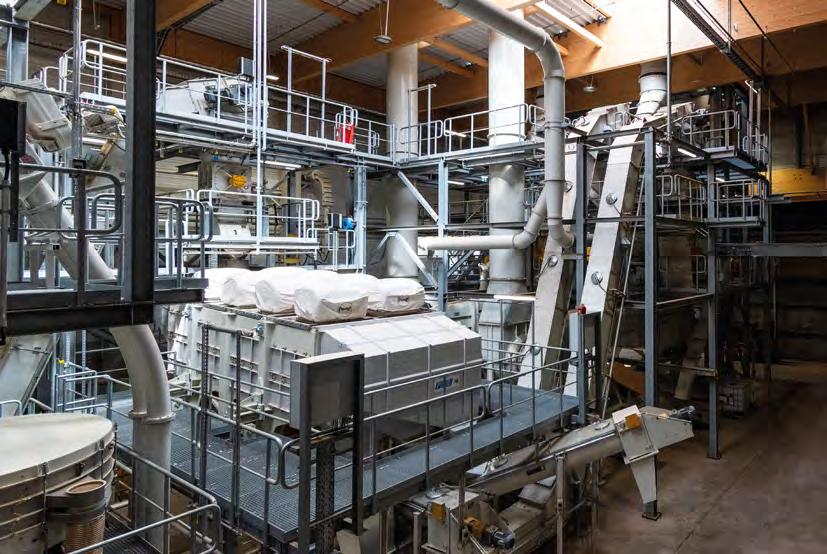
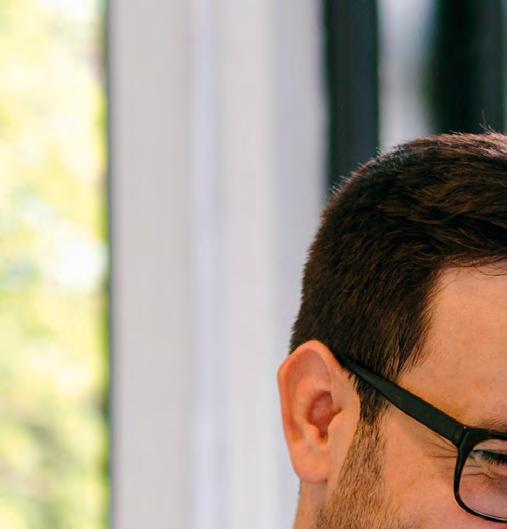
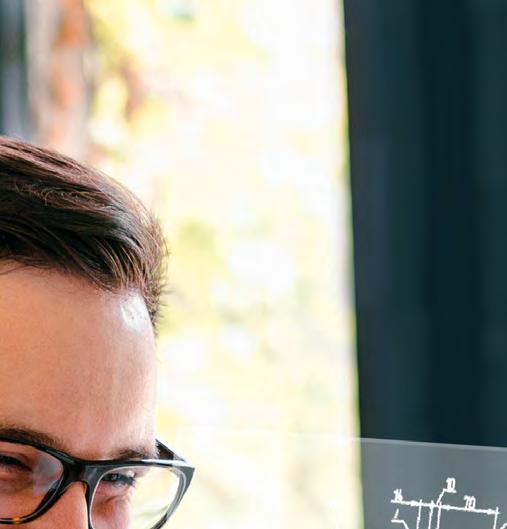
Software for Interior Design and Production
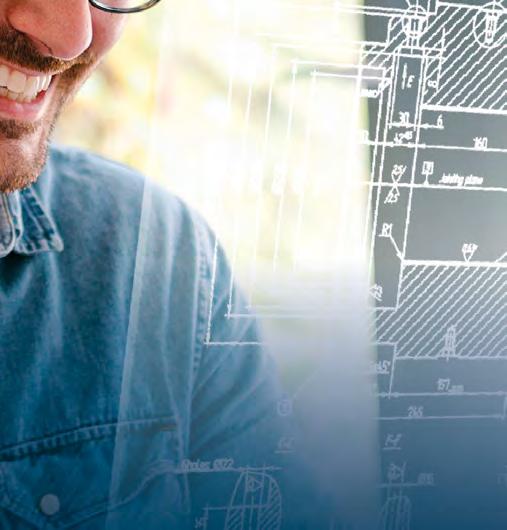
Get startet with the latest cloud solutions from CAD+T software
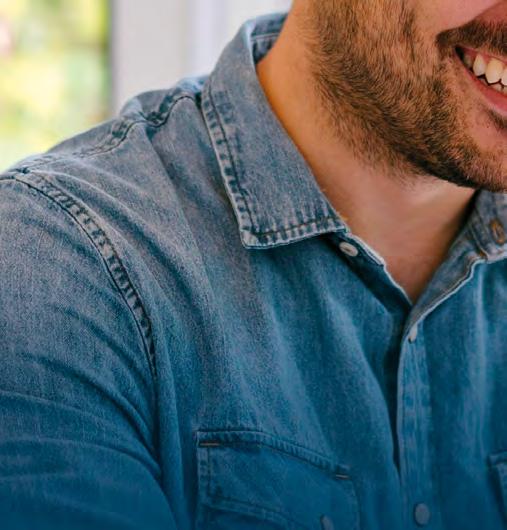
Get access to your data 24/7 from everywhere
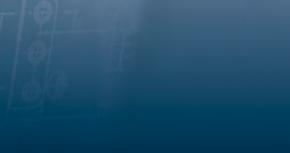

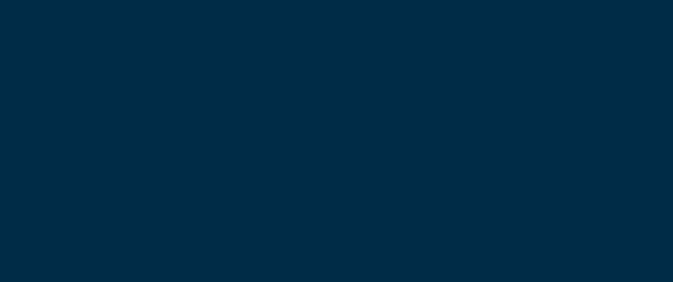
+Cloud solutions specialised for interior design and production +Manage your data anytime from everywhere + Benefi t from cloud licensing, parts lists, material master and more
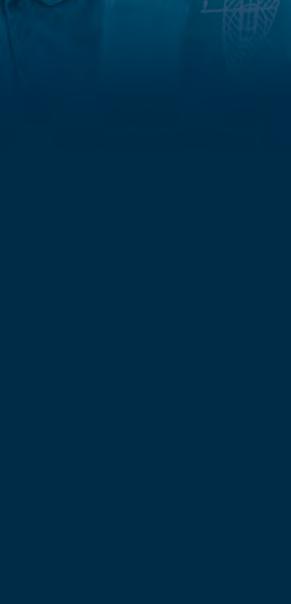

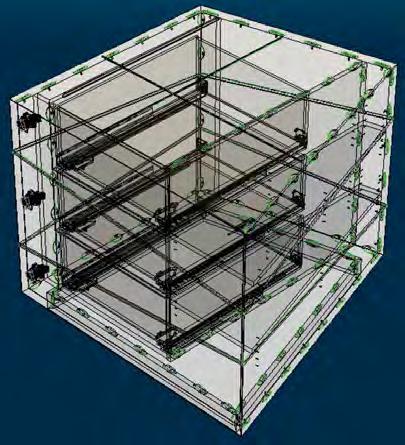
CAD+T Solutions GmbH +43 7229 83100 0, A-4052 Ansfelden office@cadt-solutions.com www.cadt-solutions.com
Record training growth for Daltons Wadkin
The Daltons Wadkin “red team” of trainers is celebrating a significant milestone in the delivery of certificated operator training courses throughout the UK and Ireland. The past 12 months has seen a record 1250 individual learners successfully trained across all types of woodworking machines, abrasive wheels and hand operated power tools.
Daltons Wadkin are a PIABC Quality Assured training provider and have been providing industry led courses for over 15 years, continually honing the content to meet both customer and legal requirements.
One of the fastest growing departments within the company, Daltons Wadkin has expanded its training team to 4 full time trainers to keep pace with demand and are now recruiting a fifth. Each trainer is a qualified teacher and assessor and has a minimum of 10 years experience in the woodworking sector operating industrial machinery.

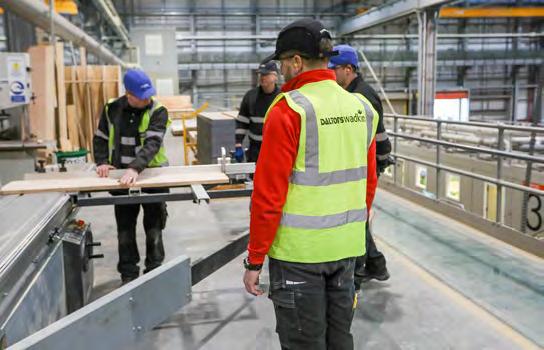
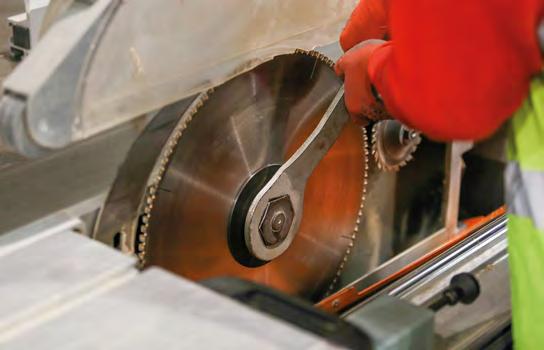
“Our standards are extremely high when it comes to recruiting trainers”, comments managing director Alex Dalton. “Our customers look to us for a professional, reliable service. The stakes are extremely high. We are working in one of the most dangerous industries with regards to accident rates and it is imperative that our trainers are suitably qualified, experienced, and confident in their knowledge.”
Training is tailored to individual requirements, whether an experienced operator or novice learner. With absolutely no PowerPoints, courses are delivered on and around customers own machinery. This hands-on approach ensures teaching and assessment is relevant to the customers workplace and production.
Each machine type is covered by an individual training unit. The aim of each course unit is to inform, access and certify the learner in Safe Setting and Operator Training on each woodworking machine in accordance with the Management of Health and Safety at Work Regulations, the Workplace Health Safety and Welfare Regulations 1992 and the Provision and Use of Work Equipment Regulations 1998.
A key component to the success of the Daltons Wadkin training department is the course material. Every machine unit is accompanied by a detailed training book. Developed in house, the course material serves as a training tool during course delivery and is kept by each learner for future reference.
“We are very proud of our course material; it is unique in the industry. Working with the HSE we are continually honing the content to ensure the latest rules and regulations are reflected”, enthuses Alex.
To discuss your training requirements contact a member of the Daltons Wadkin team on 0115 986 5201, email training@ daltonswadkin.com or visit https:// www.daltonswadkin.com/training/
Having commissioned Carbon Footprint Ltd (www. carbonfootprint.com) to conduct an independent audit earlier this year, which found that The Sash Window Workshop had reduced their emissions by an impressive 39%, the company decided the next step was to offset their emissions.
However, as an environmentally responsible company, The Sash Window Workshop felt that this wasn’t enough. So, they decided to offset all the emissions that they produced and then go further still and offset additional carbon from the atmosphere to achieve Carbon Neutral Plus.
The Sash Window Workshop believe that they are the first timber window and door company in the UK to achieve Carbon Neutral Plus status, which means that you are required to offset 125% of your carbon emissions.
When choosing which projects to support to reduce carbon emissions, the company felt it was important to choose projects that would make a real difference to local communities at the same time as reducing carbon emissions.
With the assistance of Carbon Footprint Ltd, they set out to invest in carbon offsetting projects that were Gold Standard CERs, Gold Standard Verified Emission Reductions (VERs) or Verified Carbon Standard (VCS) certified.
After assessing the different options, The Sash Window Workshop decided to invest in two offsetting projects, one of which focused on reducing deforestation in the Amazon and a second which helps provide improved cookstoves in Uganda.
The largest remaining rainforest on our planet, the Amazon is known for its biodiversity. The project works to prevent unplanned deforestation in native forests, caused by logging, squatting and attempts to implement pastures, and provides legal land-use permits for villages that actively participate in forest protection. It is expected to help avoid over 22 million tonnes of carbon dioxide over a 40-year period by managing the land to reduce deforestation, through rigorous monitoring and enforcement.
Wood fuels for cooking is one of the major causes of deforestation in Uganda. Over 95% of the population of Uganda rely on fuels such as wood or charcoal for cooking on fuel intensive traditional cooking stoves, which emit high levels of carbon. The cookstoves project helps reduce greenhouse gas emissions by distributing fuelefficient stoves which reduce fuel consumption and reduce the cost for poor families while improving health by reducing pollution.
The Sash Window Workshop are proud to support both these worthy causes and the company is committed to reducing their carbon footprint further and improving sustainability.
Managing director at The Sash Window Workshop, Richard Dollar, pictured left, commented: “We are delighted to have achieved Carbon Neutral Plus status, reflecting our company ethics and belief in the importance of helping protect and preserve things for future generations.
“We are proud to be leading the timber window and door industry in reducing and offsetting carbon emissions and hope to encourage others in the industry to follow our footsteps and become more environmentally friendly. In the future we hope to reduce our carbon emissions further still and, as the technology continues to improve, we will look to make the necessary changes to achieve this.” 01344 868 668 www.sashwindow.com www.carbonfootprint.com
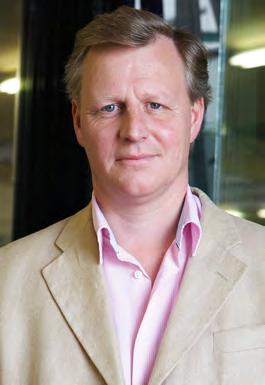
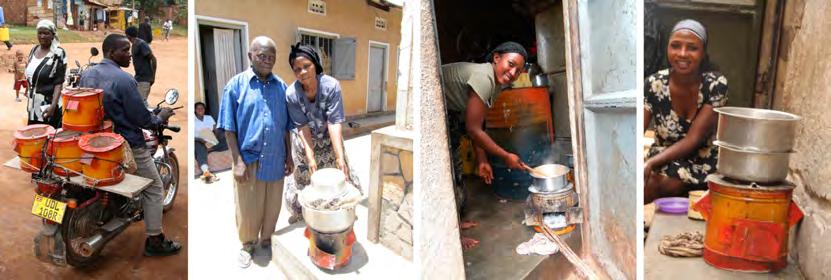
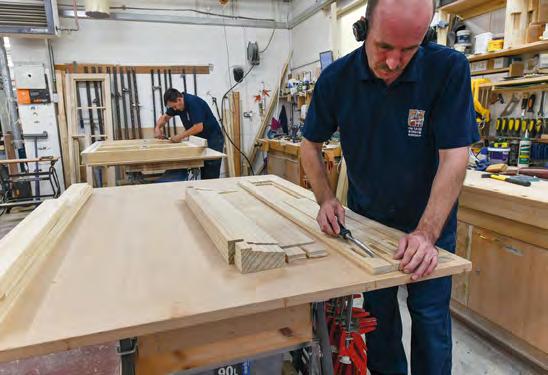
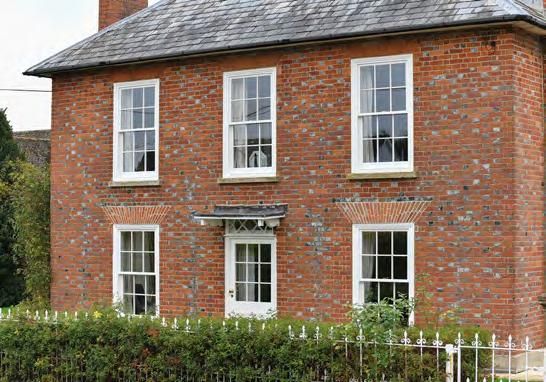

New man at the wood sector helm for Mirka
Mirka has a well-deserved reputation in the furniture and woodworking sector for its innovative abrasive developments and of course its outstanding tools and technology. Neil Newbrook, the company’s new wood sector manager was appointed earlier this year and John Legg took a trip to Mirka’s Milton Keynes Office to meet him.
Sat across from Neil, I asked him how his first six months in his new role had been… “It’s been great,” came the immediate response, “I’ve really enjoyed getting familiar with the industry from a slightly different perspective. I had six years at Mirka where I was looking after customers in the north-east, visiting end-users and distributors across that region in a technical sales role – so I was already very well versed in all things Mirka. Prior to that I have been in a number of wood industry roles for more than 20 years before I started with Mirka.”
Clearly with the internal relationship already in place and functioning well, promoting from within is typically an advantageous move for both the company and the employee. Neil says he realised straight away that this was a role that would suit him.
“When we did an internal reshuffle earlier this year, and this opportunity came up, I just wanted to do it straight away – it was exactly where I wanted to be, as I would be representing a leading brand on a national scale.
“Since the appointment, I’ve found it very interesting and it’s been great to have had the experience with Mirka up to this point, because I think without that, I might have struggled a little bit.”
Settling into his role as wood sector manager, Neil is naturally now more involved in the strategy side of Mirka’s development.
“Now I get to see more of the development process for new products and speak with the incredible team based in Finland. It’s been great to learn from their extensive experience and give them feedback from the UK. It sounds like marketing speak, but they really do pay attention to what our customers talk about. All the products Mirka are developing are trying to solve a problem we have discovered by having such a close relationship with the end-users” explains Neil.
As part of his role, Neil is part of this critical process: “I am learning more about the process from that point of view, so rather than merely being given products to take to market, my new role encompasses this important part of the wider theoretical and creative process.”
In addition, Neil is also involved in the marketing side of things, which includes seeing how things work at trade events, media and so forth. In terms of priorities for Neil, clearly his primary task of getting to know Mirka’s national woodworking customer base is not something that will be achieved overnight.
“I love meeting joinery and furniture manufacturers faceto-face, seeing their projects in development and finding out how Mirka can help them achieve their goals. It’s exciting to be able to broaden my horizon to include all areas of the UK and I cannot wait to visit more end users and distributors. Of course, it takes time to do this, but at least I know my diary will never be empty! In fact, Mirka UK are currently reorganising our Technical Sales team to create six Wood Sector Specialists to visit, demonstrate and advise. We’ve also just recently added an automated sanding arm to our Training Centre in Milton Keynes to show this new technology for consistent sanding.” Ian Deery, the Business Development Manager in charge of the UK’s AIROS project added “With automation you can take a repetitive sanding process and remove errors, deliver consistency, and save time”
“I am a person who is very happy in this job and am very excited about the future too.”
Regarding the future, Neil was able to give some insight into Mirka’s forthcoming innovation plans.
“We expect a number of new woodworking sector options to make their debut next year,” says Neil, “we have a couple of abrasive projects currently in development for the wood sector, and with all being well, will be launched in 2023. We will also be sharing a lot more details on the sustainability projects Mirka are involved in as part of our focus on responsible manufacturing”
“Looking further ahead, the next four, five, six years look set to be a very progressive phase for Mirka’s woodworking sector, so watch this space!”
In addition to the development and production of the company’s products, Neil also touched on Mirka’s own production processes. Innately, the Finns have a close affinity with the natural world, and Mirka likewise has always looked to be very considered in the way it approaches energy consumption and the carbon footprint of its business.
“Recently the company has developed new abrasive manufacturing machines, these new machines have a lot of possibilities for us,” says Neil, “in terms of how we use grain, how we make the backing, and how we apply the grain to the backing, which creates a number of possibilities for Mirka in terms of the production process and, importantly, sustainability.
“Traditional abrasive manufacturing of setting the grain to the backing is a very power hungry process – you need a lot of heat and it takes a lot of time. The company’s improved manufacturing process can achieve this, on the new Galaxy for instance, using just a fraction of the energy. The new approach also provides increased production flexibility and an example of this is the change of production runs from one product to another can now be managed much more quickly than before.”
Over the next twelve months or so, Neil will be delivering the Mirka mantra of ‘we have the product portfolio that will cover every single application within the wood sector.’ The timing of Neil’s appointment appears to have been well conceived. With his groundwork well under way and a tranche of new products hitting the wood sector next year and beyond, Neil and his team look certain to become increasingly familiar faces to those looking for premium abrasive technology solutions. With Neil’s appointment, Mirka UK’s wood sector team is well positioned as it gears up for a series of impending product launches which confirms yet again the Finnish firm’s innovative and customer-oriented stance. www.mirka.co.uk
Neil Newbrook, Mirka’s new wood sector manager
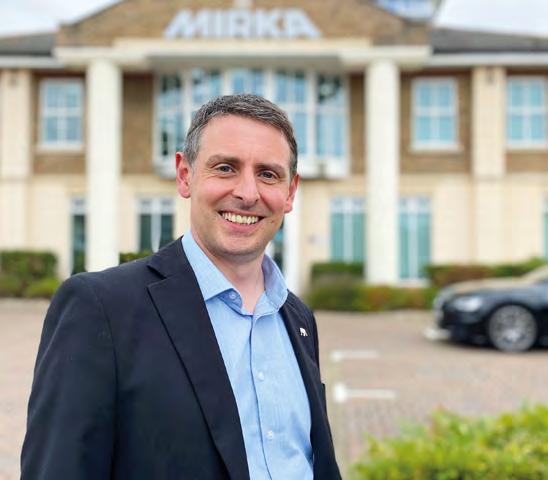
Mix & match the door size samples to create the perfect combination in the gallery.
EGGER ‘Leeds’ the way
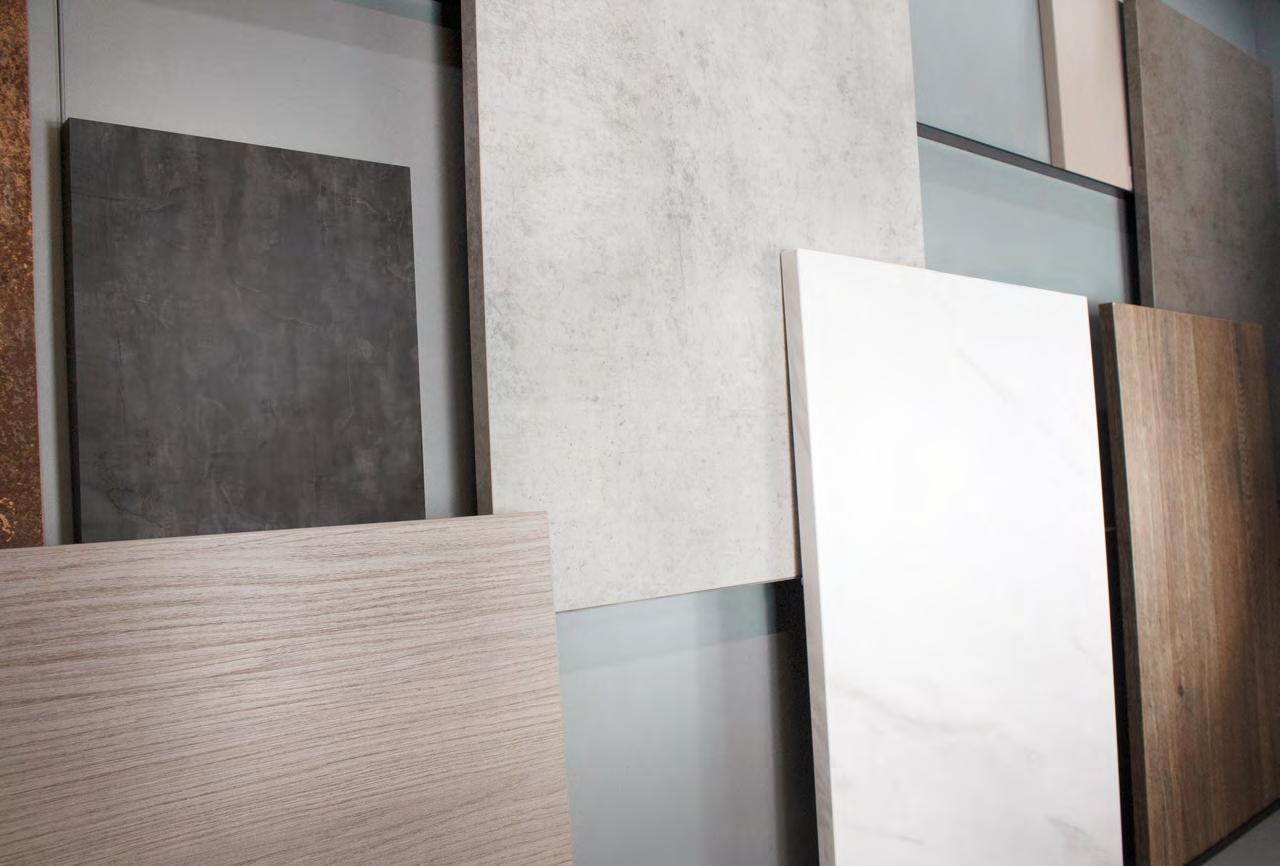
EGGER has set the wheels in motion, triumphantly making a statement in Leeds with a brandnew, deliciously colourful display at Lawcris headquarters. Cleverly merging office and showroom, the space provides customers, designers and architects with a fully functioning, imaginatively vibrant, social space to meet, share and develop creations.
Lauren Barker, head of marketing, explains “Most people walk into the room with a slight gasp, the space takes them by surprise and immediately piques their interest. Music is playing in the background as they instantly start pulling out the big sample boards and placing them into the two big gallery areas, one on each side of the room. Ample lighting allows them to play with colours and combinations in a more authentic environment. There is optimal space to stand back to look at the arrangements from multiple viewpoints. The room is suddenly a buzz of creativity, an explosion of visual pleasure.”
“Once the colour palettes begin to reveal themselves, textures need to be determined. The eye-catching table in the centre of the room has all the answers with ingenious holders to place the boards upright, side by side. This allows people to weigh up the different elements closely from the comfort of their own seats at the table, carefully choosing the perfect surface for their project.”
EGGER is renowned for its textures. It truly understands that the feel of a surface is important and has invested a lot of money into developing woodgrains and materials to be more realistic than ever. This natural appearance is highly appealing to designers. Not only for their project’s purse strings, but the simplicity of installation and easy maintenance. It provides that visual and sensory experience which adds massive value.
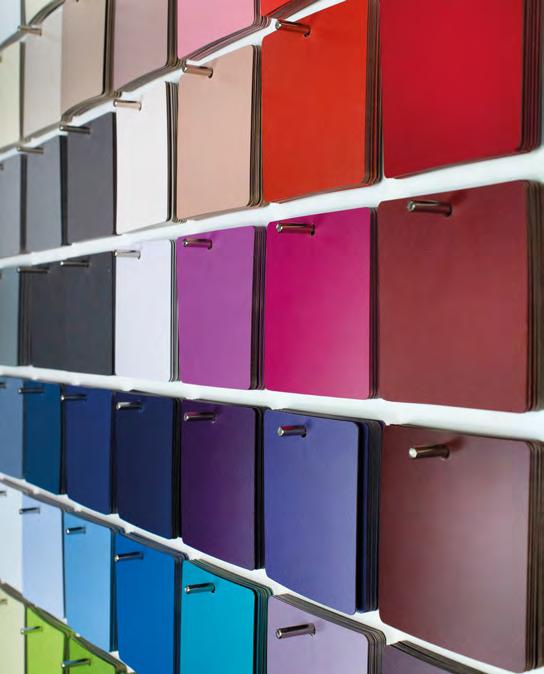
Accent edging is a very popular way to lift a design to a new level Customers can pick from glosses, woodgrains, uni colours, material decors and so much more within the space
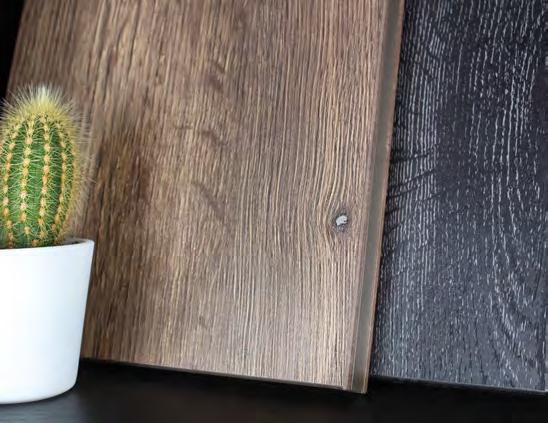
Lauren continues: “With the boards displayed in the middle of the table, people can compare the differences, especially when it comes to the woodgrains. Whether they are looking for a contemporary veneer effect or opting for something that comes very close to solid timber, balance is everything and they will always find something that works perfectly for their project.”
Designers are attracted to EGGER for their matching materials, which is one of its unique selling points. Having a selection of worktops, laminates, MFC (in varying thicknesses) and edging available in the same decor is appealing to anyone looking to create a high-end look on a budget.
Lauren says: “There are endless options to pick from around the room. Glosses that outshine anything on the market, edging with accents that refreshingly highlight and complement the board, over 250 colourful laminates and we have not even touched upon the popular painted timber effects that are in fashion. Everything on display is available on next day delivery which allows ease in their decision.”
“Once boards have been selected, it is time for designers to lockdown their choices. They scan the decors which then appear on a huge 65-inch TV screen within EGGER’s high-tech App. These can be placed in a digital mood board alongside other inspiration and photos. This allows them to take their experience away with them to helpfully inform their clients. A4 samples are also available to take away, it is a perfect balance between digital and reality.”
“The opportunity to work with EGGER on this exciting collaboration, and have the full
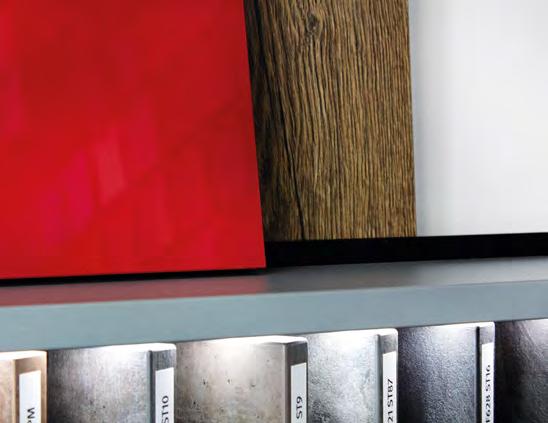
Huge investments from EGGER have resulted in products being more realistic than ever
The room is a buzz of creativity decorative collection on display was a must. To have a showroom which provides instant access to big samples, showing how EGGER products look, feel, change, contrast and combine with others, is beneficial to our customers. Local designers and architects have already taken full advantage. In addition, local joiners are now booking the space, bringing their customers down to plan out their kitchens or bedrooms.”
Dean Carroll, head of procurement, says: “There are businesses, like EGGER, in this world that stand out, they thrive in a way no others do. EGGER’s pace in terms of innovation has been monumental, a constant leader in design with a clear focus on meeting the customers’ needs. The dramatic impact of the EGGER Decorative Collection has revolutionised the interior design world. We are so happy to be part of it with a display of our own to share and inspire.”
The EGGER DesignHUB can be found at Lawcris, Leeds. Simply get in touch with their friendly sales team and book your space. 0113 217 7177 www.lawcris.co.uk

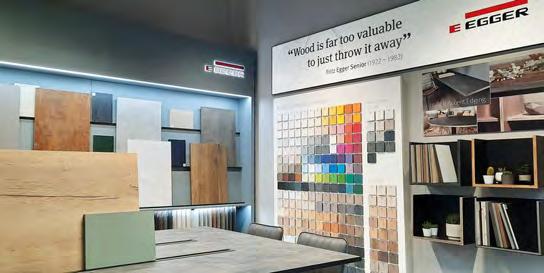
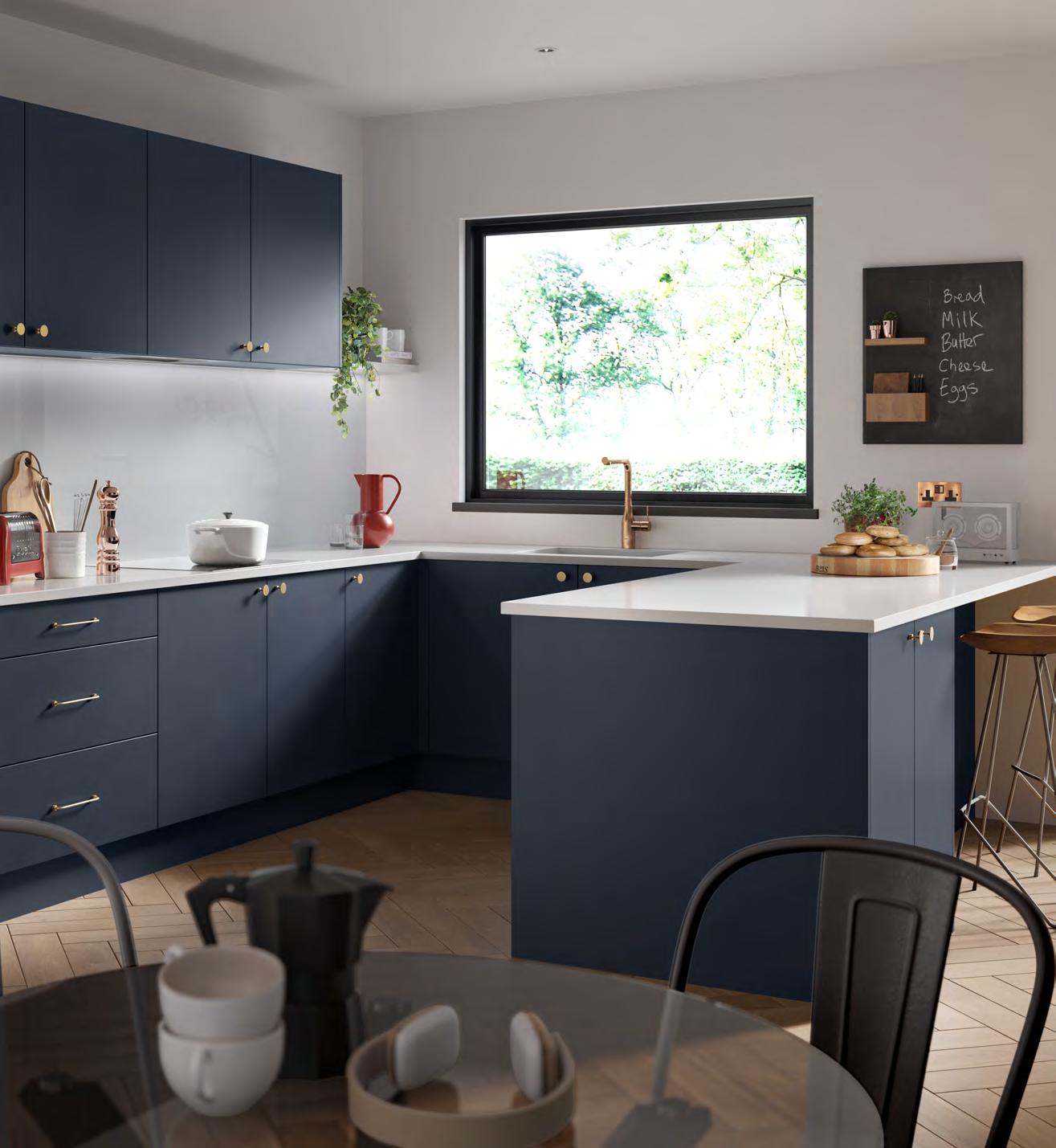
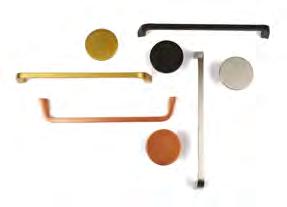