
10 minute read
Prefabricated Underfloor Heating – The Future of Underfloor is Here!
Underfloor heating combines high comfort levels, low maintenance and excellent energy efficiency — for these reasons, such systems have become popular in many European countries. Listening to the feedback from investors, designers and installers, Pipelife has taken the next step by adding prefabricated underfloor heating to the product portfolio. Pipelifeʼs Irelandʼs Technical Manager Michael Geary explains the solution and the advantages it offers throughout the construction process.
What Is Prefabricated Underfloor Heating By Pipelife
Pipelifeʼs prefabricated underfloor heating solutions entail a comprehensive service that covers everything from the design to the assembly and delivery of underfloor heating systems. The prefabricated mats and prefab manifold cabinets boast exactly the same customizability and benefits as standard hydronic underfloor heating products while speeding up the installation process 3-6 times.
The solution is particularly advantageous for large-scale building projects, such as residential complexes, row houses, hospitals, hotels and nursing homes.
COMBINING END-TO-END SERVICE WITH PREFAB
From finding qualified workforce and meeting project deadlines to keeping up with increasing customer expectations and regulations, the buildings sector currently faces plenty of challenges. Developing end-to-end services is a way building material suppliers can help mitigate these issues, and prefabrication is one of the areas with large yet relatively untapped potential.
“In many countries, like in the Netherlands for example, there is a growing demand for prefabricated underfloor heating mats,” says Michael. “We wanted to combine such a product with other services that we have been offering to our clients, such as design support and preassembled manifolds, creating a unique, all-inclusive offer on the market.”
Achieving Higher Installation Efficiency And Reliability
Construction projects are frequently delivered late and exceed their original budget. Prefabrication allows avoiding unplanned costs while taking significantly less time than traditional on-site construction. If installing standard underfloor heating in a room of 20 m2 typically takes 20-30 minutes, prefabrication allows completing the same task in just 5-7 minutes — offering major gains for contractors as well as investors.
Furthermore, Pipelifeʼs prefabricated mats and manifolds are assembled in factory-controlled environments by trained professionals using only top-quality materials. The process eliminates risks of typical installation errors, such as deviations from the drawing plan or incorrect connections.
This way, prefabrication not only allows achieving higher reliability and excellent service life of the installed heating system but can also help optimize supervision on-site.
“As the whole system is produced, preassembled and delivered by a single supplier, the reliability from the technical standpoint is very high — facilitating and speeding up the commissioning,” explains Geary.
Offering Full Design Support
Underfloor heating systems are known for their long, maintenance-free service life. If functionality issues arise, they often can be traced back to poor design. The optimal heat output of each system must be carefully calculated and depends on multiple factors, such as the insulation and age of the building, heating zones desired, heat sources available, and even the selected floor finish.
As designing heating systems requires in-depth expertise and is time-consuming, Pipelife offers full design support as part of the solution. With a design team that has more than a decade of design experience and in-depth industry background, almost 300 design projects were completed last year alone.
The service saves project designers hours of tedious work. A fully tailored heating system design, considering the unique conditions and requirements of the particular project, is prepared and sent to the customer in just a few days.
“This way, we can ensure the best technical solution for our clients while saving time for project designers — who can focus on other tasks or even take on more projects,” sums up Geary. “As time pressure in the building sector keeps increasing, just as expectations of project safety and quality, such a service is a win-win solution.”
New Opportunities For Installers
Reports show an acutely growing shortage of skilled workers in the EU, slowing down the completion of the started projects and, if unresolved, impeding future growth of the construction sector.
Prefabricated products can be installed in a shorter time and by fewer people, compensating for the lack of high-profile installers many countries in Europe are struggling with.
“Nowadays, installers are typically paid either per project completed or per square meter installed. As the demand for qualified installers is high, they often have to decline requests. Our solutions enable installers to accept more projects as they can complete their tasks faster,” explains Geary.
The new prefabricated underfloor heating solutions do not eliminate the need for skilled construction workers on-site, as their expertise is still required to carry out specific tasks like connecting the mats to a manifold and pressure testing.
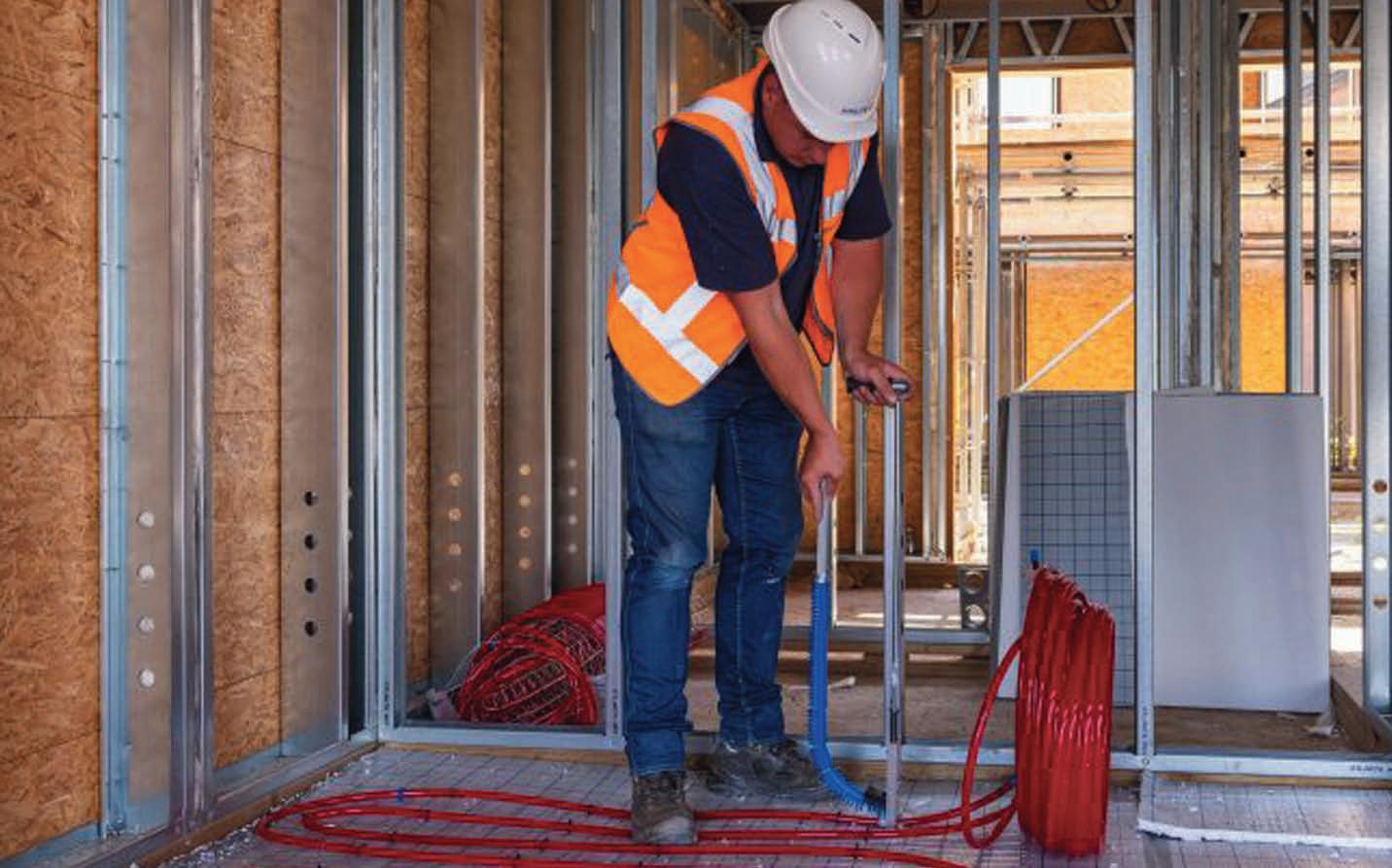
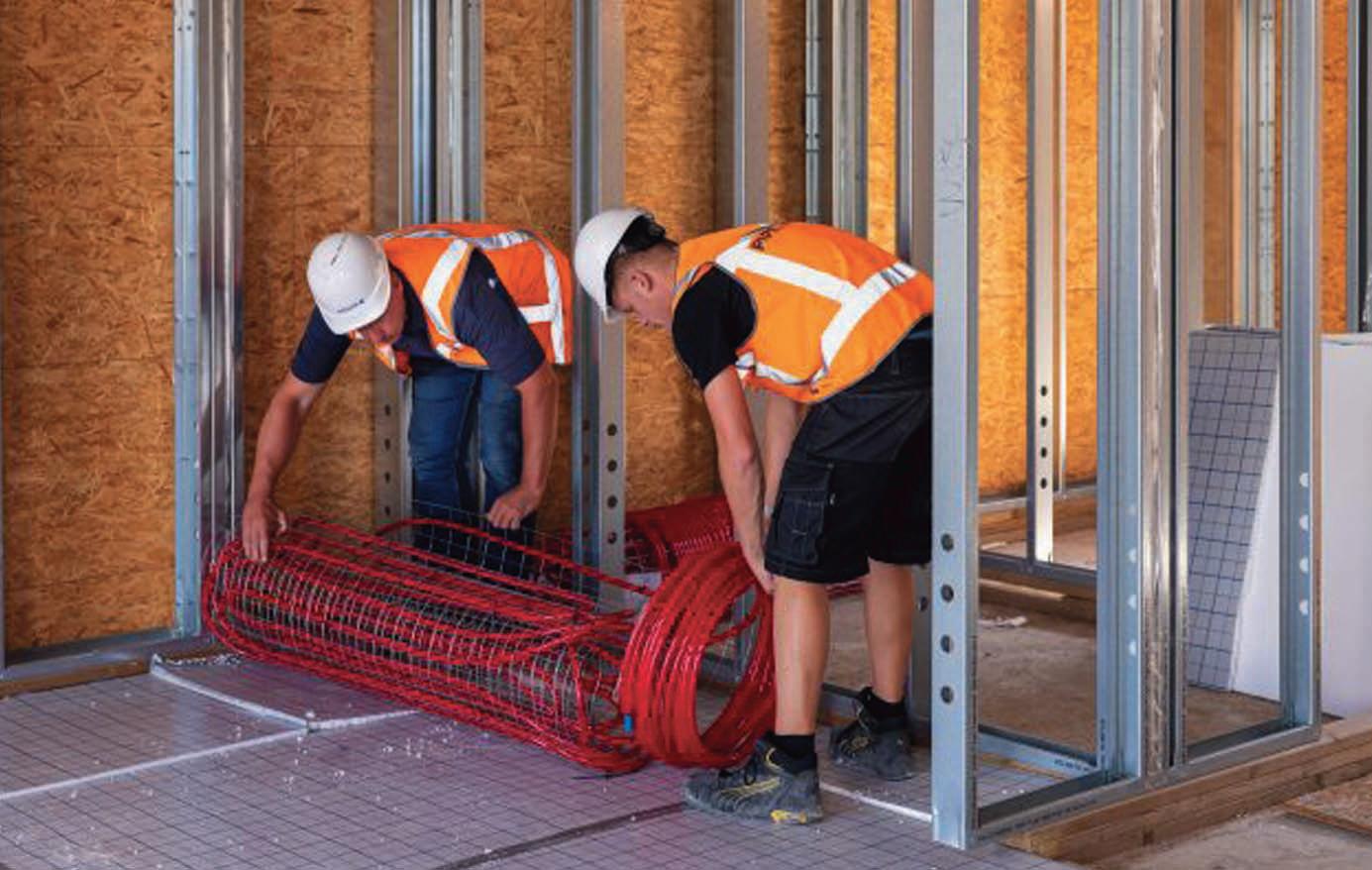
“Our prefabricated underfloor heating is tailored to each project; these are not generic products that will be available in depot stores,” Geary asserts. “The installation process is faster and simpler compared to standard underfloor heating systems, but it requires supervision and assistance from qualified specialists.”
UP TO 30% HIGHER COST EFFICIENCY
As construction material costs keep rising, the profit margins for investors and contractors have eroded over the last few years. Prefabrication is a way to address the inefficiencies that standard construction entails and minimize material waste, helping alleviate the cost increases.
The data from already commissioned prefabricated hydronic underfloor heating projects in the Netherlands, Bulgaria and Serbia show impressive cost-efficiency improvements compared to traditional underfloor heating systems.
“Considering the time savings and efficiency gains throughout each step of construction, the overall cost savings are 20-30%,” says Geary. “Our completed prefab projects clearly show how stepping away from the standard approach can open up new opportunities in the buildings sector.”
Boosting Comfort, Warmth, and Efficiency: Cork Cityʼs Home Energy Upgrade Office Supports Growing Numbers of Homeowners
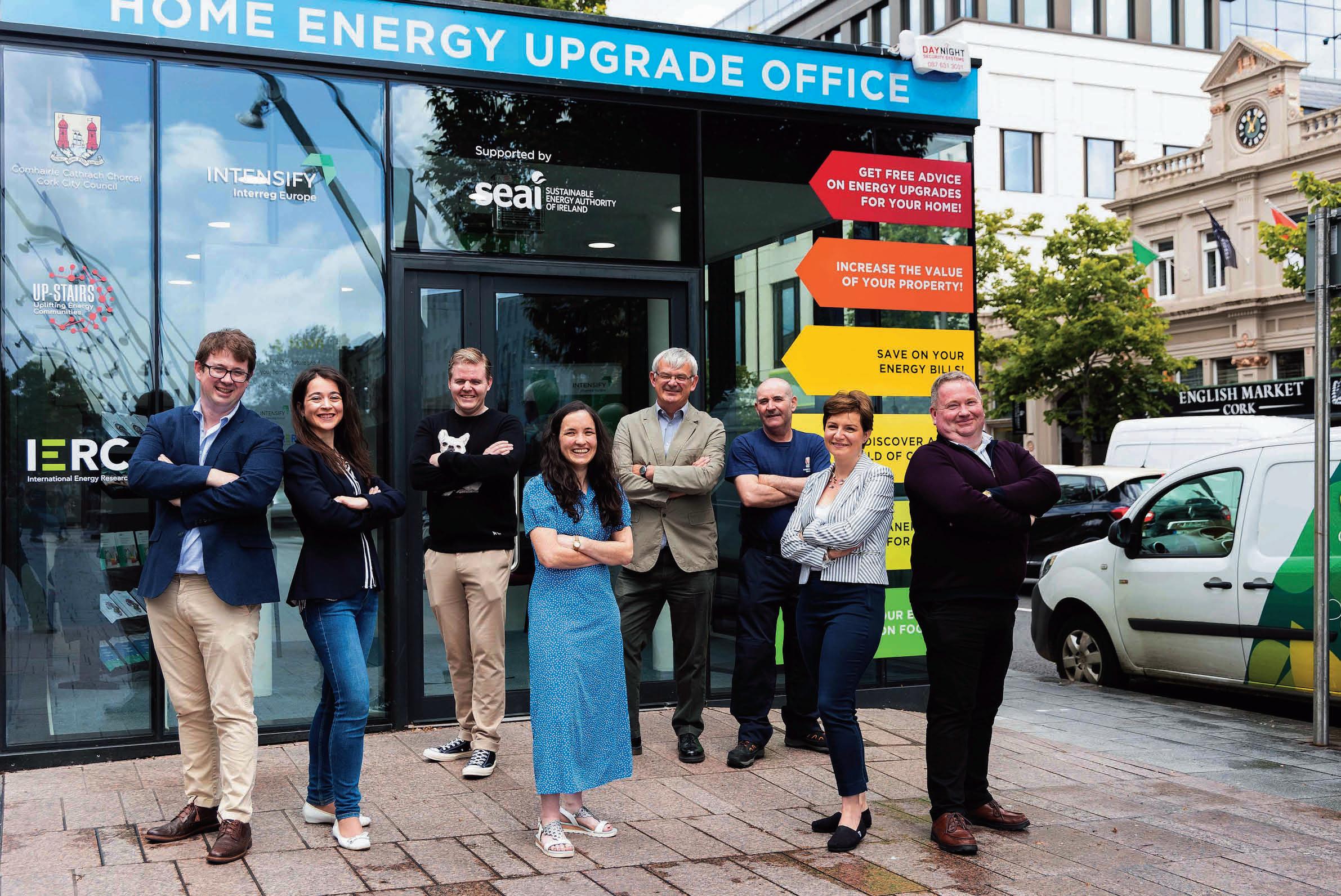
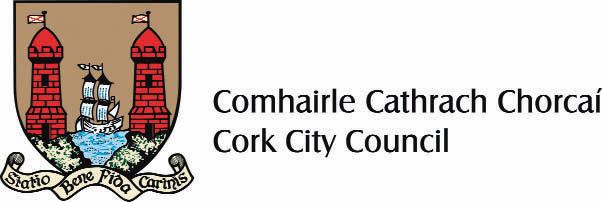
Every year, a significant proportion of home energy is wasted. Whether heating a poorly insulated home, using energy-hungry appliances, or having an inefficient energy source, these factors are all contributing to households using more energy than needed. Instead, imagine if this energy was saved. The impact this could have on keeping money in pockets, as well as the difference it could make in cutting harmful carbon dioxide emissions. With housing accounting for a staggering onequarter of all energy used in Ireland, as well as one-quarter of energy-related carbon dioxide emissions, home energy upgrades play a vital role in improving energy-use efficiency and environmental outcomes. Now, with over €8 billion in supports available through the Governmentʼs National Retrofitting Scheme, the grant funding for homeowners to implement home energy upgrade measures is unprecedented. From taking crucial action on climate change and the biodiversity crisis to protecting against rising energy costs, and with the additional bonus of having warmer and cosier homes, thereʼs no time like the present to get started. But it can be hard to know where to start. Thatʼs where Cork Cityʼs Home Energy Upgrade Office (HEUGO) comes in! In the case of retrofitting or decarbonising, to improving the efficiency of how home energy is used, individuals and communities can access the expert advice and guidance of Cork Cityʼs HEUGO, an in-person service, located on Grand Parade, in the heart of the city.
The first of its kind in Ireland, this innovative collaboration between Cork City Council, the International Energy Research Centre (Tyndall Institute, University College Cork) and the Sustainable Energy Authority of Ireland, has seen growing numbers access its services. At times seeking guidance on installing attic insulation (estimated to save up to €600 per year on home heating bills), to the installation of renewable energy systems and much more, the HEUGO is supporting homeowners across the city and wider region. With a range of grant funding available through the Sustainable Energy Authority of Ireland (SEAI), for example, up to 50% of the cost of complete home energy upgrade solution for a typical home, and up to 80% of the cost for attic insulation through an Individual Energy Upgrade Grant, there has never been a better time to take action on energy use. Alongside the recently announced planning permission exemption for rooftop solar panels, and the opportunity to sell surplus renewable energy back to the grid through the Microgeneration Support Scheme, upgrading home energy efficiency and transitioning energy systems makes good sense. Cork homeowners are seeing the opportunity for change.
As are Cork communities. The HEUGO also supports the creation of energy communities in the city. Whether part of an energy community or interested in joining one, the HEUGO can assist by guiding a community or connecting individuals that might otherwise not have been aware of a shared ambition. Working together brings many benefits such as combining costs and saving on upgrade measures, to having an overall greater impact on the environment. The benefits can go further than front doors too, for example, the upgrade of a community building, or the installation of a public electric car charger.
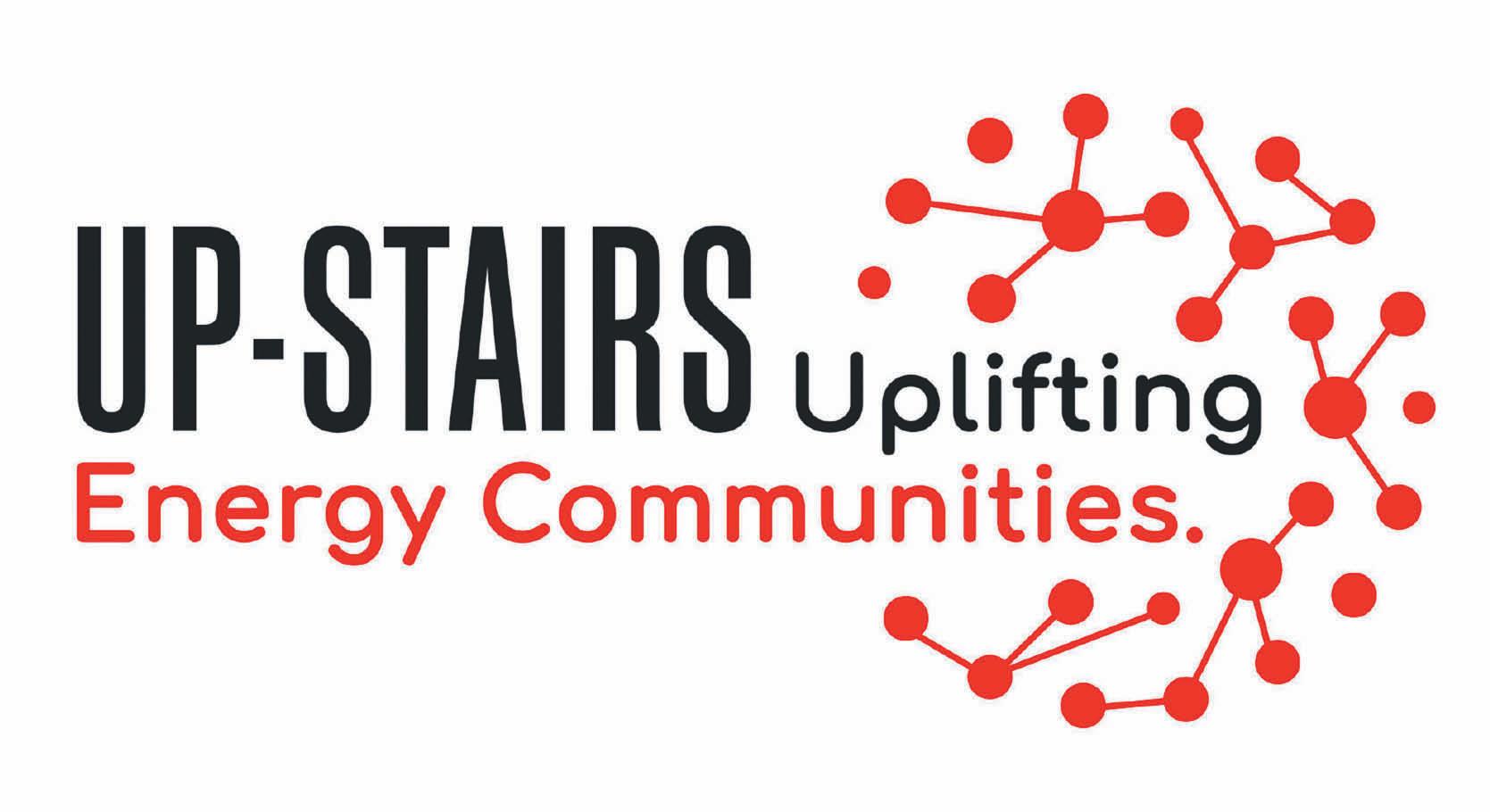
At home and abroad, biodiversity and ecosystems are rapidly deteriorating under the strain of rising carbon dioxide emissions and the escalating climate crisis. The good news is that homeowners and communities have the power to make a difference. Through an energy efficiency upgrade of a typical Cork residence alone, going from a C3 Building Energy Rating (BER) to a B2 BER, the government target for Irish homes, an annual reduction of 4,000kg of carbon dioxide emissions is made possible. The achievable reduction in emissions brings into clear focus the substantial role of home energy upgrades in securing a healthy and safe environment and future for all.
Dedicated to supporting the public, the HEUGO is open from 9am to 5pm, Monday to Friday. Funded through UP-STAIRS, a H2020 project, INTENSIFY, an Interreg Europe project, Cork City Council, and the SEAI. The HEUGO services are available at no cost.
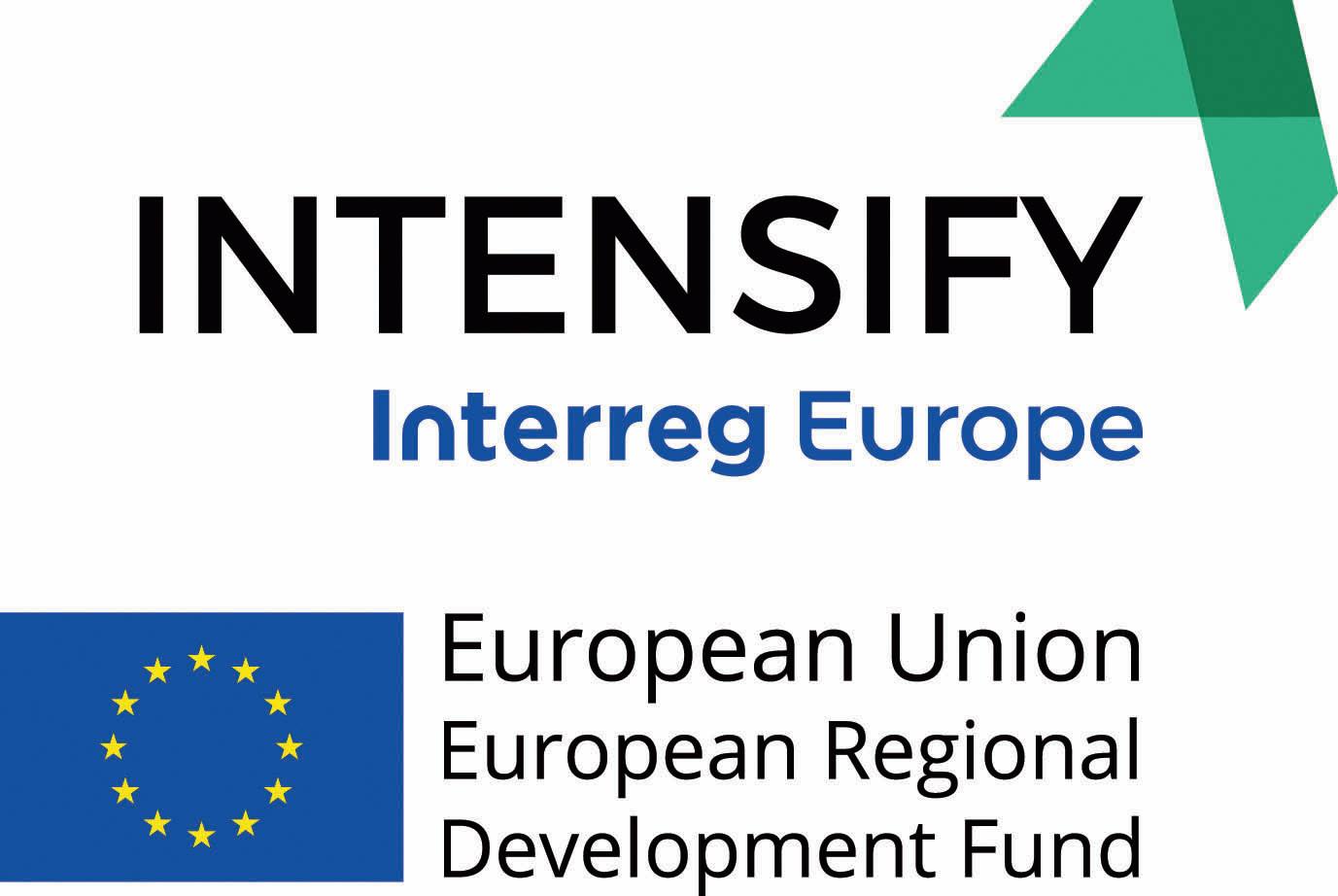
As we all look toward savings on outgoings as we come into winter, boiler efficiency is high on the list for consumers, installers, and the industry as a whole.
In the past, the boilers used in our homes typically had an efficiency of 60%, resulting in 40% of their energy being lost. Some of these older standard efficiency boilers are still in use in homes today.
Over the past number of years Firebird, manufacturer of highperformance heating solutions, has dedicated significant resources and invested heavily in developing products with increased fuel efficiency, reduced emissions and which use more renewable and sustainable fuel sources.
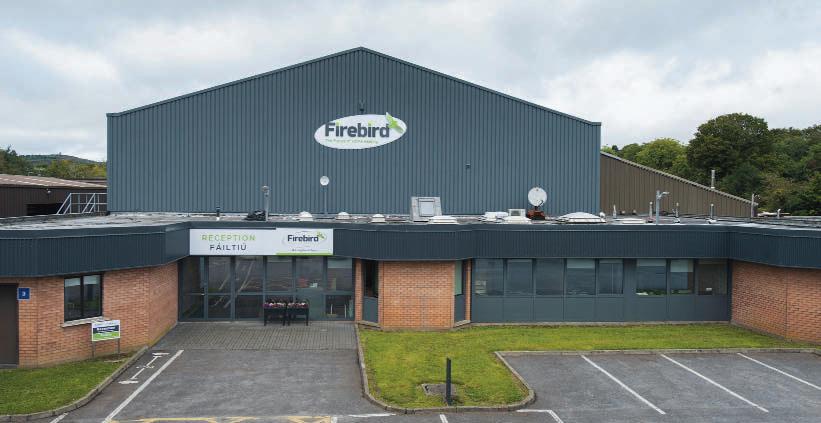
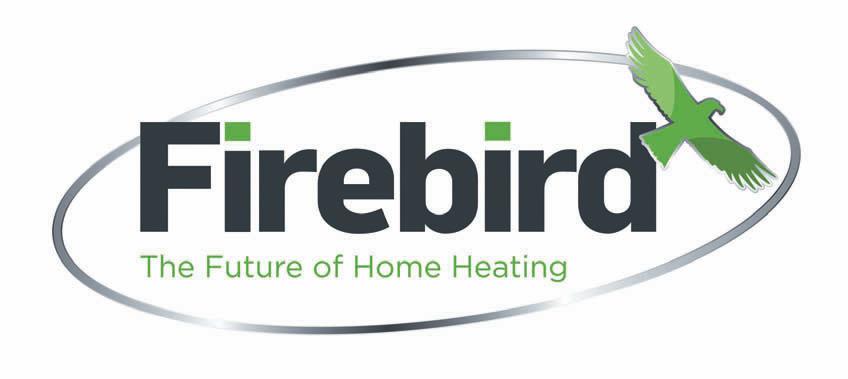
Thanks to this drive towards innovation, Firebird now has the most efficient condensing oil boiler on the market at 97.5% efficiency and NOx emissions as low as 60mg/kWhr, half the EU limits.
Research from The Sutherland Tables September 2022 findings*, shows that by upgrading from a standard efficiency boiler in a house built in the 1980ʼs to a high efficiency condensing boiler, the average savings on heating bills can be as much as €1,300 per year.
As one recent Firebird Trustpilot reviewer stated “My oil doesn't go down as quick and it gets hotter quicker".
These savings would help to alleviate the current pressure on households and businesses which have seen home heating oil almost double in price. Plus, by using less oil, these boilers are much kinder to the environment, as well as to the bank balance!
Firebirdʼs boilers are also fully compatible with Hydrotreated Vegetable Oil (HVO). A viable and sustainable drop-in replacement to Kerosene, HVO is fossil free and can reduce household emissions by up to 90%.
Leading the charge in innovation, Firebird has trialled and tested HVO in Ireland and the UK to prove that it can be implemented almost immediately. The conversion requires little or no modification to existing home heating systems - no significant investment beyond a small conversion cost, (approx. €400) to upgrade to a Firebird by Elco HVO burner.
Mark Doyle, General Manager with Firebird explained how the introduction of HVO for household and commercial boilers would be an instant game-changer for home heating.
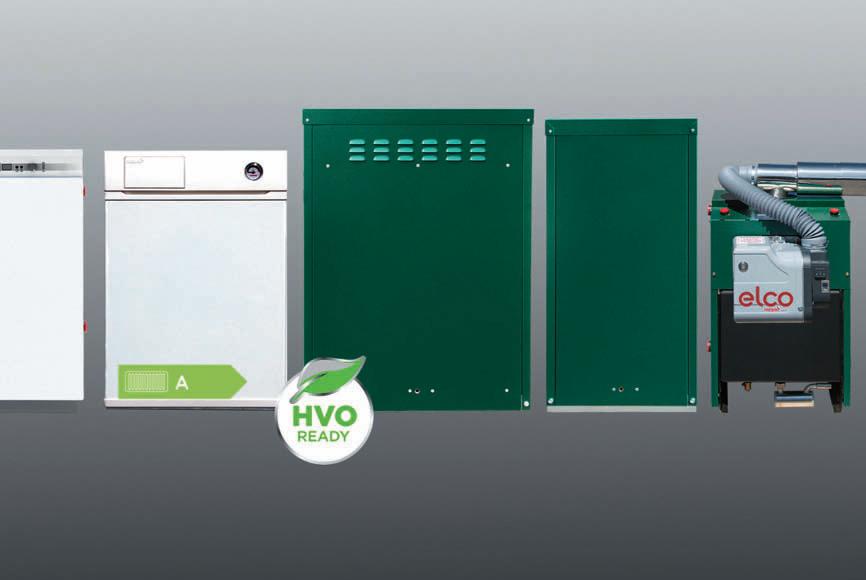
“There are 1.5 million or so homes with existing liquid fuel boilers in Ireland with few other choices available for homeowners to adopt cleaner, greener heat solutions.” he stated.
“HVO can work with any liquid fuel boiler and if used in homes, can potentially make these homes almost carbon neutral immediately. Our trials of HVO for home heating in Ireland have proven how household greenhouse gas emissions could be reduced by 90% with CO2 emissions decreasing by up to six tonnes annually, per home.”
Mark Doyle added: “We at Firebird passionately believe that we all have a part to play to reduce carbon emissions and we believe HVO is not the future, itʼs the “now”. We are continuing to innovate and drive more sustainable heating solutions that help homeowners reduce their carbon footprint and future-proof their homes. Our responsibility to our customers and the environment are the key drivers behind everything we do.” Firebirdʼs manufacturing site in Ireland and offices in England and Northern Ireland are already fuelled by HVO and the benefits can be seen every day.
Our Rural Future: Minister Heather Humphreys announces over €12.5 million for upgrade works on rural roads and laneways
•essential funding to improve access to homes, farms and outdoor amenities
•dedicated allocation for island communities introduced for the first time
•brings total investment in local connectivity to over €112 million since 2017
Minister for Rural and Community Development, Heather Humphreys, has announced funding of € 12.5 million for repairs and improvement works on our rural roads and laneways.
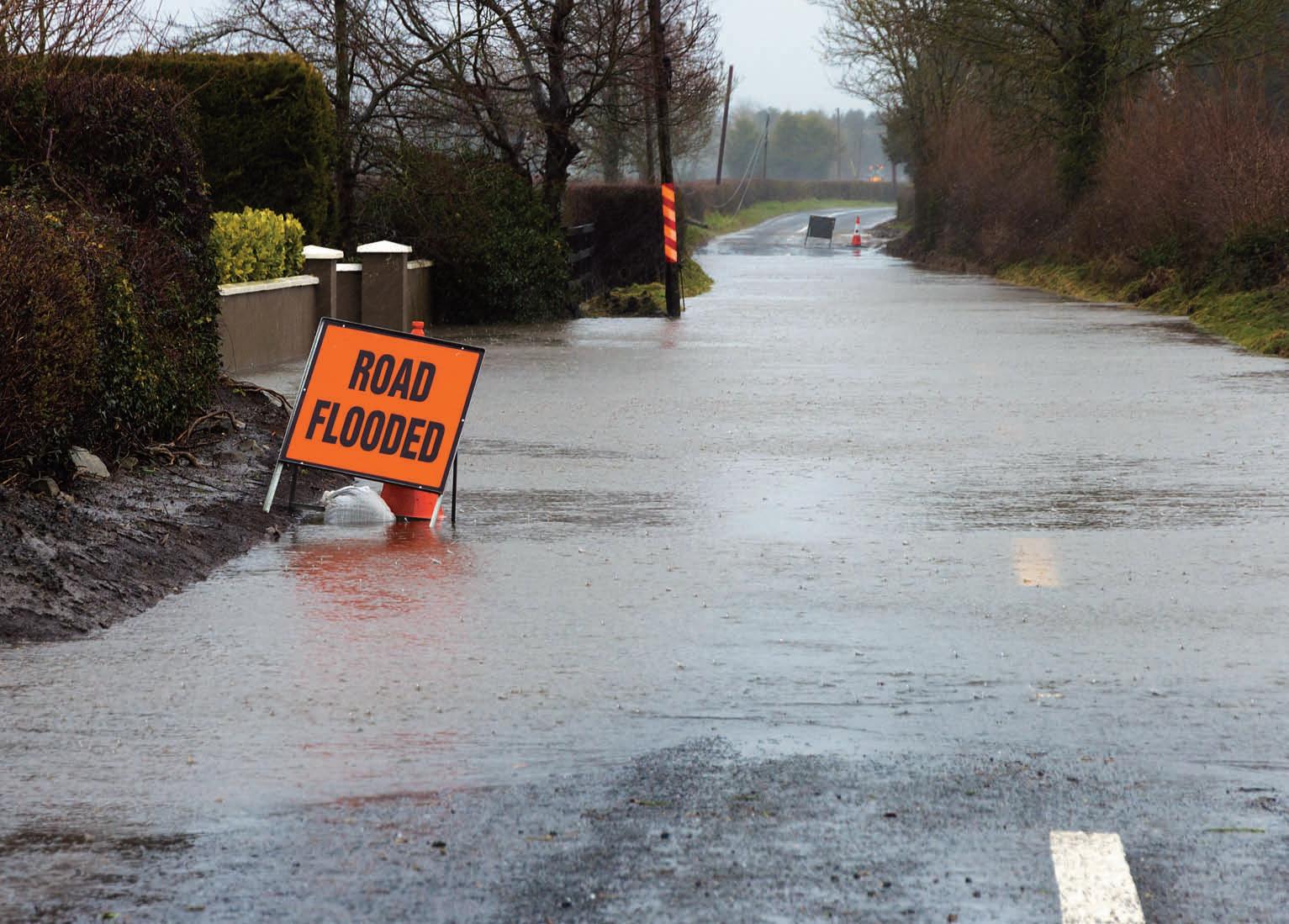
The funding, under the Local Improvement Scheme (LIS), will support the continued improvement of non-public roads and lanes that are not normally maintained by the local authorities.
The investment is key to supporting vital road infrastructure in rural communities, as well as providing access to homes, farms and outdoor amenities such as lakes, rivers and beaches.
And for the first time under the scheme, the Minister today announced the ringfencing of € 500,000 to support rural roads on our offshore islands.
This investment will benefit island communities in Galway, Cork, Donegal, Mayo and Sligo. The overall announcement by Minister Humphreys means some €112 million has now been allocated to local authorities under the Local Improvement Scheme since it was re-introduced in 2017.
Making the announcement, Minister Humphreys said:
“I am delighted to announce €12.55 million in funding to improve hundreds of roads and laneways in towns and villages across Rural Ireland. Local connectivity is absolutely vital for our rural communities and this investment will benefit the lives of families in every single county. We all know parts of rural Ireland that can be difficult to access because the road or laneway is in need of repair. The Local Improvement Scheme is about making peopleʼs lives that bit easier, ensuring we have good access to homes, farms and our local amenities. This is what ʻOur Rural Futureʼ is all about – ensuring more and more people can live work and raise a family in rural communities throughout Ireland.”
The Minister added:
“Iʼm also really pleased to announce an investment of € 500,000 specifically for our island communities. Having visited many of our offshore islands in recent months, I know that there are many road projects in need of investment. This is the first time that the islands have been specifically included in the Local Improvement Scheme, which demonstrates my commitment to enhancing island life.”
Minister Humphreys concluded:
“Since this scheme was reintroduced in 2017, over 3,700 roads have been funded for repair works. This has made a real difference to the lives of over 16,000 landowners and residents. I would urge each local authority to use the funding announced and complete the repair works on the selected roads as soon as possible.”