
10 minute read
Sustainable packaging innovations
WET SEASON
The new CW3 RUN-WET Combo from Loma Systems provides a highly e icient combination of precision checkweighing and metal detection in an e icient configuration designed to withstand the harshest production environments with frequent washdowns and strict sanitary standards. Developed in consultation with many of the company’s end-use customers in the protein, dairy, produce, meat, fish and other food industry segments, Loma’s RUNWET systems boast a sanitary design to make them easy to clean and to minimize the risk of bacterial contamination, with innovative fetures including easy-to-wash frames that use curved surfaces for quicker water run-o , minimal welds, and reduced contaminant traps for optimal deep cleaning and reduced risk of water ingress. Removable top panels provide easy access to clean the conveyor belt without compromising safety, with all the motors, controls and pneumatics safeguarded in IP69-rated enclosure to withstand high-pressure, high-temperature washdowns.
Loma Systems
UPPER CHAMBER
Designed for high-output packaging of smaller-sized ham, cheese, poultry and fish products in plastic pouches, the new compact B 425 model chamber belt machine from Multivac features a 1,00-mm-long sealing bar that makes it possible to load many products per cycle, while minimizing the volume of air to be evacuated to ensure higher cycle output. The optional sealing height adjustment, which can be performed without tools, makes it easy to adjust the sealing height to suit the particular product, while the roller shear cutting before the chamber ensures a smooth packaging process, even with very long film pouches. The patented Multivac suction system ensures that the pouch trim is reliably removed from the chamber, while an optional automatic cutting unit can be used to sever the pouch’s neck, if application requires it.
Multivac Canada Inc.
CASE IN POINT
Integrated with Yaskawa Motoman model HC10 and HC20 collaborative robots to provide greater e iciency and automation for blowmolded bottle manufacturing lines, the new Pakman case-packer from Proco Machinery Inc. features a collating indexing accumulation system to accumulate complete layers of bottles inside the packaging cell. The accumulation table stages the layer of bottles so they can be picked up by Proco’s end-of-arm (EOA) tooling and placed inside the box. Featuring Proco’s proprietary Integrated Rotary Inverting Technology for rotating a layer of bottles to neck-down orientation in a layer formation, Proco’s Pakman packaging cell has many advanced innovative features to help processors pack bottles in all neck-down orientation in a layer formation. Acording to Proco, the Pakman case-packer is a totally integrated packaging module supplied with a six-axis collaborative robotic arm, infeed conveyor, and a box conveyor all mounted onto a common sub-frame, which in turn is fitted with leveling pads and castor wheels for moving the cell into position for quick set-up and commissioning.
Proco Machinery Inc.
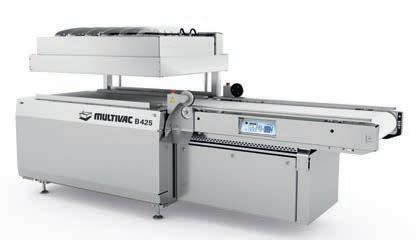

A Clear Focus on Achieving Sustainable Packaging Goals
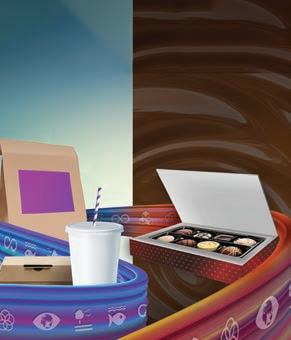
Sustainability is an environmental, economic and societal imperative that is the key to our future. As an organization, Sun Chemical considers it a clear priority to protect the health and vitality of the planet and its natural resources. This need is particularly urgent for the packaging market, and especially plastic packaging, given the visible proliferation of plastic-based waste in the environment. The products Sun Chemical supplies into the market increasingly consider environmental impact characteristics as part of their design, to enable more sustainable options, and to meet consumer and brand owner demands. Many brand owners have made ambitious public commitments to reduce the environmental impact of their packaging and are prioritizing sustainability initiatives to enable delivery on those commitments. Through its position in the packaging value chain, Sun Chemical can provide valuable product solutions and design guidance to converters, to help them offer more sustainable solutions to the brand owners they serve and to better contribute to the circular economy.

A SUSTAINABLE APPROACH
At Sun Chemical, we use what we call the “fi ve Rs”— reuse, reduce, renew, recycle and redesign—as a way to guide a three-pillar approach to our sustainability efforts, each of which contributes to our sustainability initiatives in a unique way. The fi rst pillar is operations. We utilize all “fi ve Rs” in every aspect of operations. One example is that we aim to reduce water and energy usage, waste and CO2 emissions in our operational processes and at our manufacturing facilities. The second pillar is products. Again, we apply the “fi ve R” framework to the ways in which we design products for more sustainable packaging. We aim to enable recyclability, biorenewability and/or compostability within our product offerings while helping to minimize packaging weight and complexities. The fi nal pillar is collaborations. By working through supply chain and cross-industry partnerships and associations, we actively contribute to cross-industry sustainability initiatives that are also aimed at delivering on the “fi ve Rs,” with every member of the supply chain contributing their part. Working through cross-industry associations such as the Food Packaging Institute (FPI), the Sustainable Packaging Coalition (SPC) and The Association of Plastic Recyclers (APR) allows us to understand what the needs and gaps are in achieving more sustainable packaging, and the role that we and our products play in achieving circularity. For example, by our participation in The Association of Plastic Recyclers we were able to better understand some of the challenges to increasing recyclability and reaching higher rates of recycling of PET bottles. These insights from across the value chain allowed us to develop new ink solutions intended to help overcome those challenges. Shifting our product offerings toward more sustainable solutions also means working closely with our supplier partners to ensure they are providing the necessary sustainable raw materials. Our ongoing conversations with our partners provide us with visibility into where we are as an industry currently, enable us to develop targets for the future, and show us where the opportunities are to utilize the “fi ve R” approach to bring sustainability solutions to market.
REDESIGN REUSE
REDUCE
RECYCLE RENEW
GLOBALLY ALIGNED SUSTAINABILITY GOALS
Recognizing that sustainability is a global issue, at Sun Chemical we have aligned our sustainability goals with the United Nations’ 2030 Agenda for Sustainable Development with a particular focus on climate change and resource conversation, sustainable use of natural resources, and on food, safety and health. Through this alignment we are aiming to take the necessary actions to enable a more sustainable packaging industry with an overall positive impact on the environment. We are also implementing specifi c consistent measures at our own facilities by developing internal goals to contribute to a cleaner environment. And we have introduced a Corporate Sustainability Committee, led by the Sun Chemical executive team, to ensure that we are cohesive and coordinated in our sustainability strategy and efforts company-wide. The collaborative approach and global alignment of our sustainability goals with the United Nations have helped Sun Chemical to see the full circular economy requirements, allowing product designs that consider not only cradle to gate, but also cradle to grave. That means that as part of our overall product design approach, we focus on delivering products that support biorenewability and recyclability, including compostability, with the aim to support a circular economy. Sun Chemical’s SunEco family of sustainable products exemplifi es the unifi ed approach toward global innovation and development, provides a framework for discussion of the full sustainability portfolio with customers and suppliers, and emphasizes our commitment to sustainability. For example, our SunVisto AquaGreen biorenewable inks offer foodservice brands and manufacturers printing ink with market-leading levels of biorenewable content. Use of these inks can deliver substantial reductions in CO2 emissions as compared to conventional inks based fully on fossil fuel–derived raw materials. At the same time, the SunVisto AquaGreen inks do not compromise end-use or on-press performance. To promote increased recyclability, we have developed our SunSpectro SolvaWash FL, which will be formally launched soon, and SunSpectro SolvaWash GR product lines—washable fl exo and gravure ink technology. Designed to allow inks to be removed in a controlled way from post-consumer printed packaging in typical existing mechanical recycling processes without staining the recovered plastic fl ake or the process wash water, these inks were developed initially for crystallizable PET shrink sleeves that can be recycled together with PET bottles. The washable inks enable increased recovery of high-quality, clean, recycled plastic resin. One of the main reasons plastic packaging is so diffi cult to recycle is because it is often made up of multiple plastic materials. Thus, fl exible fi lm packaging converters are considering ways to simplify the structures by taking out dissimilar layers and shifting to mono-materials. Sun Chemical brings barrier coating and adhesive product technologies, such as SunBar Aerobloc and SunBar Paslim, to enable these transformations, bringing back the functional properties that are lost when those fi lm layers are removed. Compostable packaging provides another end-of-life alternative, resulting in less waste going into landfi ll/ incineration. In the area of compostable packaging, a large range of compostable-friendly inks and coatings, including SunUno Solimax and SunSpectro Solvaplast/Aquathene, are available and certifi ed as TÜV OK Compost.
ACHIEVING A CIRCULAR ECONOMY
Building a circular economy is not only about using or manufacturing less plastic, but also ensuring that plastic, or any packaging material, can be reused, recycled or composted. As the world’s largest producer of printing inks, coatings, pigments and polymers, Sun Chemical is committed to offering sustainable solutions and working toward a circular economy. Visit www.sunchemical.com/sustainability for more information on how Sun Chemical is prioritizing sustainability or read our Guide to Sustainable Packaging at www.sunchemical.com/powerofpaperpackaging.
Going the Flextra mile for sustainability
Leading adhesives manufacturer H.B. Fuller has launched two new compostable adhesive solutions under its worldwide renowned Flextra Evolution brand, which o er many di erentiated advantages in terms of sustainability goals and manufacturer benefits.
“When people ask for a compostable adhesive, what they are likely asking for is a package with components that can be composted, and now this can be brought to life with the help of our compostable adhesives throughout the supply chain,” explains H.B. Fuller’s research scientist Wayne Eklund.
Increasing environmental awareness of consumers, strict legislation, and the popularized move towards a Circular Economy is significantly a ecting the way we live and do business, Eklund explains.
As a result, the flexible packaging industry is focused on addressing end-of-life issues, such as recyclability and compostability.
In flexible packaging, the adhesive holds the whole structure together, and to make the whole package compostable, the adhesive must also be compostable.
The company’s new compostable solutions for the flexible packaging market include: • Flextra Evolution SF1000CP/
XR2000CP, a solventless adhesive that o ers excellent design benefits, such as outstanding sound dampening and excellent adhesion, to a variety of biodegradable film substrates, from bar wrap to snack packaging and much more. • Flextra Evolution WB1200CP/
XR2200CP, a water-based two-part system that works best with paper-tofilm laminations, is fully compostable according to EN13432, ASTM D6400 standards , and is certified through the
Biodegradable Products Institute (BPI), North America’s leading certifier of compostable products and packaging.
Says Eklund: “These new solutions from our Flextra Evolution product line have similar performance to conventional multilayer packaging adhesives, show great printability and appearance, and work seamlessly with standard equipment.
“Most importantly, in industrial composting facilities the adhesives decompose with no toxic residue, microplastics, or other pollutants,” Eklund explains.
Compostable adhesives are di cult to formulate without the right polymers and expertise, but the innovation-driven scientists and engineers at St. Paul, Minn.headquartered H.B. Fuller are highly capable to provide unmatched knowledge and service in collaboration with customers to help them solve their adhesion challenges.
For the company, this means going beyond simply developing products that fit a particular adhesive application.
“It means thoroughly understanding customers’ businesses and processes to respond to changing consumer demands, new product designs, and upcoming regulatory and sustainability e orts,” Eklund states.
“As part of the broader market move toward sustainability, compostable flexible packaging allows converters and brand owners another tool towards reducing, reusing, composting or recycling,” says Eklund, noting that flexible packaging produces less waste than other packaging types, such as glass, use less resources for transporting the packaging, and utilizes fewer natural resources to make the final packages.
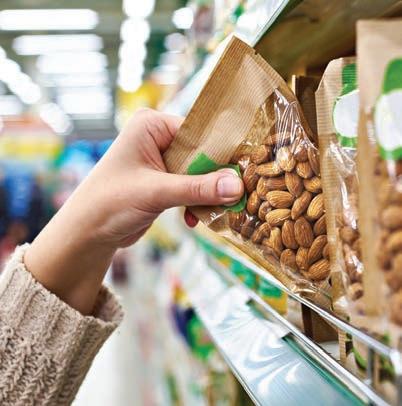
Adhesives manufacturer H.B. Fuller has just launched two new compostable adhesives for the flexible packaging market under its renowned Flextra Evolution brand.
Ink Jet Printer
SeriesUX
Next-generation leadership performance
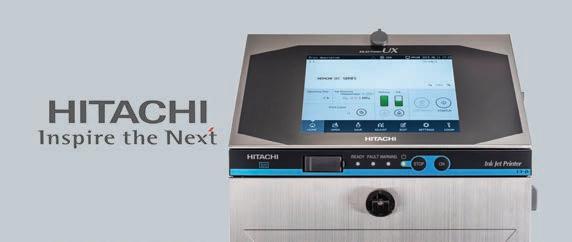
Hitachi’s UX Series continuous inkjet printers represent the pinnacle of innovation in marking and coding technology, all while showcasing