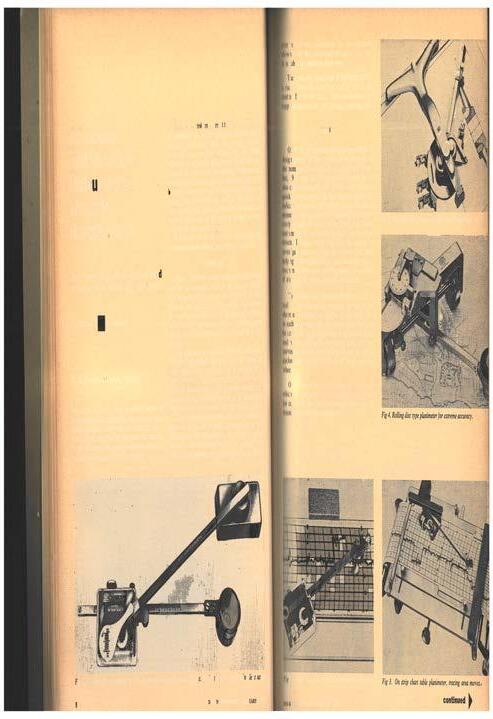
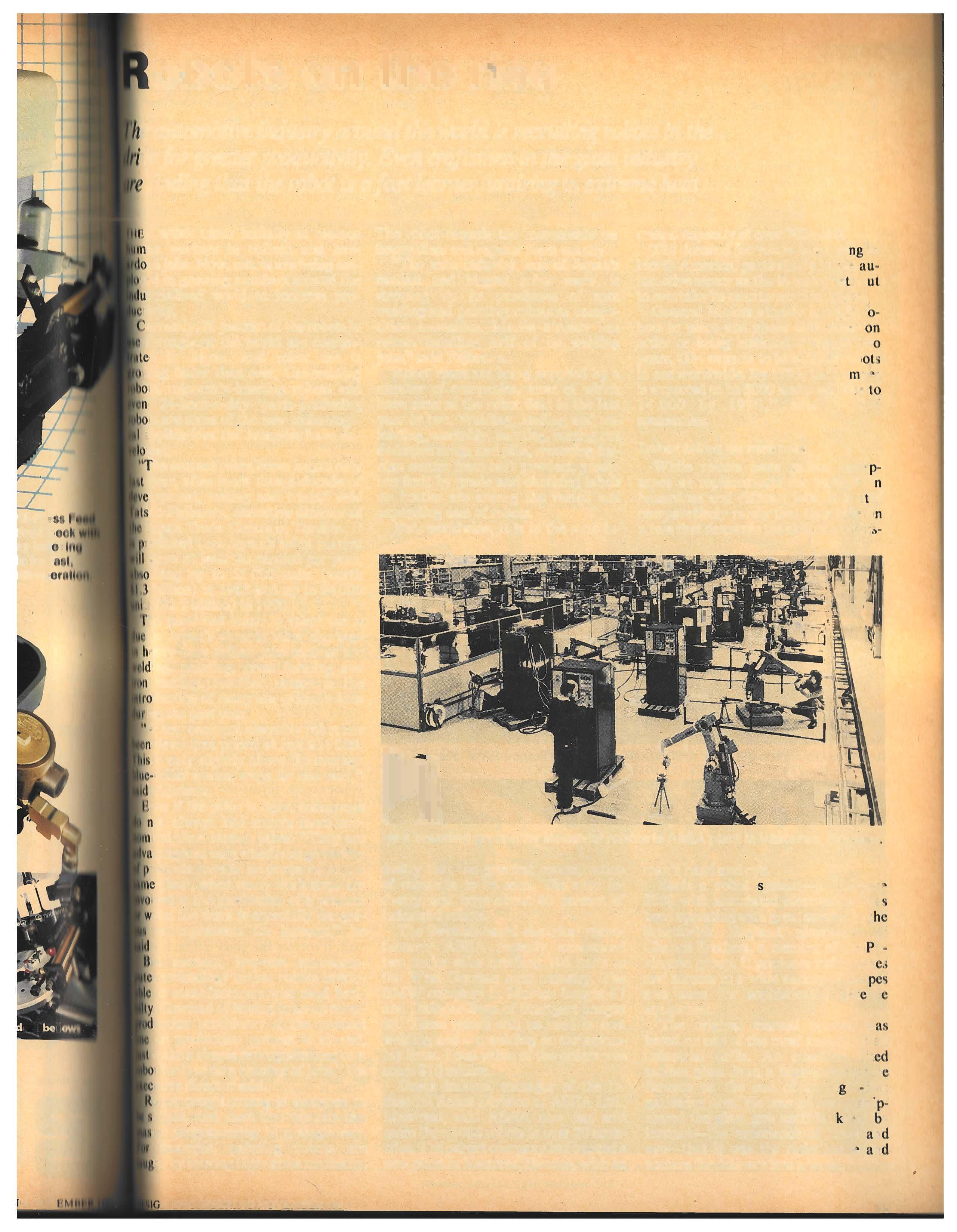
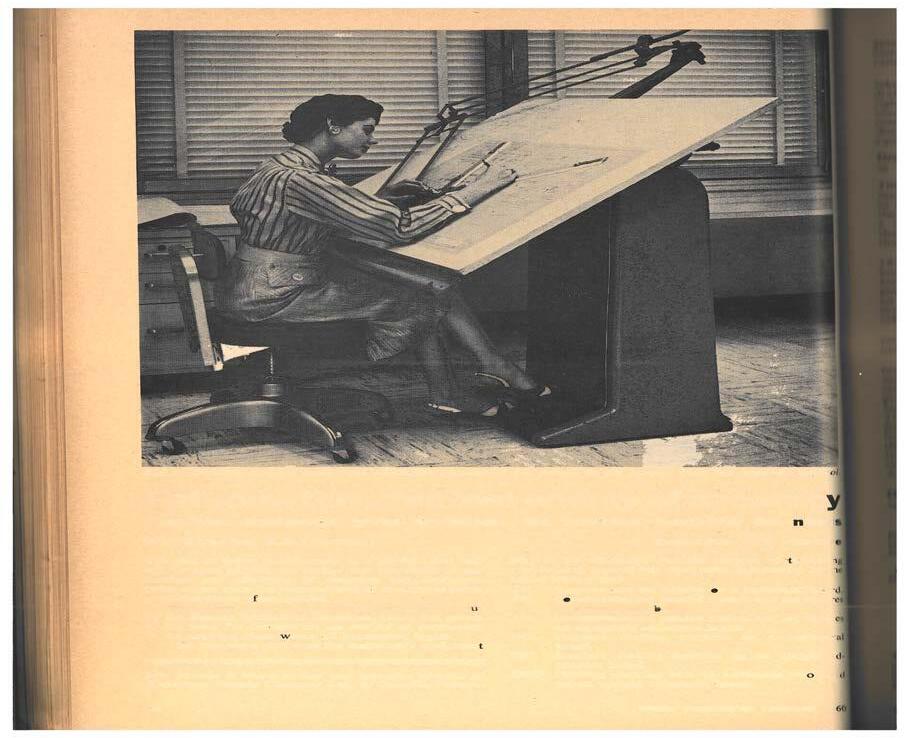
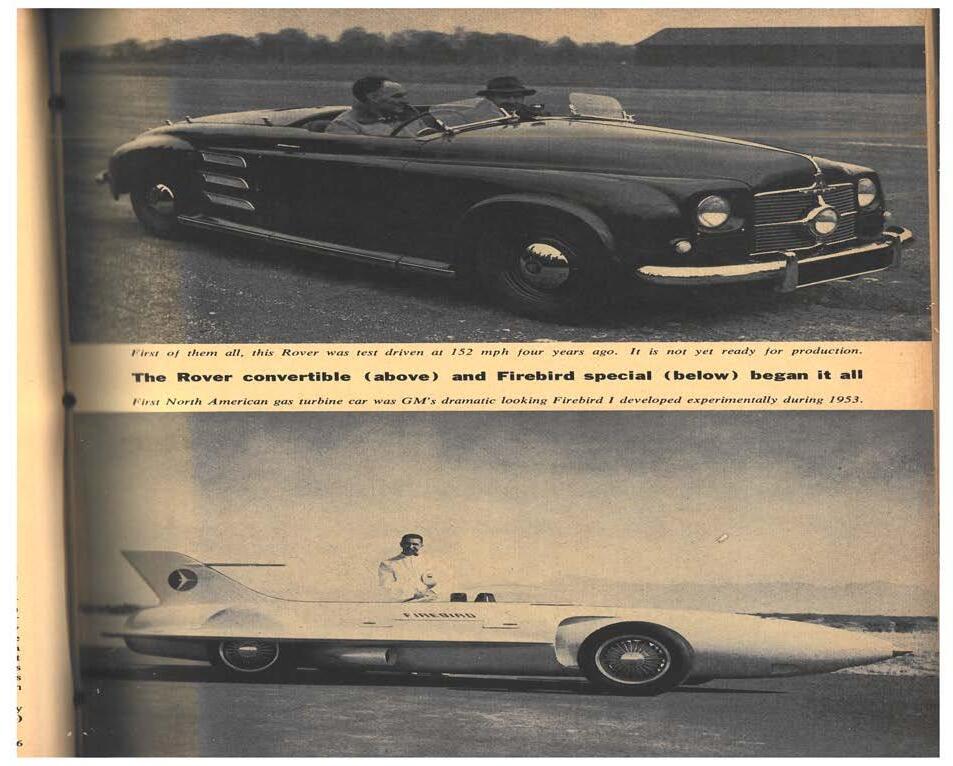
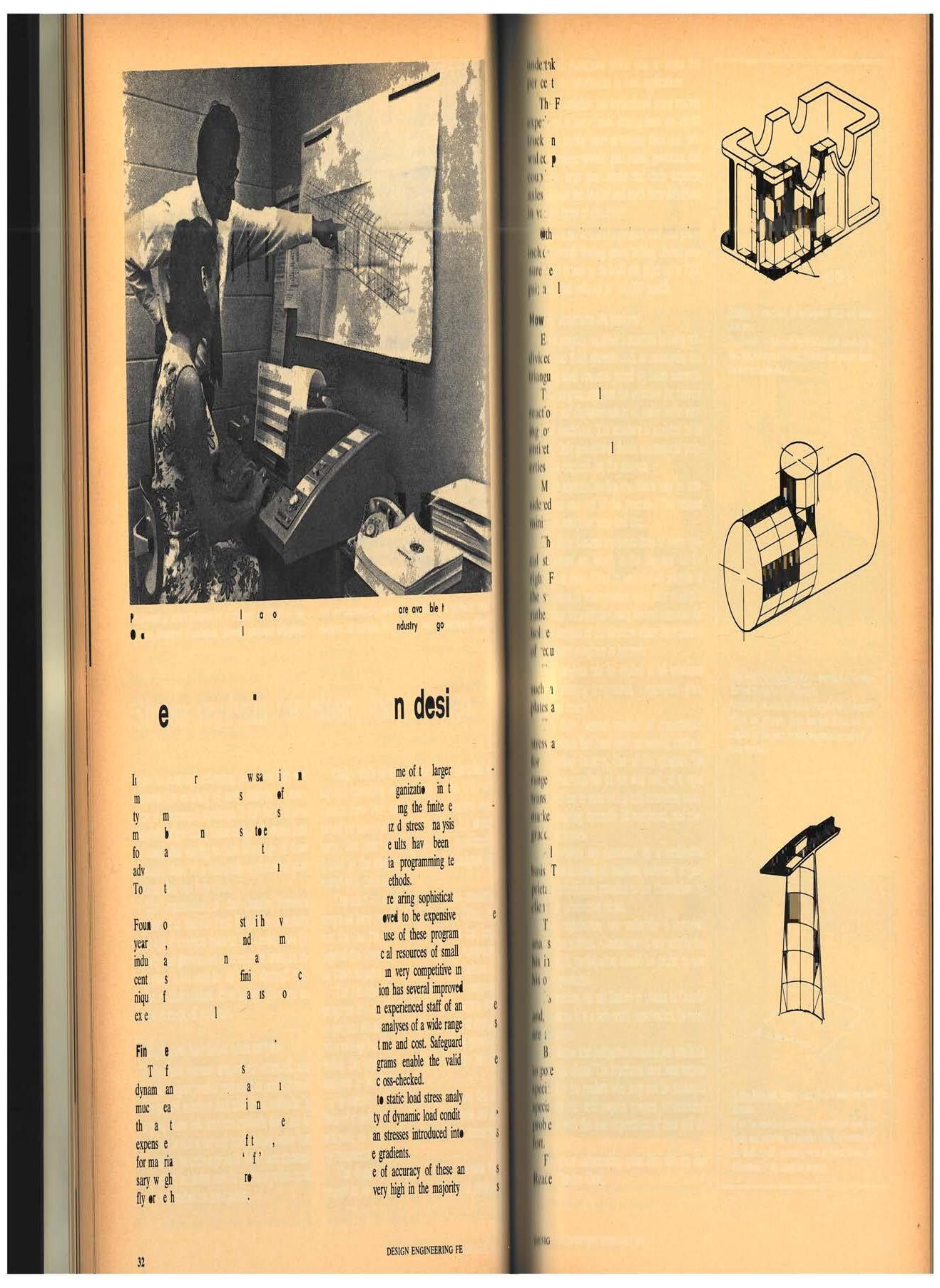
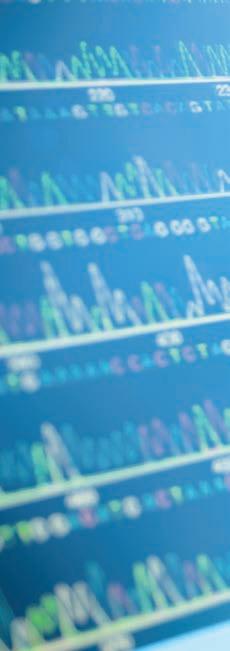
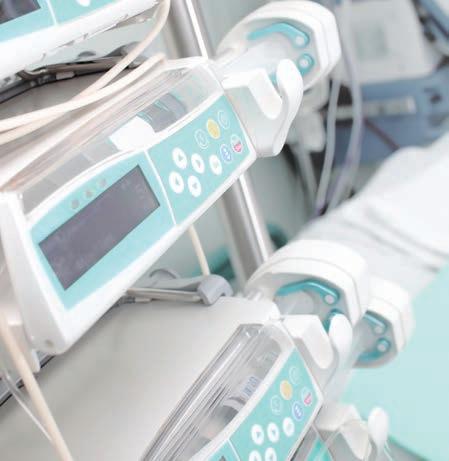
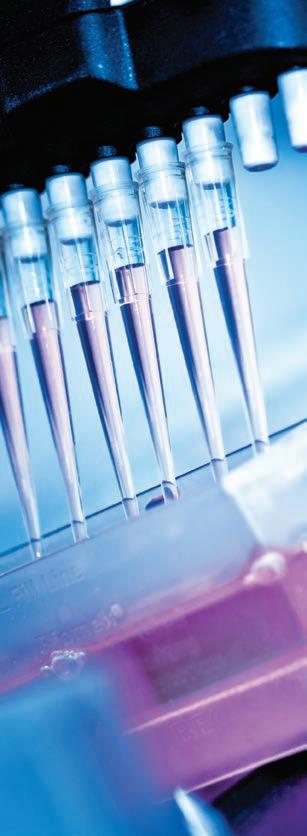
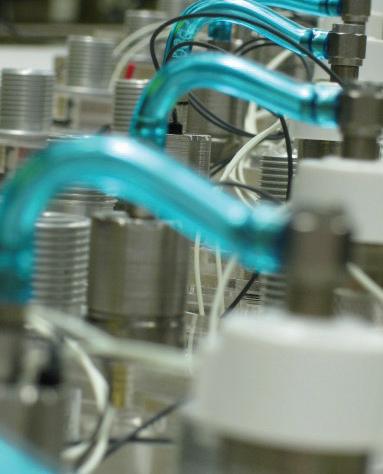
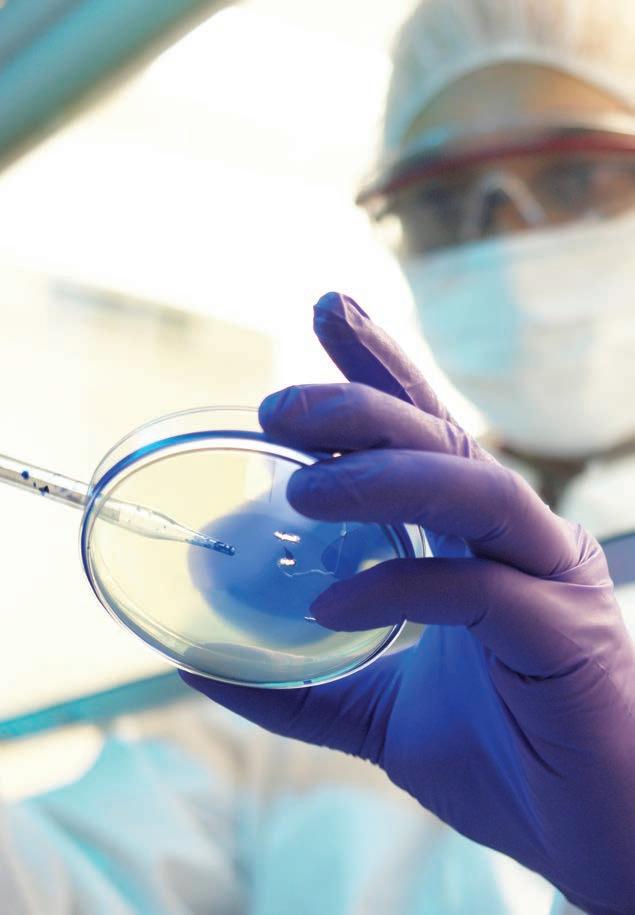
Designing efficient systems involves much more than simply understanding a few basic principles. There is a true art to balancing the specific requirements of an application in order to achieve the desired goals in the best possible way. Help us understand the unique needs of your application and together, we’ll develop something that surpasses what any of us could have done alone.
Contact your distributor to learn more, or clippard.com to request a free catalog and capabilities brochure.
Celebrating 70 years of Canadian innovation.
Nine trends driving the electrification revolution in automotive design.
esigning Victory
Additive manufacturing helps Formule ETS integrate an electric powertrain into their racer.
How localized AI is revolutionizing system design.
ransforming Homebuilding
AI-powered robotics help homebuilders build more.
ed for Efficiency
Pro-Line simplifies machine design and assembly.
Upfront New year, new board
Design News Magna awards, robot density 10 CAD Report
The highs and lows CAD 28 Idea Generator
The latest industrial products
30 Canadian Innovator Dragons snag Aruna deal
This year, Design Engineering celebrates a major milestone: 70 years of covering the evolution of design, engineering and manufacturing in Canada. Seven decades is an impressive legacy in any industry, but particularly for a print magazine that continues to deliver a physical edition.
When this magazine was first published in 1955, the world of engineering looked vastly different (see page 6). Drafting was done by hand, CAD was still decades away and automation as we know it today was the stuff of science fiction. As the pace of change accelerates, staying ahead of these trends is more critical than ever. That’s why, as Design Engineering enters its eighth decade, we are not just reflecting on our past—we are looking to the future.
To ensure we continue to deliver timely, insightful and relevant content, we have revamped our editorial board, bringing in leading voices from across the design and manufacturing spectrum. This year, we welcome:
• Kevin Bailey, CEO, Design 1st — A leader in product development and industrial design.
• Massimiliano Mor uzzi, CEO, Xaba — A visionary in AI-driven automation and robotics.
• Jayson Myers, CEO, NGen Canada — A champion for advanced manufacturing innovation in Canada.
• Dr. Mary Wells, P.Eng, Dean, Faculty of Engineering, University of Waterloo — Returning to the board, bringing an academic and research perspective to the table.
This is a living board, and I anticipate bringing in new members throughout the year to ensure that our content remains at the forefront of engineering advancements. Their expertise will help us identify the most important trends, technologies and challenges shaping the industry—ensuring that we continue to be an essential resource for our readers.
As we celebrate this anniversary, we are also looking ahead: What will Design Engineering look like in another 70 years? While no one can predict the future with certainty, one thing is clear: change is constant. Our role is to stay ahead of that change, helping engineers and manufacturers navigate the ever-evolving landscape.
Thank you for being part of this journey. Whether you have been reading Design Engineering for decades or are new to our pages, we are excited to continue exploring the future of design together.
Here’s to the past 70 years—and to the next 70, and beyond.
ANDRÉ VOSHART Editor avoshart@annexbusinessmedia.com
Editorial Board
DR. MARY WELLS, P.ENG Dean, Faculty of Engineering, University of Waterloo
KEVIN BAILEY CEO, Design 1st
MASSIMILIANO MORUZZI CEO, Xaba
JAYSON
MYERS CEO, NGen Canada
JANUARY/FEBRUARY 2025
Volume 70, No.1 design-engineering.com
READER SERVICE
Print and digital subsciption inquiries or changes, please contact Angelita Potal Tel: (416) 510-5113
Fax: (416) 510-6875
Email: apotal@annexbusinessmedia.com
Mail: 111 Gordon Baker Rd., Suite 400, Toronto ON M2H 3R1
EDITOR André Voshart (416) 510-5244 • avoshart@annexbusinessmedia.com
BRAND SALES MANAGER Trish Sutton (437) 995-4651 • tsutton@annexbusinessmedia.com
NATIONAL ACCOUNT MANAGER Ilana Fawcett (416) 829-1221 • ifawcett@annexbusinessmedia.com
ACCOUNT COORDINATOR Cheryl Fisher (416) 510-5194 • cfisher@annexbusinessmedia.com
GROUP PUBLISHER Anne Beswick (416) 510-5248 • abeswick@annexbusinessmedia.com
AUDIENCE DEVELOPMENT MANAGER Beata Olechnowicz (416) 510-5182 • bolechnowicz@annexbusinessmedia.com
CEO Scott Jamieson sjamieson@annexbusinessmedia.com
Design Engineering, established in 1955, is published by Annex Business Media, 5 times per year except for occasional combined, expanded or premium issues, which count as two subscription issues.
Printed in Canada
Publications Mail Agreement #40065710 ISSN: 0011-9342 (Print), 1929-6452 (Online)
Subscriber Services: Canada: $58.65 for 1 year; $94.35 for 2 years; Outside Canada: USA - $143.31; Overseas - $154.02; $10.00 for single copy.
All prices in CAD funds.
Add applicable taxes to Canadian rates.
From time to time we make our subscription list available to select companies and organizations whose product or service may interest you. If you prefer not to receive this information, please contact our circulation department in any of the four ways listed above.
Annex Business Media Privacy Officer: privacy@annexbusinessmedia.com Tel: 800-668-2374
No part of the editorial content of this publication may be reprinted without the publisher’s written permission.
©2025 Annex Business Media. All rights reserved. DE receives unsolicited features and materials (including letters to the editor) from time to time. DE, its affiliates and assignees may use, reproduce, publish, re-publish, distribute, store and archive such submissions in whole or in part in any form or medium whatsoever, without compensation of any sort. DE accepts no responsibility or liability for claims made for any product or service reported or advertised in this issue. DE is indexed in the Canadian Business Index by Micromedia Ltd., Toronto, and is available on-line in the Canadian Business & Current Affairs Database.
The adoption of industrial robots in factories worldwide has surged, with the global average robot density reaching a record 162 units per 10,000 employees in 2023. This figure, more than double the 74 units recorded just seven years ago, was revealed in the World Robotics 2024 report published by the International Federation of Robotics (IFR).
Canada ranks 15th globally with a robot density of 225 units—significantly above the global average.
“Robot density serves as a barometer for tracking automation adoption in the manufacturing industry globally,” IFR president Takayuki Ito says. “This year’s runner-up is China, now ranked third worldwide behind Korea and Singapore, and on par with Germany and Japan.”
Siemens looks to acquire Altair Engineering, a provider of software in the industrial simulation and analysis market.
“This strategic investment aligns with our commitment to accelerate the digital and sustainability transformations of our customer s by combining the real and digital worlds,” says Roland Busch, president and CEO of Siemens AG.
“The addition of Altair’s capabilities in simulation, high performance computing, data science and artificial intelligence together with Siemens Xcelerator will create the world’s most complete AI-powered design and simulation portfolio.”
Magna’s Dedicated Hybrid Drive system is built on a simplified platform architecture, ensuring an efficient and cost-effective operation.
Magna, a leader in automotive systems based in Aurora, Ont., has received significant awards for its innovative hybrid dr ive and transmission technologies, reinforcing its role in vehicle electrification and hybridization.
Magna secured its fir st contract for a Dedicated Hybrid Drive (DHD) Duo system with a leading Chinese OEM. This high-powered 800V system provides a longitudinal front drive solution featuring an advanced dual e-motor and multi-speed design. It ensures a smooth and efficient driving experience across all conditions, positioning Magna as a leader in hybrid technology innovation.
“Our DHD Duo system reflects our commitment to creating exceptional driving experiences that are kinder to the planet,” Magna Powertrain president Diba Ilunga says.
Part of Magna’s DHD Duo family, the system supports B to E vehicle segments, including SUVs and light buses. It accommodates various configurations—P1+P3, P2+P3, and range extender—for electric, serial and parallel dr iving modes. Production will begin in Q3 2025 at Magna’s Nanchang facility.
In addition to its hybrid drive success, Magna has debuted its Dual Clutch Transmission Eco (DCT Eco), securing a high-volume award from a European OEM. While this award is for non-hybridized internal combustion engine vehicles, the DCT Eco’s modular design allows for seamless transition to hybrid powertrains with only minor adjustments.
The DCT Eco optimizes fuel efficiency and reduces emissions for B- and C-segment vehicles. The system was already in production for South American vehicle models and was set to launch in European markets by 2025.
“We are taking an agnostic approach to supplying power to wheels, and our DCT Eco is a cost-efficient and flexible solution,” Ilunga says. “This product serves as a stepping-stone for customers looking to hybridize vehicle platforms without the need for expensive restructuring.”
Magna’s scalable Eco family addresses diverse needs, from 48-volt mild hybrids to 400-volt hybrid systems, meeting global demand for cleaner transportation technologies. |DE
BY ANDRÉ VOSHART
The design engineering profession has undergone remarkable transformations since 1955, adapting to technological breakthroughs, evolving methodologies, and shifting societal demands. From manual drafting to today’s AI-driven generative design, engineers have continually redefined the boundaries of innovation.
As generative design and AI reshape the profession, the pages of Design Engineering over its 70year history show the industry’s resilience and adaptability. Time and again, design engineers have embraced transformative shifts—evolving their tools and approaches to meet the challenges of the day.
Join us as we look back on the evolution of design engineering across the decades, exploring the innovations that have shaped the profession and the moments that continue to inspire its future.
In the 1950s and ’60s, design engineers predominantly relied on manual drafting techniques,
February 1960: A polar planimeter was essential for calculating the area of irregular shapes.
meticulously creating technical drawings by hand. This process demanded precision and a deep understanding of standardized conventions to ensure uniformity and clarity across designs.
In the 1970s and ’80s, the design engineering field experienced a shift with the integration of computer technology.
The tools of the trade included drawing boards, pencils, compasses and protractors—without conveniences like copy, paste or undo functions. Among these instruments, the polar planimeter was essential for calculating the area of irregular shapes. This device typically comprised a weighted pole, a sliding tracer arm with a pointer, a carriage with measuring wheels, and often a magnifying glass to enhance precision.
But these decades also witnessed the beginning stages of computer-aided design (CAD). In 1963, Ivan Sutherland developed Sketchpad, a revolutionary program that allowed users to create graphical designs directly on a computer display using a light pen. While not widely adopted at the time, Sketchpad laid the foundation for the CAD systems that would later transform engineering design processes.
The 1960s also marked a key period with the emergence of the design methods movement, which
sought to introduce systematic approaches to design thinking. A landmark event in this movement was the 1962 Conference on Systematic and Intuitive Methods in Eng ineering, Industrial Design, Architecture, and Communications, held in London. This conference brought together thought leader s to discuss and promote structured methodologies in design, laying the groundwork for future innovations in engineering practices.
In the 1970s and ’80s, the design engineering field experienced a transformative shift with the integration of computer technology. The introduction and g rowth of CAD software enabled engineers to create precise digital models and streamline the design process. This transition not only enhanced accuracy but also significantly reduced the time required for design iterations. (Columnist
Today, we dissect every feature of the latest CAD releases—and in the 1960s, we did the same with the latest drafting equipment.
Ralph Grabowski has extensively documented this evolution, and he highlights the highs and lows on page 10.)
During this era, the development and adoption of specialized computer prog rams allowed engineers to perform complex stress analyses more efficiently.
For instance, the creation of the DYNA3D program in 1976 facilitated the simulation of structural impacts, providing valuable insights into mater ial behaviour under stress.
In 1984, NASA initiated the Probabilistic Structural Analysis Methods project to create advanced computational tools and analysis methods for assessing the structural integrity of engine components in the Space Shuttle and future space propulsion systems.
As the 1980s progressed, the proliferation of personal computers made CAD more accessible. This widespread adoption not only improved collaboration among design teams but also paved the way for advancements in simulation and modeling techniques, setting the stage for future innovations in the field.
1990s–2000s: The digital revolution
The proliferation of advanced CAD tools and simulation software enabled engineers to create complex models, perform virtual testing and optimize designs before physical prototyping.
Software such as Pro/ENGINEER, introduced by PTC in 1988 and gaining prominence in the 1990s, offered parametric, feature-based solid modelling, allowing engineers to create
February 1971: Computer programs and an experienced staff can perform stress analyses of designs.
complex 3D models with greater precision and efficiency. This evolution enabled virtual testing and optimization of designs prior to physical prototyping.
This period also marked the rise of design thinking—a human-centered approach that emphasizes empathy with end-users, encourag ing innovative solutions tailored to their needs. The formalization of design thinking methodologies, such as the five
provided a structured framework for problem-solving.
In the 2010s and beyond, design engineering has been profoundly transformed by the integration of generative AI (gen AI) and machine learning. These technologies have enabled engineers to analyze vast datasets, facilitating the creation of optimized
Engineers are increasingly adopting sustainable and green design principles to minimize environmental impacts.
and innovative designs. For instance, gen AI design allows for the rapid generation of multiple design alternatives, each evaluated for performance and feasibility, thereby accelerating the design process and enhancing creativity
What’s more, gen AI and machine learning have significantly impacted eng ineering research and development. A study highlighted in The Atlantic in January 2025 revealed that the introduction of AI in materials science r esearch led to a 44-per-cent increase in material discoveries and a 39-per-cent jump in patent filings. But this surge in productivity also brought challenges, such as decreased job satisf action
among researchers due to the automation of idea generation. There has also been a heightened emphasis on sustainability. Engineers are increasingly adopting sustainable and green design principles to minimize environmental impacts and promote resource efficiency. This approach involves selecting eco-friendly materials, optimizing energy consumption and considering the entire lifecycle of products to ensure
environmental responsibility. As design engineering continues to evolve, the integration of AI and sustainable practices positions the profession to address contemporary challenges effectively. By embracing these advancements, engineers are better equipped to develop solutions that are not only innovative but also environmentally responsible, ensuring a sustainable future for the industry. |DE
Tracing the evolution of computer-aided design since the 1970s, from microcomputers to the cloud.
BY RALPH GRABOWSKI
CAD for personal computers first emerged in the late 1970s. The first microcomputer (as they were then called) was 1975’s Altair 8800, which you had to solder together and then program by flipping toggle switches on a front panel. It cost $2,700 in today’s dollars.
The lure of the microcomputer was strong. It promised us freedom from time-shared (and cost-shared) mainframes and mini-computers. The promise unleashed a pent-up demand that encouraged entrepreneurs to quickly advance the technology, and by the late 1970s, we could buy computers that looked like today’s. Some even came with applications more useful than the inevitable Space Invaders game.
But this unleashing had a downside. There were so many brands and standards that we became wary of jumping in; we might get stuck with an expensive asset that might prove to be a dead end. My first microcomputer in 1983 was a not-quite-IBM-compatible one that cost $12,000 (with dual floppy drives) in today’s dollars—and it went obsolete two years later.
The standards mess ended in August 1981 when IBM introduced its PC (short for “personal computer”). It was relatively expensive, but it was (somewhat) open, and because it was from IBM—the most important computer company at the time—it immediately set the standard on which we continue to operate computers today: BIOS, ISA bus, VGA graphics, Ctrl+Alt+Del, Intel CPU, DOS/Windows and so on.
The first microcomputer was the Altair 8800, which users had had to solder together.
The start of PC-based CAD CAD software for PCs began the same way.
In the late 1970s, lots of 2D CAD programs emerged from small companies, each one incompatible with the next. I think the very first one was eventually named VersaCAD. Unlike computer hardware, prices could be quite cheap, starting at $100 for a decent 2D drafting program like Generic CADD.
By the mid 1980s, CAD vendors were vying to be No. 1. VersaCAD had the advantage of being first. Architecturally oriented DataCAD was endorsed by the Amer ican Institute of Architects. Mechanically oriented CADkey offered true 3D.
But it was AutoCAD that took the lead—even though it wasn’t first, wasn’t endorsed by any organization and most certainly wasn’t 3D. But what it had was customization. Buyers of the
$1,000-program could make it work the way they worked in their niche industries, a concept unique for the times.
As with IBM’s somewhat-open PC, Autodesk’s somewhat-open AutoCAD meant that people could buy with confidence. By the late 1980s, the industry began its first attempts at standardizing on AutoCAD’s file formats so competitors could lure away customers. First with Autodesk’s open ASCII DXF format (the attempt failed) and then with the closed binary DWG format, which succeeded. Later, the building industry standardized on IFCs (industry foundation classes), a metadata exchange format devised by Autodesk with AutoCAD R13.
A Dutch company, Cyco International, was the first to figure out how to read DWG files, and so for the first time, we no longer needed to buy AutoCAD to view and
IBM introduced its Model 5150 PC in August 1981, which set the standard on which we continue to operate computers today.
print drawings. The first non-Autodesk program that used DWG as its native file format was 1996’s Vdraft from tiny software firm Softsource, followed two years later by IntelliCAD, which made DWG universal. Competitors rushed to add DWG read-and-write capabilities
This is an example of the user interface of AutoCAD Release 12, which came out in June 1992.
to their CAD programs, whether a $20,000 Catia system from France or a $0 FreeCAD from a community of enthusiasts.
We could run CAD on microcomputers
hurrah!—but it was slow. Painfully slow. At first, a single zoom or pan of the famous Nozzle drawing took five minutes. Adding Intel’s extra-cost numeric co-processor chip ($1,300 in today’s dollars) to the computer reduced the wait to a mere 30 seconds.
The breakthrough came in 1986 with AutoCAD v2.5’s near-instant zooms and pans through software-based display-list processing and the (for the times) hyper-fast 80386 CPUs. I recall an Autodesk salesman boasting that if you looked too closely to the screen, the speed would cut your nose right off.
CAD on our little computers started off cheaply enough, compared with industry giants ComputerVision and Integraph, who sold their proprietary turnkey systems for $100,000 or more per station. But then CAD on our little computers became expensive, as vendors raised prices with each new release and as we added hardware peripherals. We deployed pen plotters to produce paper copies of our electronic drawings, and the very best one—the fastest and most accurate HP Draftmaster—cost $45,000 in today’s dollars. About half as expensive were large 19inch, high-resolution (1024x768) monitors with dedicated graphics boards, but even more expensive were high-speed, large-format scanners. That thousand-dollar PC CAD program could become a $100,000 system rather quickly.
A CAD manager told me how he afforded those prices. When times were good, he would buy more CAD equipment. And when times were bad, he’d lay off some drafters and then use the savings to buy more CAD equipment.The PC CAD industry to this day never felt a recession— something I can vouch for. During my 39 years writing about CAD, I experienced none of the slowdowns that took place in the general economy.
The Windows awakening CAD programs first ran on Unix, on DOS or on proprietary operating systems, which limited their capabilities. Unix was user-hostile; DOS was neither multi-user nor multi-tasking (and stingy on memor y); and proprietary systems bled customers dry. The solution emerged from
March 1988: Ralph Grabowski reviewed five pen plotters, showcasing cutting-edge drafting technology of the era.
Back: HP
DraftMaster II and Bruning ZetaDraft 900.
Middle: HP
DraftPro, CalComp 1023.
Front: Enter Computer SP1800.
Xerox’s research lab in Palo Alto CA: the WIMP interface—windows, icons, menus, pointer— which was firstly popularized by Apple in its Lisa operating system, and then by Microsoft in Windows. WIMP removed the earlier bar riers, giving us user-friendly, multi-user, multi-tasking operating systems that handed applications near-unlimited amounts of memor y with which to work.
But WIMP was such a new paradigm that the CAD industry was reluctant to embrace it, though not surprisingly so. Windows was initially CAD-hostile. I recall being flown by a CAD vendor to its headquarters to explain “how Windows works.” It took a decade before SolidWorks 95 showed that advanced CAD could run on Windows quite well. But what made CAD plausible on Windows had nothing to do with CAD.
Early on, Microsoft chased gamers, doing what it took to make 3D interactive games run smoothly (through high frame rates). We in the CAD world got a free ride on the coattails of gamers, because those advances helped make our 3D interactive design software run smoothly. Today, we effortlessly engage in real-time rendering and benefit from instant drafting previews (like hatch patterns and fillet operations).
Within a decade, Windows and Intel CPUs were victorious. But the technology industry was dissatisfied and always on the lookout for new sources of revenues. It launched tablet-sized computers in the mid-1990s, which flopped. Not so hand-sized PDAs, like the Palm 1000, which were hugely successful but hardly handy for CAD. The Palm’s wildly triumphant 2007 offspring, the Apple iPhone, initially sucked at tasks like CAD, but competition with Google’s Android ramped up the speeds of CPUs, the capacity of memories, and the resolutions of screens to make portable CAD possible on phones and the newly revitalized tablets.
Despite the obvious benefits, the portable CAD market never made it big. So Silicon Valley came up with new ways to make money: collaboration and the cloud. But what extroverted marketing departments didn’t understand was that engineers tend to be introverts who aren’t big on the whole “real-time sharing” thing. Collaboration remains embedded in CAD but tends to involve viewing and marking up drawings once nearly finished. |DE
Ralph Grabowski writes on the CAD industry on his WorldCAD Access blog and has authored numerous articles and books.
Join us for a virtual event that brings together industry experts to share the key trends reshaping the future of design innovation and practical insights to help you stay competitive.
How simulation is helping designers and engineers test designs early on and cut development cycles.
Ross CEO and Co-Founder, Metafold 3D
How AI and new tech can help engineers advance robotic autonomy and take automation to the next level.
CEO, Xaba
Gain a deeper understanding of the new research and cuttingedge techniques in metal AM.
Vlasea Associate Professor, University of Waterloo Canada Research Chair in Sustainable Additive Manufacturing
Increasing electrification presents an opportunity to rethink how vehicles are designed.
Automotive design is undergoing a seismic shift as electrification reshapes the industry. Today’s vehicles are no longer just mechanical marvels—they are becoming mobile power hubs brimming with advanced electronics.
Electr ification is not just about swapping internal combustion engines for electric motors; it’s a comprehensive overhaul of a vehicle’s energy ecosystem. With the growth of electric vehicles (EVs) and the emergence of 48-volt systems, engineers are tasked with integrating complex electrical architectures that improve efficiency, enhance performance and support an ever-expanding array of features.
This transition presents an opportunity to rethink how vehicles are designed. Design Engineering interviewed several industry leaders about the technolog ies trends driving this evolution and the strategies engineers are adopting to overcome challenges.
The electrification of automobiles is transforming vehicle design, offering engineers unprecedented flexibility and opening the door to new innovations. “Without the need to accommodate a traditional internal combustion eng ine, auto manufacturers have more flexibility in where to distribute batteries and charging ports,” says Shawn Luke, technical marketing engineer at DigiKey. This
Meeting these demands requires a robust supply of suitable components.
shift has enabled manufacturers to prioritize passenger and cargo space, enhancing both comfort and utility.
As the market evolves, the variety of available EVs continues to expand. But challenges remain, including high costs and a lack of standardization across the industry. These hurdles are likely temporary as technology advances and production scales up. Luke is optimistic: “The cost of the vehicles will likely decrease as technology advances and production ramps up.”
The ongoing shift toward electrification also signals a growing consumer demand for advanced safety and comfort features, as well as environmentally friendly transportation options.
The shift from 12- to 48-volt electrical systems is revolutionizing automotive design. “By quadrupling system voltage, 48-volt technology boosts electric turbocharging, regenerative braking, infotainment systems and battery preconditioning for auxiliary charging,” says Frank Homann, vice-president and general manager of Connected Mobility Solutions at Molex. These advancements bring EVs closer to matching the range and convenience of internal combustion engine vehicles. In addition to boosting performance, 48-volt technology is pivotal for increasing power efficiencies across advanced systems like sensors, actuators and control units. “The delivery of higher current and voltage also is crucial to increasing power efficiencies in sensors, actuators and control units needed for advanced driver assistance systems,” he explains. But this shift brings new challenges, including increased electromagnetic interference and added complexity to wiring and harness designs
To address these challenges, design engineers must pr ioritize connector performance and reliability. Homann suggests modular platforms as a solution: “Designers should seek modular platfor ms consisting of interchangeable components, i ncluding electric motors, inverters, along with DCDC converters and batteries.” Such platforms allow f or greater flexibility and scalability, making it easier to integrate 48-volt systems into new vehicle designs.
From DigiKey’s perspective, the 48-volt bus architecture also simplifies complex power wiring harnesses, offering significant benefits for manufacturers and consumers alike. “At higher voltages, the complex power wiring harness can be simplified, further reducing weight and cost,” Luke says. This reduction not only streamlines production but also enhances the overall efficiency of EVs.
While some vehicles have already adopted 48-volt systems, many others remain to be redesigned to fully leverage their advantages.
Luke underscores the competitive edge this transition offers: “Any change that gets people on the road sooner and at a cheaper price compared to the competition is welcomed by
drivers and manufacturers.”
Gregory Green, director of automotive marketing at Vicor Corp., highlights the impact this shift will have to the sector. “The transformation of all the 12-volt loads to 48-volt loads is probably going to take 10 to 15 years,” he says. “It’s a very big trend within the industry because automakers want to reduce the weight and cost, and the 48-volt transition is a big improvement in cost and weight.”
As the automotive industry accelerates toward higher levels of autonomy, the demand for advanced driver-assistance systems (ADAS) is reshaping vehicle design.
“The main challenge is scaling the necessary
compute power in a cost-effective manner,” says Cyril Clocher, senior director at Renesas. To meet this demand, Renesas has adopted a chiplet approach—a modular design strategy that enables scalable performance without additional o verheads. “The chiplet approach extends the base SoC with an AI accelerator through standardized interconnects.”
This architecture not only allows for enhanced performance scalability but also offer s flexibility for seamless upgrades, enabling vehicles to accommodate evolving AI models. This adaptability is critical as automakers race to implement ADAS features that enhance safety, such as collision avoidance and lane-keeping assistance, while preparing for future
levels of autonomy.
Pierre Olivier, CTO at LeddarTech, emphasizes the growing importance of data in advancing ADAS and autonomous driving (AD). “Recent trends in AI show that data is increasingly becoming both the bottleneck to better AD performance and the key to reaching the level of performance required for safe and reliable ADAS and AD,” he says. The challenge lies in obtaining high-quality data for training and validating AI models—a task that traditional methods struggle to fulfill efficiently.
To address this, innovative simulation technologies are emerging as a game changer. These methods reduce the reliance on live data collection and annotation, streamlining the development process for ADAS systems.
The evolution of wireless charging in the automotive industry is accelerating with the adoption of Qi 2.0 and upcoming Qi v2.x standards. “With the arrival of Qi2.0, automotive OEMs and Tier 1 suppliers are giving automotive wireless charging solutions a major boost,” Molex’s Homann says. According to ResearchAndMarkets, the installation rate of wireless charging modules in new cars jumped from 6.9 per cent in 2020 to 44.1 per cent by mid-2024, reflecting the technology’s growing appeal. Qi 2.0 has been pivotal in restoring consumer trust in wireless charging, thanks to its 15W unified charging standard and the introduction of the magnetic power profile. “Qi 2.0 meets consumer demand for mediumand higher-power wireless charging,” he explains. Looking ahead, iterative releases in 2025 and 2026 will enable 25W and 50W wireless charging, marking a significant leap forward from the early 5W solutions.
Staying current with these advancements is essential to meet growing demand for higher-power wireless charging. While private protocols capable of reaching 40W to 50W exist, Homann notes that “alignment with WPC initiatives and standardized solutions offers a more seamless path to unified wireless charging.”
The automotive industry is undergoing a significant transformation from hardware-centric designs to softw are-defined vehicles (SDVs). This shift enables enhanced user experiences, personalization and seamless connectivity.
This evolution is fundamentally driven by factors like the facilitation of secure over-the-air (OTA) updates, modular and collaborative hardware and software, increasing silicon consolidation and integration, and the reduction of wiring harness complexity.
At the heart of SDVs is the decoupling of hardware and software, allowing for OTA updates like those in smartphones but with added layers of safety and security. Renesas’ RoX SDV platform exemplifies this approach by combining cloud-native development with a customizable simulation environment, facilitating both pre- and post-development deployment.
As vehicles incorporate more software, traditional distributed electrical/electronic (E/E) architectures str uggle to meet demands for computing capacity, reliability and OTA upgradeability.
LeddarTech’s Olivier notes that “the promises of hardware-centric reliability and maintainability are no longer met, and manufacturers are struggling to deliver quality software-based features.”
To address these challenges, solutions from enterprise computing—such as virtualization, containerization and standardization—are being adopted, necessitating a move toward centralized or zonal architectures.
The automotive industry is increasingly adopting zonal architectures to support the evolution of SDVs. This
approach simplifies vehicle design by consolidating electronic control units (ECUs) into specific zones, reducing wiring complexity and enhancing scalability. By organizing the vehicle’s E/E systems into zones, manufacturers can more easily implement updates and integrate new technolog ies.
As vehicles transition to zonal architectures, the demand for compact, durable connectors has surged. Molex’s Homann highlights that these connectors “blend the best of miniaturization and ruggedization,” enabling critical applications such as zone-to-zone communications, infotainment systems and high-resolution displays.
The shift to zonal architecture also helps reduce copper use and wiring complexity. “When you go to 48 volts, that power cable diameter goes down from six millimetres to two and a half millimetres,” Vicor’s Green says. “The copper content goes down by about two-thirds in a 48-volt zonal application you start by routing 48 volts around the car. That takes up to 85 per cent of the wire harness weight out.”
The convergence of interconnect ruggedization and miniatur ization is facilitating major innovations.
Vicor’s focus on power density has revolutionized power systems in automotive applications. The company says its compact DC-DC converters, offering up to 10,000 watts per cubic inch, allow manufacturers to reduce vehicle
weight by up to 25 kilograms and cut costs by $100 per vehicle.
“We are very comfortable saying we have the highest power density on the planet,” Green says. “Within an EV, there are several power conversions, particularly between the 800-volt main battery and the 48-volt and 12-volt systems requiring separate housings.”
He says this innovation supports miniaturization and integration. “Reducing the size and weight of DC-DC converters allows OEMs to integrate the DC-DC converter into other subsystems, such as onboard charg ing systems, creating a pathway to designs that are lighter and more space efficient.”
The shift from distributed to centralized compute architecture is transforming vehicle design. “The E/E architecture is mo ving toward a centralized compute model, reducing the number of ECUs and wiring harnesses,” Renesas’ Clocher says. By integrating multiple domains into a single module, manufacturers can streamline design while enhancing performance and reliability.
One of the challenges in this transition is ensuring robust isolation between safety-critical and non-critical functions. “The recently launched R-Car Gen 5 uses the latest technology node for industry-leading power efficiency and incorporates unique hardware-based
freedom from interference (FFI) technology for stringent isolation,” he says. This technology securely separates critical systems like brake-by-wire, assigning them redundant domains with independent CPU cores, memory and interfaces. This architecture prevents failures in non-critical domains from affecting essential safety functions.
Many automakers are also looking toward hybrid architectures—where zonal controllers handle local processing while a centralized compute unit makes high-level decisions.
The automotive industry is undergoing a significant transformation in how it approaches innovation, marked by a shift toward consolidation and collaboration.
“Over the last decades, we have seen the auto industry move from vertical integration to outsourcing,” LeddarTech’s Olivier says. Now, as software-based features become the primary differentiator in vehicles, OEMs and Tier 1 suppliers are grappling with the challenge
of meeting consumer demands for the technologies like autonomous driving.
Consolidation among industry giants, such as Stellantis, Marelli and ZF, is emerging as a critical solution to streamline resources and strengthen capabilities. But Olivier emphasizes
that collaboration, where historical competitors share platforms and technology innovations, will become “more and more prevalent.” This approach enables companies to pool expertise and resources—accelerating the pace of innovation. |DE
24_012018_Design_Engineering_JAN_FEB_CN Mod: November 4, 2024 10:51 AM Print: 11/27/24 page
How additive manufacturing helped Montreal’s Formule ETS integrate an electric powertrain into its racer. BY
KARIM JASSIR
The Formula SAE competition, operated by SAE International, brings together over 600 teams from universities around the world. In the Formula SAE competition, teams compete by presenting a business plan to judges, describing their vehicle design philosophy, creating a project cost list, and by competing in races.
Based at the École de technologie supérieure university (ÉTS) in Montreal, Formule ETS is a Formula SAE team that has been competing in the combustion category of Formula SAE for more than three decades. In 2020, the team decided to enter the electric category instead, which would mean redesigning their vehicle to one with an electric powertrain.
“Formule ETS is a serious competitor in Formula SAE, we have been reaching the podium in the combustion category for years,” says Léa Tonini, biomechanical engineering student at ÉTS and 2023-24 co-Captain of Formule ETS. “When we made the decision to switch to an electric vehicle, we wanted to do so in a way that continued to push the boundaries of motorsports and maintained our leading position.”
The team built its first electric car, MANIC-20, over two years during the pandemic as a learning experience. They then optimized the car’s design into a second iteration, named MANIC-22, for
For the new vehicle, the Formule ETS team came up with an organic-type geometry for the uprights that required a different manufacturing process.
the 2022 season, which saw the team win first place in multiple competitions.
“After a successful 2022 season we wanted to build on our vehicle to create the best performing car in the history of the competition,” says Tommy Gélinas, mechanical engineering student at ÉTS and team member involved in the powertrain design. “The main challenge was achieving our weight reduction target. Designing a car that weighed 400 lb overall would involve developing significantly lighter components for the MANIC-23 vehicle.”
One key component selected for lightweighting was the
The additive manufacturing of the uprights enabled the team to reduce upright material use by 45 per cent.
upr ights. These components connect several sub-assemblies in the vehicle, enabling the transmission of wheel motion to the suspension arms and subsequently, to the shock absorbers. All four uprights in the vehicle house an electric motor and act as supports for the planetary gear system contained in each wheel. Using additive manufacturing for the uprights would enable the team to reduce the vehicle’s unsprung mass, improving control over its dynamic behaviour.
For previous vehicles, the uprights were machined from 7075T6 aluminum on a five-axis CNC milling machine. For the new vehicle, the team came up with an organic-type geometry that required a different manufacturing process.
“We identified that metal additive manufacturing would give us the design freedom to create
lightweight parts without compromising the vehicle performance, while meeting the competition’s compliance requirements. However, we could not initially find a partner capable of producing the new uprights,” Gélinas says.
Having seen a previous par tnership between Renishaw and a Formula Student team, the ÉTS team got in touch to ask if the company could help with the manufacture of the uprights.
Renishaw stepped in to support Formule ETS by advising on design choices, assisting with topological optimization and manufacturing the final parts.
“The choice of material was a key decision during the development process,” says Carl Hamann, technical sales and business development manager at Renishaw Canada. “We provided the Formule ETS team with technical information on powders, ranging from Young’s modulus data to fatigue test results. Following the testing, the team opted for AlSi10Mg powder as it offered the required stiffness while being lightweight. The team was also able to optimise build time and support design using our QuantAM build preparation software.”
“From the outset, Renishaw showed a genuine interest in Formule ETS and the development of the new uprights,” Gélinas adds. “The company’s technical experts helped guide our design choices by giving valuable insight and advice, and we worked closely with the Renishaw team in Ontario throughout the project.”
The development of the new uprights enabled the team to achieve a significant weight reduction for both the front and rear uprights—30 and 28 per cent, respectively. This decreased the vehicle’s unspr ung mass, resulting in better control of the vehicle’s dynamic behaviour.
The team met the competition’s compliance criteria by reducing camber compliance by 18 per cent for front upr ights. Furthermore, the additive manufacturing of the uprights enabled the team to reduce upright material use by 45 per cent.
During its competition season in June 2023 with the MANIC-23 vehicle, the Formule ETS team won the Nor th American Electric Formula SAE (FSAE) competition in Michigan, coming first out of 69 teams, and scoring 919 out of a possible 1,000 points
The team also experienced success
competing in European competitions, finishing in second place in the Croatian competition FSAE Alpe Adria. 2023 marked the first time since 2001 that Formule ETS has achieved second place on European ground. The
European events also highlighted areas the vehicle could be further improved upon for future seasons. |DE
Karim Jassir is the content marketing strategist with Renishaw Canada.
How localized AI is revolutionizing real-time decisions, security and scalable solutions in manufacturing.
BY ANDRÉ VOSHART
Edge AI is reshaping how manufacturers approach decisionmaking, security and scalability in an increasingly data-driven world. Unlike traditional cloud-dependent systems, Edge AI processes data directly where it’s generated—on devices and at the source. This approach eliminates cloud latency, enabling real-time anomaly detection, predictive maintenance.
“If the AI model is running on the device, you can get the answers much faster,” says Jack Ferrari, technical marketing engineer at MathWorks. Beyond speed, this paradigm shift also enhances cost efficiency by reducing reliance on cloud infrastructure.
What’s more, a new Avnet Embracing AI survey revealed that eng ineers are embracing AI as a transformative force in product development. According to the survey, 42 per cent of engineers have already incorporated AI into their product designs. What’s more, respondents expressed optimism about AI’s potential, with nearly all (96 per cent) ag reeing that it is “somewhat-to-extremely likely” to impact key aspects of product development.
Edge AI represents a challenge and an opportunity. Integrating advanced sensors, modular AI platforms and secure data architectures requires new approaches to system design. But the benefits are transformative—supporting applications like machine vision, federated learning, and digital twins, while strengthening data security and scalability.
We’ll explore the technologies and strategies driving Edge AI’s adoption.
Edge AI is evolving from simple inferencing to federated learning, letting distributed computing devices collaborate in training models locally.
Edge AI enables manufacturers to bypass cloud latency, delivering immediate decision-making capabilities at the source. This is pivotal for real-time applications where delays could hinder perfor mance. “If the AI model is running on the device, you can get the answers much faster,” Ferrari says. “Besides time, money is another factor. If you’re not relying on the cloud, you don’t need to pay to host the model there or shuffle data back and forth.”
This real-time processing also provides a foundation for advancements in machine vision and enabling real-time anomaly detection in manufacturing.
Ferrari notes the growing relevance of deploying AI in environments where internet connectivity may be unreliable or nonexistent: “AI can be . . . deployed in remote environments where maybe there’s no internet connection or maybe it’s unreliable.”
For engineers, integrating advanced sensors and edge-capable AI systems into machines enhances data capture and
processing reliability. MathWorks has streamlined the workflow from data collection to edge deployment, ensuring seamless operation across various environments. Ferrari elaborates on the impor tance of robust testing, particularly for high-stakes environments like automotive safety.
“We want to make sure these things are tested quite heavily and released . . . responsibly,” Ferrari says. “That’s kind of our take on how Edge AI can be used in the context of a safety-critical system like in the automotive space.”
AI with federated learning
Edge AI is evolving from simple inferencing to federated learning, allowing distributed computing devices to collaborate in training models locally.
“Federating compute power at the edge allows for closed loop training cycles, shortening the time needed for updates,” says Pierluca Chiodelli, vice-president of engineering technology with Dell. “With federated learning, you can use the computing power
at the edge to train models locally across thousands of devices, creating a closed loop.”
Designing hardware and systems that support localized training and real-time inferencing helps ensure secure and efficient operations without relying on centralized cloud systems.
In the Avnet survey, the top challenge engineers foresaw was security and privacy concerns. By processing data locally, Edge AI enhances data security, especially in high-stakes environments like medical devices and autonomous vehicles. Ferrari highlights the security advantages: “If you’re just running on the edge, you no longer need to pass potentially sensitive data to the cloud, reducing attack vectors.”
For privacy-intensive environments and industries, maintaining data privacy is paramount. “For consumer electronics and medical devices, it’s very impor tant that personal information stays on the device, so you can get the benefits of the AI . . . without having to worry about where your data is being stored and if it’s being used for training other models,” Ferrari says. This not only addresses privacy concerns but also aligns with regulatory requirements and user expectations.
Comprehensive tools from providers like MathWorks and Dell are helping streamline edge AI implementation, making it accessible for engineers without extensive AI expertise. MathWorks leverages MATLAB and Simulink to provide an end-to-end workflow that simplifies the deployment process.
“Our tools make it easier for engineers to get to a proof of concept without dealing with infrastructure setup,” Ferrari says. The integration of user-friendly interfaces and pre-built functionalities let engineers focus on solving specific problems rather than navigating complex software setups. “We are basically . . . building this whole tool chain for deploying AI models to the edge in house and we’re constantly testing it through every release.”
The MathWorks approach addresses challenges engineers face when transitioning from high-level languages like
MATLAB to embedded device languages like C or C++. By streamlining these workflows, engineers can quickly move from concept to deployment.
For companies new to Edge AI, starting with small, impactful projects helps with adoption. “Start with a use case that changes and improves your business, like reducing waste or addressing supply chain issues,” Chiodelli says. “Choose a platform that allows rapid
deployment across multiple locations after initial success, cutting down on proof-of-concept time.”
Implementations can vary across industries, requiring customized approaches for sectors like automotive, aerospace and medical devices. As adoption expands, we’re seeing emerging applications in areas like semantic segmentation, virtual sensors and real-time monitoring. |DE
AI-powered robotics help homebuilders build more using flexible automation and distributed drive technology.
BY CHRIS BLADEK
Imagine a world where affordable, sustainable housing isn’t a dream but a reality.This vision faces two significant hurdles: skyrocketing construction costs and a shor tage of skilled labour. These issues are making it harder than ever to build enough homes at a fast pace and reasonable price.
Enter Promise Robotics, a Canadian startup reinventing prefabrication by enabling builders to harness the power of AI and automation. The company is bringing the most intelligent, flexible, and compact industrial robotic systems for construction, powered by a proprietary cloudbased software platform that manages the entire production lifecycle from planning to factory floor operations, scheduling, and logistics.
The platform introduces the concept of a Homebuilding Factory-as-a-Service, enabling customers to access expertise and advanced technology to streamline the building process.Through this concept, homebuilders can expect to dramatically reduce on-site assembly of homes by up to 70 per cent compared to traditional methods. For example, a single-f amily home could be assembled in about five hours and a 64-unit, three-story apartment building in two weeks.
“Automation is not very common in the construction industry, which remains heavily labour-intensive,” Promise Robotics CEO and co-founder Ramtin Attar says. “Our goal at Promise Robotics is to build foundational technology—an automation system with a tangible return on investment and without limits for wide adoption.”
Developing Promise Robotics’ innovative construction systems presented challenges. These systems require a delicate balance— achieving precision and speed while still being able to adapt to the complexities of real-world construction methods and building codes.
A pr imary hurdle was the need for a robust, high-performance control system. Specifically, real-time processing was crucial for precise robot movement and feedback control. Traditional construction relies heavily on human judgment and expertise, even today, when the most experienced workers are retiring at a rapid rate. Robotic systems, however, are not an off-the-shelf replacement; they require constant feedback and precise control to ensure accurate execution.
“One of the key lessons we’ve
learned is how to use perception to handle material variations that can occur during production,” explains Farid Mobasser, director of software at Promise Robotics.
“We have to provide feedback to the robots and adapt to unique scenarios that might disrupt the process. It’s a continuous learning curve—we test and build different structures, shapes and handle edge cases to improve our systems.”
Another key challenge was ensuring a compact, integrated design. Minimizing wiring and complexity was essential for facilitating quick deployment in a dynamic construction environment with limited space.
Laying a solid automation foundation
To address these challenges, Promise Robotics leveraged several Beckhoff products, including TwinCAT 3 automation software,
and the high-speed EtherCAT industrial Ethernet system for data transmission between controllers, drives and I/O.
TwinCAT offers an end-to-end engineering and runtime platform for all automation functionality, from machine control logic and motion control to safety and HMI. The TwinCAT development environment allows Promise’s eng ineers to leverage a wide range of programming languages, including structured text, ladder logic, and C++ to rapidly build robust applications.
EtherCAT can handle real-time communication with minimal latency—a cr itical requirement for precise robotic control. Its high-speed performance seamlessly integrates motion control, safety functions and other machine components, enabling Promise Robotics’ construction systems to operate smoothly in dynamic environments.
“The flexibility and scalability of EtherCAT was a big factor,” says Darren Brix, director of hardware at Promise Robotics. “EtherCAT really makes it simple and efficient to complete a harmonized, consistent industrial solution at a high standard.”
The CX2043 embedded PC (IPC), featuring an AMD Ryzen V1807B CPU with four cores and a clock speed of 3.35 GHz, is the backbone of Promise Robotics’ control system, managing the entire automated construction process and allowing seamless integration with all Beckhoff I/O components. Paired with TwinCAT automation software, the CX2043 becomes a high-performance PLC and motion control system, supporting both 32-bit and 64-bit modes, and providing precise, deterministic processing with the short cycle times needed for Promise Robotics’ automated systems.
A CP3924 multi-touch control panel, leveraging CP-Link 4, serves as the main interface for operators to control the robotic systems. This touchscreen interface provides intuitive control and monitoring capabilities, allowing operators to easily interact with and manage the automation system.
Precise control of the robotic arms and actuators is achieved using Beckhoff’s AMI8122 servo drives, which combine the servomotor, output stage, and
fieldbus connection in a space-saving design. Promise Robotics leveraged the compact AMI8122 servo drive to build a custom end effector paired with a KUKA robot to achieve the precision alignment required to build different structures, shapes and sizes.
The AMI8122 is part of Beckhoff’s distributed drive solutions, which bring drive technology out of the control cabinet and place it directly on the machine.
This design reduces the control cabinet size, overall machine footprint and cable length, making it ideal for dynamic constr uction environments.
By standardizing their control system and relying on a flexible and open fieldbus, Promise Robotics has accelerated research and development cycles and reduced commissioning times.
“Standardizing on a single fieldbus means our development teams can learn one system and become very proficient with it,” Brix says. “It’s allowed us to keep all of our control systems harmonized and universal, decreasing our deployment times and timeto-market.”
By adhering to open standards like EtherCAT and using a scalable control platform, Promise Robotics is building a flexible system that ensures compatibility with emerging technologies. This
standardized approach simplifies maintenance, ensures consistent operation across all machines, and allows seamless integration of new innovations—reducing downtime.
Moreover, this future-proof architecture enables Promise Robotics to adapt over time, laying the foundation for expansion.
“Right now, we’re focused on wood frame construction, which is about 80 per cent of residential construction in the U.S. and Canada. But essentially, we are
building the largest AI library for construction tasks for robotic assembly that could extended to all kinds of building assemblies,” Attar says, explaining the challenges involved in attempting to transfor m an entire industry.
“There’s a reason why automation has not scaled in this massive, multi-tr illion-dollar industry. While there have been some successful custom implementation, scalability and rapid deployment have been rather limited. Our goal is to deploy these systems very rapidly in non-custom factories, where you can take over a warehouse, turn on the lights, and start returning profit on your capital.”
While challenges remain, the company’s commitment and optimism for the future of construction has only been buoyed by initial results.
“Other industries have been successfully deploying automation and robotics in manufacturing processes over the past 50 years,” Brix says.
“We’re doing the same very quickly now, in a compressed timeline. We’ve made great progress, but there’s still lots to do— and that’s the fun part.” |DE
Starting at $278.00 (EKI-1221-CE)
Advantech serial-to-Ethernet Modbus gateways provide easy integration of Modbus RTU/ASCII and Modbus TCP networks for convenient centralized machine communication management. Use these Modbus gateways to make quick and easy connections of multiple isolated serial devices to an industrial Ethernet network.
• Two 10/100 Ethernet ports for LAN redundancy
• Up to four software selectable RS-232/422/485 ports
• Up to 16 peer connections under Modbus Client mode and up to 32 peer connections under Modbus Server mode on each serial port
• Up to 64 simultaneous Ethernet connections
• Easy setup and troubleshooting via easy-to-use web interface that provides configuration, monitoring, and troubleshooting tools
BY DAVID GERSOVITZ
The continuing skills shortage facing Canadian industry has many manufacturers scrambling to cope. Facing its own skills challenges, Pro-Line Automation Systems in Woodbridge, Ont., is using new technology to help simplify design and assembly of its products for labour-saving benefits. Festo’s CPX-AP-I automation system and SDBT-MSX magnetic proximity switch fit the company’s strategy to make building its next generation of products “simpler and faster by being more efficient.”
Pro-Line is a leading OEM of CNC and other large fabricating systems used by window a nd entry-door manufacturers for residential, commercial and industrial buildings—principally sawing, drilling and joining PVC and aluminum for framing and finishing of all styles and sizes. Since the 1990s, the company has carved a large footprint in the southern Ontario fenestration industry. It has built out from that, doubling its sales the past five years and hoping to double them again over the next two to three.
Part of its success comes from developing systems that better align output to customers’ needs than the universal machines of its mainly European competitors.
“Most of the high-rise buildings built in Toronto over the last 10 to 15 years are done on machines we produced for all of the players in that business,” Pro-Line president and CEO Vinode Ramnauth says.
“One European-made universal machine can produce 30 windows a day, while two of our machines working next to each other can produce one floor per shift for those high-rise buildings.”
Paradoxically, many of those competitor machines are too large and complex for smaller window manufacturers, who tend to lack the capacity to service such equipment, so Pro-Line has machines sized for their needs.
Considering the ongoing skilled labour shortage, Ramnauth says his objective is to make the design of new models simpler and, in doing so, build machines faster and get more out of ProLine’s people.
Pro-Line is an eager early-adopter, so when it likes a technology like the SDBT-MSX switch, tends to run with it. (It’s already the biggest user of the switch in North America.) Employing SDBT-MSX with its auto-teach feature allows Pro-Line to dispense with a mandatory post-commissioning adjustment for all the proximity switches on a machine or production line, saving time.
“I like the innovativeness they (Festo) have with new technology, which is where we want to go,” Ramnauth says. “We want to take our machines to the next level. And just as our customers have issues with personnel, we have our own. Some of the new products we are testing with Festo eliminate some of the time spent by high-level assembly guys.”
Pro-Line’s automated machining and fabricating centres provide window and door manufacturers with high volume production capacity for cutting, fabricating and joining framing materials in window and door assembly.
A prime example of this rethink is shifting the design of new products to remote I/O networking with the Festo CPX-AP-I automation system, beginning with a four-point parallel welding machine for vinyl used for framing windows, patio doors and sashes. This machine, ordered by a local customer, is big—six metres wide and four metres deep. Next up is a casement window production line— six metres wide and 22 metres deep—with three sections and automatic transfer between them.
Illustrating the labour shifting possible with remote I/O, Ramnauth cites an existing model, where “an electrician normally spends about 40 hours doing wiring.” With remote I/O, “that
guy will spend about five hours. I can have lower-skilled people doing all the work up to the point where (the electrician) only has to spend half a day on it and it’s completed.” Total wiring time is reduced as well.
A CPX-AP-I network consists of a bus interface and, in the vinyl welder, input modules. Key components like the Festo VTUG valve manifold and SDBT-MSX sensors connect to the PLC via the CPX-AP-I module as opposed to having to be connected directly to the bus backbone. It’s a simpler, low-voltage system to install. “You don’t need to have an electrician wire each piece to a junction box,” Ramnauth adds.
Controls engineer Andrew Nauth says the move to remote
Employing Festo’s CPX-AP-I low-voltage network in its latest CNC centres and production lines allows Pro-Line to use skilled labour more efficiently. Key components like the VTUG valve manifold (top) and CPX remote I/O modules (below) connect to the PLC via the CPX-AP-I Control module rather than to the bus backbone.
I/O has been flawless—and the benefits aren’t limited to labour. Valve terminals and I/O modules can be located right at the function they are actuating rather than being concentrated at one end where they often must be sized larger.
“We’re trying to save space in a lot of our designs,” he says, “so being able to mount the valve terminal and I/O modules where we want and having them on the same network is an advantage to us.” It also means less tubing and electrical lines, and shorter cycle times.
CPX-AP-I also facilitates troubleshooting. Nauth says Pro-Line staff or customer s can recognize a malfunctioning device just by looking at its status on the module rather than having to go back and forth to the electrical cabinet or HMI to see if a signal is reaching the PLC. That’s especially important when devices are difficult to reach or even see. When replacing that device and cable, there’s no need to reset parameters or make hard wired connections; swapping in a new one “is basically plug and play, reducing the requirement for specific skilled labour, time and avoiding human errors.”
A CPX-AP-I network can be used for remote I/O and IO-Link.
Festo’s CPX-AP-I lineup includes an IO-Link Master. Nauth says Pro-Line has interest in IO-Link for future projects, particularly for connecting analog devices to a CPX-AP-I network so it can eliminate those remaining device cards in the PLC. It would also be able to pre-configure the settings of IO-Link devices and transfer the parameters automatically to replacement components.
With the SDBT-MSX proximity switch, the auto teach-in function makes it essentially set-it-and-forget it technology. When the machine is powered on the first time and completes just four cycles, the auto-teach feature automatically sets the correct, final switching point. No follow-up adjustment is required. That may only save a few minutes per switch, but with dozens of switches on a large machine, the minutes saved add up. Sometimes, those switches are in difficult-to-reach locations on a machine, or worse, the fine-tuning has to be done at the end user, adding travel time and expense.
“That’s a huge time-saver,” Nauth says. |DE
David Gersovitz is a Toronto-based writer focused on manufacturing and process technologies. This feature was submitted by Festo.
Beckhoff’s ASI8100 stepper motor with built-in drive adds another space-saving tool to the company’s broad range of compact drive technology products (up to 48 V DC). The ASI8100 series combines a stepper motor, stepper motor output stage, and fieldbus connection in a fully integrated design. These EtherCAT devices mount directly on the machine without a control cabinet or upstream I/O, allowing for highly
compact, control cabinet-free machines. With the integrated travel path control, simple function blocks for motion applications are built in.
RealMan Robotics has unveiled its ultra-lightweight robotic arms. Designed with cutting-edge materials and advanced motion control, these arms enable lifelike movements, making them ideal for manufacturing, service industries and even domestic assistance. Additionally, RealMan’s robot
integrated actuator combines motor, sensors and control systems in a compact design. Its high-performance capabilities enhance robotic efficiency across a wide range of applications, from industrial automation to collaborative robotics.
Orbex Group has introduced a new family of compact wheel drives (CWD), increasing its offering of precision motion solutions. The 600W CWD-500 and 1,200W CWD-1000 are integrated motor, gearbox, encoder and wheel combination units, designed to facilitate easy application in compact robotic applications like autonomous mobile robots and automated guided vehicles. Their design also offers excellent power and torque density and high axial and radial load capacities, while quality construction provides smooth, precise and reliable motion for up to 30,000 hours.
igus has released its iglide JPF, a self-lubricating plain bearing material delivering high wear resistance and durability without the use of PFAS or PTFE. This dry-running, wear-resistant polymer offers comparable friction and wear performance to iglide J, and its development is a response to growing global
regulatory pressures to limit the use of harmful substances in industrial and consumer products. The company’s goal is to transition its standard materials to PTFE-free formulations.
Novotechnik has introduced the MC-1 2800 44-turn magnetic encoder with IO-Link output interface. The patented non-volatile technology retains turn count even when power is lost and reports correct count when power is restored. Key specifications for the MC-1 2800 include measuring range of 15,840° (44 turns), measured variable information of angle, turns, speed and limit switch points. Measurement rotational speed is from 0 to 546 rpm. Resolution is 16-bits. Absolute linearity is ≤ ±1°. Repeatability is ≤ ±0.1°.
Kollmorgen has announced the latest update to its SafeMotion Monitor (SMM) firmware: SMM2.0. This upgrade allows OEMs to leverage SMM functional safety features with more encoder and motor types to support a wider range of applications such as material forming, multi-axis measurement equipment, food processing and food packaging. It will now be compatible with all motors that feature any HIPERFACE-DSL rotary-safe feedback system.
Festo has introduced the VTEP (“the world’s first proportional valve terminal”), an ideal solution for flexible gripping, web tensioning, force-controlled polishing, precision piloting, dispensing, dosing and diaphragm pump control. It provides closed-loop control of moderate air flow and comes in two-, three- and five-valve variants, which can control up to 10 channels. Each valve contains an integrated pressure-temperature sensor, an airflow control algorithm and four digitally controlled 2/2 piezoelectric cartridges.
AutomationDirect has added CITO StackFlow modular process valves. This system of high-flow, robust components can stack together to form a valve bank assembly. Each module includes common inlets at each end and an outlet discharge at the bottom. Manual and solenoid valves are available, as well as distribution blocks that can all be included in the same assembly. Port adapters are sold separately, allowing multiple threaded connection options to the inlet or outlet port. Flow control outlet port adapters allow fine-tuning fluid flow out of the discharge.
WAGO’s updated 750-1632 proportional valve module is a compact, high-performance solution that offers improved response time, superior precision and better diagnosis. Features include a large current range, a minimal width of just 12 mm, and the capability to have two single coil valves or one dual-coil valve controlled either unidirectionally or bi-directionally, offering high repeatability.
Teledyne DALSA has introduced its Z-Trak 3D Apps Studio, a suite of software tools developed for in-line 3D machine vision applications. Designed to work with Teledyne DALSA’s Z-Trak family of laser profilers, it simplifies 3D measurement and inspection tasks on production lines. Capable of handling 3D scans of objects with varied surface types, sizes and geometric features, it’s ideal for automation applications across a range of industries including electric vehicles, automotive, electronics, semiconductors, packaging, metal fabrication and many more.
NewTek vented M-375 Series of Linear Variable Differential Transformers are used in hydraulic cylinders to precisely measure position and monitor the position of pistons. This capability helps prevent piston over- or under-extension, ensuring safe and high-precision operation. In industrial automation applications, these miniature AC-operated sensors provide feedback on cylinder positions, facilitating accurate control in manufacturing lines and injection molding machines.
Emerson has launched its new AVENTICS DS1 dew point sensor to monitor dew point, temperature, humidity levels and quality of compressed air and other noncorrosive gases in real time from one device. The DS1 can help operators detect and mitigate excess moisture in its early stages and prevent moisture-related equipment damage. By optimizing air quality in this way, operators can better control processes, extend pneumatic component life, ensure regulatory compliance and reduce maintenance and unplanned downtime.
Aruna Revolution secured a deal with Dragons Michele Romanow and Manjit Minhas, solidifying its mission to redefine the disposable hygiene industry with innovative compostable menstrual products.
Dur ing the January 9, 2025, airing of Dragons’ Den (episode 12), the Aruna team came in asking for $250,000 for a 10-per-cent share in their business. After some negotiations, Romanow and Minhas came together and offered $300,000 for 25 per cent of Aruna Revolution, which was accepted.
Aruna Revolution is tackling the significant environmental impacts of traditional disposable hygiene products, which contributes to global waste, water pollution and soil degradation. In North America alone, 20 billion menstrual products and their packaging end up in landfills annually.
The company’s compostable menstrual products, crafted from plant-based fibres, align with sustainability goals while ensuring accessibility and equity for diverse communities.
In the September 2024 issue of Design Engineering, Aruna Revolution CEO Rashmi Prakash was named as one of the Top 10 Under 40. At the time, she said that she has learned the importance of resilience and adaptability in the face of challenges in her role as CEO.
“Leading a startup in the sustainable product space has taught me to navigate complexities in manufacturing, regulator y compliance and market penetration without
compromising our core values of sustainability, responsibility and inclusivity,” she said.
Aruna says its products help reduce global waste and pollution. By 2030, the company predicts that its period products could prevent the release of as much carbon dioxide as nearly 2,000 trees would absorb over 10 years. Aruna also says its period products help organizations comply with regulations requiring free menstrual products in employee washrooms, offering an eco-friendly solution that meets legal obligations while supporting sustainability goals.
Prior to Aruna, Prakash’s career contributions spanned from developing assistive technologies for individuals with disabilities to enhancing the safety of surgical devices and pioneering surgical robots for MRI-guided breast biopsies
“One of my most memorable
moments was developing a modified gaming controller for Timothy, a 10-year-old who had lost fine motor control due to hypoxia,” she said during her Top 10 Under 40 interview. “This controller allowed him to enjoy video games just like any other kid, something he had never been able to do before.”
Aruna Revolution integrates Indian heritage with moder n innovation. The company’s name, Aruna— symbolizing a new dawn— reflects a commitment to holistic solutions inspired by cultural traditions. Prakash’s journey from Bengaluru to leading a globally recognized Canadian company showcases the power of blending her itage with cutting-edge technology to address global challenges like waste management, environmental deg radation, and menstrual equity. “Our Indian-inspired
name and values guide us as we create products that serve individuals, communities and the planet,” Prakash adds. Headquartered in Nova Scotia, Aruna Revolution represents the power of women-led innovation. Its team, composed of engineers and experts from institutions like the University of British Columbia, University of Manitoba, Dalhousie University and Saint Mar y’s University, brings expertise and passion to tackling one of the healthcare industry’s most critical issues.
Aruna Revolution’s feature on Dragons’ Den spotlight positions the company as a pioneer in transforming disposable hygiene into a circular, inclusive industry while setting the stage for a more sustainable future. |DE
Watch Aruna on the season final episode on CBC Gem at gem.cbc.ca/dragons-den
Langley, British Columbia
April
Ottawa, Ontario May