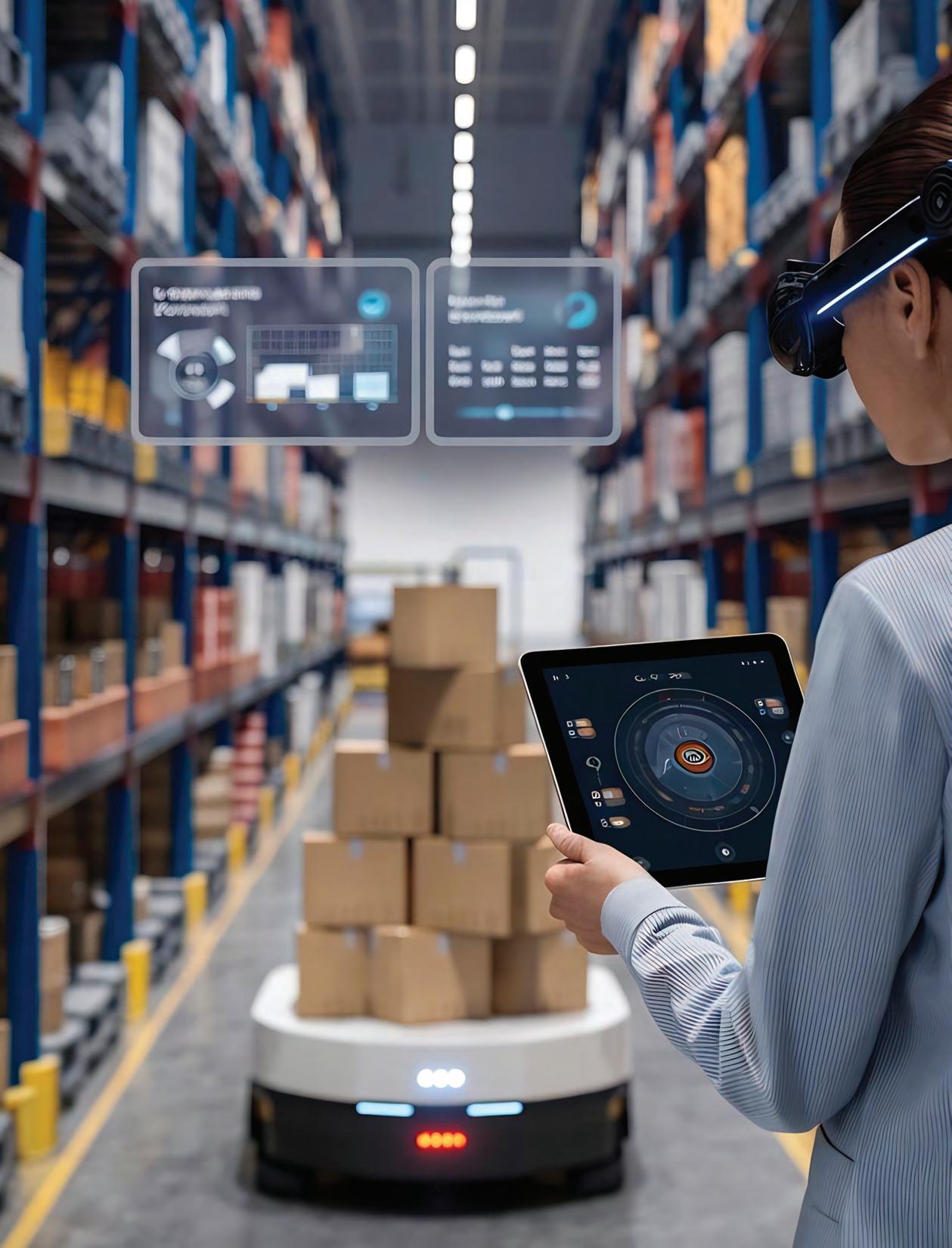
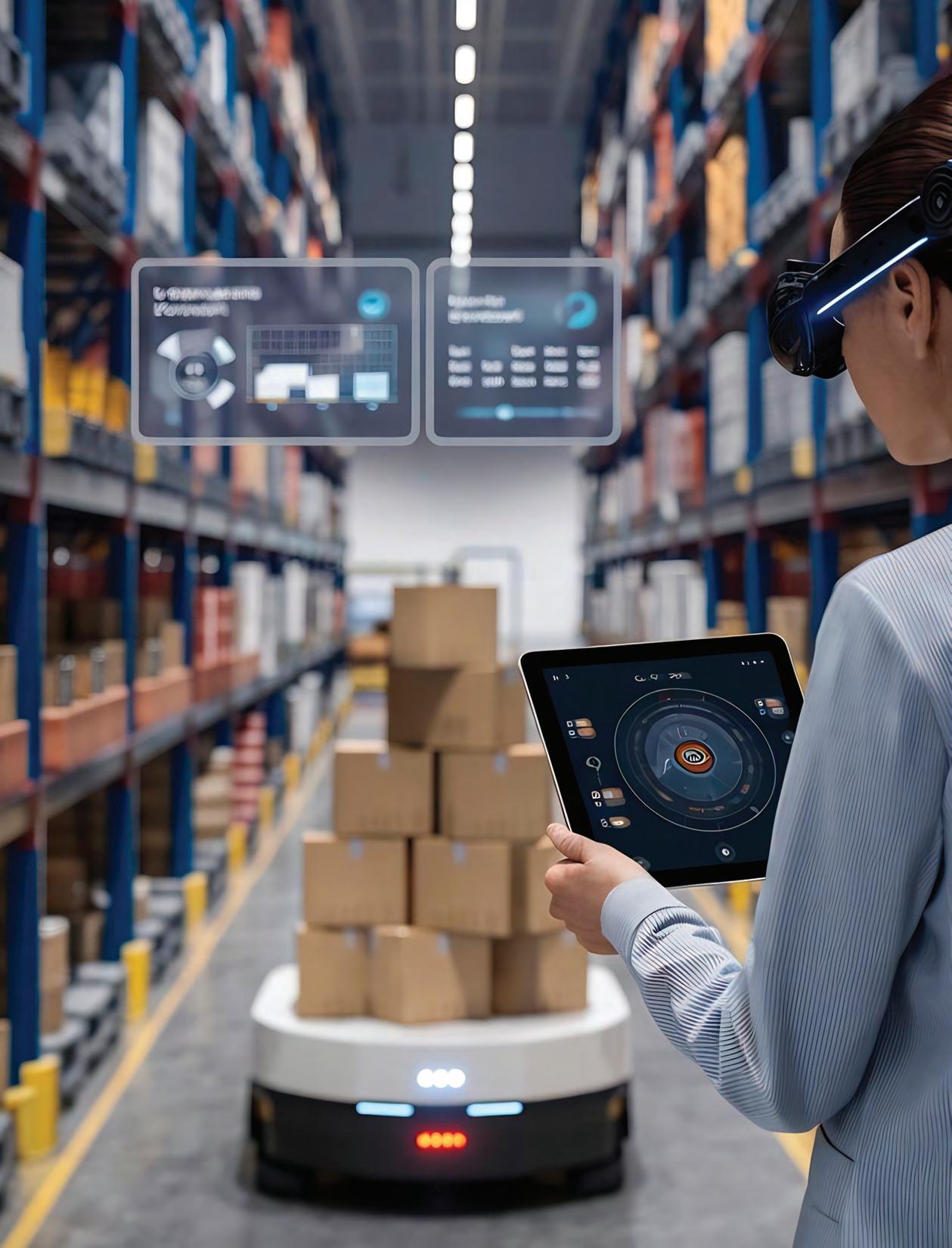
SUPPLY CHAIN OUTLOOK
AI expected to continue making waves in global supply chain in 2025
› State of logistics
› Southern Alberta supply chain
› The year of labour disruptions
• Daily scheduled Canada & USA departures
• Overnight LTL by 5PM standard arrival times to select destinations
• Priority PlusTM overnight LTL by noon between Toronto & select USA cities

• Industry-leading, over the road cross border transit times
• Simplified process with express border clearances via automation
• Online ordering, real-time tracking & 24/7 customer support
99.21% ON-TIME DEPARTURES 92.15% ON-TIME ARRIVALS
1.800.409.2269

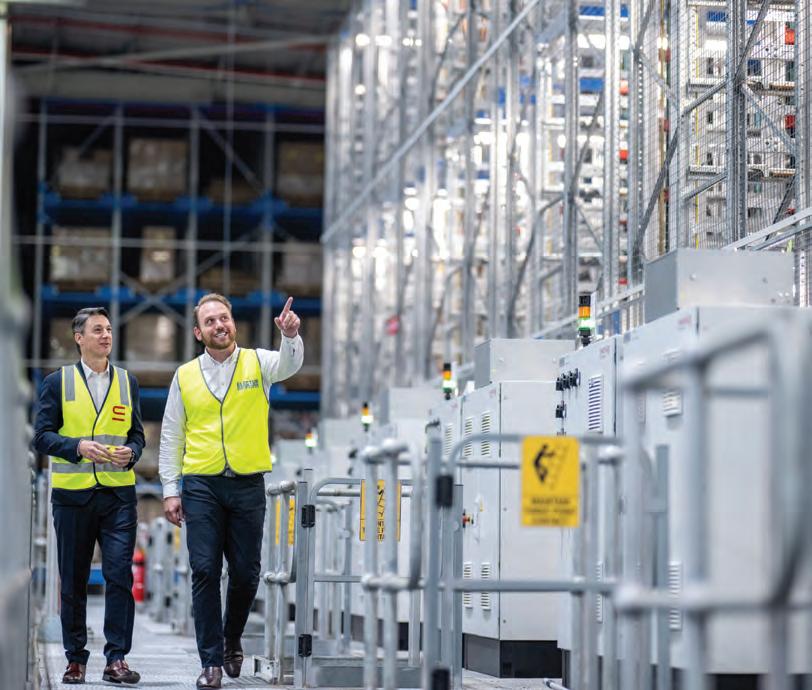
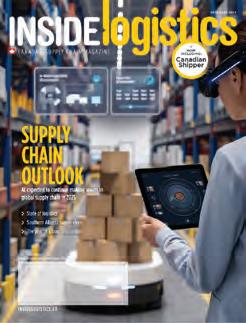
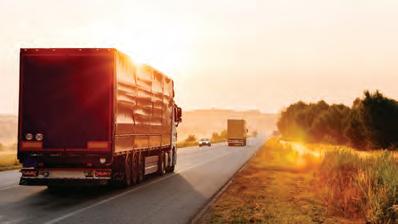
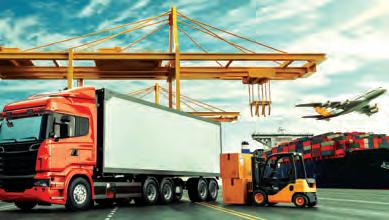
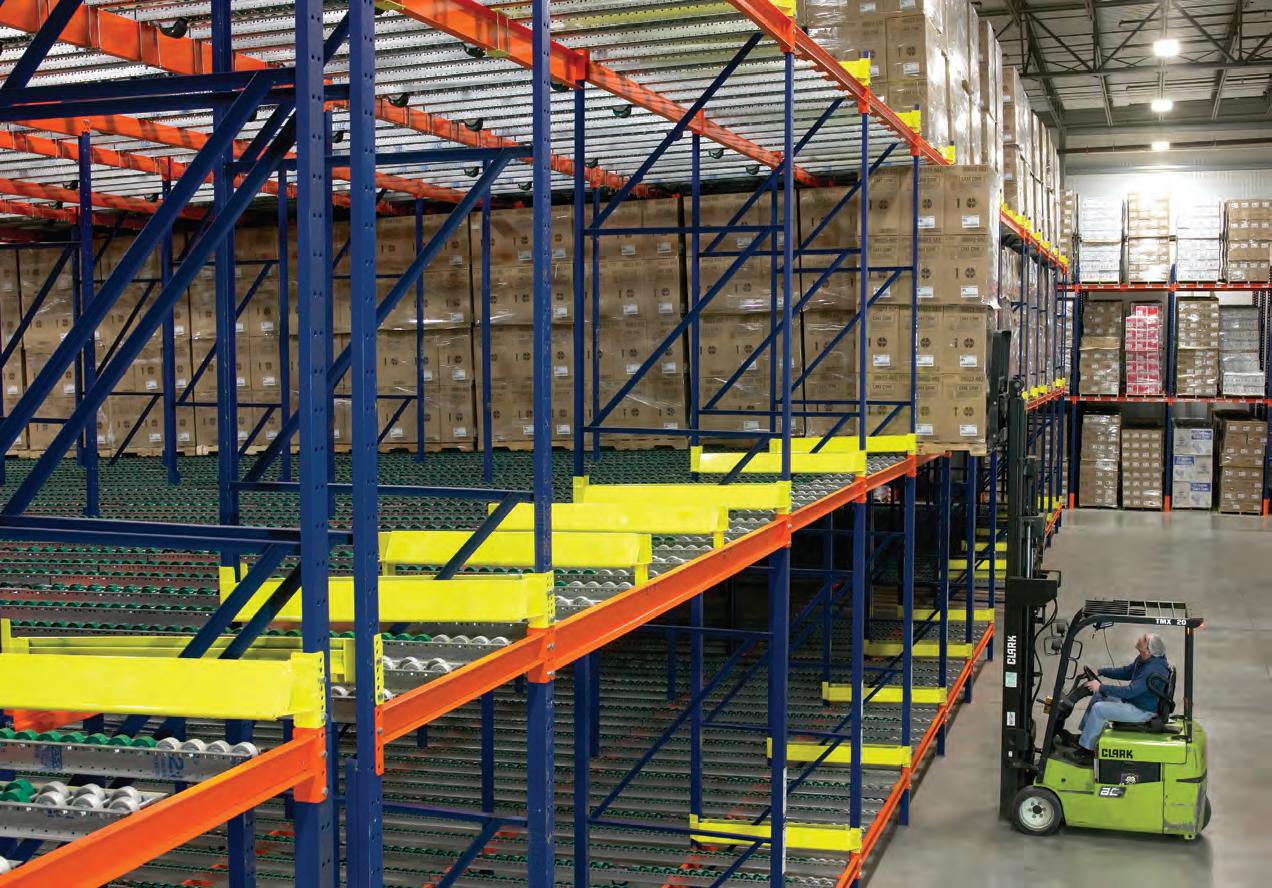
Engineered for Strength, Designed for Flexibility –3D
Storage Solutions Delivers More Than Just Racks
3D STORAGE SOLUTION S
For the past 30 years, 3D Storage has been designing and constructing warehouse storage solutions for a wide variety of industries including,
• Manufacturing
• Third Party Logistics (3PL)
• Retail
• Distribution Centers
• Cold Storage
• Ecommerce
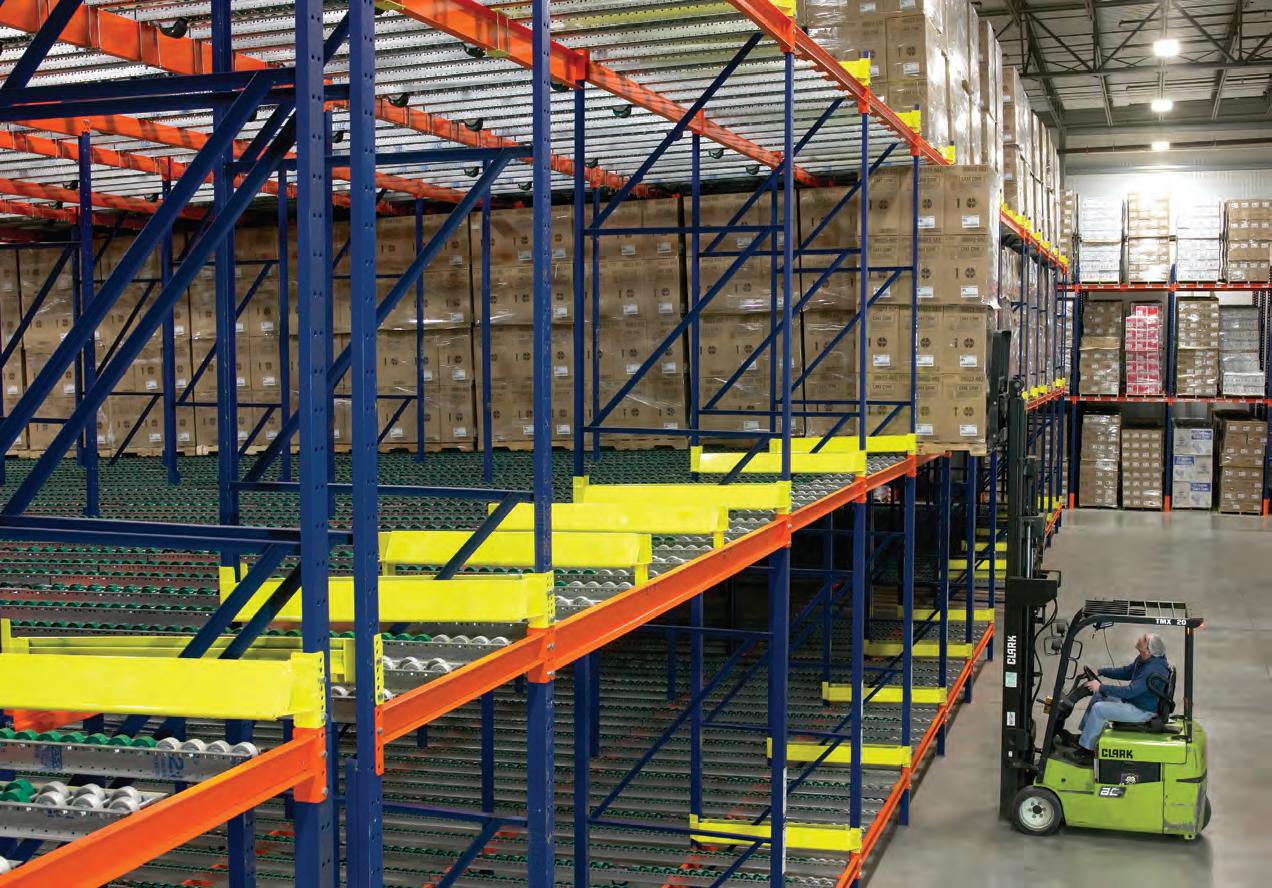
Publisher | Delon Rashid (416) 459-0063 delon@turnkey.media
Editor | Derek Clouthier (416) 605-5346 derek@turnkey.media
Contributing Writers | Norm Kramer, Christian Sivière, Victoria Jones
Creative Director | Samantha Jackson
Video / Audio Engineer | Ashley Mikalauskas, Nicholas Paddison
Sales | Delon Rashid, (416) 459-0063 delon@turnkey.media
Peter Bulmer, (585) 653-6768 peter@turnkey.media
Production and Ad-ops | Tracy Stone tracy@turnkey.media
Inside Logistics magazine is published by Turnkey Media Solutions Inc. All rights reserved. Printed in Canada. The contents of this publication may not be reproduced or transmitted in any form, either in part or full, including photocopying and recording, without the written consent of the copyright owner. Nor may any part of this publication be stored in a retrieval system of any nature without prior consent.
Canada Post Canadian Publications Mail Sales Product Agreement No. 43734062
“Return Postage Guaranteed” Send change of address notices, undeliverable copies and subscription orders to: Circulation Dept., Inside Logistics magazine, 48 Lumsden Crescent, Whitby, ON, L1R 1G5
Inside Logistics magazine (ISSN No.: 0025-5343 (Print); 1929-6460 (Digital) is published six times per year by Turnkey Media Solutions Inc., 48 Lumsden Crescent, Whitby, ON, L1R 1G5
From time to time we make our subscription list available to select companies and organizations whose product or service may interest you. If you do not wish your contact information to be made available, please contact us.
President & Managing Partner | Delon Rashid Head of Sales & Managing Partner | Peter Bulmer
Corporate Office
48 Lumsden Crescent, Whitby, ON, L1R 1G5


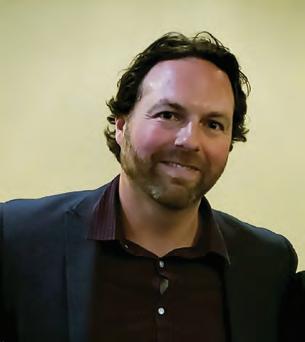
Overcoming challenges in 2025
IN OUR FINAL ISSUE OF THE YEAR
, it’s fun to reflect on what shaped the supply chain sector in the last year and anticipate what will influence the industry in 2025. We explore this topic in our Outlook 2025 feature on page 16, focusing primarily on the role of AI and other emerging technologies. However, a look at what our readers engaged with most online, coupled with recent developments—such as the U.S. election, the Canada Post strike, and ongoing uncertainties in Ukraine and the Middle East— indicates that the coming year will significantly impact the global supply chain.
U.S. TARIFFS AND CANADIAN TRADE IMPLICATIONS
The recent election of Donald Trump, and his proposed tariff policies, is already shaping up to be a challenge for many countries, Canada among them. For example, Trump’s intention to implement a 25 per cent tariffs on Canadian goods coming into the U.S. starting Jan. 20, 2025 will certainly have an impact on both countries’ economies, trade and overall relationship.
LABOUR DISPUTES DOMINATE HEADLINES
An overview of the most-viewed stories on InsideLogistics.ca since our website relaunch reveals a clear trend dominating Canada’s supply chain in 2024 – labour disputes. We addressed this in our previous issue, but since then, another major development has emerged – the Canada Post strike. Launched by the Canadian Union of Postal Workers Nov. 15 and heading into the holiday shopping season, the strike has significantly disrupted postal operations.
Of our Top 10 viewed stories since January, seven focused on labour issues—primarily in Canada but also including the U.S. East Coast port strike. While it may be coincidental that so many work contracts are up for renewal simultaneously, the disruptions caused by these disputes underscore their importance to supply chain operations.
SUSTAINABILITY ON THE RISE
Sustainability will be a driver of change in the supply chain in 2025, driven by regulations, environmental accountability and the quest for improved efficiency.
Transitioning to sustainable practices often requires upfront investments. Upgrading fleets, installing renewable energy systems, or sourcing materials ethically can strain resources, especially for small- and medium-sized businesses. However, the long-term benefits can be extremely beneficial, both environmentally and financially.
There’s no doubt 2025 will bring significant changes to Canada’s and the world’s supply chains and we’re excited to continue covering these developments, keeping our readers informed and equipped to tackle any and all challenges that could arise.

PORT OPERATIONS
Government invokes binding arbitration at Canadian ports
7 WARNING
CTA warns supply chain partners of dangers of Driver Inc.
11
MOVERS + SHAKERS
Appointments and promotions
14
Canada Post workers on strike, delays expected
By Inside Logistics Staff
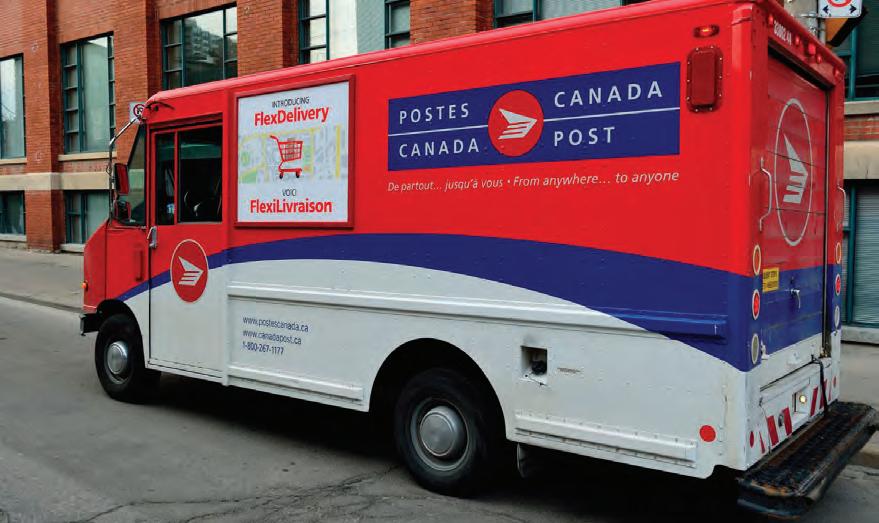
AT 12:01 A.M. NOV. 15, around 55,000 postal workers, represented by the Canadian Union of Postal Workers (CUPW), commenced a strike following unsuccessful negotiations with Canada Post to secure a new agreement.
“After a year of bargaining with little progress, postal workers made the difficult decision to strike,” CUPW said in a release. “Canada Post had the opportunity to prevent this strike, but it has refused to negotiate real solutions to the issues postal workers face every day. Instead, Canada Post left us no choice when it threatened to change our working conditions and leave our members exposed to layoffs.”
CUPW said its demands are reasonable, which include fair wages, safe working conditions, the right to retire with dignity and the expansion of services at the public post office.
“We still believe we can achieve negotiated collective agreements, but Canada Post must be willing to resolve our new and outstanding issues,” the CUPW said.
Canada Post said its operations will shut down during the national strike, affecting millions of Canadians and businesses across the country, and that it is disappointed with the decision.
“This decision will have a significant and immediate impact on millions of Canadians, small businesses and charities who count on Canada Post during the busy holiday season. As well, a national strike by CUPW means service to remote and Northern regions that rely on Canada Post is shut down,” Canada Post said in
a release. “Understanding the importance of the service we provide, Canada Post had informed the union, and our customers, that we would continue operating and maintain service in the event of rotating strikes while discussions continue. We are committed to remaining at the table to negotiate new collective agreements.”
Customers will experience delays due to the strike activity. Mail and parcels will not be processed or delivered for the duration of the national strike, and some post offices will be closed. Service guarantees will be impacted for items already in the postal network. No new items will be accepted until the national disruption is over.
All mail and parcels in the postal network will be secured and delivered as quickly as possible on a first-in, first-out basis once operations resume. However, a national strike of any length will impact service to Canadians well after the strike activity ends, said Canada Post.
“Shutting down facilities across the country will affect Canada Post’s entire national network,” Canada Post said in a release. “Processing and delivery may take some time to fully return to normal.”
Canada Post said it and CUPW have agreed to continue the delivery of socio-economic cheques during any upcoming labour disruption, for eligible and participating government organizations. The agreement ensures government financial assistance delivered by mail will reach seniors and other Canadians who rely on it.
Socio-economic cheques for the month of November will be delivered Nov. 20. Canadians will receive their cheques the same way they normally receive their mail.
Photo courtesy of flickr
Workers resume operations at B.C. and Quebec ports
THE CANADIAN GOVERNMENT stepped in and invoked binding arbitration at B.C. and Quebec ports, ordering operations to resume, with employees returning to work between Nov. 14-16.
“I have directed the Canada Industrial Relations Board to order that all operations and duties at the ports resume and to assist the parties to settle their collective agreements by imposing final and binding arbitration,” Minister of Labour Steven MacKinnon said during a press conference.
MacKinnon also ordered that the terms of the existing collective agreements until new ones are established.
The Maritime Employers Association (MEA) said it welcomes the government’s decision to intervene by asking the Canada Industrial Relations Board (CIRB) to order binding arbitration to resolve the “total impasse” in the dispute with Longshoremen’s Union CUPE 375 and awaits instructions from the CIRB on next steps.
The Port of Montreal Longshore Union CUPE Local 375 rejected a final offer from the MEA resulting in a lockout at the port Nov. 10.
“The end of this labour dispute means that we can resume operations and aim to restart supply chains across all our activities as soon as possible. I thank those who are facilitating the resumption of operations for our partners and clients. Restoring services will
allow us to resume international trade, benefiting thousands of businesses and consumers who rely on reliable and smooth port activities,” said Julie Gascon, president and CEO of the Montreal Port Authority.
At a press briefing this morning, the minister noted that despite a lengthy negotiation process and the intervention of specialists from his department’s Federal Mediation and Conciliation Service, negotiations had reached an impasse.
The B.C. Maritime Employers Association (BCMEA) said it intends to follow direction received from the CIRB and will inform member employers of operational updates as soon as possible.
“We look forward to safely resuming operations across Canada’s West Coast Ports,” BCMEA said in a release. “The BCMEA and its members are committed to working to strengthen Canada’s reputation as a trusted trading partner and rebuilding labour stability for the long-term.”
International Longshore and Warehouse Union (ILWU) Local 514 workers’ strike activity commenced at 8 a.m. Nov. 4 at the Port of Vancouver’s BCMEA member terminals.
Port of Quebec workers have been locked out for more than two years with replacement workers filling in since.
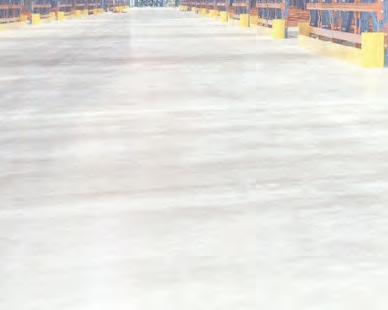
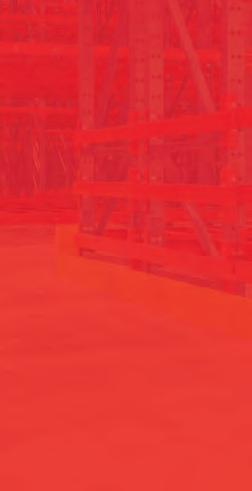

Amazon opens new fulfilment centre in Cambridge, Ont.
ON NOV. 13, AMAZON celebrated the official opening of its latest fulfillment centre, YHM2, in Cambridge, Ont. The facility spans nearly one million square feet and began operations with over 250 employees.
The new facility offers in-demand skills training and career growth opportunities while helping optimize Amazon’s regional operations network.
Because of Cambridge’s strategic location, YHM2 plays a key role in supporting Amazon fulfilment centres in southwestern Ontario as the company prepares for the holiday season.
Employees will have the opportunity to build new skills and grow their careers by participating in training and certification programs related to the technology operated by the site, including forklifts.
At the ribbon cutting ceremony, Amazon welcomed Ontario’s minister of red tape reduction, Mike Harris, MPP Brian Riddell, Karen Redman, regional chair of the Water-
Swisslog - IL - December Print Ad.pdf 1 11/27/2024 9:10:08 AM
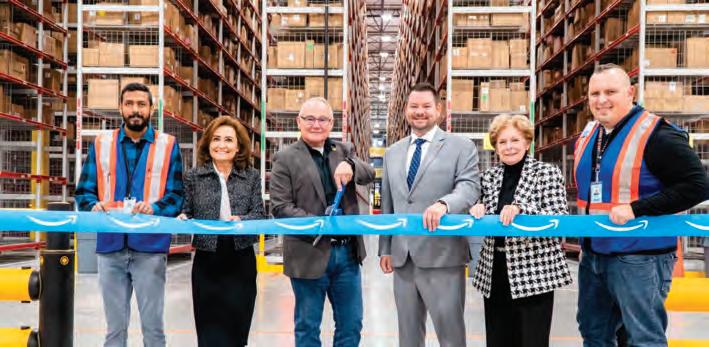
loo Region and City of Cambridge Councillor Helen Shwery.
At YHM2, Amazon product inventory is stored, managed and distributed to regional Amazon Robotics fulfilment centres, allowing them to fulfil a wider selection of customer orders at the fastest-possible delivery speeds.
“YHM2 brings the best of Amazon’s logistics expertise to Cambridge while making the city an important part of how we support our local fulfilment network and offer a leading product selection to customers,” said Greg Clutton, YHM2 site lead. “We are proud to be creating good jobs while making important contributions to the local community.”

Swisslog automates e-grocery intralogistics with solutions designed to increase the speed, accuracy and e iciency of order fulfillment.
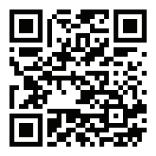
swisslog.com/e-grocery
Amazon's new Cambridge fulfilment centre helps optimize the company's southwestern Ontario network.
Government takes ownership of Québec Bridge from CN, plans to restore
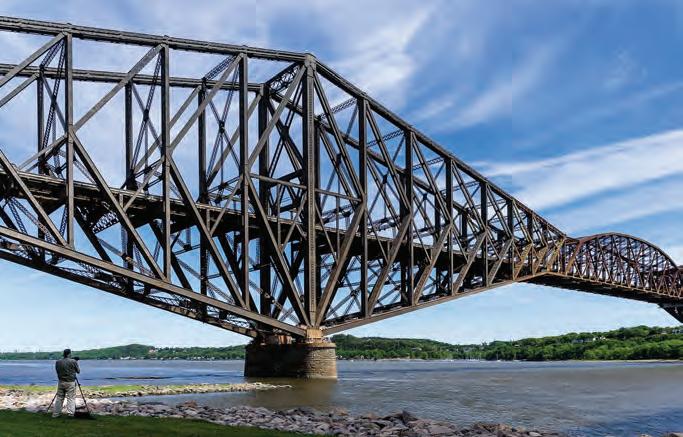
CANADIAN NATIONAL RAILWAY (CN) has handed over ownership of the Québec Bridge, a historic structure crossing the Saint Lawrence River between Sainte-Foy and Levis, Que., to the Government of Canada.
The government announced in May that it had reached an agreement in principle with CN to transfer ownership of the Québec Bridge. The agreement was formalized by the signing of a deed of transfer between Canada and CN Nov. 12.
For over 100 years, the people of the region have relied on the Québec Bridge for their daily commutes, tourism and trade. The Government of Canada said it recognizes the importance of the bridge as a strategic freight corridor for regional, national and international markets, and as an important link in the Canadian supply chain.
The retrocession of the Québec Bridge will enable the Government of Canada to ensure the sustainability of this strategic infrastructure so that it can continue to benefit the economies of Canada and Quebec, as well as the entire population of the greater Québec City region.
Management of the Québec Bridge will be entrusted to the federal Crown corporation Jacques Cartier and Champlain Bridges Incorporated (JCCBI), which will assume all responsibilities as owner of the infrastructure, and will be responsible for implementing the rehabilitation plan for the Québec Bridge. The Government of Canada said it is confident that the expertise and experience acquired by JCCBI over the years, notably in operating the Jacques Cartier and Honoré Mercier bridges in Montreal, will enable it to successfully carry out this rehabilitation plan.
JCCBI will work closely with the two other partners and users of the Québec Bridge – CN, which remains responsible for the rail corridor, and the Quebec government, which remains responsible for the road corridor and bicycle path. A collaboration agreement between these three partners will be drawn up to optimize coordination and ensure the completion of all activities on the Québec Bridge.
The Government of Canada will invest more than $40 million a year over a 25-year period in the rehabilitation program. This program will begin with inspections and various studies to make the right diagnoses, prepare a detailed rehabilitation plan and prioritize the work to be carried out. The work will include repair and reinforcement of the steel, piers and footings, as well as a painting program to protect the steel from corrosion and improve the overall appearance of the bridge structure.
Port of Quebec looks to electrify five of its docks
THE PORT OF QUÉBEC is receiving $22.5 million in funding to support the electrification of five of its docks, two hosting cargo ships and three welcoming cruise ships.
This is a key plank in the port’s sustainable development plan which seeks a 40 per cent reduction in greenhouse gases (GHGs) over its entire territory by 2035.
The federal government is providing the financial assistance from Transport Canada’s Green Marine Corridors Program – Clean Ports. The Port of Québec’s dockside electrification is a project evaluated at $55 million. Once all conditions are met, the project could consist in installing five electrical connection stations to serve two docks for general cargo ships connected to the resupply of the mining industry in the Canadian North, as well as three docks dedicated to cruise operations.
“We have made dockside ship electrification a pillar of our Vision 2035 for good reason,”
–
Mario Girard, Port of Québec president and CEO.
“We have made dockside ship electrification a pillar of our Vision 2035 for good reason,” said Port of Québec president and CEO Mario Girard. “This project will position the Port of Québec as a world leader and will have a major impact on the decarbonization of port activities in Québec City. We are very pleased to reach this major threshold today,”
The port said ships account for more than 80 per cent of the GHGs generated by all activities on the Port of Québec territory. With these investments in electrical connections, the port said it is addressing the main source of its GHG emissions and atmospheric contaminants.
Fewer than three per cent of the world’s ports are equipped for dockside electrification.
The Port of Québec now intends to pursue talks with the Québec Government to secure the remaining investments needed to complete this project.
Photo courtesy of Alain Girard, flickr
Canada’s manufacturing sector to help drive global logistics automation market
A RECENT STUDY PROJECTS that the global logistics automation market will reach a value of US$81.5 billion by 2033, with Canada's manufacturing sector playing a key role in driving this growth. Conducted by Straits Research, the study also predicts a 10.2 per cent annual growth in the logistics automation market between 2025 and 2033, leading to an increase from its current value of US$34 billion.
In addition to warehouses being one of the main drivers of the growth, the study said Canada has one of the world’s largest and most advanced manufacturing economies. A
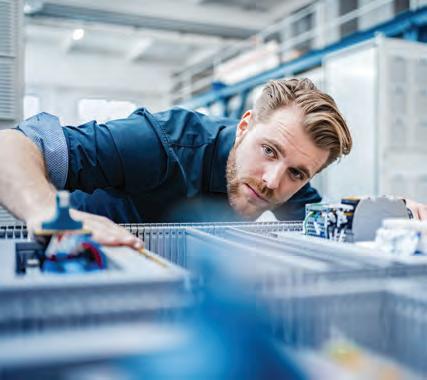
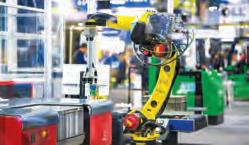
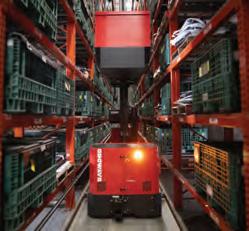
THE FUTURE OF INTRALOGISTICS IS INTEGRATED
Build smart. Stay agile. Now is the time to take a broader look at your overall intralogistics strategy and optimize. Making adjustments to combat today’s challenges will prepare you for a strong and sustainable future. And we can help.
Together, we’ll analyze the strategy and systems you’ve built to move, manage, store and protect goods and bring forward new ideas to enhance or secure the investments you’ve already made. Let’s get started.
RUN BETTER. MANAGE SMARTER.™ Discover how Johnston Equipment can help optimize your facility.
highly productive sector of the economy is the production of plastics, metal products, consumer goods and vehicles. Despite growth in the manufacturing sector, there is a sizable demand from the country’s e-commerce-focused storage and logistics industry.
“Automated warehouses have driven the demand for quicker responses and the requirement to manage a more significant number of stock-keeping units (SKUs) with less error due to the introduction of always-on e-commerce," the analysis indicated. "The urgent need to cut costs, reorganize workflows and boost productivity propels robotic breakthroughs."
Automation has increased efficiency while enhancing control and making various purchases more manageable. It is also beneficial for controlling inventory and the manufacturing process. It assists in improving both customer service and the delivery of multiple commodities throughout time. Automation in this area has benefitted transportation and storage due to the increased use of automated vehicles, automatic mobile robots, robotic arms, automated retrieval, and storage systems. The usage of software and services has increased, which has enhanced warehouse management. It provides real-time updates on the loading and unloading of the cargo. In addition to these factors, the growing e-commerce sector will raise the demand for inventory management and warehousing.
The endeavour has been driven by increased funding from Asian economies and a flood of innovation from start-ups. As a result, there will be more warehouses and FCs worldwide. According to a recent Honeywell Intelligrated survey of 171 material-handling executives in the U.S., 35 per cent of the executives said that their primary challenge was to fulfill more orders (quicker and cheaper), while their secondary concerns were to reduce order processing errors/improve order accuracy and to find enough labor to support operations.
To meet the demand for home delivery, warehouses and fulfillment centres have been observed using one of two strategies: extending their current location or building new ones (or curbside delivery). The latter, however, costs more than the former. By 2020, warehouses will have grown to approximately 200,000 square feet, up from an average size of roughly 65,000 square feet in 2000.
CTA warns supply chain partners about the dangers of Driver Inc.
ON OCT. 24, the Canadian Trucking Alliance (CTA) warned attendees at the Canadian Policy Forum of the Global Cold Chain Alliance about the risks of hiring carriers that utilize drivers through the Driver Inc. model.
“It is critical members of the supply chain understand the negativity associated with Driver Inc., its impact on workers’ rights, road safety and on legitimate, law-abiding trucking companies,” Geoff Wood, senior vice-president of policy at the CTA, said during the Ottawa event. “And it’s even more vital that all supply chain partners do their part to stop funding the practice.”
“It is critical members of the supply chain understand the negativity associated with Driver Inc., its impact on workers’ rights, road safety and on legitimate, law-abiding trucking companies,”
– Geoff Wood, senior vice-president of policy at the CTA.
Driver Inc. is a model based on hiring commercial drivers, who do not own, lease or operate their own vehicle, and become incorporated and receive payments from their carrier with no source deductions, such as WCB, overtime or other costs, which leaves the driver and company hiring the carrier vulnerable and at risk.
Members of the Global Cold Chain Alliance in attendance, like other groups CTA has been addressing, will be provided a toolkit to assist them in identifying Driver Inc. companies among their transportation supplier base, which will help protect their operations from exposure to the types of illicit practices proliferating throughout the underground economy.
Additional items discussed included the need for supply chain partners to assist CTA in advo-
cating for infrastructure resiliency, like additional rest areas to support drivers on the national highway system, as well as improved winter road maintenance – both of which are key components of CTA’s interprovincial trade barriers report.
Additionally, Wood touched on long-standing Canada-U.S. trade issues, including the need to expand U.S. in-transit allowances and to address the ability for the repositioning of foreign empty trailers.
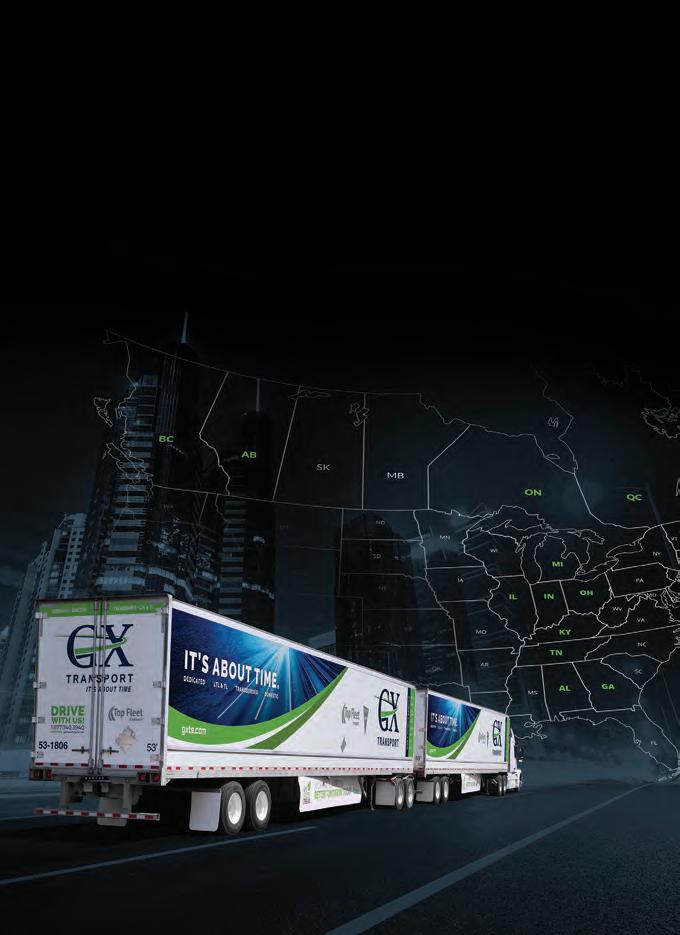
Air Canada Cargo opens new cold chain facility at Heathrow Airport
AIR CANADA CARGO has launched a new cold chain facility at London Heathrow, its largest hub in Europe, to enhance services for customers transporting temperature-sensitive goods.
The upgraded facility will feature nearly 900 square-feet of temperature-controlled areas to fully meet strict industry standards and global regulatory requirements, ensuring products stay within the required temperature range.
“The launch of our new London Heathrow cold chain facility continues to show our customers that we are committed to maintaining the integrity and safety of their temperature-controlled products throughout their journey,” said Matthieu Casey, managing director, commercial at Air Canada Cargo. “This enhancement of our capabilities at one of our key global hubs will play a key strategic role in further expanding our already robust global network and advancing our capabilities
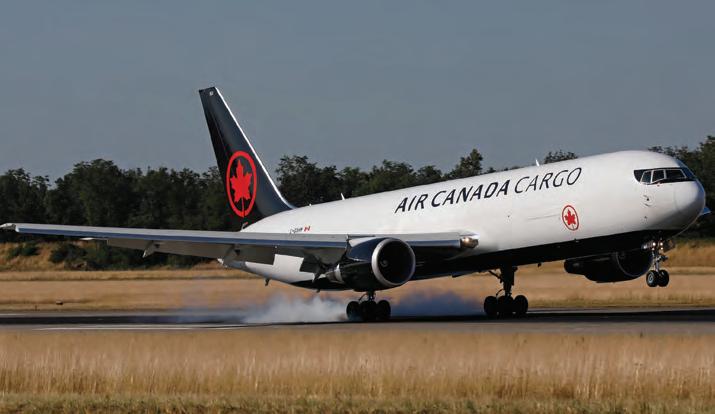
for our customers.”
Air Canada Cargo connects London Heathrow to and from its global network with over 45 weekly widebody flights.

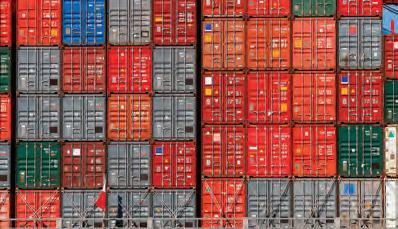


Air cargo market grows 9.4 per cent in September
THE INTERNATIONAL AIR TRANSPORT ASSOCIATION (IATA) published data for the global air cargo market in September, reporting a growth of 9.4 per cent, with international operations seeing an increase of 10.5 per cent.
Total demand, which is measured in cargo tonne-kilometers (CTKs), rose for the 14th consecutive month.
Capacity, measured in available cargo tonne-kilometers (ACTKs), increased by 6.4 per cent compared to September 2023, or 8.1 per cent for international operations. This continued to be largely related to the growth in international belly capacity, which rose 10.3 per cent extending the trend of double-digit annual capacity growth to 41 consecutive months.
“September performance brought continued good news for air cargo markets. With 9.4 per cent year-on-year growth, cargo volumes continued to mark all-time highs for demand,” said Willie Walsh, IATA’s director general. “Yields are also improving, up 11.7 per cent on 2023 and 50 per cent above 2019 levels. All this points to a strong finish for this year. For longer-term trends, the air cargo world will be closely following the outcome of the U.S. election for indications of how U.S. trade policy will evolve.”
Several factors in the operating environment include:
■ Year-on-year, industrial production rose 1.6 per cent while global goods trade increased 2.8 per cent for a sixth consecutive month of growth. Monthly trade grew by 1.4 per cent, the highest in seven months.
■ The Purchasing Managers Index (PMIs) for global manufacturing output, and the PMI for new export orders, were both below the 50-mark at 49.4 and 47.5 respectively, indicating contraction.
■ U.S. headline inflation, based on the annual Consumer Price Index (CPI), declined by 0.2 percentage points to 2.4 per cent in September, marking the seventh straight month of easing inflation. In the same month, the inflation rate in the EU fell by 0.3 percentage points to 2.1 per cent, continuing a process started in January 2023. China’s consumer inflation remained low at 0.4 per cent in September amid concerns of an economic slowdown.
North American carriers saw 3.8 per cent year-on-year demand growth for air cargo in September. Capacity increased by 4.2 per cent year-on-year.
Latin American carriers saw 20.9 per cent year-on-year demand growth for air cargo in September, the strongest growth among the regions. Capacity increased 7.9 per cent year-on-year.
African airlines saw 1.7 per cent year-on-year demand growth for air cargo in September, the slowest among regions. September capacity increased by 13.9 per cent year-on-year.

movers + shakers
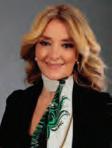
Computer Generated Solutions
CGS announced that Jamie Elias will join the company’s BlueCherry team as managing director and country head for Canada.
The CGS BlueCherry Enterprise Suite provides clients with digital supply chain management software solutions to drive their fundamental business processes.
As managing director and country head for Canada, Elias will focus on helping her clients overcome complex supply chain challenges and improve operational efficiency. With over 20 years in senior executive management positions at multinational IT corporations, Elias has developed expertise and served as a trusted advisor to her clients on their IT strategies and operations.
Kinaxis
Kinaxis, an end-to-end supply chain orchestration, announced Mark Morgan as president of commercial operations.
Morgan has more than two decades of executive

and sales leadership experience in supply chain, including leading the commercial operations for Coupa and Blue Yonder, where he also held the role of interim CEO.
In his new role, Morgan will manage Kinaxis sales teams in North America, EMEA and APAC, the global go-to-market and strategic operations team, global customer care and business consulting.
Vancouver Fraser Port Authority
The Vancouver Fraser Port Authority announced that Captain Shri Madiwal has been appointed as vice-president of operations and supply chain. Madiwal brings more than 30 years of experience in maritime operations and supply chain to the role. Since joining the port authority in 2019, Madiwal has made significant contributions to the organization and provided leadership on the delivery of key projects. Madiwal is a certified master mariner—the highest internationally recognized level of seafarer qualification available—and holds an
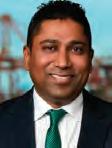
MBA from Simon Fraser University. He sits on the boards of Clear Seas and the International Sailors Society of Canada.
Madiwal has been acting vice-president of operations and supply chain at the port authority since December 2023
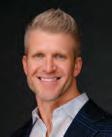
AutoScheduler
AutoScheduler, a warehouse orchestration platform and WMS accelerator, announced that Ian Johnston will replace Stephen Zujkowski, who is retiring, as vice-president of customer success. Johnson, who previously served as director of supply chain at Amazon, has more than a decade of experience in supply chain operations, logistics management and strategic leadership. He will use his expertise to help AutoScheduler’s customers gain value and success from deploying AutoScheduler solutions.
24_012006_Inside_Logistics_DEC_CN Mod: October 31, 2024 9:56 AM Print: 11/12/24 page 1 v2.5

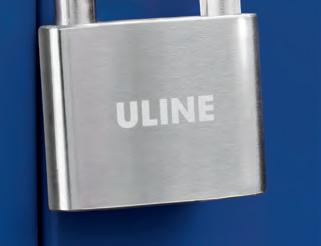
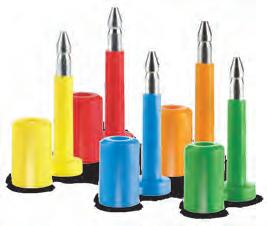
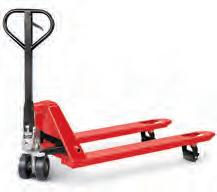
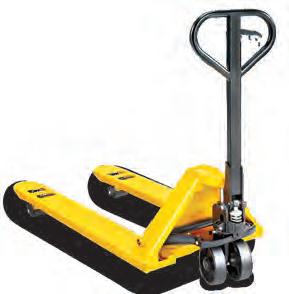
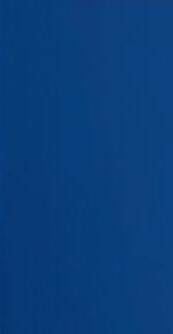
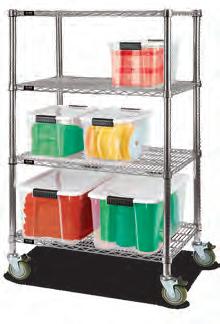


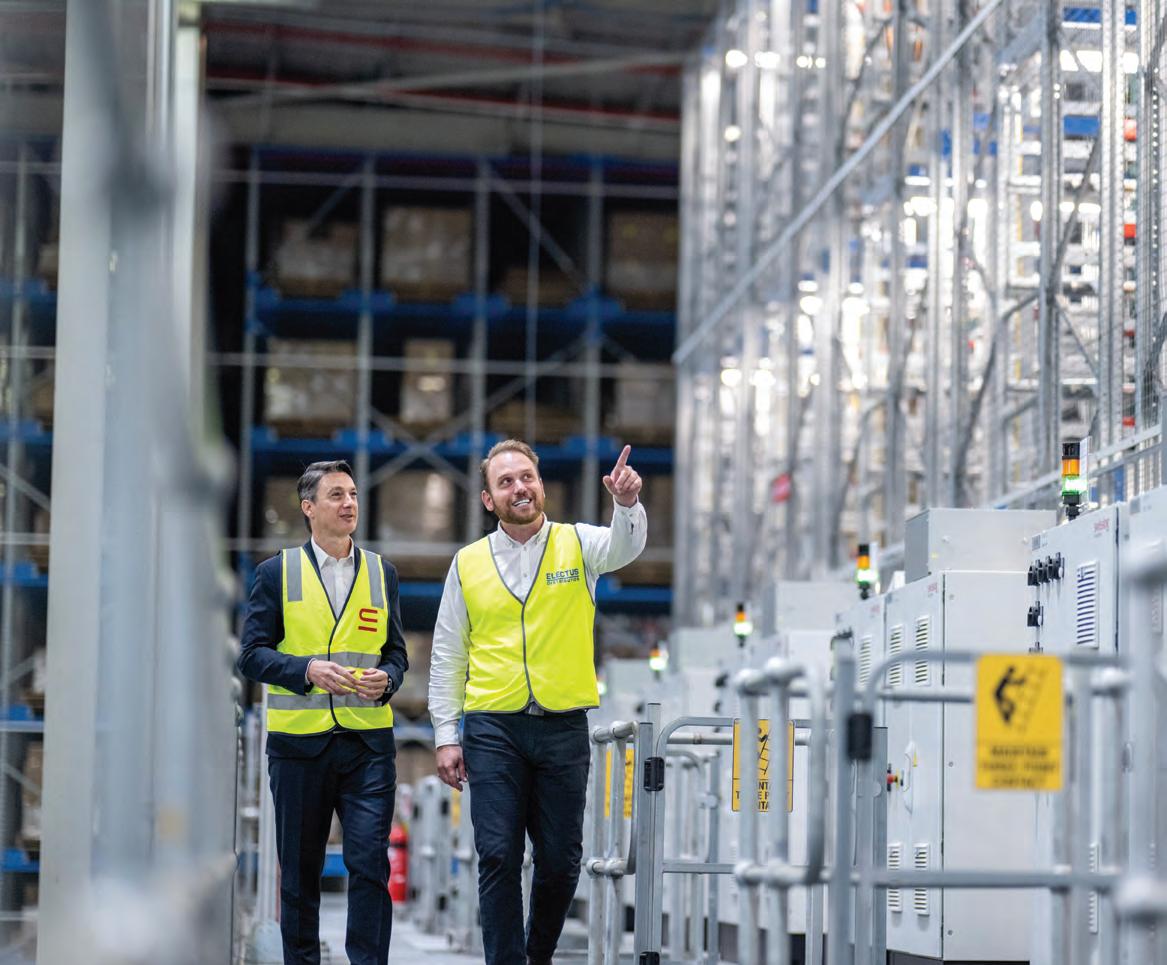
SUPPLY CHAIN 2025
A look at the trends and technology that will continue to shape the global supply chain
As we look toward 2025, the consensus is clear: artificial intelligence (AI) will continue to make waves in the global supply chain. Whether optimizing warehouse operations, improving inventory management, creating more efficient transportation routes, boosting labour productivity or mitigating disruptions, the potential benefits of AI will be invaluable for those who deploy the technology effectively.
“AI will continue to be one of the most transformative forces in supply
chain management next year and beyond, driving advancements across three key areas: productivity, process, and product,” said Paul Magel, president of the business applications and technology outsourcing division at Computer Generated Solutions and its BlueCherry team.
Magel explained that AI will enhance productivity by improving day-to-day operations, introducing new tools and streamlining processes to optimize decision-making. From a product standpoint, he believes AI will remain integral to technology solutions, enhancing workflows
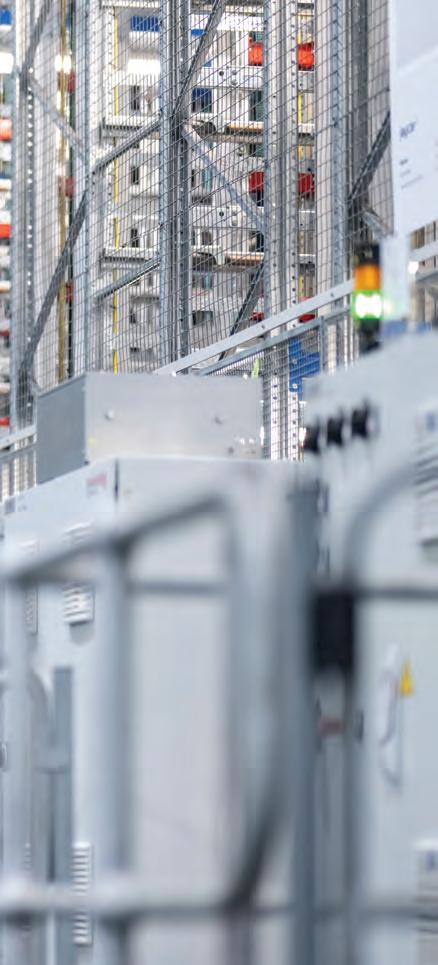
“AI will continue to be one of the most transformative forces in supply chain management next year and beyond...”
– Paul Magel, president of the business applications and technology outsourcing division at Computer Generated Solutions and its BlueCherry team
and enabling more intelligent automation.
“AI will evolve to a point where systems can operate independently — analyzing data, solving problems and taking action without user input, leading to a more seamless and self-sufficient supply chain,” he said.
AI will also play a critical role in predicting and mitigating the impact of global disruptions, such as the Canadian rail strike and the U.S. East Coast port strike.
“Looking ahead to 2025, supply chain teams will increase their investments in AI solutions across the end-to-end supply chain, focusing particularly on improving predictive analytics and scenario planning capabilities to enhance resilience and agility,” said Jeff Trino, supply chain leader at Genpact. “While both the Canadian rail and U.S. port strikes were resolved fairly quickly, they left suppliers scrambling to reroute products. If there’s one thing 2024 taught us, it’s that supply chain disruptions will occur, and preparing for them seems to be an obvious step for suppliers to take in 2025 to stay ahead of the curve.”
Another area where AI will continue to evolve is order management.
“Traditionally, the order management process has been time- and labour-intensive. It can take hours for a human to triage a new request, interpret and classify it, match it with data and triage it before sending it to the client,” said Trino. “Now, AI agent models can auto-classify client requests, remember prior interactions and generate recommendations for the next best action, which are quickly reviewed by team members for accuracy. That’s hours of saved time across the team, allowing them to focus on more strategic, customer-facing activities.”
AI will also improve data analytics, a challenge that can be overwhelming if not done properly.
“Access to real-time visibility and predictive analytics relies on quality data and smart data management practices,” said Trino. “AI can help enrich data catalogs, cleanse data sets and detect anomalies. Organizations with AI embedded throughout the supply chain — across planning, sourcing, making, delivering and aftersales functions — can respond to disruptions more quickly and make data-backed decisions to redirect goods and inventory.”
With improved real-time visibility through better predictive analytics, demand forecasting will also be optimized, allowing companies to develop ideal stocking recommendations based on past behaviour, macroeconomic trends and other factors.
“As the predictive capabilities of AI models improve, the target level of inventory to be produced and stocked can be adjusted to maximize profitability,” said Trino.
Trends in transportation
While there are realities in the transportation sector that AI cannot change — such as distances between pickup and delivery locations, cargo weight and shipping rates — Tom Perrone, senior vice-president of professional services at project44, believes AI-driven optimization in manufacturing, production, routing and scheduling will become high-value use cases for the Canadian supply chain.
“Generative AI is becoming increasingly effective at predicting pricing, enabling businesses to optimize their supply chain vendors,” he said. “As AI makes it easier for smaller companies to enter the space, we’ll see greater diversification and, therefore, increased competition in Canadian supply chains.”
Perrone also anticipates that changing governments will impact both Canada and the U.S., from trade tariffs to the renegotiation of the U.S.-Mexico-Canada Agreement (USMCA).
“Despite calls for Canadian trade to diversify, the U.S. remains Canada’s largest trading partner, with 60 to 70 per cent of goods moving by truck,” said Perrone. “There will also be a federal election in Canada no later than October 2025, so companies may face a double whammy of regulatory changes brought on by political shifts. Canadian businesses will need to assess their risk mitigation strategies, such as alternative product sourcing, increased safety stock and diversifying their carrier network to ensure resilience in the face of inevitable disruptions.”
With the election approaching, Perrone noted that governments are promising large infrastructure projects, including improvements to the Quebec City-Windsor corridor.
“Passenger and freight trains share the same tracks, with freight taking priority over passenger commutes,” he explained. “The promise to build dedicated passenger tracks will alleviate
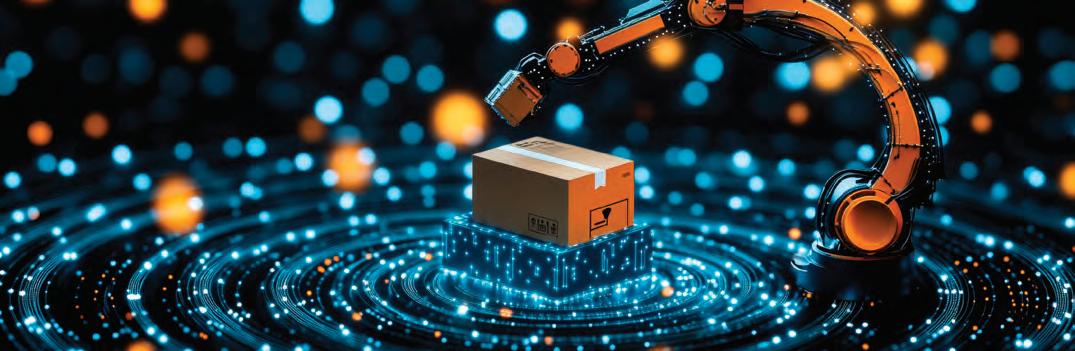
congestion along these vital routes. While the promise of faster rail moves will benefit passengers, the improvements for freight will be even more substantial.”
On the terminal side, Perrone expects the Port of Prince Rupert to increase its capacity to 1.8 million TEUs, while Vancouver plans to add 2.4 million TEUs annually. The Port of Montreal is also slated for a potential expansion.
“These developments are heavily influenced by mode shifts to greener transportation methods, capacity requirements, and changing consumer needs,” he said.
A persistent challenge in the trucking industry, as Perrone points out, is the labour shortage, which accounts for 63 per cent of open positions in the logistics sector.
“This is putting pressure on smaller companies, where unfilled positions can significantly impact revenue, particularly in sectors reliant on long-haul transportation,” he said. “Without increased recruitment and retention efforts, projections suggest that vacancies in trucking and logistics could surpass 25,000 positions in the coming years, potentially compromising supply chain efficiency and economic productivity across Canada.”
Warehouses
Warehouse operations are among the largest adopters of AI and robotic technologies. Bill Stenger, head of sales for the Americas region at Swisslog, said there is a shift toward highly adaptable technologies that use data to drive greater efficiency.
“Collaborative robotics will play a key role in adapting to labour availability and productivity challenges,” said Stenger. “These technologies will allow operations to run longer, helping meet customers’ expectations for service levels.”
Stenger also emphasized AI’s growing importance in addressing the global labour shortage.
“You don’t have employees with 10, 15 or 20 years of experience who know the ins and outs of operations,” he said. “We need to empower employees who will be with us for one, three or five years with data and decision-making tools. AI will play a crucial role in providing suggestions to operators, helping them make smarter decisions and boosting their confidence.”
Sustainability
Perrone noted that many companies are realizing that sustainability
also drives operational efficiency.
“Today, ESG (environmental, social, and governance) concerns may feel imposed through regulation and external pressures, but over the long term, logistics companies will see sustainability as a crucial source of savings and a competitive advantage,” he said.
Magel echoed this sentiment, adding that technology helps improve efficiency across the entire supply chain, enabling manufacturers to produce less and create less waste.
Magel believes government will continue to play a role in shaping companies’ approach to sustainability, alongside pressures from customers and internal operations.
“As such, technology will remain essential for collecting, parsing and sharing data in the required formats,” he said. “Whether it’s the government, your customers, or your own company, technology will be vital for tracking the vast amounts of data involved.”
However, Perrone pointed out that one area where the supply chain sector is lagging in sustainability is the electrification of trucking fleets.
“While EV technology has spurred innovation in sustainable transportation, the lack of charging infrastructure remains a barrier to adoption, especially for heavy trucks,” said Perrone. “In 2025, with Canada’s vast, sparsely populated landscape, I expect more research and investment in alternative fuels and clean energy sources beyond just electrification.”
Magel expects the consumer products industry to continue leading the way in adopting advanced supply chain technologies. He noted that sectors like fashion, footwear and accessories face increasing pressure from compliance requirements related to labour and material sustainability, while customers continue to demand lower-cost goods. Technology will help companies address these challenges.
The bottom line
AI and other technologies are generating significant buzz about their potential to help supply chains navigate the challenges of 2025. But, as Trino cautions, one of the biggest challenges suppliers will face is separating the hype from the reality of what AI can deliver.
“There’s plenty of opportunity for success, but also a lot of hype that could lead to failed initiatives. It’s important to have a team that understands the technology and sets realistic expectations for what it can do today,” he said. “AI initiatives should be driven by clear business objectives. It’s essential to identify areas where AI can have the most impact and align these with strategic goals.”
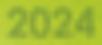
Congratulations, CITT-Certified Logistics Professionals
CITT is proud to present the CITT-Certified Logistics Professionals who earned their CCLP designations between November 2023 & October 2024. Congratulations to these dedicated supply chain logistics professionals who now join the ranks of the industry’s elite.

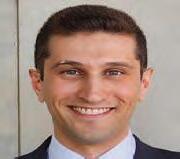

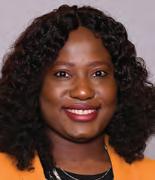
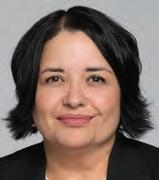
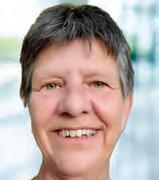
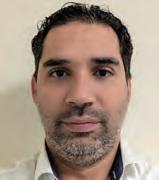
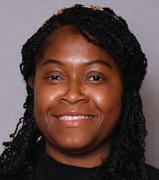


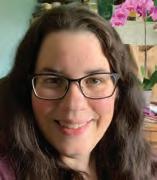
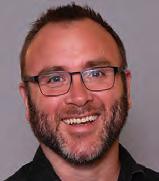
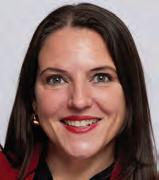

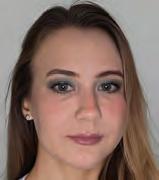

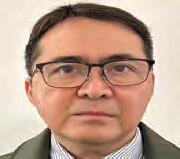


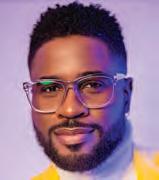


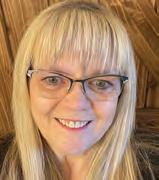
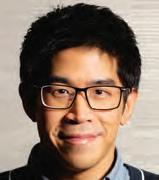
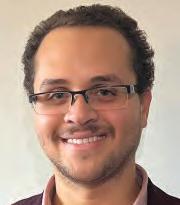

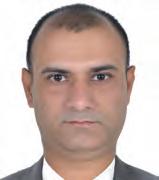
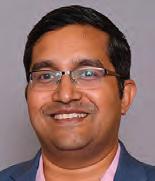
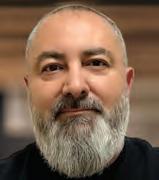
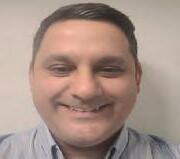
Talal Akkad, CCLP Toronto, ON
Abdullateef Alabi, CCLP Mississauga, ON
Oluwatosin Abiodun, CCLP London, ON
Fehintola Ariyo, CCLP Brampton, ON
Alma Arzate, CCLP Toronto, ON
Susan Beatty, CCLP Surrey, BC
Sanishi Bryson-Brown, CCLP Orangeville, ON
Jennifer Carneiro Demers, CCLP Ottawa, ON
Pratik Choudhary, CCLP Oakville, ON
Jennifer Coffey, CCLP Cornwall, ON
Jason Cripps, CCLP Cambridge, ON
Stacey Cummings, CCLP Mississauaga, ON Christina Cuthbertson, CCLP, Abbotsford, BC
Flavia Dos Santos Muniz, CCLP, Toronto, ON
Darien Edison, CCLP Saint John, NB
Jonas Gagajena, CCLP Delta, BC Abhishek Gomber, CCLP Saskatoon, SK
Ismail Benmezdad, CCLP Dorval, QC
Saiful Hossain, CCLP Toronto, ON Alpheus Johnson, CCLP Edmonton, AB
Victoria Jones, CCLP Oakville, ON
Manirathnam Kanagasundaram, CCLP Toronto, ON
Carla Kingston-Floyd, CCLP, Cornwall, ON
Kevin Lai, CCLP Surrey, BC
Yazid Lazrak, CCLP Oviedo, Spain Gamaliel Alphee Loemba, CCLP, Montreal, QC
Parav Kumar Malhotra, CCLP, Dubai
Vinod Maliyekal, CCLP Stoney Creek, ON
Massimo Mambro, CCLP Pointe-Claire, QC Chris Mantelos, CCLP Toronto, ON
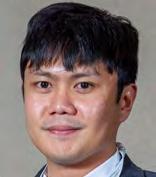
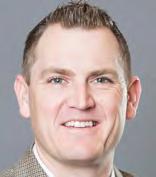




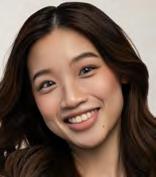
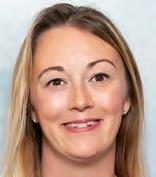

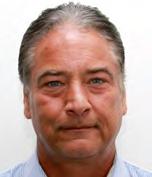
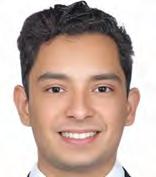
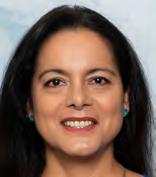
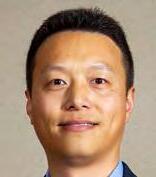
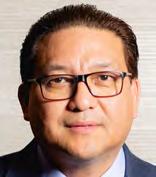
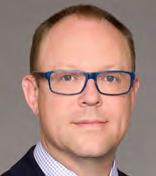
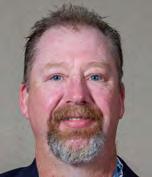
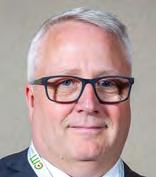
Photos of the following new CITT-Certified Logistics Professionals were not available:
Barry Adeyinka, CCLP, Hamilton, ON
Kathy Best, CCLP, St.Jacobs, ON Kevin Brown, CCLP, Mississauga, ON
Greg Cummings, CCLP, Mississauga, ON Rakesh Dasari, CCLP, Toronto, ON Dimitare Dimitrov, CCLP, Toronto, ON Mathieu Ducharme, CCLP, Saint-Zotique, QC
Brian Duff, CCLP, Peterborough, ON Jean Lui Duffoo, CCLP, Toronto, ON
Theodora Ene, CCLP, Calgary, AB
Nahun Fonseca, CCLP, Langley, BC
Rahul Gulati, CCLP, Mississauga, ON Srinand Iyengar, CCLP, Saskatoon, SK
Wei Jin, CCLP, Richmond Hill, ON
Nicole Johnston, CCLP, Etobicoke, ON Damanjeet Kaur, CCLP, Brampton, ON
Barjit Kharyal, CCLP, Breslau, ON
David Larouche-Couture, CCLP, , QC
Austin Leach, CCLP, Niagara Falls, ON William Liang, CCLP, Thornhill, ON Kwok Liu, CCLP, Edmonton, AB
Matthew McKinnon, CCLP, Morinville, AB
Monish Mehta, CCLP, Saint-Jean-Sur-Richelieu, QC
Isaac Mussell, CCLP, Oakville, ON Huy Nguyen, CCLP, Vancouver, BC
Tomas Nieto, CCLP, Burlington, ON Robert Noon, CCLP, Milton, ON Priya Alphy Philip, CCLP, Edmonton, AB Lalindra Ranaweera, CCLP, Ajax, ON Pamela Rooney, CCLP, St-Laurent, QC
Angela Santos, CCLP, Toronto, ON Arasu Sekaran, CCLP, Concord, ON Shrey Shah, CCLP, Milton, ON Janet Wallace, CCLP, Dorval, QC
See the list of all current CCLP designation holders at www.citt.ca/community/cclps
John Lorenzo Manuel, CCLP, Blumenort, MB
Daniel Marsh, CCLP Aldersyde, AB
Kevin Mascarenhas, CCLP Mississauga, ON
Maxime Michaud, CCLP Montreal, QC Tolulope Oladotun, CCLP Saskatoon, SK Shakthi Perera, CCLP Toronto, ON
Celine Pham, CCLP Calgary, AB Lindsey Prowse, CCLP Calgary, AB
Chandra Reddy Sugu, CCLP, Milton, ON
Bill Robinson, CCLP Puslinch, ON
Bruno Salazar Martin Del Campo, CCLP Richmond, BC
Rosa Sanchez Garcia, CCLP, Saint John, NB
Yingsong Tang, CCLP Winnipeg, MB
Christopher Tumaru, CCLP Vancouver, BC
Brian Ware, CCLP Mississauga, ON
Sheldon Scott Wiens, CCLP Steinbach, MB
Michael Woolman, CCLP Winnipeg, MB
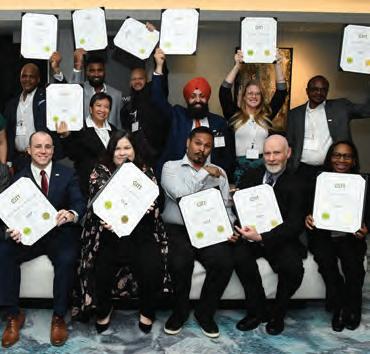
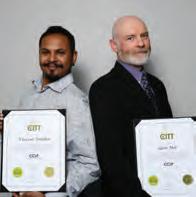
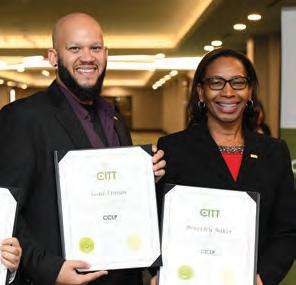
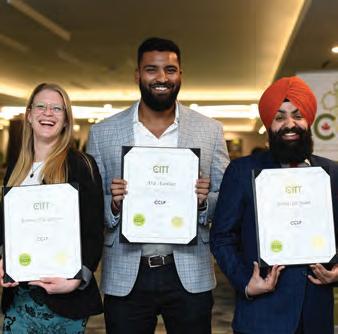
For a logistics career that stands out, professionals choose CCLP
When you see CCLP after someone’s name, you immediately know you can trust their specialized logistics expertise and commitment to professional excellence. CCLP is widely held and respected across the business – from carriers of all modes to shippers across sectors, 3/4PLs and beyond.
CITT-Certified Logistics Professionals have the proven, recognized ability to manage profitable and resilient logistics operations. Professionals with CCLP after their name go further in their careers and stand out for their abilities, integrity and dedication to excellence in transportation logistics.
If you’re looking to demonstrate to employers, partners, customers and your peers that you’re a certified expert in transportation and logistics, look no further than Canada’s Logistics Credential – CCLP
Challenge exam available year round. Or take courses online - next start January 20, 2025
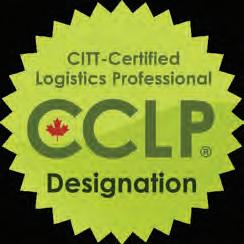
NATIONAL AND LOCAL SUPPLY CHAIN
Lethbridge event highlights supply chain issues, brings together local industry
During the first-ever Southern Alberta B2B Trade Show and Conference in Lethbridge, Alta., attendees received an overview of both national and local supply chains, with Canada’s relationship with China taking centre stage.
Trevor Lewington, CEO of Economic Development Lethbridge, said that while tariffs on electric vehicle imports from China help protect the domestic economy, they pose a challenge for Alberta.
“Canada is the largest supplier of canola to the world. We are the largest supplier of that commodity and value-added products,” said Lewington. “China is the largest market that takes and consumes canola products, so it’s not a surprise that a few weeks after Canada implemented a 100 per cent tariff on Chinese imports of adhesive battery components, the Chinese government announced a review of Canada’s dumping practices of canola into the global market.”
Lewington believes the turbulent relationship between Canada
and China will significantly impact the Canadian economy, as well as the Lethbridge region, which, he said, has tripled its exports over the last decade.
“When you go back to about 2012 or 2013, the Lethbridge region exported about $600 million worth of goods,” he said. “Today, that number is more than $2.2 billion. That’s Lethbridge-manufactured goods, not raw commodities. About 70 per cent of that total is manufactured goods.”
Despite this increase, Lewington said southern Alberta and Lethbridge are becoming more exposed to global trade disruptions.
Brand disloyalty
Lewington also highlighted a PricewaterhouseCoopers (PwC) Canada brand study showing that Canadians are now more willing to switch brands to save money.
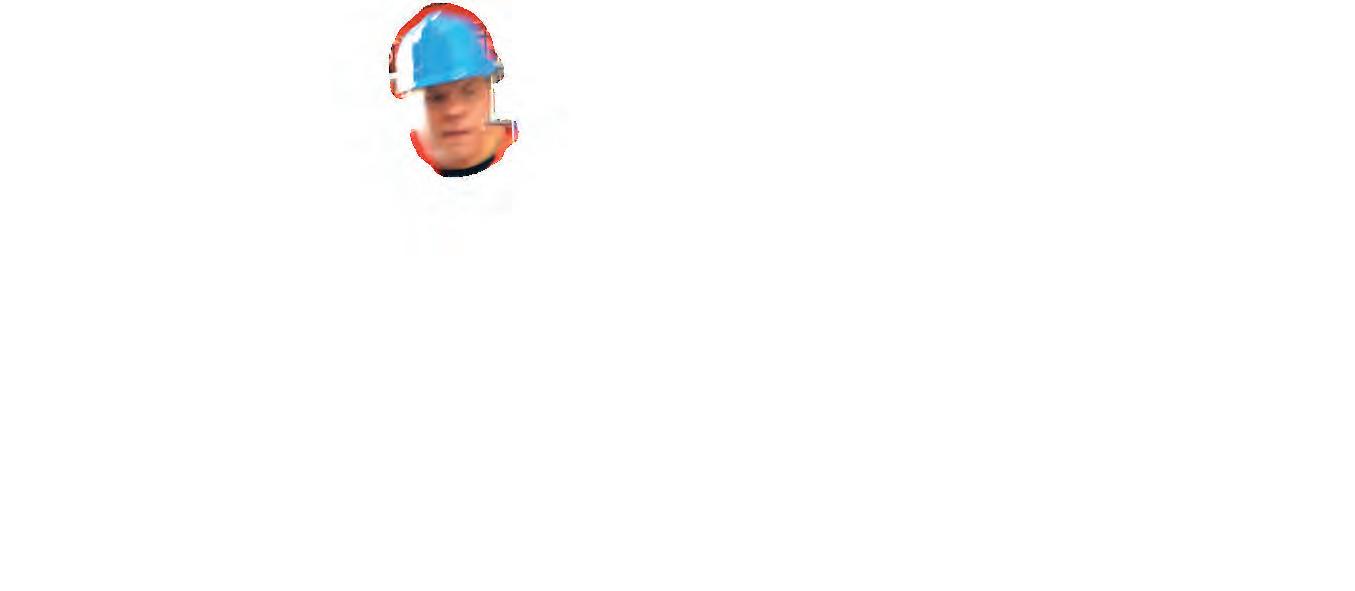
CHAIN ISSUES
“Canadian consumers, believe it or not, are very brand-loyal,” he said. “But in PwC’s most recent survey, what they note is that given current inflationary pressures, consumers are willing to switch brands based on pricing and promotion, which is pretty rare compared to what we’ve seen before. In that survey, 43 per cent of Canadian consumers said they would switch to a competing brand.”
Lewington urged attendees to keep this in mind when making business decisions, as the relationship between businesses and consumers is changing in Canada.
“Almost half of your consumers are quite happy to leave you overnight despite whatever relationship you might have built,” he said. “If the price is different, everyone is price-conscious at this moment, and that is driving the conversation.”
Managing global distribution
There is no shortage of disruptions affecting supply chains worldwide—piracy, strikes, lockouts, weather events and even poor driving that results in ships blocking canals or hitting bridges.
Lewington said there’s a silver lining to these ongoing issues: how companies are responding.
“The good news for me, as an economic developer, is that many companies with large, global, interconnected supply chains are saying, ‘It’s too much risk,’” he said. “‘We want to reshore, we want to bring manufacturing back to Canada. If our market is in North America, we want to do business here.’”
Locally, Lethbridge has adopted a similar approach by building what it calls a trade corridor with Great Falls, Mont.
“We lovingly refer to it as Canada’s Western Gateway,” said Lewington. “Southern Alberta has the infrastructure. Although we get some crazy weather, it is relatively predictable. It’s seasonal—we know when it’s coming. We don’t get hurricanes, and tornadoes are small-scale. We can be a destination for investment. We can be a manufacturing hub, and from here, we can support the entire Pacific Northwest.
“We have access to different markets, and

Canada has access to more free trade agreements than the U.S.
“We’ve seen lots of disruptions. I don’t think any of them are going away anytime soon.”
Trucking disruption
The trucking industry faces its own set of disruptions. Brad Beerling, logistics manager for Alberta and Saskatchewan at Meridian Manufacturing and Armtec, pointed to Driver Inc. as a longstanding issue.
“They are taking advantage of many new Canadians and people who just don’t have the knowledge,” said Beerling. “They hear they’ll be paid as independent contractors, don’t have to pay taxes and can write off expenses. That’s fine until someone gets hurt on the job and finds out they have no WCB coverage.”
Beerling stressed that not only do drivers need to avoid Driver Inc., but those hiring carriers must also be cautious.
“If you hire trucking companies that aren’t safe, and they get into a wreck, you
could find out there’s no WCB coverage because it happened under a contractor arrangement,” he explained. “If you hire a subcontractor and they don’t have WCB coverage, you’re left holding the bag.”
A nother hot topic in the trucking industry is emissions, particularly the shift from traditional fuel sources to alternatives like hydrogen, which Beerling said has advantages.
“The advantage over electric is that we can actually produce hydrogen here in Alberta, and that’s going to be huge for us,” he said. “We need to push forward to get the infrastructure in place; we need those fueling stations. It’s great that you can buy a truck for half the price with all the grants, but if you can’t fill it up, it doesn’t much matter.”
The Southern Alberta B2B Trade Show and Conference was held on Oct. 10 at the Lethbridge and District Exhibition. It was organized by Wida Procurement and Supply Chain Solutions, which plans to make it an annual event.
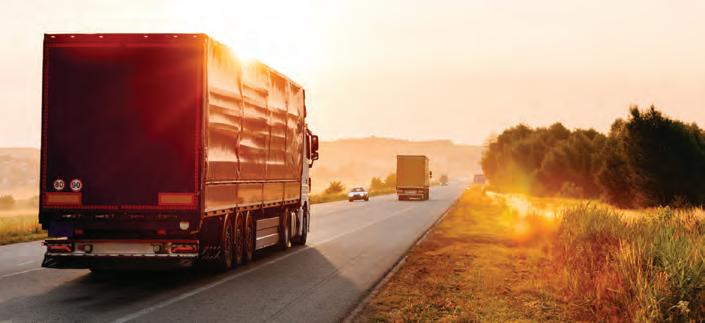
Trevor Lewington, CEO of Economic Development Lethbridge, speaks during the Southern Alberta B2B Trade Show and Conference.

STATE OF THE SUPPLY
Report looks at performance of U.S. supply chain and expectations for the future
The U.S. supply chain sector saw declines across various modes of transportation over the past year due to softening demand and higher fuel prices. At the same time, costs for storage, container rates and other financials were down, though these varied greatly by sector.
During a presentation at the Council of Supply Chain Management Professionals (CSCMP) Edge 2024 Conference in Nashville, Ten n., in October, Josh Brogan of Kearney — which authors the report in collaboration with Penske Logistics and CSCMP — highlighted findings from the 35th annual State of Logistics Report.
Motor carriers
Examining the performance of transportation modes in 2023, Brogan said motor carriers saw an 8.6 per cent decrease due to softening demand and stable capacity. Spot rates for motor carriers were relatively flat in the U.S. last year, with no indications of increases until late 2024.
Citing a Morgan Stanley index, Brogan noted that while motor freight capacity was inflated in 2023 and 2024, demand has beg un to pick up in some regions, including cross-border routes between the U.S. and Mexico, driven by increased nearshoring and long-haul loads out of Pacific ports. Spot and contract rates for dry van shipping also remained low, putting pressure on carriers’ margins.
For the first time since the COVID-19 pandemic, there was a decline in the number of carriers and brokers in the U.S., with a
six per cent drop in 2023. The report indicated that about 25,000 asset-based carriers and 1,500 freight brokers exited the market last year, a trend Brogan said is continuing in 2024.
Air freight
Air freight was down significantly in 2023, dropping by 15.4 per cent as ocean carriers entered the air cargo market. The State of Logistics Report projects demand for air freight will increase by 4.5 per cent in 2024, while rates will remain stable. Revenues, however, are expected to decline despite rising demand, a trend attributed to stagnant international trade and shippers leveraging expanded passenger freight capacity.
Geopolitical disruptions, including conflict in the Middle East and turmoil in ocean lanes, are pushing some shippers toward air freight.
Rail
Rail saw mixed results in 2023, with moderate year-over-year traffic growth of two per cent in April, though down three per cent from the same period in 2022. U.S. Class 1 railroads experienced a two per cent drop in revenue, an 11 per cent decrease in operating income, and a four per cent increase in operating ratios.
Carload volumes rose 1.6 per cent, but intermodal volumes — often viewed as a key growth driver — dropped 5.7 per cent, reaching a three-year low.
The outlook for 2024 is positive for rail, with dwell times de-
CHAIN
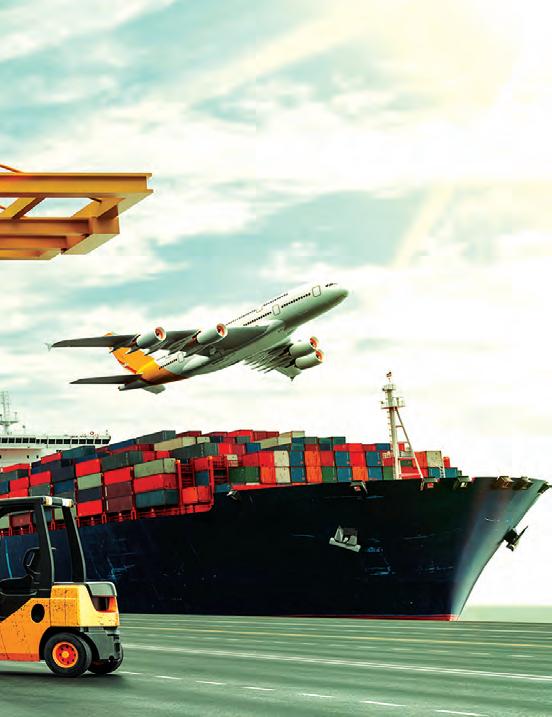
Ready
creasing by 1.8 per cent and potential cross-border expansion involving Canadian National, Union Pacific and BNSF.
Ocean and ports
The normalization of ocean freight rates from inflated pandemic peaks led to a 64.2 per cent drop in water expenditures. However, ongoing disruptions in various ocean lanes caused spikes in certain trading lanes throughout 2023 and into 2024.
Discussions during the State of Logistics Report presentation turned to the U.S. East Coast port strike, which began just before the session. Ronald Marotta, vice-president of Yusen Logistics, Americas, emphasized the significant impact of port disruptions on supply chains, noting para llel strike action at the Port of Montreal.
“Our lives are sustained by a smooth global supply chain, and I don’t think we expected dock workers to take this action,” he said, adding that each day a port shuts down requires four to five days to recover. “I hope the executive branch of the government recognizes this is not just a labour issue but a humanitarian one.”
Dur ing the pandemic, ocean carriers saw record profits, prompting fleet expansions and an eight per cent increase in container capacity in 2023. Growth of 41 per cent is projected in 2024.
Parcel and last-mile delivery
In 2023, shippers turned to regional partners for multi-sourcing, with parcel volumes for major carriers dropping and overall volumes down 0.5 per cent. The U.S. e-commerce market grew by eight per cent, though at a slower pace than pre-pandemic rates.
The “buy online, pick up in store” (BOPIS) market grew by 37 per
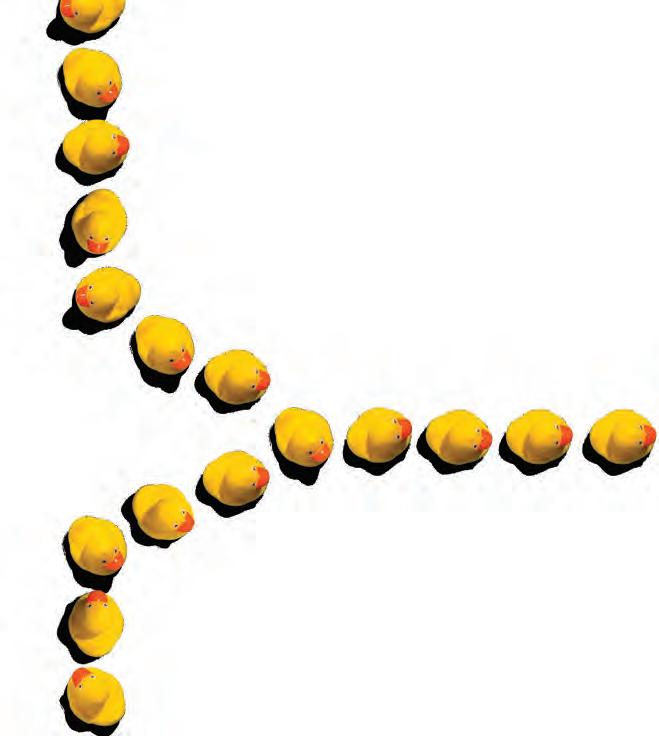
to get your fulfillment operations in a row?
Discover automation and software solutions aligned with your business goals at TREWautomation.com.






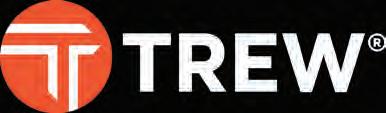
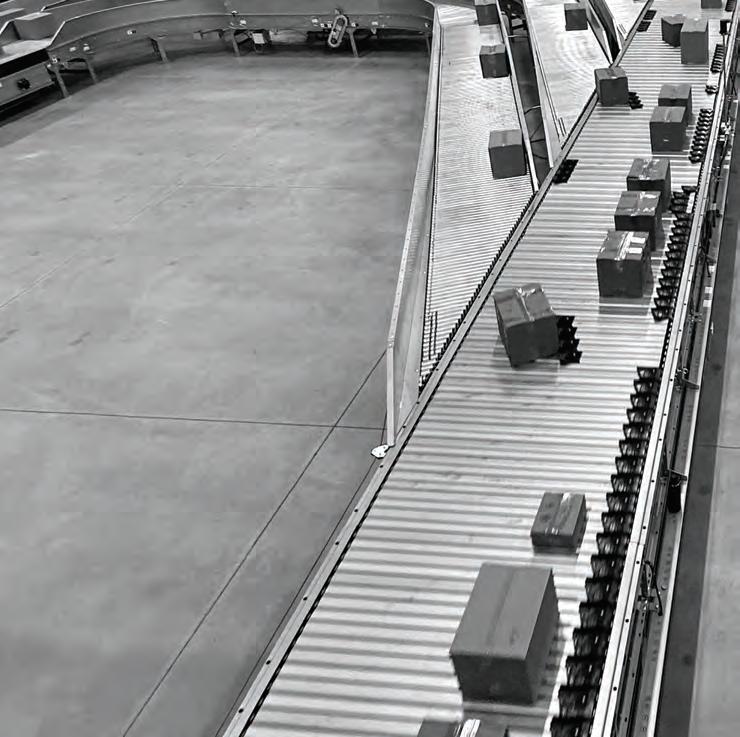
“Our lives are sustained by a smooth global supply chain…”
– Ronald Marotta, vice-president of Yusen Logistics, Americas
cent, significantly contributing to the e-commerce sector.
FedEx, UPS and the U.S. Postal Service all saw year-over-year declines, while Amazon surpassed FedEx and UPS in total deliveries for the first time. E-commerce represented 15.6 per cent of tota l retail sales in 2023, up from 5.9 per cent in 2013.
Freight forwarders and 3PLs
Freight forwarders and third-party logistics (3PL) providers will need to implement strategies to keep up with shipper demands and industry trends to maintain market share. Although the freight forwarding sector experienced a financial performance decline in Q4 2023, it is expected to grow at a rate of 5.5 per cent annually through 2032.
Brogan said focus areas for freight forwarders and 3PLs include technology investments, new and value-added services, targeting higher margins and mergers and acquisitions. Low freight rates and excess capacity may drive consolidation, particularly among smaller 3PLs.
Warehousing
Vacancy rates for industrial real estate in the U.S., including warehouses, distribution centres and storage, spiked 68 per cent yearover-year by the end of 2023. Rental rates increased despite the high vacancy.
According to Statista, a global data and business intelligence platform, Canadian warehouse rental rates were highest in B.C. at the end of 2023. Vancouver rates averaged $21.44 per square foot, followed by Victoria at $20.42. Rates in Toronto were $18.45, while Calgary’s rates stood at $11.80 per square foot.
By Q4 2023, the U.S. had 156 million square feet of warehouse space available for sublease. An additional 610 million square feet of industrial space was built last year, contributing to record-breaking construction levels over the past four years.
RENEW YOUR COMPLIMENTARY SUBSCRIPTION!
Simply complete this form today and Email to delon@turnkey.media Or Visit
https://www.insidelogistics.ca/subscribe/magazine/
(Email Required
YES, I WISH TO RECEIVE INSIDE LOGISTICS MAGAZINE FREE!
YES, I WISH TO RECEIVE INSIDE LOGISTICS E-newsletter FREE!
Choose your Edition: Print Digital Print & Digital
Signature:
Date:
PLEASE ANSWER THE FOLLOWING QUESTIONS TO QUALIFY FOR YOUR FREE SUBSCRIPTION:
1. Do you purchase, or influence the purchase, of goods and/or services related to distribution logistics, including warehousing operations (receiving, storage or shipping) or inventory control or materials handling? Yes No
2. If Yes, do you have plans to buy any of the following in the foreseeable future? (Check as many as apply)
(A) Forklifts and mobile materials handling equipment
(B) Racking, shelving and storage equipment
(C) Software, eg WMS, TMS, YMS, WES, etc
(D) Automated materials handling systems
(Z) None of the above
TRANSPORTATION SERVICES:
(E) Third-party logistics services
(F) Transportation services
(G) Real estate, warehouses, existing or new building
(H) Data capture and inventory control equipment
LTL Trucking Truck Load Trucking Intermodal Marine Rail Courier Air Freight None
3. What is your company's PRIMARY business?
MANUFACTURING (Check one only)
(01) Food & Beverage
(02) Consumer Durables
(03) Paper & Print
(04) Automotive Parts
(05) Clothing, Apparel & Textile Products
(06) Chemicals, Petroleum & Hazardous Waste
(07) Pharmaceuticals
(09) Computers & Electronics
(10) Transportation Equipment
(11) Lumber & Building Materials
(12) Manufactured Industrial Inputs
(98) Other Manufacturing (please specify)________________________________________________________________________
NON-MANUFACTURING (Check one only)
(13) Agriculture, Forestry, Fishing & Mining
(14) Transportation Services
(15) Storage & Warehousing Distributor
(16) Distributor
(17) Construction
(18) Retail Trade
(99) Others Allied to the Field (please specify)____________________________________________________________________
4. Which of the following categories best describes your PRIMARY function? (Check one only)
(A) Executive Management
(B) Purchasing / Procurement
(C) Engineering / Design Engineering / Research & Development
(D) Storage & Warehousing
(E) Financial / Administrative Management
(F) Plant Production / Operations / Maintenance Management
(G) Transportation & Distribution
(H) Materials Management
(Z) Other (please specify)____________ _
5. What is the approximate number of employees at this location?
TURMOIL AND RESILIENCE
Labour disruptions, trade uncertainties and record-breaking strikes mark 2024 as one of the most challenging
years for Canada’s logistics sector
THE THEME FOR 2024 in the Canadian supply chain has been marked by labour disruptions, union tensions and international trade challenges.
From labour disputes involving dockworkers on the West Coast, the Montreal port strikes and the Air Canada pilot strike, to the Canada Post strike and the arbitration for one of the most significant lockouts in histor y between CN and CPKC—still unfolding as I write—2024 has certainly been one for the books.
Though these disputes address different issues, they all pose the same risk: a significant impact on Canada’s supply chain and, ultimately, the economy.
Here’s a look back at what has undeniably been one of the most turbulent supply chain years in recent history:
In June, the Canada Border Services Agency (CBSA) was in a legal strike position, citing fair wages, flexible work hours and improved benefits. While the strike was averted, a work stoppage could have led to extended border wait times and entry documentation delays, potentially catastrophic for many Canadian impor ts.
The CN/CPKC lockout ended Aug. 26, though no resolution has been reached. This dispute stemmed from worker demands for better wages, benefits and scheduling. Although the current collective agreement prevents further strikes or lockouts, mediation isn’t scheduled until March 2025. If no agreement is reached, arbitration will begin in April, with a 60-day period for the arbitrator to issue a decision.
Air Canada pilots narrowly avoided a potential strike with one of the largest wage increases in Canadian history, amounting to a 42 per cent raise and nearly $2 billion in additional value over a four-year period.
On Oct. 31, two of Montreal’s four port terminals were shut down as dockworkers initiated a new partial strike, disrupting 40 per cent of operations at one of Canada’s busiest ports. This walkout was part of an ongoing strike on overtime shifts, following a three-day strike at the same terminals ear-
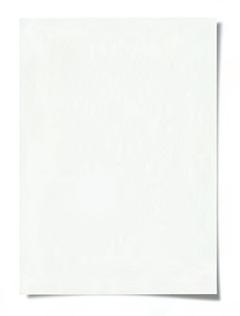
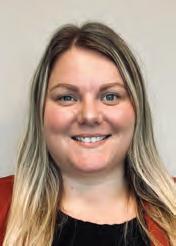
VICTORIA JONES is a supply chain specialist at Tyers Foods
lier in the month.
Meanwhile, the International Longshore and Warehouse Union Ship and Dock Foremen Local 514 launched an open-ended strike Nov. 4, affecting Vancouver and Prince Rupert, Canada’s busiest ports. This strike is expected to have ripple effects, driving up freight costs and causing congestion at ports and inland rail facilities just as we approach the holiday season. It’s anticipated that this work stoppage could impact $800 million in goods daily. In a similar strike last year, a 13-day stoppage affected over $6 billion in Canadian trade.
As the world’s largest producer and exporter of potash, Canada’s West Coast ports are essential for exporting this resource overseas; a shutdown would cost the industr y $9.7 million in lost revenue per day. With 33.72 per cent of Canada’s GDP tied to exports and 33.54 per cent tied to imports, disruptions at ports could have astronomical consequences.
Canada Post workers also went on strike Nov. 15, impacting parcel and mail service for millions of Canadians as the holiday season approaches. Canada Post announced Nov 12 it had received a 72-hour strike
notice from the Canadian Union of Postal Workers (CUPW) for both urban and rural and suburban mail carrier bargaining units with CUPW in a legal position to begin strike activity. Canada Post said it would continue delivering packages it had received prior to the strike but would not accept any new mail or parcels while negotiations were ongoing.
If that wasn’t enough to keep supply chain professionals awake at night, the U.S. election has added another layer of uncertainty. Canadians were on edge awaiting the outcome, as both presidential candidates raised concerns around potential trade disruptions. Either a Kamala Harris or Donald Trump presidency brought the possibility of renegotiating the United States-Mexico-Canada Agreement (USMCA) and broader trade with Canada. Trump, in particular, campaigned on imposing global tariffs and encouraging U.S. manufacturing.
Now, with Trump elected as the 47th president, there’s much anticipation about what this could mean for Canadians. A key issue is the USMCA, which Trump renegotiated during his first term. In 2018, he signed the USMCA, replacing NAFTA, which he had labelled “the worst trade deal ever made.” Now, he’s looking to renegotiate it once more. Early on election night, Trump announced plans to impose a 10 per cent global tariff on all imported goods, a move that could significantly impact the Canadian economy.
Ottawa has signaled a willingness to negotiate, seeking either tariff exemptions or some form of relief—a discussion that will be watched closely by Canadians and supply chain professionals alike.
With the future of Canada’s ongoing labour disruptions uncertain and the looming possibility of trade conflicts with the U.S., it’s clear that nothing is set in stone as we approach 2025. However, if the Canadian supply chain has proven anything, it’s resilient, and we’re ready to take on whatever challenges lie ahead.
HOW TO PREVENT STRUCK-BY INCIDENTS
A hazard management process including a review of past incidents is the best way to prevent traumatic, and often deadly, struck-by incidents
INCIDENTS INVOLVING being struck by objects are a major hazard in warehouses and distribution centres, often resulting in severe, life-altering injuries and fatalities. These incidents typically happen in two ways: when vehicles or mobile equipment hit pedestrians, and when materials fall from racks or high storage, striking nearby workers.
Given the significant impact these incidents have on workers and workplaces (including both direct and indirect costs), warehouses and distribution centres need to take proactive steps to prevent them.
This requires a thorough hazard-management process to identify and effectively control struck-by risks. Engage internal stakeholders in the process, including the warehouse manager, shippers/receivers, safety committee members, mobile equipment operators, truck drivers and pedestrians, among others.
A proven approach includes reviewing all related documentation, such as incident reports, policies, procedures and training records; conducting observations and interviewing key staff; and consulting applicable industry best practices, such as CSA Standard B335, Safety Standard for Lift Trucks and A344, User Guide for Steel Storage Racks.
How can incident reports help?
Reviewing past incidents and asking relevant questions can help isolate root causes, address them, and determine appropriate control measures. Here are two examples:
Incident 1: Struck by a falling load
A lift truck operator places a pallet on the upper level of a storage rack. Unaware, the operator inadvertently pushes a dislodged box into an adjacent pallet, causing it to fall to the floor and strike a worker.
Questions arising from this incident include:
1. Are loads secured with wrapping or strapping before being placed on racks?
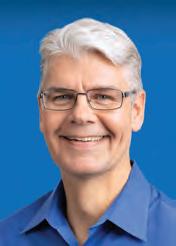

NORM KR AMER, CRSP, P.MM, provides expert, in-depth health and safety consulting services for Workplace Safety & Prevention Services (WSPS) as a warehouse specialist in the Greater Toronto region.
2. Are workers, such as order pickers, working on one side of back-to-back racking while a load is being placed from the opposite side?
3. Do lift truck operators have good visibility, possibly aided by camera technology?
4. Are lift truck operators competent, with sufficient practical training, including experience placing pallet loads at higher elevations in a safe environment?
5. Are racking accessories like mesh decks, safety bars, backstop beams or netting in place to prevent loads from falling?
6. Are pallets inspected to ensure they can support the load and are free of damage that could cause instability?
7. Are pallets the correct size for the racks? A pallet that’s too large (with excessive overhang on the beam) or too small (barely touching the beam) increases the likelihood of loads falling.
8. Is there sufficient flue space between back-to-back racks to prevent one pallet from pushing against another?
Incident 2: Struck by a forklift truck
A lift truck operator reverses into a worker pulling a pallet jack to the shrink wrapper, causing a critical injury.
Questions to consider:
1. Do lift truck operators need to reverse? Can risks be minimized by implementing a one-way traffic flow?
2. Can foot traffic be reduced or eliminated in areas where lift trucks operate?
3. Can workplace equipment, including the pallet wrapper, garbage compactor and pallet dispenser, be reorganized to reduce traffic congestion for both people and mobile equipment?
4. Is the correct mobile equipment being used? Would a standup counterbalance forklift, which allows operators to face their direction of travel, be safer than a sit-down model?
5. Could pallet loads be lower to improve visibility and reduce the need for reversing?
6. Do lift trucks have safety features such as backup alarms, cameras or swivel seats to improve operator comfort and allow for safer operation?
7. Are operators trained to use the horn to warn pedestrians at blind corners or when reversing, especially since battery-powered equipment may be harder to see or hear?
8. Are mobile equipment operators maintaining a safe speed, particularly when people are nearby, in confined spaces or at blind corners? Should the workplace adopt lift truck speed control technology to limit speeds? The Material Handling Equipment Distributors Association generally recommends a maximum speed of 13 km/h (8 mph).
Hazard management, including identifying struck-by risks, cannot be left to chance. Follow a structured process, involve appropriate personnel and seek input from those with firsthand experience. Lift truck operators, who perform their tasks daily, often have valuable insights into preventing struck-by injuries.
THE POTENTIAL IMPACT OF THE TRUMP PRESIDENCY
THE U.S. PRESIDENTIAL election has already begun reshaping global dynamics, particularly in trade, even before the president-elect assumes office Jan. 20, 2025. It is an unprecedented situation: elected for a first term in 2016, Donald Trump lost the 2020 election but secured a majority of electoral votes and the popular vote in 2024. This, despite his claims of victory in 2020 and his role in inciting the Jan. 6, 2021, attack on the U.S. Capitol.
During his first term, Trump appointed three ultra-conservative judges to the Supreme Court of the United States (SCOTUS). The court later granted him immunity from prosecution, further consolidating his power. The Republican Party, under his leadership, also regained majorities in both the House of Representatives and the Senate, giving the new president unprecedented influence.
But these developments alone do not fully capture the shift in global realities. One particularly alarming development during the campaign involved Elon Musk, the world’s richest man and a vocal Trump supporter. Musk offered $1 million in a daily lottery to individuals who were registered voters in swing states and had signed his petition in favour of free speech and the right to bear arms—an act that, while some questioned its legality, went unpunished. Instead, Musk saw his stock holdings soar in value. Such overt electoral corruption, more commonly associated with autocratic regimes in so-called “banana republics,” marked a troubling first in U.S. politics. While some observers believe the election was effectively bought, few are willing to say so outright.
This is the new reality: laws no longer apply equally to everyone, and money can buy almost anything. Moreover, it seems the loudest and most aggressive voices now dominate, regardless of the substance of their message.
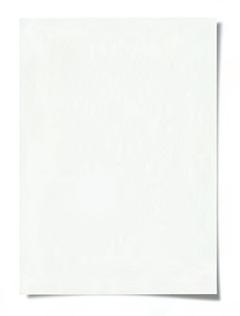
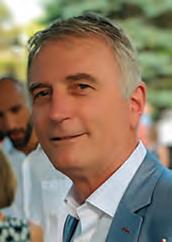
CHRISTIAN SIVIÈRE runs Solimpex, and is an international trade consultant and lecturer. christian.siviere@videotron.ca
Trump’s promises on trade reflect this chaotic approach. He has proposed a 10 per cent tariff on all imports into the U.S., while simultaneously pledging to reduce consumer goods prices—an obvious contradiction, given the high proportion of imported goods in U.S. markets. If enacted, such a policy would almost certainly trigger retaliatory tariffs from trading partners, leading to trade chaos. By late November, Trump’s rhetoric shifted again, with threats of 25 per cent tariffs specifically targeting Canada and Mexico—classic bullying tactics against smaller nations.
Dividing allies has long been a Trump trademark, as evidenced by his demands on NATO, the renegotiation of NAFTA and his public admiration for autocrats like Vladimir Putin, Kim Jong Un and Xi Jinping. His intentions regarding China remain unclear: he could impose even steeper tariffs, or Beijing might find a way to appease his ego with some form of deal. Either way, his tax cuts for corporations and the wealthy will exacerbate inequality—a trend
already well documented in recent years. Growing disparities in wealth indirectly fuel the migrant crisis, as those in poverty seek better opportunities in wealthier nations like the U.S., Canada and European countries. Expelling undocumented immigrants addresses the symptom, not the root cause, of these challenges.
The environmental outlook under Trump is similarly grim. The U.S. will likely withdraw from international climate efforts, already undermined by the recent COP conferences hosted in oil-rich autocracies. With the rallying cry “drill, baby, drill,” his administration appears poised to side with climate change deniers, to the detriment of the planet. Early government appointments offer little reassurance: someone who has been called an anti-vaccine conspiracy theorist overseeing health policy, a former wrestling executive in charge of education and Musk tasked with slashing government spending. This shift from serving the public good to prioritizing a business-first ethos will deepen societal divides. Musk’s potential conflicts of interest—overseeing agencies regulating his businesses—are another red flag, reminiscent of the failures seen when Boeing began self-certifying its aircraft amid a weakened Federal Aviation Administration.
Trump’s current rhetoric raises concerns about the global order. His admiration for dictators is well known, but will he abandon Ukraine as he did the Sahrawis and Kurds during his first term? Will he strike a deal with China that could pave the way for an invasion of Taiwan? His encouragement of Benjamin Netanyahu’s hardline policies suggests a continued disregard for fostering peace. At a time of escalating local conflicts, environmental crises and human challenges, the world needs cooperative leadership. Unfortunately, it seems unlikely that the United States under Trump will rise to that challenge.
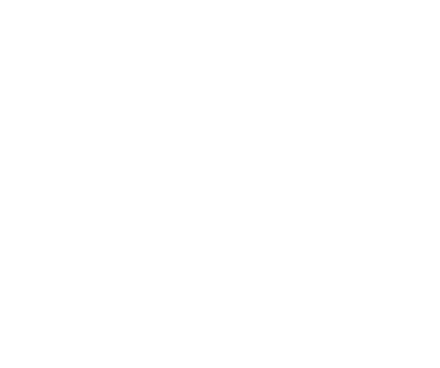
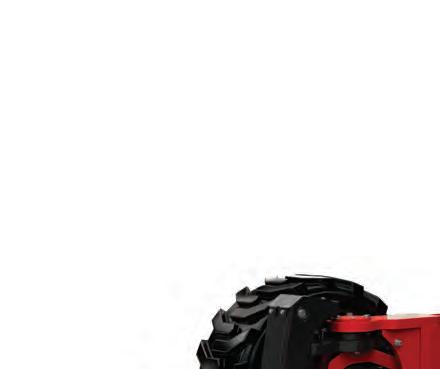
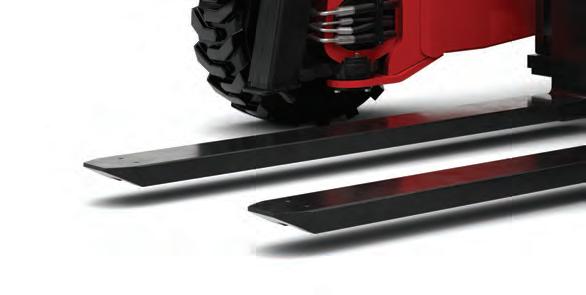
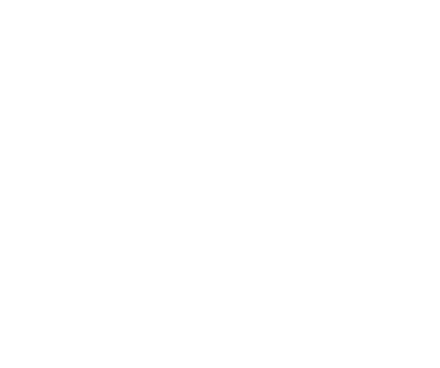
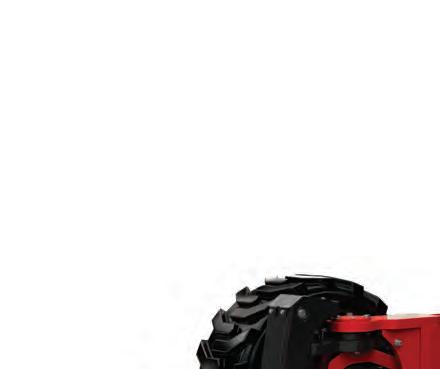
BUILT TOUGH. MOUNTS EASY.
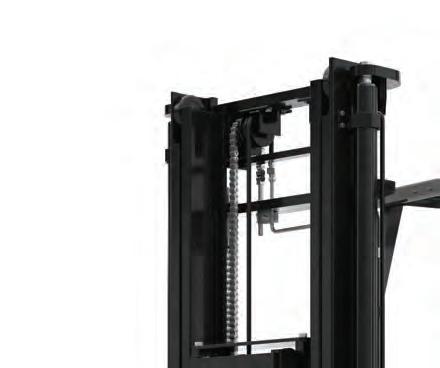
TMM 45 TMM 45-4W

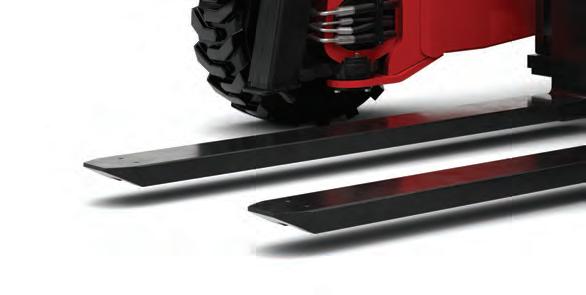
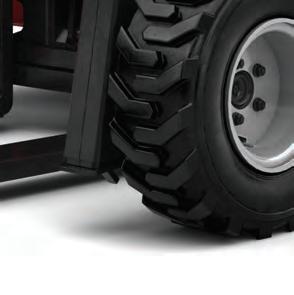
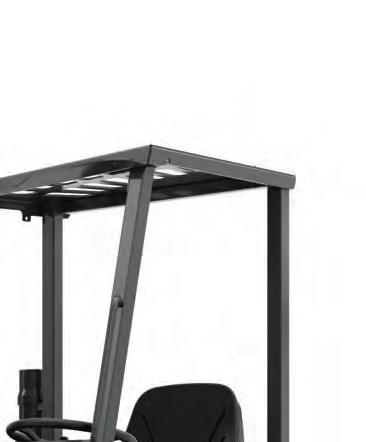
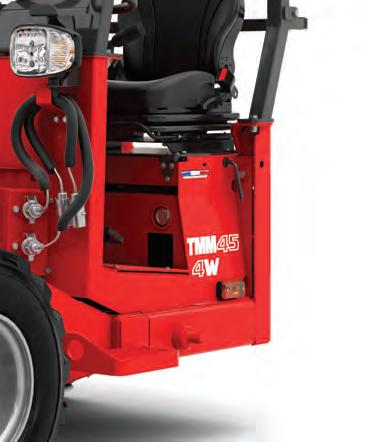
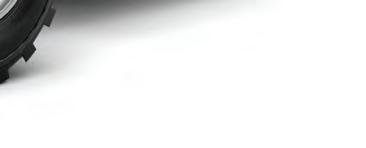
IN-STOCK NOW INQUIRE ON END-OF-YEAR DEALS
Manitou has set the industry standard in heavy-duty forklifts for decades — and the lineup of TMM truck-mounted forklifts combine the reliability and strength of its o -road forklifts with the responsiveness and control of its industrial forklifts. Each machine is perfect for o -road operation with 10 inches of ground clearance — and the four-wheel steer model provides added versatility while carrying long loads.
Manitou has units in stock now for end-of-year ordering + limited-time year-end financing o ers. Contact your local Manitou dealer today for more information!
See our full range of solutions for your business at Manitou.com.
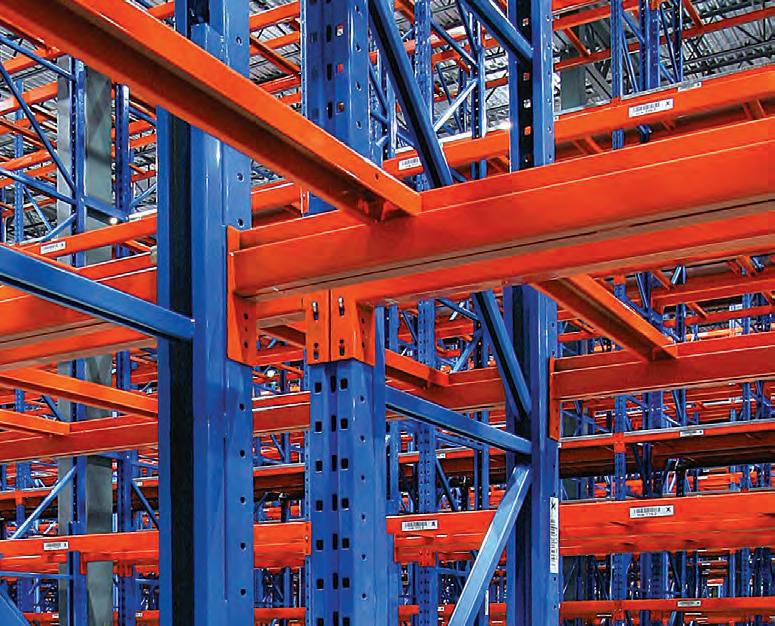

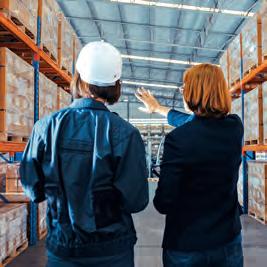
Your partner in facilities evolution
Strong foundations. Smart evolution.
To stay competitive and get ahead, you need innovative, scalable and safe solutions. These solutions can help with better storage, distribution, fulfillment or any combination that can grow with your business as it adapts to change.
As your partner in facilities evolution, you can count on Konstant to transform your facilities. Collaborate with our team to optimize your facility today and evolve, anticipate, adapt and imagine the facility of your future.
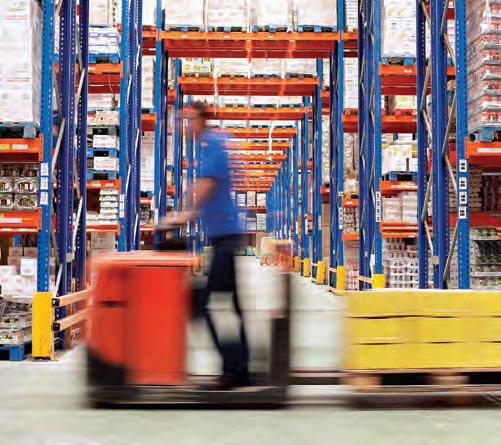
ECOSYSTEM
Get integrated logistics solutions: racks, shelving, trucks and robotics from our partners including Johnston Equipment and GNJ Automation.
EXPERTISE
Access comprehensive services for your project lifecycle, from planning to ongoing management with a skilled team ensuring quality at every step.
EXPERIENCE
For more than 50 years, Konstant has served businesses across Canada, adapting our services to evolving facility management needs.