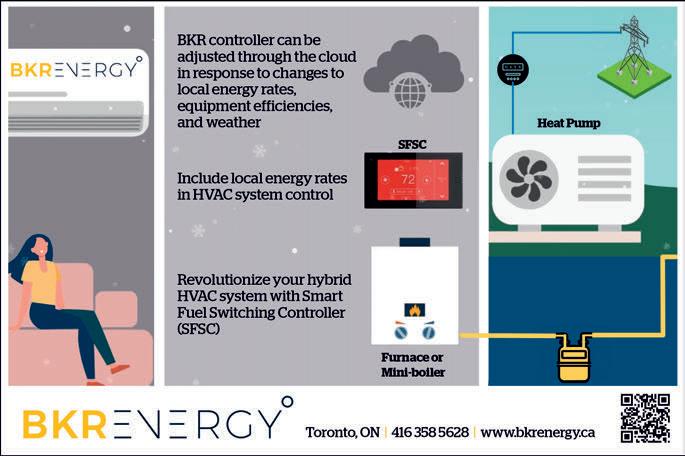
4 minute read
EXPLANATION
frigerant to enter from either fitting, directing it to flow from the outside of the core to the inside, and then exiting the shell through the opposite fitting.
Suction Filter-Drier: In the case of a highly contaminated system, where a suction filter-drier is needed to assist in the removal of contaminants, the only location for this would be between the outlet of the four-way reversing valve and the inlet of the compressor.
Given the limited space between these two components, a standard suction filter-drier is too large to be piped in. A special “pancake” style suction filterdrier must be used (see Figure 5, previous page). (note the Schrader access fittings on the inlet and outlet, as these are present to monitor the pressure drop through the filter-drier.)
Expansion Device: The indoor coil and outdoor coil both require an expansion valve. Since standard thermostatic expansion valves (TEV) are not suitable for reverse flow, they must be piped in parallel with a check valve.
This piping arrangement allows (1) liquid refrigerant to enter the TEV when a coil is used as an evaporator, and (2) condensed liquid to exit the coil (through the check valve) when a coil is used as a condenser.
There are also special “reverse flow” TEVs with internal check valves available. The internal check valve provides a reverse flow path (liquid entering the valve’s outlet, flowing around the TEV port via the check valve, then flowing into the common liquid line) when the coil is used as a condenser.
In package heat pumps, where there is a minimal distance between the indoor and outdoor coil, an electronic expansion valve (EEV) can be used in the common liquid line.
Ground Source
For years, when the term “heat pump” was mentioned it was understood to mean a conventional heat pump as de - scribed above: that being a compressor, indoor and outdoor coils, and some form of expansion device for each coil, and a four-way reversing valve mounted between the compressor outlet and the inlet to the outdoor coil.
Over the years there have been advancements to heat pumps which have allowed them to operate more efficiently and over a broader range of temperatures in the winter. Aside from the air source options there are also “ground source” heat pumps (GSHP) that use either ground water or surface water as the outdoor coil’s heat transfer medium—a heat sink in the cooling mode or a heat source in the heating mode.
Ground source water a depth of 5- to 10-feet will remain at a fairly constant temperature year round. Likewise, water from subsurface aquifers and water from surface bodies will remain fairly constant in temperature (although at slightly greater depth would be required for surface bodies).
This is in contrast to the near 100F temperature difference that the outdoor ambient air temperature may experience between summer and winter conditions. This provides two benefits for heat pump operation:
• In the heating mode, the constant ground water temperature will provide a constant heat load for the outdoor coil, allowing sufficient load on the compressor to generate sufficient mass flow and heat of compression to provide a constant source of heat to the conditioned space.
• In the cooling mode the comparably low water temperature used as the heat transfer medium for the outdoor coil (condenser) will result in lower discharge pressures as compared to an air cooled condenser in the dead of summer. This results in greater compressor capacity and reduced electrical consumption, and can be illustrated by the higher SEER ratings available with GSHPs.
The various methods available for using the ground source water, can be categorized into either closed loop or open loop systems.
Closed Loop: This is an application where the outdoor coil is buried in the earth below the frost line, with the earth or ground water being used as the heat source/heat sink. In essence, the outdoor coil is fashioned into either a vertical or horizontal heat exchanger, and buried in the ground (see Fig. 6).
Horizontal heat exchangers require significantly more land area, but given the fact that they are not buried nearly as deep as vertical heat exchangers, they are less costly to install.
Vertical heat exchangers are normally used on larger buildings where it would be impractical to dedicate the necessary land required for burying a horizontal heat exchanger. These will be constructed of polyethylene and buried in holes drilled approximately 100- to 400-feet deep, and located approximately 20-feet apart. Each hole will have two vertical pipes connected at the bottom with a U-bend, forming a loop. Each vertical loop is connected via a manifold, and then connected to the heat pump.
Surface water heat exchangers can be used if the location has an adequately sized body of water. Depending on the Btu capacity of the heat pump there will be minimum requirements for volume and depth of the water body (in colder climates the water will need to be of sufficient depth such that the heat exchanger can be located well below the freeze line. Additionally, the water quality would need to meet some minimum specifications.
Open Loop: Imagine a system with a water cooled condenser being fed by an endless supply of 60F water. Because it’s an endless supply of supply water, there is no need for a cooling tower to transfer heat from the condenser water.
Or imagine a chiller receiving an end - less supply of 60F water at its inlet. The water sees a 10F reduction in temperature in the chiller heat exchanger, but because of the endless supply of water there is no need for a fan coil unit to absorb heat to the chilled water.
That is the essence of an open loop system, an endless supply of water available as a heat sink for cooling or a heat load for winter applications. A pump supplies water to the heat exchanger in the heat pump. Since it is an endless supply, it is simply pumped through the heat ex- changer, and then onto another location separate from the source of the water.
One drawback of this method is that there might be an issue with fouling of the heat exchanger due to the condition of the water. As fouling increases, it will then cause a reduction in the efficiency of the process.
In larger commercial applications hybrid systems might be employed where the presence of refrigeration equipment using water cooled condensers (and the accompanying water tower) would pro - vide a year round supply of water for the heat pump’s heat load needs in the winter, and supply water for the heat sink needs in the summer.
The embrace of heat pump technologies around the world is growing. With the shift to decarbonization and electrification, it’s best to learn more about how these systems operate and can be applied for your clients. <>
Dave Demma holds a degree in refrigeration engineering and worked as a journeyman refrigeration technician before moving into the manufacturing sector where he regularly trains contractor and engineering groups. He can be reached at ddemma@uri.com.
(This article originally appeared in HPAC Magazine, October 2022)