
2 minute read
STUDY OFFERS NEW INSIGHTS ON INJURY PREVENTION
Workers and managers have differing views on workplace safety, and that’s a problem
A NEW STUDY FROM Toronto Metropolitan University and Workplace Safety & Prevention Services has found significant differences between workers and managers when it comes to their attitudes, beliefs and perceptions of health and safety in the workplace.
Differences like these can lead to misunderstandings, conflict, increased risk, and poorer safety performance, says the study. It sets out a roadmap that workplaces, including those in warehousing and distribution, can follow to reconcile the different views of managers and workers, with the goal of reducing injuries.
Key differences
Surveys filled out by 2,401 workers and 1,562 managers/supervisors gauged their perceptions of health and safety, their beliefs and attitudes, and their top occupational health and safety concerns.
A larger number of workers felt the workplace ‘a bit unsafe.’ Although this may be because workers often face more hazards than managers do, employers should consider opportunities to improve employees’ perception of safety. For example, ask employees via an anonymous survey what they think the top three hazards are, and what could improve safety. Review and implement some of the great ideas presented.
The vast majority of workers and managers could not identify the ‘employer’ as the party primarily responsible for health and safety in the workplace. This may reveal a lack of understanding or interpretation of the internal responsibility system.
In addition to providing training to clarify roles, employers should tangibly demonstrate their responsibilities by participating in safety communications and training; following all safety procedures; participating in workplace inspections; and providing adequate resources for implementing safety suggestions in a timely way.
More workers felt that health and safety training was insufficient and inadequate. The foundation of safety training is a well-documented hazard assessment. Is a training matrix completed on an annual basis, considering the safety training needs of every position? This includes safe lifting for manual material handlers, to operation of power walkies, as well as training on correct pallet placement on steel storage racks to name a few. Does safety training include visual demonstrations and practice sessions, which make it much more effective?
Workers were less confident about health and safety measures in the workplace. This included the frequency of safety communications in the workplace. Short safety messages on a regular basis stick better than one lengthy training program once per year. It also included the frequency with which they were asked about their safety concerns. This is a huge missed opportunity. Your workers know what is working and what is not. So, get their valuable input.
The majority of managers and workers agreed that ‘workplace injuries and accidents are an inevitable part of life’. This finding is concerning. Are injuries occurring because productivity is prioritized over performing tasks safely, which encourages unsafe behaviors, such as operating mobile equipment at high speeds in the warehouse? Or because of inadequate training and supervision? Injuries can be prevented by identifying and controlling the root causes of risk and ensuring work procedures are clearly defined and workers are held accountable.
Four recommendations
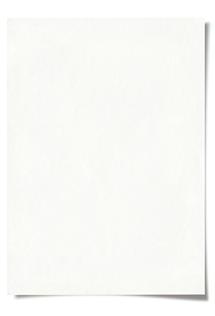
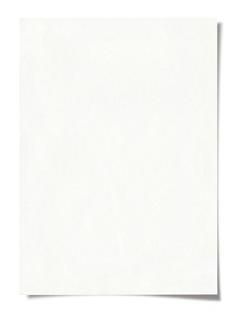
Workers’ safety performance is greatly influenced by their relationship with their managers, including a reduction in injury rates when their managers showed greater concern for them and supported the workers’ positive safety behaviors. Bridging gaps in perceptions, attitudes, and belief is critical to improving performance. The study recommends employers take four steps.
First, provide more education and training. Health and safety training leads to improvements in knowledge, safe behaviors and health and safety outcomes, says the study.
Second, be proactive about health and safety concerns. Don’t wait for an incident to happen before adequate controls are put in place.
Third, improve your safety culture. Workers will quickly determine if what is said in training is happening on the warehouse floor. There shouldn’t be a disconnect, and if there is, this is a management issue. Improvements to safety culture can be made by many seemingly small things, such as having a safety budget, providing ongoing equipment maintenance, sending the message that safety always trumps speed, effective inspections, quick reporting and correction, good housekeeping, to name a few.
Fourth, improve communication on health and safety issues. Constant and effective communication will ensure both managers and workers are singing from same song sheet.