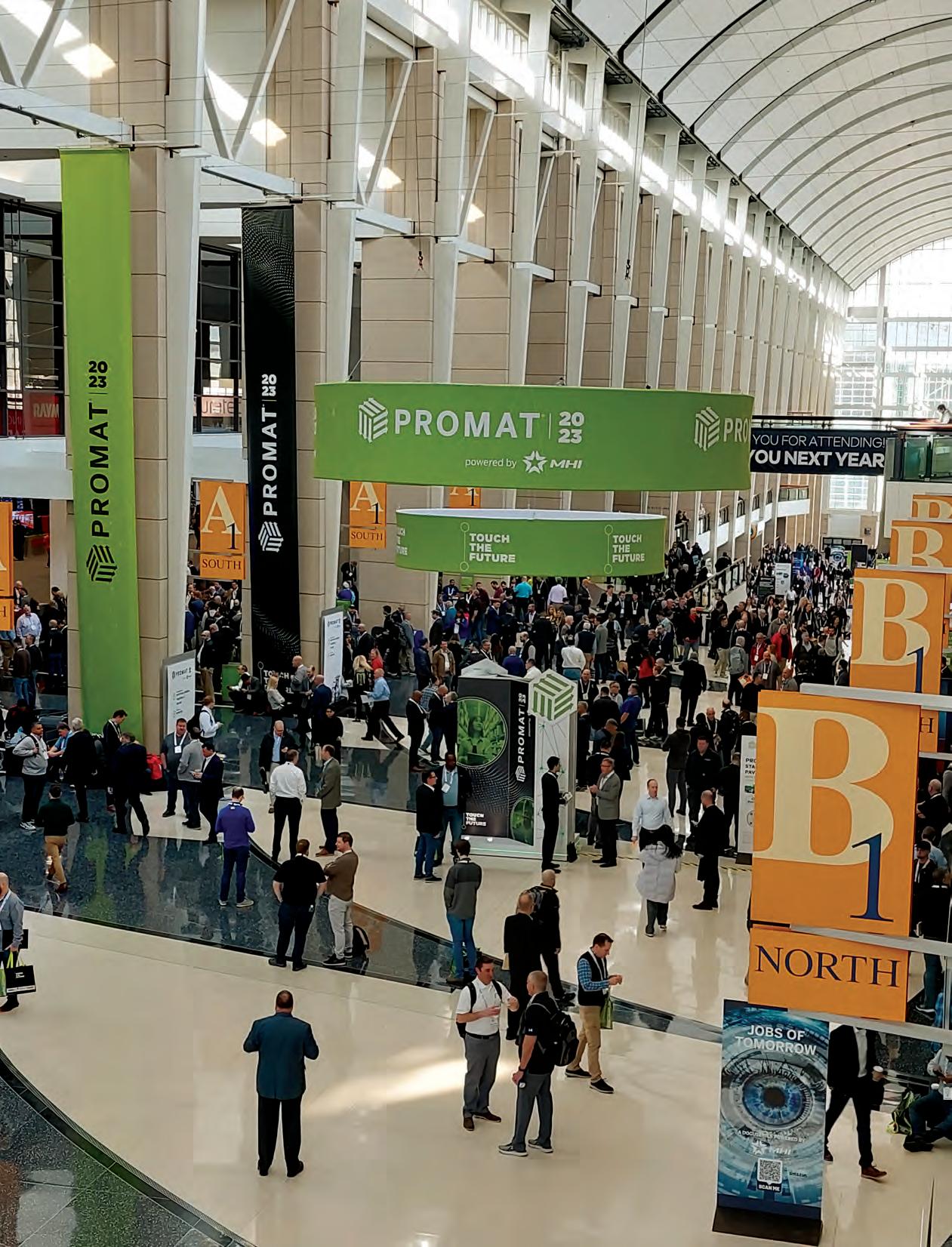
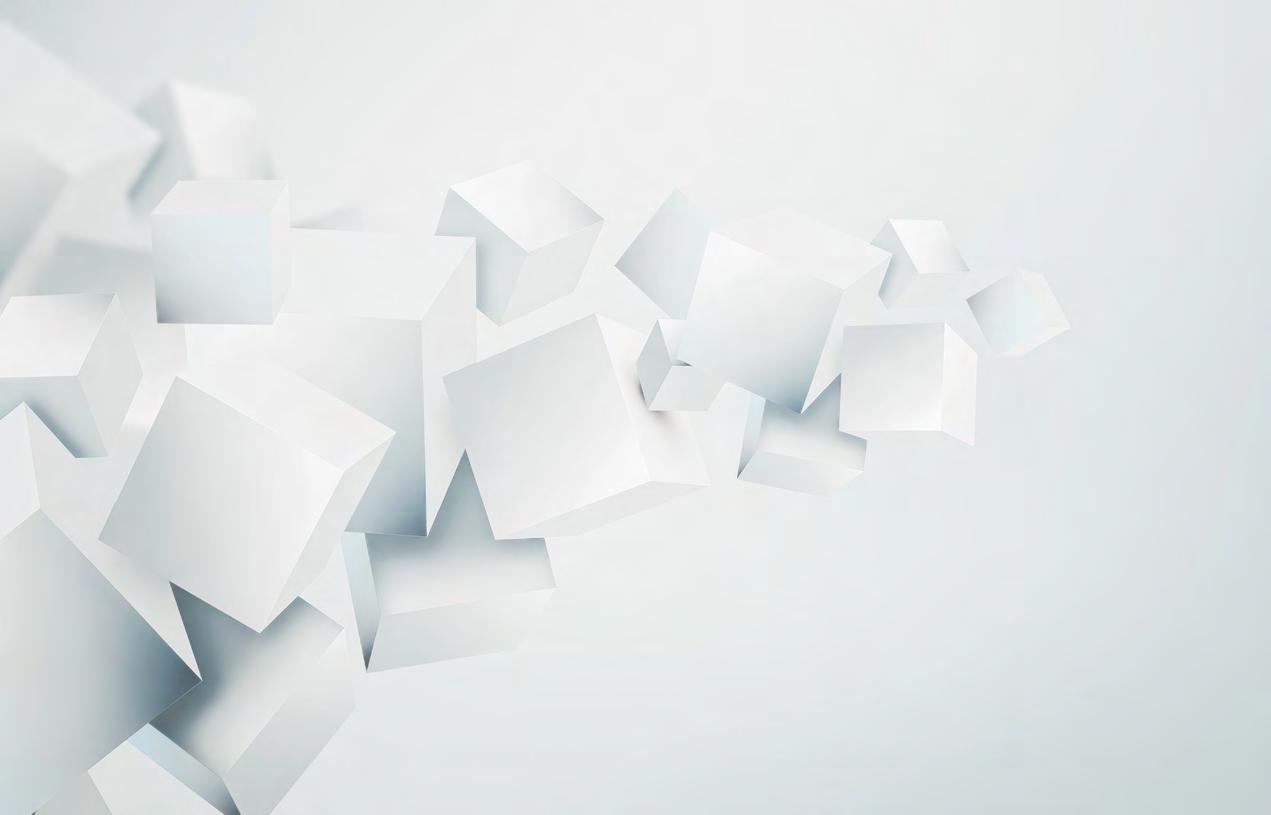
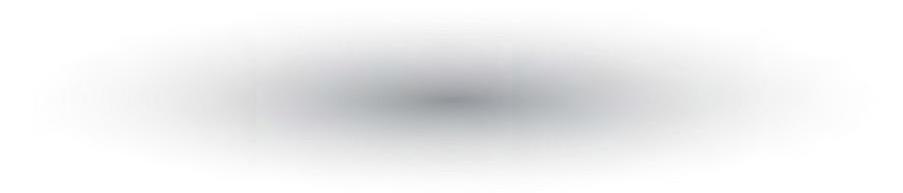
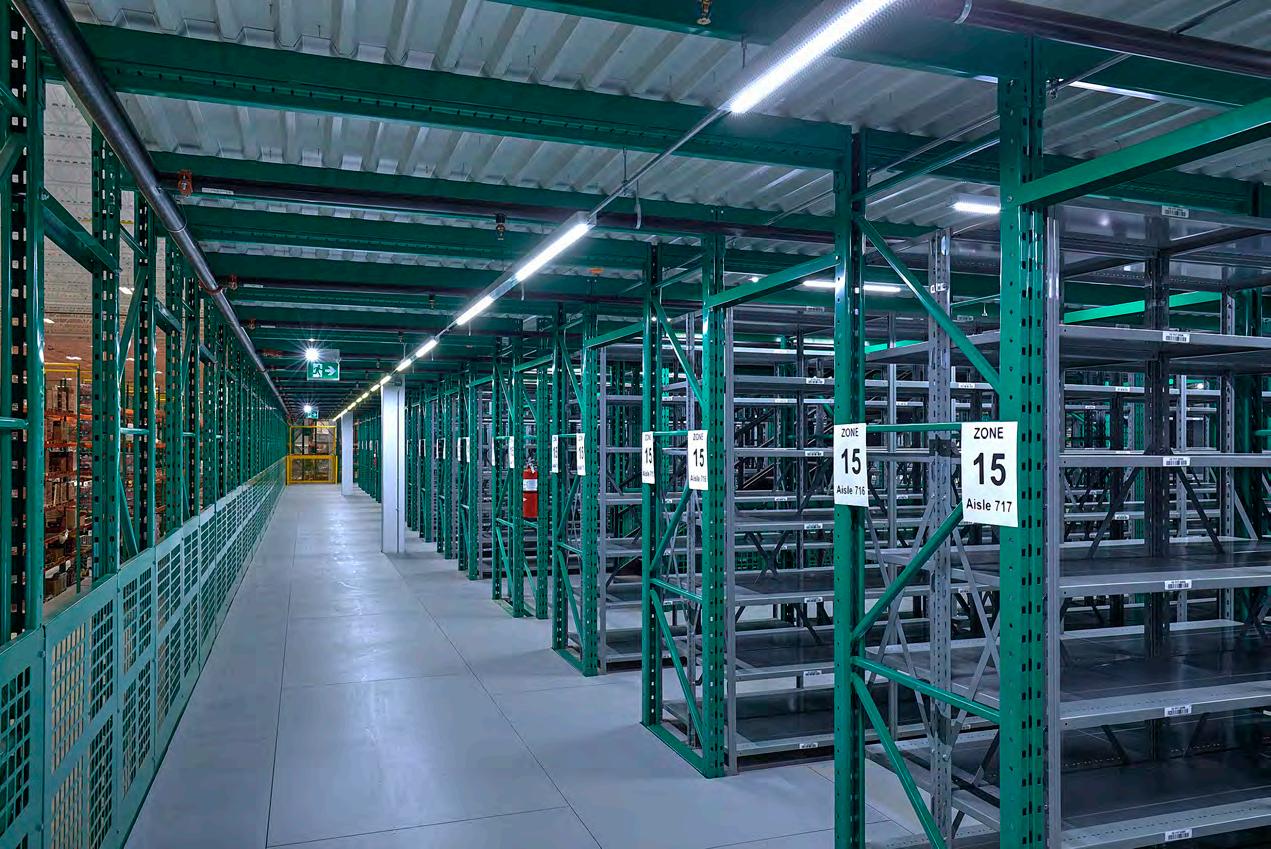
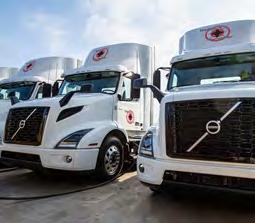

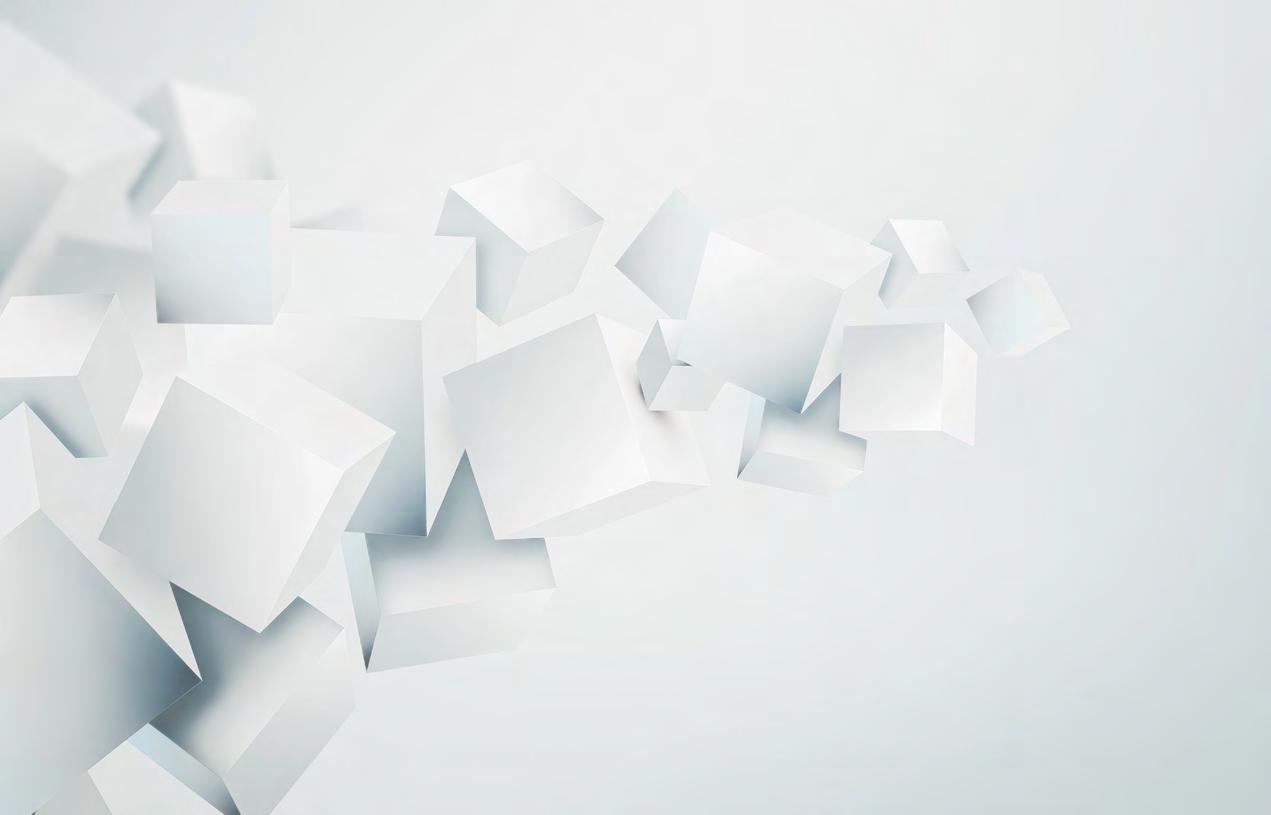
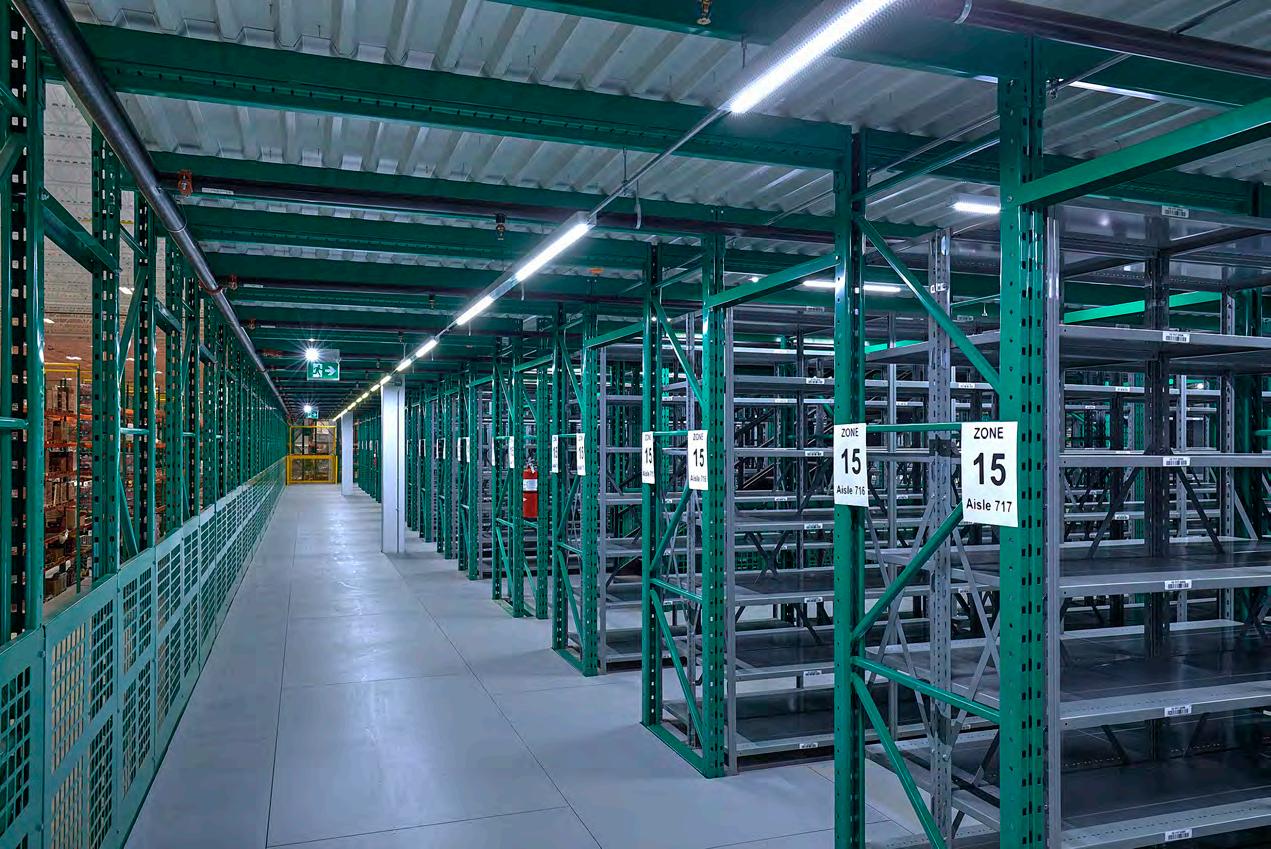

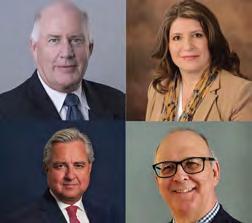
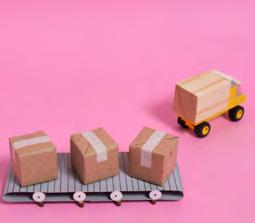
CITT is Canada’s Logistics Association - and also the home of Canada’s Logistics Community. If you’re involved in the business of logistics in Canada, you can officially join your national community of practice today.
Be well-connected. You’ll be part of Canada’s most engaged community of logistics professionals. Enjoy the insiders’ forum and interactive networking. Learn, share ideas, and connect for career and business opportunities.
Be informed. Enjoy free webinars from the community’s thought leaders. Get priority registration to learning events. And receive significant discounts to attend Canada’s Logistics Conference, take courses towards the CCLP designation and more
Be recognized. You’ll get a fully verified digital credential identifying you as part of Canada’s most respected logistics organization.
Publisher | Delon Rashid (416) 459-0063 delon@turnkey.media
Editor | Emily Atkins (416) 262-4106 emily@turnkey.media
Contributing Writers | Roger Brereton, Craig Fairclough, Dave Heller, Norm Kramer, Christian Sivière, Andrew Welling
Creative Director | Samantha Jackson
Video / Audio Engineer | Ashley Mikalauskas, Nicholas Paddison
Sales | Delon Rashid, (416) 459-0063 delon@turnkey.media
Peter Bulmer, (585) 653-6768 peter@turnkey.media
Production and Ad-ops | Tracy Stone tracy@turnkey.media
Inside Logistics magazine is published by Turnkey Media Solutions Inc. All rights reserved. Printed in Canada. The contents of this publication may not be reproduced or transmitted in any form, either in part or full, including photocopying and recording, without the written consent of the copyright owner. Nor may any part of this publication be stored in a retrieval system of any nature without prior consent.
Canada Post Canadian Publications Mail Sales Product Agreement No. 43734062
“Return Postage Guaranteed” Send change of address notices, undeliverable copies and subscription orders to: Circulation Dept., Inside Logistics magazine, 48 Lumsden Crescent, Whitby, ON, L1R 1G5
Inside Logistics magazine (ISSN No.: 0025-5343 (Print); 1929-6460 (Digital) is published six times per year by Turnkey Media Solutions Inc., 48 Lumsden Crescent, Whitby, ON, L1R 1G5 From time to time we make our subscription list available to select companies and organizations whose product or service may interest you. If you do not wish your contact information to be made available, please contact us.
WHILE THE ROBOTS, automated guided vehicles and fully autonomous equipment were the must-see exhibits at ProMat 2023 in Chicago last month, a rising category of software is gaining traction alongside the automated machinery.
An increasing number of software providers are offering the ability to coordinate autonomous equipment from different vendors into a single cohesive fleet. Their solutions promise to communicate seamlessly with all the diverse units you need in your operation, and link to your warehouse management, control or execution software.
This orchestration software offers numerous benefits for the warehouse operator. It can speed up the deployment of automation by eliminating the need for extra programming. They use simple, drag and drop interfaces that allow users to create fleets almost instantly.
It also means the DC can employ a shifting cast of robotic characters, depending on the volume and speed of orders being processed. In an era where companies getting robots as a service instead of buying them, allowing for a changing line-up, this means configuring your equipment to meet changing needs is that much easier.
Of course, to achieve this kind of agnostic fleet orchestration, the software has to be able to bridge between each vehicle’s unique operating system and communications protocols and the warehousing control system. Interoperability is the term the industry is using to describe the capacity for different units to communicate, and it’s a stumbling block that has not been completely overcome.
The industry struggles to even define the term, says TJ Fanning, chief operating officer of SVT Robotics, one of the companies offering an orchestration service. And while there are interoperability standards that some manufacturers are using, such as MassRobotics in the US and VDA 5050 in Europe, these have not yet been adopted across the board.
That leaves companies like SVT and its competitors still trying to figure out how to conquer the Babel that is robot communications. Being able to translate myriad robot languages so that they can talk to one another and the control software, surely opens up potential for more efficient operations.
President & Managing Partner | Delon Rashid Head of Sales & Managing Partner | Peter Bulmer
Corporate Office
48 Lumsden Crescent, Whitby, ON, L1R 1G5
ISSN 0025-5343
Online 1929-6460
This is a significant area of opportunity in the warehousing and intralogistics space, and it’s one that we will be following closely and reporting on as it evolves.
The corporation has set aside $1 billion to also achieve net zero by 2050.
– Suromitra Sanatani chair of the Canada Post Corporation board of directorsconversion it has been working on with a step-van manufacturer.
By Emily AtkinsIN
announcements last month, sister companies
Purolator and Canada Post unveiled new commitments to fleet electrification.
Purolator revealed it expects to invest approximately $1 billion to electrify its Canadian network over the next seven years. This includes a plan to purchase more than 3,500 fully electric last-mile delivery vehicles and the electrification of more than 60 terminals across Canada. The spending will be the company's largest network investment in its 63-year history, with more than $100 million to be invested in 2023 alone.
More than 100 all-electric vehicles will be added to the fleet this year, with an additional 150 coming in 2024. This new fleet comprises Ford E-Transit, Motiv Power Systems EPIC4 and BrightDrop Zevo 600 models.
In March, Purolator began deploying 25 Ford E-Transit vans in London, Ontario, Richmond, British Columbia, and Quebec City. A further 55 Motiv and 15 BrightDrop models, along with several lowspeed vehicles and electric cargo bikes (e-bikes), will be added later this year.
The moves are aimed at helping Purolator reach its decarbonization goals. It wants to reduce GHG emissions by 42 percent by 2030 and reach net-zero by 2050. The company will achieve this goal by electrifying 60 percent of its last-mile delivery vehicles and investing in alternative-fuels and low-carbon technologies. It also plans to reduce emissions from electricity by 100 percent through the use of renewable sources and by diverting more than 70 percent of its waste from landfill.
For its part, Canada Post opened its first all-electric distribution depot in Nanaimo, B.C. and took the wraps off an all-electric truck
The depot will use 14 fully electric cargo vans for collection and delivery services, replacing internal combustion vehicles. As part of Canada Post’s plan to reach net-zero emissions by 2050, the company has committed to electrifying half of its national fleet of approximately 14,000 vehicles by 2030 and the entire fleet by 2040.
The corporation also unveiled the first all-electric C250 delivery truck at the Work Truck Week tradeshow. Custom-built for Canada Post by Morgan Olson, a walk-in step van body manufacturer, the C250 meets the rigorous demands of Canada Post’s delivery operations and safety requirements. While the C250 was initially developed as a gasoline model, Morgan Olson is currently developing a commercially available all-electric C250, which Canada Post is planning to test along with other electric vehicle options.
“The C250 is custom-built with employee safety, comfort and increased capacity in mind. Developed over several years, the vehicle is made to withstand the rigours of day-to-day use and to help streamline our operations for the long-term growth of our delivery business,” said Alexandre Brisson, vice-president, operations transformation, Canada Post.
The corporation has set aside $1 billion to also achieve net zero by 2050, said Suromitra Sanatani, chair of the board of directors. It will be spent on retrofitting facilities, constructing new net-zero carbon buildings, and sourcing renewable energy for its real estate and operations.
NEARLY THREE quarters of supply chain leaders are increasing their supply chain technology and innovation spending according to an industry report released at ProMat 2023.
This investment includes solutions for improved supply chain transparency and sustainability, according to the 2023 MHI Annual Industry Report, The Responsible Supply Chain: Transparency, Sustainability, and the Case for Business, which Deloitte wrote for MHI.
“Responsible supply chains must react in real-time to changing conditions, this requires actionable data, automation and automated decision-making,” said John Paxton, CEO of MHI.“Investments in automation and other digital solutions like IoT, advanced analytics and AI not only arm your operations with speed, accuracy, and improved visibility. These solutions enable the real-time decision-making and transparency necessary for reporting and improving performance up and down the responsible supply chain.”
Once again, hiring and retaining qualified workers (cited by 57 percent of respondents) and the talent shortage (56 percent) were the top supply chain challenges. This was followed closely by supply chain disruptions (54 percent), out-of-stock situations (52 percent) and customer demands (52 percent).
The worker shortage is spurring companies to invest in technologies that not only improve agility and efficiency but also reduce the need for repetitive, manual labour.
The integration of robotics into operations is seen as one solution to the labour shortage, but it’s not without challenges. “A large obstacle for organizations looking to invest in robotics is perception management. Largely, this technology is not brand-new but has matured over years to reduce errors, risk and dependency on labour,” said Jake Heldenberg, head of solution design at Vanderlande.
“Robotics are likely the next advancement
For over 100 years, Oceanex has been providing efficient and reliable intermodal transportation services safely and with environmental leadership. With our fleet of 3 vessels and the largest dedicated fleet of containers and trailers servicing the province of Newfoundland and Labrador, we keep retail shelves stocked and deliver the materials that build and support our communities, keeping the economic engines of the province running.
to automate more complex tasks to achieve significant increases in throughput while upskilling labour.”
Companies are faced with increasing pressure to become more environmentally responsible and sustainable. Almost half of this year’s respondents (48 percent) say they face increased pressure from many angles, including consumers, regulators, industry groups, traditional and social media, and other stakeholders that increasingly expect brands and their supply chains to adhere to their own high standards.
Paxton said it's incumbent on supply chain leaders to drive transparency and coordinate change to reduce emissions and move toward a circular economy.
“Sustainability will become a key competitive advantage for in the future. Investments in sustainability and transparency help reduce risk and build loyalty with customers and employees alike,” he said.
THE 2023 FEDERAL BUDGET includes a few measures to address supply chain issues.
The measures included are described in the budget document as a "down payment on Canada's National Supply Chain Strategy," which the government promises will be released in the coming months. It will be informed by the recommendations of the National Supply Chain Task Force report.
Topping the list, Transport Canada will have $27.2 million over five years, starting in 2023-24, to establish a Transportation Supply Chain Office. It will work with industry and other orders of government to respond to disruptions and better coordinate action to increase the capacity, efficiency, and reliability of Canada's transportation supply chain infrastructure.
This includes collaborating with industry, provinces, territories, and Indigenous Peoples to develop a long-term roadmap for Canada's transportation infrastructure to better plan and coordinate investments required to support future trade growth.
The Freight Management Association of Canada's president John Corey said this is something shippers have been asking for. The office will "hopefully improve communication and understanding of the supply chain’s importance to all government departments, something that currently not apparent," Corey said. He cautioned, however, that the danger is it will simply add a new layer of bureaucracy.
The budget also suggested amendments to the Canada Transportation Act will allow the government to "compel data sharing by shippers accessing federally regulated transportation services".
Compelling shippers to reveal confidential data may be harmful to shippers competitiveness, Corey said. "Without knowing, what type of data, how it will be collected, where the data will reside, who will have access to the data and how it will be used, it is difficult to comment positively on this item," he added.
Other regulatory changes planned in the budget include extending rail interswitching in the prairie provinces. Corey said extended interswitching was a key shipper recommendation in the National Supply Chain Task Force report, and is thus welcome. "Unfortunately the measure is temporary and limited geographically, but the hope is it will eventually become a permanent extension of the limit and made available to shippers across Canada," he said.
The Railway Association of Canada (RAC) said the extension of interswitching will end up costing Canadians. "This policy will cause Canadians to pay more for virtually everything that moves by rail,” said Marc Brazeau, the RAC’s president and CEO. Interswitching can slow down goods movement by 25 percent, he said.
Canadian Pacific has said that on April 14, 2023, it will exercise the authority granted by the U.S. Surface Transportation Board’s (STB) March 15 final decision and combine with Kansas City Southern (KCS) to create Canadian Pacific Kansas City.
Mediterranean Shipping Company (MSC) has taken delivery of the world’s latest record-breaking containership. The MSC Tessa has a capacity of 24,116 TEUs, stacked up to 25 layers deep.
Eight commercial fleets have signed up to retrofit trucks to use hydrogen fuel in Prince George, British Columbia. This means 82 Class 8 trucks will be retrofitted using Hydra Energy’s proprietary hydrogen-diesel, co-combustion conversion technology. They will refuel at the hydrogen refuelling station Hydra is building in Prince George.
Ontario's budget released in March is putting an extra $2.8 billion into transportation infrastructure. It calls for $27.9 billion to be spent on highways over the next decade, including $3.2 billion in 2023-2024. Most of the work planned is in the Greater Toronto Area and Golden Horseshoe regions of southern Ontario.
THE NORTHERNMOST heavy-cargo port on the Great Lakes is being developed by the BMI Group and the Red Rock Indian Band.
The two groups signed a memorandum of understanding (MOU) that will allow them to explore the redevelopment of lands formerly used by a linerboard mill in Red Rock, Ontario, as a deep-water port. Red Rock is on the northernmost shore of Lake Superior, just off the Trans Canada highway, about 110 km northeast of Thunder Bay. It is the closest port to the Ring of Fire mining development area.
The Red Rock Integrated Marine Supply Chain, RRIM SC partnership between the BMI Group and the Red Rock Indian Band intends to connect the Great Lakes seaway to existing transportation infrastructure from the Red Rock
Join
port through to the Trans-Canada Highway and the northern Community Infrastructure Corridor.
The former linerboard mill site is a 360-acre property within the Township of Red Rock. The mill was closed in 2006 and most of the buildings were removed.
“The Red Rock Mill site is well known for its industrial history, but now we would like to turn the page and work with the Red Rock Indian Band to create other opportunities for the region,” said Paul Veldman, BMI managing partner.
“We have put considerable resources into the site this year to initiate environmental remediation and develop an initial concept for redevelopment. We recognize the Red Rock Indian band as a key partner and we look forward to working with them.”
• 15+ learning sessions on must-know industry issues, including updates on each of the modes, the economy, HR, latest developments in tech and more
• Connect and re-connect with other industry professionals with many dedicated networking opportunities including the popular opening reception and prestigious annual awards dinner
• Fellow attendees from carriers across modes, shippers representing a wide range of sectors, solution providers, and many others
• 20+ years as Canada’s can’t-miss event for logistics professionals
The Montreal Port Authority (MPA) has appointed of Nathalie Pilon as chair of the board of directors. Pilon has been a member of the MPA board since 2017, when she was appointed by the federal government. Pilon was president of ABB in Canada, member of the executive board of ABB Americas and president of Thomas & Betts Canada, where she was with the company since 1996 as vice-president of finance and information technology. Named one of Canada's Top 100 Most Powerful Women in 2011 by the Women's Executive Network, Pilon received the Leadership Award from the Association of Québec Women in Finance (AFFQ) in 2015, and in 2018, an honorary doctorate from Concordia University. She holds a Bachelor of Business Administration from HEC Montreal.
Shannon Karl has joined Tecsys Inc. as chief marketing officer. Karl brings over 25 years of
executive marketing experience, most recently at Intelex, where she was CMO. Previously, she was vice-president of industry marketing at SAP. She has held global and regional marketing leadership roles at IBM and PwC Consulting.
Bolloré Logistics Americas has appointed Nicolas Saignat as vice-president airfreight, Americas. Saignat is based in Calgary, and will report directly to Alexandre Yamada, vice-president solutions. Saignat has worked in the air transport industry for more than 20 years. Before joining Bolloré Logistics, he was the head of commercial, cargo at WestJet. Before that, he was vice-president for Air France KLM in the US, managing the trans-Atlantic joint venture jointly with Delta Airlines. Saignat earned a master’s degree in engineering and management from the Ecole des Mines de Saint-Etienne.
Seven aviation members have been reappointed to the Transportation Appeal Tribunal of Canada Blaine Beaven (Saskatoon, Saskatch-
ewan); Yves Duguay (Sainte-Marguerite-du-LacMasson, Quebec); Deborah Warren (White Rock, British Columbia); Keith Whalen (Riverview, New Brunswick); and, Andrew Wilson (Ottawa, Ontario) have been reappointed as part-time members for four years. Fazal Bhimji (Delta, British Columbia) and William Cottick (Victoria, British Columbia) have been reappointed as parttime members for three years.
The Women In Trucking Association (WIT) has appointed Jennifer Hedrick as president and CEO. Hedrick has 17 years of association leadership experience and is a accredited by the American Society of Association Executives (ASAE). For five years she led the National Industrial Transportation League (NIT League) focusing on issues across highway, rail and ocean freight transportation. Hedrick began working with WIT in January, and formally took on full leadership responsibilities on March 16. She assumed the role from Ellen Voie who was president and CEO since she founded WIT in 2007.
Anew third-party logistics provider is aiming to disrupt the traditional fulfillment model to meet the unique needs of small- to mediumsized Canadian businesses.
Called Darwynn – a play on the founder’s name Wynn Xie and Charles Darwin, the father of the theory of evolution – the company offers a unique combination of IT and physical assets to serve its customers. It recently opened a new distribution centre in Toronto’s Scarborough suburb, increasing its operational assets to four across the country.
In an interview, the company’s CEO Reza Bafandeh explained the thinking behind the new venture. “Most people underestimate how complex the Canadian market is,” he said.
Bafandeh put it in context by comparing Canada to California. With a land size about 25 times that of the US state, we have about the same population and about half the GDP. “So as a result, you’re dealing with a country that’s exceptionally widespread, and with significantly less invested infrastructure,” he explained. “So, by default, that means companies that start up, especially in the small to medium range, have a lot of operational issues that they’re faced with to be able to compete effectively.”
One of those issues is regionalization of service providers. Bafandeh pointed out that the majority of transport providers and fulfillment providers are provincially based or focused on a single channel, meaning companies have to build a diverse group of suppliers if they want national reach for their products.
For many small businesses, especially those that have risen to quick success using social media marketplaces, this creates a major headache and impediment to growth. These small businesses are left asking how to manage inventory, and how to ensure they’re able to fulfill through multiple channels, Bafandeh said.
Providing a solution to these problems was the genesis for Darwynn. The idea was to create a single portal for companies to be able to access the Canadian market, coast to coast. The company combines market access using physical locations within reach of 80 percent of the population, and an integrated IT platform that provides real-time data and feedback to vendors, as well as managing their fulfillment requirements.
Bafandeh said Darwynn helps eliminate variations in pricing and fulfillment styles, as well as allowing smaller companies to avoid losing margin by spending on a middle-man, like a national distributor, to get their products to customers. “Our goal is to be the world’s most merchant-centric company, where we focus on the needs of the seller, focusing on how they want to operate their business, and building an infrastructure with an adequate amount of configurability, where companies can decide how their inventory is managed,” he explained.
To that end, Darwynn has no minimum limits on the amount of inventory it will hold, and charges only for the space the product takes up. “You can literally hold one case in Vancouver, and you’ll pay the storage for the cubic volume of that one case,” Bafandeh said.
It manages smaller inventory through a propriety inhouse designed AS/RS system, while larger items and pallet or case lots reside in traditional racking.
As well, customers can configure how their inventory is handled, whether on a first-in-first-out basis, or last-infirst-out, or by expiry dates, or by item level SKUs, cases, pallets and so on, or with kitting and other value added services, Bafandeh said.
“Most companies – especially when you’re starting small – you’re picking and choosing your battles,” he said. “’Where do I invest my money? Do I invest it in marketing? Do I invest it in individual operations people? Do I invest it in data analytics?’ And we’ve decided to build this infrastructure where a lot of this becomes hands free.”
Companies using the system have access to all the data about their inventory. They get insight into replenishment data, insight into costing on an order level, and transparency on nuances like expiry, or batch ID. Bafandeh said that a typical small company using third-party suppliers would have to hire two people to get this level of data and be able to use it.
And, in keeping with the micro-enterprise model that so many are using for e-commerce, Darwynn allows companies to onboard themselves through the company’s website portal. Bafandeh espouses customer service that’s so good it doesn’t need to exist, and the Darwynn interface is designed to be simple, seamless and fun.
“Our goal is to make sure that merchants can manage their operation without calling in, having full visibility, full transparency. We’re trying to create it into a system where people, companies, individuals, owners, operational professionals, can tap into a resource where they
Full Name: Company:______________________ Title:___________________
Address:_____________________________________________________________________________
Phone: ______________ Email:__________________________________ (Email Required
YES, I WISH TO RECEIVE INSIDE LOGISTICS MAGAZINE FREE!
YES, I WISH TO RECEIVE INSIDE LOGISTICS E-newsletter FREE!
Choose your Edition: Print Digital Print & Digital
Signature: Date:
PLEASE ANSWER THE FOLLOWING QUESTIONS TO QUALIFY FOR YOUR FREE SUBSCRIPTION:
1. Do you purchase, or influence the purchase, of goods and/or services related to distribution logistics, including warehousing operations (receiving, storage or shipping) or inventory control or materials handling?
Yes
No
2. If Yes, do you have plans to buy any of the following in the foreseeable future? (Check as many as apply)
(A) Forklifts and mobile materials handling equipment
(B) Racking, shelving and storage equipment
(C) Software, eg WMS, TMS, YMS, WES, etc
Third-party logistics services
Transportation services
Real estate, warehouses, existing or new building
(D) Automated materials handling systems (H) Data capture and inventory control equipment
(Z) None of the above TRANSPORTATION SERVICES:
3. What is your company's PRIMARY business?
(Check one only)
NON-MANUFACTURING (Check one only)
Others Allied to the Field (please specify)____________________________________________________________________
4. Which of the following categories best describes your PRIMARY function? (Check one only)
Other (please specify)____________
5. What is the approximate number of employees at this location?
can manage their business the way they want, not the way that it’s forced upon them.”
With facilities in major markets – Vancouver, Calgary, Toronto, and soon in Montreal, ranging from 44,000 to 91,000 square feet – the company claims it is within easy fulfillment distance of the entire Canadian population. With its modular AS/RS system and relatively small footprints, Bafandeh said that scaling up to meet new demand can be quick and seamless. The new, 45,000 square-foot facility in Scarborough will be able to fulfill approximately 10,000 orders per day at full capacity.
Darwynn partners with carriers and last-mile providers, as well as customs brokers to facilitate customers’ cross-border needs. The software algorithms determine which carriers to use based on the parameters of the shipment and the customer’s service level agreement. The company has also begun rolling out its own fleet, with 100 percent electric vehicles.
If it sounds like Darwynn is reinventing the wheel by creating its own platform and hardware, that’s intentional. Bafandeh says the environmental has radically changed, and fulfillment needs to follow.
“When there’s a flood, wheels don’t work any more. You need a boat, right? And that’s the nature of where we are within the e-commerce space,” he said.
Twenty years ago it was bricks and mortar retail, and mom-andpop shops were the small businesses of the time, he explained. If a manufacturer wanted to make the big time they’d sign with a big retailer like Walmart to reach more buyers.
“Now it’s completely changed. Companies are tapping into a global infrastructure, tapping into platforms that never existed.
New platforms are arising out of nowhere. And for companies to be able to compete effectively, they need to maintain that adaptability,” Bafandeh said.
That takes us back to the name. Darwin talked about the survival of those that adapt the best, Bafandeh added. “We understand that with this technology, with this software, with this infrastructure, even though we have it, we understand we are at just the cusp of what operational fluidity and operational perfection is. We know that the business model is going to change, and we need to make sure that adaptability is the core component of our entire culture.”
The manufacturing and supply chain community came together in a big way after a four-year hiatus for a record-setting ProMat event, according to show producer MHI.
With an overall registration count of 50,924 and 1,051 exhibitors, the event attracted 12 percent more attendees than the last Promat in 2019, before the pandemic. The event also saw a rebound in international attendance with attendees representing 178 countries.
“MHI is committed to bringing this industry together to share leading-edge trends, technology, and innovations. The success of ProMat 2023 is proof of that and the supply chain industry’s continued relevance to the marketplace and central role in commerce,” said John Paxton, CEO of MHI.
“No other event showcases all this industry has to offer to improve operational productivity and efficiency across manufacturing and supply chains. With so much tech and end-to-end solutions, ProMat offers this industry a one-stop-shop for solutions and the unparalleled education attendees need to survive and even thrive in a constantly changing marketplace.”
“The energy on the show floor and the connections being made is a clear sign of the power of this industry,” added Daniel McKinnon, EVP of exhibitions at MHI. “Attendees representing the Fortune 500, the top 100 retailers and consumer goods firms brought large teams to ProMat to source the latest technologies and to learn
leading trends impacting supply chains. They came to ProMat with plans in hand and budgets in place to improve their operations and build resilient supply chain operations for future success.”
The dominant trend at ProMat was a focus on digital supply chain solutions including automation, robotics, artificial intelligence, autonomous vehicles, augmented reality, the Internet of Things, and end-to-end data transparency. A major focus at the show was on the technologies that let these solutions communicate with existing material handling solutions.
“We’re seeing a big acceleration in the adoption of these technologies over the next five years in manufacturing and supply chain operations,” said Paxton. “The solutions on display this year were evidence of this trend.”
MHI announced the winners of the 2023 MHI Innovation Awards at the show. A panel of judges chose three winners.
Agility Robotics won the best new product award for Digit, its human-centric, multi-purpose robot. The robot walks like a human, with arms, legs and torso, but no head. It weighs in a 65 kg and can carry up to 16 kg. It’s able to walk forwards, backward and side to side, as well as turning in place and crouching. It can walk up slopes and over uneven terrain. Agility demonstrated it picking totes from a rack and placing them on a conveyor at its booth. It qualifies as a collaborative
“THEY CAME TO PROMAT WITH PLANS IN HAND AND BUDGETS IN PLACE .”
robot as it is programmed to avoid contact with humans. The company says future versions of the robot will be able to unload trailers, and eventually automate last-mile deliveries.
The best IT innovation award went to EPIQ Structural Solutions, an engineering firm, for its OneRack web-based storage rack design software. It gives rack professionals the ability to create their own rack designs, answer their customers’ questions, utilize their inventory, and solve problems. OneRack’s structural engineers can stamp and approve drawings created using the system.
Hai Robotics took the best innovation of an existing product award for its autonomous goods-to-person picking robot, A42T. It can
autonomously pick from racking up to 10m tall. It can handle most totes sizes and types, even cardboard boxes, on standard industry shelving structures.
MHI startup award
sSy.ai was the winner of the 2023 MHI startup award. This award was chosen by ProMat attendees during the first three days of the event. sSy.ai uses AI and machine learning to transform standard cameras into sensors. Besides object recognition, this technology allows the extraction of data such as indoor tracking, distance or speed of any asset or object in the warehouse.
Yale lift trucks made a big announcement at the show, changing its branding to Yale Lift Truck Technologies.
“Warehouses face a tough outlook, with persistent labour challenges threatening productivity and risking safety incidents. But when operations look to suppliers for help, they’re met with complacency and rigid terms based on what’s best for the factory – not the needs of modern warehouses,” said David Furman, president, marketing, strategy and business development, Yale. “We think it’s time warehouse operations rethink what they expect from lift trucks, technology and suppliers. That’s why we’ve invested in a more creative approach built around the customer, engineering lift trucks as smart technology foundations and bringing innovations to market, faster.”
The company also announced broader availability of its safety technology, Yale Reliant. The company has added the proximity and stability technology to 13 models. Electric counterbalanced trucks in the 3,000-12,000-pound capacity ranges, and the company’s very narrow aisle (VNA) turret truck and enclosed end rider join the five other core warehouse models available with the operator assistance technology, which first launched in 2021 and won recognition as a product of the year. The company demonstrated the stability and pedestrian detection functions in a dedicated booth at the show.
Otto Motors unveiled its newest autonomous mobile robot (AMR), Otto 600, a “Goldilocks platform” fitting in the middle of its range according to Dave Northup, the company’s director of product management, who demonstrated it at the show. The Otto 600 can move pallets, carts and other payloads up to 600 kg. The company has also updated its operating software so that it conforms to AGV standard VDA5050, which allows for interoperability with other brands of AMR. Otto Motors is the first AMR vendor to support the standard, letting customers manage dissimilar types of material handling solutions from a third-party master controller interface.
In the category of nimble and adaptable, Tompkins Robotics showed off several of its new order fulfillment solutions at the show. The PickPal product series currently includes two pick assist (PA) autonomous mobile robots. The standard PickPal can carry 60 kg of orders, while the PickPal+ handles up to 100 kg. It is the company’s first foray into the goods to person market, according to Mike Futch, Tomkins Robotics president and CEO. Futch said at the show that it is designed for third-party logistics operations that want a low capital expenditure and don’t have the volume to need a fixed order fulfillment solution. The company is offering it on a robot-as-a-service (RaaS) model to keep outlay low.
Dutch Toyota subsidiary Vanderlande showed off its second-generation order fulfillment system, Fastpick, with a fully operational goods-to-picker (GtP) 2.0 modular workstation integrated with a RightHand Robotics piece-picking robot. According to Jake Heldenberg, the company’s head of solutions design, warehousing, North America, the system is faster, and can be customized with different grippers designed for the type of product being picked. He said the three-finger configuration they showed is extremely versatile and can handle soft items like textiles in bags as well as more regularly shaped items. He also pointed out that robot can now use its digits to reposition an item in a tote in order to be able to grasp it correctly.
As part of its 25th anniversary celebrations, Irish forktruck manufacturer Combilift brought the 75,000th truck it has built to Chicago, and donated it to charity. At a special event during the show week, Combilift CEO Martin McVicar presented the Aisle Master articulated forklift to Convoy of Hope, a non-profit humanitarian and disaster relief organization. The organization’s expansion has seen a corresponding increase in the requirement for warehousing capacity to accommodate the supplies that are stored and ready for delivery to areas in need. This will be the not-for-profit’s fifth Combilift truck.
“We are so grateful that Combilift and Martin and the whole team have actually given us one of these trucks for our operations. This is going to help people for years – and ensure that every day someone in the world will receive aid – and that brings hope,” said Erick Meier, senior vice-president – supply chain at Convoy of Hope.
• Plan and execute the delivery of goods by air, sea and land transport.
• Deliver on any logistics challenge, with a creative, agile and networked approach.
• Meet industry standards on education to handle complex freight.
Scan and find a freight forwarder to help you with your next important shipment.
CIFFA members are the professionals who arrange for and move goods around the world. Let us help you choose a global logistics provider for your international business.
IS
“CIFFA’s 300 plus member firms help Canadians do business with the world.”Combilift CEO Martin McVicar (seated) and Geroid O’Hare, the company regional representative in Canada, show off the forktruck that the company donated to Convoy of Hope. image: Emily Atkins photo
Seegrid demonstrated how its Palion Lift and Palion Tow Tractor now work in combination to load and unload carts with no human intervention. The Palion Lift autonomously transports up to 1,590 kg and retrieves or places palletized goods at heights of up to two metres. The Palion Tow Tractor autonomously tugs cart trains and other payloads up to 4,545 kg. Palion Lift can now work directly with Palion Tow Tractor to load and unload carts, which has previously been a time-consuming and labour-intensive workflow.
“Expectations and supply chain pressures continue to become more demanding and complex, requiring more integrated material handling solutions,” said chief sales officer David Griffin. “Not only does this automation mean improved safety, reliability, and throughput, but through coordinated movements between Seegrid Palion AMRs, the business case for our customers gets even stronger.”
Do you know what Canadian industry associations are doing to improve business conditions in 2023? Here’s a primer on what some of the major industry groups are tackling this year.
Mandate
CIFFA was founded in 1948 and represents some 300 member firms from the largest global multi-national freight forwarding companies, freight brokerage businesses and drayage firms to small and medium sized Canadian companies. It advocates for these members, and provides shippers with a list of freight forwarding companies that operate according to Standard Trading Conditions and abide by a strict code of business ethics.
The most significant challenges facing our sector are a lack of infrastructure to serve the needs of Canada’s supply chain in terms of fluidity, reliability and resiliency, and the resulting costs arising from backlogs, disruptions and bureaucratic delays. The supply chain sector also faces challenges in terms of available data and transparency, as the sector remains siloed. CIFFA
continues to work on collaborative relationships with our association partners and supply chain stakeholders, bringing all players together for important conversations where local issues can be discussed and resolved, even while global factors cannot always be controlled.
Our top priorities in 2023 are to continue to escalate member concerns around rising costs and competition concerns due to detention and demurrage charges. We will continue to raise the profile of CIFFA at all levels of government and will continue to lobby on existing regulatory and competition policies as well as on emerging issues as they arise. We will push for the go-ahead on infrastructure projects that are bogged down in approvals processes. We have commenced a strong outreach program across Canada, going out to existing members and member prospects to talk about what CIFFA is doing on the advocacy front, what education, training and certification we offer, and what benefits and opportunities CIFFA members can enjoy. We will continue our strong tradition of relationship-building, being proactive and not reactive, and keeping abreast of work being advanced domestically and internationally through various committees, on matters involving
air cargo, marine cargo, rail, trucking, customs and trade. And of course, as 2023 is our 75th anniversary, we will be celebrating that milestone at regional gala dinners and golf events.
We are proud of the work we have done to raise CIFFA’s profile and member issues before the federal Supply Chain Task Force in response to the Task Force Final Report. We are also pleased to have appeared twice before the House of Commons of Canada’s Standing Committee on Transport, Infrastructure and Communities, both in view of its study on Anticipated Labour Shortages in the Canadian Transportation Sector and also in view of its study of the State of Canada’s Supply Chain.
We have been meeting with rail, freight forwarder, drayage and customs partners on congestion and clearance issues for containers at the ports and rail containers. CIFFA has been instrumental in putting together these meetings and they’ve been successful because it is an opportunity for our members to have access to the right officials who can hear what the concerns are on the ground. It also pushes officials to be accountable and to develop solutions from an operational perspective that can help our members.
CITT serves the Canadian logistics and transportation sector – both organizations and individuals.
Individuals come to CITT for professional development and to be part of an interactive and connected network of industry professionals. Businesses come to CITT to develop their people, and for a range of HR needs, such as recruitment and retention. CITT also serves organizations interested in creating new business relationships with shippers or carriers. We also serve academic institutions with curriculum, recognition of their programs, and as a bridge to connect their students with industry.
Our mandate is to bring together and support everyone in Canadian logistics for our collective benefit. We help individuals and organizations do the business of logistics better – be it through training, certification, hiring, retention, business development and much more. And we endorse and celebrate organizations and people who demonstrate excellence in our field.
Freight Management Association of Canada (FMA)
John Corey, President
Mandate
FMA primarily serves the shipper community, both nationally and internationally. As the national voice of the shipper, the FMA’s mandate is to represent the freight transport concerns of the buyers of freight transportation to all levels of government in Canada and to UN and other relevant international agencies.
We are addressing four main challenges in 2023. These are: Lack of competition in the rail and ocean container service industries; the need for robust government action
The transportation industry faces many hurdles in the short and long term. But the biggest challenge remains talent. We believe that the right people with the right expertise can solve nearly any problem facing industry today – as well as find new opportunities. But there’s competition for talent from other industries, as well as from within our own, and the common lack of investment in developing and keeping people. With rare exceptions, the only businesses we speak with that don’t have difficulty hiring and retaining people are those that have made talent a top strategic priority.
One of our top priorities is to connect industry. CITT is the nexus for organizations and people involved in logistics and we want to develop formal and informal ways for industry to connect. Particularly, we’ve been growing our collaborations with other industry associations.
We recently enabled anyone in industry to formally become part of our organization as affiliates of CITT. We’re putting a big focus on growing awareness that anyone in and around logistics can join CITT and become part of Canada’s logistics community.
A few years ago, we undertook the important work of developing a competency
to address carrier dominance in the rail and ocean container service markets; the shortage of skilled labour in the freight transportation sector, particularly trucking; and the need for infrastructure investment in rail, ports, inland terminals, roads.
Our priorities this year, in advocating for shippers, are:
❏ Improving intermodal services, primarily by ocean carriers.
❏ Monitoring rail service in Canada and the U.S. to flag problems of equipment supply, on-time service, rail safety, adequate experienced staffing, and infrastructure investment.
❏ Encouraging action by the government in response to the Supply Chain Task Force final report.
❏ Working on a global basis on the problem of transportation of invasive species in and on containers with governments, ocean carrier industry and UN agencies,
profile of the logistics professional. We built it in close collaboration with industry and experts from across sectors. As the competency profile is a cornerstone of our learning offerings and the CCLP designation, it’s crucial that we audit the competencies and update them frequently.
As I mentioned, talent and people is one of, if not the most important challenge facing our industry today. To help organizations tackle this, we’re collaborating directly with HR departments. Be it working to build an employee value proposition, hiring, training and beyond, we’re putting a major focus on helping HR build and keep talent.
CITT has made big strides in opening up and becoming an organization that anyone in and involved in logistics can be a part of. Starting with the faster challenge exam to the CCLP designation, and now with anyone able to become part of CITT as an affiliate, we’re now truly an association for the whole industry.
Another win is our corporate endorsement programs – Endorsed Logistics Employer, and Endorsed Business Partner. We endorse and partner with organizations in need of talent solutions, and those looking to form new business relationships. We’ve already formally endorsed and partners across industry, and we’re looking forward to many more collaborations in the years to come.
to ensure actions will mitigate the invasive species problem while not causing significant delays and additional costs.
❏ Monitoring major transportation labour agreements and keep the shipper community informed of potential work stoppages.
Along with other shipper associations, the FMA made a submission to the Canadian Competition Bureau to bring attention to the anti-competitive behaviour of ocean carriers who serve Canadian customers. During Covid, there were serious service issues or no service at all and very high rates. The FMA continues to ask Transport Canada to repeal the Shipping Conference Exemption Act (SCEA), the act that allows ocean carriers to reduce competition. The FMA is an active member of the Global Shipper Forum, and is working to develop a strategy to reduce the movement of invasive species in and on ocean containers.
The Railway Association of Canada (RAC) represents approximately 60 member railways and another 60-plus associate members. The R AC advocates on behalf of its members and associate members to ensure that Canada’s rail sector remains globally competitive, sustainable and safe.
We ensure government decision-makers at all levels have the facts they need to develop and implement evidence-based policies and regulations. Canadian railways are among the most regulated entities in Canada. On behalf of its members, the RAC works to ensure that any additional regulations do not have negative consequences nor undermine private-sector investments.
The RAC plays an important education and awareness role by providing hands-on training courses and hosting regular events to keep government officials, first responders, and communities informed and at the forefront of our ever-evolving industry.
The federal government is considering imposing additional regulations on Canadian railways. Extending regulated interswitching and the banning of replacement workers in the case of work stoppages, contrary to all available evidence, would only serve to make our supply chains less efficient and less resilient, and hurt performance.
We have shared several suggestions with the federal government to in fact improve supply chains’ efficiency and capacity, and we remain open to all good, fact-based ideas to improve how all supply chain links work together to move Canada forward.
We need more innovation, accountability, and data-sharing from all supply chain players, especially at operational levels. This includes more rigourous scrutiny of not just railways, but of trucking firms, warehouses, storage facilities, rail customers, port terminals, and others.
In 2023, the RAC is focused on:
1. Ensuring any new economic regulations imposed on Canadian railways actually improve supply chains.
2 . Providing fact-based arguments to counter a proposed ban on the use of
railway work stoppages.
3. Working with member railways and the communities they serve to further improve upon Canada’s enviable rail safety record.
4. Advocating for strategic investments in safety, sustainability, and supply chain capacity.
5. Educating decision-makers (at all levels) about important contributions our freight, commuter, intercommunity, and tourism railways make to Canada’s economy and Canadian society.
Our most recent Rail Trends report clearly outlined railways’ economic and environmental contributions, including advancements in safety. A recent independent study done by CPCS confirmed that Canada’s rail freight rates are the lowest of all market-based economies surveyed and among the lowest in the world.
And the RAC has just completed an important analysis of supply chains’ performance over the pandemic that confirms rail has been a reliable link with strong, consistent performance. In fact, rail-led the reduction in total transit times for bringing Canadian grain to world markets.
These are important evidence-based contributions to the vital supply chain conversa-
11%
Canadian rail freight rates have grown more slowly than U.S. rates –43% vs. 72% – over the last 33 years, and at less than half the rate of commodity and general prices over that same period.
Rail freight rates in China and Russia are lower than Canada’s, but both are stateowned, and are not on a level playing field with Canadian railways. India, where the railway is also government owned and operated, and Japan show the highest rates.
New research shows Canada’s average rail freight rate is 11% lower than that of the U.S. and significantly lower than rates in other parts of the world. Canadian rates are significantly lower than those of market-based economies in Europe and Asia – all of them leading trading nations like Canada.
30% -2.8%
In 2021, shippers paid 4.16 U.S. cents per revenue ton-mile on railways in Canada and Western grain shippers paid nearly 30% less than the average rate at just 2.97 U.S. cents per revenue ton-mile.
+1.2%
fuel consumption
Overall, total rail industry fuel consumption was 2.8% below 2020 levels and 5.5% below the 2016-2020 average.
$350 billion efficiency $2.3 billion investment
Canadian freight railways transported half of our country’s exports in 2021, and a total of $350 billion worth of goods.
Freight fuel efficiency improved by 1.2% to 704 revenue ton-miles per gallon – setting another record. Initiatives that contributed to this improvement included investments in locomotive fleet modernization, fuel saving technologies, and low-carbon fuels. Improved operational practices, such as running longer and heavier trains and training employees to optimize fuel efficiency, also contributed to greater fuel efficiency.
In 2021, railways invested $2.3 billion into their Canadian assets, bringing the total to $20.9 billion over the past 10 years. RAC members also contributed over $1.9 billion in various taxes to Canadian governments, bringing the total to $16.9 billion over the past decade.
We’ve known for a long time that Canada’s freight railways are the safest in North America. They are also the most cost effective on the continent and have among the lowest rates in the world.”– Marc Brazeau, president and CEO of RAC.
The buzz around electric cars has been going for quite some time, but now the focus has shifted to electric trucks. The idea of being free from the pump and doing something positive for the environment is certainly appealing. However, this aspiration is yet to become a full-blown reality.
The Biden administration in the US aims to make all new commercial trucks electric by 2040. While it may seem like a laudable goal, there are significant challenges to overcome. The technology required to make electric trucks at this scale is still in its early stages, and perhaps most importantly, the country lacks the infrastructure and power grid to support it.
One of the significant hurdles on the path to electric trucks is the lack of a charging infrastructure. We do not have the electrical infrastructure in place to handle the infusion of thousands of battery-powered trucks. Electric trucks require a massive amount of power to charge, and the grid is not equipped to handle that demand. The country’s power grid needs to be updated to handle what is currently in play. And, even if the power grid were upgraded, the cost would be enormous – definitely in the billions, if not trillions. Furthermore, the time it takes to charge an electric truck battery
is much longer than refueling a traditional truck. Currently, the time it takes to fully charge a car can be measured in hours, while the time to fill a fuel tank is measured in minutes. We do not have an extensive enough charging infrastructure, and what exists often is not efficient enough to meet the needs of time-sensitive travelers.
Another significant challenge is the size and weight of the batteries required to power an electric truck. The amount of goods transported across the country by trucks is only increasing, but the size of an electric truck battery severely limits the amount of space available for transporting goods. The heavier the battery, the less cargo it can carry, and that will impact the supply chain as well. It would stand to reason then, that to move the current amount of freight we would require even more trucks on the road.
Electric trucking is then met with two issues already very present in the industry – a shortage of drivers and truck parking spaces. If electric trucks carry less cargo, then more trucks are needed on the roads to efficiently transport goods. With more trucks, comes the need for even more truck parking spaces. Currently, truck drivers spend an average 56 minutes a day looking for parking, which significantly cuts into their driving time and causes delays in the supply
chain. There is no telling how long truckers would spend looking for spaces if the industry went fully electric.
While there are ongoing efforts to improve the technology of electric trucks, significant breakthroughs are yet to be made. The development of new battery technologies that are lighter and more powerful is still in the experimental stage, and the timeline for a viable solution is uncertain. But it would be foolish to bet against innovation; we might see a breakthrough in battery technology at any time.
Our skepticism about the administration’s ambitious policy goal should not be seen as opposition to cleaner energy. We recognize that the trucking industry faces challenges in reducing its environmental impact. The demand for freight transportation is increasing, which means that there are more trucks on the road than ever before. The industry has taken – and continues to take – several steps to decrease its impact on the environment.
When the Environmental Protection Agency (EPA) implemented regulations to reduce emissions from diesel engines in heavy-duty trucks, the industry stepped up and embraced those regulations. They have resulted in cleaner-burning engines and reduced emissions. The trucking industry has made progress in improving fuel
efficiency. Newer trucks are equipped with more efficient engines, and technologies such as aerodynamic designs and low rolling resistance tires have been adopted to improve fuel economy.
The industry has also been exploring alternative fuels such as natural gas, biodiesel, and electric power. These fuels emit fewer greenhouse gases than diesel and can help to reduce the carbon footprint of the industry.
The trucking industry has also adopted eco-driving practices that utilize new technologies such as GPS, telematics, and automated transmissions to improve efficiency and reduce emissions.
Overall, there are several ways the trucking industry can and does help the environment, from implementing fuel-efficient technologies to adopting alternative fuels and improving logistics and route planning. While electric trucks may not be a viable option yet, there are many other things that can be done to reduce emissions and improve sustainability.
The idea of electric trucks is still more of an aspiration than a reality. While the Biden Administration’s goal is admirable, it remains to be seen if it is achievable. However, with ongoing research and development, it is possible that electric trucks will become a reality in the future and when that happens, the trucking industry will be ready to embrace those standards.
The final mile, or last mile, of a delivery refers to the transportation of goods from the transportation hub to the final destination. If you speak to anyone who is familiar with the delivery ecosystem, they will tell you that this final mile is the most difficult.
It is also, however, the easiest to electrify. Those commercial vehicles responsible for the middle mile – delivery from the depot to the stores – are large and must travel long distances. They require very heavy, expensive batteries and range anxiety becomes more of an issue for long haul journeys. In comparison, smaller vans are easier to electrify.
While there might be disagreement on the net contribution of e-commerce to our carbon footprint, there is less disagreement about the benefits of delivery companies electrifying their fleets. In the US, for example, transportation is responsible for over 25 percent of greenhouse gas emissions, more than any other sector.
Some have argued that even if electric vehicles have no tailpipe emissions, the electricity used to charge them would still leave a substantial carbon footprint, thereby making the switch to EVs pointless without first de-carbonizing the grid. Recent academic research has debunked this argument, showing that in 95 percent of the world, electric vehicles produce less CO2 emissions than fossil fuel powered cars. The small exceptions are in countries which rely heavily on coal to produce electricity.
Governments around the world are incentivizing businesses to switch to electric fleets. For example, in the UK, electric vehicles are eligible for a 100 percent discount on charges in the London congestion zone. A vehicle entering the zone five days a week for 50 days a
year would therefore save $4,400.
Electric vehicles also allow businesses to save money on maintenance and fuel costs. Until recently, these lower maintenance costs compensate for higher purchase prices. However, the cost of the vehicles themselves is constantly coming down. And, as more companies make the switch to electric, economies of scale and improvements in battery technology will drive the costs down even more.
Even when the environmental and business case for electric vehicles is strong, things are not always so simple in practice. That’s what Amazon found out when it first sought to electrify its fleets.
The company had begun by assuming that it simply needed to find a model already on the market that matched its requirements. What it found instead was that the existing vehicles did not meet is specific requirements or those that did were not produced on a large enough scale. The company therefore entered into a partnership with Rivian to help design its own vehicles and play a role in scaling up the market. Amazon ordered 100,000 vans from Rivian – the largest single purchase of electric trucks in history.
T he Amazon-Rivian partnership highlights the importance of design flexibility. Both vehicle manufacturers and their parts suppliers need to be able to adapt to the specific requirements of different delivery ecosystems. Many companies will trial a dozen or more alternative fuelled vehicles on a small scale before s witching permanently from diesel engines, so the ability to offer customizable designs and bespoke parts will help accelerate t he electrification transformation.
Today, 41 percent of consumers expect their online purchases to arrive in less than 24 hours. As projections for delivery times gradually shorten, and international trade increases in popularity, manufacturers and distributors are adjusting their cross-border logistics strategies to ensure that timely delivery is a top priority. Concurrently, systemic supply chain disruptions, lack of proper infrastructure, and regulatory obstacles all contribute to the complexity of managing cross-border freight transportation.
In order to move goods efficiently, remain agile through unforeseen circumstances, and maintain strong relationships with customers across borders, businesses are turning to experienced third party logistics (3PL) providers for help. A 3PL services provider will help shippers deliver consistent and predictable performances by providing the framework and resources for a successful cross border logistics operation.
Here are three ways partnering with a 3PL provider can optimize cross-border distribution:
Given the constant flow of trade across borders, avoiding traffic congestion can be a considerable challenge without the insight of a seasoned multimodal cross-border logistics expert. Taking a data-centric approach, 3PL partners can combat these issues by identifying and scheduling the right service across a variety of modes. By reviewing historic distribution and performance data, the business can begin to unveil pain points, gain a clear understanding of their needs and limitations, and implement process improvements.
E-commerce sales accounted for 22 percent of total global sales in 2022. As a result, e-commerce retailers with a high frequency of small order volumes must utilize less-than-truckload (LTL) consolidation to navigate the challenge of delivering pallets, half pallets, or parcels in a short window of time. To do so, businesses need access to a large network of consolidation points, including cross-docking, transloading, and short- or long term warehousing.
Additionally, though over-the-road transportation is most common for cross-border shipments, relying on a single route solution does not provide supply chain flexibility and agility. To keep goods flowing through unexpected downtime, 3PL providers who also offer international shipping services can factor in intermodal and ocean solutions as cost- and time-efficient alternatives.
Although labour is cheaper in other parts of the world than Mexico and Canada, global supply chain shortages have proven the importance of staying close to end customers. Subsequently, many businesses have shifted their manufacturing locations to Mexico to provide customers with a localized experience along with gaining duty-free
benefits under the United States-Mexico-Canada Agreement (USMCA).
Mexico is currently one of the top trading partners of the US, which is why it’s important to have connections and clear communication with a variety of port locations across either side of the border. An established 3PL services provider can connect businesses with brokerages, warehouses, consolidation points, and deconsolidation points all across the US, Mexico, and Canada.
Laredo, Texas, for example, is home to the busiest port between the US and Mexico. More than half of all US-Mexico trade passes through this point of entry, so having a skilled bilingual staff to communicate quickly and effectively is crucial for time sensitive, high pressure logistics situations.
Maintaining real-time shipping status enables actionable insight and a smooth delivery process. However, shipment traceability tends to decline once cargo crosses the border, which can lead drivers into very dangerous situations. In the first half of 2022, robberies and hijacking accounted for 87.2 percent of cargo lost to theft in Mexico.
Experienced 3PL partners prioritize keeping a network of Customs Trade Partnership Against Terrorism (CTPAT) certified carriers. These carriers are trained to strengthen the supply chain, improve border security, and mitigate risks by identifying security gaps, implementing best practices and measures, and addressing challenges through action plans. In addition to alleviating the vulnerability of driving through unknown territory, CTPAT drivers benefit from reduced Customs and Border Protections (CBP) exams, access to Free and Secure Trade (FAST) lanes, shorter wait times at the border, and more.
The landscape of Mexican freight transportation is evolving, and industry leaders are working towards cross-border logistics technology that will provide the 360 view businesses desire. Until then, it’s important to keep the flow of goods and services moving by connecting with trained carriers who can address a broad range of security risks and avoid cross border logistics disruptions.
Having an efficient cross-border strategy in place is key to ongoing transportation success. Today, establishing a global footprint is not only favored by business owners with expansion in mind, but necessary to remain competitive through the future of unlimited market options.
Navigating the complexities of the supply chain, managing unforeseen circumstances, and delivering the expedited shipping experience consumers crave calls for an experienced 3PL provider. By leveraging the knowledge and resources 3PL partners offer, businesses ensure they are selecting the right carriers and services, maintaining realtime insight, and keeping cargo safe and secure.
IT’S BEEN OVER a year since Russian tanks invaded their neighbour, Ukraine, on February 24th 2022. The invasion was completely unjustifiable. There was no provocation or aggression by Ukraine against Russia of any sort.
This war is total madness, and to attempt to understand it requires some historical perspective. The collapse of the Soviet Union in 1991 started a movement of liberation and democratization on the West side, with the Estonia, Latvia and Lituania, Poland, Romania, Czechia, Slovakia and Hungary becoming democratic countries and eventually joining the European Union and NATO.
On the East side, the former Soviet republics of Azerbaijan, Kazakhstan, Kyrgyzstan, Uzbekistan, etc. also became independent, but stayed in the Russian sphere of influence, and remained despotic regimes.
Ukraine stayed in between until the Maidan revolution of 2013, which led to a pluralistic political system, with protection of basic human rights and liberties. In short, Ukraine became a democracy, very much like Canada, in contrast with the authoritarian regime in Russia. The invasion of Ukraine is nothing less than a Russian attempt to re-create the Soviet Union, a sort of colonization of its former republics.
A world divided Western countries did well to support Ukraine and to impose sanctions on Russia. Referring to Western sanctions is actually the wrong word. We should call them democratic sanctions instead, since democratic countries in the East, like Japan and Singapore support them fully.
We now have a world split in two, with democratic countries around the world fully supporting Ukraine, and authoritarian regimes like China, most African, Middle Eastern and South East Asian countries supporting Russia, directly or indirectly. Brazil supported Russia under its former president Jair Bolsonaro. However, under its new president, Luiz Inácio Lula da Silva, who took office in January 2023, it voted with democratic countries at the last United Nations vote in February.
India is an oddity. In principle, it’s a democratic country, but it supports Russia. Their
bilateral trade is booming, with Indian imports from Russia having quintupled in a year. For example, India imports huge quantities of Russian crude oil, some of which is re-exported after being refined into diesel, gasoline or jet fuel.
The costs of the war are staggering in human losses (although we lack precise figures), destruction and human misery in Ukraine. But the whole world is affected, with higher energy costs, disruptions in commodities and shortages affecting many industries. The ongoing war and its consequences are the main factor driving inflation, destabilizing post-pandemic economic recovery.
Also, its effect on the availability and price of food is much worse in developing countries. In Ukraine itself, according to UN estimates, at least 12 million people have fled their homes, with more than eight million (representing about 20 percent of the population) having fled to neighbouring countries, Czechia, Germany, Poland, Romania, and Slovakia. Compounding matters, there was a steep reduction in the Ukrainian grain harvest last year and this year’s crop could be down by another 15 percent.
Why does this matter to us? It’s not simply a matter of principles like peaceful relations
between countries, fairness and basic freedoms for all.
Because Canada is a trading nation and international trade accounts for over 60 percent of our gross domestic product. We therefore depend on a stable, rules-based international system to prosper.
The ongoing Russian invasion and its direct or indirect support from many countries, actually breaks world order. There were good examples of that early on. Russia literally stole over 400 passenger planes which were owned by western leasing companies, by passing a law to confiscate them and switch them to Russian registry. Russia also passed a law forbidding Russian companies to make royalty payments to Western countries.
So, just imagine a Canadian company leasing equipment to a foreign customer or entering into a licencing agreement with a foreign company, which could become worthless at the whim of that country’s despotic ruler. That’s not the kind of global business world we want to live in. That was confirmed by our finance minister, who when visiting Washington a few months ago, spoke about the importance of friend-shoring.
As we continue to hear the sad news from Ukraine, the continuous bombing of civilians and civilian infrastructure, let’s not become indifferent. Or worse, let’s not indirectly side with Russia, like former US president Donald Trump, who recently said the Russian invasion of Ukraine was just a “territorial dispute” and does not threaten our vital interests.
It’s actually the opposite, and the International Criminal Court in The Hague has recognized this, by issuing an arrest warrant for war crimes against Vladimir Putin on March 19, 2023. It may not be enforceable easily, but it has a huge symbolic value, and 123 countries can apply it.
We must foster trade with countries that support democracy and the rule of law, and avoid granting favourable trade terms to those countries that don’t. Canada must continue to work with its allies to provide Ukraine with maximum support. It’s in our interest.
Workers and managers have differing views on workplace safety, and that’s a problem
A NEW STUDY FROM Toronto Metropolitan University and Workplace Safety & Prevention Services has found significant differences between workers and managers when it comes to their attitudes, beliefs and perceptions of health and safety in the workplace.
Differences like these can lead to misunderstandings, conflict, increased risk, and poorer safety performance, says the study. It sets out a roadmap that workplaces, including those in warehousing and distribution, can follow to reconcile the different views of managers and workers, with the goal of reducing injuries.
Key differences
Surveys filled out by 2,401 workers and 1,562 managers/supervisors gauged their perceptions of health and safety, their beliefs and attitudes, and their top occupational health and safety concerns.
A larger number of workers felt the workplace ‘a bit unsafe.’ Although this may be because workers often face more hazards than managers do, employers should consider opportunities to improve employees’ perception of safety. For example, ask employees via an anonymous survey what they think the top three hazards are, and what could improve safety. Review and implement some of the great ideas presented.
The vast majority of workers and managers could not identify the ‘employer’ as the party primarily responsible for health and safety in the workplace. This may reveal a lack of understanding or interpretation of the internal responsibility system.
In addition to providing training to clarify roles, employers should tangibly demonstrate their responsibilities by participating in safety communications and training; following all safety procedures; participating in workplace inspections; and providing adequate
resources for implementing safety suggestions in a timely way.
More workers felt that health and safety training was insufficient and inadequate. The foundation of safety training is a well-documented hazard assessment. Is a training matrix completed on an annual basis, considering the safety training needs of every position? This includes safe lifting for manual material handlers, to operation of power walkies, as well as training on correct pallet placement on steel storage racks to name a few. Does safety training include visual demonstrations and practice sessions, which make it much more effective?
Workers were less confident about health and safety measures in the workplace. This included the frequency of safety communications in the workplace. Short safety messages on a regular basis stick better than one lengthy training program once per year. It also included the frequency with which they were asked about their safety concerns. This is a huge missed opportunity. Your workers know what is working and what is not. So, get their valuable input.
The majority of managers and workers agreed that ‘workplace injuries and accidents are an inevitable part of life’. This finding is concerning. Are injuries occurring because productivity is prioritized over performing tasks safely, which encourages unsafe behaviors, such
as operating mobile equipment at high speeds in the warehouse? Or because of inadequate training and supervision? Injuries can be prevented by identifying and controlling the root causes of risk and ensuring work procedures are clearly defined and workers are held accountable.
Workers’ safety performance is greatly influenced by their relationship with their managers, including a reduction in injury rates when their managers showed greater concern for them and supported the workers’ positive safety behaviors. Bridging gaps in perceptions, attitudes, and belief is critical to improving performance. The study recommends employers take four steps.
First, provide more education and training. Health and safety training leads to improvements in knowledge, safe behaviors and health and safety outcomes, says the study.
Second, be proactive about health and safety concerns. Don’t wait for an incident to happen before adequate controls are put in place.
Third, improve your safety culture. Workers will quickly determine if what is said in training is happening on the warehouse floor. There shouldn’t be a disconnect, and if there is, this is a management issue. Improvements to safety culture can be made by many seemingly small things, such as having a safety budget, providing ongoing equipment maintenance, sending the message that safety always trumps speed, effective inspections, quick reporting and correction, good housekeeping, to name a few.
Fourth, improve communication on health and safety issues. Constant and effective communication will ensure both managers and workers are singing from same song sheet.
With exceptional LTL and transportation services
Asset-based, award-winning Canadian LTL carrier
Delivering to & from all points USA and Canada
Canada and USA customs bonded carrier
LTL, TL, & global 3PL
Warehousing & distribution within Canada
Industry-leading transit times & on-time delivery
Expedited next day service between USA & Canada
Online ordering, rating, transit times & real-time tracking
Cutting-edge technology including AI, robotics, distributed ledger & smart contract process
Intelligent customs document processing for efficient cross border shipping to Canada & USA
Technology company providing intelligent automation software