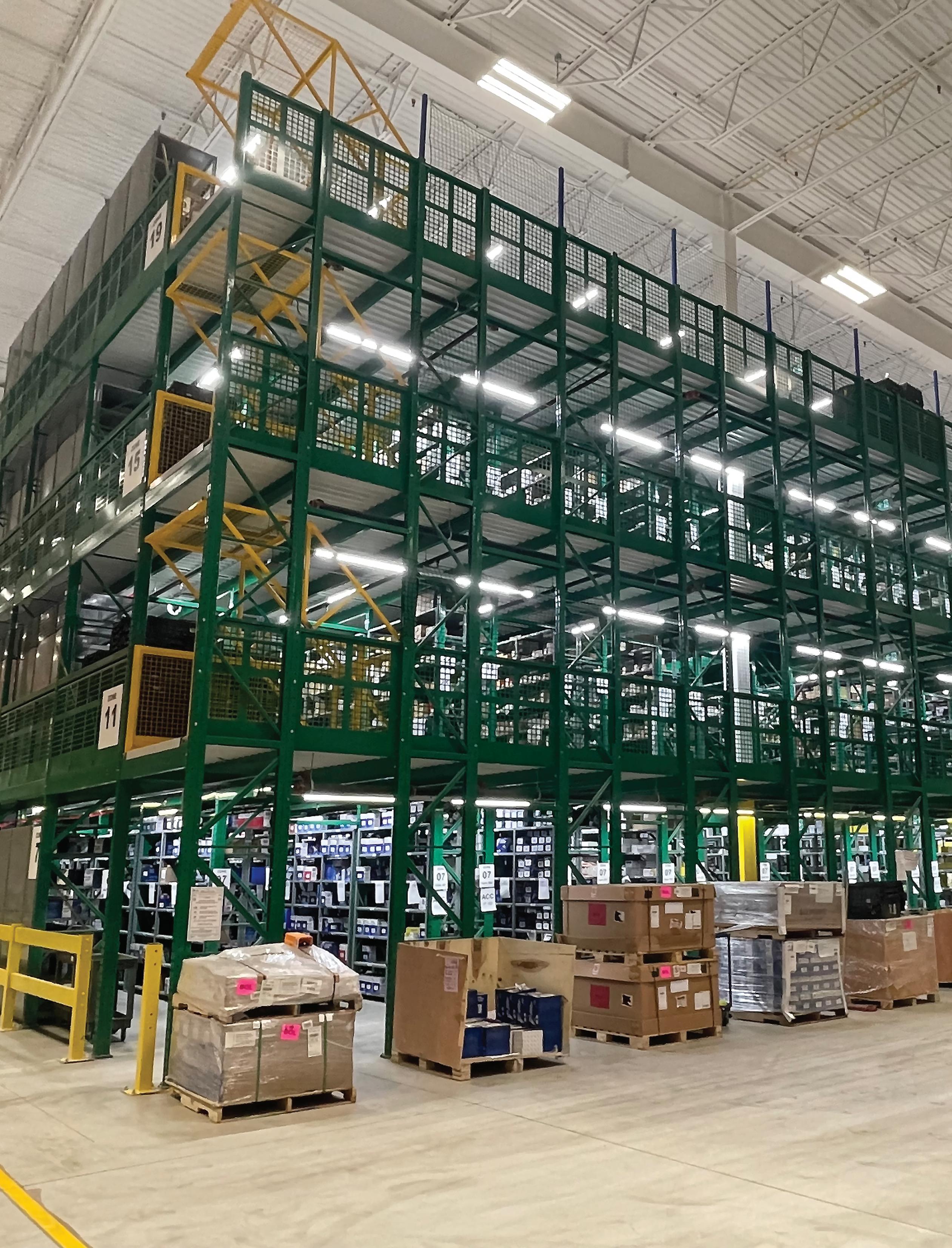
5 minute read
PARTNERS IN PARTS
What happens when you bring distribution operations under one roof for two major players in an industry?
For Advance Auto Parts, which has merged the DCs of its Worldpac and Carquest brands, the results are savings in space and time, along with improved productivity. The two companies are sharing a newly opened distribution centre in Bolton, Ontario. The companies, both vehicle parts distributors, have never collaborated in a DC before, so this is a learning experience for everyone involved.
The 580,000-square-foot greenfield building sits close to Ontario’s Greater Toronto Area (GTA) distribution hub, with easy access to intermodal rail, air and highway transportation. It serves all 112 Carquest retail stores in Ontario and eastern Canada, along with 15 Worldpac locations, and can fill special orders from across the country. These stores and branches serve more than 37,000 professional repair shops and automotive dealerships.
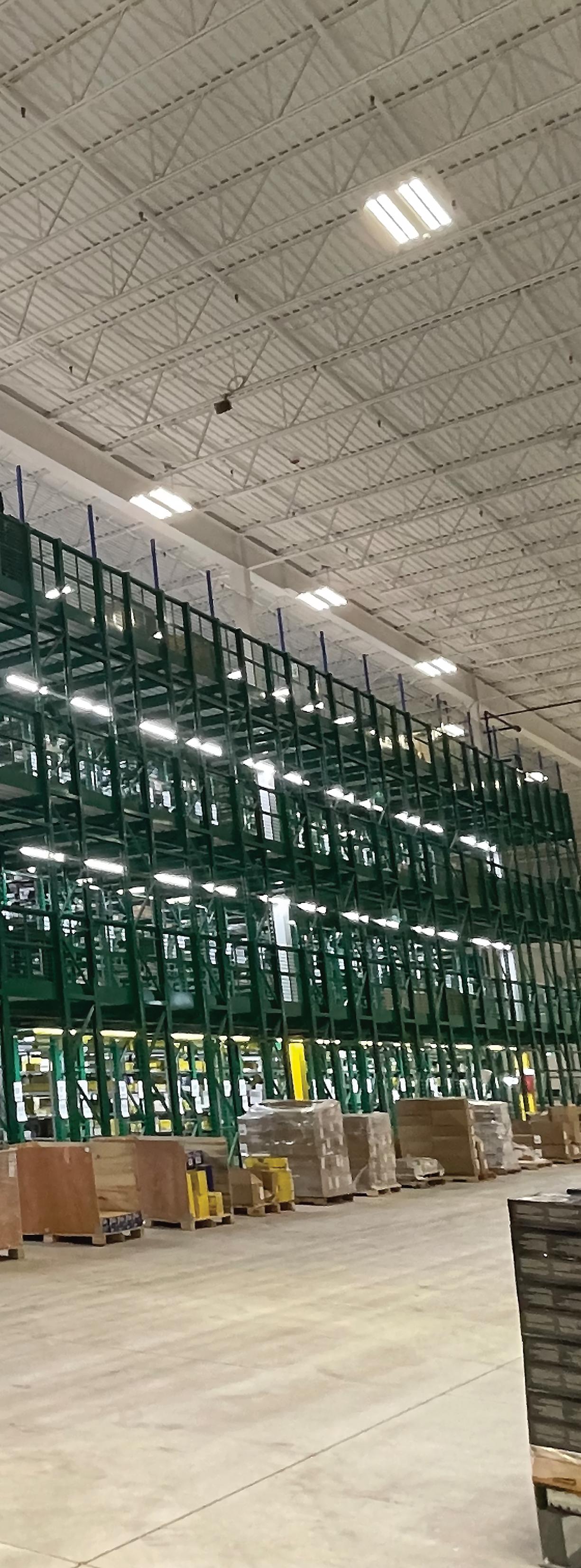
“With more motorists holding onto their vehicles longer, an expanded product offering is required to keep those older vehicles on the road,” said Jason Yurchak, Worldpac senior vice-president, Canadian operations.
“Bringing our Worldpac parts inventory together with Carquest under one roof allows us to carry parts for virtually every type of vehicle on the road today. Our DC team offers nightly replenishment of every Worldpac and Carquest facility with multiple same day deliveries, ensuring customers get the right part at the right time.”
Room for expansion
While it’s been operating since last fall, at the grand opening event on May 6, 2023, the facility was not yet at capacity, a state of affairs that is quite intentional. Advance Auto Parts executive vice-president Bob Cushing said at the event that the facility is currently housing about 150,000 active SKUs, with capacity to hold 350,000.
The room for expansion is part of the company’s growth plans in Canada, according to Cushing. “This is another investment in Canada,” he said. “We have high aspirations, basically to double our business here.”
And while he declined to mention the timeline for that growth, Cushing did mention a new 220,000-square-foot DC that Carquest opened about a year ago in British Columbia. “The market is terrific. Our customers are great. So it’s kind of exciting for us to have both banners in one facility. It’s just beginning, obviously. So we’ll be moving this across Canada, the same way,” he noted.
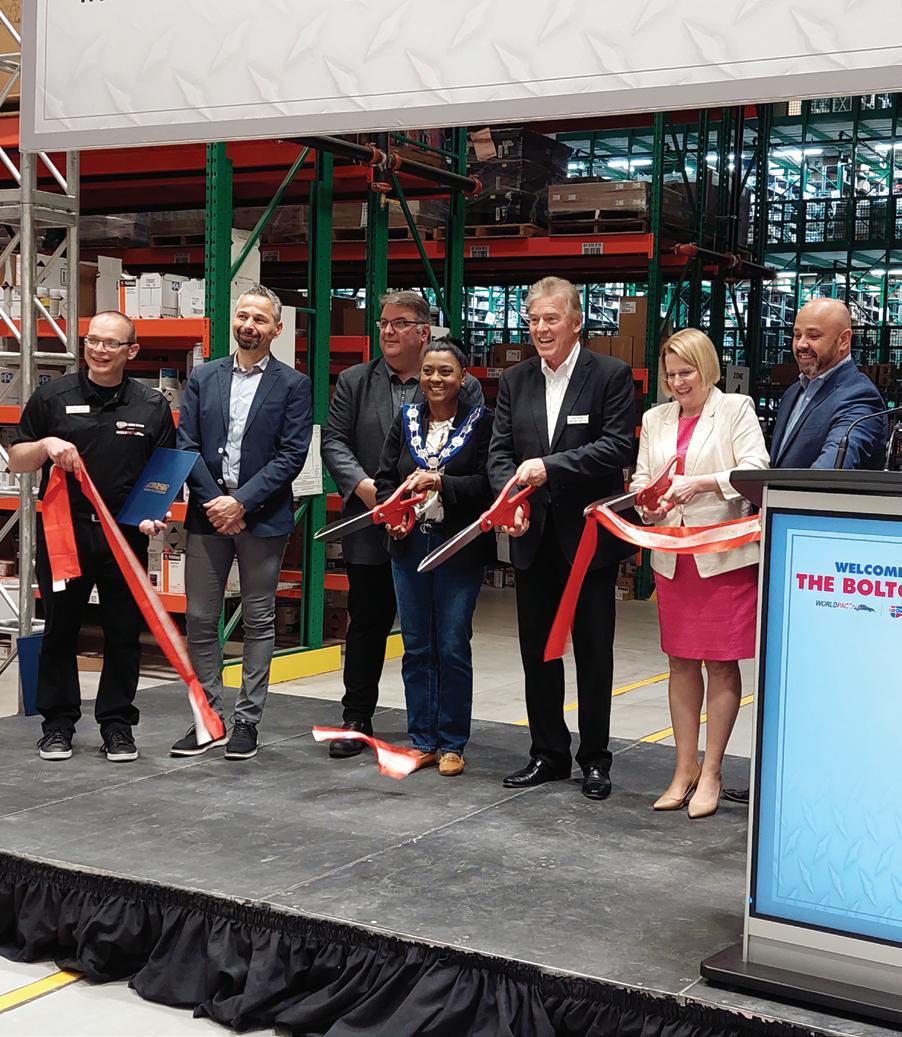
A vision for Canada
Before moving to the consolidated building, Carquest and Worldpac operated two separate DCs, both near Pearson airport. According to Cushing, Carquest had run out of space in its Rexdale facility about five years ago. And Worldpac, in nearby Mississauga, had moved three times into larger facilities.
So three years ago Advance Auto Parts decided to build a master DC and bring the two operations under one roof. “That’s different, right? So every banner was independent,” Cushing said. “Take our hats off and throw them away. Say, ‘Hey, we’re actually Canada and that’s all we care about.’ We don’t want to say it’s CarQuest Canada, it’s not Worldpac Canada, it’s Canada.”
Simplicity first
With that in mind, Lucien Jurca, Carquest Canada’s director of supply chain, set to work designing a facility that would separately house inventory for both operations, while at the same time allowing for combined distribution and replenishment. What he and his team came up with is simple and elegant.
Under 40-foot-clear ceilings high-bay pallet racking from 3D Storage surrounds a four-storey pick tower that houses small parts inventory. Totes are delivered to pickers in the ‘green monster’ as the team affectionately call it, via a spiral conveyor and exit directly to the loading zones via a conveyor on the opposite side.
All picking is done manually, using a new suite of Motorola RF guns and Gladiator scanners. The companies have been using RF since 2009, Jurca said, but the new equipment has speeded processes up considerably.
The DC can handle up to 190,000 lines per week, at the moment, with a target of 400,000 in time. That will be after the companies bring in additional technology, Jurca said. He pointed out some open areas that could be developed with goods-to-person picking automation, something he and the team recently scoped out while visiting the Promat show in Chicago.
But the initial configuration was chosen for a simple reason: cost effectiveness. They started out considering automation like Autostore, and other goods-to-person systems, Jurca explained.
“We started looking at the numbers,” he said. “What can we do to improve efficiency, what we can do to improve the throughput, the speed and all that. And after a couple of months we realized that step number one was, let’s not overcomplicate things. We wanted a system that’s efficient, a system that is not going to kill us from the investment standpoint. And something that gives us the opportunity to grow.”
A need for speed
So, with the basic principle of keeping it simple, they designed it around a conveyor system that’s able to bring product from A to B through some consolidation points. It also needed to be able to run either totes or product. Being able to convey product directly on the conveyor is new for the companies, Jurca noted. They also wanted a conveyor that was fast.
And this one, that was custom designed for them by Burlington, Ontario-based Mainway Handling Systems, is. It operates at 30 packages per min-
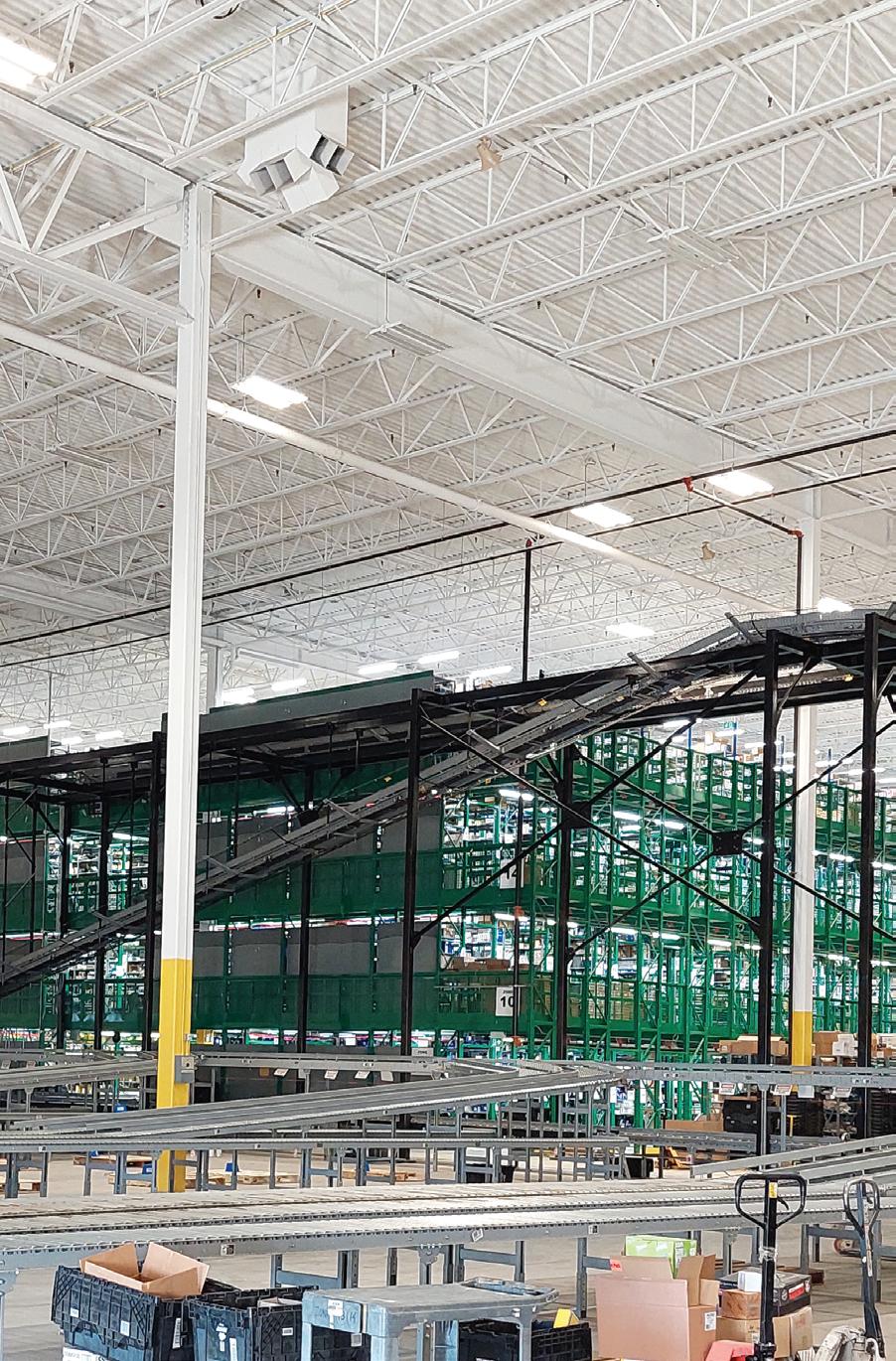
We are expecting a pretty fast return on the investment because productivity is going up,” Jurca said. “We see pieces per hour going up. And we also see the green monster swallowing more and more volume. Today we are pushing 65 percent out of that. That’s high-velocity products.
WORLDPAC-CARQUEST DC AT A GLANCE
Location: Bolton, Ontario ute, which is about 15 times faster than the system at the old Rexdale DC. Picked product takes nine minutes to travel from the green monster to the consolidation points. They also have the option to run it in reverse, if need be, for replenishment.
Size: 580,000 sq.ft.
“We are expecting a pretty fast return on the investment because productivity is going up,” Jurca said. “We see pieces per hour going up. And we also see the green monster swallowing more and more volume. Today we are pushing 65 percent out of that. That’s high-velocity products.”
The system allows the staff to focus on consolidation or picking, depending on the types of order being processed, he noted. The conveyors minimize the distance associates need to walk, which enhance productivity and workers’ job satisfaction.
“It’s technology that we love and technology that really works for us and enables us to grow because we have the insertion points we going to add going forward,” he said. “It’s one of my biggest achievements professionally. I’m very excited and I’m looking forward to, to work on additional opportunities because this is just the beginning.”
Cushing confirms that the building and systems were designed with growth in mind. He noted that there is room for more pick towers if required. “This was the first go around. It’s like proof of concept and then we can basically add more where we need to. It’s a kind of new technology for us,” he said.
“We want to make sure that the capacity of this facility can sustain our business growth over the next 10 years.”
Everybody all in
It was something of a gamble to bring the Carquest and Worldpac DCs under the same roof. As Cushing noted, it required a lot of new thinking and dropping siloed thinking for everyone involved.
“To me, the most fascinating part of it is knowing the change management that you needed to go through. When you think about bringing together two businesses that were both successful, it’s involved,” he said.
“And when you see this place and the work to build something like this, that’s where you build that camaraderie. When you’re working on a major project like this, you need all hands in. There’s no such thing as us and them. That’s gone. And that’s really what happened here. That was what enabled us to really make it one dream, one team.”
Capacity: 350,000 SKUs
Configuration: 40-ft clear, pallet racking, 4-level pick tower, high-speed conveyor
Access: 128 dock doors & 2 drive-ins
Throughput: DC Customer Orders (daytime shuttle deliveries) 19,000 units/week
Replenishment: 5 times/week
Employees: 200 (hiring up to another 30)
MHE: 67 Yale EV pallet jacks, forktrucks etc.
WMS: HighJump