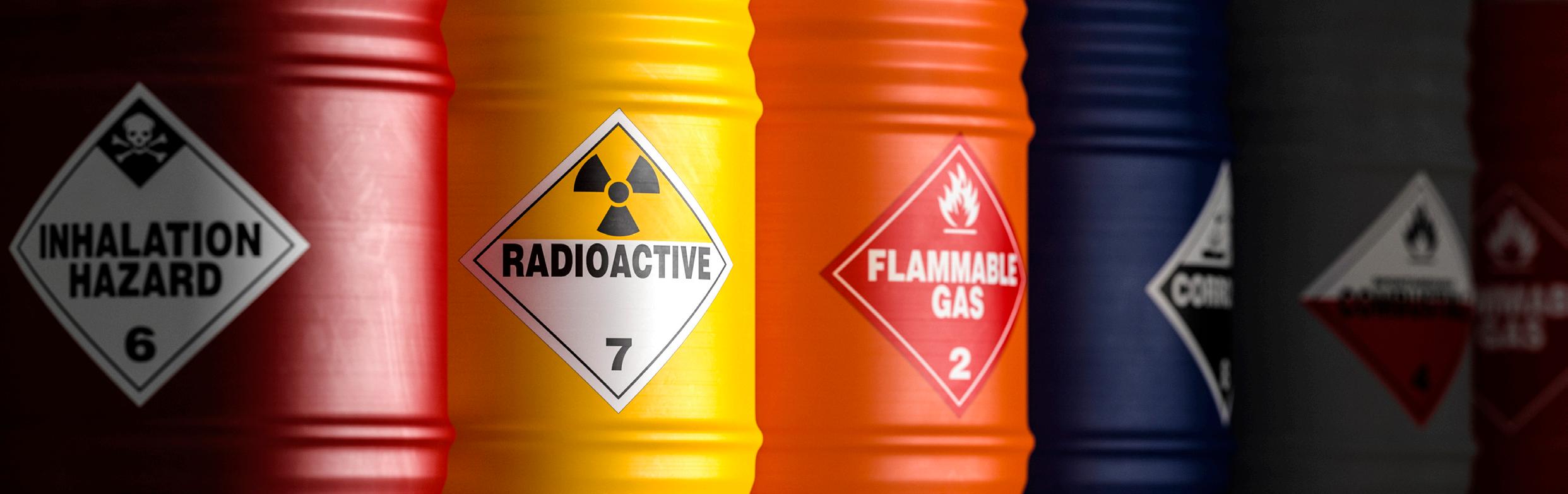
3 minute read
DANGEROUS GOODS COMPLIANCE
How it can be a competitive advantage for your business
The rapid proliferation of electric vehicles, the growth of e-commerce, and the rise in consumer goods that use lithium batteries have had a profound effect on the dangerous goods (DG) and hazmat market. The DG market is growing. According to SPER Market Research, the global hazardous goods logistics market is expected to reach nearly $432 billion by 2032, with an annual growth rate of 7.25 percent.
The strong growth also brings supply chain challenges. Moving DG is a complex, time-consuming, and challenging process. And in today’s highly competitive environment, organizations that ignore DG compliance put their operational efficiency, competitive agility, reputation, and bottom line at risk.
The complexity of DG shipping
The regulations that govern DG transport are complex, constantly evolving, and can vary by country and transportation mode, making it challenging to ensure all shipments (including labels, packaging and documentation) are compliant. In fact, in a Labelmaster global survey of DG professionals: 51 percent of respondents found it challenging to keep up with the latest regulations, and 28 percent were not confident, or unsure, that they could ensure DG regulatory compliance across their organization.
Ensuring compliance is especially difficult for organizations with multiple business units or locations, or those where senior leadership views DG management as a “necessary evil” and don’t properly invest in it.
Even though effective DG management technology solutions are available, many companies still rely heavily on manual, inefficient, and error-prone compliance processes. This approach further compounds the challenges of shipping hazmat safely, compliantly, and efficiently, and puts their employees, customers, and business at greater risk.
The risks of noncompliance
When a hazmat shipment fails to meet shipping regulations, it ends up stuck until the shipper can find a way to make it compliant. This can cost a business millions of dollars in fees, expenses, and lost customers and revenue. Beyond that, it’s important to understand the far-reaching risks of noncompliance.
Costs resulting from noncompliance can add up – from fees related to stopped shipments, to increased insurance liability following an accident, to the hidden costs of inefficient operations. All told, fees, fines, and other costs can reach into the millions.
Incorrect shipping labels, incomplete documentation, or other compliance-related errors can result in stalled shipments, late deliveries, and frustrated customers. Ultimately, they can also lead to additional penalties levied by the customers themselves.
Incidents with DG that impact public safety or the environment can also harm brand equity. If it involves noncompliance, this can create a negative sentiment – in the press and, most importantly, from customers, consumers, and other business partners.
Businesses that ship DG effectively have a competitive edge, offering products that other companies cannot, and shipping those products safely and faster than competitors (which may include your company).
Improving processes and transparency
The risks of regulatory non-compliance are a constant concern for organizations that move dangerous goods. That’s why many employ DG software to help achieve supply chain goals.
Software can automate and streamline the shipping process by producing documentation and validating shipments, packaging, labels and markings against the latest regulations. These repeatable and reliable processes can then be implemented across all locations, departments, and supply chain partners.
Compliance challenges slow down (or completely stall) processes across the supply chain – from fulfillment to transport. Automating DG shipping processes and ensuring compliance for labels, packaging, documentation, permits and shipping method, helps companies prepare and ship goods faster, and ensure they’re delivered on time.
Automating DG shipment validation helps avoid fines, streamline operations, and identify more cost-effective solutions to ensure they’re not overspending on packaging. They can also ship more goods without having to add personnel.
Shipping technology requires organizations to have complete and accurate master data. This detailed product information not only helps those directly responsible for DG management, but also helps manufacturing and procurement, carriers, 3PLs, customers, and other supply chain partners.
While technology can improve DG shipping operations significantly, it’s important to realize that complete, accurate data and proper employee training are critical to maximizing the potential and value of the solution.
Reducing risk
Shipping and handling DG will only become more difficult as supply chains become faster, regulations evolve, and new goods are introduced. Whether a company sends a few DG shipments per month or oversees a complex, global supply chain, ensuring the safe movement of goods is critical.
Compliance is not optional – it is a major risk and success factor. By prioritizing hazmat compliance, investing in technology and training, and implementing better processes, companies can be confident they are fully compliant with the latest rules and regulations. Shipping DG safely and compliantly is simultaneously a strong competitive advantage and risk mitigator.
Mario Sagastume is vice-president of software and customer success for Labelmaster.