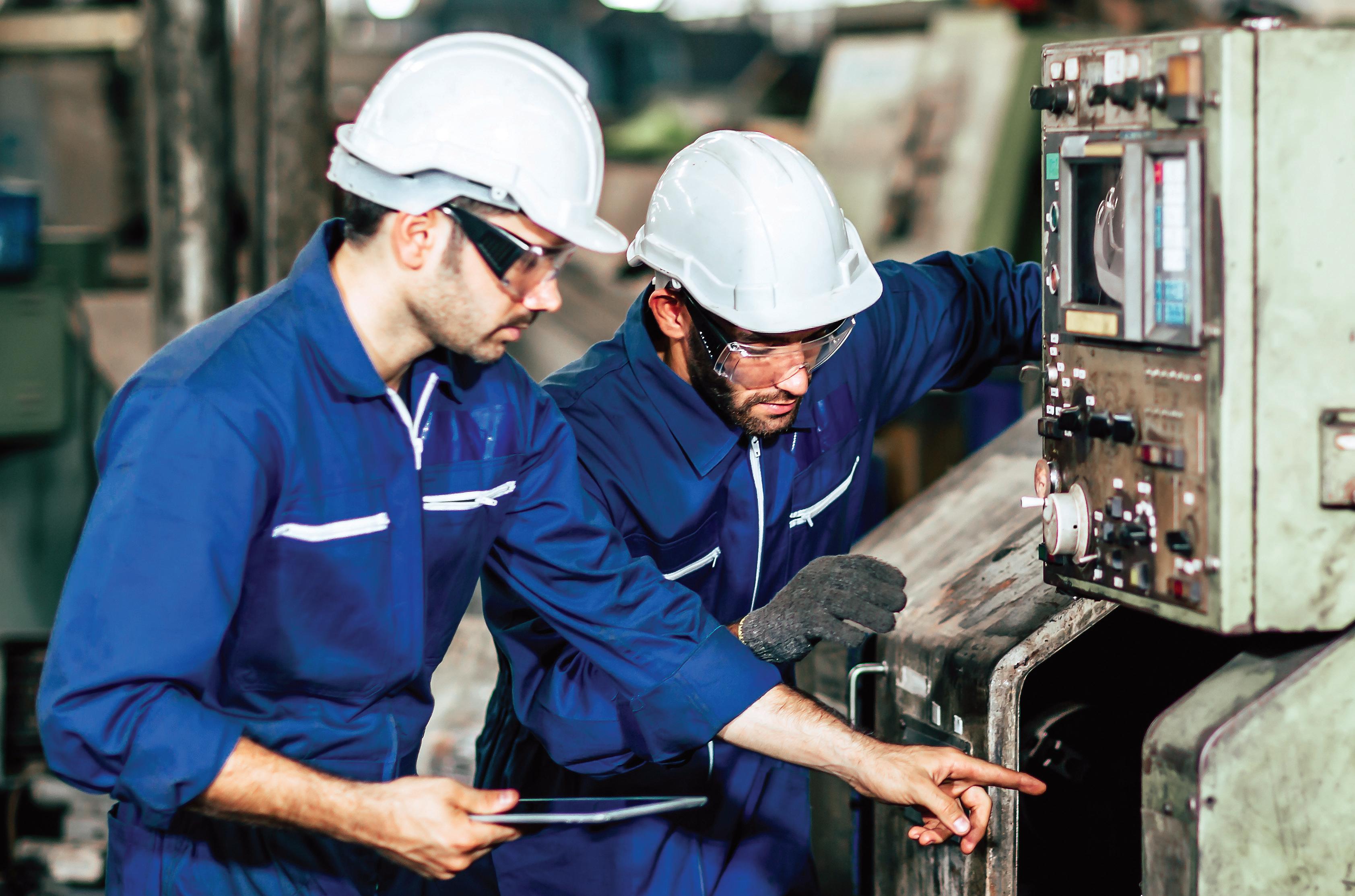
7 minute read
MRO Quiz
IGNORING EXTREME OPERATING CONDITIONS CAN COST INDUSTRY MILLIONS OF DOLLARS
The reliability of industrial machinery can be reduced by 50 per cent or more if extreme operating conditions are not considered. BY L. (TEX) LEUGNER
Many highly skilled, well qualified and well-meaning engineers and maintenance managers diligently and consistently apply sound maintenance ideas to their plant and industrial machinery, yet they fail miserably in their attempts to extend machinery life cycles or improve machine reliability.
Why is this so? One important reason is that plant management fail to consider the “extreme or unusual operating conditions” to which the organizations machinery may be subjected. This is a particular problem in plants, where the management group has little or no technical training or experience, and ignores recommendations made by those who have. Machine reliability problems directly associated with extremes in operating conditions include; • Poor design of new machinery. • Excessive machine vibration. • Extreme temperature conditions.
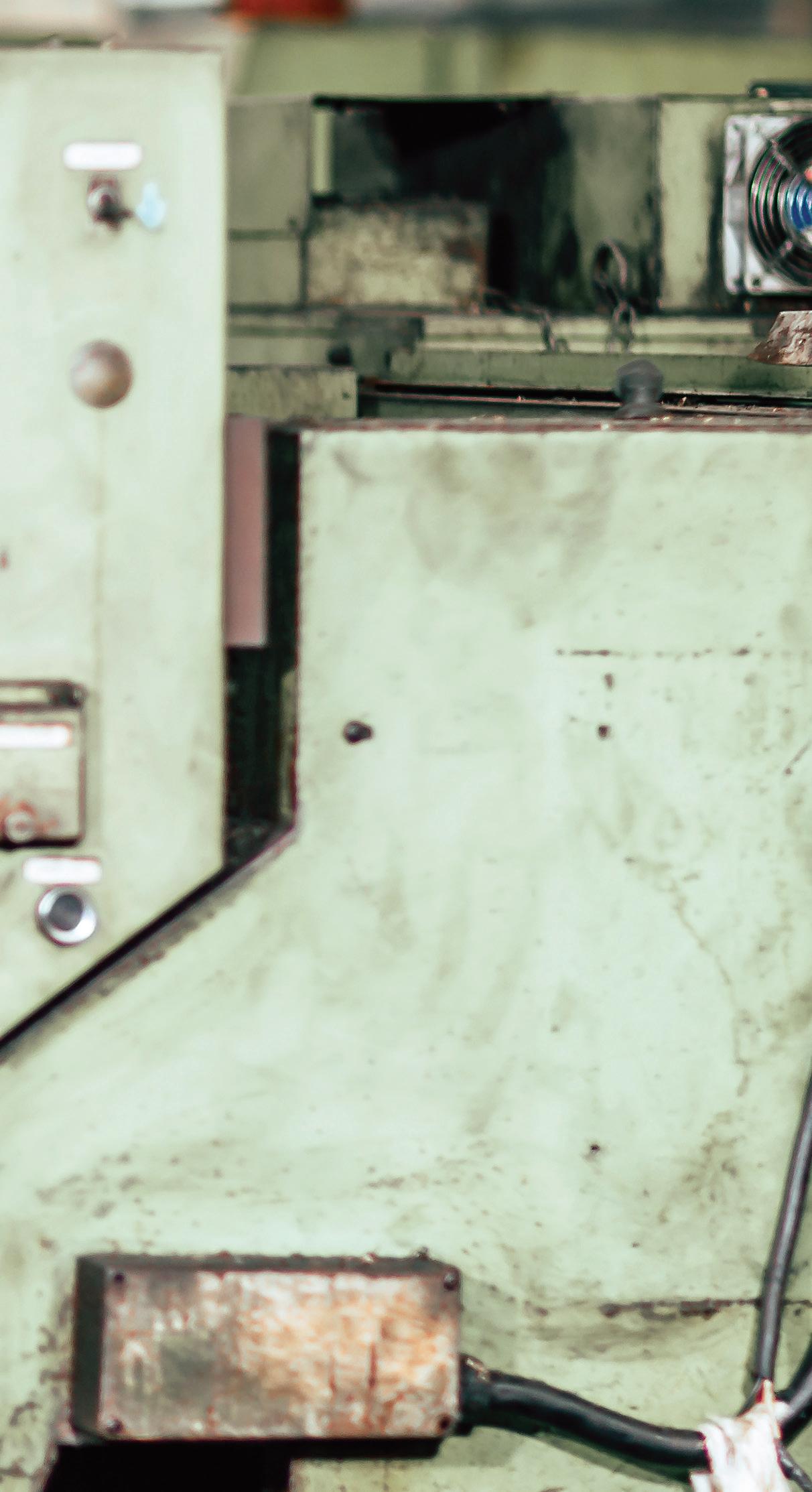
• Excessive contamination levels.
Let’s look at these conditions more closely and see how each affects machinery life cycles, equipment reliability and ultimately the efficiency and productivity of industry.
How does your organization plan for the acquisition of new machinery?
Logic: The relationship between life cycle costs and machinery design is a concept that is not always applied when the initial design of replacement machinery is considered. Put simply, life cycle costs include the total costs related to the design, manufacture, commissioning, operation, and maintenance, and finally, the disposal of any piece of machinery.
If for example, only 40 per cent of the life cycle costs are applied to the design, manufacture, and commissioning stages of a new piece of machinery, it stands to mathematical reason that most of the remaining 60 per cent of the life cycle cost will be spent during its operational lifetime. What this means is that regardless of the level of maintenance or the techniques applied, this machine will experience failure after failure throughout its operational lifetime. On the other hand, if 80 per cent of the life cycle cost is spent during the design, manufacture, and commissioning of a piece of machinery before it is put into operation, the machine will live a long, reliable, problem-free life, provided it is operated for the purpose for which it was intended. The lesson here is that no amount of maintenance can correct a poor design.
Does your maintenance group pay sufficient attention to the resolution of vibration-related problems?
Logic: Vibration analysis experts suggest, and the statistics related to vibration problems confirm, that most machinery vibration problems are the direct result of component or drive system misalignment, component unbalance, mechanical looseness, or machine resonance related to its design. Machinery wear or bolt loosening can cause mechanical looseness conditions.
Misalignment can be caused by worn components, such as in gear drives, but is caused primarily by poor initial installation and set up of drive shafts, couplings, and belt drives.
Component unbalance can be caused by wear, but frequently, it is caused by dirt buildup on fan blades or pump impeller erosion. Resonance is the term applied to a machine’s inherent (natural) vibration frequency. If the operating speed of the machine is such that its operational frequencies consistently come near to or continually pass through its resonant frequency, the operating frequencies can so seriously excite the resonant frequency that the machine can literally fly apart.
Designing a machine installation including the base, piping, duct work, pedestals, and accessories so that there are no natural frequencies coincident with any significant excitation generated by the machine’s operating frequencies must be considered because manufacturers are constantly reducing the machine’s mass and increasing capacities and loads in today’s equipment. As a result, resonance can be a problem throughout industry.
Is your organization aware of how both extreme ambient and operating temperatures can affect equipment operation?
Logic: Extreme temperature conditions include both high and low temperatures. In the case of temperatures below zero, industrial equipment requires the use of synthetic lubricants with high viscosity indices. This will ensure that oil flows are sufficient to allow the formation of satisfactory oil film thicknesses that will prevent wear during cold machine startup.
On the other hand, high temperature operation should be a greater concern in southern North American plants. Even a five degree rise in temperature above those recommended can eventually cause severe damage. Many factors can affect temperature, but the most common are the use of lubricants of the wrong viscosity, excessive loads or speeds, dirt and dust buildup on components that have an insulating effect, or contaminated lu-
Table 1: Common mechanical systems and their recommended operating temperatures.
Rolling Element Bearings Temperatures should not exceed 71⁰C (160⁰F). (Acceptable operating temperatures can be higher if synthetic oils are applied).
Hydraulic Systems Bulk oil temperature (at exterior of reservoir), should not exceed 60⁰C (140⁰F).
Gear Drives Operate best in a range of 49⁰C-60⁰C (120⁰F-140⁰F). Keep in mind that an operating temperature rise of 50⁰C (90⁰F) combined with an ambient temperature of 15.6⁰C (60⁰F) will result in a total “oil operating” temperature of 66⁰C (150⁰F) in gear drives.
bricants that can cause viscosity changes, foaming, oxidation, or other conditions that will dramatically affect the oil’s ability to disperse heat.
Another problem is that of overheated bearings that are grease lubricated. It is a mistake to apply more grease to an already overheated bearing. The additional grease simply adds to the problem because the lubricant acts as an insulator, the oil in the grease oxidizes and the increased temperature is absorbed by the bearing itself. In these cases, consideration should be given to the application of oil lubrication using a centralized oil mist system. Oil mist systems can reduce bearing temperatures by 20 to 30 per cent, because excessive lubricant is never allowed to remain in the bearing housing.
Do the personnel in your plant understand how contamination negatively affects equipment reliability?
Logic: Excessive contamination is the cause of approximately 70 per cent of all failures related to lubrication in systems, where close tolerances of machine parts are critical. This includes high pressure hydraulic systems, precision bearing applications, and engines.
It is a common mistake to conclude that if contaminants can’t be seen, it’s not present. Consider this: water contamination caused by condensation can be as high as 2,000 parts per million (PPM), yet may never be discovered without accurate analysis. In some machinery, where high lubricant flow rates are present, such as in a turbine, water contamination as low as 250 PPM can cause lubricant foaming. This can also occur in poorly designed piping systems, where high flow rates can cause turbulence.
Very small amounts of condensation moisture can cause serious damage in bearings, which are installed in seasonally used machinery, because the water slowly evaporates after a hot shutdown, causing corrosion of uncovered bearing surfaces. Consider dirt and dust contamination. Poor air filter system design and the application of poor-quality oil and air filters cause numerous machine failures in North America annually, but since careful failure analysis is not always carried out, these failures are incorrectly filed under “normal wear and tear”.
The lesson here is that dirt and dust particle sizes that cause the most damage are those that cannot be seen with the naked eye. These contaminants are in the size range of 10 to 40 micrometres and are referred to as “silt” contamination. Therefore, many equipment manufacturers and oil companies highly recommend that new lubricants are filtered prior to installation, and that contamination levels in lubricants in service should be monitored regularly using particle count analysis techniques. MRO
L. (Tex) Leugner, the author of Practical Handbook of Machinery Lubrication, is a 15year veteran of the Royal Canadian Electrical Mechanical Engineers, where he served as a technical specialist. He was the founder and operations manager of Maintenance Technology International Inc. for 30 years. Tex holds an STLE lubricant specialist certification and is a millwright and heavy-duty mechanic. He can be reached at texleug@shaw.ca.
“SEW-EURODRIVE products “modular components. are distinguished by their
—Shane Carnegie, Electronics Product Manager
Multitude of configurations Flexible mounting capabilities Advanced electronics ensuring efficiency
TORONTO MONTREAL VANCOUVER 1.800.367.8039 1.800.361.2928 1.800.972.5481

CIAL
M E D I A
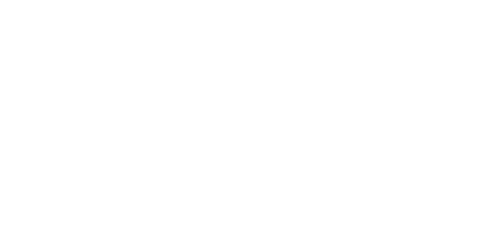
The Podcast for MRO Professionals
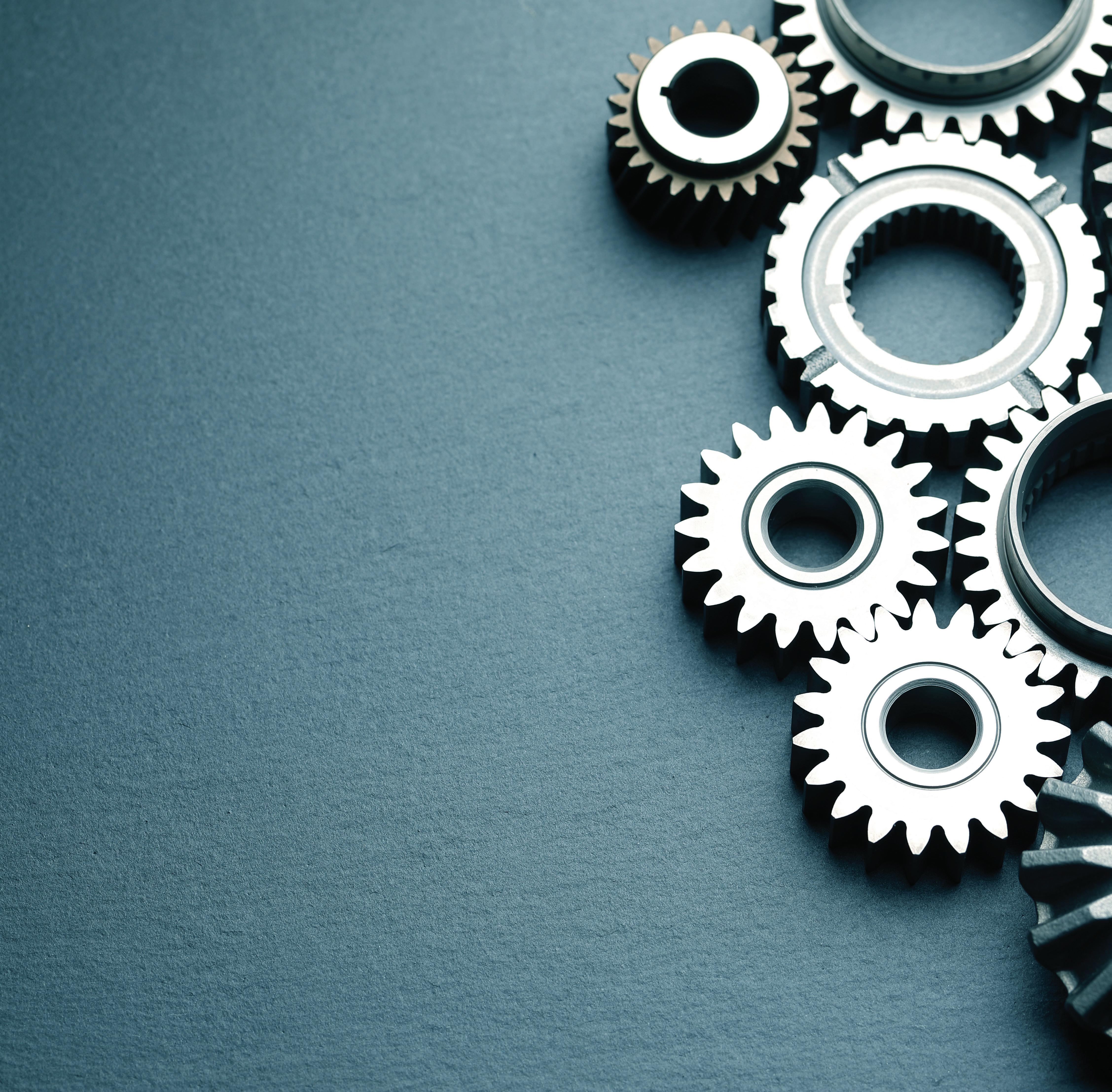
The podcast features conversations with industry experts about maintenance, reliability, and operations. Topics that are of utmost importance to MRO readers.
Previous guests and topics have included:
• Scott MacKenzie – Maintenance at TMMC Plants with a Focus on the Environment • Martha Myers – Importance of Networking and Education in Maintenance • Doc Palmer – Focus on Scheduling and Planning of Maintenance • James Reyes-Picknell – Managing Maintenance and Reliability • Shawn Casemore – Engaging Your Employees in a Safety Culture
For sponsorship opportunities, contact
Paul Burton, Senior Publisher, pburton@annexbusinessmedia.com
For guest/topic suggestions, contact