AUGUST 2022 PM #40065710 www.on-sitemag.com CONTROLSDIGGINGDIGITAL > INSIDE < CONCRETEON-SITE PG.37 SCANCONCRETE:BEFOREYOU ROADWORKINFRASTRUCTURE:FACINGCONSTRUCTION:CUTACREDITCRUNCHAHEAD 2022 INFRASTRUCTURE REPORT PG.13
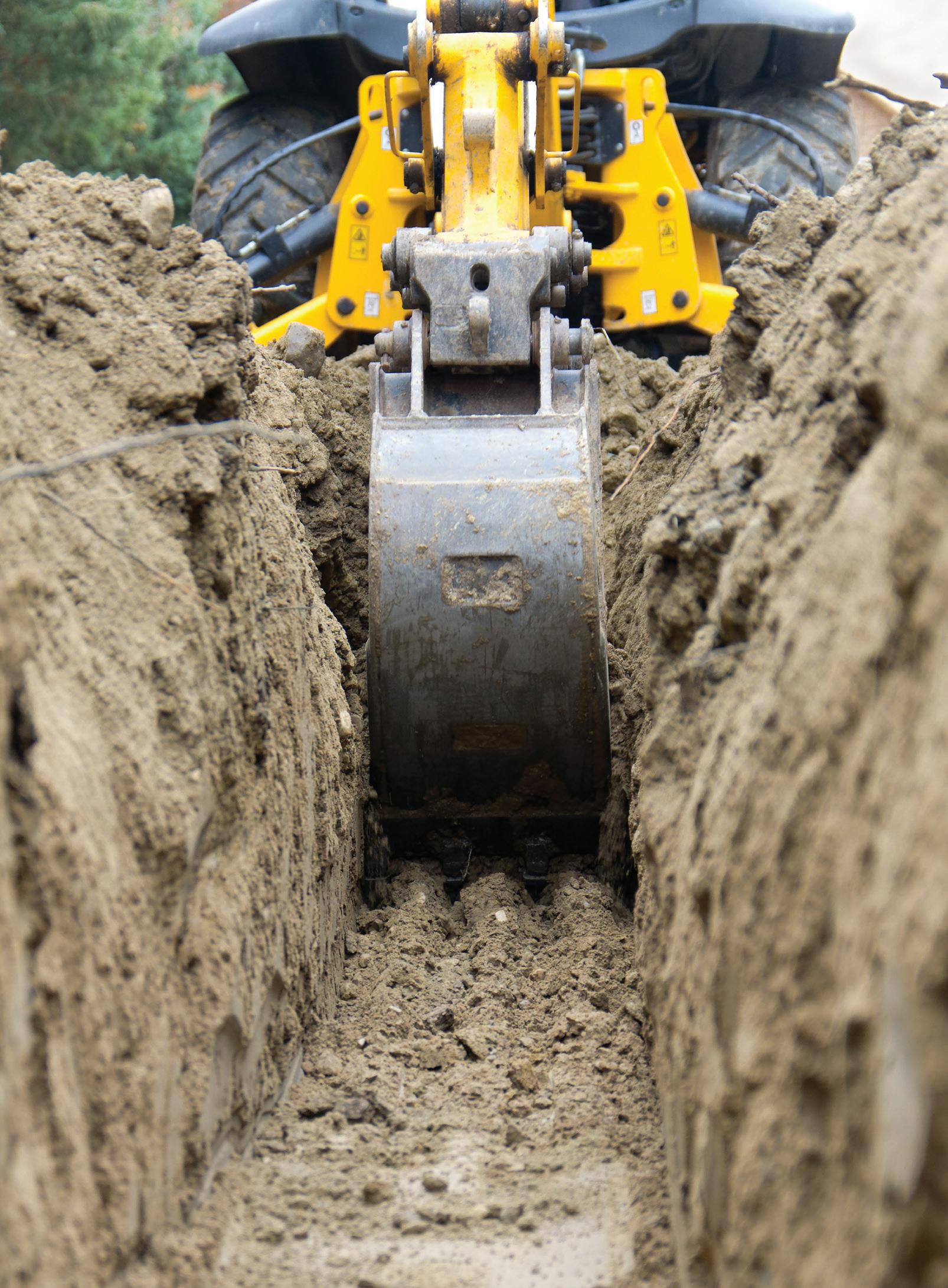
A thousand factors impact your bottom line every day. Some in your control, some well beyond it. One thing you have the power to choose is who you work with. Our job is to keep you moving forward. Our machines are engineered with a “get it done” mentality and our After Sales Solutions are designed to keep you up and running. The tougher your job gets, the easier it is to see we’re here when you need us most. Explore the latest innovations like the new ZX210LC-6 high performance construction excavator.
PROTECTING YOUR REPUTATION AND YOUR BOTTOM LINE. Hitachi Construction Machinery Americas Inc.

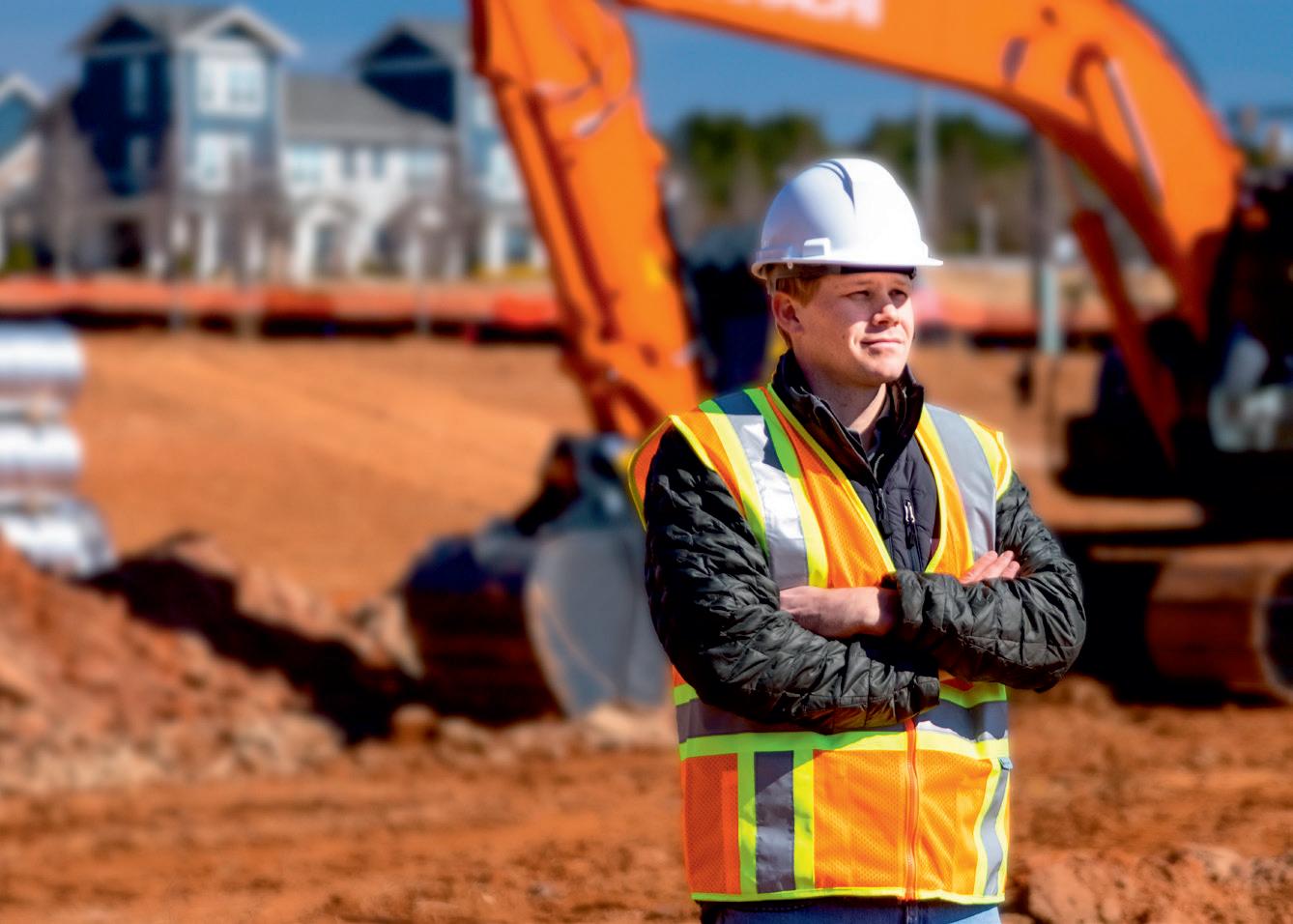
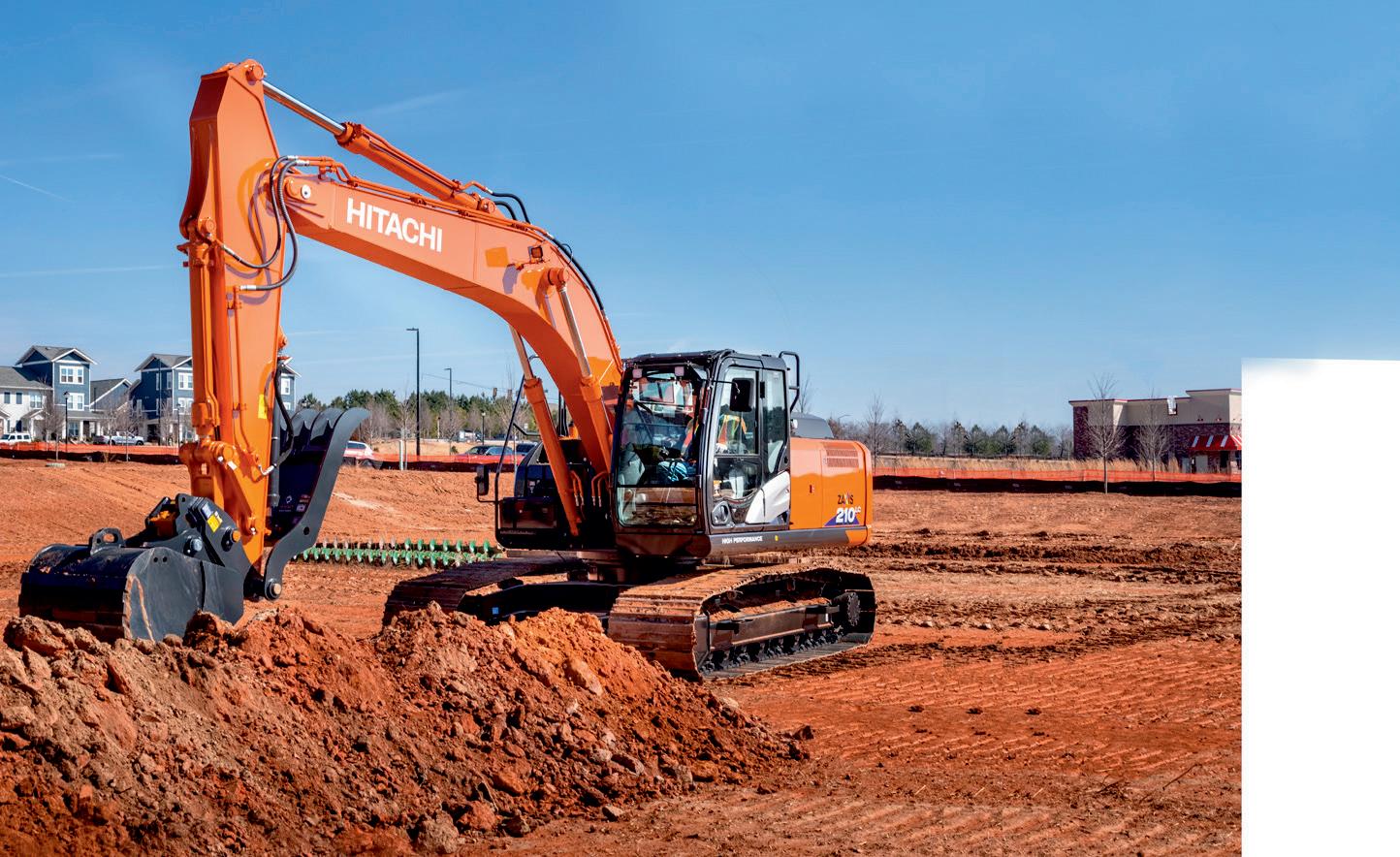
on-sitemag.com / 3 28 COVER STORY 31 Setting machine perimeters and parameters How geofencing and virtual fencing improve excavator safety and performance. IN THIS ISSUE 5 Comment The show must go on 8 News 12 Construction Stats 26 Streamlining subcontractor data 28 Recycling (aggregate) on the job 36 Choosing the right lubricant 2022 INFRASTRUCTURE REPORT 16 Roadworks work for the economy Five projects to watch. 22 Going digital for wastewater plans Toronto’s Ashbridges Bay Treatment Plant outfall project. 31 COLUMNS 24 Risk The construction credit crunch 48 Efficiency Lean delivers value 50 Technology Scheduling democratized 52 Contractors and the Law Resolving disputes on public infrastructure projects CONCRETE ON-SITE 39 Scan before you cut (or core) Modern scanning methods provide a clear picture of what’s happening below the surface. 42 Concrete solutions Finding low-emission paths to concrete production. 22 VOLUME 67, NO.5/AUGUST 2022 I53ndex AdvertisersofIMAGES.GETTYVIAPLUSIMAGESGETTY/ISTOCK/SIMPLYCREATIVEPHOTOGRAPHYCREDIT:PHOTOCOVER
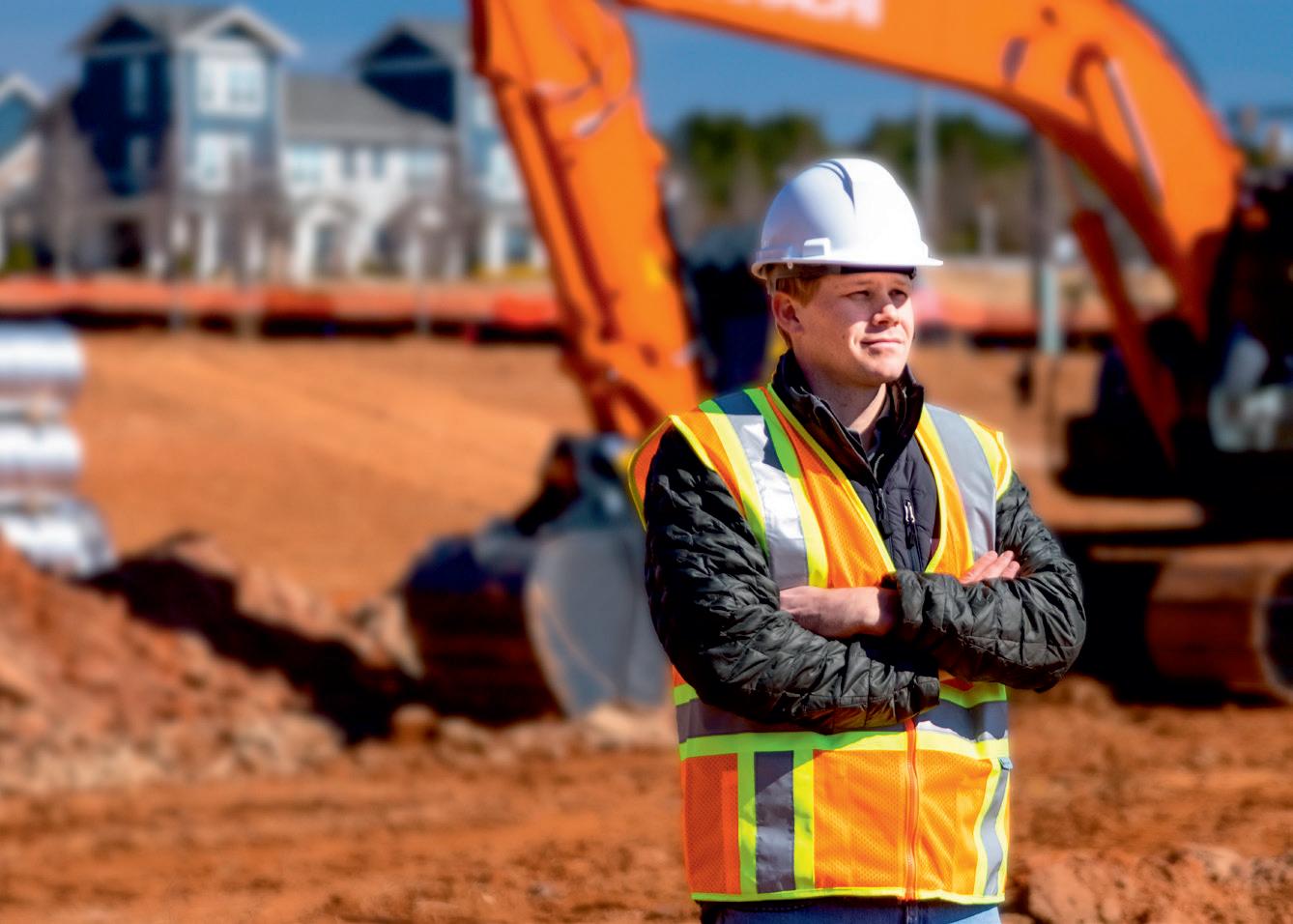
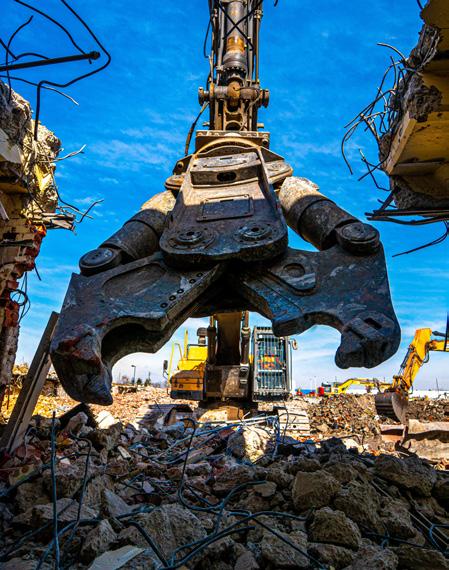
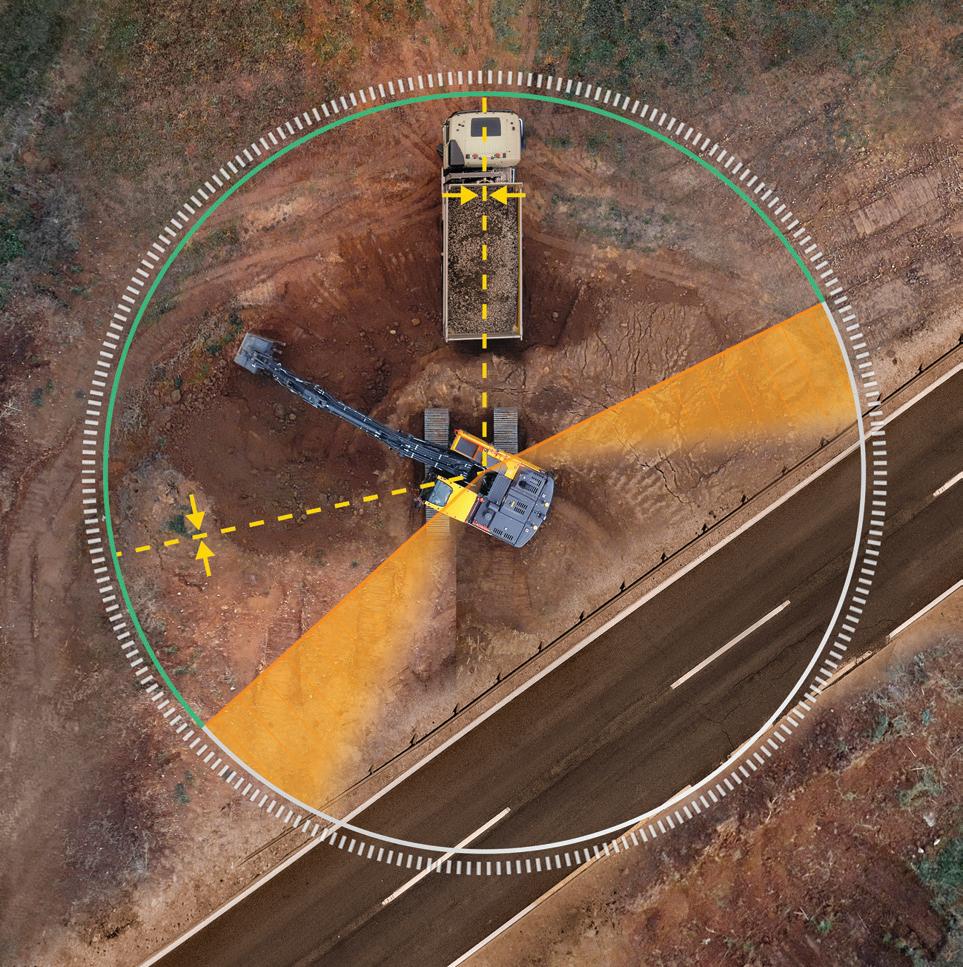
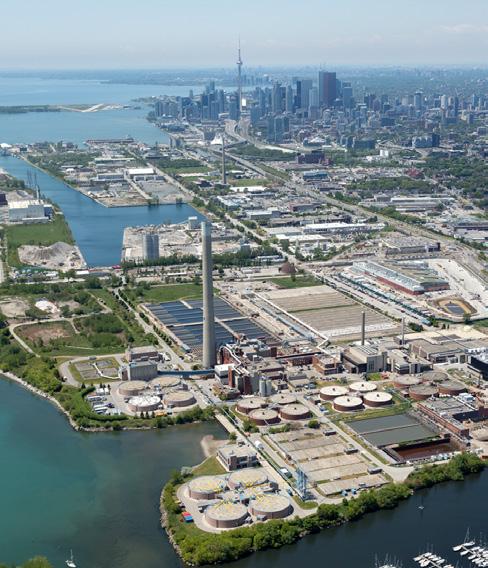
MARCH 14-18 / 2023 / LAS VEGAS / NEVADA 2.7M Square Feet of Exhibits 130,000 Attendees 1,800 Exhibitors 150 Education Sessions REGISTER at conexpoconagg.com Save 20% with promo code SHOW20 TAKING CONSTRUCTION TO THE NEXT LEVEL. “OUR INDUSTRY IS ALWAYS EVOLVING, AND CONEXPO-CON/AGG KEEPS US AHEAD WITH EQUIPMENT THAT MAKES OUR JOB EASIER, FASTER AND MORE EFFICIENT.” — AMERICAN PAVEMENT SPECIALISTS, DANBURY, CT
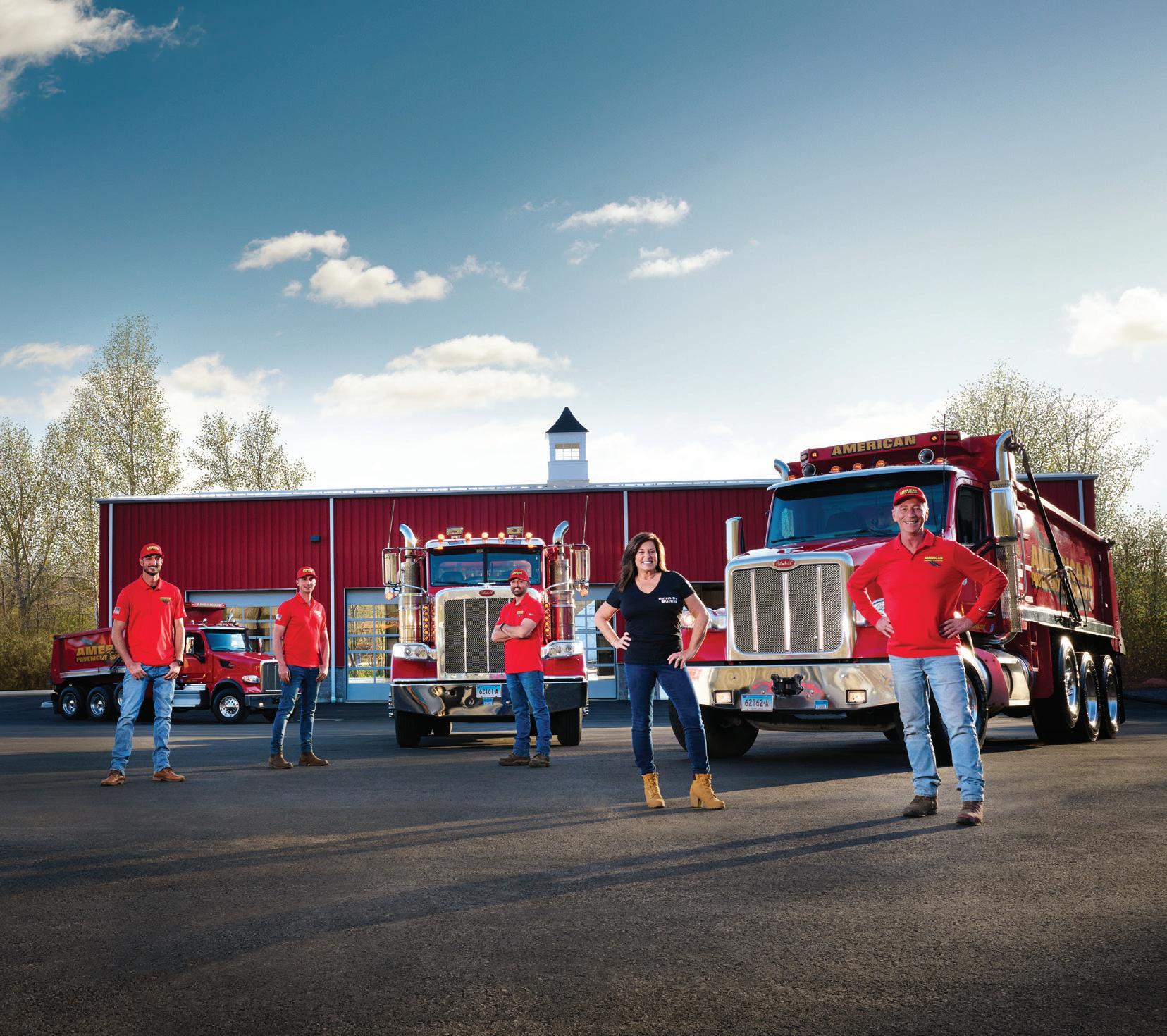
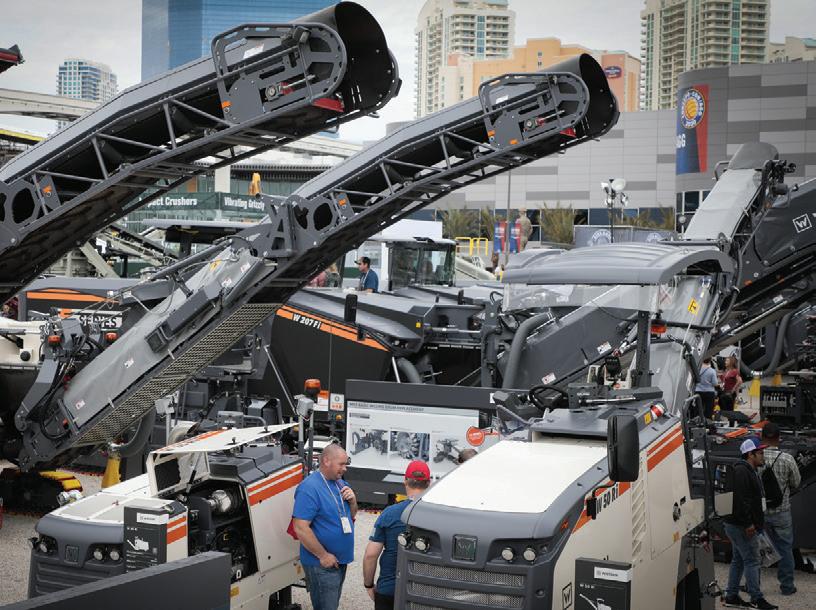
Having seen wood pipes firsthand, including some that have been removed from service in just the past five to 10 years, I couldn’t help but dive into Statistics Canada’s recent snapshot of the nation’s water infrastructure. With roughly 20 per cent of Canada’s water, sewer and storm water pipes having been built prior to 1970— more than 85,000 km of pipe—it’s no wonder that the pace of construction of underground piping networks has been on the rise.
While nobody wants to see projects shelved, some selective rework and prioritization may actually help those projects that do proceed, bringing a silver lining for some.
Adam Freill / Editor afreill@annexbusinessmedia.com
Deerfoot project that will be salvaged; they will get funded because they are deemed to be so necessary that they simply cannot be put off.
Inflation, Bank of Canada rate hikes, labour shortages, the ongoing saga of material shortages; the list of reasons why a project could be delayed or cancelled is plentiful this year, and some have already been put on hold, either temporarily or permanently. Thankfully, however, many have not, and that’s the basis of this year’s Infrastructure Report, which starts on pageDespite13.
When it comes to critical infrastructure, the show must go on
the challenges being faced by the construction industry, there are transportation-related projects underway from coast to coast in Canada, many of which have delivery targets more than a year out, meaning there will be work happening no matter where interest rates and inflation take the economy and Canadian economic sentiment in the near-term. While we’ve only listed a handful, projects like the ones profiled are the kinds of activities that will keep the sector busy as we weather these latest economic storms. In some cases, plans are also set to be reworked. For example, the recently announced cancellation of Calgary’s Deerfoot trail P3 proj ect included indications that several segments of the project would be broken out into individu al projects that will be put out for tender. While disappointing that the full scope of the project is unlikely, reassessments like these should allow the most critical components of larger projects to happen. So, while the size of the projects may be smaller, the volume of work is not being completely eliminated. And with the inflationary forces at play, projects that do move forward will be doing so at a higher price, so the spend in the sector may not take a hit, despite a potential drop in actual volume of work. Beyond roadways and bridges, other infrastructure work is also ongoing, like the water-related infrastructure project at Toronto’s Ashbridges Bay Treatment Plant outfall that’s outlined on page 22. Some of the water infra structure projects that will happen over the next few years will be much like the portions of the
Get the constructionlatestnews! Follow us @OnSiteMagTwitteron COMMENT
A 2021 report in Ontario pegged the infrastructure gap for water and wastewater in that province—the spend necessary to bring the infrastructure into good repair—at more than $12.5 billion in that one province alone. That’s a lot of potential new work; work that’s better tackled proactively rather than waiting on water main breaks and flooding to make it a priority.
on-sitemag.com / 5
That said, even with a jump from an average of less than 7,000 km of new pipes installed per year between 2000 and 2018 to more than 10,000 km per year since, the remaining useful life of water and sewage assets is on the decline, meaning more activity, and funding, is needed.
Regardless of the segment, rising lending rates are going to add more complexity to any civil or ICI project over the next little while, how ever, and some municipalities may use those rates as reasons to throttle back on less essen tial projects. Of course, having fewer projects may have an unintended consequence of easing some of the materials shortages and normalizing some pricing in our sector.
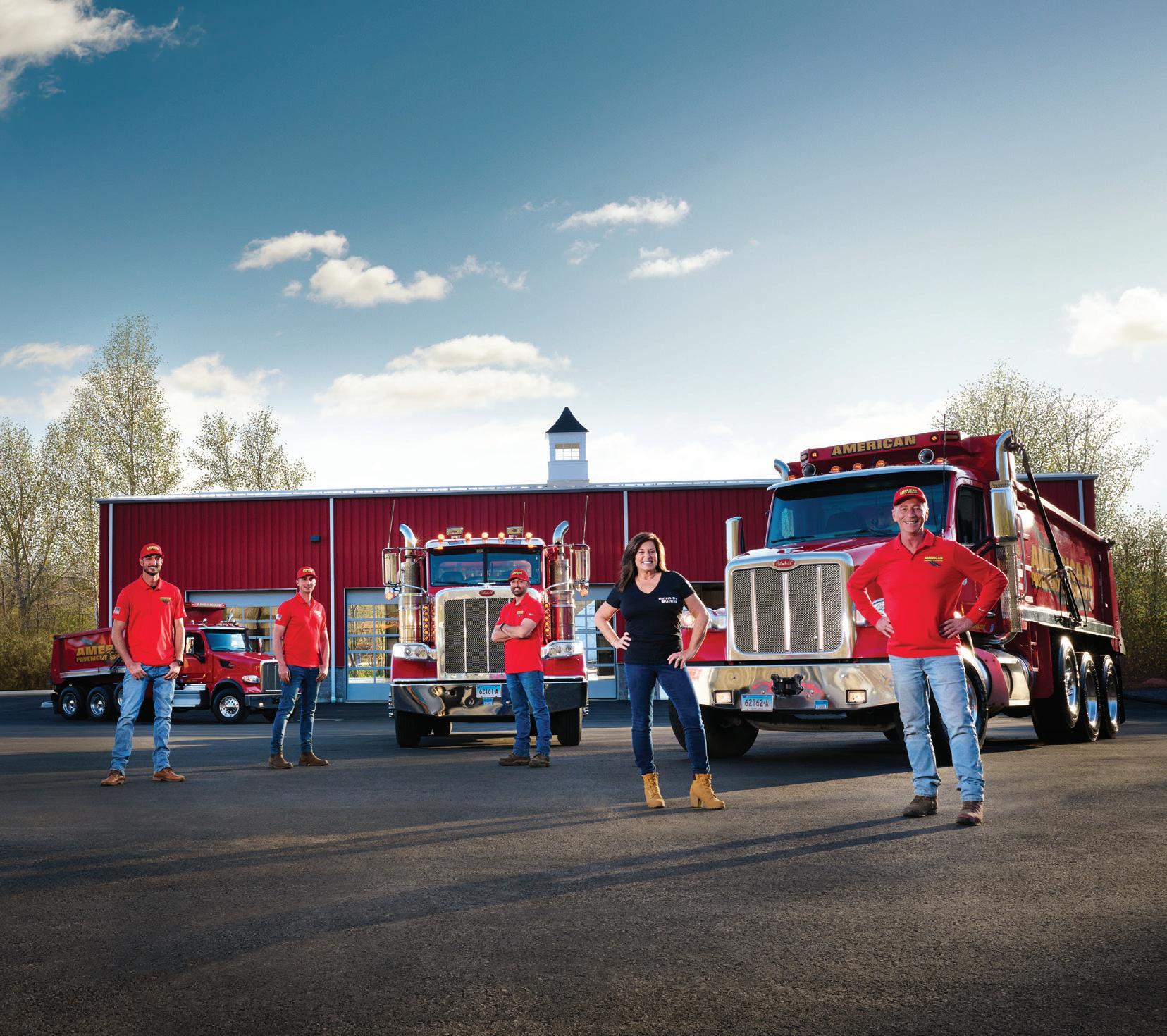


6 / AUGUST 2022 NATE HENDLEY / Freelance Writer and Author On new digital controls for heavy equipment: “Put simply, geofencing is about setting machine perimeters while virtual fencing is about setting machine parameters.” DAVID BOWCOTT / Growth Director – Innovation & Insight, Global Construction & Infrastructure Group at AON Risk Solutions On availability of capital, credit and cashflow: “It is time to strengthen your credit relationships.” JACK STATHAM / Lean and Sustainability Specialist at Chandos Construction On Lean Construction: “To truly implement and benefit from Lean Construction it must be embedded into the culture.” TRISH MORRISON / Partner and National Business Leader at Borden Ladner Gervais LLP On dispute resolution: “As with all contractual clauses, dispute resolution procedures can be negotiated and vary from contract to contract.” MEET OUR CONTRIBUTORS FOR THIS ISSUE CONTRIBUTORS VOLUME 67, NO.5/August 2022 READERwww.on-sitemag.comSERVICE Print and digital subscription inquiries or changes, please contact Angelita Potal Email: apotal@annexbusinessmedia.com Tel: (416) 510-5113 Fax: (416) 510-6875 Mail: 111 Gordon Baker Road, Suite 400, Toronto, ON M2H 3R1 PUBLISHER | Peter Leonard (416) 510-6847 pLeonard@on-sitemag.com EDITOR | Adam Freill (416) 510-6821 afreill@annexbusinessmedia.com MEDIA DESIGNER | Lisa lzambri@annexbusinessmedia.comZambri ASSOCIATE PUBLISHER | David Skene (416) 510-6884 dskene@on-sitemag.com ACCOUNT COORDINATOR | Kim Rossiter (416) 510-6794 krossiter@on-sitemag.com AUDIENCE DEVELOPMENT MANAGER | Urszula Grzyb (416) 510-5180 ugrzyb@annexbusinessmedia.com COO | Scott 111byEstablishedsjamieson@annexbusinessmedia.comJamiesonin1957,On-SiteispublishedAnnexBusinessMediaGordonBakerRoad,Suite400,Toronto, ON M2H 3R1 Publications Mail Agreement No. 40065710 ISSN: 1910-118X (Print) ISSN 2371-8544 (Online) SUBSCRIPTION RATES Canada $49.50 per year, United States $113.00 per year, Other foreign $136.50, Single Copy Canada $13.50. On-Site is published 7 times per year except for occasional combined, expanded or premium issues, which count as two subscription issues. Occasionally, On-Site will mail information on behalf of industry-related groups whose products and services we believe may be of interest to you. If you prefer not to receive this information, please contact our circulation department in any of the four ways listed above. Annex Business Media Privacy privacy@annexbusinessmedia.comOfficer Tel: Content800-668-2374copyright©2022 by Annex Business Media may not be reprinted without permission. On-Site receives unsolicited materials (including letters to the editor, press releases, promotional items and images) from time to time. On-Site, its affiliates and assignees may use, reproduce, publish, re-publish, distribute, store and archive such unsolicited submissions in whole or in part in any form or medium whatsoever, without compensation of any sort. DISCLAIMER This publication is for informational purposes only The content and “expert” advice presented are not intended as a substitute for informed professional engineering advice. You should not act on information contained in this publication without seeking specific advice from qualified engineering professionals. MEMBER OF ConstructionCanadianAssociation JACOB STOLLER / Principal, StollerStrategies On collaborative scheduling and project management: “One of the boldest approaches to collaborative scheduling and project management requires nothing more than a whiteboard, coloured marking pens and sticky notes.”
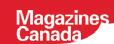
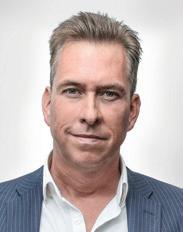
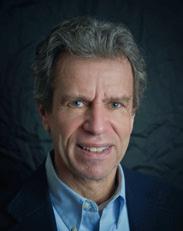
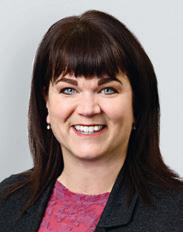

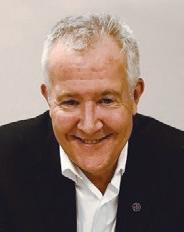
The leader solutionssustainableinair Atlas Copco’s range of e-air compressors provides a sustainable option for any application. See why E-Air fits your business, saves you money, and reduces your overall fleet emissions. 7 Benefits of Reduced Footprint Increased Reliability Lower Cost Ownershipof Easy to Use Less Downtime Low Noise Emissions CO2Zero • Pipeline testing and cleaning • Exploration drilling • Pigging • Road paint spraying • Cable blowing • Road maintenance • Quarrying • Blasthole drilling • Rock excavation • Sandblasting SCAN NOW TO LEARN MORE • Geothermal drilling • Renovation maintenanceand • Ground engineering drilling • Tunneling, metro and constructionsubway • Waterwell drilling Applications:


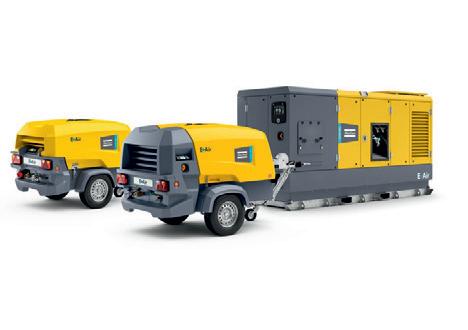

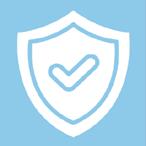

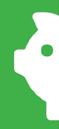

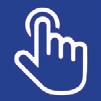

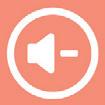


INDUSTRY>NEWS
honoured to see our longstanding commitment to trades training programs and BCIT recognized in this way,” stated Podmore. “This centre and these programs are key to equipping diverse, hardworking Canadians with the skills to secure well-paying jobs in construction, and we remain committed to working with our industry partners to find practical solutions to challenges that affect us all.” In the mid 1990s, Podmore first brought together industry leaders to address a shortage of skilled trades labour and subsequently founded Concert’s Corporate Annual Charity Golf Tournament to raise funds for trades-training programs. In 2002, Podmore and industry partners launched and provided funding for BCIT’s Trades Discovery Program, which has helped people across B.C. explore and pursue careers in different construction
BCITANDPROPERTIESCONCERTOFCOURTESYPHOTO:
A new trades and technology centre that will be developed at the Burnaby campus of British Columbia Institute of Technology (BCIT) will bear the name of Vancouver-based real-estate developer Concert Properties.Oncecompleted, the Concert Properties Centre for Trades & Technology will provide a space for innovation in skilled trades and engineering, applied learning, research and industry collaboration, and build capacity for 700 additional students which will alleviate trades training waitlists and help to build up a healthy talent pool in B.C. The centre will also anchor a new and renewed nine-building Trades and Technology Complex (TTC), under development at BCIT. This complex will include a covered works yard, simulation-based learning areas, maker spaces, and power, welding and construction areas. Concert has donated $7.5 million for the centre, which represents a key phase of BCIT’s Inspire Campaign. That campaign, chaired by Concert Properties co-founder and chair David Podmore, had raised more than $100 million as of July and is part of part of a six-year $680-million infrastructure investment target at the learning institute. “We’re extremely humbled and
INDUSTRY NEWS
8 / AUGUST 2022
David Podmore of Concert Properties (left) and Paul McCullough of BCIT share an advanced look at the yet-to-be-built Concert Properties Centre for Trades & Technology.
BCIT names training centre for Vancouver developer have resulted in pricing volatility and historically high inflation in the construction industry, which means a P3 approach to Deer foot Trail improvements is not economically viable.” As Alberta’s busiest freeway, Deerfoot Trail is a key commuter route in Calgary. With the city doubling in population since initial construction of the roadway in the 1970s, improvements are needed to accommodate current and projected traffic demands, as well as improve safety along the route. “We will focus on improving the most congested areas on the highway first to improve traffic flow and reduce travel times for commuters in the Calgary region,” said Panda. “Work is underway to identify the most critical areas for improvement that can be tendered and completed as quickly as possible.”
While the P3 plan for improvements for Calgary’s Deerfoot Trail has been put on ice by Alberta Transportation, upgrades to the highway will move forward as smaller projects, says the province’s minister of transportation, Prasad Panda. “While the government is not going ahead with a P3 approach, we remain committed to making improvements to Alberta’s busiest highway and will move ahead with the neces sary upgrades to help people get to their destinations safely and more efficiently,” he stated in July. “Current economic conditions Calgary’s Deerfoot Trail P3 plans cancelled; government aims to focus on smaller projects trades for the past two decades. Since the first annual charity golf tournament was held in 1995, it and other initiatives led by Concert have contributed over $2.4 million to the Trades Discovery Program. With the $7.5 million donation towards the new centre, Concert’s total financial commitment to BCIT over the past quarter-century has reached nearly $10“Themillion.Concert Properties Centre for Trades & Technology will help meet the demand for an estimated 85,000 new trades jobs expected over the next 10 years in B.C.,” stated Paul McCullough, interim president of BCIT. “It will set a new standard for applied education, research and collaboration–where together we will advance education, industry and society.” Construction of the centre is scheduled to begin in 2023.
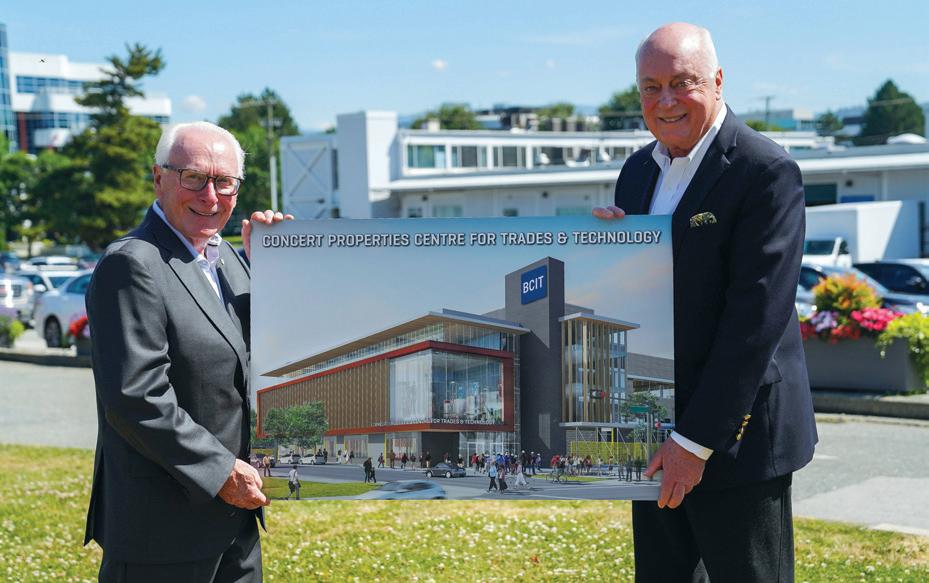
TW95
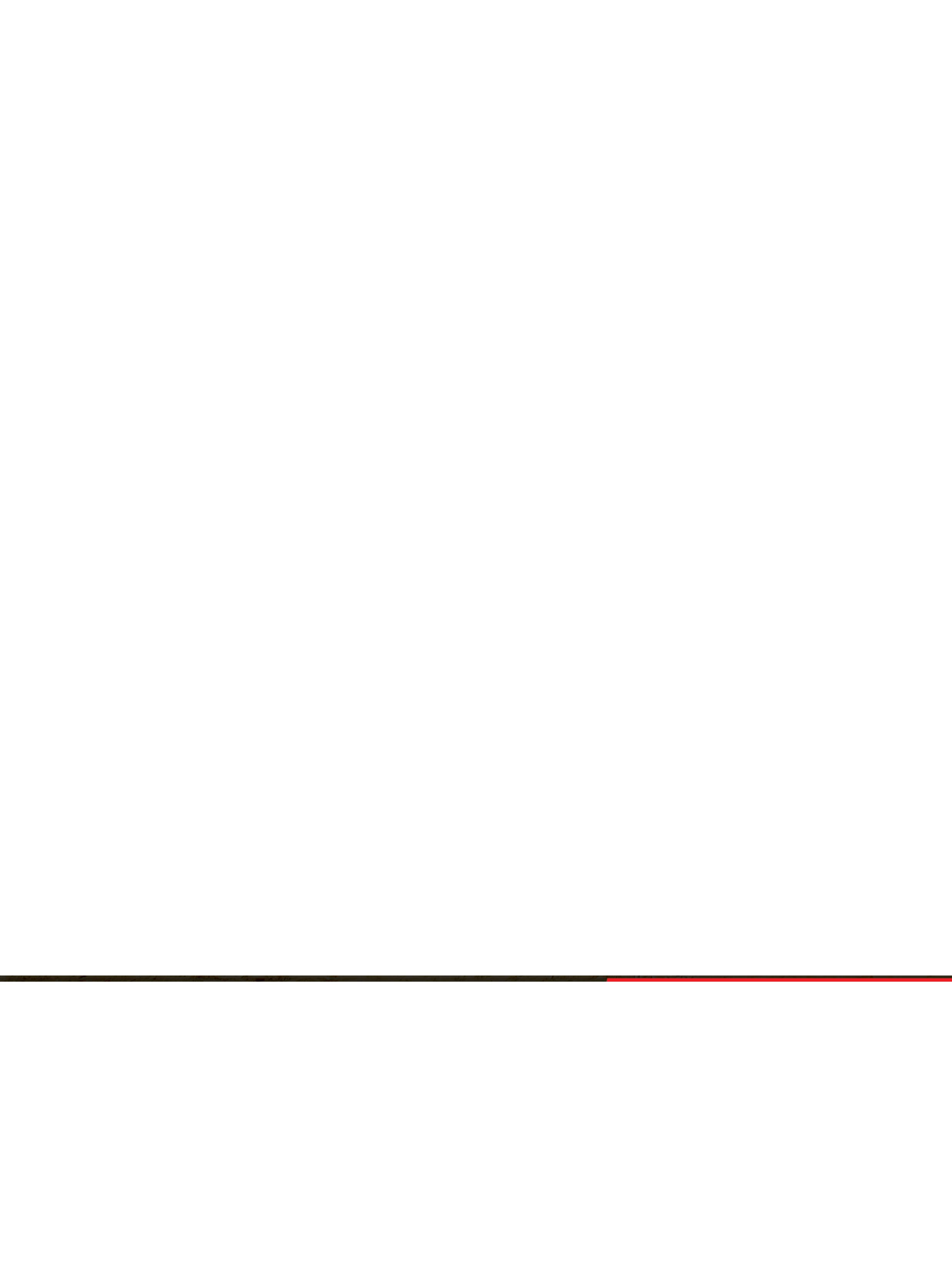
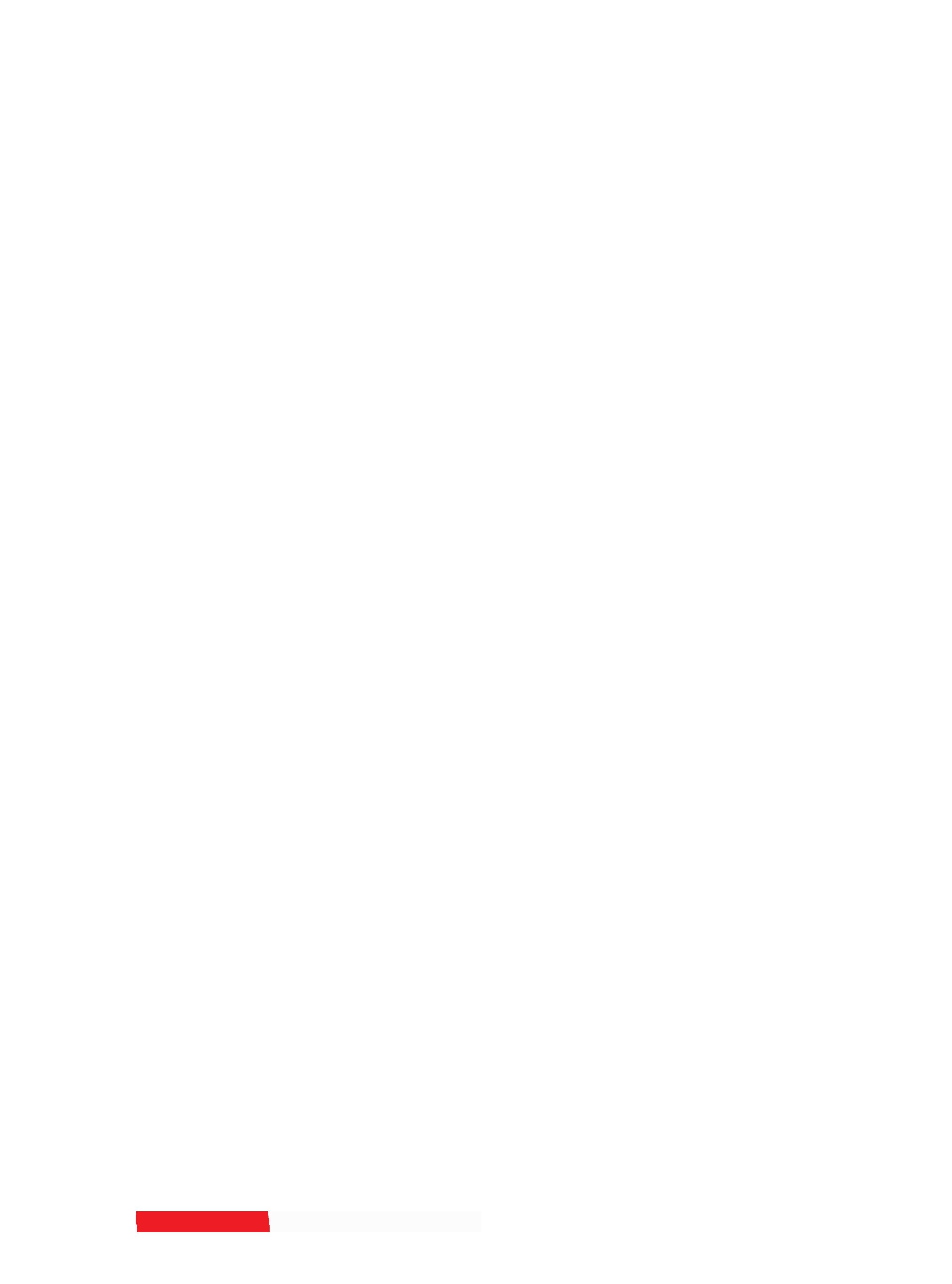
CIQS holds largest congress in recent memory
The contract for development and early construction work on sections of the Coquihalla between Hope and Merritt has been awarded to KEA5, a joint venture between Peter Kiewit & Sons and Emil Anderson Construction. The work to return the Coquihalla to the previous full, fourlane capacity will take place at three sites:
• Falls Creek Bridge, 55 kilometres south of Spences Bridge;
• Bottletop Bridges, 50 kilometres south of Merritt; • Juliet Bridges, three kilometres south of Bottletop; and • Jessica Bridges, 48 kilometres south of Juliet. Work is expected to be substantially complete this winter, and all efforts will be made to minimize traffic disruptions during peak travel hours, and crews will work overnight when possible.
The project will be completed through a collaborative construction model where the owner and contractor work together to complete the design and construction of the project, including sharing risks and incentives.
The RFP process invites select contractors who qualified through the Highway Reinstatement Program request for qualifications (RFQ) process to take part in the competitive selection process to design and construct the permanent repairs needed at:
In late June, British Columbia’s Ministry of Transportation and Infrastructure reported that permanent repairs to flood-damaged sections of the Coquihalla (Highway 5) and Highway 1 were set to start this summer. “This marks a significant milestone in our recovery from the devastating atmospheric river events of last fall,” said Rob Fleming, Minister of Transportation and Infrastructure. “Following the extraordinary work that was done to reconnect these highways in December, we’re building back permanent infrastructure that will be equipped to better withstand the impacts of climate change and future extreme weather events. I want to extend my sincere thanks and appreciation to all those who have worked together to help us recover from the unprecedented floods, including the local First Nation communities that continue to work closely with us as we move into this next phase of recovery.”
The ministry has also issued a request for proposals (RFP) for damaged sections along Highway 1 through the Fraser Canyon.
Featuring insights into Canada’s political climate, as well as inspiration to foster and promote the next generation of skilled trade professionals, the first in‐person Canadian Institute of Quantity Surveyors (CIQS) Congress since 2019, held this past June in Ottawa, was one of the largest in over a decade. With a focus on professional develop ment, educational sessions kicked off with a presentation on government relations by Huw Williams of Impact Public Affairs. He shared his insights on the political climate in Canada and CIQS’s advocacy campaigns. With delegates emerging from two years of virtual events, they had the opportunity to take in an in-person congress B.C.’s Ministry of Transportation and Infrastructure is moving forward on permanent repairs to a number of sections of highway, including the Coquihalla/Highway 5. Huw Williams of Impact Public Affairs talks politics. Permanent repairs coming to Coquihalla and Highway 1
OFMINISTRYB.C.OFCOURTESYPHOTO:CIQSOFCOURTESYPHOTO:INFRASTRUCTURE/FLICKR.COMANDTRANSPORTATION
The ministry is continuing to make progress on restoring access throughout the Highway 8 corridor. The storms completely washed out 25 sections of that highway, leading to the closure of the highway between Merritt and Spences Bridge. Since then, the ministry has completed temporary repairs at 18 locations and construction has started on another two. Work is being planned for the near future at the five remaining sites to complete temporary repairs along this route.
• Tank Hill Crossing, 23 kilometres south of Spences Bridge; and • Nicomen River Bridge, 19 kilometres south of Spences TheBridge.RFP for the repair project will close September 14, 2022, with the contract awarded shortly thereafter.
agenda that covered a vast range of topics, such as prompt payment, risk management, MEP pre‐fabrication initiatives, P3 projects and dispute resolution.
Saturday morning’s keynote session featured Jamie McMillan, who shared an inspirational tale about how she climbed the proverbial mountain of life to attain her goals of becoming an iron worker, role model and advocate for the next generation of skilled trade professionals. Not going completely virtual-free, this year’s annual general meeting and yearly review was offered in a hybrid presentation, allowing all members with voting rights the opportunity to make their voices heard. With 599 members registered to participate, and 400 who submitted proxies, this was the largest AGM since the inception of CIQS. Founded in 1959, CIQS is the voice for Canada’s construction economists. The self‐regulatory, construction and infrastructure economics professional body currently represents over 2,000 national and industry professionals.
10 / AUGUST 2022 INDUSTRY NEWS
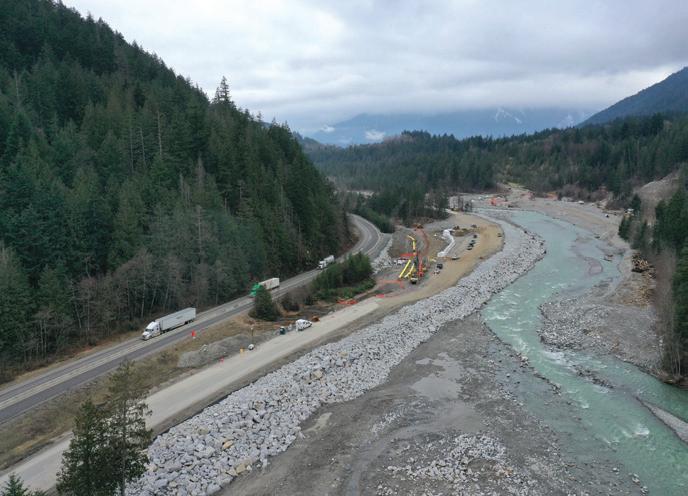
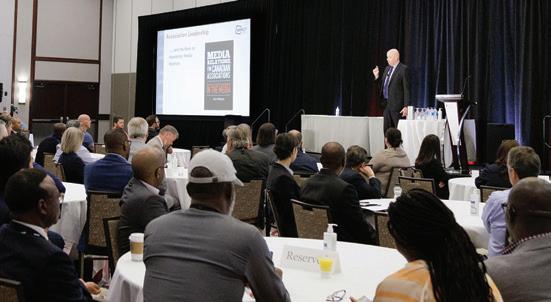
Moving Forward in withConstructionAvetta
COUNCILWOODCANADIANTHEOFCOURTESYPHOTO:
on-sitemag.com / 11
In a media announcement following the test, CWC stated, “It can be concluded that the fire performance of the mass timber structure was similar to that of non-combustible construction and confirms that mass timber can perform well under the very rare fire scenario in which the sprinkler system fails, and the fire department is unable to respond.”
Schedule your demo today at avetta.com/demo
OnSite_Avetta_June22.indd 1 2022-06-06 10:22 AM
The Avetta platform provides access to a roster of industry-leading professionals, vetted and verified to meet your team’s standards.
More information about the fire tests and mass timber is available on the CWC’s website.
Mass timber fire test lives up to expectations
In a recent full-scale fire test conducted at the Canadian Explosives Research Lab in Ottawa and hosted by the Canadian Wood Council, a mass timber structure withstood a full burnout. More than 150 experts from across Canada, including fire officials, building regulators, insurance industry representatives, engineers and architects, witnessed the unique event, which aimed to learn about and observe the behaviour of mass timber construction exposed to fire. To date, the majority of exposed mass timber compartment fire tests have been conducted on simulated residential occu pancies. This test demonstrated the fire performance and fire dynamics in a typical occupied open-plan office space in a mass timberSimulatingbuilding.an office, the space was much larger than previ ous tests, both in the area and floor-to-ceiling height. To get a more accurate estimation of performance, the test area included a large fire load of simulated furniture and other contents.
The CWC was happy to report that the research fire test performed as expected, and the fire largely burned out within the first hour. The test extended for an additional four hours, however, to monitor for any potential re-ignition. To help monitor the fire, the research test structure was outfitted with 400 thermocouples and radiation sensors, which helped researchers document the fire development.
In an industry where all eyes are on compliance, Avetta keeps job sites safe and TRIR rates down – while still protecting ROI.
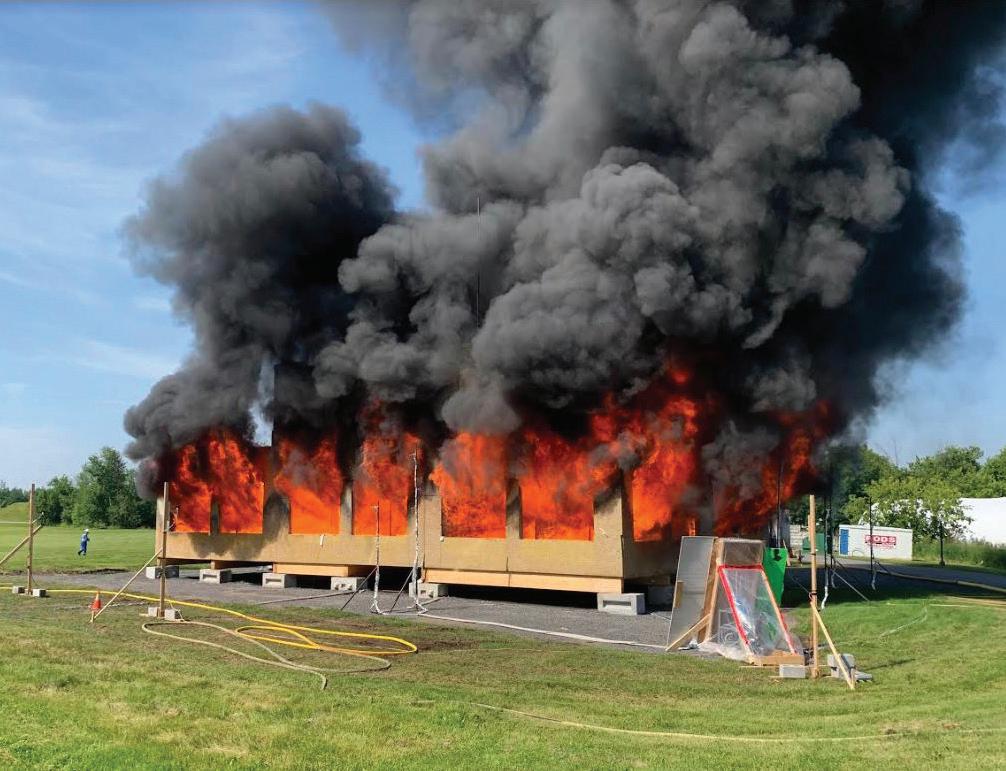
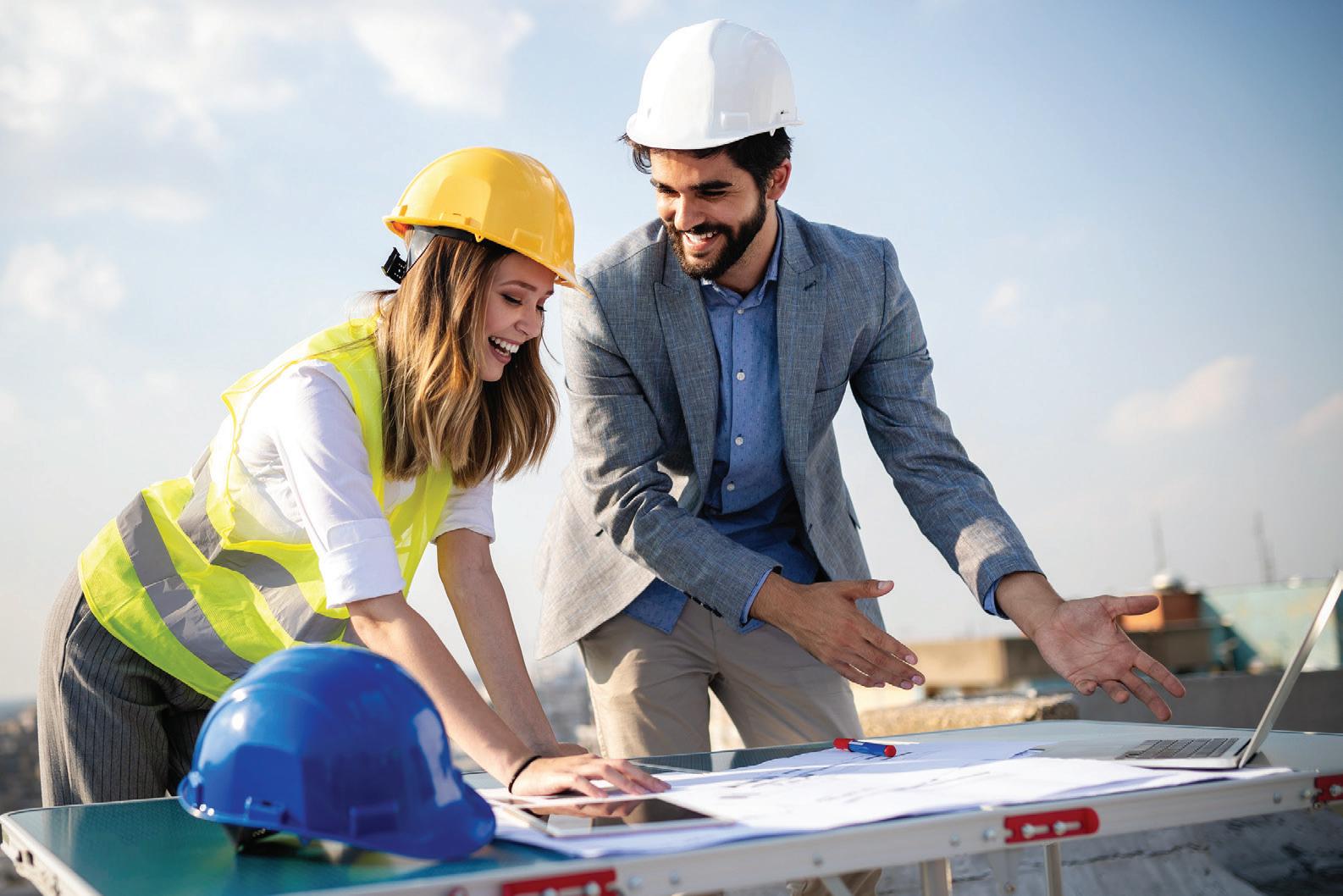
According to a recent report from Canada Mortgage and Housing Corporation (CMHC), housing supply has not responded to demand over the past 20 years in Canada, especially in some of the country’s large urban areas. This, says CMHC, has resulted in the loss of affordability. The report, Canada’s Housing Supply Shortages: Estimat ing what is needed to solve Canada’s housing affordability crisis by 2030, takes initial steps to estimate how much additional housing supply is required to restore affordability by 2030, the date upon which CMHC has set as its aspiration for everyone in Canada to have a home they can afford and that meets their needs. CMHC projects the housing stock to increase by 2.3 million units between 2021 and 2030 if current rates of new construction continue, reaching close to 19 million housing units by 2030. According to the report, Canada would need an additional 3.5 million units to restore affordability. That means that the housing stock would need to climb to over 22 million housing units by 2030 to achieve affordability for everyone living in Canada. Housing Starts, SAAR 273,841 Housing Starts Trend 258,259 $Millions) Labrador Edward Island Scotia Brunswick Columbia Northwest Territories 6.3
According to the latest figures compiled by Canada Mortgage and Housing Corporation (CMHC), the trend in housing starts came in at 258,295 units in June, up from 252,444 units in May. The trend measure, a six-month moving average of the monthly seasonally adjusted annual rates (SAAR) of housing starts, didn’t quite match the standalone monthly SAAR, which saw a decrease of three per cent from May, coming in at 273,841 units for all areas in Canada in June, but housing starts remain historically high.
19.2 Nova
STRIKES IMPACT MAY BUILDING CONSTRUCTION VALUES
$ Investment in construction,non-residentialMay2022 (in
In the residential sector, multi-unit construction continued to climb, increasing 3.4 per cent to $7 billion, while investment in single-family homes declined 2.5 per cent, ending a seven-month growth streak.
70.2 New
CANADIAN HOUSING STARTS TREND HIGHER IN JUNE
Thanks to a considerable recovery of activity on construction sites in 2021, this year’s payouts hit a record total, rising 10 per cent over last year’s $503 million that was paid out.
3.7 Nunavut
53.9 Quebec 1,334.8 Ontario 2,033.3 Manitoba 160.5 Saskatchewan 102.6 Alberta 674.1 British
A selection of data reflecting trends in the Canadian
construction industry CONSTRUCTION STATS
The agency attributes the dip to strikes among many of Ontario’s unionized construction workers during the month. These strikes caused significant delays in numerous residential and non-residential construction projects throughout the province. Excluding Ontario, investment increased just over one per cent at the national level.
“The monthly SAAR was lower in June compared to May; however, the level of housing starts activity in Canada remains historically high and well above 200,000 units since 2020,” said Bob Dugan, CMHC’s Chief Economist.
QUEBEC CONSTRUCTION HOLIDAY PAYOUT: $553 MILLION
TABLE: STATISTICS CANADA Canada 5,228.3 Newfoundland and
34 Prince
Statistics Canada is reporting investment in building construction was almost flat in May, edging down 0.2 per cent on a month-to-month basis to $20.6 billion.
The Commission de la construction du Quebec (CCQ) sent out almost 182,000 vacation cheques to construction workers in that province in advance of the annual construction holiday, amounting to a total of more than $553 million.
725.8 Yukon 10
12 / AUGUST 2022
CANADA IN NEED OF 3.5 MILLION HOUSING UNITS
The workplace stoppages also resulted in the end of a 13-month streak of growth in the non-residential sector. Combined, the components contracted 0.9 per cent to $5.2 billion in May despite gains in eight provinces, with all three components moving downwards compared to a month earlier.
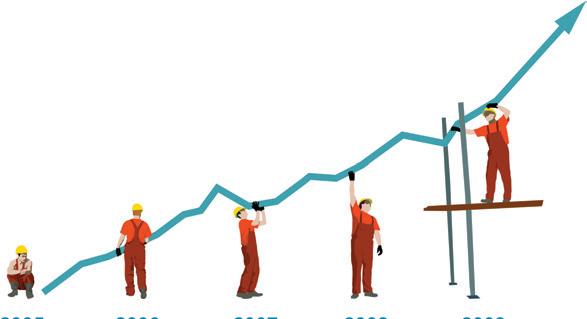
2022 INFRASTRUCTURE REPORT ROADWORKPROJECTS FORGING PATH AHEAD PHOTO: © VOLODYMYR SHEVCHUK / ADOBE STOCK
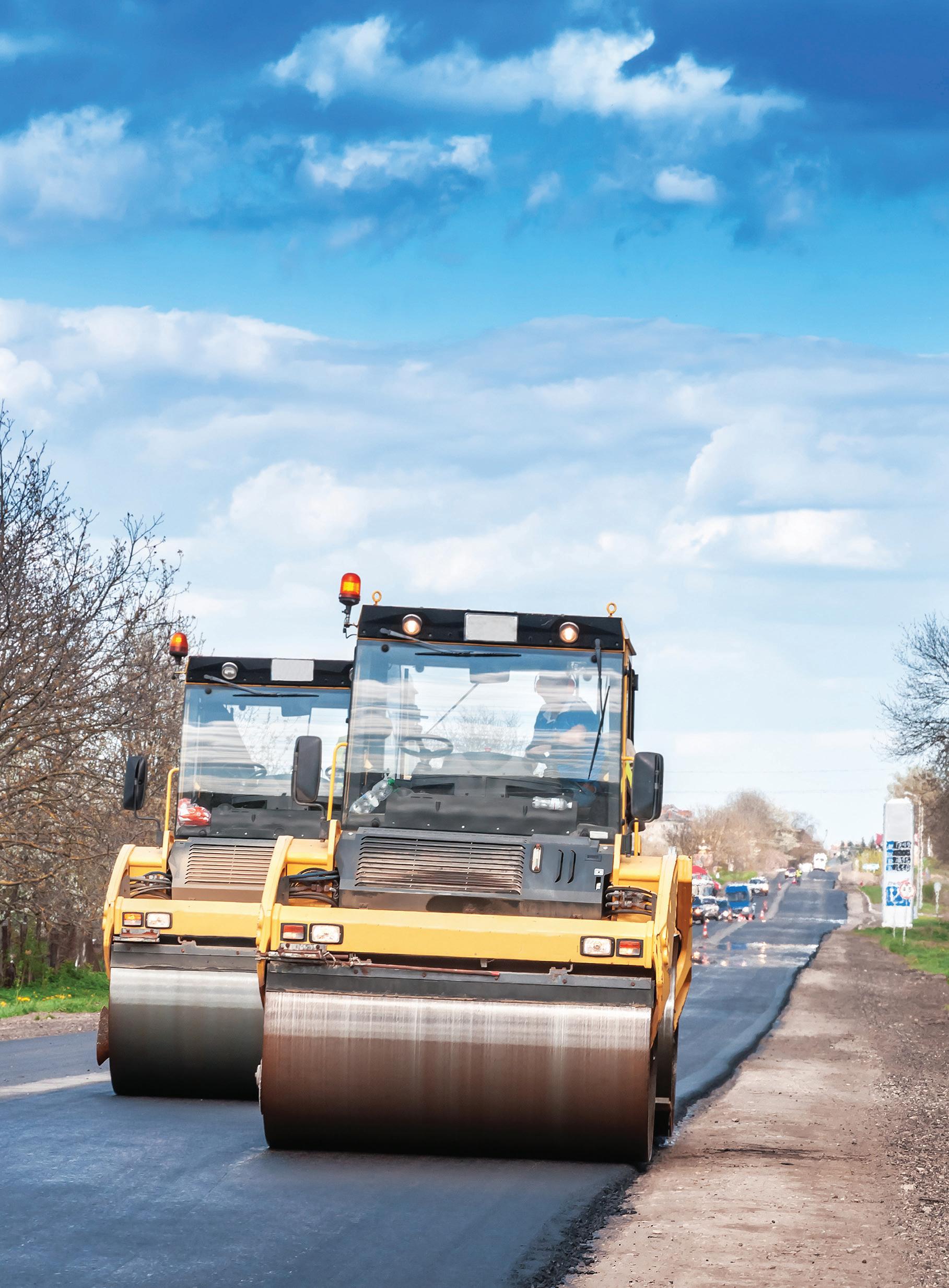
WIRTGEN AMERICA, Inc. · 6030 Dana Way · Antioch, TN 37013 · CLOSE TO OUR CUSTOMERS. The extremely productive HD+ performance and outstanding compaction quality to your ease of use along with perfect visibility. A WIRTGEN GROUP UncompromisinglyCOMPANY HD+ TANDEM ROLL ER S –THE PROFESSIO NA LS FOR ROAD CONSTRUC TIO N
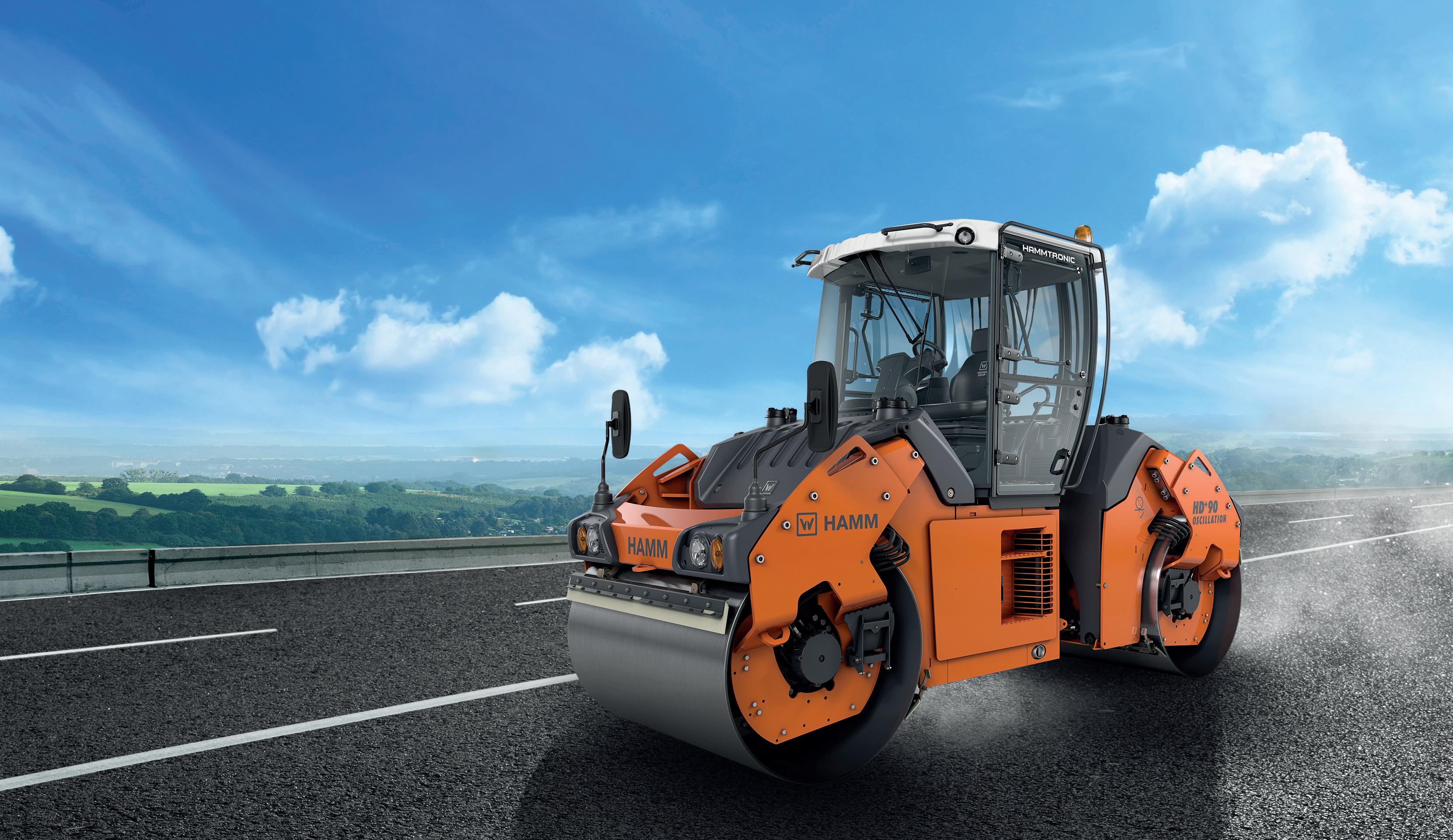
· Tel: +1 615 501 0600 www.wirtgen-group.com series tandem rollers bring high compaction construction site. Throughout, they offer impressive good
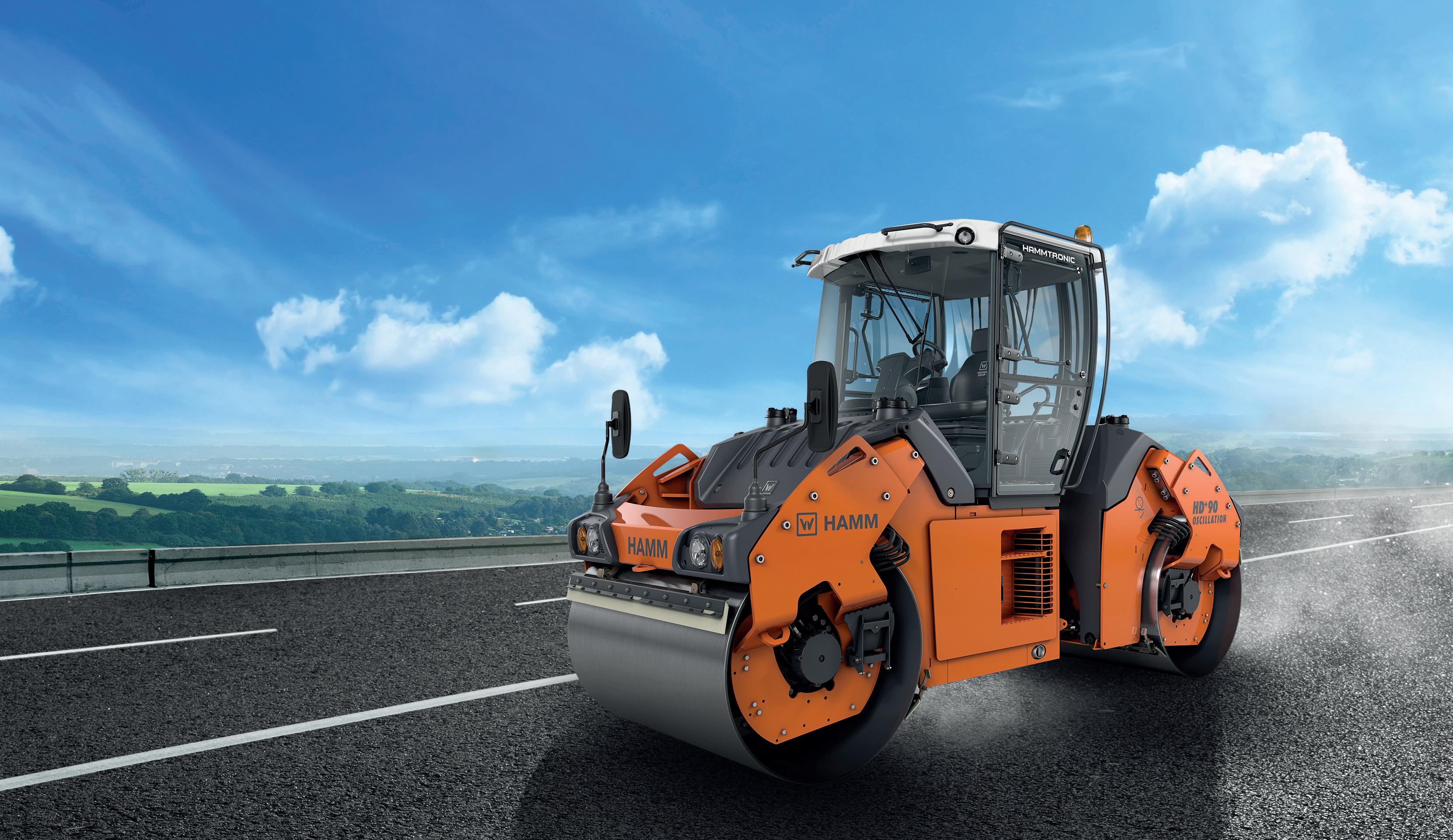
INFRASTRUCTURE REPORT
Three phases of work through Kicking Horse Canyon have similarly widened 21 kilometres of narrow, winding two-lane highway across some of Canada’s most mountainous terrain, and a $440.6-million design and build contract has been awarded to Kicking Horse Canyon Constructors for a fourth 4.8-km section. The consortium for this segment includes Aecon Group, Parsons and Emil Anderson Construction. Work is slated for substantial completion in winter 2023-24.
ROADWORKSWORKFORTHEECONOMY As inflation rises, and with it, economic uncertainty, here are five projects to watch as construction continues across Canada.
BY SAUL CHERNOS across Canada over the next few years.
16 / AUGUST 2022
STOCKADOBE/SCOTT©PHOTO:
W hen Doug Ford’s Conservative government was re-elected in Ontario this past June, that province’s on-again, offagain plan to build Highway 413, a new route across the north end of the Greater Toronto Area, received a significant boost; or so it Overseemed.theyears the 59-kilometre corridor has had its ups and downs. It has been touted for its potential to ease gridlock yet derided for the environmental footprint it would leave across a sensitive greenbelt that successive governments have pledged to protect. During the month-long campaign, pundits billed the vote as a referendum about the highway, which would skirt around Brampton and Vaughan. However, with information about species at risk living along the proposed route coming to light after the election, the project remains on precarious ground. Still, despite a range of environmental, economic and geopolitical pressures, many road, bridge and tunnel projects remain ongoing and look to keep road crews busy
While not an exhaustive list, the following spotlights and profiles in five regions across the country help highlight some of the ongoing prospects for roadbuilding that will be happening in the coming years.
BRITISH COLUMBIA: HIGHWAY 1 Construction of the Highway 99 Tunnel, rebuilding flood-damaged highways, and multiple side-road projects are keeping B.C. roadbuilders busy, but Highway 1 continues to lead the way as a multi-year road improvement endeavour. The details vary by segment, but the overall goal is to improve safety and expand one lane in each direction to two while building barriers and landscaped medians to support a 100 kph speed limit. Much of the work also includes expanding brake check areas, adding acceleration and decel eration lanes, improving passing opportuni ties to accommodate increased traffic, and enhancing active transportation. Work is being completed in phases and has been underway for nearly a decade. Segments immediately east of Kamloops are long done, and a two-kilometre stretch east of Revelstoke at Illecillewaet was finished in November 2021. Construction is also progressing on new four-laning segments in Chase and Salmon Arm.
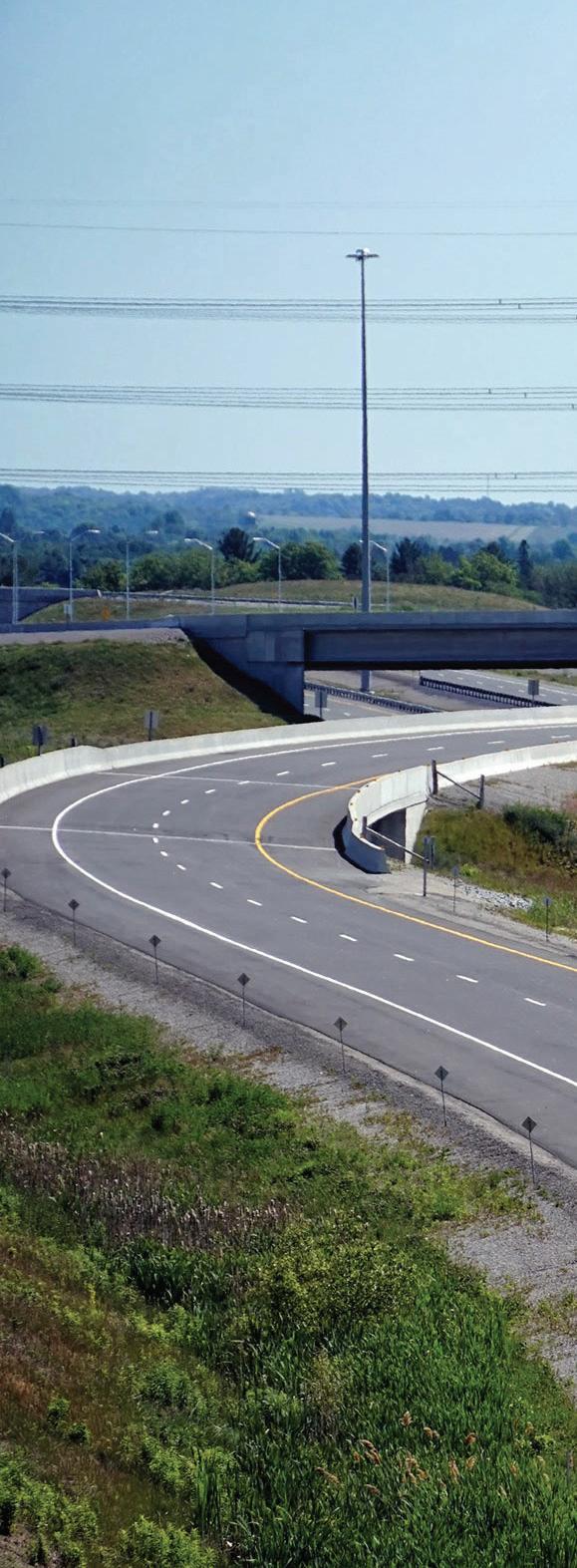
on-sitemag.com / 17
ANDTRANSPORTATIONOFMINISTRYB.C.OFCOURTESYPHOTO:
INFRASTRUCTURE
Also on tap are a 4.3-km, $243 million stretch from Ford Road to Tappen Valley Road, which will see the Tappen Overhead Bridge replaced and widened; construc tion of the new $123.7 million four-lane Quartz Creek Bridge; and the projected $224.5 million replacement of the R.W. Bruhn Bridge. Contractors for currently active projects include: Dawson Civil (Chase Creek Road to Chase West), CIF Construc tion (Chase West to Chase Creek Bridge), Springline Construction Services (Salmon Arm West), and Pennecon Heavy Civil (Quartz Creek Bridge). BC Road Builders and Heavy Construction Association president Kelly Scott calls the entire billion-dollar-plus


The lead contractor on the project, EBC Inc., started work this past spring. The project will see approaches to adja cent intersections redesigned and a fourth vehicular lane added to end the need to continually change the directionality of a middleElectricallane. networks and cabling and sewer and water lines are also being installed and renewed to improve services on the island. The new bridge will also include a lookout, which is being installed in the middle of the bridge, and the adjacent Parc Denis-Benjamin-Viger is being redeveloped. Urban furniture will feature throughout the structure. To attain the bridge’s projected 100-year life span, engineers proscribed galvanized reinforcing steel, high perfor mance coating and improved drainage systems to add reinforcement and cope with de-icing salt and freeze-thaw cycles.
“This project is a fine example of efficient economic stimulation,” says Gisele Bourque, CEO of the Quebec Road Builders and Heavy Construction Associa tion. “These are structuring projects that put several types of jobs and businesses
MANITOBA: WINNIPEG PERIMETER HIGHWAY In announcing a three-year, $1.5 billion plan for Manitoba’s network of highways, Manitoba’s Transportation and Infrastructure Minister Doyle Piwniuk emphasized the importance of the routes to trade and Whilecommerce.ongoing work on the northsouth Highway 75 corridor is designed to improve access to and from U.S. markets via North Dakota, the Winnipeg Perimeter Highway is a key project for which investment is expected to ring in at more than $346“Ourmillion.government recognizes targeted investments in roadways and bridges are foundational to our economic growth and the quality of life for all Manitobans,” Piwniuk said in an April budget announcement. “Advancing our highway network will enable market access for international, interprovincial and regional movement of goods, and will position our province to become a national transportation hub.”
INFRASTRUCTURE REPORT
MONTREAL.OFCITYTHEOFCOURTESYPHOTO:
Chris Lorenc, president of the Mani toba Heavy Construction Association, says the multi-year capital program for highways recognizes the critical role transportation infrastructure plays in economic“Manitoba’sgrowth.economy
Lorenc says Canada needs a sustainable, predictable, incremental national plan that can be coupled with concurrent provincial investment strategies focusing on efficient and cost-effective trade gateways and corridors. “The federal government has allocated $640 million to enhance trade gateways and corridors over the next five years, which is a drop in the bucket,” Lorenc says. “There’s no national plan recognizing that 66 per cent of Canada’s GDP is generated by trade.”
relies on trade for about 54 per cent of its GDP, and the Perimeter Highway and Highway 75 are two of the key trade gateways and corridors in the province,” says Lorenc. “The fact that the province has identified, or is in the process of identifying, trade as an economic-enabling instrument is important, and we’re glad that the Perimeter is getting this kind of attention.” With a new interchange at St. Mary’s Road underway, and another at McGillivray Boulevard set to go, Lorenc anticipates improvements to overall traffic flow. “These are all factors that are required to ensure you’re not start-stop, start-stop, start-stop. They will improve safety as well as the general comfort and ease with which product can be moved around.”
The Ile-aux-Tourtes bridge in Montreal and Ile d’Orleans bridge near Quebec City stand to keep work crews busy for the next few years. Of particular note, however, is a new bridge being built to replace the aging Jacques-Bizard Bridge, which dates to 1965 and is the lone road link between Montreal and Ile Bizard.
The $85 million structure, first approved in 2015 and slated to open in 2023, with landscaping and finishing work to carry into 2024, is to be located next to the existing bridge and is intended to address increased congestion by enabling 30,000 vehicles to cross the Riviere des Prairies on a daily basis while facilitating active travel with a two-way bike path and a widened sidewalk.
QUEBEC: JACQUES-BIZARD BRIDGE
18 / AUGUST 2022 package a significant investment that stands to enhance safety and efficiency. “The work continues to bolster the western trade corridor we keep talking about,” he says. “This is a critical artery. All communities will benefit from the improved, efficient, safe road system, with better access to health care, education and supplies.”
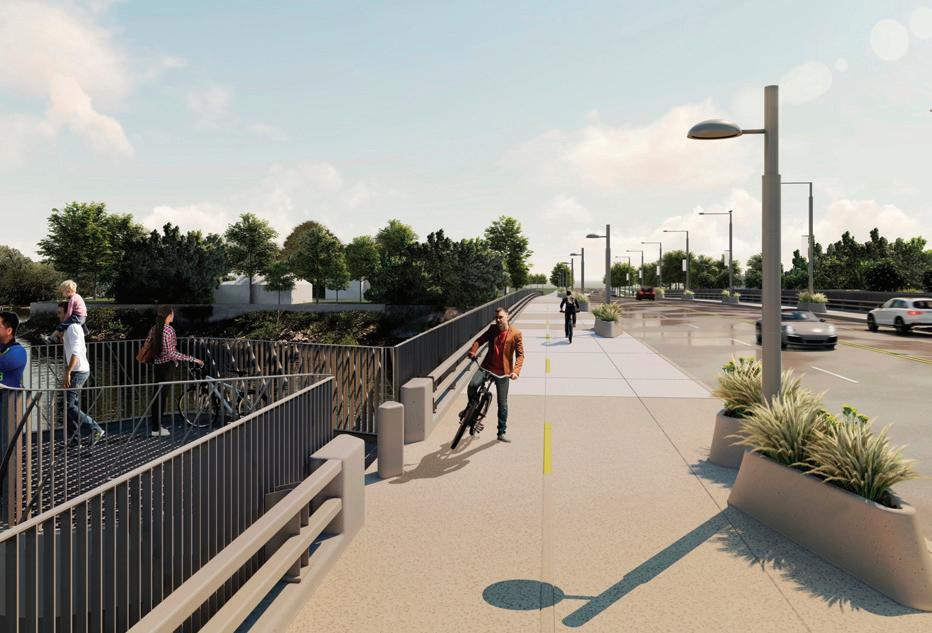
MTWO Construction Cloud, The Next Generation SoftwareConstructionof MTWO is a construction cloud solution that connects all stakeholders, processes, and data in one platform enabling better collaboration, driven decision making. With applications that address the plan, build, and operate phases of construction, MTWO is the next generation of construction project lifecycle management software. Download our whitepaper and learn how to set a sustainable digital foundation. Digital Handover MgmtFacility Prefabrication Procurement Scheduling Finance Estimating BuildingPermit QuantityTakeoff Mgmt.Site BIMModelMgmt Tender&Contract Simulation5D &ProjectMgmtCollarboration RMgmtesourceControlProject PLAN BUILD OPERATE www.softwareone.com/construction Construction Cloud
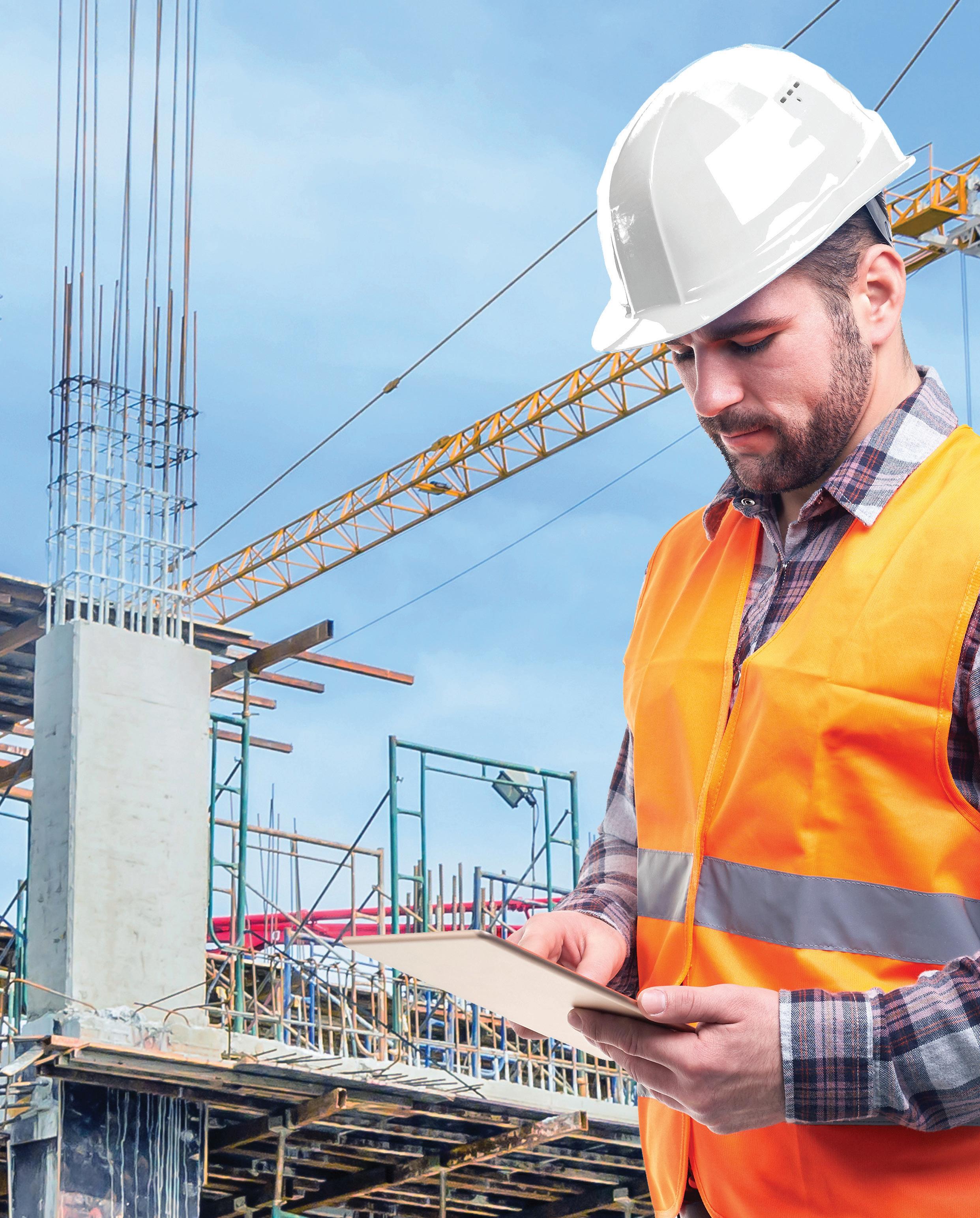
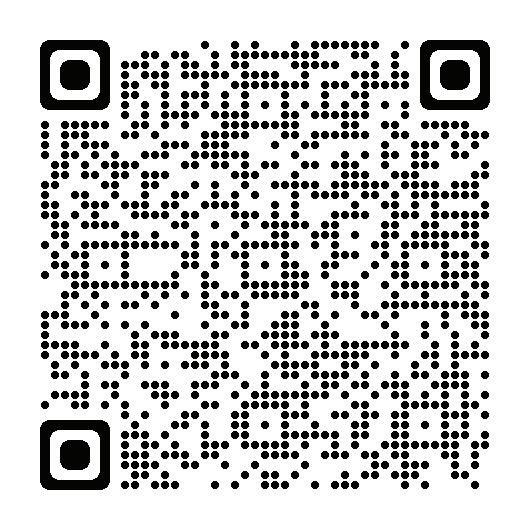
ONTARIO: BRADFORD BYPASS Highway 413 may be facing uncertainty, but road signs along Highways 400 and 404 declaring “The future site of the Bradford Bypass” suggest shovels may soon be on their way to the Greater Toronto Area’s northern reaches. While still at the planning stage, this 16.2-kilo metre route linking the two north-south highways enjoys relative support with far less opposition than what Highway 413 has Plansfaced.call for a 100-metre-wide rightof-way with four lanes and a mix of grass medians and concrete barriers.
HurdHurdsays.considers projects like this good news for Ontario’s economy. “Anytime there’s a substantial amount of work in a given area it supports local economies in addition to the provincial GDP.”
INFRASTRUCTURE REPORT
YUKON: NISUTLIN BAY BRIDGE When blasting started earlier this summer, the Yukon government heralded the $160-million replacement of the Nisutlin Bay Bridge as critical to the local community, territory, country and continent.
The bridge, billed by the government as the largest capital project in Yukon history, crosses Teslin Lake north of the Yukon-B.C. border and keeps traffic flowing along the Alaska Highway, a major artery for travel, goods and essential services. The original bridge, built in 1953, was aging, and the government wanted a modern-day structure to accommodate increased traffic volumes, including trucks bringing goods and services to the rest of the territory and into Alaska.
Project completion is slated for early 2026, and the current bridge, in service 20 metres away, will be demolished when that happens.
The Ontario Ministry of Transportation (MTO) has retained AECOM Canada to coordinate work on the preliminary design, including a provincial environmental assessment. And, with no federal assessment expected, provincial projections call for design completion by early 2023.
The new concrete and asphalt bridge was designed in collaboration with the Teslin Tlingit Council, which signed a project charter with the territory to formalize plans to minimize disruptions from construction and maximize local economic benefits.
With population growth projected to continue across southern Ontario, Hurd also pointed to ongoing work to widen Highway 401 and improve Highway 7 between Guelph and Kitchener, coupled with work on rail and other public transit systems, as vital to supporting trade and other economic activity.
20 / AUGUST 2022 to work. Starting with general contrac tors and their subcontractors, this type of project involves several specialties … and also requires the involvement of manyBourquesuppliers.”points to a clear link between public infrastructure investments and longterm economic “Investmentsperformance.inpublicinfrastructure are necessary for a healthy economy, not only in times of crisis but also in times of economic growth,” she says, noting that the construction industry is a major economic force in the province. As a whole, it represents 14 per cent of Quebec’s GDP.
Andrew Hurd, director of policy and stakeholder relations with the Ontario Road Builders’ Association, says the bypass was included in this past spring’s provincial budget and, while the post-election budget had yet to be reintroduced at press time, the government looks poised to reintroduce largely the same “Governmentdocument.projections indicate that commuters using the highway will save up to 35 minutes and that construction will support an estimated 2,600 jobs per year during construction and generate an estimated $274 million in annual GDP,”
Saul Chernos is a freelance writer and regular contributor to On-Site.
The new bridge will be 483 metres long, nearly 13.5 metres wide to accom modate heavier truck traffic, and will include two lanes of traffic, a widened shoulder for cyclists, and a sidewalk that’s lit and separated from traffic. A walkway will also be built underneath the bridge so pedestrians and snowmobiles can cross Projectsafely.spokesperson Krysten Johnson, from the Government of Yukon’s Depart ment of Highways and Public Works, says local employment is key to the project and Graham Infrastructure, the lead constructor, has committed to prioritizing hiring Teslin-based businesses, contrac tors and “Thistradespeople.specificproject will ensure a number of local opportunities and community development opportunities including involvement in environmental monitoring, gravel pit development, and the design and installation of artwork to be installed on or near the new bridge,” Johnson said.
YUKON.CA.OFCOURTESYPHOTO:
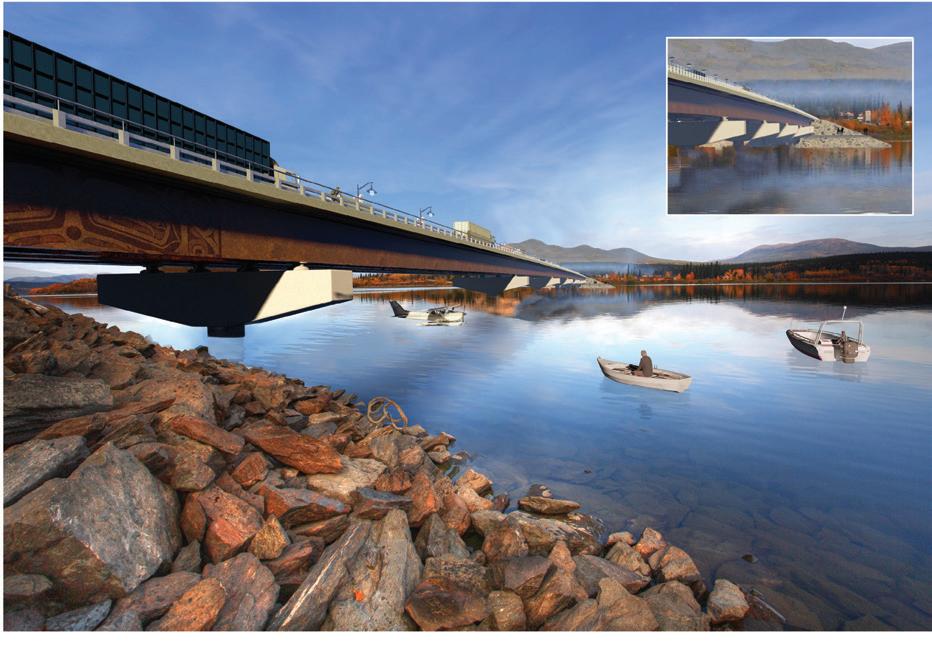
.
You goodknowroads. We know thathigh-qualitythematerialsbuildthem.
Well-built, durable roads are built by experts like you. But what about the materials that go into these roads? At General Liquids Canada, our team of experienced technicians break down and analyze virtually every aspect of asphalt-based materials at our state-of-theart CCIL & AASHTO accredited testing facility. The roads that keep our world connected start with quality materials, and with GLC you can rest assured that you’re building with the best. Learn more about our testing facility and experienced team at general-liquids.com
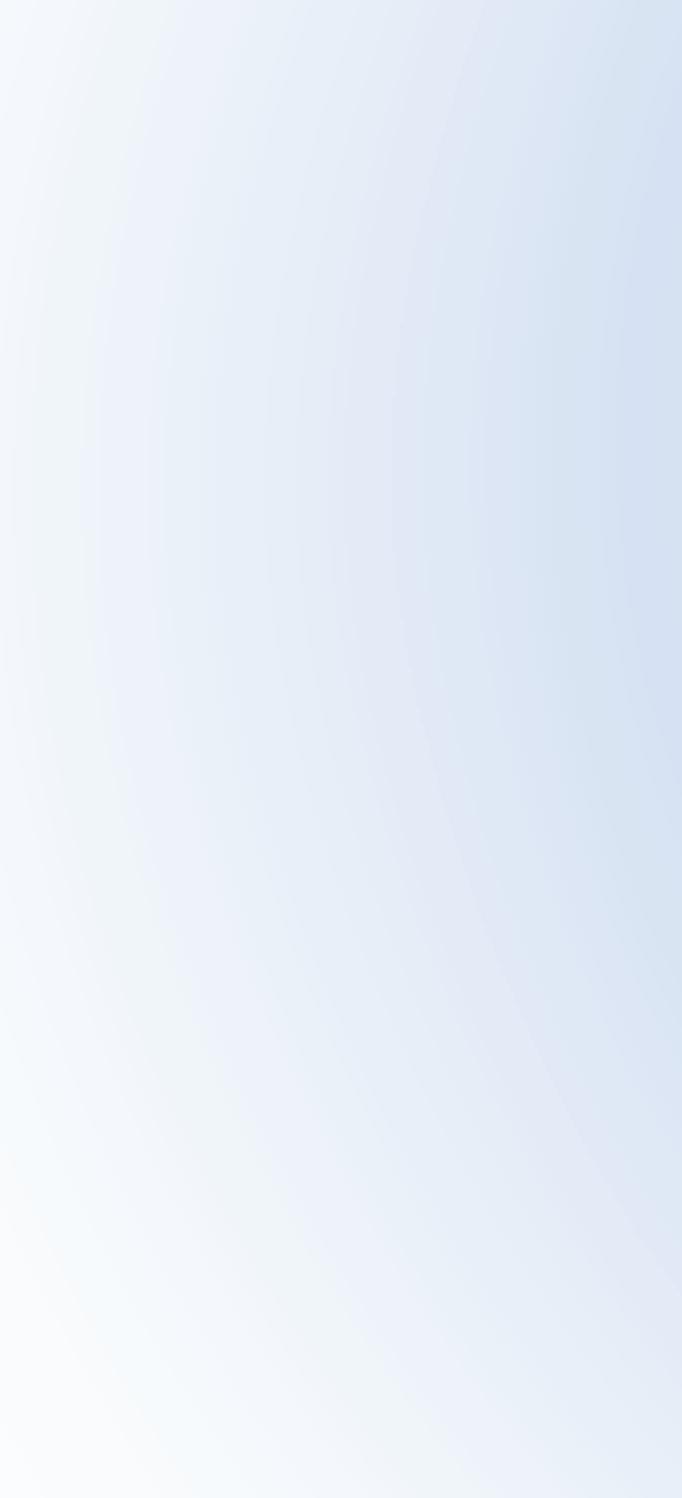
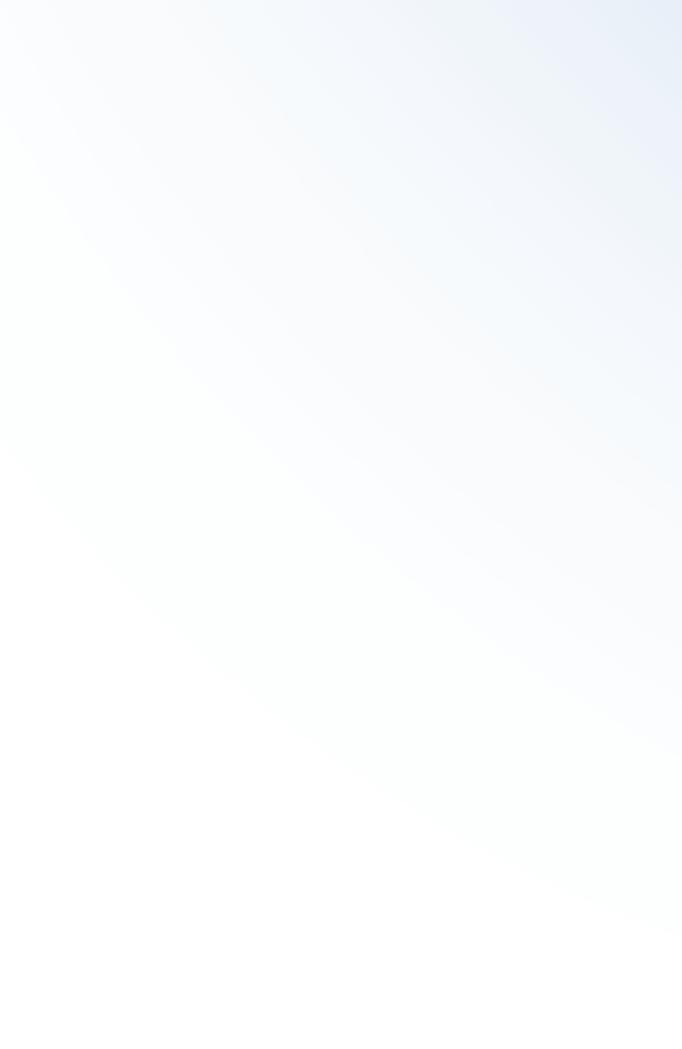

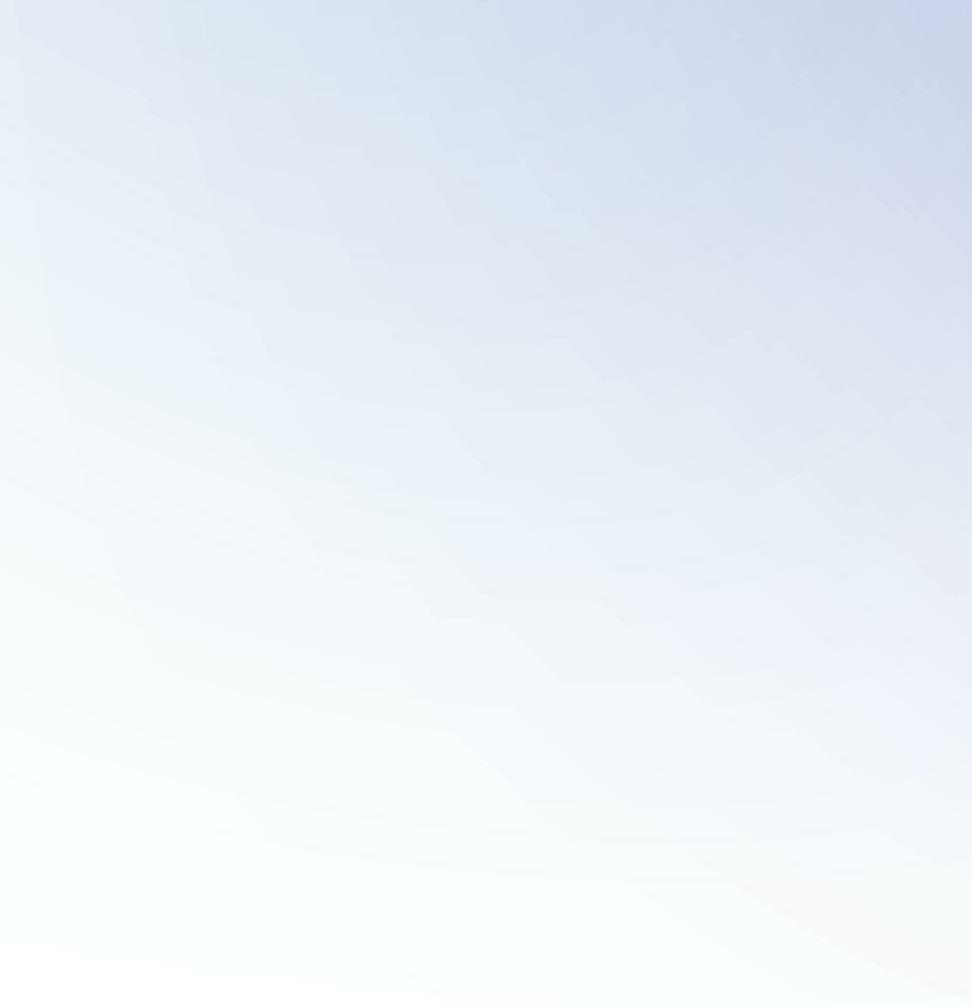
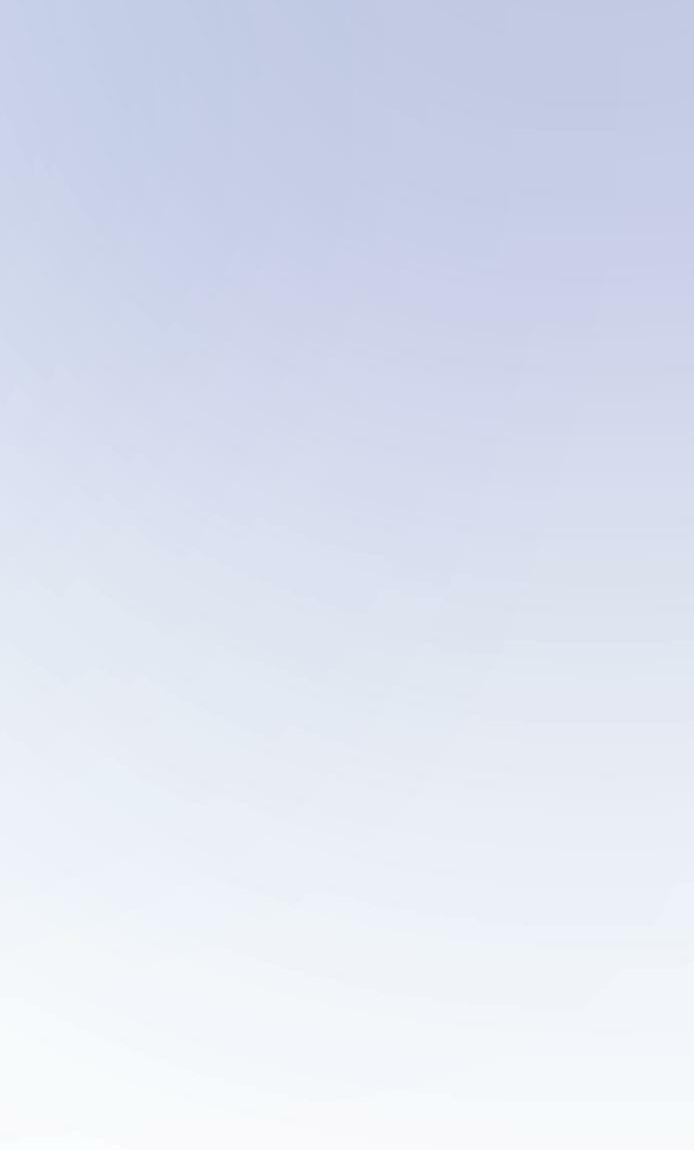
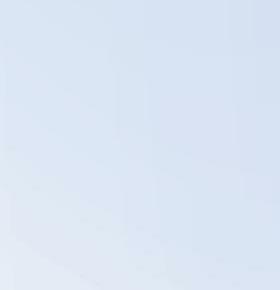
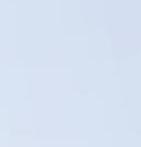
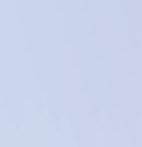
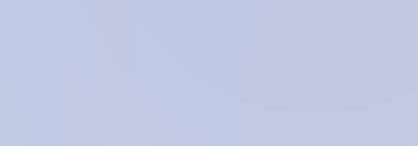
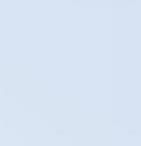
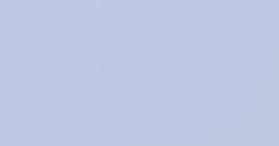
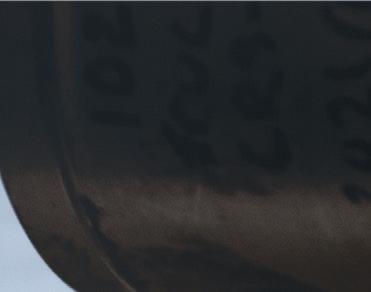
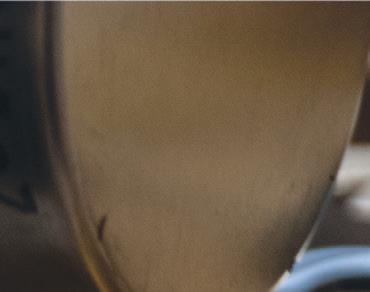
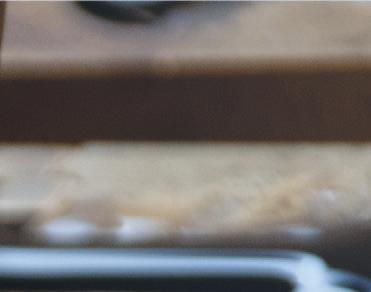

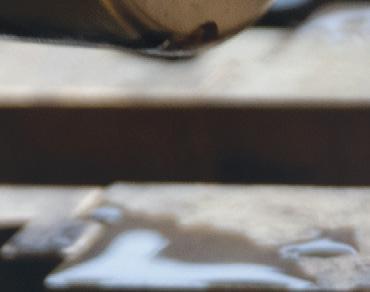

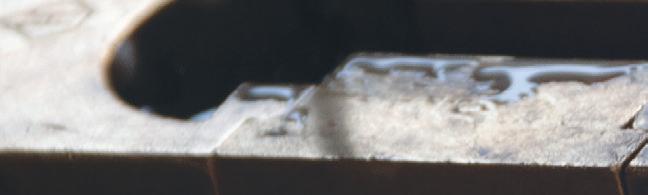
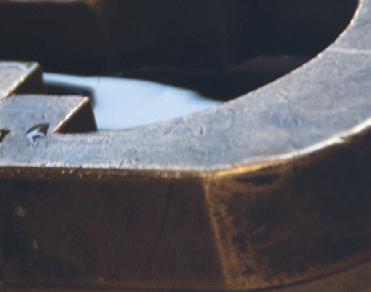
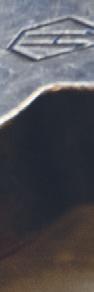


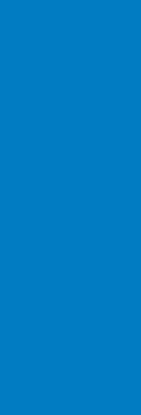


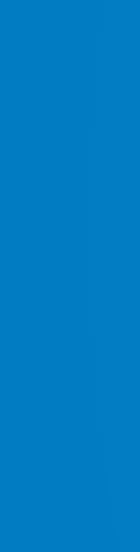
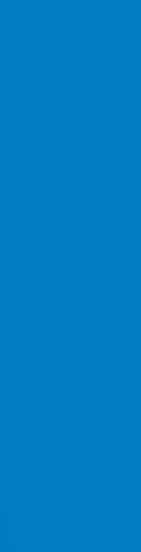
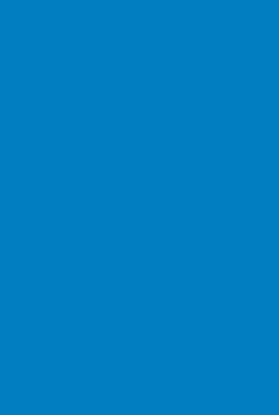
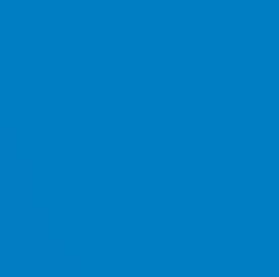
HATCH.OFCOURTESYPHOTOS:
BY DENISE DEVEAU
The most challenging construction
22 / AUGUST 2022
The design involved, among other elements, sinking a shaft adjacent to the shoreline and then mining a tunnel through rock beneath the lakebed below Lake“ToOntario.beclear, this is not any typical tunnel,” says Waher. “We’re effectively building a shaft, which is a football-field deep into the ground, a tunnel that is approximately three times the length of the Golden Gate Bridge, and a tunnel diameter [that is] the size of an average two-storey house.”
Toronto’s Ashbridges Bay Treatment Plant outfall project uses 3-D modelling to deliver results on time and within budget.
Toronto’s Ashbridges Bay Treatment Plant is one of Canada’s largest and oldest wastewater treatment plants, servicing approximately 1.6 million residents. The century-old facility discharges treated effluent into Lake Ontar io through an existing one-kilometre-long outfall that dates back to 1947. With that tunnel reaching the end of its service life and having limited hydraulic capacity, work on a replacement is underway. The city turned to Hatch, an engineer ing and construction consultancy firm with a global team members, to design the new tunneled outfall. The design process started in 2015; construction began in 2019; and the target is a completion date in 2024. Throughout the process Hatch has relied on a suite of Bentley’s 3-D modelling appli cations to ensure deliverables would be on time and within budget.
DESIGNING FOR SUCCESS Hatch and the city of Toronto evaluated numerous alternative outfall design concepts for the shaft, tunnel(s) and risers, including various construction methods such as tunnelling and in-lake dredging. The decision was made to proceed with a single large-diameter tunnel. “The preferred outfall alternative was assessed to have the lowest life cycle costs with the least environmental impact during construction,” says Kevin Waher, senior project manager, tunnels at Hatch. “It also allows treated effluent to flow by gravity from the plant, through the effluent conduits, into the shaft, along the tunnel, and be dispersed into the lake via risers from tunnel crown to the lakebed along the last 1,000 metres. Ports are installed on the top of each riser to enhance treated effluent dispersion into Lake Ontario.”
GOING DIGITAL FOR WASTEWATER PLANS
Located at Lake Ontario, Ashbridges Bay Treatment Plant is serving more than 1.5 million residents of Toronto, and is one of Canada’s largest and oldest wastewater treatment plants.
INFRASTRUCTURE REPORT
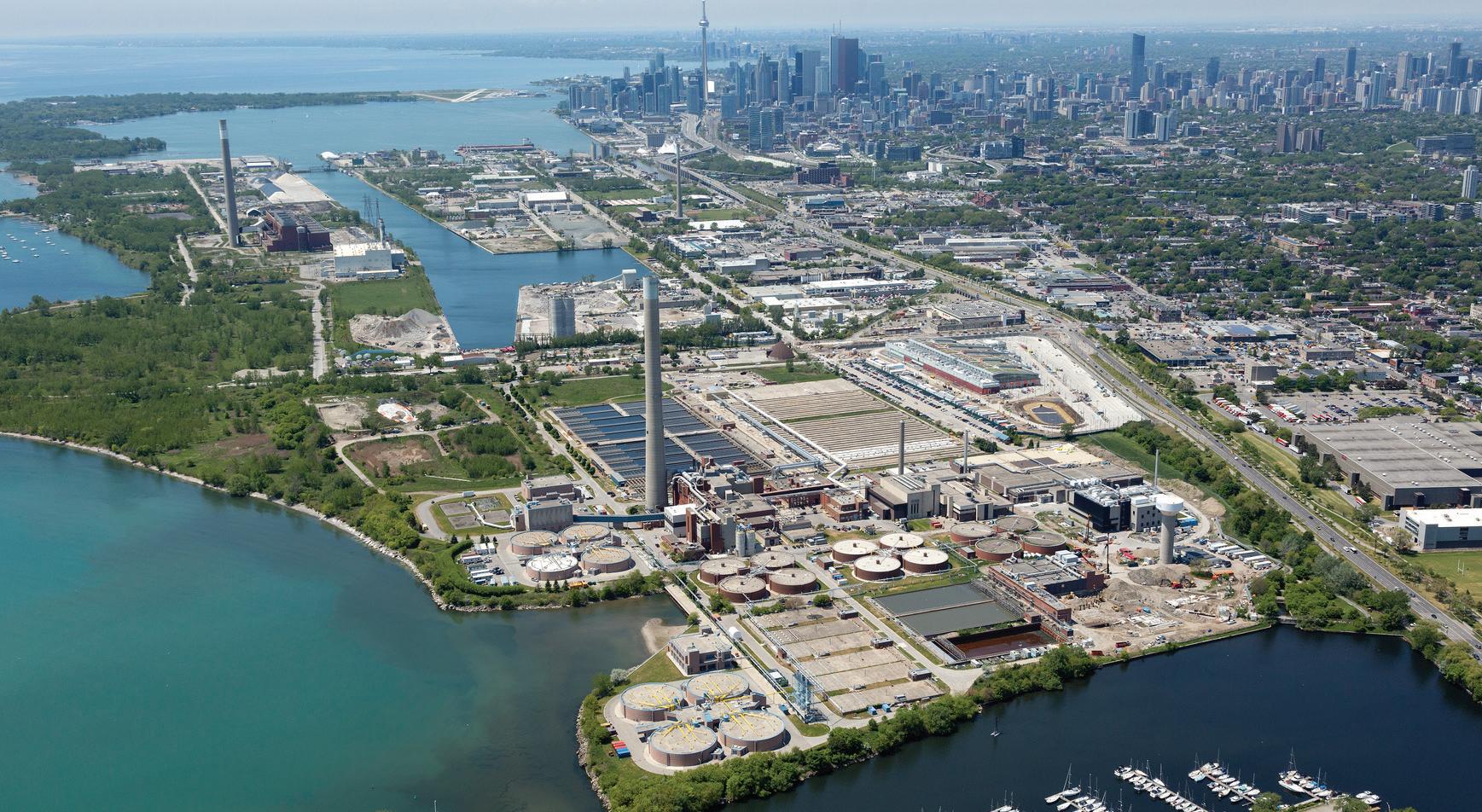
The location, complexity and scale of the project required an inte grated approach leveraging computer-aided design with engineering analysis, while considering the underwater soil and environmental features. The team used Bentley’s 3-D modelling software during the project’s design phase for all major design elements, including the effluent conduits, shaft support of excavation and final lining, tunnel liner, riser-to-tunnel connections, risers, ports, and port protection.
on-sitemag.com / 23 sequencing constraint was to have all risers installed, grouted, and tested for leaks before tunnelling below with a tunnel boring machine (TBM), explains Waher. “Without this constraint, the risk of over-drilling a riser into a completed tunnel would result in significant worker safety, property damage, schedule, and financial impacts to the outfall project.”
The design of the system was accomplished using digital models and structural analysis, conserving resource hours and allowing the the detailed design to be completed on time and within budget.
The software was key in expediting delivery, reducing costs and delivering the detailed design on time and within budget. Hatch estimates that the digital tools saved roughly 2,000 hours of staff labour, with digital collaboration and the use of 3-D models for technical peer and constructability review workshops adding to the savings as well. “The outfall project design phase was completed to the city’s satisfaction, on time and under budget, which is commendable,” says Justyna Teper, senior engineer with the City of Toronto, and the outfall project manager.
“When all 50 riser-to-tunnel connections are complete, we will demobilize from the tunnel and place concrete within the starter tunnel and shaft final lining up to the ground surface before making the final connection between the shaft and the effluent conduits. The tunnel will then be flooded before ports are installed on the top of each riser.”
Consultant (Organization): Hatch Digital Solutions: Bentley Systems
Owner/Client: City of Toronto (Toronto Water)
work will include final lining installation in the shaft, effluent conduit construction, tunnel flooding, and then the final ports and port protection installation over the next few years, adds Waher.
LEVERAGING THE POWER OF DIGITIZATION
3-D modelling also assisted in the development of each segment of the precast concrete tunnel lining (PCTL), he adds. “It allowed us to design a complete tunnel PCTL ring and then determine the ‘clocking’ or rotation of each ring, as well as predict possible tunnelto-riser connection issues and generate bid design drawings.”
Project: Ashbridges Bay Treatment Plant Outfall
Location: Toronto, Ontario
Another constraint involved probing ahead of the TBM to assess the potential for water inflows and to implement pre-excavation grouting to improve rock quality and limit water ingress into the tunnel, as required.
The software allowed engineers to create surfaces from borehole logs, including the lake’s water level and the anticipated tunnel invert. This enabled the prediction of geological boundary conditions below the lake to make significant design decisions. “This is an important design approach to mitigate potential risks of tunnel inundation from the above lake,” says Waher. “Generating the lakebed surface profile using 3-D tools also enabled us to locate the diffuser risers as far as possible from the shoreline, to improve dispersion and minimize environmental impacts within Lake Ontario, and prior to the local underwater feature called the ‘Toronto Scarp.’”
THE ROAD TO COMPLETION Construction commenced in 2019 and is expectedo be completed in 2024.“With the risers installed and the tunnel now complete, we’re approximately two-thirds of the way there,” says Waher. “The next challenge involves placement of grout within the rock above the tunnel crown to mitigate potential groundwater inflows, install rock bolts to support the precast concrete tunnel lining segments, and then strategically remove specific segments to excavate and support the final one to two metres of rock between the tunnel crown and eachSubsequentriser.”
When completed, the Ashbridges Bay Treatment Plant outfall will be the largest in Canada and one of the largest outfalls in North America. “We believe this project will act as a blueprint for future outfall and intake projects locally and across the world,” says Waher. “This is a mega project in the water industry,” confirms Sandra DiMatteo, Bentley’s director of industry marketing for water. “It compares to the prominent Tuas deep tunnel sewerage system in Singapore where digitalization and technological advancements play a key role in the development project. That’s the way progress is made, one project at a time, advancing digitalization, advancing engineering, and advancing infrastructure together towards quality of life for our communities.” Adds Waher, “Our exceptional and diverse team continues to successfully collaborate and innovate to solve construction chal lenges on this project. We are all looking forward to the day we can celebrate the outfall as commissioned and ready to receive flows from the Ashbridges Bay Treatment Plant.”
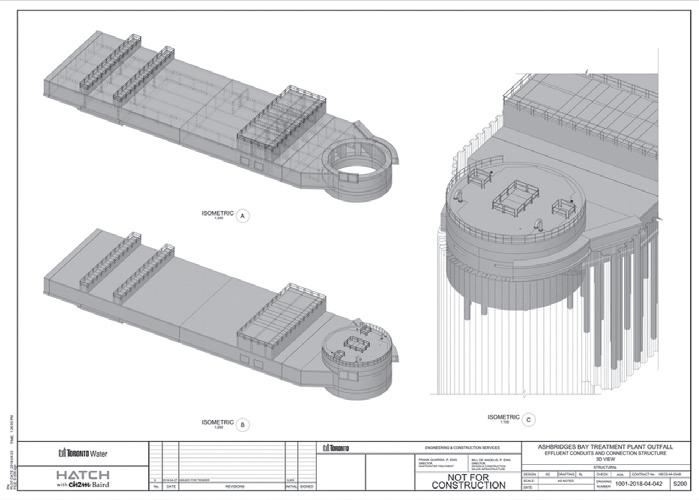
David Bowcott is Global Director – Growth, Innovation & Insight, Global Construction and Infrastructure Group at Aon Risk Solutions. Please send comments to editor@on-sitemag.com.
• Press for government support.
ACCESS TO SURETY AND BANK CREDIT
INCREASING INTEREST RATES AND PROJECT CANCELLATIONS
The construction credit crunch: A perfect storm RISK
• Qualify bids to consider rapid price increases.
• Purchasing and storaging materials in advance of needs.
As inflation, unpredictable supply chains, interest rate increases and construction project cancellations make their way through the global economy, the financial health of construction stakeholders will continue to face challenges. Those supplying credit to the construction sector are already beginning to take notice. One can expect we will be entering a phase of tight surety and bank credit. Construction stakeholders should invest in strengthening relationships with their surety and bank credit providers. Sit down with your trusted advisors and ensure you have the right credit partners to weather the future tight credit storm. It is time to strengthen your credit relationships.
INFLATION
The inevitable next step after a supply chain disruption is an increase in prices for materials in short supply. We have seen massive increases prices for key materials like timber, steel, concrete, fuel, road building materials, copper, and virtually every other construction material. To combat the impact of inflation:
• Use escalation clauses in contracts.
24 / AUGUST 2022 By David Bowcott
• Educate your customers around inflation (show hard evidence).
ACCESS TO LABOUR
The construction sector, for the most part, has very thin margins, especially when viewed in the context of the risks taken via contract over the past decade. Of concern is the rapid rise in risk over the past three years as events such as the COVID-19 pandemic and geopolitical instability created by war in eastern Europe have added uncertainty into the marketplace.
Supply of materials isn’t the only area of weakness. The supply of labour is going from bad to worse. There is already price pressure on labour due to lack of supply. This will only increase as inflation starts being raised as grounds for seeking new employment. Take all precautions within your organization to ensure you are assessing current talent needs, benchmarking cost of talent, and have tools to ideally allocate talent across your organization. It is also wise to adopt best practices to attract and retain top talent.
• Conducting detailed assessments of materials and supply chain feasibility with the owner and specifier.
• More intense monitoring of vendors in your supply chain.
• Consider paying a premium for greater certainty in pricing.
• Increase due diligence around the projects you pursue.
• Consider proof-of-financing in bid security instruments.
• Use technology to track the supply chain and price increases.
• Do a deep dive over the various sectors of the economy to determine which are likely to suffer cancellations.
The past few years, and the coming several years, will be very challenging when it comes to financial health and access to credit. Be mindful of the various impact areas driving these turbulent times and harness the power of tools and best practices to ensure each of these disruptive areas do not have a material impact on yourOnceorganization.thestorm has been weathered you want to be in a strong financial position to take advantages of the post-credit crunch marketplace.
• The use of technology to monitor the supply chain.
SUPPLY CHAIN DISRUPTION
Availability of capital, credit and cashflow is dropping at a shocking pace.
• Calls for more use of domestically manufactured materials.
The supply chain was, and continues to be, dramatically disrupted, resulting in many knock-on impacts. This disruption wasn’t just about paying higher prices to get what you needed, it was whether you could even get what you needed, regardless of price. Many best practices and solutions have been suggested to help deal with the impact, including:
Construction stakeholders need to be laser focused in the coming five to 10 years as the impacts of these risk-fuelling events continue to manifest within the global construction economy. The construction sector has already begun a journey down the road of a massive credit crunch and the availability of capital, credit and cashflow is beginning to drop at a shocking pace. As forward-minded companies, there are some solutions that warrant consideration to help mitigate credit crunch impacts.
As inflation and prices go up, so too will interest rates. We have already seen massive increases in prime lending rates by central banks globally to fight inflation. This has led many projects to undergo a feasibility review as costs related to supply chain infla tion and costs related to interest rate increases combine to put many public and private projects on hold. Expect to see more proj ects being “mothballed” or cancelled in coming months and years. To minimize your company’s exposures to project cancellations:
• Assess the financial strength of the companies you work with.
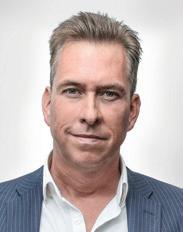
MANY JOBS. ONE SOLUTION. Cross more off your landscaping to-do list with the Kubota SVL Compact Track Loader. Compact and compatible with attachments such as graders, stump grinders, box scrapers, powered rakes and post hole diggers, it digs deep and gets the job done. It’s all in a day’s work, from a comfortable cabin. MADE FOR CANADIANS KUBOTA.CAAVAILABLE EXCLUSIVELY AT YOUR LOCAL KUBOTA DEALER
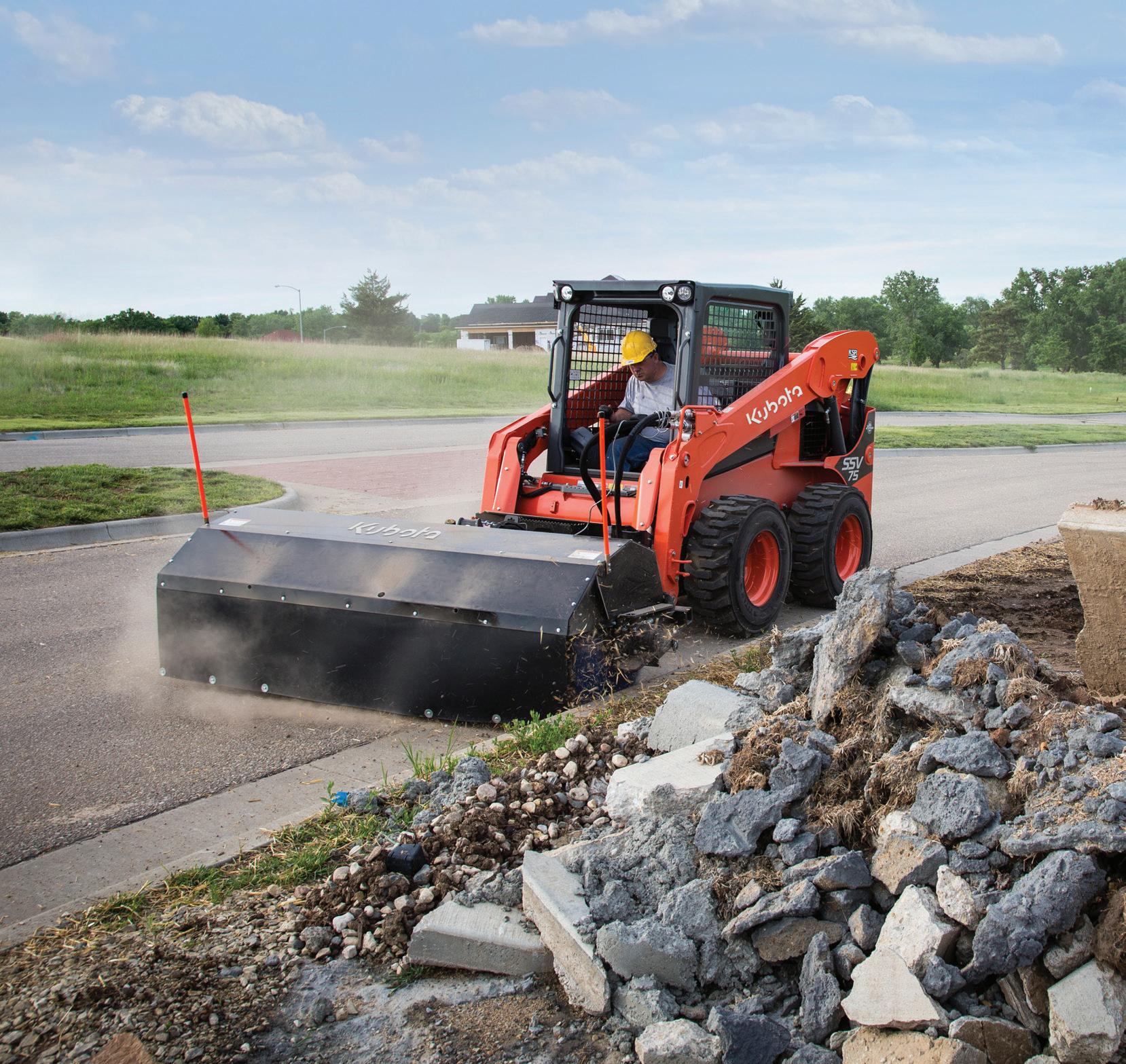
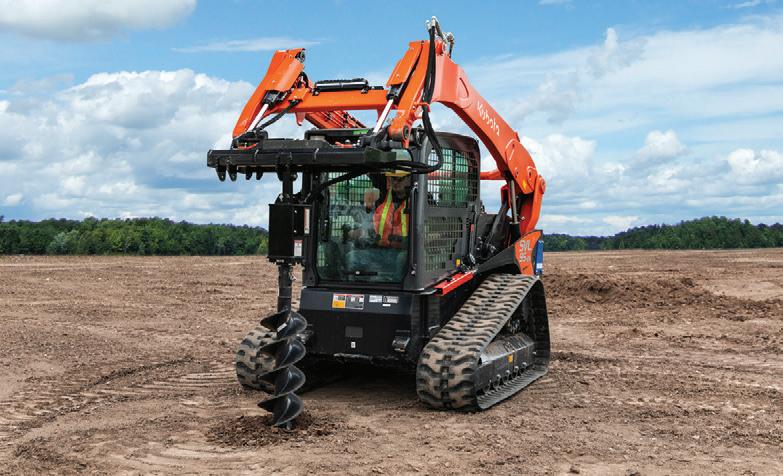
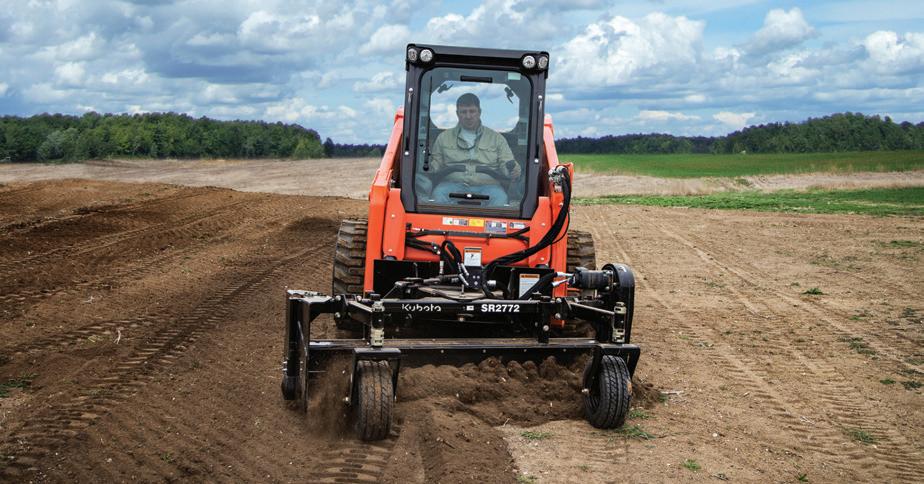
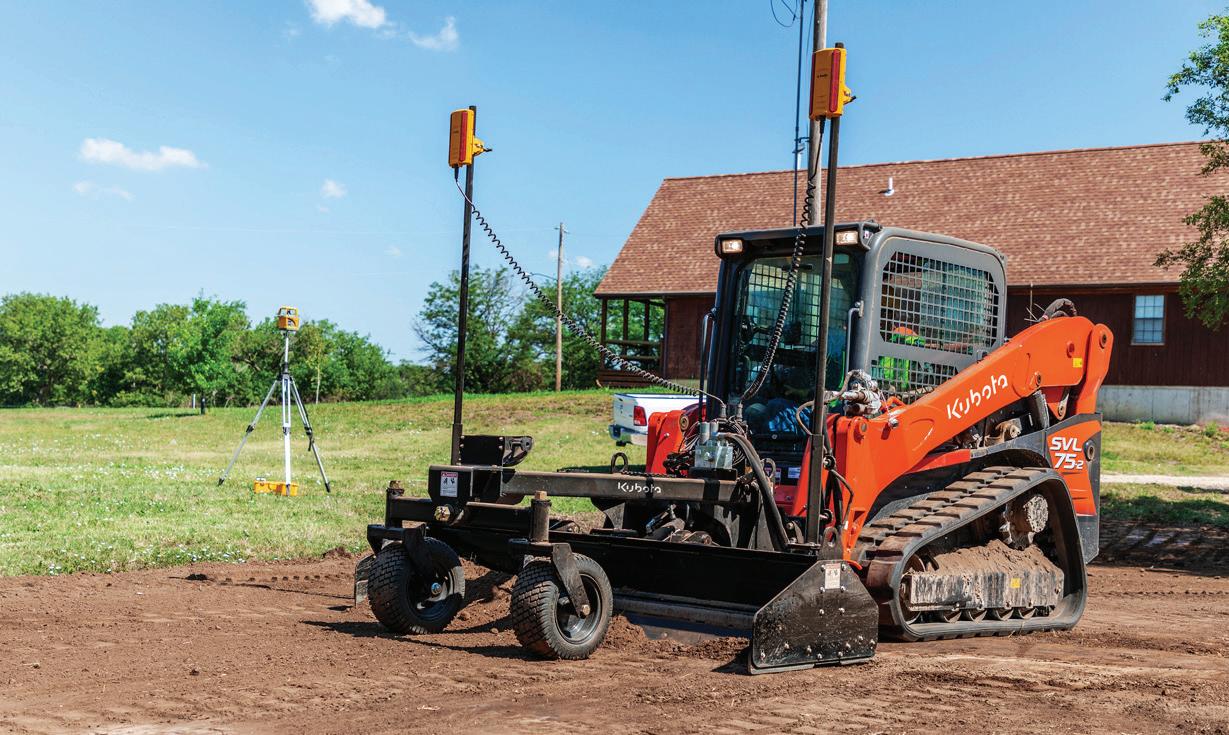





Subcontractors will embrace new technology if they realize it will also help them. When deciding on a digital reporting solution, make sure to choose a system that is easy for the field to use, that cuts down on the time it takes to complete reports and doesn’t overcomplicate the process. Field-focused software is designed for easy use on the job. It helps protect subcontractors as well as GCs, giving them an easy way to ensure their work is completed as expected and on schedule.
FAST DATA CAPTURE With the right tools, effective reporting doesn’t have to add more work. Software with mobile data capture capabilities helps SOFTWARE
subcontractorStreamlining data
26 / AUGUST 2022
subcontractors collect quality data fast with less room for communication errors than pen and paper. Some may even offer voiceto-textUsingfeatures.digital software, GCs can create and provide checklists or templates, and assign tasks to specific subcontractors, giving them clear guidelines for how their day, and their reports, should be structured. They can even add custom cost codes to timecards so subcontractors can easily track hours in a way that makes sense for their particular job or business. And, when GCs receive digital informa tion from the field through a consolidated reporting system, they can see daily prog ress at a glance without having to spend time translating handwriting or completing dataDigitalentry.
Some subcontractors may resist using digi tal project management software, especially if they are still using paper reports inter nally. Digital reporting will only help GCs if subcontractors participate, so how can general contractors encourage adoption?
RAKENOFCOURTESYPHOTO:
When reports go digital, they are more quickly and easily shared from the field. Project management software with cloud storage capabilities allows for some of the fastest insights possible, since anything uploaded to the cloud can be viewed by anyone with access to the system instantly. Real-time data can mean the difference between a massive schedule delay and a slight adjustment. General contractors who get day-to-day updates from the field have an incredibly accurate picture of how a project is truly progressing. They can closely track productivity and ensure deadlines are being met, and they can react right away when an issue develops. With digital storage, general contractors will also have access to a variety of histori cal data that can be searched and reviewed without having to sort through hard copies of files. In the event of a dispute, they can quickly locate the digital “paper trail” of reports and prove exactly what occurred on-site and when it happened.
General and subcontractors can both benefit when their reporting aligns.
COMMON REPORTING CHALLENGES
BY BRIAN POAGE
Managing large-scale construc tion projects that involve multiple subcontractors is no easy feat. In order to accurately predict a project’s status, project managers need to assess productivity on a daily basis, but without consistent, organized data, it can be difficult to gain accurate and timely insights from the field. Modern technology is designed to help general contractors streamline subcon tractor reports and make more informed decisions about budget and schedule. The use of digital construction management software allows for the consolidation of on-site updates, improvements in accuracy and simplified communications.
ENCOURAGING ADOPTION RATES
Improving the quality of data received from subcontractors takes effort, but it is easier with the right technology, and with the right understanding about how digital documentation and reporting helps both the subcontractors and GCs. When buy in happens, both have the opportunity to save time and money while providing more accu rate insights into project progress. Brian Poage is the senior construction support manager at Raken, where he helps construction companies gain better insights and build more profitable projects.
Complex projects have many moving parts and when several different subcontractors are working on the same job, stakeholders spend a significant number of hours collect ing field data. These hours rise when a GC must intervene at a granular level. Additionally, each subcontractor has their own process for completing and delivering reports, and it’s often the GC’s time-consuming responsibility to consoli date information that’s submitted in several different formats. The goal of effective project manage ment is to mitigate risks, but when GCs are spending more work hours on data collec tion and organization rather than assess ment, they may struggle to reach that goal. Consistency is key, which is aided by leveraging tools that make it easy to receive fast, detailed data from the field on a regular basis.
software improves not just speed of reporting but also accuracy. The two go hand and hand, because when daily reporting is a quick, painless process, subcontractors are much more likely to consistently provide higher quality data. With some digital reporting solutions, subcontractors can even take photos and videos and attach them to reports directly within the software.
REAL-TIME INSIGHTS
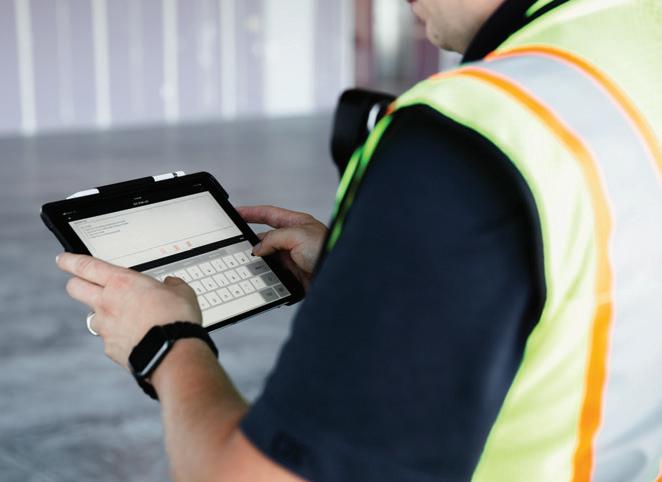
Locating Dig Safe Leaders $$$1,000500250 Be recognized and win big for safe excavation — How do you ensure safe digging on your job site? Share your best practices or initiatives and how they’re helping your crew stay safe. You could win: © 2022 Enbridge Gas Inc. All rights reserved. ENB 892 06/2022 Submit your entry and find resources at: enbridgegas.com/safeexcavationGrandprizeSecondprizeThirdprize gift card plus lunch for your crew! home improvement store gift card home improvement store gift card
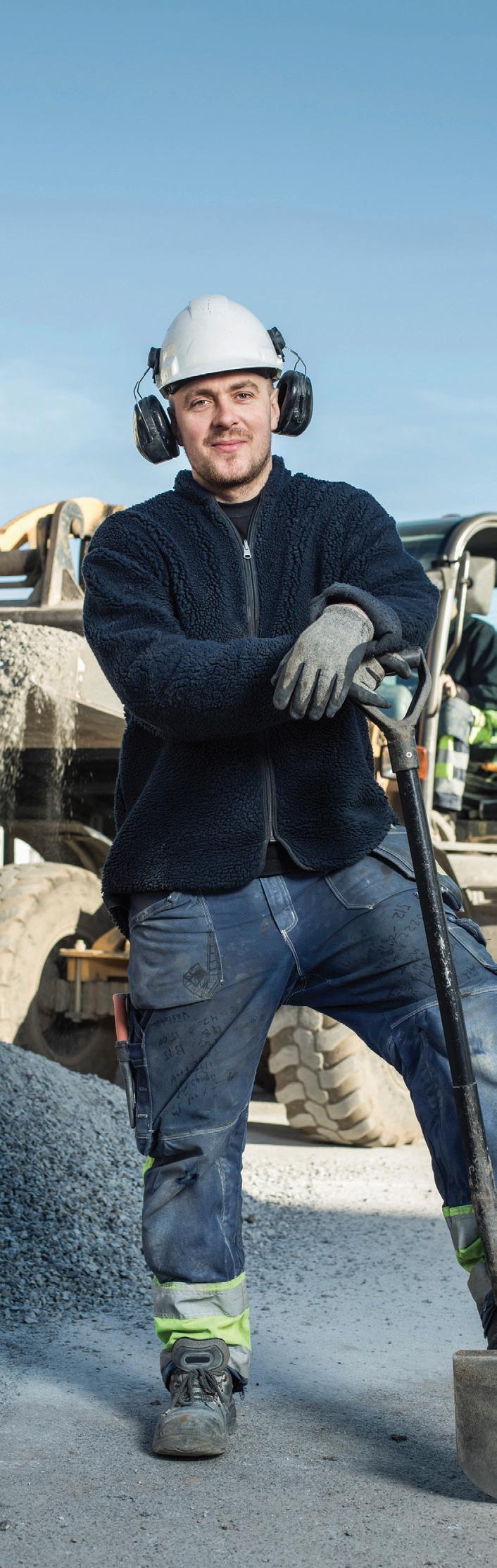
“At a high level, recycled aggregates with strict quality control should perform as well as virgin materials in most applications,” says Sanguineti. “In some European countries, recycled aggregates are being used as up to a 100 per cent substitute for virgin materials in certain concreteCurrentlymixes.”inCanada, most reclaimed crushed concrete materials are used as backfill or, in some jurisdictions, as base materials for roads.
And while the use of recycled aggregate is on the rise, the segment is still just scratching the surface of its potential in the Canadian market.
“There is momentum to evolve the industry into a more sustainable path,” says Peter Sanguineti, vice-president of Aggregates at Lafarge Eastern Canada, producer of Aggneo, a 100 per cent recycled aggregate. “Our innovation teams have identified and developed multiple technologies; processes to not only recycle materials but also reclaim, and upcycle materials, further increasing the opportunities to use in new applications and increasing the percentage of reused materials in our offerings.”
AGGREGATE
BY ADAM FREILL
INC.DEMOLITIONPRIESTLYOFKOLK/PAVIC/COURTESYDERVANDERRICKPHOTO:
28 / AUGUST 2022
As construction companies look for ways to hit carbon-neutral and Net Zero targets, finding novel ways to work with existing materials, such as pre-existing concrete structures at jobsites, is gaining interest.
“When I first got in this business, we didn’t crush a spec material. Usually, we would crush to a four- or five-inch material and then just push it into the hole, and then you would buy a spec material to place on top of it,” says Dave Wray, project manager at Priestly Demolition, which offers its customers an option to crush concrete materials on site. “Now, we crush the material right to a spec and then it’s reused on site. It helps us to not have to buy spec material because we can make it right on Whilesite.”the more hesitant in the industry may raise questions about the quality of performance of these materials, testing programs and even its use elsewhere in the world will help to ensure that the performance of the product matches to the requirements of the application.
JOBONRECYCLINGTHE
“We usually crush it to a three-quarter crush or a two-inch crush, which can be used as a B gravel or an A gravel,” explains Wray, adding that this material has been approved by Ontario’s Ministry of Transportation for use on roads—a relatively recent development. “We can use this crushed material on roads, where you never used to be able to. The spec is that you can use it, providing that you have a proper grade plan for the drainage.” To that end, his company has been involved on the resurfacing of some of the Scratching the surface on the use of aggregate sourced from demolition.
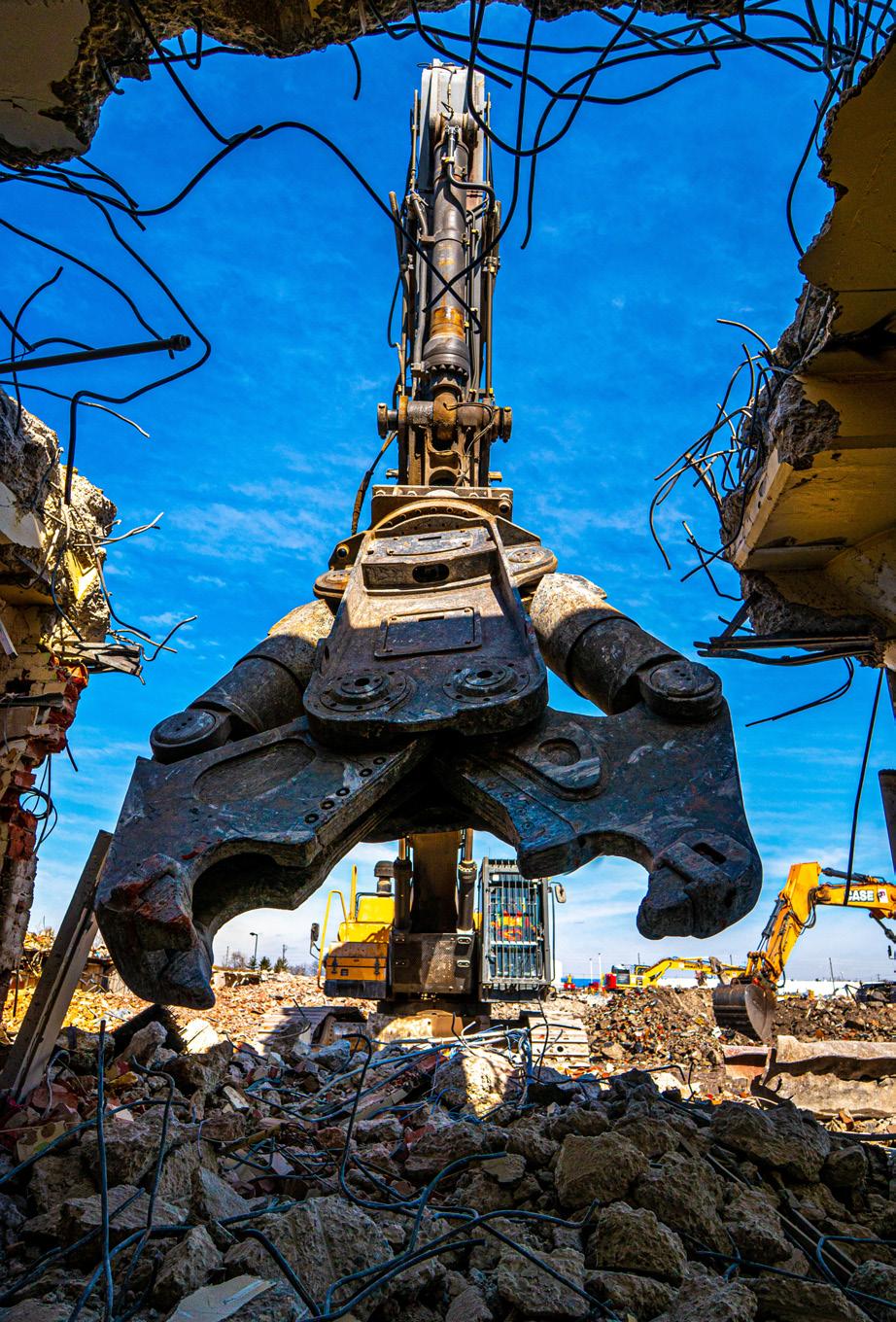
Copyright © 2022 Husqvarna AB (publ.). All rights reserved. Husqvarna is a registered trademark of Husqvarna AB (publ.). Your potential is our driving force. It inspires us to design technology that develops your professional skills. You know exactly how to get the job done – and our solutions let you to do it smarter, safer and with new levels of power. We’re proud to present a whole new range of Husqvarna DXR robots that give you much more than power. Get ready to experience control like never before. 4 NEW DEMOLITIONREMOTEMODELS VISIT HUSQVARNACP.COM TO LEARN ALL ABOUT OUR NEW DXR UNITS MORE CONTROL. MORE POWER. MORE YOU. REDEFINE YOUR POTENTIAL WITH THE
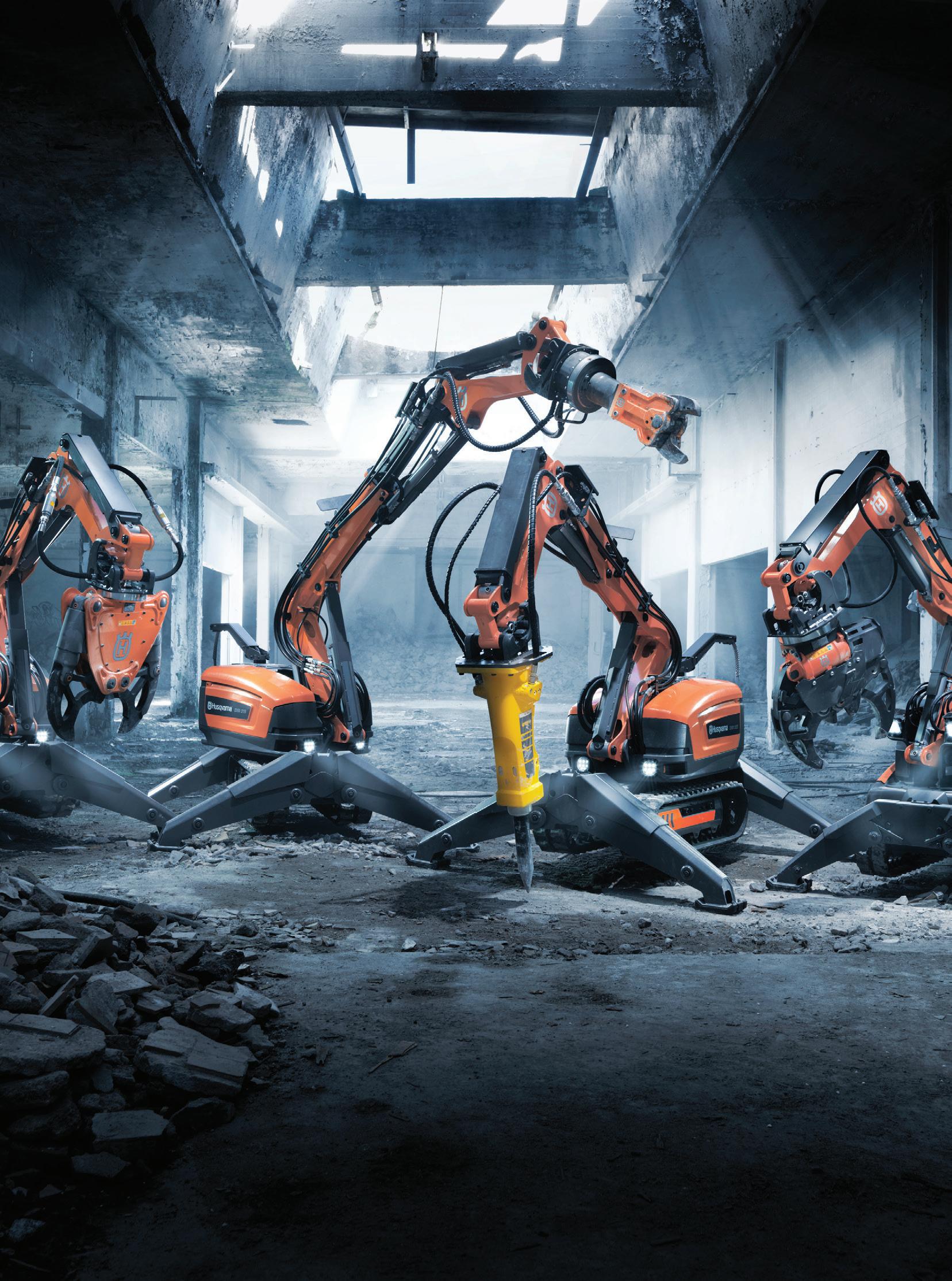
“Currently CSA A23.1 allows for the use of Recycled Concrete Aggregate [RCA] as partial or total replacement of virgin coarse aggregate in non-structural and low risk concrete applications,” says Nicolas Ginouse, technical director, Ready-mix, with Lafarge Eastern Canada. “To be able to expand the utilization of RCA in different structural concrete applications, this would require a shift in the regulatory mindset from prescription focused to perfor mance-based specifications. This would open the way to more applications using RCA concrete mixes while ensuring perfor mance and durability are maintained.”
This concern about working with quality source materials is core to Lafarge’s recycled aggregate products.
“It wouldn’t make sense to ship all the concrete off site and then turn around haul crushed concrete back, or an aggre gate back,” says Wray. “It helps to control the Withcost.”shipping being such a significant portion of aggregate costs, Priestly has even come up with creative solutions for sites too small or difficult to access with its large crushing units. “A lot of times in downtown Toronto, there isn’t the room to bring the crusher in,” says Wray. “What we have done in the past is rent a lot down by the lake, truck concrete to that site, crush it, and then turn around and truck it back to the lot that we demoed and use the crushed concrete to backfill the void.” That shorter trip makes logistics much easier, and it saves on both fuel and the associated greenhouse gases. Beyond saving on the cost of transport, the materials themselves tend to be less expensive than virgin product as well. “If you have the opportunity, or the ability to use it, it totally makes sense,” he adds. “If it meets all the specs, and you can buy it for a few dollars a ton cheaper, you’re going to save money. To me, it makes total sense in a business aspect, to use it.”
“In order for the regulators to change the standards and regulations they need reliable data from the laboratory and, more importantly, from the field, in order to make changes with confidence,” says Ginouse. “Even if we do have a lot of internal data, we should invite the infrastructure owners to actively participate in more pilot projects in collaboration with the supplier, designer and even academic experts.” “The key for increased adoption is to tie the recycled offering to an exist ing standard to bring reassurance of the performance to the end user without having the customer go through individual testing and the related risk,” adds Sanguineti. “If regulators would open the possibilities for recycled aggregates use in concrete, the RMX producer would work with its recycled aggregates supplier to develop mixes that use recycled aggregates and meet standard performance specifications for strength and durability requirements.”
Of course, for a business case to be made for expanded applications of recycled aggregate, most company owners will want to know more about its impact on a project’s bottom line. “Although Lafarge Eastern Canada has set the target to double recycled volumes in five years as part of our path to Net Zero, we recognize that in order for sustainability initiatives to be successful over time, they need to be profitable,” states Sanguineti. “The case for recycled aggregates is solid, as logistics costs are a significant compo nent of the total aggregates supply cost and recycled aggregates are typically supplied from urban depots, which are usually much closer to market than the pits and quarries located outside the city boundaries.”
Along with the ability to help a project’s budget, and the potential to deliver at a performance level comparable to virgin aggregate, the use of recycled aggregate is also compelling from an environmental perspective, especially with today’s focus on CO2 reduction.
PERFORMING IN THE REAL WORLD
His company will also consider concrete rubble from construction demolition projects but adds that Lafarge uses a thorough screening process to ensure that the recycled raw materials will deliver on the brand’s performance expectations.
“Any contaminants are cleaned prior to coming to the crusher,” says Wray, explaining that any materials that contain contaminants will not be included in the recycled products it sells to its customers.
MAKING DOLLARS AND SENSE
30 / AUGUST 2022 AGGREGATE runways at Toronto’s Pearson airport, where the existing concrete was hammered, crushed and used as base materials below the new Sanguinetisurface.says
“Making sure that the right type of feed is used in the Aggneo production process is critical to ensure its performance and consistency and is one of the main differentiating factors of our offer, and the reason behind its branding,” explains Sanguineti. “The feed typically comes from both our internal and external RMX customers as well as major infrastructure projects like roads and bridges.”
that the OPSS 1010 Standards, which are used for Ontario’s provincial highways, allow for Granular A material to be produced entirely from recycled concrete rubble, as well as up to 30 per cent recycled asphalt pavement, although he adds, “Many municipalities are still reluctant to expressly incorporate this into their own regulations or tenders, even if the application, road base, is the same.”
“In some specific applications, like cement production for example, recycled aggregates can offer incremental benefits versus virgin materials from a CO2 emissions perspective, as it minimizes emissions from the calcination process,” explains Sanguineti, adding, “We significantly reduce transportation related CO2 emissions, preserve natural resources and divert materials from landfills.”
To help foster this change in approach, it would also be helpful to have more real-world examples to truly illustrate the performance of these materials in the Canadian market.
While the financials make sense, perhaps more important is the performance of recycled aggregate, and a reputable supplier will ensure that the materials serv ing as source product is cleared of anything that could contaminate the end product so that the performance of the supplied recy cled materials will live up to expectations.
ENVIRONMENTAL CONSIDERATIONS
GROUPPOSITIONINGTOPCONOFCOURTESYPHOTO:
One of these tools, virtual fencing, has recently become an increasingly common feature in controls offerings from the major machinery manufacturers. Another technology, geofencing, is also quickly gaining widespread acceptance in excava tor circles.Whilethey may sound similar in name, there is a core, and significant, difference between the two. Put simply, geofencing is about setting machine perimeters while
PERIMETERSSETTINGMACHINEANDPARAMETERS
on-sitemag.com / 31 E
EQUIPMENT
BY NATE HENDLEY
xcavators tend to be one of the flagship machines in any construction fleet. This means that there is considerable interest from the machine owners and the oper ators any time that new technologies or features are developed that promise to enhance a machine’s capabilities. “Whether it’s road building, site devel opment, underground utilities—you name it—the excavator is typically the lead machine on the jobsite. So, the excavator operator is usually one of the more expe rienced operators on the jobsite—coordi nating this orchestra of work happening around them,” states Justin Steger, solu tions marketing manager for Site Develop ment and Underground at John Deere. Given their importance, OEMs have devoted considerable resources to devel oping high-tech tools to enhance excavator performance and safety.
How geofencing and virtual fencing improve excavator safety and performance.
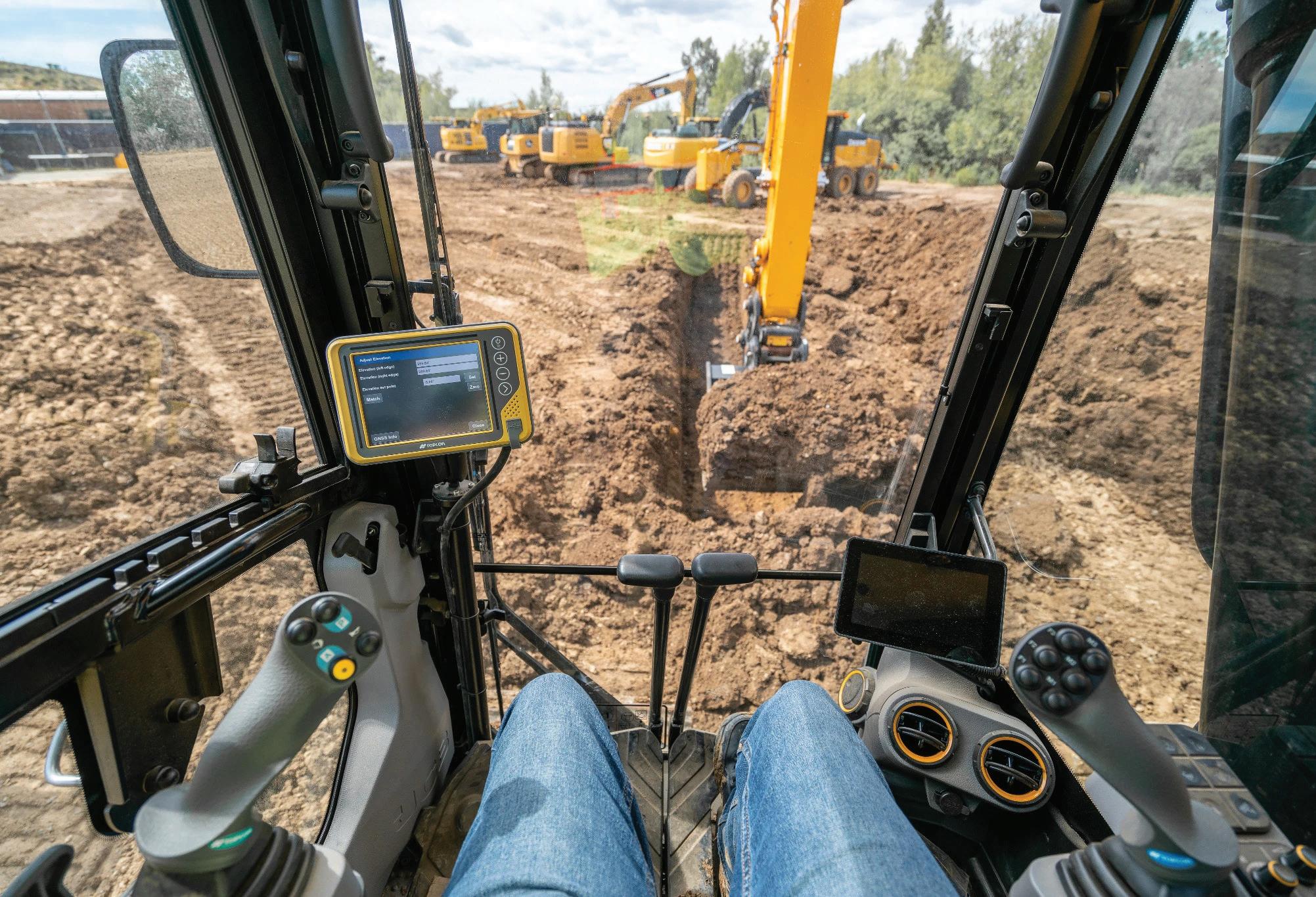
In November of last year, Topcon
32 / AUGUST 2022 EQUIPMENT
GROUPPOSITIONINGTOPCONOFCOURTESYPHOTO:
virtual fencing is about setting machine parameters.Virtualfencing allows the operator to program in height, depth, and width limits on their machine to prevent boom, bucket, arm, cab, or body overreach. If a pre-determined boundary is attained, an audio or visual alarm is activated. On some systems, the machine may also be automatically slowed down. Geofencing involves programming a “digital barrier” around a machine or worksite to track movement. “Geofencing is separate from virtual fencing technology. Geographic or geofencing is done through telematics. It’s looking at the machine GPS coordinates for location; where the machine is at,” explains Steger. “If you put a geofence around your jobsite, and a machine leaves the jobsite, the system will send alerts,” explains Mike Wehling, product manager for Sitelink3D Services at Topcon Positioning Systems, as he outlined the obvious benefits of geofencing.“Itwillalso ping wherever that machine is, once outside the geofence. You will continue to get updated position ing as where the machine is,” he adds. “If someone is hauling it to Mexico, you’re going to be able to track it.” A leader in tech-based measurement and workflow solutions for construction equipment, Topcon offers two different applications that use geofencing for differ ent purposes: Sitelink, the company’s wireless data management system, and its Tierra telematics line. In addition to preventing thefts, Topcon’s geofence solu tions can also be used for other purposes. “Sitelink uses geofencing for tracking machine productivity and tasks. If I’m hauling material from one area to another, we use geofences to define the regions,” says Wehling. “Geofencing is also used by our Tierra products for telematics information: machine hours, fuel burn, all the metrics and machine information you might get through a telematics system.”
DEEREJOHNOFCOURTESYPHOTO:EQUIPMENTCONSTRUCTIONVOLVOOFCOURTESYPHOTO:
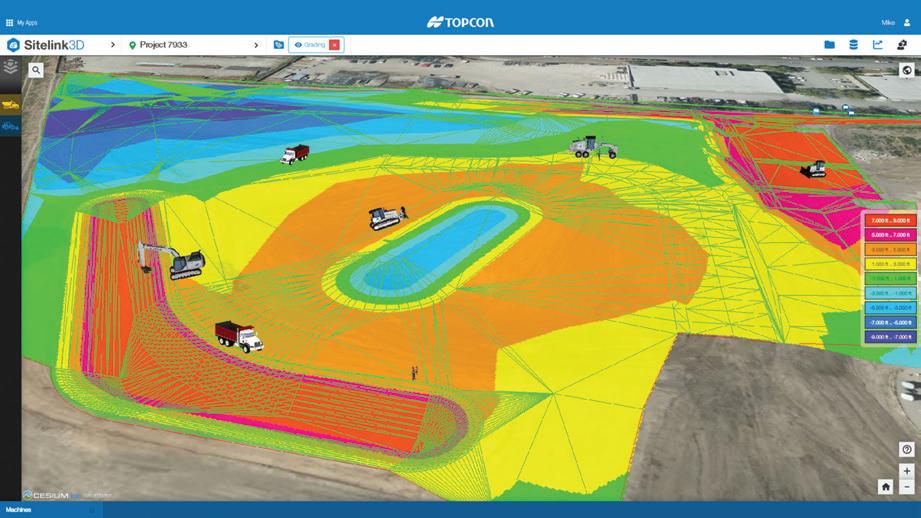
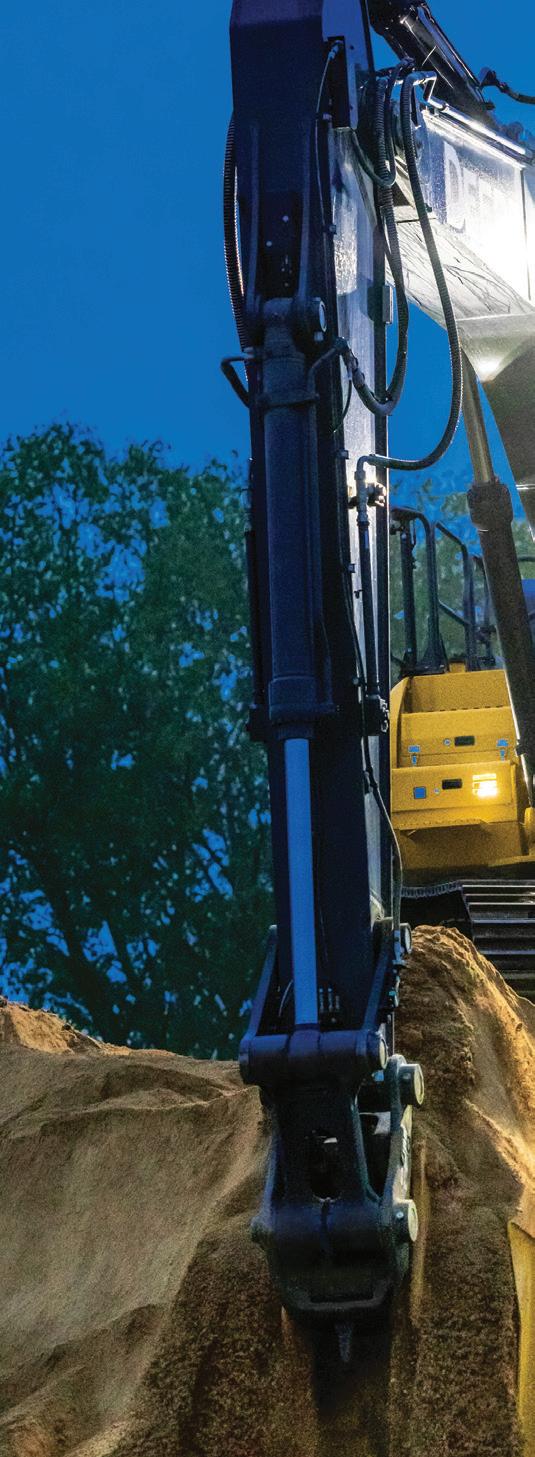
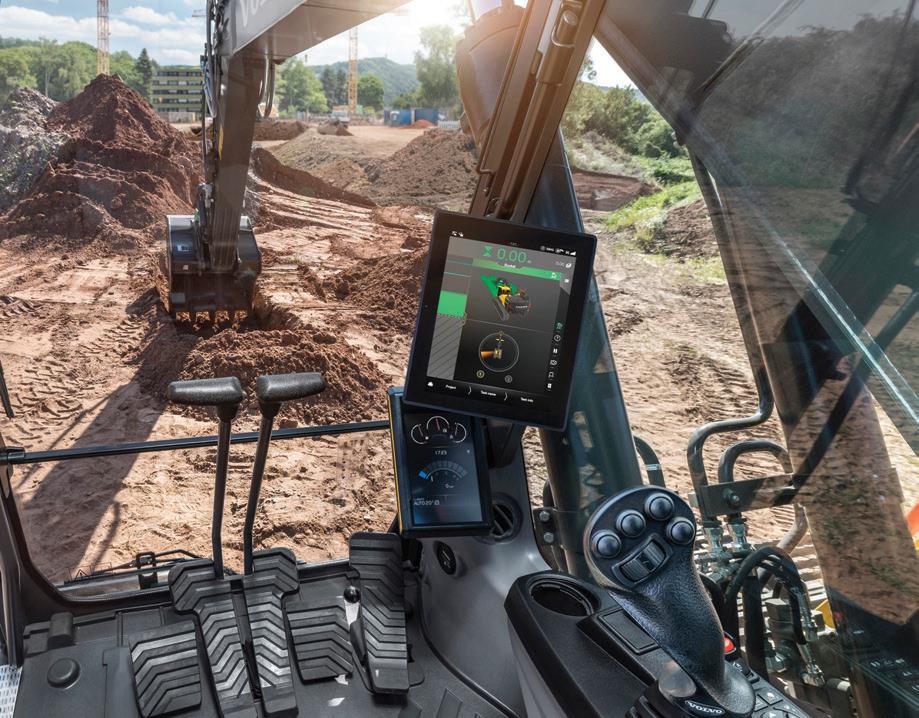
“Once the feature is turned on, it will prevent the boom, arm, bucket or whatever happens to be at the highest at that point, from breaking that ceiling.”
Lorem ipsum
Depth limits are for “customers worried about underground utilities. If you dug down to a certain limit and think there might be a gas line … it will prevent the bucket from going below that point,” he continues. Two other features, Swing Control and Swing Fence, are useful for loading applications. Swing Control entails soft stops
“If you know the power line is 22 feet high, you might want to raise your boom to a safe height. Give yourself maybe [a few feet] below what you’re trying to avoid,” says Matthew McLean, product manager for Dig Assist at Volvo Construction Equipment.
OS_BKTTires_Apr21_CWM.indd 1 2021-04-09 10:41 AM
The IMUs, working in tandem with SmartGrade, allow an operator to program the virtual ceiling, floor, wall, front and swing limits for the machine. Virtual fencing is a prominent feature in Active Control, a solution from Volvo. Active Control automatically adjusts bucket and boom movement and enables boundary limits, as Volvo calls them. Activated via joystick keys or a touch screen in the cab, boundary limits, or virtual fences, impose restraints on swing, height and depth.
WHEREVER YOU ARE, BKT IS WITH YOU BKT provides you tires that are sturdy and resistant, reliable and safe, able to combine comfort and high performance.
on-sitemag.com / 33 released MC-Max machine control for dozers and excavators. Based on the company’s MC-X machine control platform and backed by Sitelink3D, MC-Max offers automatic bucket and blade control and remote monitoring capability.
John Deere’s JDLink telematics system also includes a geofencing component. “With JDLink, one of the features in there, other than seeing fuel burn, machine hours, etc., we have geofencing capabilities that can be set through the JDLink dashboard,” states Steger.
Lorem ipsum
The company’s 210G LC, 350 P-Tier, 380 P-Tier, and 470G LC excavators are also fitted with Inertial Measurement Units (IMUs), which Steger says is “a fancy name for a sensor.”
For info: Western Canada 604-701-9098 Eastern Canada 514-792-9220
A LONG TOGETHERWAY
WHEREVER YOU ARE, BKT IS WITH YOU BKT provides you tires that are sturdy and resistant, reliable and safe, able to combine comfort and high performance. BKT is with you, even when work gets tough.
WHEREVER YOU ARE, BKT IS WITH YOU BKT provides you tires that are sturdy and resistant, reliable and safe, able to combine comfort and high performance. BKT is with you, even when work gets tough.
If an excavator unexpectedly passes through a geofence, or if it is turned on outside a pre-set “curfew,” the system will issue an alert, he adds. On the virtual fencing side, John Deere’s SmartGrade control technology automates excavator bucket and boom control and offers over-dig protection.
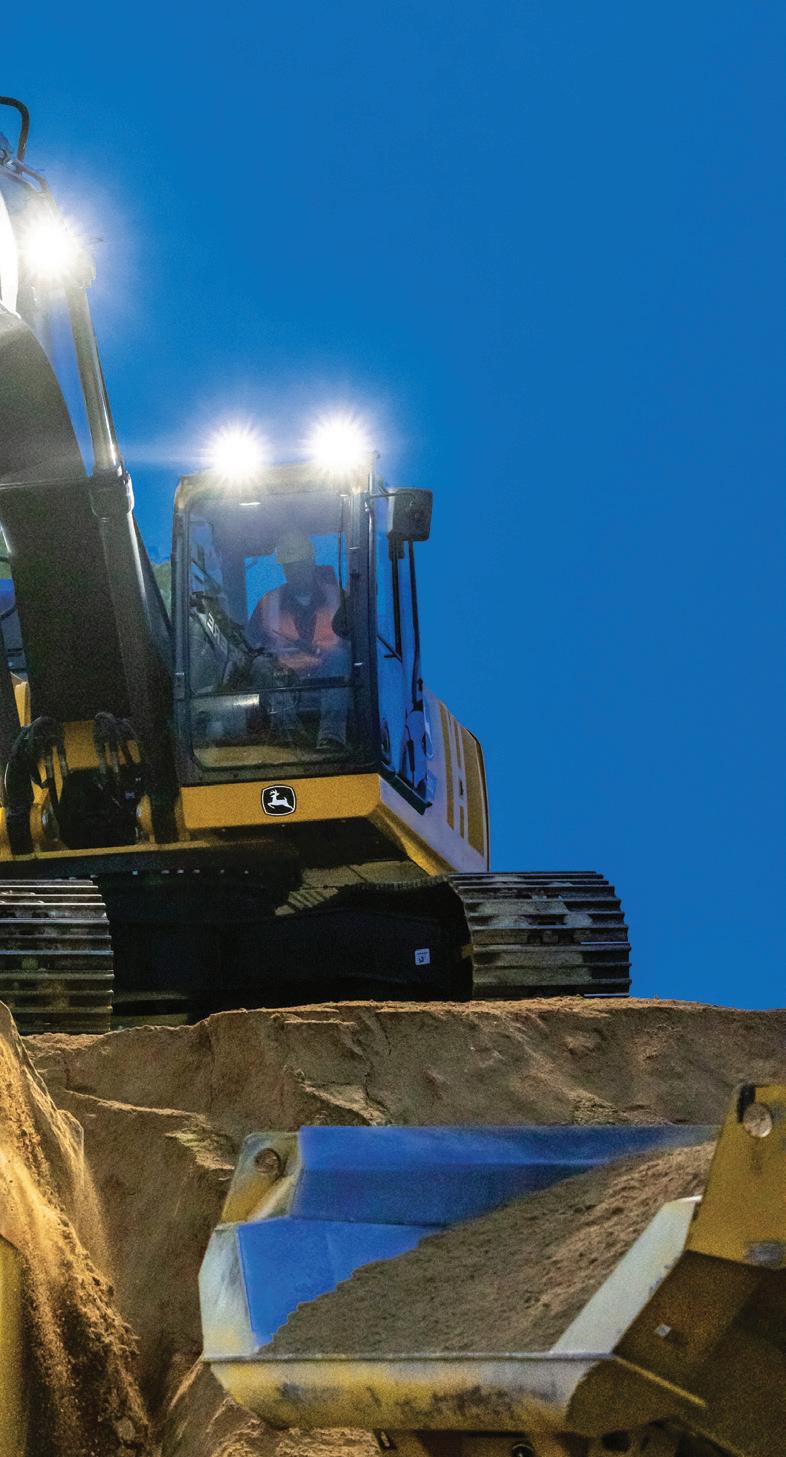
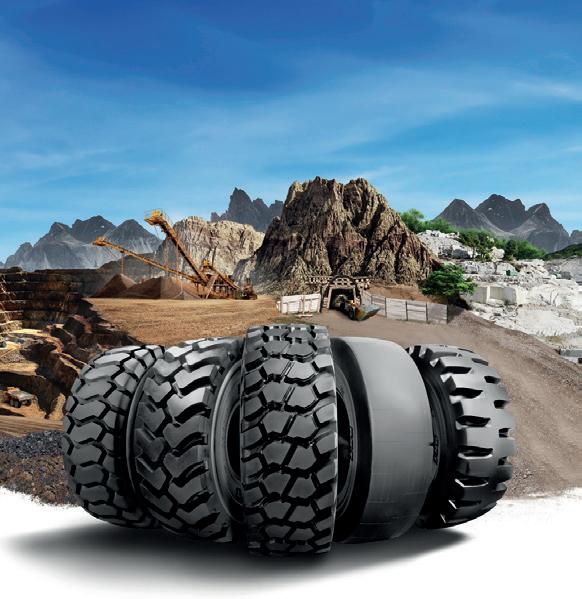
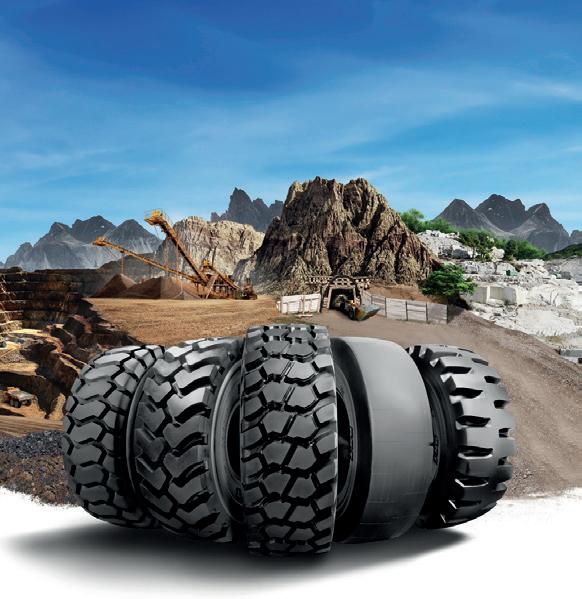
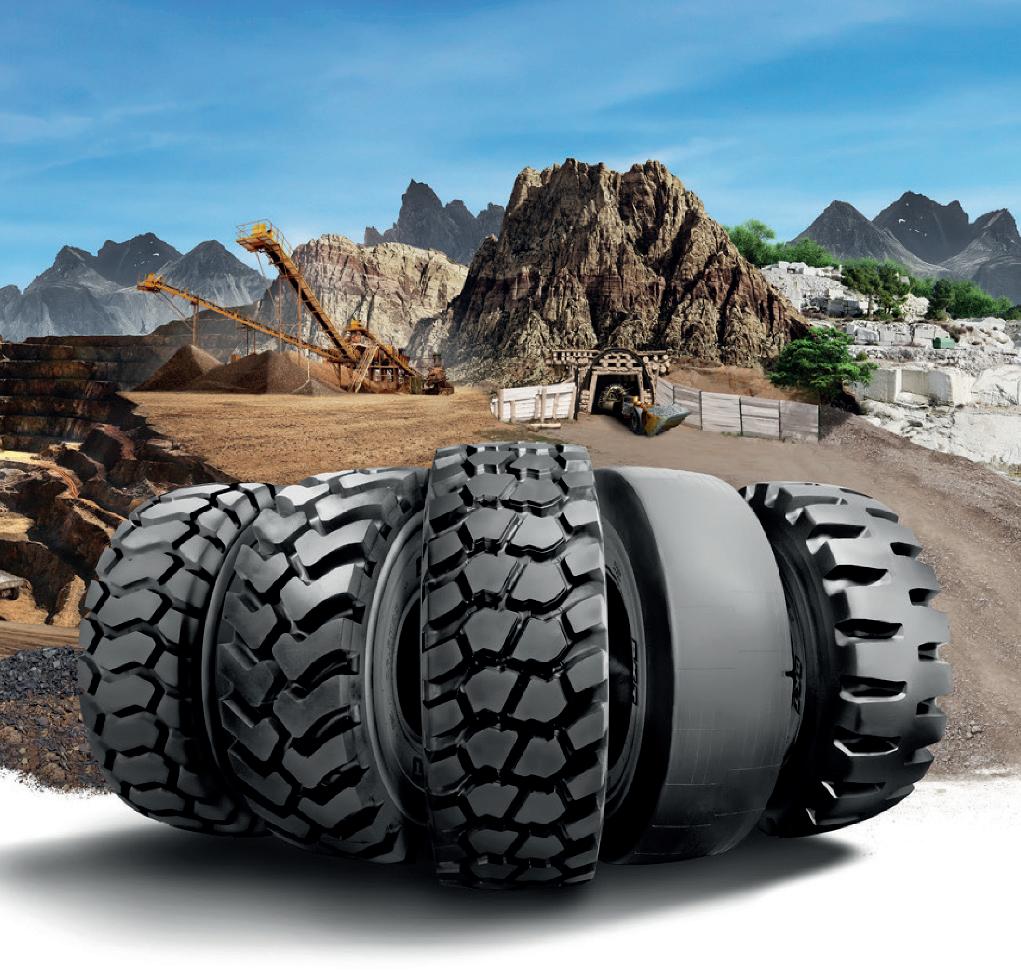
Dig Assist, Volvo’s comprehensive suite of tech tools, is available on all company excavators. Active Control is only available on five Volvo excavators in North America at present, the EC 220E, EC 250E, EC300E, ECR235E and ECR355E. Volvo plans to expand the number of excavators fitted with Active Control as soon as possible.
34 / AUGUST 2022 EQUIPMENT with swing motion automatically halted at a pre-set position. If desired, the operator can override a Swing Control stoppage, whereas Swing Fence provides a hard stop that cannot be overridden.
CATERPILLAROFCOURTESYPHOTO:EQUIPMENTCONSTRUCTIONVOLVOOFCOURTESYPHOTO:
Caterpillar’s E-Fence solution is also designed to be user-friendly, with “shortcuts within the monitor” designed to make it easy to adjust settings, adds Neal. John Deere also offers shortcuts, to streamline the process of setting up virtual fences.
Caterpillar offers its Cat Grade control for grading purposes and Cat 2D E-Fence for virtual fencing. The latter solution includes E-Ceiling, E-Floor, E-Swing, E-Wall and Cab Avoidance features, and is standard on Caterpillar non-GC excavators from the 313 to 395 models.
“The main objective is obviously safety. Often, compact radius exca vators are working on the road and there’s live traffic on one side or the other. [E-Fence] can prevent the machine from swinging into live oncom ing traffic, due to inadvertent stick movement,” states Ryan Neal, product application specialist for North America Caterpillar. “Anything we can do to prevent anybody from getting injured is our number one goal. E-Wall, E-Swing, E-Ceiling, Cab Avoidance—all of them can help that.”
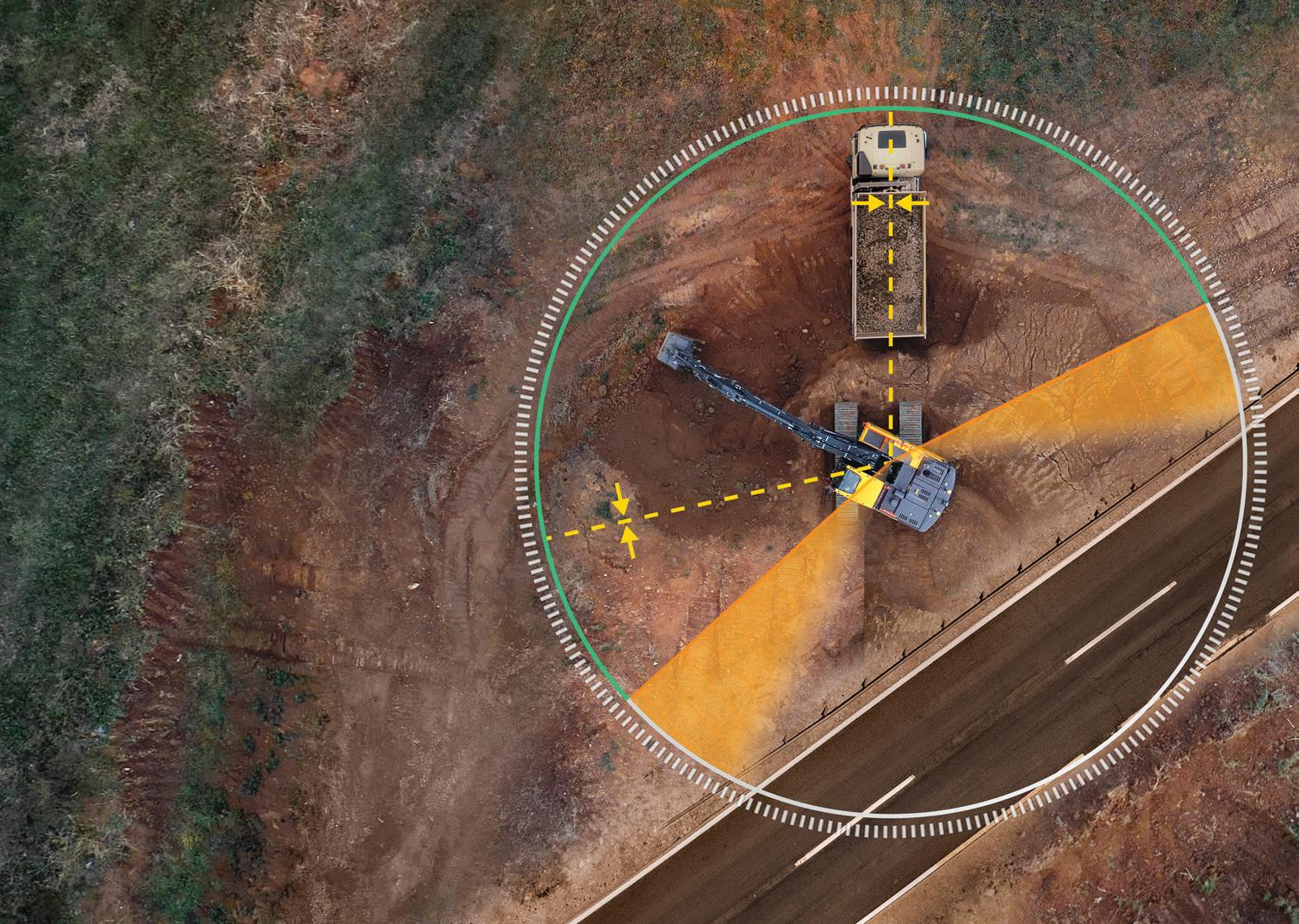
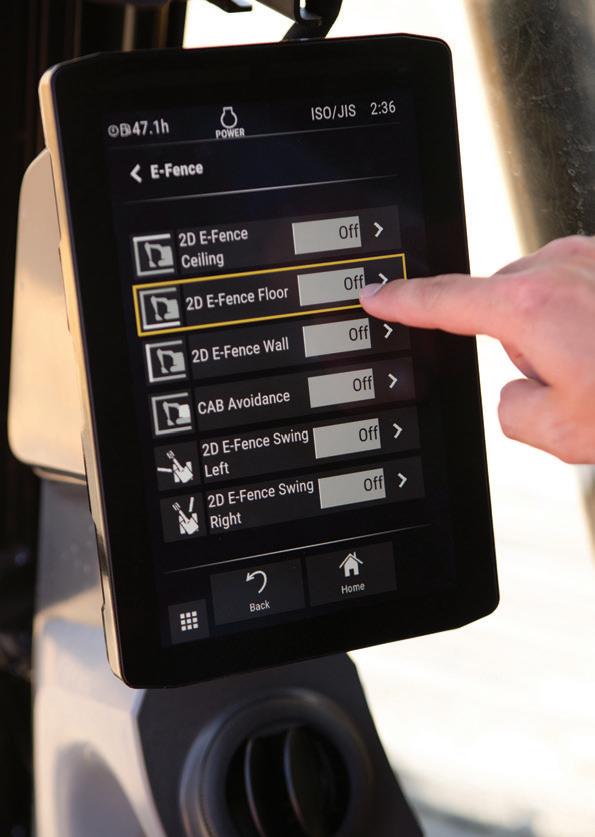
on-sitemag.com / 35 OnSite_Western_Aug22.indd 1 2022-07-22 9:56 AM “In our SmartGrade monitor, you can set shortcuts on how to get a virtual fence limit faster. That’s all found in the operator’s manual. As jobsite condi tions change, we don’t want you to have to go through multiple touch points,” saysUser-friendlinessSteger. and the ability to quickly see the set limits is also a key selling feature cited Volvo about its Active Control“Whensystem.you’re setting up a bound ary limit function, it takes up the whole screen. You have a picture of the excava tor. It depends on whether you’re doing swing, height, or depth whether it’s a top view or a side view,” says McLean. Regardless of which OEM produces the best system, there is widespread agreement about the importance of geofencing and virtual fencing. Virtual fencing is particularly noteworthy for making excavator applications safer and more productive. “If you think of everything that [excavator] operator has to monitor based on the work that’s directly in front of them, while also monitoring their surroundings, adding this technology and allowing them to set limits to be notified as they approach them, it really kind of takes a couple things off their plate,” states Steger. “They can focus less on their surroundings; the machine is doing that for them, so it’s going to improve safety. It’s going to improve efficiency, because I know I can swing until the machine starts telling me I’m getting close to something.”
Nate Hendley is a freelance writer and author, and is a regular contributor to On-Site Magazine.
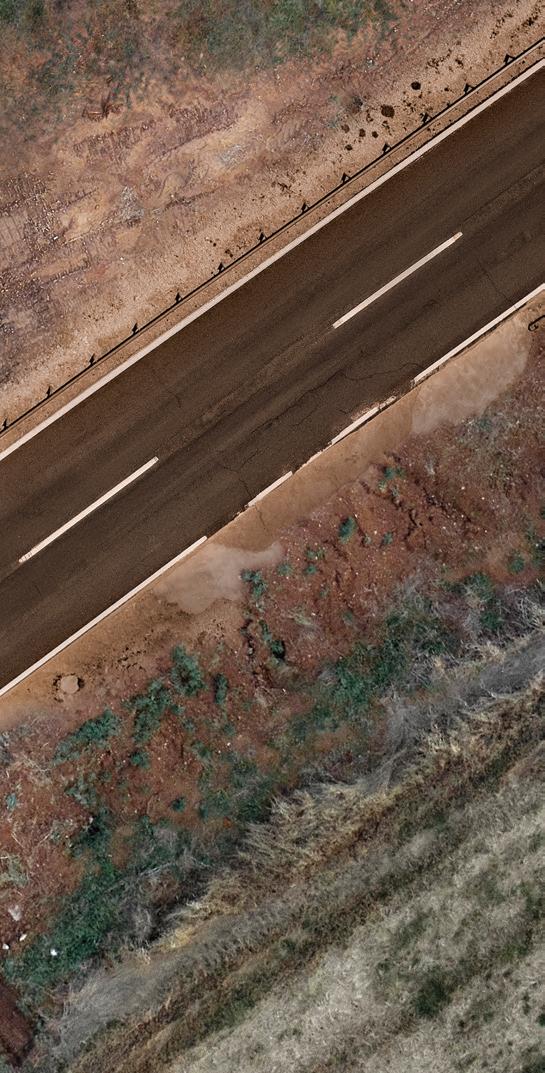
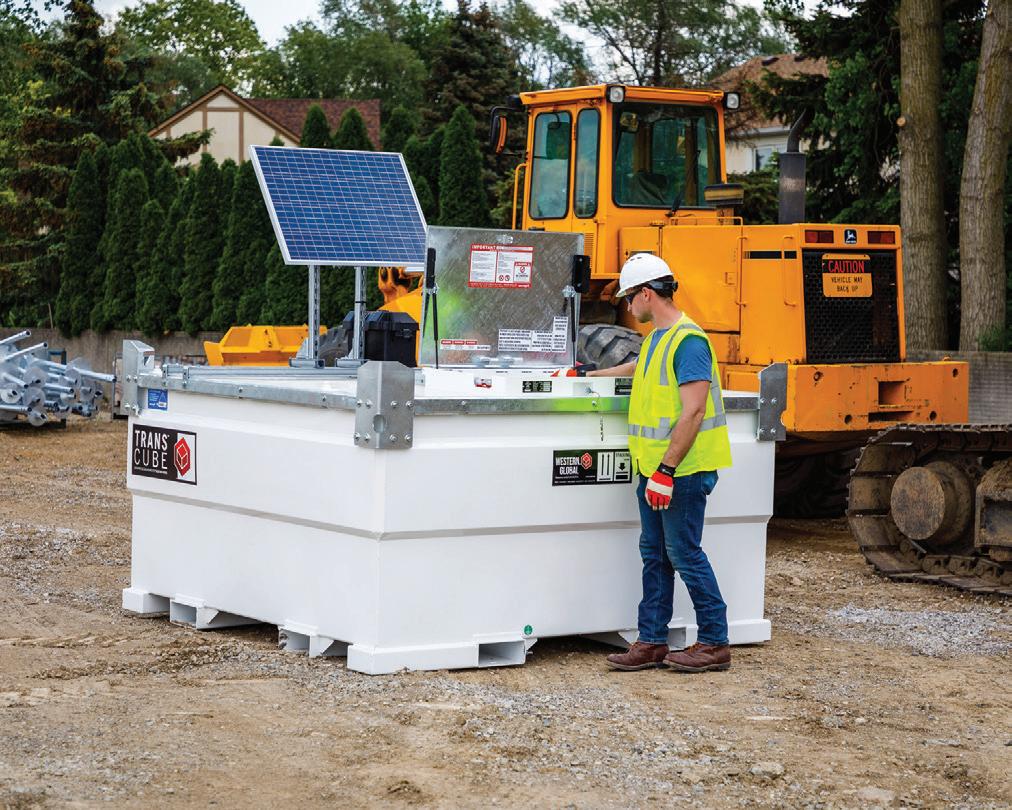
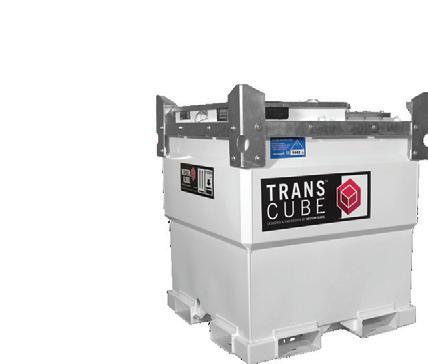
If you operate haul trucks, tractors, bull dozers or dump trucks, you’re likely fa miliar with heavy-duty oils, but you may not know that different types of heavy machinery require different lubricants. Any machinery part that rotates or moves requires lubrication to function correctly. Your choice of lubricant is an essential decision that should take into consideration engines, transmissions, differentials, final drives, hydraulic systems, cooling systems and gear reduc ers. Each of these parts requires special ized care and consideration. The environment, application and bearing speed are all important factors to consider when choosing a lubricant to maintain optimum equipment performance, and the oils required must also meet spec ifications set by the Original Equipment Manufacturer (OEM).
The environment has an enormous impact on how well a lubricant will perform. For example, one may perform well in a hot and humid environment, while another may prefer a cooler, drier climate. Other environmental factors impacting lubricant performance include dust, dirt and water. The season in which you operate is also a factor to consider. Cold winter tempera tures require a lubricant with a lower pour point, while the summer heat may demand one with higher shear stability that does not thin out.
OTHER MAINTENANCE Along with selecting high-quality, heavyduty lubricants for your on- or off-highway needs, it is also essential to look at your other fluids and product selections. This should include fuel, whether it be gasoline, diesel or biodiesel, as well as the selection of Diesel Exhaust Fluid (DEF), different types of coolant and antifreeze for a mixed fleet, and the type of grease for particular grease applications. It is also good practice to keep vehicles and equipment clean and well-organized. Proper cleaning may include regular washing, keeping a clear windshield or area for visibility, and ensuring that windshield washer fluid and DEF are always topped off.
Another important consideration when purchasing lubricant for heavy machinery is ensuring the product has been tested and approved for the applications in which you will be operating. Oils used within the HEAVY MACHINERY
ENVIRONMENTAL FACTORS
A proper maintenance schedule can help you identify a minor problem before it becomes significant and costly. Ensuring your team follows OEM guidelines and recommendations is always a good policy when beginning a proper preventative main tenanceAlongprogram.withadhering to OEM compliance, we highly encourage the implementation and use of a used-oil analysis program. Oil analysis enables a starting point or baseline in which one can follow and study trends. This type of program also allows for a scientific and data-focused approach regarding the setting of oil drain intervals. Additionally, used oil analysis programs are helpful when analyzing information from a sample report, such as viscosity, wear metals and presence of water.
EFFECTS OF IMPROPER MAINTENANCE
BY JUSTIN KRAUS
APPLICATION CONSIDERATIONS
MAINTENANCE SCHEDULES
Choosing the right lubricant Analysis is part of an effective maintenance plan.
OEMs will also have a recommended interval for changing out all lubricants. An end-user may be able to adjust these inter vals using a fluids analysis program, which gauges wear particles, and by upgrading to a semi- or full-synthetic oil. A fluids analy sis program can help construction profes sionals save on downtime and repair costs.
36 / AUGUST 2022
Improper equipment care or an unreliable preventative maintenance schedule can cause unexpected and increased equipment downtime, as well as costly repairs. A machine in the shop is unproductive and can cost a company a lot of money. Downtime can lead to an increased cost of ownership and ultimately lower profits. In addition to these inefficiencies, worker safety may also be at risk. You can easily avoid lower profits, inefficiency and safety concerns by choos ing the correct lubricant and maintaining proper equipment upkeep. If you consider the climate, applications and maintenance requirements, you’ll be able to keep your machinery running like new throughout the year. Justin Kraus is the supervisor of commercial sales in Ontario for Parkland and its lubricant brand Ridgeline.
STOCKADOBE/ZAJDATOMASZ©PHOTO:
construction industry are different from those used within the automotive industry in manyManyways.lubricants developed and formu lated for the construction or off-highway sector have undergone rigorous testing. This testing allows them to perform well in heav ily loaded, harsh operating conditions. Some have also been enhanced with Extreme Pressure (EP) additives, and addi tives such as moly in greases provide better lubrication in high shock load applications, such as pins and bushings on an excavator.

AUGUST 2022 IN THIS ISSUE: REMOVING THE GUESSWORK ANDCUTSCAN,CORE 42 Sustainable Concrete: From theory and standards to practical use. PHOTO CREDIT: ROOTSTOCKS / ISTOCK / GETTY IMAGES

Copyright © 2022 Husqvarna AB (publ.). All rights reserved. Husqvarna is a registered trademark of Husqvarna AB (publ.). More holes drilled per working hour. That’s what makes a Husqvarna core drill system your most profitable investment. When developing and improving our core drill motors, drill stands and diamond bits we look at the whole system, and at every part, to find ways to make skilled drill operators work even more efficiently and effortlessly. Whatever your demands are when it comes to core drills, it’s the focus on productivity that makes a Husqvarna concrete core drill system stand out. HUNDREDS OF CORE BIT OPTIONS TO CHOOSE FROM VISIT HUSQVARNACP.COM TO LEARN ALL ABOUT OUR CORE DRILL SYSTEMS DM 400 & DM 430 CORE DRILL SYSTEMS STRONG, SMART & RELIALBE
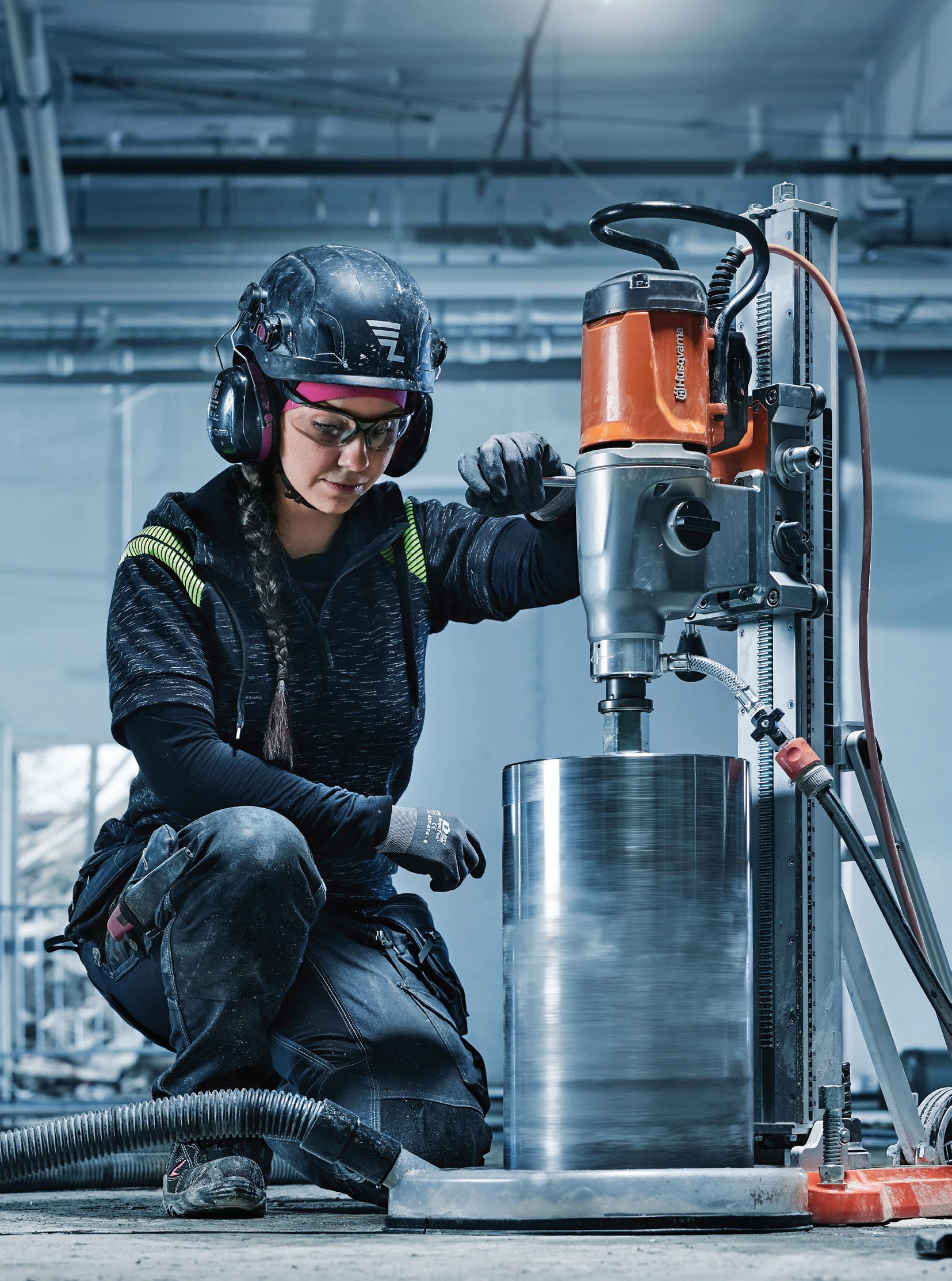
XRADAROFCOURTESYPHOTOS
BY JESSE HODGINS
on-sitemag.com / 39 CUTTING & CORING
T he most common reason to perform a concrete scan is to detect objects embedded within the concrete slab, and more often than not, these scans are done because there is a need to cut, drill or core into the concrete. And this is not an unusual task; it happens every day on a vast variety of construction projects. There might be a need to install utilities like water pipes or sewer lines, or phone and computer lines may be needed for a specific area. In these instances, a concrete scanning technician can be brought in to image the area to identify which objects are buried within the slab, and at what depths.
THE BENEFITS OF SCANNING BEFOREHAND Existing concrete infrastructure can be riddled with embedded objects. These are often planned, as is the case with electrical conduits, radiant heating lines, post-tension cables, rebar and wire mesh, but knowledge of their exact, precise positioning is rarely available, and even with a layout in hand, there is a possibility that something may have shifted during the concreteElectricalpour. conduits usually measure between 20 and 50 mm in diameter, and are commonly found within a concrete
Many troubles can be avoided when modern scanning methods are combined to provide a clear picture of what’s happening below the surface.
SCAN(ORCUTCORE)BEFOREYOU
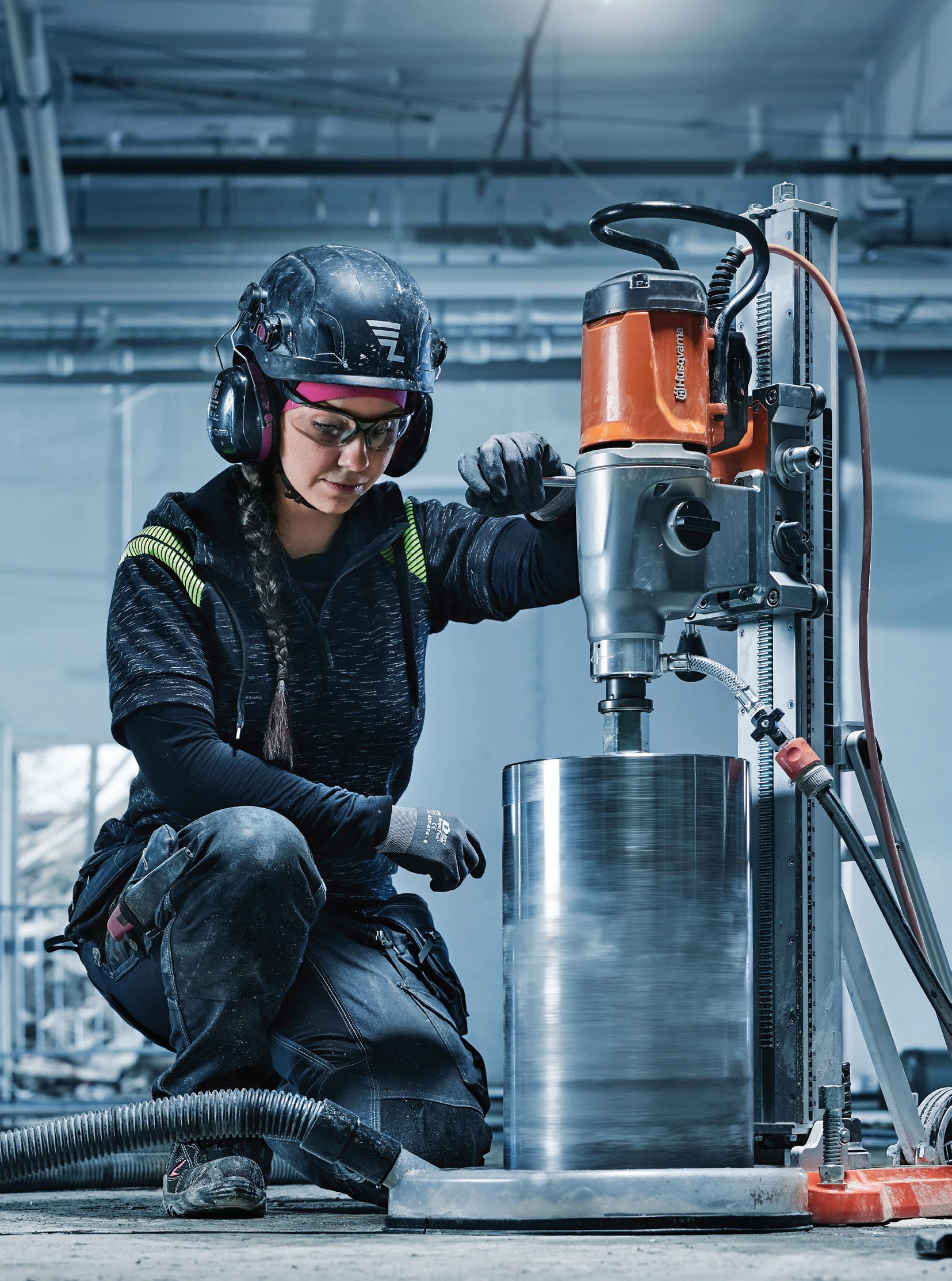

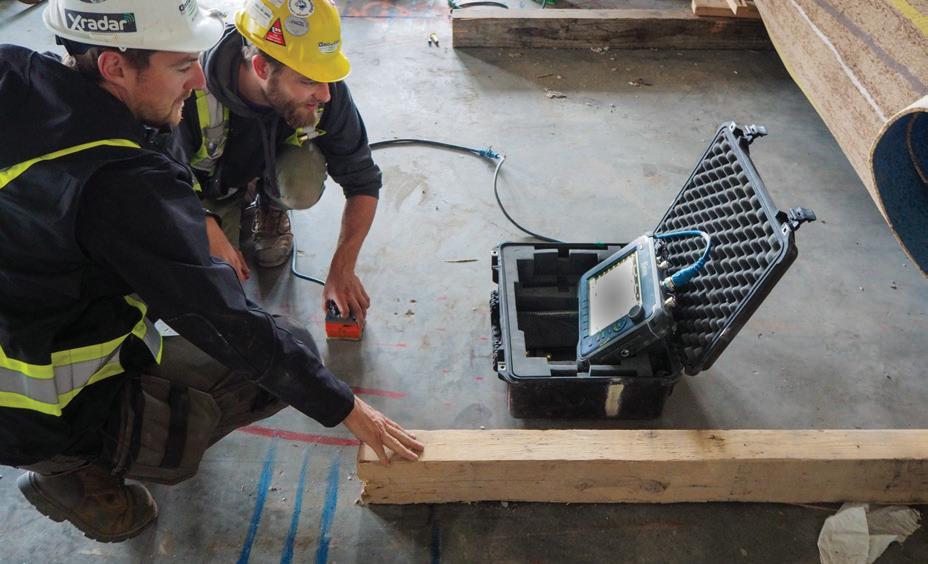
CUTTING & CORING
The most established method for concrete scanning and imaging, GPR works by transmitting high-frequency electromagnetic waves into the structure via an antenna. It’s quick, efficient and relatively affordable, but its findings require a high level of interpretation.
METHODS OF SCANNING AND MAPPING
40 / AUGUST 2022 OnSite_AdrianSteel_April22.indd 1 2022-04-06 1:53 PM
structure. If one of these conduits is severed, power outages can occur, internet access can go down, and coring technicians run the risk of being electrocuted. Cutting into post-tension cables, rebar, or wire mesh can cause significant structural damage to a building. In addi tion to potentially compromising building safety, repairing the damage can result in project delays and risingThankfully,costs. all of the above scenarios can be avoided by simply scanning before any cutting is performed. With a detailed report in hand, coring techni cians will be able to cut confidently without risking their own health and safety of the structure. Safety is one thing; efficient project planning is another. In addition to preventing damage to objects beneath the surface, concrete scans can help guide next steps at various stages of construction. Professional companies, like the one I work for, can produce accurate and detailed surveys, along with accurate as-built drawings. These comprehensive reports can detail slab thickness, reinforcement cover, spacing, rebar diameter and foundations. Structural drawings provide valuable information that allow engineers to make data-driven decisions for planning and construction phases. Raw data, maps and CAD-ready files can easily incorporate existing as-built slab conditions into structural design and analysis.Thebenefits of concrete scanning are far-reaching. Having a scan done prior to cutting and coring concrete can save time, help make informed decisions, prevent costly mistakes, and ensure safe measures are being taken.
There are several methods used to scan concrete, each with its own set of advan tages and limitations. Known throughout the industry as non-destructive testing, the most widely used methods are Ground Penetrating Radar (GPR), Ultrasonic Pulse Echo (UPE), X-ray, Half-Cell Potential (HCP), and Ultrasonic Pulse Velocity (UPV). Ground Penetrating Radar
Ultrasonic Pulse Echo UPE is able to provide accurate readings at larger depths than GPR. It is an advanced imaging technique that can vividly map out honeycombing, large cracks and voids. This method can determine the thickness of reinforced concrete structures up to eight feet in depth. It runs up against issues when testing on rough or unfinished concrete, however. X-ray Using X-ray to scan concrete results in a direct image of the subsurface. It provides a great snapshot of the objects within the slab but is restrictive, expensive and can be very time-consuming.
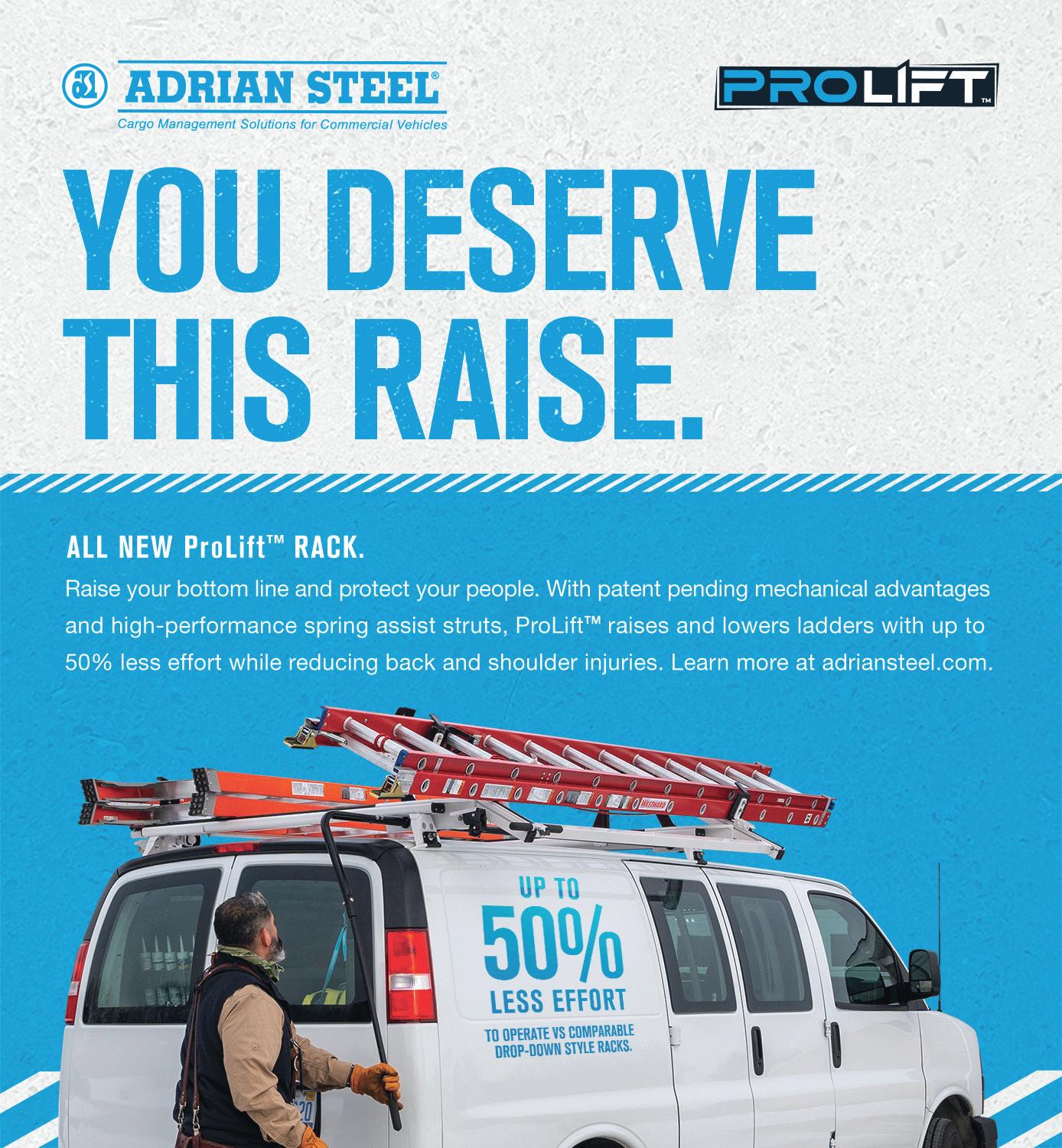
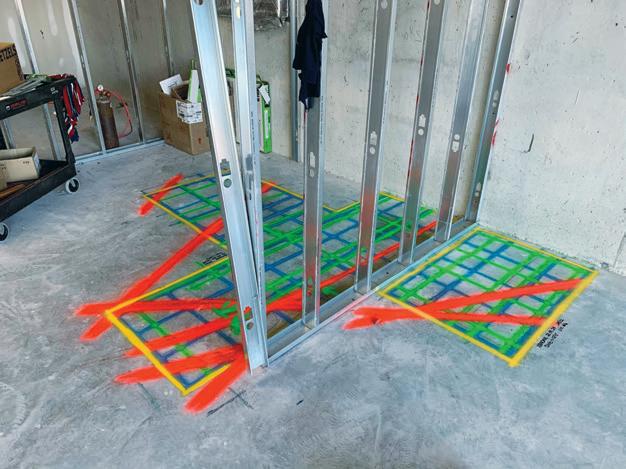
This type of measurement can gauge the potential for corrosion, and thus, the durability of concrete reinforcement. HCP is advantageous when working with concrete structures like parking lots, concrete piers, docks and tunnels. Ultrasonic Pulse Velocity UPV can be used to assess the quality of concrete structures, such as beams, columns, walls and slabs. With this technology, ideally there is access to both sides of the structure, but even if access to the structure is one-sided, indirect transmission can be used.
SCAN TO VISIT OUR WEBSITE
on-sitemag.com / 41 MAX USA Corp. • 205 Express St. Plainview, NY 11803 • U.S.A. - Phone: (800) 223-4293 • FAX: (516) 741-3272 • www.maxusacorp.com
The Wire Pull Back Mechanism dispenses the precise amount of wire needed to form a tie. The Dual Wire Feeding Mechanism increases productivity on job sites. The TwinTier®’s Wire Bending Mechanism produces a shorter tie height. Less concrete is needed to fully cover a wire tie.
OnSite_MaxUSA_Aug22.indd 1 2022-08-04 1:35 PM
The two main limitations to this method of scanning are that X-rays are unable to provide the depth of embedded objects, and access to both sides of the slab is required. X-ray cannot be used with concrete slab on grade. Half Cell Potential
Although conventional GPR scanning is a proven method for concrete scanning, it has its shortcomings. Take slab-on-grade for example—the bottom layer is often quite weak or can be laying on a range of base materials. When scanning slab-ongrade with GPR, a technician will likely have difficulty determining the depth of the slab or getting a reliable read. By making use of a combination of the varying methods, based on the project assigned and deliverables required, it is possible to retrieve an accurate reading for slab-on-grade that more conventional single-method scanning cannot match. When methods are combined, it becomes possible to “see” through wire mesh, and the technician is able to distinguish between specific objects. The postscan report will show if the slab contains electrical conduits, radiant heating lines, rebar, or post-tension cables. It might even have them all!
Jesse Hodgins, C.Tech, has worked with Xradar, a leading provider of concrete scanning services in Canada, since 2017. He recently spearheaded the company’s expansion into Ottawa.
COMBINING THE POWERS
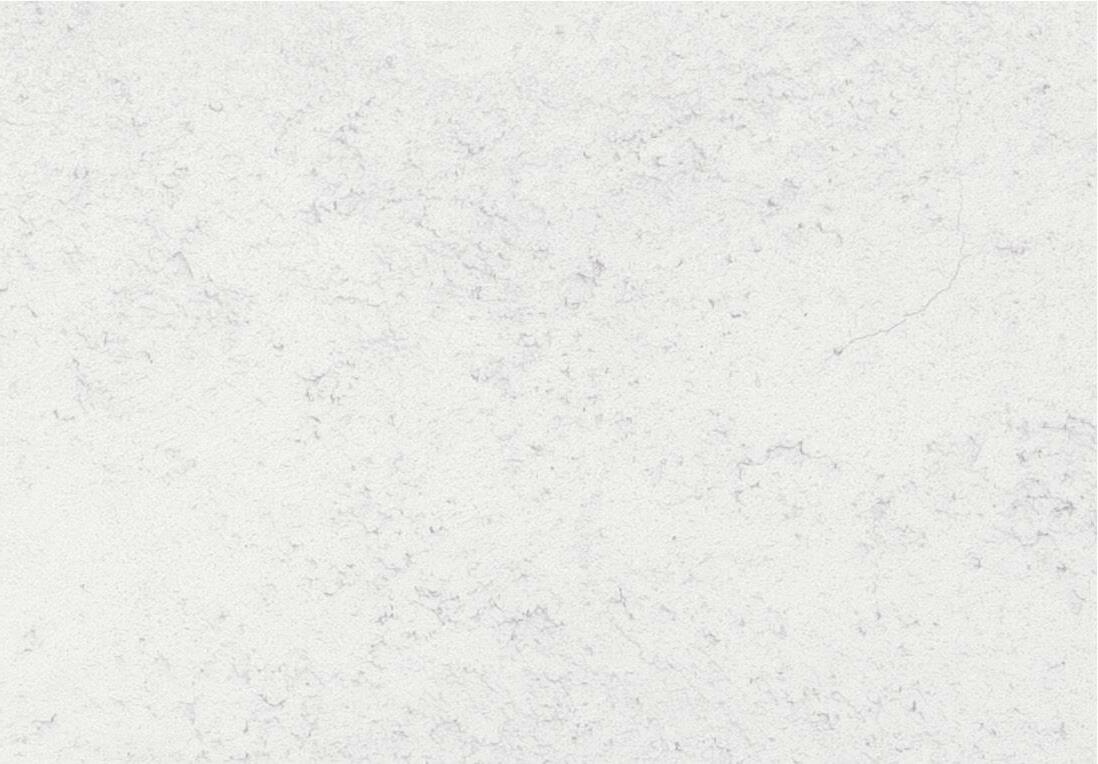
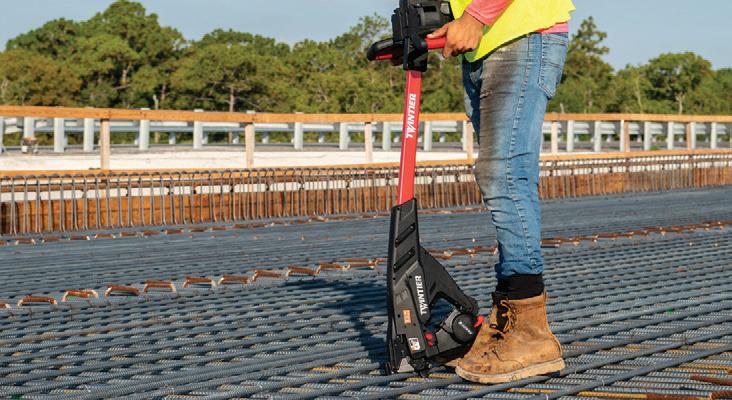

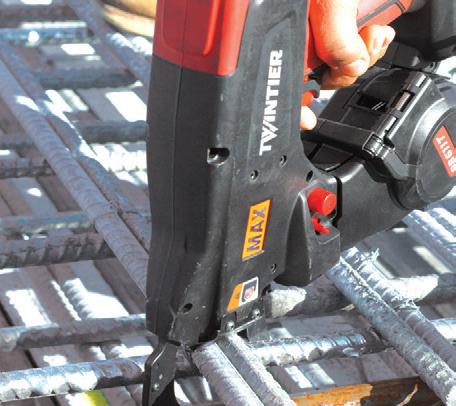
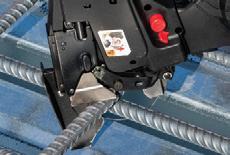
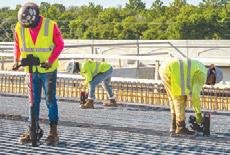
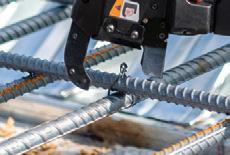

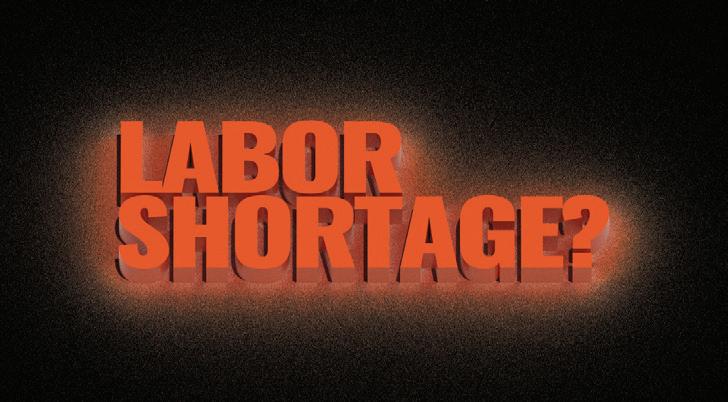
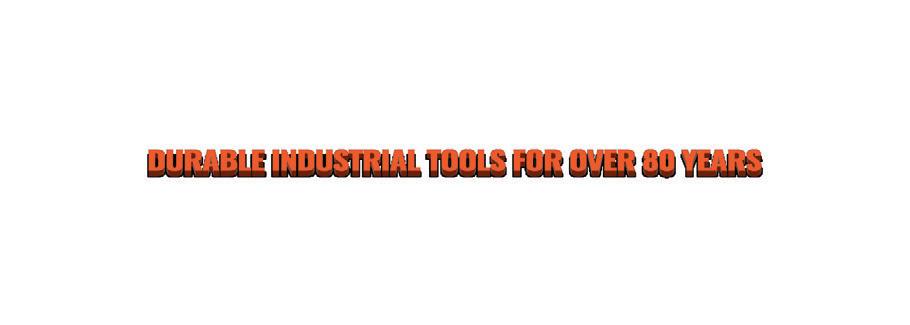

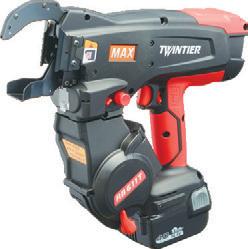

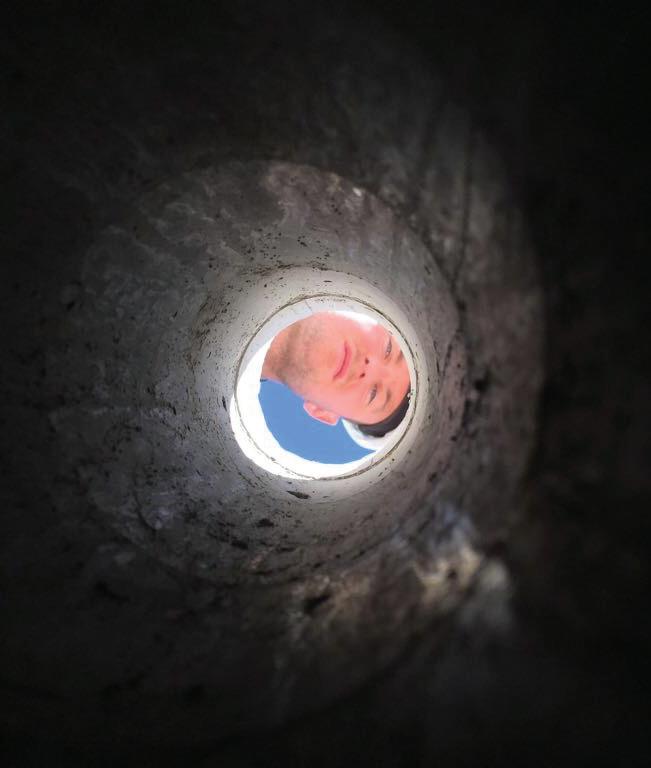
He says that governments need to think more horizontally across their own portfolio about how the different levers they have on the policy side must work together to pave the way for industry to be able to make big investments in the technologies that are needed.
Auer pointed to carbon capture technol ogies from companies like Carbon Upcy cling Technologies and Blue Planet Systems as examples of how innovative aggregate and additives can be part of the discussion.
BY ANDREW SNOOK
He says that government instruments like capital funding through the Net Zero Accelerator Initiative (NZA)—that’s the investment tax credit for carbon capture, utilization and storage—can help accelerate the pace of “They’rechange.talking about some really innovative instruments around carbon price certainty through things like carbon contracts,” he says, adding that programs like NZA help encourage the adoption of earlier stage, more capital-intensive tech nologies like carbon capture and storage.
“In cement in particular, and I think it probably applies to a lot of other heavy manufacturing sectors, there’s really no silver bullet,” he says. “There’s a menu of technologies and policies, and they all come together to work.”
42 / AUGUST 2022 When 196 parties signed on to The Paris Agreement at the end of 2015, the level of public and political attention given to greenhouse gas emission produc tion spiked dramatically. With that commit ment to limit global warming through the lowering of emissions, certain industries, including the concrete industry, were going to be impacted, and potentially pressured, far more than others to find sustainable solutions for their products—and sooner rather than Fortunatelylater.for the sector, many compa nies, research organizations and govern ments around the world have been hard at work for many years to help make concrete production more sustainable.
Concretesolutions
Finding low-emission paths to concrete production.
“In Canada, we’re in a really inter esting phase of the climate discussion,” says Adam Auer, president and CEO of the Cement Association of Canada. “So much of the climate discussion over the past number of years is really focused on carbon pricing as the primary instrument for decarbonization, both on the consumer side and on the industrial side. It feels like that sort of background policy is now wellButunderstood.”thepathto decarbonization is more complicated than simply dollars on a ledger. And Auer says that the cement and concrete industry have been leaders in helping find solutions. “If you understand the construction value chain, it’s quite complicated,” he explains. “If you want to decarbonize that chain, it’s not just about material manufac ture, which is obviously a big component, but it’s also about codes and standards. It’s about the willingness of architects, develop ers and specifiers to accept innovation and try new things. It’s about the willingness for the market to pay more for really lead ing-edge stuff. It’s about thinking through things like material efficiency in the same way that we’ve thought through things like energy efficiency.”
“There’s a huge opportunity to use concrete as a vehicle to sequester carbon,” he says, adding that other technologies are also under development, and in need of support. “It’s about making sure that
SUSTAINABILITY
STOCKADOBE/SHARKTRICKY©PHOTO:
Some of these options, such as moving away from carbonized fuel supplies, are already happening, but the sector is still in the early stages, and some of the avail able technologies are expensive, making it difficult to build a business case to support their use without government incentives.
There are some impressive technologies related to carbon utilization in cement and concrete that are currently being created.
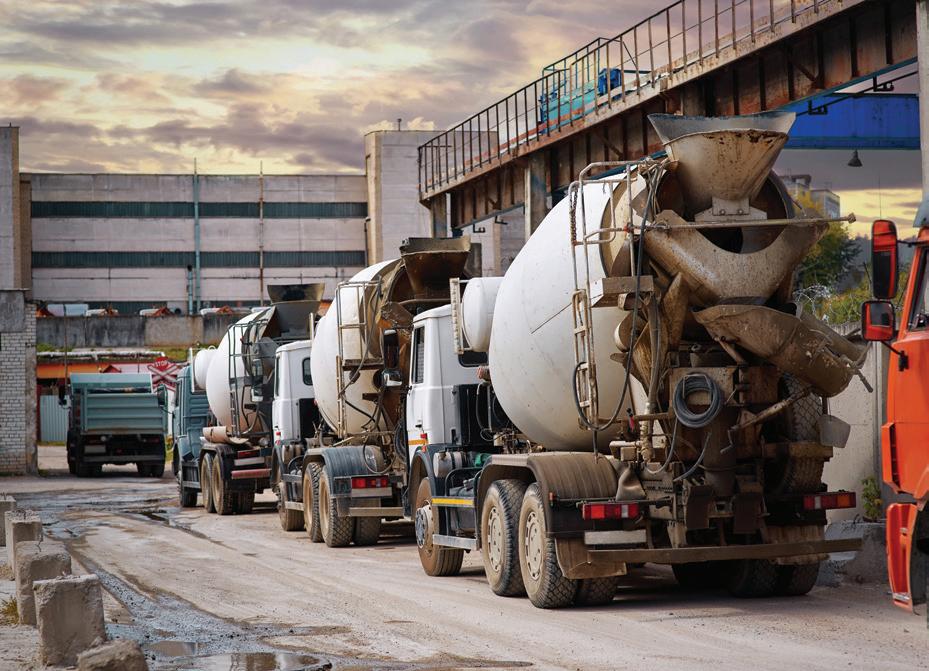
CONCRETE STREETS AND HIGHWAYS x AIRPORT RUNWAYS x CURB AND GUTTER x SIDEWALKS RECREATIONAL TRAILS x SAFETY BARRIER x BRIDGE PARAPET x BRIDGE DECKS x IRRIGATION CANALS GOMACO CORPORATION IN IDA GROVE, IOWA, USA x 712-364-3347 www.gomaco.com x info@gomaco.com GOMACO offers the full range of concrete slipform pavers, curb and gutter machines, trimmers, placer/spreaders, texture/ cure machines and bridge/canal finishing equipment. GOMACO equipment features our exclusive and proprietary G+® control system, created in-house by our software engineers from the wants and needs of contractors paving in the field. At the heart of GOMACO equipment is our passion for concrete and our commitment to our customers. We look forward to visiting with you about your upcoming paving projects and your concrete paving equipment needs. Our worldwide distributor network and our corporate team always stand ready to serve and assist you. The Worldwide Leader in Concrete Paving Technology
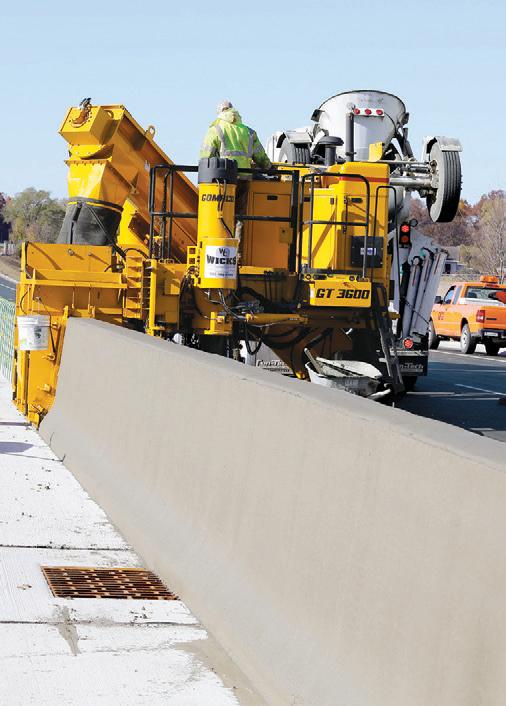
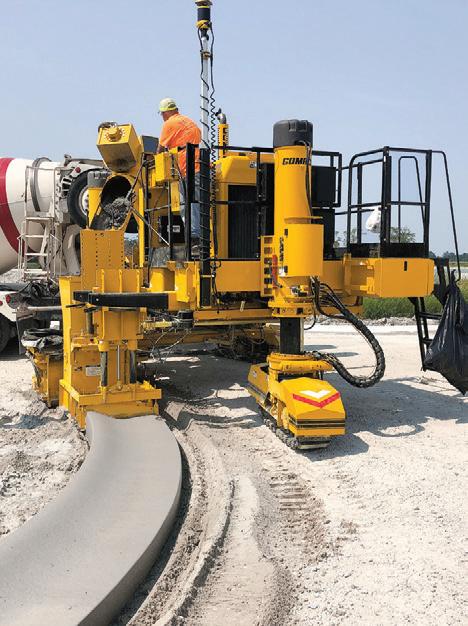
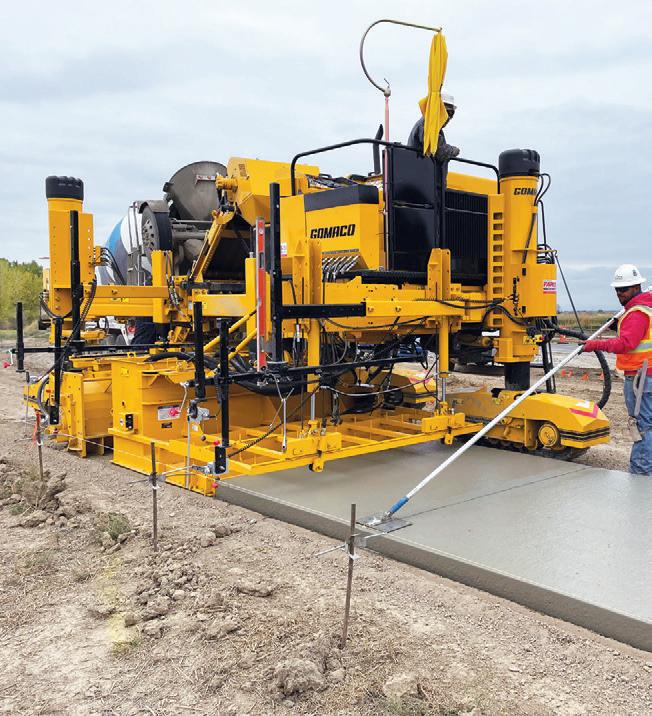

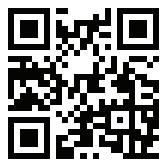
STOCKADOBE/TOUCH1976©PHOTO:
BIOPRODUCT SOLUTIONS
Of course, there’s no sense in waiting, since even a small step is a step in the right direction. As Auer says, “Let’s not wait for the silver bullets, like carbon capture utili zation. Yes, we’re investing in those things. But in the interim, there’s a lot of things we can do today.”
The first implementation of the CarbonStar standard is underway at the San Francisco International Airport (SFO), which has adopted the standard to reduce the warming impact of the concrete it plans to use on its upcoming building and infrastructure projects. The airport lists three levels of CO2 intensity in its specifications for concrete, using the CarbonStar rating system with the minimum requirement being no more than 200 pounds of CO2 per cubic yard (119 kg/m3), and ramping up to a best case of not more than negative-200 pounds per cubic yard — or 60 per cent below the current industry average.
HIGHER STANDARDS
One of the solutions to help make concrete production more sustainable may come from the forestry sector.
To ensure that the standard is being met, the concrete manufacturer will also be required to provide an Environmental Product Declaration (EPD) for its concrete mix and to document the EPD so that the airport and other stakeholders can record the embedded carbon. Riley, who is CEO of the World Cement Association, says that concrete suppliers are mainly using blends to lower the CO2 in the concrete they are producing and supplying to meet requirements like those requested by the SFO. “Concrete suppliers are reducing their CO2 footprints mainly by using blended cements instead of OPC [Ordinary Portland Cement], since these have lower carbon footprints and supplementary cementitious products such as slag, fly ash and natural pozzolans,” he says. New technologies may include geopoly mer concretes, mainly with slag (some times fly ash, red mud and other materials) and no cement; as well as synthetic aggre gates made from sequestered CO2, such as those created by Blue Planet.
For the past five years, FPInnovations, a private not-for-profit organization that specializes in the creation of solutions in support of the Canadian forest sector’s global competitiveness, has been research ing ways to introduce wood pulp fibres to improve concrete recipes.
“Additionally, AI can be used to optimize the packing of the particles, reducing the amount of binder needed. However, these technologies are in limited usage,” Riley says.
The calculations used in the CarbonStar standard are designed to account for the emitted and sequestered carbon per unit of concrete. It was created to limit global warming to 1.5°C by 2050.
“The major improvement is during the curing process to control cracking behaviours. By adding these fibres, we can control the amount that the shrinkage occurs, and ultimately, the cracking,” she explains. “What happens, especially with high-performance fibres for high-perfor mance concrete, is that you don’t have a large amount of water, which increases the shrinkage.”Ifthe porous network of the concrete doesn’t have enough free water, the cellu lose fibres release water to the concrete. “This is how you’re reducing the shrinkage, and ultimately, the cracking,” she says. “That’s an interesting property improvement that we’ve FPInnovations’seen.”
“We see that there’s a lot of improve ments when adding the fibres,” says Helen Lentzakis, manager of the Biomaterials Division at FPInnovations. To date, only small amounts of fibres have been added to concrete mixes with a variety of different fibre types being used in the recipes. Some of the mixes include the additions of Thermomechanical Pulp (TMP) fibres, Bleached Chemi-ThermoMechanical Pulp (BCTMP) fibres, softwood, and North Bleached Softwood Kraft (NBSK) fibres, as well as Crystalline Nanocellulose (CNC) and Cellulose Filaments (CF). With each mix, Lentzakis says her team has discovered different types of improvements.
44 / AUGUST 2022 when we look at the suite of options that are available for decarbonization, that we’ve gotten the right kind of policy, and support for each of those different stages.”
Biomaterials Division has the capabilities to measure all the properties of the concrete from the fresh state to the hardened states. They test all
SUSTAINABILITY
One of the tools now available in the war on greenhouse gas emissions is the CarbonStar standard. Initially developed for Canada and the U.S., this standard offers governments and companies “a rigorous, transparent way to quantify, specify, and then reduce the carbon intensity of concrete based on a standard simple way to measure, report and specific CO2 intensity,” according to Decarbonising our Built Environment, Concrete Block by Concrete Block, written by Greg Kats of Smart Surfaces and the World Cement Association’s Ian Riley and Manon Burbidge.
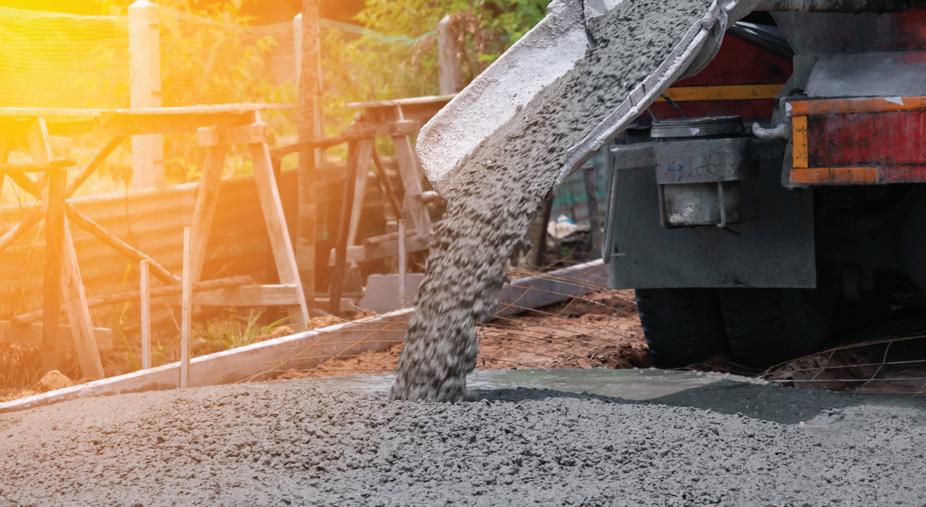
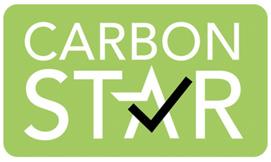
MARCH 14-18 / 2023 / LAS VEGAS / NEVADA TAKING CONSTRUCTION TO THE NEXT LEVEL. 250,000 sqm of Exhibits 130,000 Attendees 1,800 Exhibitors 150 Education Sessions REGISTER at conexpoconagg.com Save 20% with promo code SHOW20 “ATTENDING CONEXPO-CON/AGG FOR 50 YEARS HAS GIVEN US A DISTINCT COMPETITIVE ADVANTAGE.” — SILVI CONCRETE, PHILADELPHIA, PA
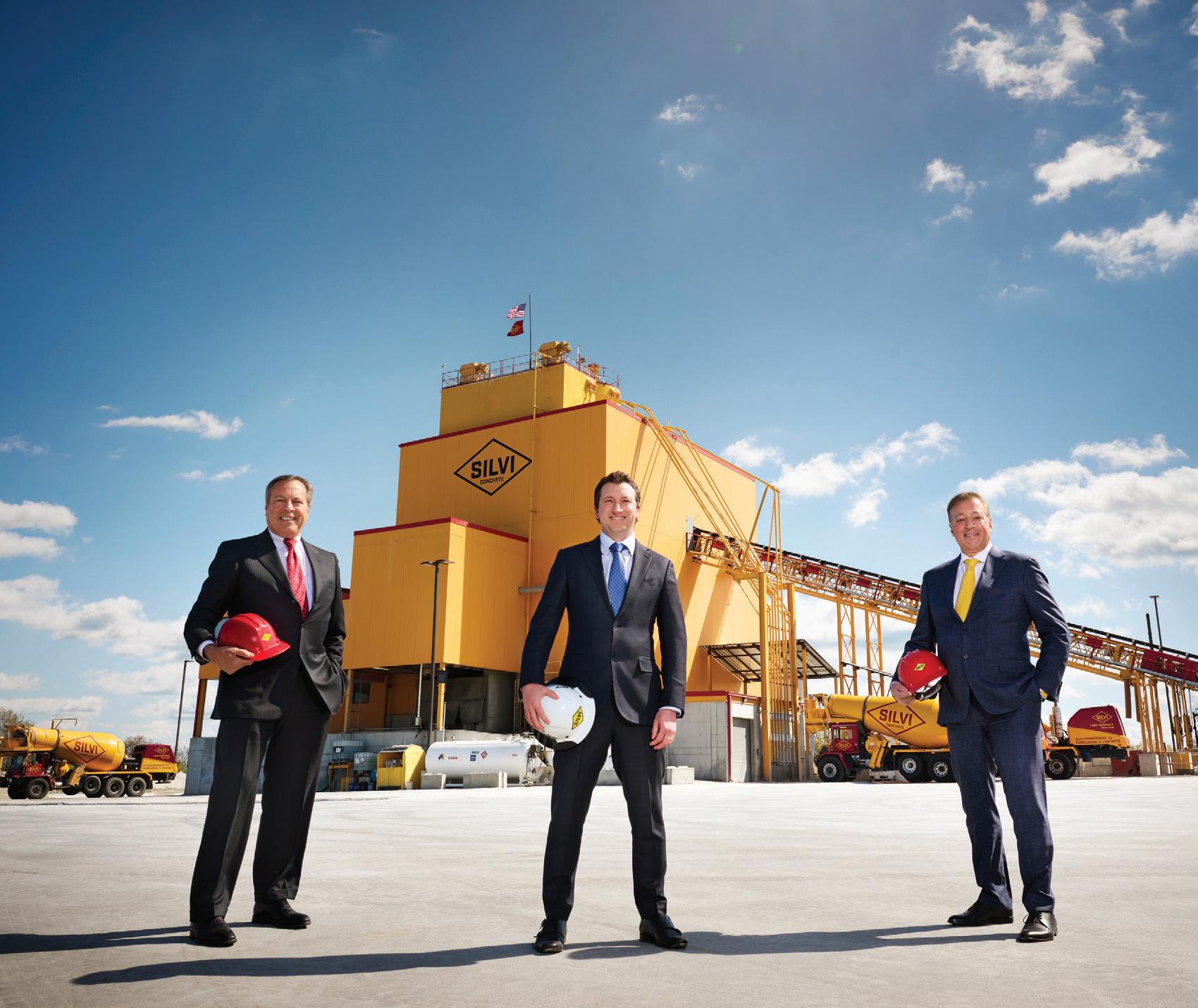

“We find that we have to repeat that process,” Paine says. “It takes extraordinary resources. That kind of time and manpower will require the industry. We strongly encourage that cross-knowledge transfer of experience.”He’shoping that industry associations can press for changes to that process, to make it less cumbersome for industry players.“Iwould strongly encourage associa tions within the country to make sure that they’re using their platforms to talk about successes across geography,” he says. “So that maybe when someone in Ontario has agreed that a pilot was successful, then Alberta or Manitoba looks at that data and says, ‘That’s good enough for us.’”
BARRIERS TO IMPROVEMENT
SUSTAINABILITY
STOCKADOBE/TOUCH1976©PHOTO:
Andrew Snook is a freelance writer and editor.
46 / AUGUST 2022 the fresh properties including rheology properties, isothermal calorimetry, and most of the mechanical properties as well, including the flexural strength and the tensile strength as well as major concrete durability indicators. So, what are the bene fits of adding these various fibres? “The benefit is to increase the dura bility, especially the freeze-thaw resis tance, which obviously is an important property in Canada,” says Lentzakis. “We test freeze-thaw cycles, and we see that there’s an improvement with the addition of theFPInnovationsfibres.” has not yet fully assessed the CO2 impact because they are working with such small amounts of fibres, but the benefit of increased durability in concretes certainly makes for an argument for more sustainable concrete production. Also, cellulose filaments (CF) make it possible to use local, lower quality sand sources without compromising performance. “Because you’re improving the mechanical properties, such as a structural toughness, the advantage would be to use less concrete,” Lentzakis says. “Concrete is usually classified by compressive strength, so if you can increase the classification and have less concrete, and replace some concrete with fibres, you can have a signifi cantFPInnovationsimpact.” has also found that the use of these fibres in the concrete have helped with preventing corrosion in rein forced“Weconcrete.did corrosion activity monitoring
While there are new technologies and products available and coming to market, one of the biggest roadblocks to the imple mentation of modified concrete products is human in nature. It can be difficult to convince engineers to change their specifi cations in a project away from long proven building materials. The same can be said for codes and standards as well.
on outdoor reinforced concrete elements by applying chloride, and we saw that the fibres helped with retarding the corrosion that’s usually caused by chloride,” says Lentzakis. “We managed to have the 26 elements with different types of fibres of TMP, CNC, CF, BCTMP and NBSK fibres at different loading, and we saw with the improvement in corrosion there was a differ ence between how much fibre we are using. So, when you use too much fibre, you don’t see improvement in corrosion mitigation, but when you use less fibres, you see that improvement in corrosion, so that’s pretty interesting as well.”
While the industry has the ability to provide products and solutions with a lower embodied carbon, these products are sometimes at odds with traditional or boiler plate specs and, in some of these cases, these newer designs go against what has “always been done,” which is why there is a need for alignment across all players in the construction value chain to achieve more sustainable“Well-intentionedoutcomes. policies may run up against practices that are built on years of experience, and rightfully so,” says Ian Paine, director of Ready Mix Performance, Western Canada, at Lafarge Canada. “We greatly appreciate that the people responsible for our infrastructure are exceedingly conservative.” As he says, the performance of the concrete material in a building or structure will always be the primary concern driving the material selection process, but once the appropriate level of performance for a mix has been demonstrated, there needs to be an ability to work these newer products into the specifications stream.
While engineers may see increased risk, companies like Lafarge have thoroughly tested their newer mixes and designs and stand by the performance of these materials in the same manner as they do with their traditional mixes. “While we fully appreciate the responsibilities of the stakeholders around the table, we are also very open to agreeing to an innovation process,” he says. Even where there is a pathway for innovative products to be specified, a major challenge is the need to prove processes in multiple jurisdictions, duplicating efforts. Even when one jurisdiction in Canada approves a particular process or product, it can take several years for other jurisdictions to adopt it.
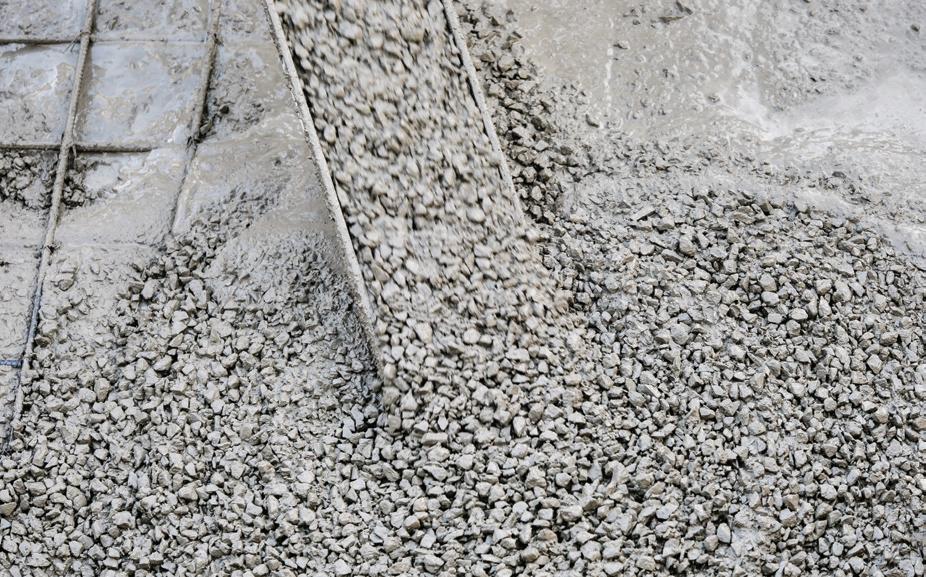
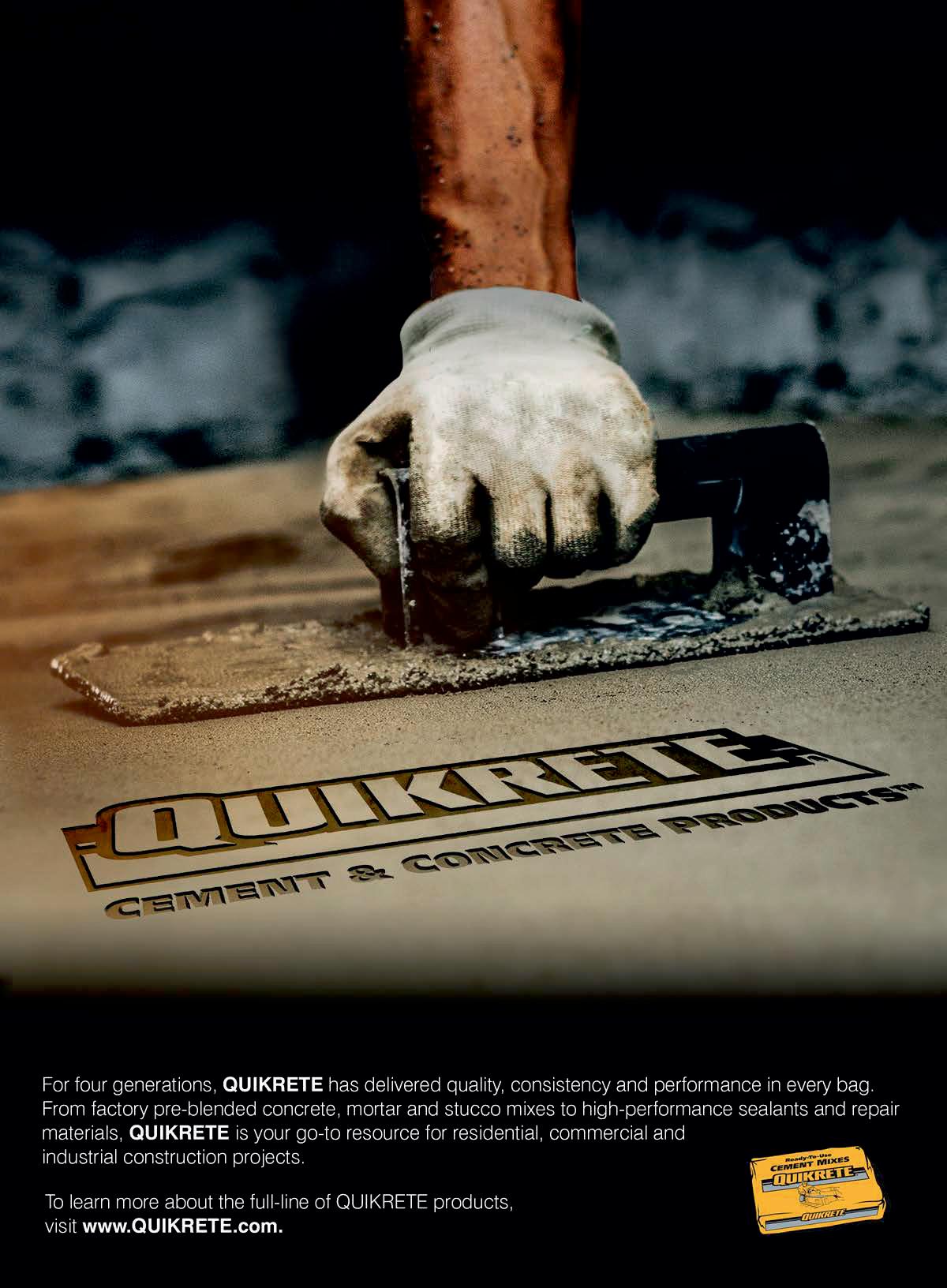
In his role as a lean and sustainability specialist at Chandos Construction, Jack Statham advises project teams on how to reduce carbon and waste across the lifecycle of a project.
48 / AUGUST 2022 EFFICIENCY
By Jack Statham
THE 8-WASTES
This is one of the fundamental tools within Lean. Most practitioners start with understanding the 8-Wastes because typically any source of frustration or delays in a project stem from one of these, and typically any reduction in waste provides substantial benefits to the project.The acronym DOWNTIME can help recall the components: Defects, Overproduction, Waiting, No Regard for Knowledge, Trans portation, Inventory, Motion, and Extra Processing. It is important to look at a process when understanding waste because what is observed may not always be the root cause, but instead be a symp tom of a larger problem.
T racing its roots to the Toyota Production System (TPS) that was first developed in the late 1940s by the Toyota Motor Corporation, Lean Construction is a management system that aims to provide the most value to the customer then improving flow and eliminating waste. The customer is defined as any stakeholder receiving finished work from the previous step in the process, or previous process. Value is what they need, when they need it, with the quality and quantity of what they expect. Although similar to traditional Lean Management used within manufacturing, Lean Construction does have differences. Most notably, the Last Planner System of Production Control, created by Glenn Ballard and Greg Howell in the early 1990’s. This was the catalyst for the creation of what we know as Lean Construction.
5S The five Ss are Sort, Set-in-Order, Shine, Standardize, and Sustain. This is a management system focused on ensuring working areas Lean delivers value
PRACTICAL APPLICATIONS
Developed initially for manufacturing environments, Lean is lending its benefits to the construction industry. remain organized and clean. I believe this is one of the most important tools of Lean because of its ease to implement on any project, and its substantial benefits. When working areas are organized and clean, they become safer, people are naturally more productive, and the environment is conductive to a higher quality product. Furthermore, when the project leadership is committed to maintaining clean, safe, and productive working environments it demonstrates that they truly respect the people—one of the funda mental principals of Lean.
THE LAST PLANNER SYSTEM Commonly referred to as “pull-planning,” this system is designed to allow the people closest and most familiar with the work to contrib ute to making the construction schedule and sequence of activities. The construction team works backwards from a milestone outlining the predecessor tasks, durations, potential constraints, possible time savings, and then committing to completing their activities.
There are three main tools implemented within most Lean Construction projects, the Last Planner System (LPS), The 8-Wastes, and 5S.
Lean tools are used to assist with the training and implementation of lean practices; however, to truly implement and benefit from Lean Construction it must be embedded into the culture. This is something that I have the most passion behind because I have had the opportunity to see true Lean in action. During the start of the COVID-19 pandemic, nobody knew what was happening and there was a lot of stress. Our teams knew that to keep working we had to ensure that people were safe, both physically and mentally. Instead of waiting for direction from leadership, our site teams started making improvements to their projects, taking videos of those improvements, and then sharing themThesecompany-wide.improvements were rapidly improved upon by other teams and reshared. By the end of the first month, we had almost 100 shared videos outlining different improvements ranging from our sign-in process, improved sanitary facilities, digital pull-plan ning, outdoor pull planning, and everything in between, all with the focus of keeping our teams working and most importantly safe. Our leadership team also demonstrated exceptional communi cation through our weekly company wide stand-up meetings and multiple townhall meetings to share information. Additionally, our COO Sean Penn conducted a cross-country tour visiting our projects to talk directly with our field teams. Now, almost two years later, most of the improvements are still in use. Many became standard policy, and Chandos has grown exponentially. My current goal is to maximize our culture of continuous improvement and direct it towards our Net Zero 2040 commitment. Many of our teams have already made amazing improvements with sustainability as a focus, and I look forward to sharing how Lean can be used to improve sustainability in the next column.
By having the construction team create the schedule with the understanding of the entire process, it naturally builds account ability. There are several steps and processes built into the LPS to ensure constraints are removed prior to the start of each task, and daily huddles to track progress or discuss constraints.

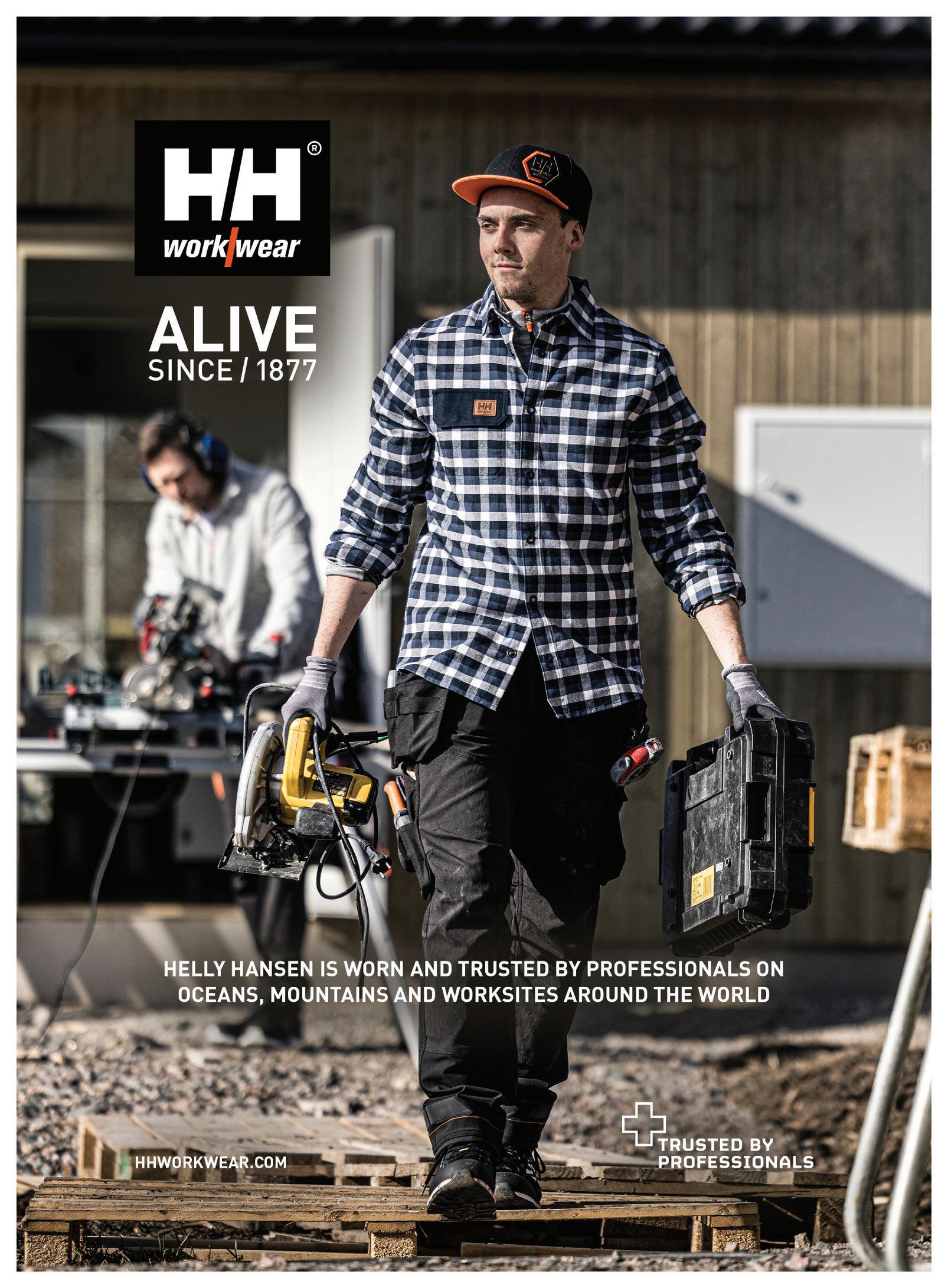
“Construction has been doing things the same way for a long time,” says Maxwell, “but I do see a change in how some top tier contractors are trying to operate. And I believe Last Planner is one of those tools for becoming, to use our CEO Geoff Smith’s expression, fast, fluid, and flexible.”
A growing number of general contractors are experimenting with a collaborative scheduling and project management system that does not depend on digital devices.
It may seem surprising, therefore, that one of the boldest approaches to collaborative scheduling and project management requires nothing more than a whiteboard, coloured marking pens and sticky notes. Last Planner was developed in the 1990s. It was inspired by the Total Quality Management (TQM) movement in manufacturing that, thanks to the efforts of the Lean Construction Institute, is seeing gradual but steady growth in construction. The system, in a nutshell, replaces the traditional top-down scheduling approach with a more collaborative system where the general contractor and subcontractors work peer-to-peer to determine the most efficient way to meet schedule milestones, and then keep things on track through frequent interactions. “This is very different from the traditional command-and-control general contractor approach that everyone’s been so used to,” says Ashley Maxwell, senior project manager at EllisDon. The key is that foremen and superintendents who supervise the day-to-day work take ownership of the project schedule, which is typically posted in timeline fashion on a large whiteboard in the jobsite trailer. Everybody commits to weekly one-hour planning meetings in which constraints that might jeopardize the schedule are discussed and resolved through direct collaboration. This is supplemented by 15-minute “daily huddles” where immediate issues are brought forward.
TOWARDS A BROADER VISION
Jacob Stoller is principal of StollerStrategies. Send comments to editor@on-sitemag.com
“One of the biggest things about Last Planner is that it gives us a forum for people to talk openly,” says Andrew Brennan, superintendent at PCL Construction. Because Last Planner leaves scheduling details in the hands of the foremen in the field, the difficulty of reconciling an externally created schedule with day-to-day reality is avoided.
“You have to have the right people in the room,” says Sylvia Poon, operational support supervisor at PCL Construction, “and it can’t be something where people just log in during a weekly planning meeting. People are making commitments to each other, and the plan is going to be referred to throughout the week.”
The business case for construction management technology is often based on the drawbacks of handwritten notes, paper forms and hard copy drawings. These are time-consuming, cumbersome, and error-prone, the argument goes. Digitizing them is the obvious solution.
“It’sframework.”apowerful tool,” adds Maxwell. “Guys who really get it, when it clicks, say they’ll never build any other way again.”
“Here’s where you have those conversations about who’s working in which quadrant so that people can stay out of each other’s way,” says Maxwell. “Instead of having your superintendent as the hub of communication, now you have foremen getting together every day so they can have those conversations directly. This makes communication a lot more efficient, and it builds better relationships.”“There’sa lot of value in getting everybody in a room together,” says James Barrett, vice-president and chief innovation officer at Turner Construction, “and it’s really powerful when a contractor turns to another contractor face-to-face and says, ‘I’m committing to getting this done on this day so you can get your workLastdone.’”Planner also provides the opportunity for sharing specific concerns and requirements.
“I think it’s just an outdated notion that a person or a handful people can possibly dictate every day over the course of three years,” says ContractorsBarrett.arealso experimenting with online Last Planner tools, and the advantages, such as ease of sharing and updating, are obvious. Facing COVID-19 constraints, PCL used the virtual approach successfully in a recent hotel renovation. The key was ensuring that the people who controlled the work on site were present, and that all participants understood that they’d be committing their teams to specific timelines.
50 / AUGUST 2022 By Jacob Stoller
democratized TECHNOLOGY
“Last planner changes the work environment and the culture, and drives a lot of positive behaviours,” says Barrett. “That’s a hard thing to do in this industry, which is adversarial by tradition. We see Last Planner as a stepping-stone to a larger Lean approach, where we introduce the broader continuous improvement
On the surface, Last Planner is an innovative tool for improving how jobsites are managed. More broadly, it transforms how general contractors interact with their trade partners.
Scheduling
PCL is also having success with a hybrid approach where site personnel meet live and others, such as a material supplier whose delivery timing might affect jobsite workflows, are connected virtually.
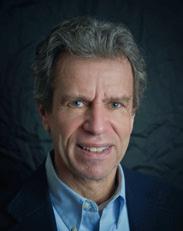
We uptimeequipmentimprovedto95%. That’s money in the bank. BEN BARRIERETUCKERCONSTRUCTIONBreaknewground, win more work and complete it more profitably with the unified ONE Platform for heavy construction estimating, operational workflows and business insight. HEAR BEN’S SUCCESS STORY AND MORE AT B2WSOFTWARE.COM/BEN B2W Maintain
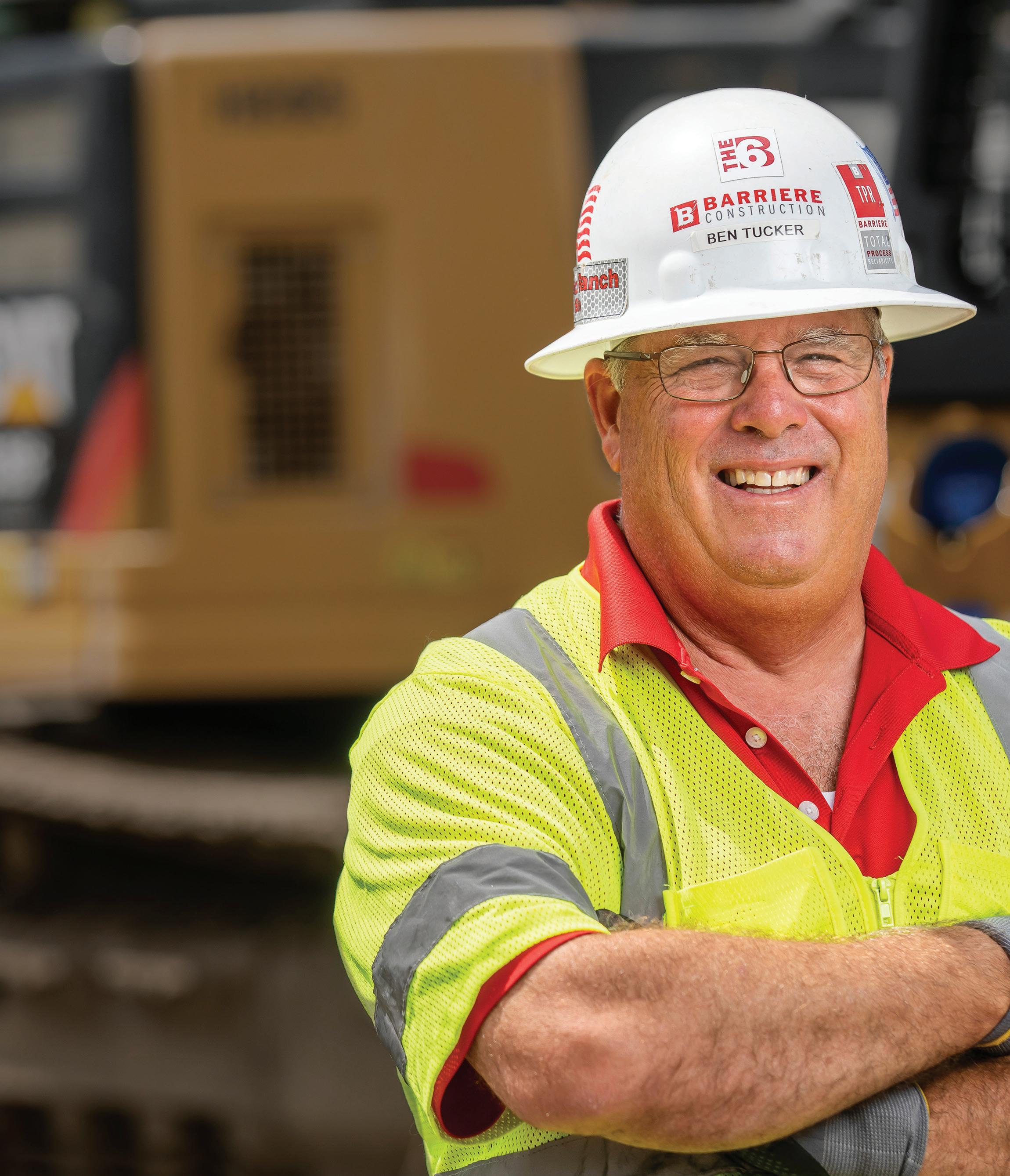

There can be a lot of variety in the dispute resolution procedures included in public infrastructure project contracts. One common ality, however, is that they generally include a stepped process that must be followed. These often include negotiation between senior members of the parties, followed by an interim consideration of the issues by a referee or adjudicator or expert panel, followed by liti gation or arbitration. The similarity between the dispute resolution processes often ends there, however.
52 / AUGUST 2022 By Trish Morrison
A contract may state that an interim decision is final and binding unless a notice of dispute is delivered within a specific deadline. Other contracts only allow certain types of disputes to proceed further in the dispute resolution process.
Careful consideration of these contractual provisions must be made early, as the binding nature of the outcome could impact the route a disputing party wants to take.
LIMITATION PERIODS
STEPPED DISPUTE RESOLUTION PROCESSES
Construction disputes are just as common on public infrastructure projects as they are in the private sector, however the details of those disputes, or often even their existence, are generally not known, as the disputes are often addressed through confidential processes such as mediation, referee reviews, adjudication and arbitration. Unless one of the parties files an appeal or judicial review with the court, there is very little ability for the public to learn about the details of the disputes. This prevents parties from being able to reference those arbitral decisions as precedents in later disputes.
CONTRACTORS & THE LAW
The treatment of interim decisions is an area where there is a lot of difference in public infrastructure contracts. As noted above, many dispute resolution processes include multiple streams for address ing disputes before a final litigation or arbitration process. Some are of the steps are non-binding.
However, some contracts include a further step in the dispute resolution process that has an “interim-binding” result. This could involve an expert panel, a dispute resolution board or an adjudica tion. The findings or determination of these bodies may be binding if they are not disputed and referred to litigation or arbitration by one of the parties. For these processes, the contract will generally include language regarding the nature of the recommendation or decision, such as whether the process is “without prejudice” or binding, and the steps which need to be taken by a party who wants to dispute an interim-binding determination.
As with all contractual clauses, dispute resolution procedures can be negotiated and vary from contract to contract, even when more than one contract is made with a single client. Therefore, dispute resolution procedures need to be reviewed carefully at the beginning of and throughout a project.
TREATMENT OF INTERIM DECISIONS
If the contract does not address the tolling, suspension or extension of limitation periods, it may be prudent to consider entering into a tolling agreement. The specific language contained in the contract will be central in the determination of these issues and legal advice should be sought early, so that the right to make a claim is not lost.
One issue that is addressed very differently in public infrastructure project contracts is the impact of the dispute resolution process on the limitation period. A limitation period is the deadline by which a party must commence arbitration or litigation, failing which the claim is time barred. Some contracts expressly address the tolling or suspension of the limitation period, once certain steps have been taken, while others are entirely silent, meaning that the limitation period will be governed by the applicable limitation legislation and common law. For example, in Ontario, certain public infrastructure contracts provide that the limitation period is tolled when an effective “notice of dispute” is delivered by a party. The tolling of the limitation period ends on the first date upon which the dispute may be referred to arbitration. In British Columbia, some provincial infrastructure contracts include different treatment of limitation periods, depending on the type of dispute notice delivered. In some contracts, the delivery of an “expert panel dispute notice” will suspend the limitation period from the date the notice is issued until 60 days after a decision is rendered by the expert panel, or the parties receive a notification from the panel of its inability to achieve a unanimous decision. Other contracts, with other governments, may not expressly address tolling or suspending limitation periods during the dispute resolution process. In that case, other considerations need to be made, such as whether the applicable limitation period legislation provides for an automatic suspension during certain processes, or whether the right to arbitrate even arises until all of the mandatory pre-requisites dispute resolution steps have been taken.
For example, in British Columbia, in some contracts, the determination of the expert panel is final and binding, except for disputes over a specified value, or if the expert panel was not unan imous, or if the parties agree to proceed to arbitration.
Resolving disputes on public infrastructure projects
MULTI-PARTY DISPUTES
As anyone involved in large infrastructure projects knows, it is very common for disputes to involve multiple parties in different tiers of Dispute resolution options may vary from contract to contract.
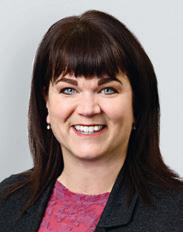
on-sitemag.com / 53 ADVERTISERS’ INDEX & WEBSITES Adrian Steel..........................www.adriansteel.com....................................................40 Atlas Copco www.atlascopco.com 7 Avetta www.avetta.com/demo..................................................11 B2W Software www.b2wsoftware.com/Ben 51 BKT Tires www.bkt-tires.com 33 CIQS www.ciqs.org 54 CONEXPO..............................www.conexpoconagg.com 4, 45 CSA csagroup.org/OHScollection 55 Enbridge...............................www.enbridgegas.com/safeexcavation 27 General Liquids Canada www.general-liquids.com 21 Gomaco www.gomaco.com 43 Helly Hansen www.hhworkwear.com 49 Hitachi Construction www.hitachicm.us 2 Husqvarna............................www.husqvarnacp.com 29, 38 Kubota..................................www.kubota.ca 25 Max USA www.maxusacorp.com Wirtgen.................................www.wirtgen-group.comRakenQuikrete................................www.quikrete.com.........................................................4741www.rakenapp.com.......................................................56SoftwareOnewww.softwareone.com/construction19Takeuchiwww.takeuchi-us.com.....................................................9WesternGlobalwww.western-global.com3514,15 follow us on www.linkedin.com/company/ SHOW OFF YOUR SITE in the 2022 CANADIAN CONSTRUCTION PHOTO CONTEST Submissions open now! SUBMISSION CRITERIA: 2021 Winner 2020 Winner 2019 Winner 2018 Winner • Shot on a Canadian job site • Taken in 2022 • Shows construction in progress • please send your photos and descriptions editor@on-sitemag.comto Sponsored by
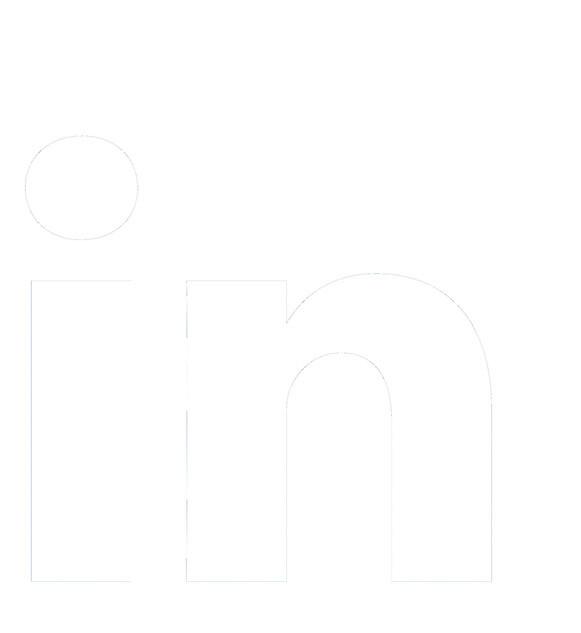
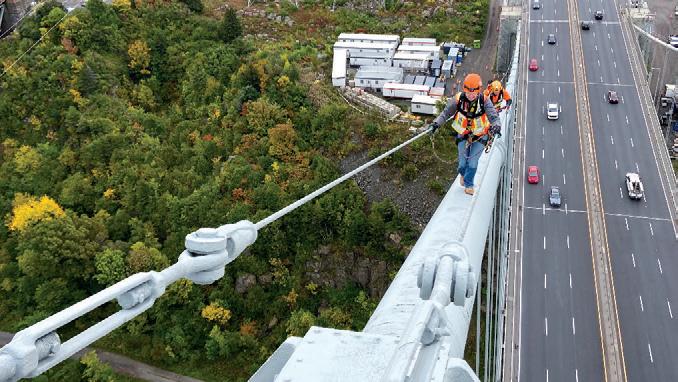
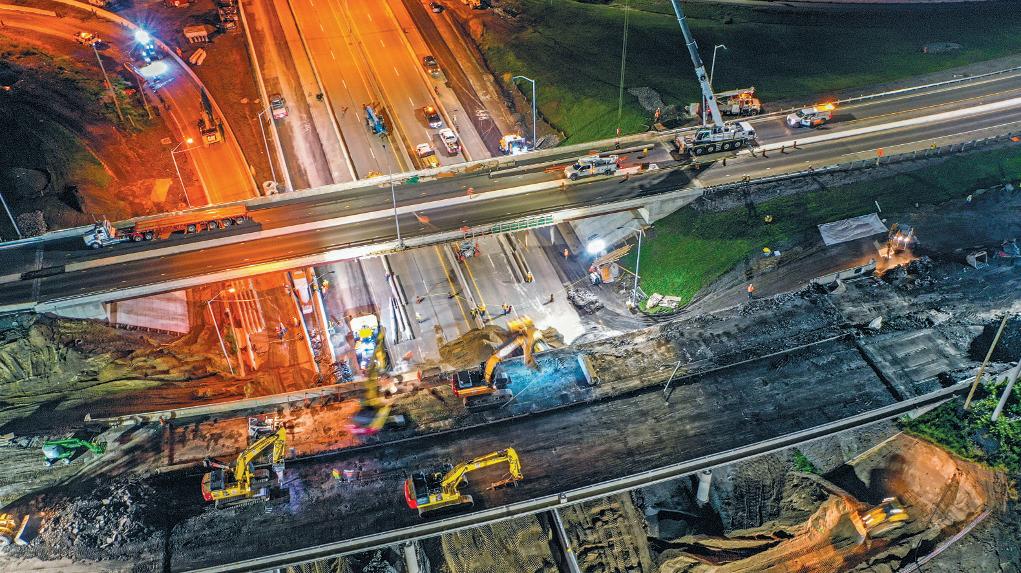
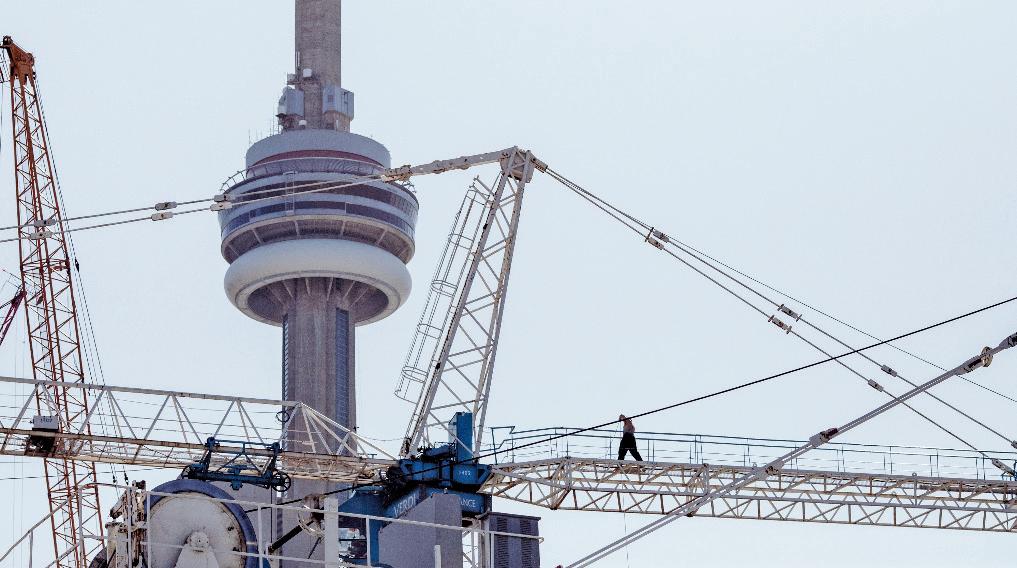
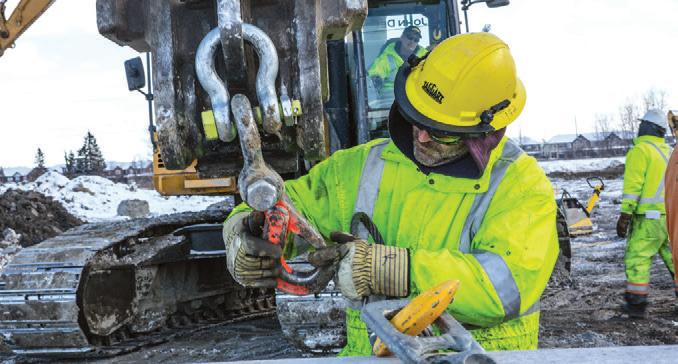
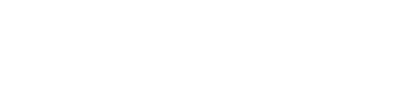
CONTRACTORS & THE LAW the contractual chain. However, with arbi tration, it is generally not possible to require other parties to participate in the arbitration without the consent of all of the parties. Agreement to participate in a multi-party arbitration, with other parties involved in the project, can be included in the dispute reso lution procedure set out in the contracts. To be effective, an agreement to participate in a multi-party arbitration must be expressed very clearly and must be included in every contract in the contractual chain. More often than not, construction contracts are silent on this issue, and it is difficult to get all parties to agree to participate in a multi-party arbitration after the dispute has arisen. This often results in multiple arbitrations being conducted. Some public infrastructure project contracts include language to address this issue, such as by including clauses that address joinder or consolidation of arbitra tions. Some contracts indicate that there is “no joinder” except with written agreement of both contracting parties, as well as the party being joined. Other contracts include language that the parties agree that an arbi tration between the parties can be consol idated with arbitrations with other parties on the project, either by agreement or by direction of the Referee or the Arbitrator.
Trish Morrison, partner and national business leader, is a construction lawyer at Borden Ladner Gervais LLP. This article provides an overview and is not intended to be exhaustive of the subject matter contained therein. Although care has been taken to ensure accuracy, this article should not be relied upon as legal advice.
Disputes on public infrastructure projects may also be impacted by the nature of the contract itself. Over the past few years, Canada has started to see an increase in the use of collaborative contracting models on large infrastructure projects. Under these types of contract models, the intention is that the parties share the risk of project delivery, and the contracts often include provisions that are intended to ensure that no disputes arise or are very limited in scope and the amount of potential exposure.
Careful consideration should be given to these clauses before the head contract and subcontracts are finalized. Alternatively, parties may want to consider agreeing to a project level dispute resolution process, which would allow issues to be addressed once and would allow for contribution and indemnity claim to be addressed at the same time.
COLLABORATIVE AGREEMENT MODELS
54 / AUGUST 2022 OnSite_CIQS_Aug22.indd 1 2022-07-19 11:04 AM
Parties are generally expected to agree not to litigate disputes except in very limited circumstances, such as disputes involving wilful default or fraud. As a result, it is very common for collaborative agreements to include significant waivers of claims, limited indemnity provisions and broad limitation of liability language.
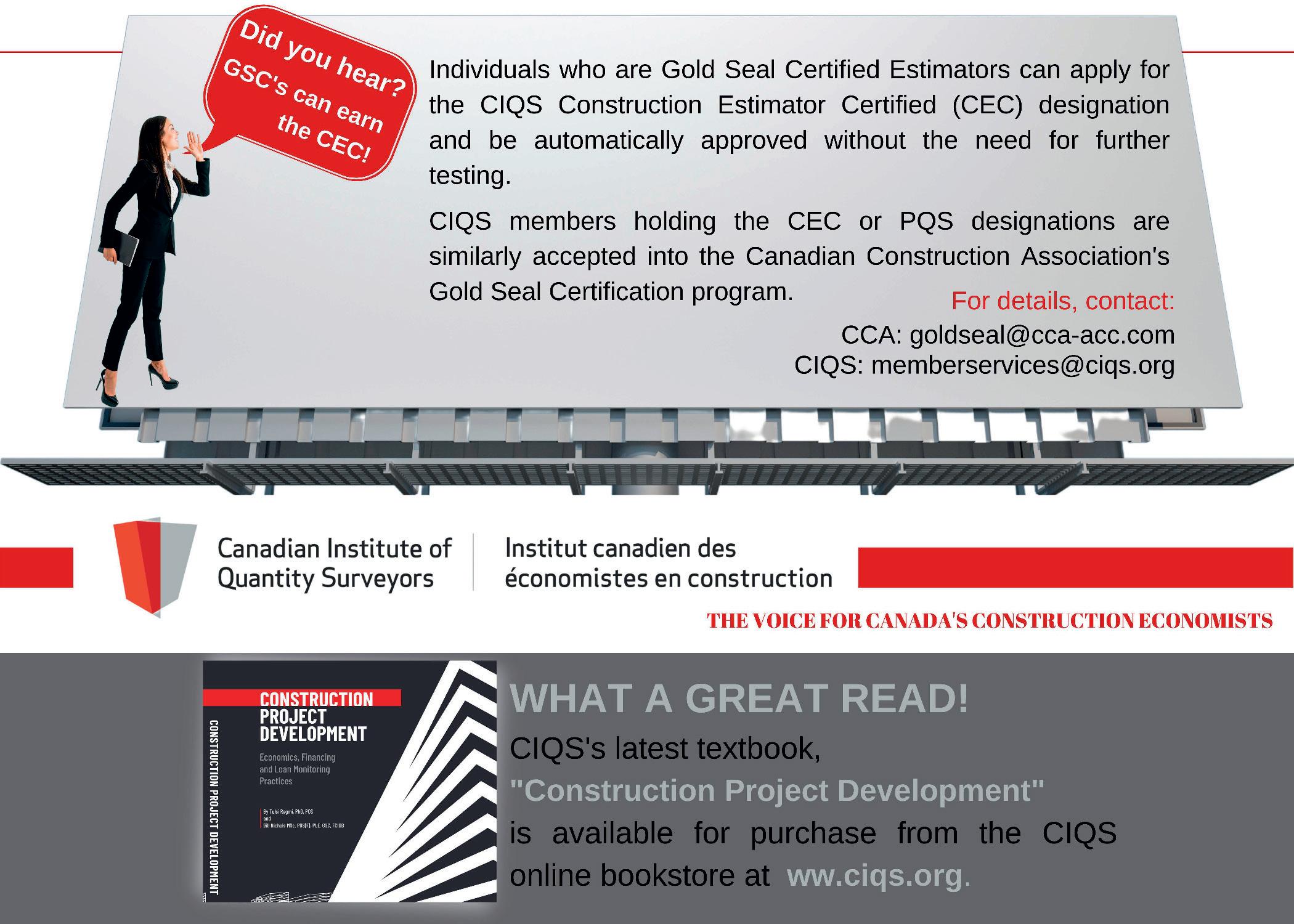
CSA Z259.19:22, Managed fall protection training, a new standard published in 2022, guides organiza tions through the development and implementation of training programs aimed at improving workers’ safety.
New standards can help improve fall protection in the workplace
underlines the need to identify organi zation’s specific fall hazards and risks in order to determine training objectives, content, and requirements that meet the needs of workers and employees being trained. These standards are just a few latest additions to a suite of CSA standards focused on fall protection and workers’ safety. Learn more about CSA standards that can help protect your workers at csagroup.org/OHScollection
ADVERTORIAL
CSAtectionanddardmentingComplethestanforselectionuseoffall-proequipment,Z259.19:22
Fall accidents remain one of the leading causes of injuries in many industries. In construction, 21% of all lost-time injury claims in 2020-21 were due to falls, according to the Workplace Safety and Insur ance Board data. While many organizations have started to use robotic and autonomous devices to reduce the need for work at heights, this approach is not al ways possible or feasible. Management of work at heights, proper fall protection equipment, rescue procedures, and adequate training are critical com ponents of occupational health and safety practices and procedures organizations need to implement in order to protect their workers. CSA Group’s suite of fall protection standards offers organizations a robust toolkit they can leverage to better protect their workers. New Standard for management of work at heights
The first standard of its kind, CSA Z259.17:21 helps address the lack of consistency on how to select, care for, and use active fall-protection equipment and systems. It provides information, methods, and criteria to assess how equipment and assembled systems behave and how solutions should be select ed and implemented, considering the type of work, frequency of access, knowledge and skills of work ers, and other factors.
The recently published standard CSA Z1009:22, Management of work at heights, provides an over view of steps organizations need to take to establish and maintain an effective work at heights (WAH) management program. It encourages a preventative approach, bringing work tasks to a safer ground level whenever possible, and sets requirements and recommendations for developing detailed WAH plans, work procedures, and training programs that outline roles and responsibilities at all levels of the organization. How to select and use fall protection equipment and systems
ISTOCK.COMSOURCE:IMAGE
Helping your team gain skills and knowledge to perform work at heights

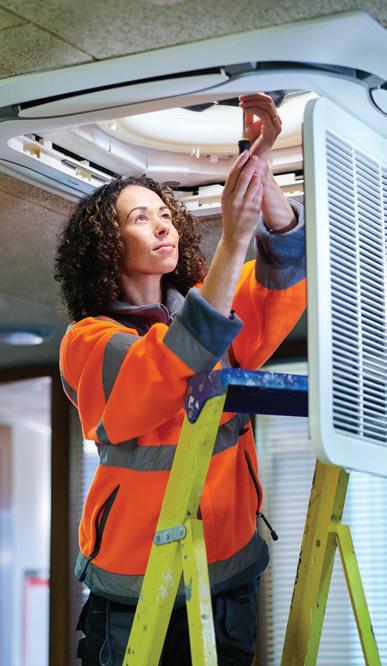
4.7 4.5 4.79 The wrong construction tech slows you down. (And gives you more headaches than answers.) Raken’s field-friendly app makes documenting and tracking projects easy. So easy that your crews will actually use it—and give you the field data you need in real time. Say no to overcomplicated tech. Say yes to Raken. Technology doesn’t have to suck.
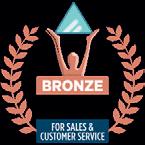


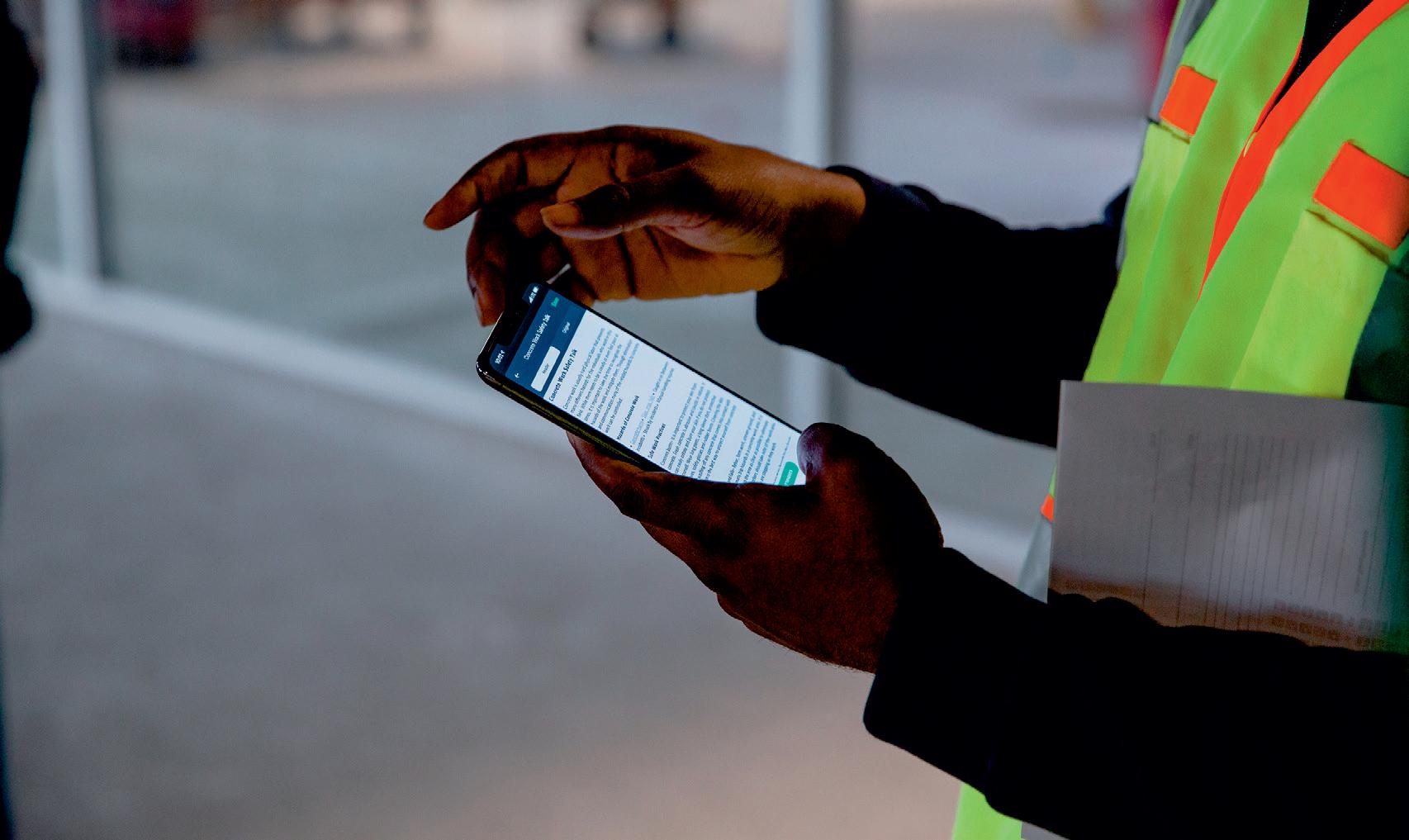
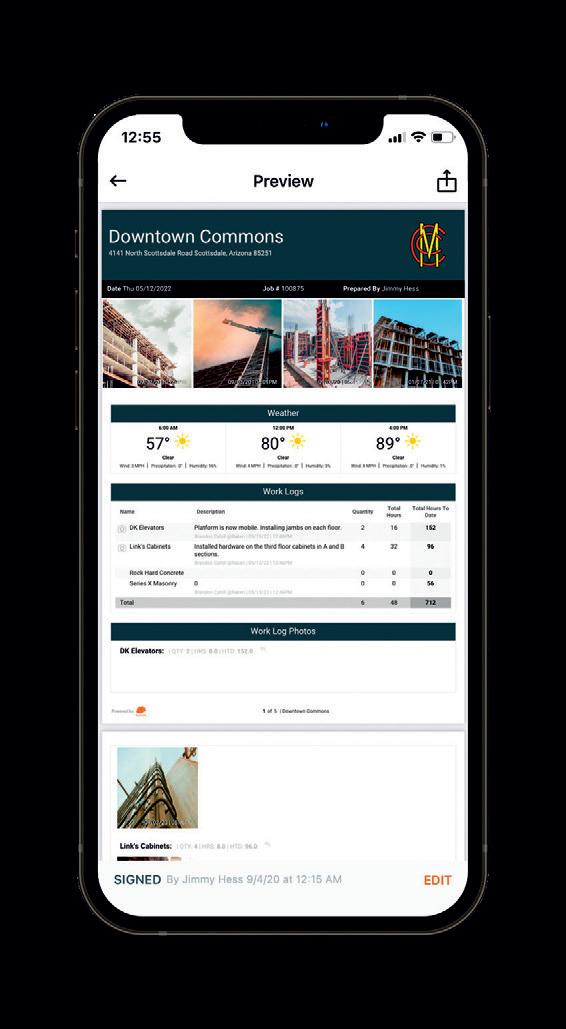
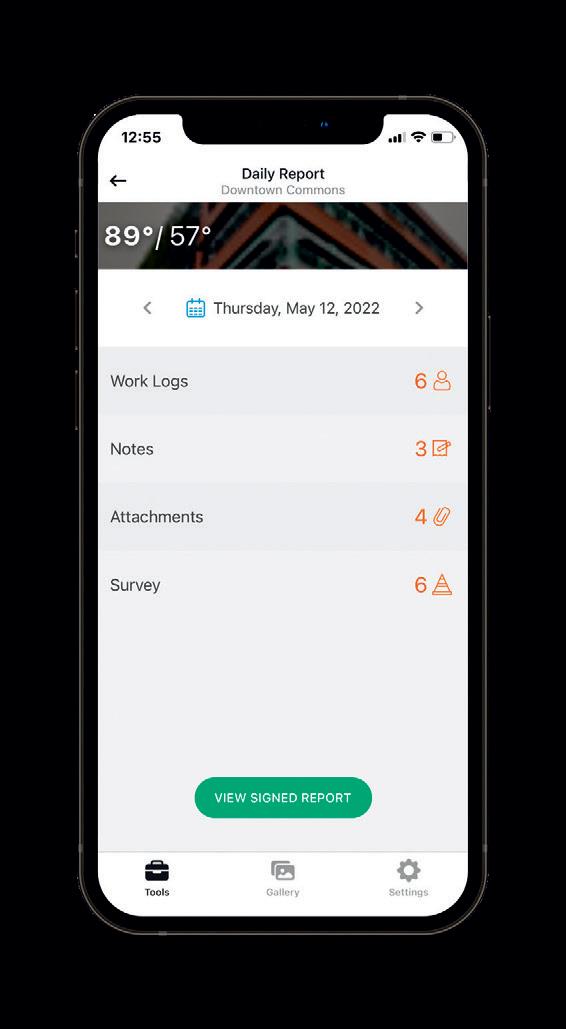
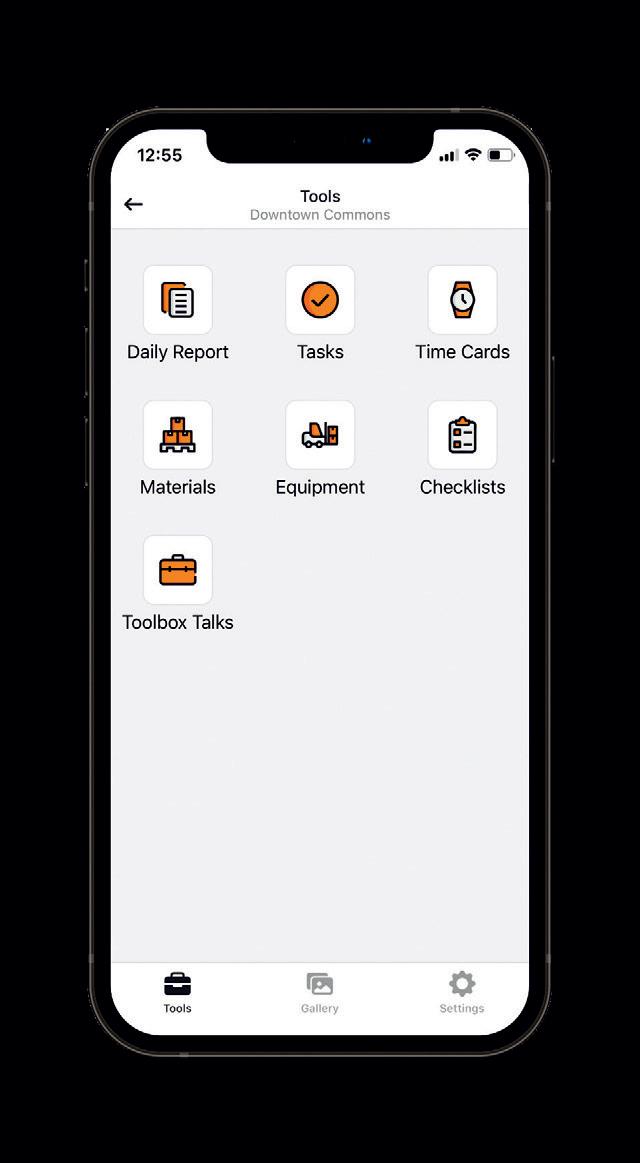