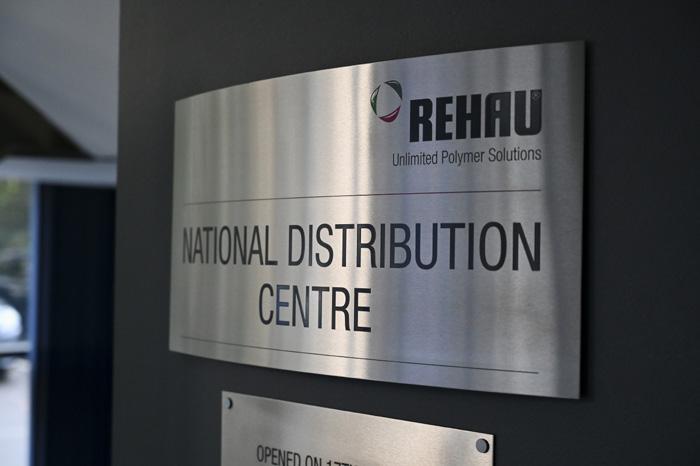
6 minute read
REHAU INVESTS IN PROCESSING, PEOPLE AND SUSTAINABILITY
Joining an Editor’s Visit to REHAU’s plants at Runcorn and Blaenau Ffestiniog, Glass News’ Editor, Chris Champion, had the opportunity to see how PVCu windows are recycled at PVCR Runcorn, profile extruded at Blaenau, and then transported to the distribution centre in Runcorn for onward travel to their customers.
We think of REHAU as being one of the largest systems houses for PVCu window profiles, but it is easy to forget both its origins and its influence throughout the world.
From being a family-owned business, formed in 1948, REHAU is still a family business some 74 years later, the difference being that from its origins in Bavaria it is now a company that produces products for the construction industry, automotive and general industry and from some 170 locations in 54 countries throughout the world. It employs around 21,000 people that work, essentially, on the company’s polymer-based products. In fact, the automotive division is its largest and, as you drive along a motorway, bumper to bumper with other road users, it’s interesting to reflect on the fact that a good proportion of those bumpers you are staring at have their origins within REHAU! Automotive was there from the start: along with, would you believe, shoe welting and garden hoses and with just one extruder and three employees! Some time ago I conducted a somewhat ad hoc survey of homeowners as to whose profile their PVCu windows were made from. As expected, most replied with the name of the installer as opposed to either the fabricator or the system used. When then prompting them regarding the profile coming from a system house, the one name that seemed to be known was REHAU. Further delving found that the company had conducted a national consumer advertising campaign many years ago but there was still recall of that campaign! Whether that campaign was successful in persuading customers to ask for REHAU profile by name, is unknown, however for whatever reason the company has continued to grow within the UK such that continual investment has been required to keep up with demand and, indeed, changing customer preference. REHAU is not just focussed on profit. The issues of energy efficiency, renewable energy, water management, mobility and future living are all high on the agenda. There is plenty of evidence of this thinking, none more so than at PVCR in Runcorn. This is the recycling centre that not only saves PVCu disappearing into landfill but feeds the extrusion lines at Blaenau Ffestiniog. Although some 15,000 tonnes are processed annually, the company is committed to upping that output to 24,000 tonnes – a substantial 60% increase in processing. To achieve this they are introducing a pre-shredding operation which speeds up shredding while reducing energy consumption by 20%. This preshredding involves two rollers which break down recycled frames into 150mm size pieces, metal components are then stripped from the profiles to then be removed with magnets before the polymer proceeds through the shredding process.
This pre-shredding has been in operation for around eight months and has increased the amount of material that can be delivered to REHAU’s extrusion plant in Blaenau which, in turn, means more Co-ex products can be manufactured and distributed to customers. This has been achieved while reducing energy consumption by employing smaller motors within the machinery. Pretty impressive!
The key priority is the polymer recoverability to meet the 2024 target. Currently about 15% of material is jazz, the impure coloured plastic which cannot be used in REHAU polymer but, in an effort to prevent wastage, this material is now being used for other parts of the frame, such as reinforcement. Around 85% of a recycled frame is re-employed but PVCR are looking to increase this percentage by improving separation and this will be key to achieving their 2024 target.
REHAU’s sustainability programme is wide ranging from recycling to power saving but it also embraces the use of electric vehicles and not just cars for this company – their delivery trucks are also included. The DAF units that have been acquired are high tec even to the point of disposing with those huge mirrors that we are all used to seeing on lorries. These are replaced by cameras such that the cab interior looks like something out of Star Trek with screens everywhere giving the driver an all-round view of what is going on. The simple fact is that those vast mirrors have a very significant effect on fuel consumption and replacing them with cameras reduces the drag.
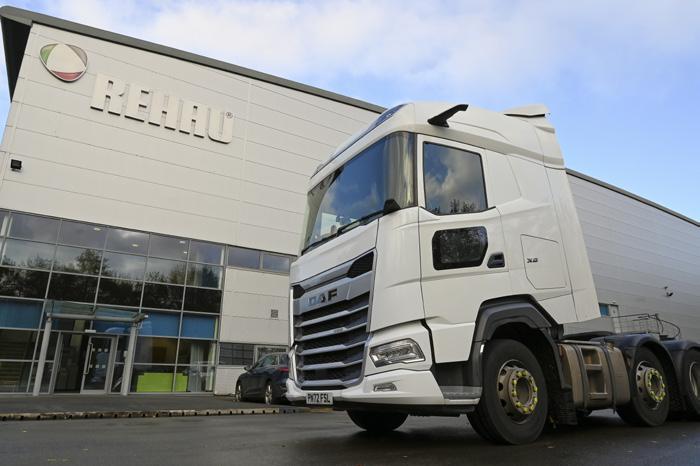
These are the vehicles that ship the recycled material to the extruders based at Blaenau and that feed REHAU’s ever growing demand for profile. This growth has seen significant investment at Blaenau which has come a long way from making garden hose, white goods items and small automotive parts back in 1979 with window extrusion starting in 1987. From those early years that saw the plant employing just 20 people now boasts a workforce of some 246 plus 8 apprentices after having four major expansions. This is a busy site working 24 hours per day, 7 days per week.
Over the years it has developed a selfsufficiency with its own purpose-built mixing department, automated process compound production, a melt filtration department which converts the with a capacity of 1,100 tonnes per month converting post-consumer material ready for Coex production fed in parallel from its 17 external silos for raw material storage. There is also a semi-automated process for production of coloured blends and a 90-ton external silo dedicated for white blend with a screw feeder process to supply extrusion lines.
The extrusion department has a production capacity of over 3000 tonnes per month and employs multiple extrusion lines. These produce profile lengths of 5.3 to 6.5 metres that are packed in purpose built stillages to ensure protection during handling.
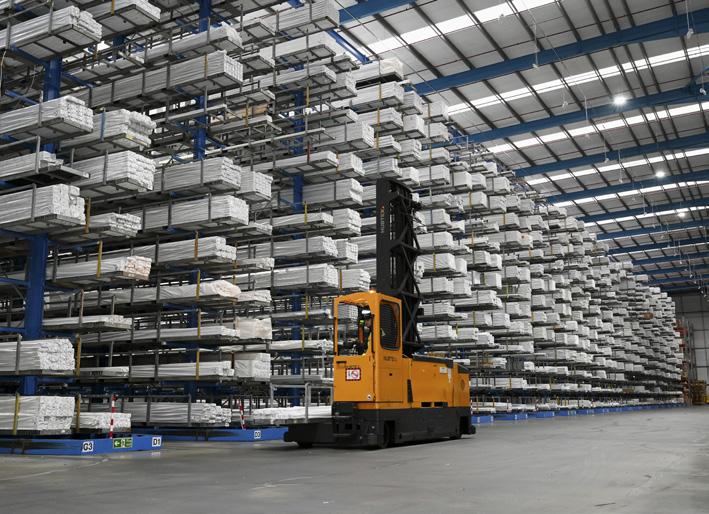
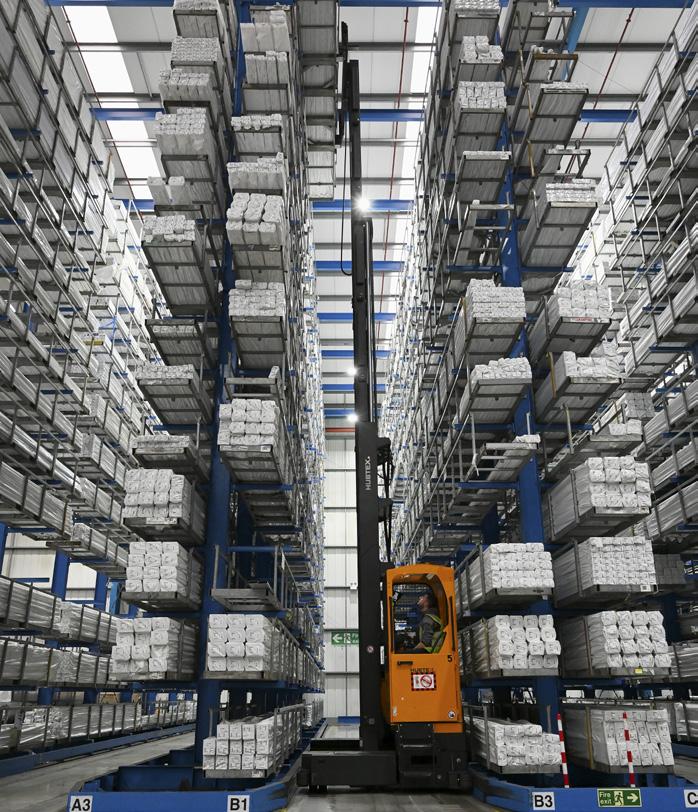
Again, as part of their sustainability programme, 99% of plant scrap is recycled. 30% of the profile produced is processed further with the addition of a wood effect or uni-coloured foils and the lamination department has a production capacity of over 850,000 metres per month.
Importantly, this was one of the first lamination plants that adopted water-based primer in the processing, moving away from the solvent-based primer that was originally utilised. Additionally, it was one of the first UK plants to convert from lead-based stabiliser to calcium organic stabiliser.
Very significant investment has been made at Blaenau with processing capability enhanced with the addition of two new extrusion lines and a double-sided lamination line. It has installed its sixth coextrusion line, which became operational in November, while a new mono line will be up and running in the new year.
The incorporation of the new lines is in response to increasing customer demand for mainframe white and laminated window frames. The facility’s ability to retain quality while increasing capacity was recognised when the facility achieved a 96.7% rating in a recent Lamination Target Process audit, conducted by technical experts from REHAU.
So what are the end products that are produced at Blaenau? Well, there’s the 60mm window and door system; the Total 70 system with its chamfered range that includes the Co-Ex profiles, the sculptured range, fully reversible and Rio, the Flush Fit casement window. There is also Heritage the PVCu vertical slider and multiple other ancillary profiles. Yet REHAU haven’t forgotten their origins with hosepipes and the like and nowadays produce the RAUVITHERM PE-Xa district heating underground pipe at Blaenau. Ensuring the highest quality is maintained is essential and REHAU has a full range of testing and quality assurance including laboratory testing, charpy and ball drop testing and they are proud to comply with BSEN 12608 with its bi-annual independent audit and profile testing while REHAU’s Quality Management System is based on the requirements of ISO9001:2015.
On leaving Blaenau the products find their way to the impressive distribution centre at Runcorn where product is neatly racked ready for picking and despatch. The size of this centre and the height of the racking is quite staggering and, watching the quiet and efficient distribution taking place, is impressive and is sure to be reassuring to REHAU customers who are awaiting product to fabricate windows and doors.
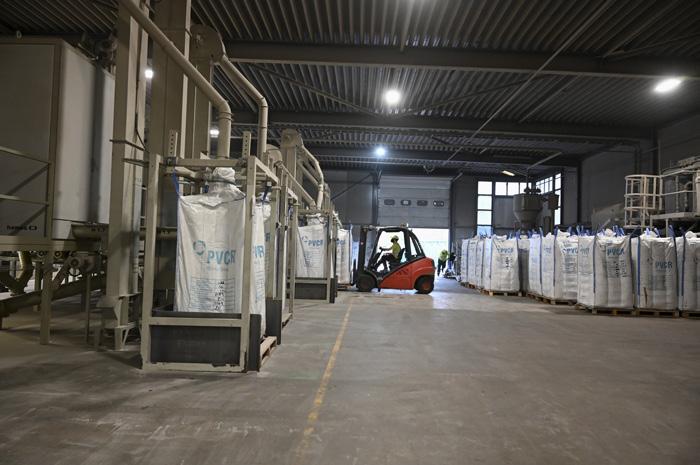
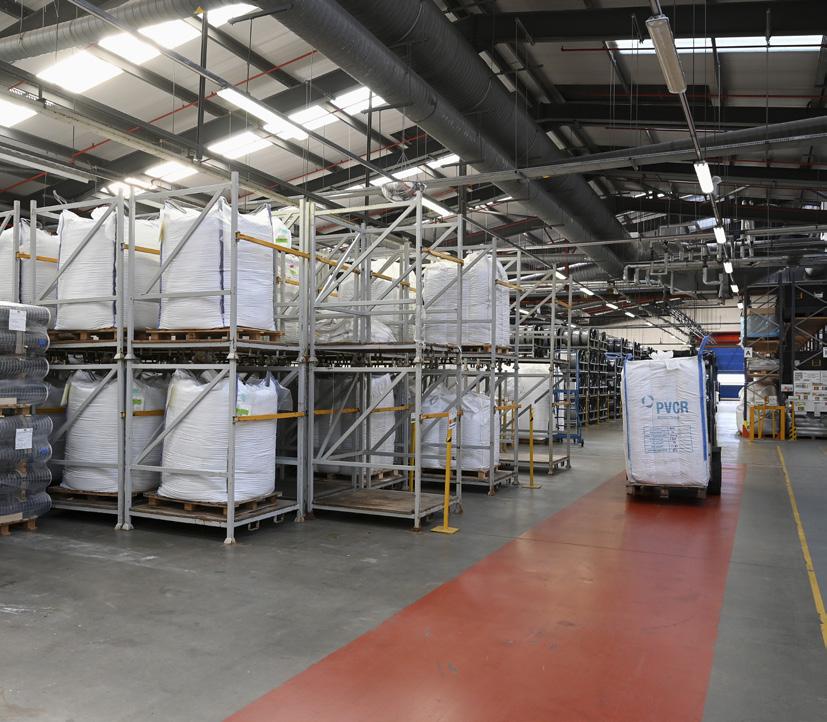
It is interesting to note that REHAU, while concentrating on production and bolstering its green credentials, has not ignored its workforce with additional support brought in to support the running of the lamination lines for 5 days per week which, in turn, has promoted the most technically experienced operators to team leader positions.
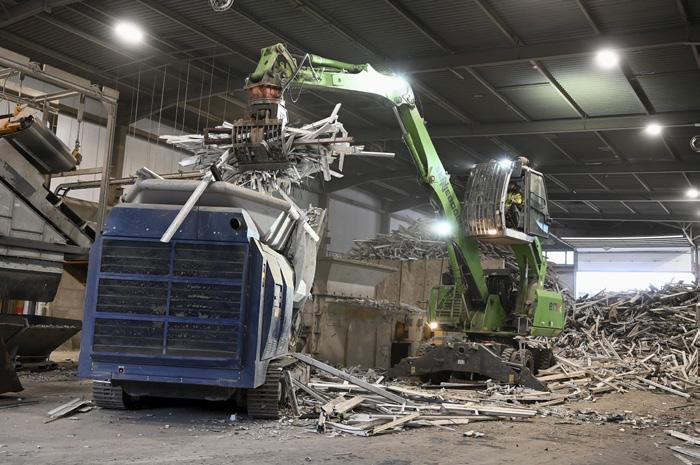
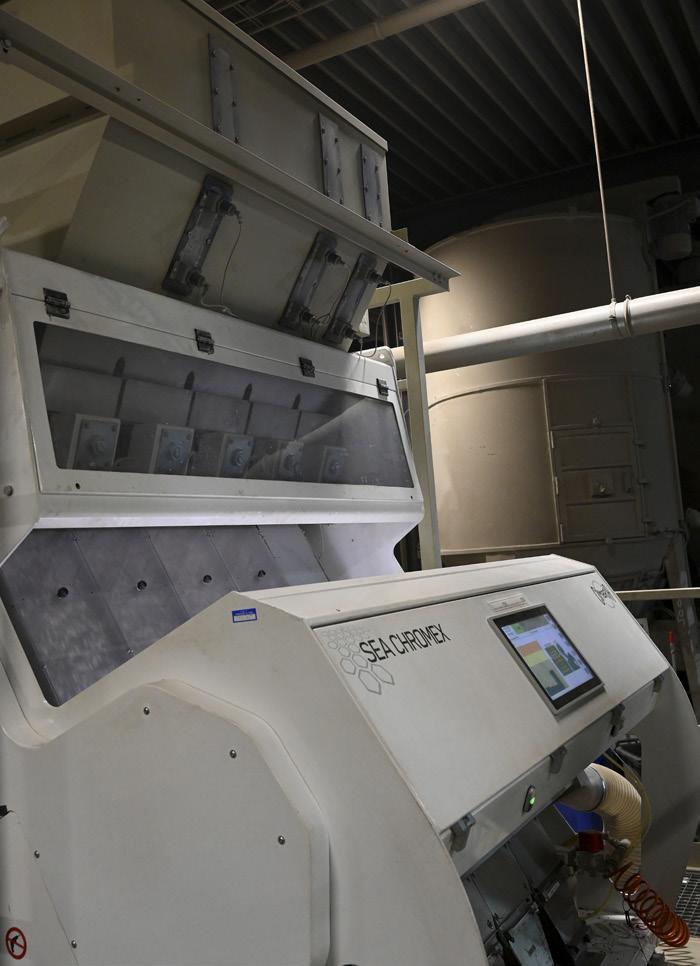

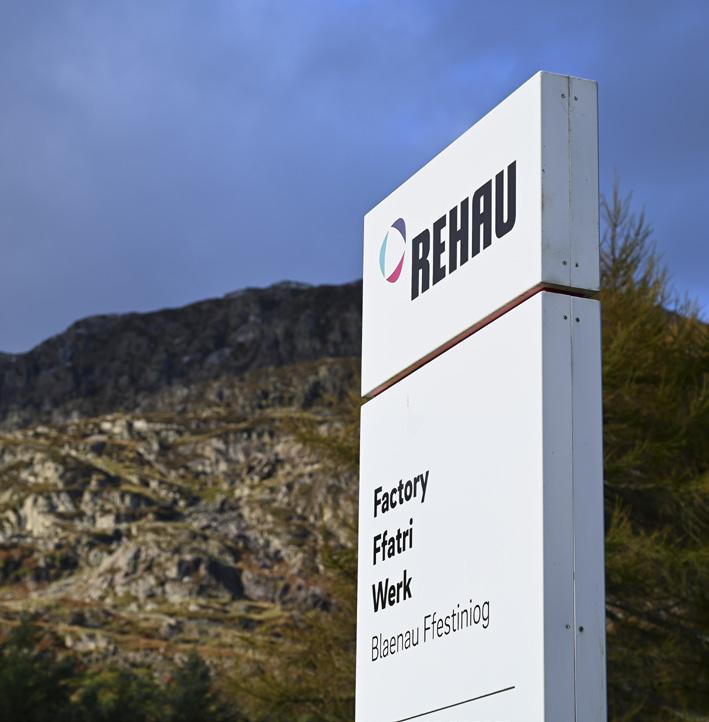
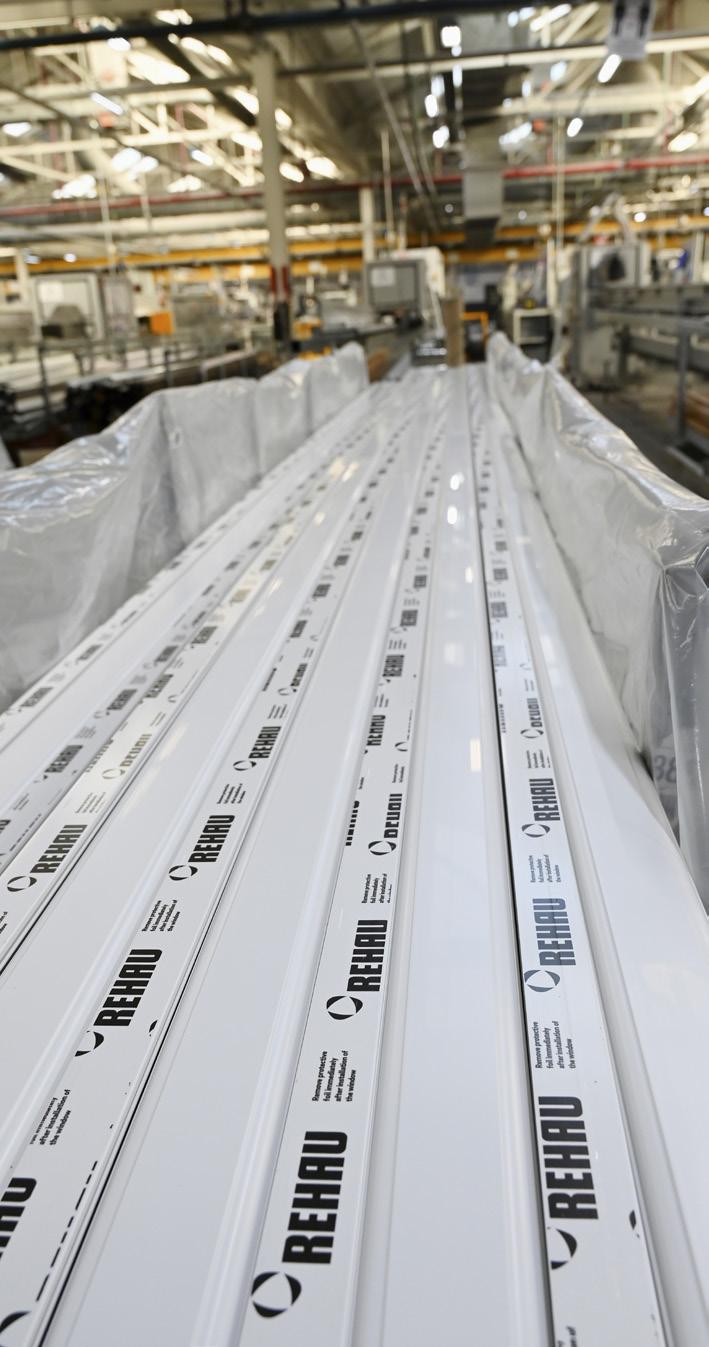
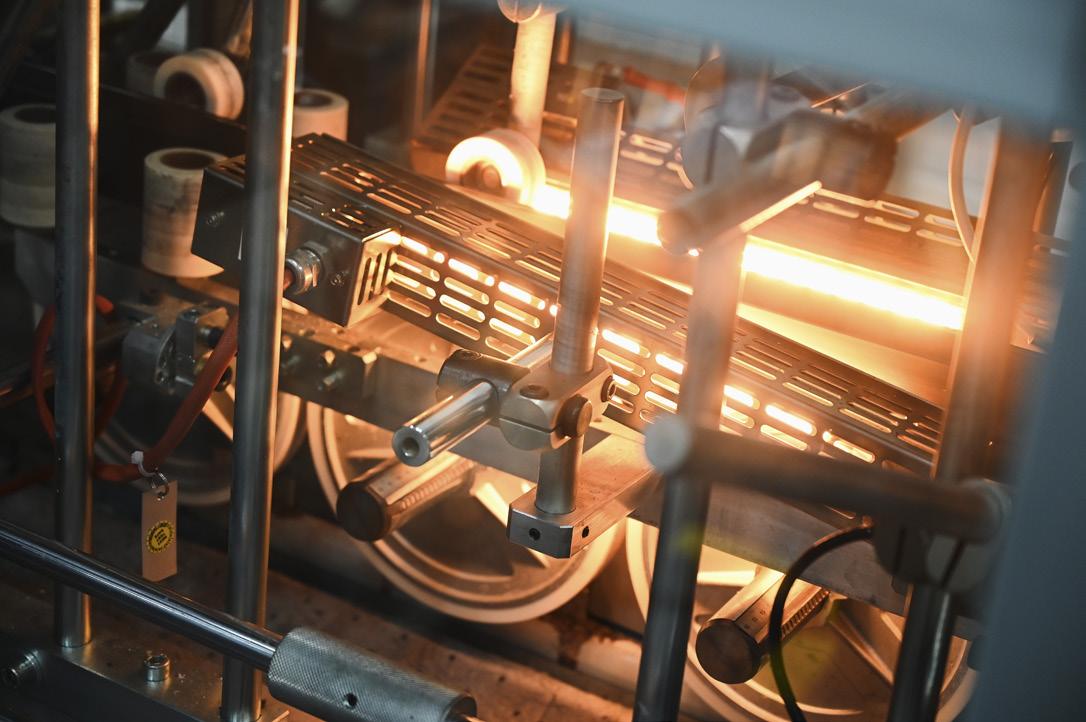
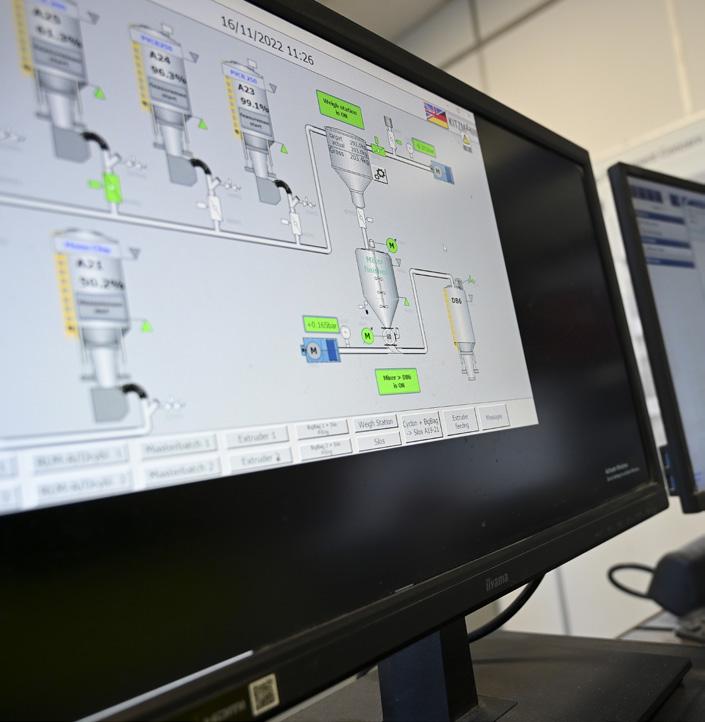
The internal promotion policy has also seen Gwyn Jones promoted to the Plant Director position from his previous role as Production and Logistics Manager.

Much has been talked about attracting new blood to the industry and, particularly, the role of apprenticeships. Finding that Gwyn started life at REHAU as an apprentice electrician at Blaenau, and has worked his way up to be the Plant Director, is a fine example of what can be achieved and the value of apprenticeships in our industry.
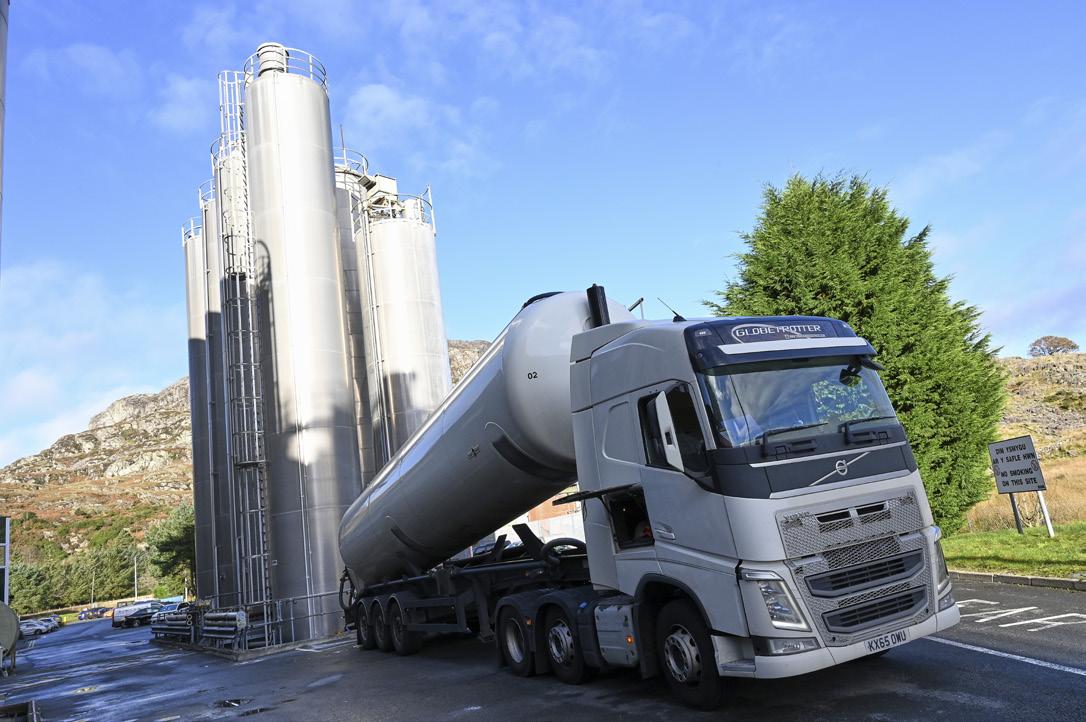