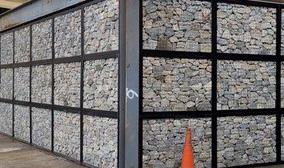
5 minute read
Weld mesh sets new gabion trend
from IMIESA April 2022
by 3S Media
The Midrand site's wall thickness is 300 mm
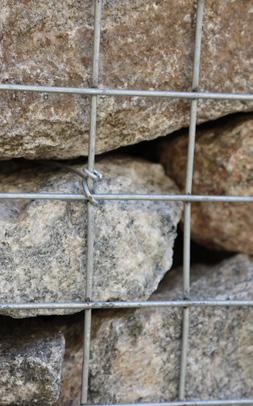
Advertisement
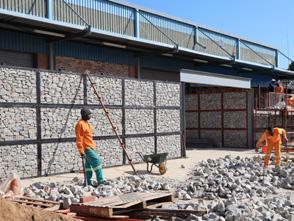
The traditional role of gabion wire mesh baskets as an environmentally engineered solution is evolving with a parallel growth in weld mesh systems for architectural applications. In both instances, their rockfilled composition provides a natural aesthetic appeal and a value-engineered solution, says Louis Cheyne, managing director, Gabion Baskets.
By Alastair Currie
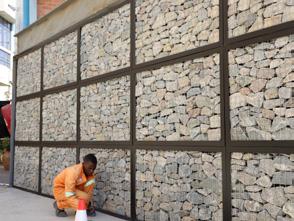
Double-twisted hexagonal wire mesh is the standard product used to form gabion baskets and gabion mattresses. Within an environmentally engineered context, this product characteristic is important because it enables a degree of flex. This is crucial in river applications, where gabion retaining walls and weirs will experience varying hydraulic conditions and potential debris impact. However, this degree of flexibility is less important for lateral soil support applications on land – a classic example being slope stabilisation with mass gravity retaining walls. Here, the key consideration is the permissible degree of permeability factored into the design, given the fact that a typical 1 m x 1 m rock-filled wire mesh gabion has a void percentage of around 35%. Controlled drainage is essential to avoid hydraulic pressure build-up behind soil-retaining structures. This is achieved via the integrated use of either woven or non-woven geotextiles, depending on the soil type.

Weld mesh for engineering tasks
“Wire mesh remains the most widespread product employed for environmental engineering. However, within this segment, we are also experiencing growing demand for weld mesh in roles like landscaping and retaining walls where the priority is aesthetics, especially where a more exact, flat finish is required. Very precise tolerances can be achieved, generally within a range of 2 mm to 4 mm and, in most cases, geotextiles are still required,” Cheyne explains.
“However, the fastest expanding market for weld mesh gabions is in the architectural field for projects that include residential, office and commercial developments,” Cheyne continues.
Popular weld mesh gabion roles include pillars, free-standing feature walls, boundary, terracing and retaining walls, and even fireplaces.
Configurations and custom builds
The most common weld mesh configuration supplied locally has a 50 mm x 50 mm
Clinton Cheyne (left), operations manager at Gabion Baskets, together with managing director Louis Cheyne
Individual steel framed rectangular gabion box panels were bolted together to form this architectural wall section
Approximately 35 m3 of granite rock fill was used to fill the gabion box panels, with material handsorted and shaped on-site
aperture and is fabricated using 3 mm diameter Class A galvanised steel wire. Alongside this, Gabion Baskets supplies panels with a 50 mm x 100 mm, and a 75 x 75 mm aperture configuration, both of which provide a lesser degree of rigidity compared to the 50 mm x 50 mm specification.
Made-to-order weld mesh gabion baskets are fabricated at Gabion Baskets’ factory in Johannesburg. For applications like building cladding, weld mesh is also supplied in roll or panel form. Rolls measure 2.1 m wide by 30 m in length. That equates to an area of around 63 m2 when supplied with a 50 mm x 50 mm aperture. Panels can then be cut and wired together on-site according to the architect’s or engineer’s design requirements.
“Weld mesh has definitely caught the imagination of designers, and we’ve responded by providing custom solutions,” says Cheyne, adding that the company provides turnkey design, installation and project management services.
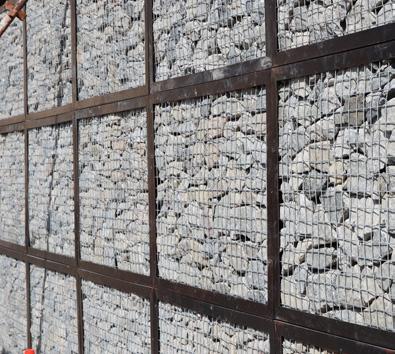
Steel frame design for Midrand wall
A recent example is a project in Midrand where the client presented a design proposal that comprised a combination of free-standing brick work and weld mesh gabion walling as part of a building extension.
The final design comprises a weld mesh gabion wall measuring 2.7 m in height, with a total length of around 40 m and a width of 300 mm. Approximately 35 m3 of granite rock fill was required.
“The unique aspect to this job is that the gabion wall is made up of 3 mm thick steel frame box panels, as opposed to the traditional purely weld mesh wire frame box,” Cheyne explains.
Rectangular in shape, each box panel measures 900 mm in height, 1.50 m in length and 300 mm in width. During installation, the design made provision for four cut-to-fit weld mesh inserts to be slotted neatly into position on the bottom, front, rear and sides, secured in place by the subsequent rock fill. The only exception are the front and rear weld mesh inserts, which are attached with bracing rods.
To build the structure, the box panels were stacked three high in sequence to form one, seamless wall. They are bolted
WELD MESH BENEFITS
• Blends well with existing architectural structures • More rigid than woven mesh, making it easier to build vertical facings, like wall cladding • More appealing than woven mesh for domestic use • Weld mesh boxes are faster to fill and don’t bulge easily like woven mesh • Weld mesh comes in three aperture sizes to suit visual preferences
A section of the Midrand wall
together at the top and bottom, as well as laterally with their neighbouring panels.
Within each vertical three-panel box group is a central 75 mm x 75 mm x 3 mm tubular steel pillar support anchored using screw bolts drilled approximately 200 mm into the existing concrete floor. To add to the overall structural integrity, at designated points, these pillars are welded into I-beams that run along the top of the integrated gabion and brick wall.
The works were completed within a twoweek construction period, with Gabion Baskets providing construction and project management, as well as training for the SMME subcontractor.
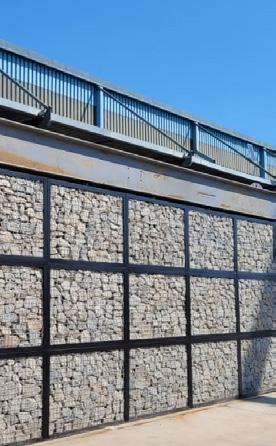
Completed sections
“Gabions provide endless opportunities to combine architectural and engineered elements to create amazing structures, which can also be softened or enhanced with vegetation. We continue to explore the possibilities,” Cheyne concludes.


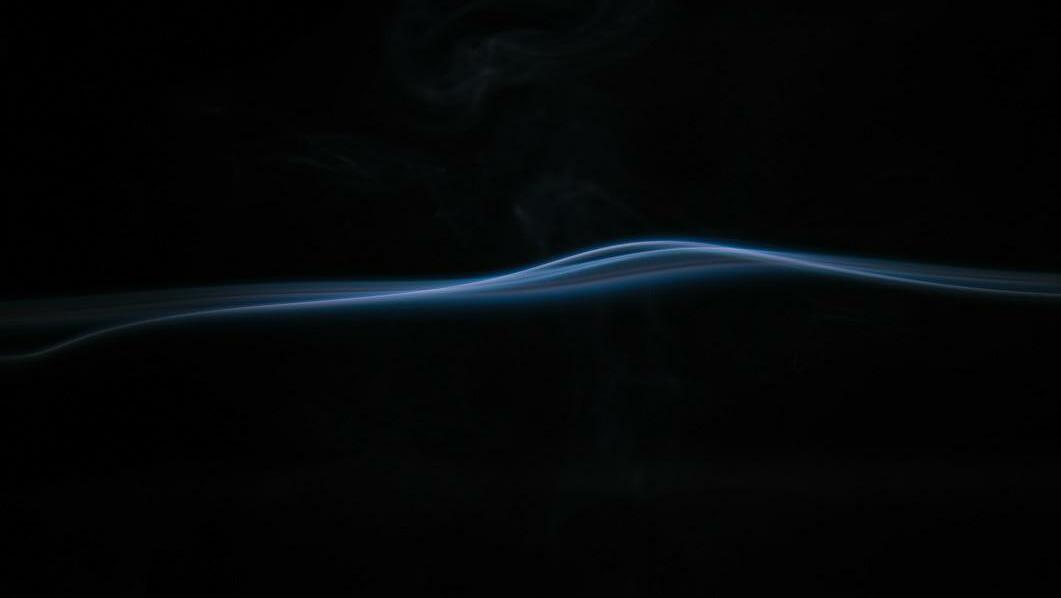
APE Pumps Split Case Pump
Operating Range Flow - 10m³/hr up to 2500m³/hr Head - 4m up to 120m
Applications - General liquid pumping - Power plants - Bulk Water - Steel mills - Refineries - Chemical plants Polihali access road under construction - Cooling and heating systems