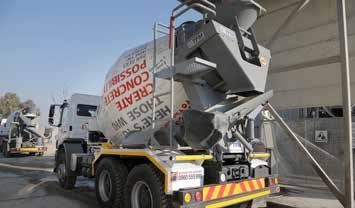
2 minute read
Ways to manage readymix waste streams
from IMIESA August 2021
by 3S Media
The management of waste poses various challenges for the readymix industry and with it a need for sound environmental stewardship. In response, AfriSam has developed a range of innovative solutions that reinforce its commitment to People, Planet and Performance.
AfriSam has pioneered the use of covers on the discharge chutes of its readymix trucks to avoid minor concrete spillages
Advertisement
The sector’s sustainability issues include greywater, concrete spillage and soil contamination; however, one of the biggest environmental headaches for producers is dealing with returned concrete from customer sites, says Russell Wearne, national operations manager: Readymix at AfriSam.
“If we have a quarry site nearby, we are often able to recycle a considerable proportion of concrete that is returned from a site,” he says. “It is dumped in a designated, controlled area of the quarry to harden, and is then crushed and added into our G5 material – subject to the agreement of the customer.”
With the correct planning, AfriSam has also been able to cast blocks and bricks from wet returned readymix before it sets. These have been used extensively on its quarry operations for road markers and other purposes. Where planning allows, the readymix has even contributed to community projects, going into classroom floors of needy schools, among other applications.
Slurry residue
Another potential environmental impact is the slurry residue that remains in a readymix truck after the product has been offloaded. This has to be rinsed out on a daily basis to prevent material hardening on the inside of the drum.
“The resulting greywater is carefully channelled into settling pits, from where we can use it in a number of plant activities to conserve water use,” says Wearne. “On certain sites, the residue ‘slush’ is agitated in a pond, monitored, sampled and reused in the batching plant to mix with the cement, aggregate and sand.”
Covers that reduce spillage
AfriSam has also pioneered the use of covers on the discharge chutes of its readymix trucks, to avoid minor spillages of concrete on-site, as well as en route to or from the batching plant.
“In the unlikely event of any spillage, each plant has a clean-up crew that will respond quickly with the necessary equipment,” he says. This capacity is also valuable as the country’s environmental regulations tighten up generally on the impact of construction activities. A closer focus on possible soil contamination on sites, for instance, means that suppliers must support the contractor’s environmental compliance efforts.
“A truck that leaks oil is a source of soil contamination, so we pay special attention to ensuring this kind of pollution does not occur. If it does, we are in a position to respond timeously and mitigate the impact,” Wearne concludes.
At AfriSam’s readymix operations, greywater is carefully channelled into settling pits. From there, it can be used for various plant activities to conserve water
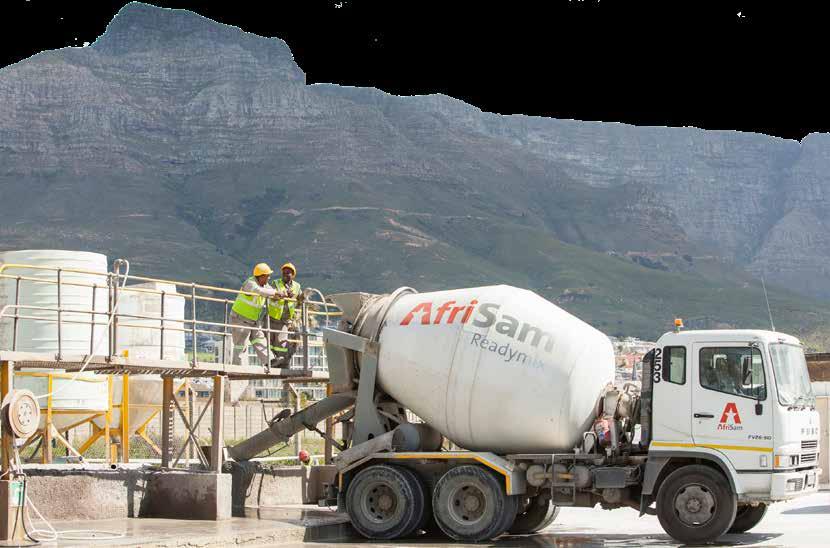