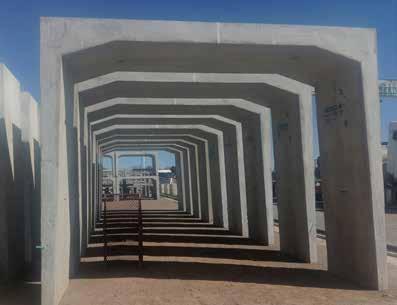
3 minute read
Novel culvert bridge design for village
from IMIESA August 2021
by 3S Media
The use of these secondary materials has become popular – in fact, encouraged – because of environmental and economic benefits.”
the compaction and density of the resulting concrete with positive effects on placeability, bleeding and long-term strength. Good-quality fly ash also has a fine filler effect in stimulating the hydration of the cement up to 28 days – an important consideration for concretes in which large proportions of the cement are replaced by a cement extender.
Advertisement
On the other hand, GGBS is a latent hydraulic material that will hydrate in the same way as cement when mixed with water. So, if GGBS is added to a concrete mix together with the cement, the presence of calcium hydroxide and other alkalis accelerates the hydration of the GGBS, although the rate of hydration of the GGBS is considerably slower than that of the cement. It is thought that GGBS also participates in a pozzolanic reaction, although to a considerably lesser extent than fly ash and CSF. The extent of its involvement in the reaction appears to depend on the composition of the GGBS.
“Since the major contribution of GGBS to the binding effect of the cement phase is through hydration, GGBS concretes are sensitive to inadequate curing at early ages because of this slow rate of hydration. With normal replacement of about 50%, particular care should be taken in curing the concrete during the early period after casting,” he advises.
Density and impermeability
CSF, because of its fine particle size, can fill the spaces between cement particles, which results in an increase in the density of the cement paste phase. This boosts the impermeability and durability of the concrete.
As far as curing is concerned, at normal replacement levels – where about 7% of the cement is replaced by CSF – the resulting concrete may be treated in the same way as Portland cement concrete. However, if the replacement is based on achieving equivalent strength, one part of CSF can be used to replace between three and five parts of Portland cement, depending on the strength level. In this case, CSF concrete is considerably more sensitive to initial curing and care should be taken to avoid surface drying.
“When mixed with Portland cement and water, finely ground limestone is chemically virtually inert, although there may be some minor reactions. But, depending on its fineness, limestone may act as ‘fine filler’ in fresh paste. The effect of limestone on the properties of concrete or mortar depends on the specific limestone, whether a grinding aid is used in production, and the fineness of the limestone,” adds Perrie.
“In general, extended cements are more sensitive to poor, late or inadequate protection and curing, and require more effective curing, over longer periods, to ensure optimal performance of the concrete,” Perrie concludes.
Novel culvert bridge design for village
Outlying rural areas are often confronted with major inconveniences when the rainy season or severe storms come around. Roads become flooded, bridges are submerged underwater or completely washed away, cutting off communities from food supplies and essential services. Ga-Diboye Village, near
Kuruman in the Northern Cape, is such a location.
Rocla recently supplied rectangular portal (RP) culverts and bases, and the link slabs to ensure that stormwater is effectively dispersed without cutting off the Ga-Diboye Village community from its school and shops.
“The Ga-Diboye Village project required RP culverts measuring 3 600 mm x 3 000 mm, with RP bases of 3 600 mm. Rocla is the only company that manufactures RP culverts of this size and we manufactured 32 for this particular project,” explains
Dillon Carter, sales consultant, Rocla.
Unique configuration
“The installation is unique, and a first in terms of bridge design in South Africa in that four rows of eight culverts in length were installed in a culvert-link-culvert-link formation,” he continues.
Bolts and anchor grout were required to secure the slabs to the culverts and were supplied by Rocla and Technicrete’s Mining Division. (Rocla and Technicrete form part of ISG.) A crane hired by South 32 Mine, the project investor, was employed to offload the culverts on-site.
“An integral part of this culvert project were the 3 600 mm link slabs that we supplied, which were crucial to the formation of the culverts for this particular application. The style of the formation was not dissimilar to a truck and trailer concept,” says Carter.
Rocla’s precast concrete RP culverts are normally supplied in 1.22 m lengths and in 50S, 75S and 100S strength classes – but custom-made designs can be manufactured, as was the case for the Ga-Diboye Village project.