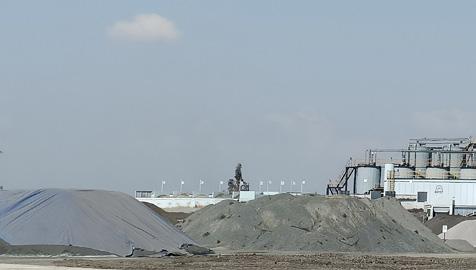
7 minute read
Solutions for sustainable asphalt
from IMIESA August 2022
by 3S Media
Within an environment currently characterised by significant risks, AECI Much Asphalt is putting its focus firmly on sustainability in response to the challenges faced by the asphalt industry following the Covid-19 pandemic.
Trial at the University of Pretoria in collaboration with the CSIR, using nonrecyclable waste plastic as an aggregate and binder modifier in the asphalt
Advertisement
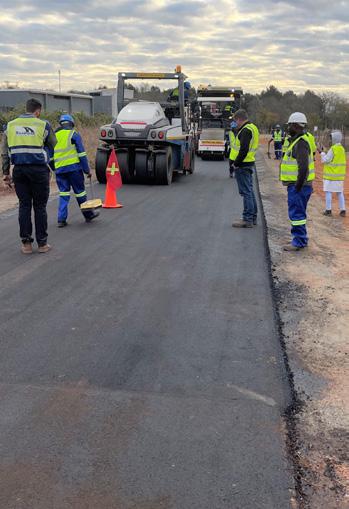
It is not an option to continue as normal and wait for the tide to turn,” says Bennie Greyling, CEO, AECI Much Asphalt. “As a company, we are proactively preparing for what will be a very different future.”
He points out that the Covid-19-induced shutdown of the asphalt industry has been followed by several other potentially devastating impacts. “Delayed and cancelled road construction and rehabilitation projects are now normal for various reasons, despite the public outcry on the condition of our roads,” says Greyling.
Also threatening asphalt and binder production is the fact that only one South African refinery, NATREF, is currently producing petroleum-based products. “We are therefore importing bitumen on a large scale and putting extensive measures in place to ensure that we receive quality products to adhere to our stringent specifications,” Greyling explains.
Advantages of bitumen
Greyling adds that bitumen, as the bottom of the crude oil barrel, is the only crude component material that does not require further combustion processing to be useful in everyday life. “Refined fuels, comprising the remainder of the barrel, are essentially ‘burnt’ during singleuse activities such as heating or transport, adding significantly to the emissions count during their use. Bitumen used during asphalt production does not contribute further to carbon emissions, but instead is neutralised during its many years of useful life in a roadway in its natural state as it was obtained from the refining process,” says Greyling.
AECI Much Asphalt subsidiary AECI SprayPave now produces 10/20 penetration grade bitumen through its multistage bitumen converter in Cape Town – one of only two in the world – using feedstock bitumen from NATREF or through importation.
“This capability is critical to us at present, with no other source of 10/20 penetration grade bitumen available in South Africa,” Greyling points out.
To remain sustainable in increasingly challenging market conditions, AECI Much Asphalt is also exploring new business opportunities, investigating strategies to replace non-renewable aggregate materials in the manufacture of asphalt, and putting measures in place to conserve energy and reduce its carbon footprint.
“Broadly, we aim to seek non-traditional revenue streams, expand our footprint into Africa, and focus on operational efficiencies to remain a best-cost and quality producer,” he explains.
“I am very proud of our teams who are demonstrating their commitment by putting safety first despite all the setbacks of the past few years. Our safety record has improved from one of the worst in the AECI group to one of the best. This is a great platform on which to build our future.”
Driving sustainability
The drive to sustainability for AECI Much Asphalt goes further than the company’s bottom line. Greyling believes that as a leader in the South African asphalt industry and the biggest commercial supplier of asphalt in sub-Saharan Africa, the company has a responsibility to pioneer new and more sustainable, environmentally friendly products that also improve quality, longevity and safety for users.
Aggregates extracted from the earth such as sand, gravel and crushed stone make up about 95% of an asphalt mix by mass. “The need to explore alternative materials that can reduce our industry’s dependency and impact on the environment is critical,” says Joanne Muller, regional technical manager: Gauteng, AECI Much Asphalt. “When the solutions also reduce waste streams that are not recycled into other materials or products, this is a step in the right direction.”
The material most often recycled in the asphalt industry consists of existing sections of road that are milled out due to upgrade or rehabilitation. Most new asphalt produced at
Much Asphalt’s Benoni flagship facility
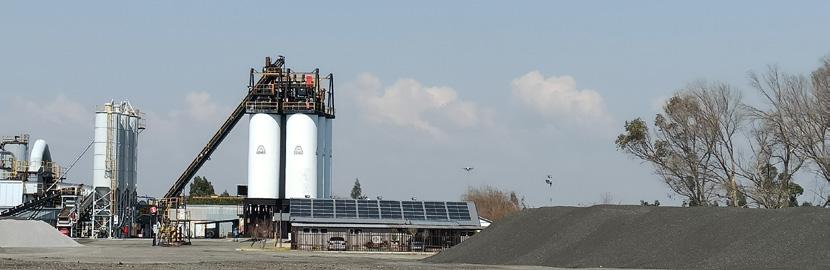
AECI Much Asphalt’s production plants around South Africa contains between 5% and 20% reclaimed asphalt.
“An extremely small proportion of reclaimed asphalt goes to waste, reducing not only the dependency on virgin aggregate from quarries, but also the volumes of virgin bitumen required from fossil fuel industries,” Muller points out.
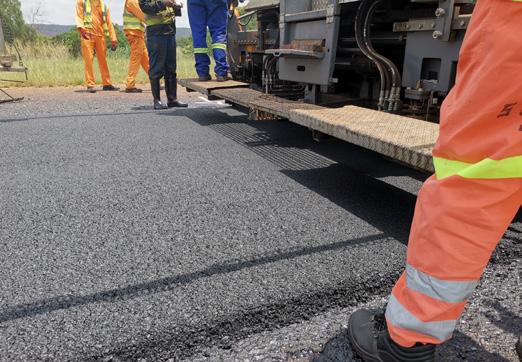
Slag and tyres
AECI Much Asphalt’s extensive footprint has enabled some of its production facilities to leverage other aggregate streams to reduce the use of virgin aggregates. One example is the plant in Witbank where several asphalt products are manufactured using recycled slag aggregates.
Slag aggregates are obtained by processing waste material from smelting operations in steel manufacturing, among others. The waste consists mainly of the flux used to remove the impurities and/or non-ferrous constituent materials from the ore. The replacement of approximately 20 000 t of virgin aggregate with slag aggregate annually over several years has contributed greatly to the drive for sustainable use of materials at this plant.
The use of recycled ground tyre rubber into asphalt mixtures at several AECI Much Asphalt production facilities has multiple benefits. It reduces the volume of virgin bitumen used by replacing about 20% of the binder in the asphalt, aids pavement longevity, reduces noise pollution on the road, and results in fewer tyres going to landfills.
Pushing the boundaries
Some years ago, assessments by the CSIR and AECI Much Asphalt showed the use of non-recyclable glass to be technically viable as a partial aggregate replacement. Certain low-impact niche applications were identified for further exploration and AECI Much Asphalt is collaborating with Interwaste, an integrated waste management provider, in investigating alternative recycling streams for glass waste destined for landfills.
An upcoming trial will involve the production of 20 t of hot mix asphalt, incorporating 10% waste glass, at the Eerste River plant for placement on walkways at the Strand Golf Club in the Western Cape.
Together with the CSIR, AECI Much Asphalt is also actively tackling the significant problem of waste plastics. Two full-scale trials done to date have focused on the proportion of nonrecycled and non-recyclable waste plastic that can potentially be used as an aggregate and binder modifier in asphalt.
Aspects considered include the potential presence of microplastics that may contaminate water courses. However, data to date shows product performance improvements and no environmental contamination.
The mix that went down in the first trial by AECI Much Asphalt using non-recyclable plastic
Energy efficiency
As the production of hot mix asphalt requires heating to temperatures in excess of 140˚C, energy used is a significant factor in the cost and environmental impact of the final product.
Ultra-thin porous surfacing with A-R 2 (warm mix ground tyre rubber binder) on the N5 in Harrismith, supplied by the Bloemfontein plant
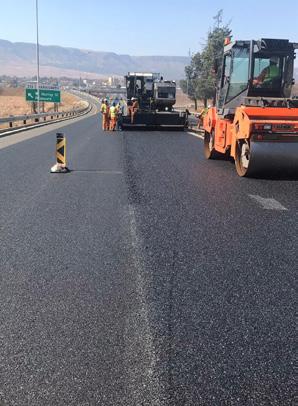
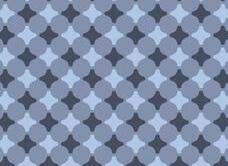
“We are continually exploring improvements to the energy efficiency and carbon footprint of our operations,” says Muller. “Our first grid-tied solar installation was recently commissioned at the AECI Much Asphalt Benoni plant laboratory and offices.”
This pilot project for the group will now be extended to include the Gauteng regional offices and the regional laboratory, in turn expanding the overall impact footprint to other production facilities in the group that use the regional facilities.
Bitumen heating is one of the main consumers of energy at asphalt plants. The Benoni facility already uses natural gas in place of burner fuel to dry and heat material during the production of asphalt. This plant is now conducting a feasibility study into gas generator technology to replace standard heat sources for bitumen heating. A potential CO2 emissions reduction of up to 50% is anticipated from this process.
The project entails the design, manufacture and installation a 201 kVA combined heat and power gas generator to power the heating of the bitumen tank farm for the site. Scavenged heat from this fixture will serve as an alternative heat source in the manufacturing process, with significant positive impacts for product quality and timeous delivery to sites.
All AECI’s business activities are underpinned by the group’s BIGGER values of being Bold, Innovative, Going Green and being Engaged and Responsible. AECI Much Asphalt is confident that its drive for sustainability meets every one of these values.
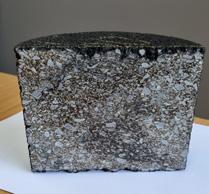
Asphalt core containing waste glass
www.muchasphalt.com
Recycled asphalt feeding from the screening plant
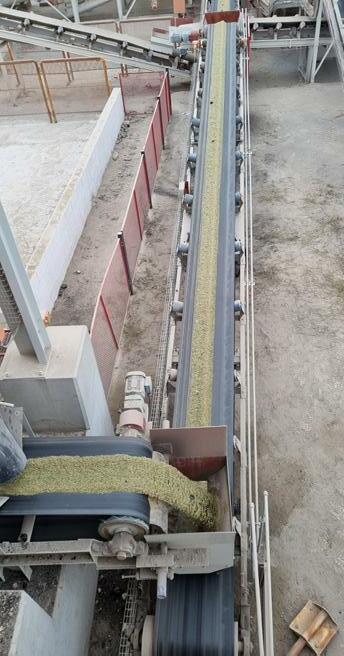
Hot mix asphalt trial incorporating waste glass
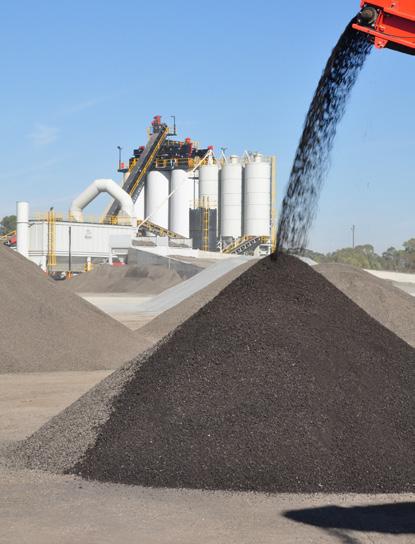