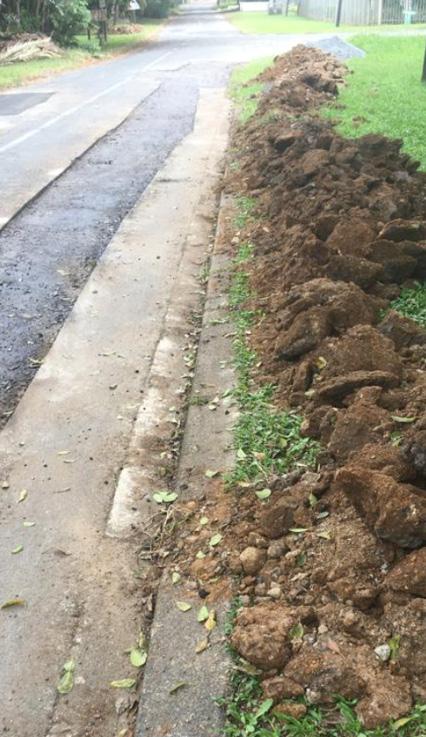
6 minute read
An engineered response to pothole repairs
from IMIESA August 2022
by 3S Media
As with any structure, flexible pavements deliver the best return on investment over their designed lifespan when routinely maintained. Alastair Currie speaks to Johan Hattingh, founding director at PHB Consulting Engineers, about the occurrence of potholes along the way, their causes and repair interventions.
Even the best constructed pavements locally and globally will have some element of inherent failure due to ensuing factors that include geology, roadbed reactions and moisture under the road. At times, these and other causes result in the formation of potholes that need immediate repair. However, their occurrence on new infrastructure should be isolated incidences.
Advertisement
“The starting point is to ensure that roads authorities have an up-to-date asset management system, which includes current data on the health of their road network,” Hattingh explains.
“The ultimate goal is to optimise utilisation through scheduled preventative maintenance programmes according to accepted civil engineering design codes (like TRH4), which include resealing roads at regular intervals. This helps to prevent, or at least reduce, the occurrence and prevalence of potholes as the road ages,” he continues.
Hattingh stresses that getting the basics right is the foundation for any maintenance strategy. If one pothole forms within a 200 m section, then the situation is not a major concern, but it still requires investigation and remediation. However, if a whole road starts to pothole, then it’s time for a rebuild, since any money spent on patching will be a recurring, expensive and pointless exercise. “Any emergency patch has a very short lifetime,” he explains. “That’s fine if it’s an immediate safety issue, and where works need to be opened to traffic as soon as possible, but a lasting and effective repair still needs to be done.”
Determining the causes of failure
Repairing potholes requires an expert understanding. This will determine the underlying cause of the failure, examples of which include deformation, binder properties, ravelling, crack activity, pumping and poor drainage.
“Each distress type tells a story. For example, signs of deformation usually indicate that the problem is deep down; sharp rutting – typically at an intersection – most probably indicates an issue with the asphalt binder properties; while ravelling – or failing from the top – is generally due to ageing,” says Hattingh.
Once an analysis has been completed, this then forms the basis for the intervention, which includes determining the choice of patching materials, the thickness of the asphalt repair, reinstatement of drainage, how long the repair is expected to last, plus any follow-up activities required.
Like for like
“The fundamental principle is that the patching material must be compatible with the existing pavement. This means that a granular base must be matched with granular material of similar properties; a macadam base with macadam material; and a cemented base with cemented material,” Hattingh explains.
Hattingh is a recognised expert on asphalt materials. He founded the Macadam Franchise Company in 1999 and completed his master’s degree in 2012 based on the research and development of slurry-bound macadam (SBM) technology. The remarkable durability of macadam roads has been well proven over the years since the pioneering development of this technology by Scottish engineer John McAdam in around 1820.
“The whole of Gauteng’s West Rand up until the 1970s was built using water-bound macadam materials, while roads in central business districts like Johannesburg have been constructed with penetration macadam. Now, these roads are at the end of their life. Without a full rebuild option, they can be extended for now with SBM patching. No other alternative asphalt patch material will work,” Hattingh explains. He adds that the most common form of macadam failure is ravelling. The layer works condition tends to be sound due to the excellent stone interlock.
Basic construction techniques
Even with the optimum material selected, a patch can still fail if the incorrect repair technique is employed. Some fundamental points noted by Hattingh include: • Limiting the depth of the sawcut joint to 5 mm. A common error is to cut through the asphalt using a diamond cutting blade. This tends to smear the bitumen and close up the voids in the asphalt. Since asphalt is naturally permeable, this needs to be avoided at all costs to prevent moisture entrapment. The softening point of bitumen is between 60˚C to 80˚C, and
Poor joint placement
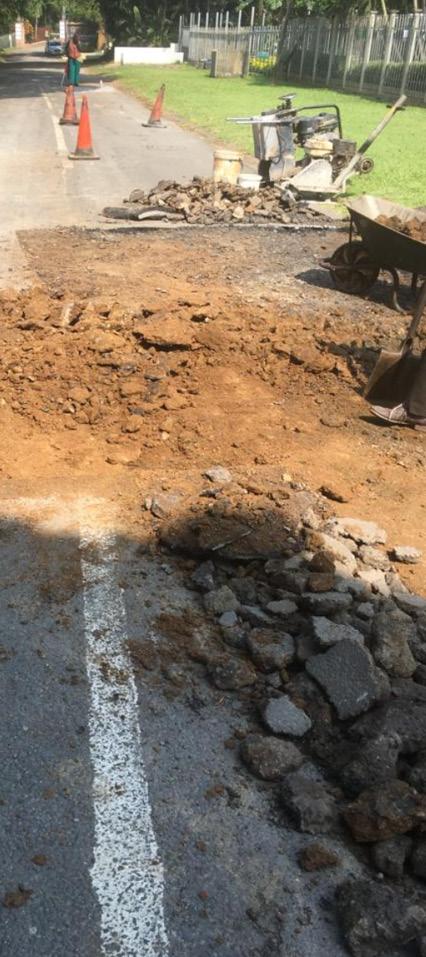
An example of well-intended, but poorly executed, pothole patching. Key errors to note are the incorrect choice of base material, as well as poor joint placement
the road temperature is approximately double the ambient temperature. If moisture is trapped in the asphalt layer, the bitumen starts to soften and strip from the road stone on very hot days. • Avoiding jointing in the wheel tracks. The recommended approach is to vary the joints either between the wheel tracks, or between lanes. • Avoiding vertical excavation walls. The recommended approach is to step or incline the excavation. • Avoiding ‘dam wall’ formation in the layer works. “The layer works of a road can be compared to a laminated beam. The more uniform the road, the better its life. When you break into it, you break into the structural system, potentially aggravating the situation if you don’t understand the root cause,” Hattingh continues.
For example, incorrect patch techniques can change the natural flow of moisture in the pavement, with the potential of creating a reservoir under the wheel tracks. Patches can also change the reaction of a vehicle’s suspension, resulting in poor riding quality and the build-up of stresses in the pavement, which accelerate the formation of new potholes. “It’s comparable to a hammering effect, compounded by a pumping effect where there are moisture concentrations,” says Hattingh.
Segregation of G1 patching material creating a permeable joint
Life-cycle maintenance and rebuilds
It's a well-known fact in industry that it can cost around 10 times more to rebuild a road than to maintain it. Leading authorities like Sanral understand this, setting the benchmark for asset management and routine maintenance on its tolled and non-tolled national routes, responding to and fixing reported potholes within 48 hours. However, this is not the case for a growing proportion of secondary provincial and municipal roads, many of which have severely deteriorated. A recent development in response is the launch in August 2022 of Operation Vala Zonke by South Africa’s Minister of Transport. This is a national campaign to tackle the pothole pandemic, which will be spearhead by Sanral as it engages with provincial and municipal roads entities to map the way forward. The campaign will include the introduction of a pothole reporting app, which will operate in conjunction with an existing Sanral app.
“This is very positive step to stem the current situation. It also provides a great opportunity to train local roads authorities in the right repair techniques and to reinforce the need for an expert determination by suitably experienced engineers,” adds Hattingh.
“However, the best approach going froward is to stick to maintenance plans and steer away from temporary emergency patching, which wastes funds that can be better spent on longerterm in situ recycling and resurfacing operations,” Hattingh concludes.
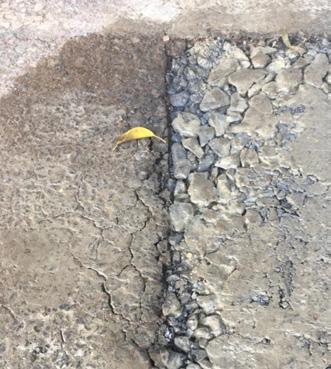