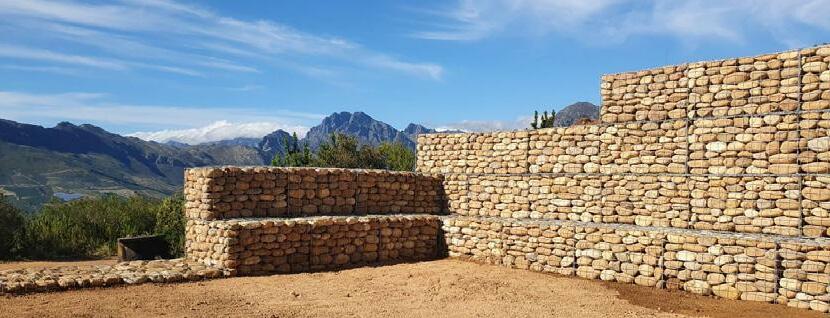
5 minute read
Gabions build a foundation for SMME development
from Imiesa February 2022
by 3S Media
Purpose-designed to shape environmentally engineered structures, gabion designers can use a range of wire or welded mesh options to form them. Being labour-intensive, their construction also presents major opportunities to create community employment, and develop specialist SMME subcontractors, says Louis Cheyne, managing director of Gabion Baskets.
By Alastair Currie
Advertisement
When we started the business some 15 years ago, our core focus was on fabricating gabion systems sourced from locally manufactured Class A galvanised and PVC-coated, double-twisted hexagonal woven mesh wire systems – the latter designed for more corrosive environments,” explains Cheyne.
“We then subsequently branched out into welded mesh products as an allied offering for the environmental engineering, architectural and landscape markets,” Cheyne continues, adding that this service includes design recommendations, costing and project management, as well as integrated solutions such as geotextiles and erosion control blankets. Another key development is the provision of SMME contactor business training and installation services for both public and private sector clients. Via its in-house programmes, Gabion Baskets employs full-time instructors that travel to client sites to conduct installation training – locally and into Southern Africa. In terms of the latter, various projects have recently been completed in countries that include Zambia. Externally, Gabion Baskets refers clients to CETA-accredited FET colleges that include Tjeka.
“Contractors are increasingly approaching us for project design recommendations when it comes to community-based contracts that incorporate gabions. We’re also receiving an unprecedented number of enquires from SMMEs who need advice on how to enter the gabion construction market,” says Cheyne.
“Since our Johannesburg factory borders Alexandra township, we’re especially aware of the unemployment crisis within previously disadvantaged communities. Where the skills don’t exist, we feel an obligation to help aid South Africa’s economic reconstruction and recovery plan through our own or externally facilitated business and skills development programmes. In recent years, this has enabled us to support a growing network of industryaccredited SMMEs,” Cheyne continues.
A boundary wall section constructed using welded mesh and filled with river stones for maximum aesthetic effect
Quality control
Building the right foundation is essential for SMMEs to grow and flourish. Poor design is the starting point for a potential gabion failure. However, even the best design can fail if the correct bracing, lacing and packing techniques are not applied. The classic gabion contains around 35% voids and is intentionally meant to provide a greater or lesser degree of permeability. Understanding and executing the design brief is therefore essential.
Adherence to material qualities is equally important. SANS 1580:2010 sets the standard locally and globally for the correct manufacturing specification for hexagonal steel wire mesh gabions and revet mattresses. In turn, SANS 1200 DK:1996 governs the correct installation techniques for gabion systems.
“Generally, when you buy mesh from a hardware store, it’s commercially galvanised. In other words, it doesn’t meet the SANS 1580: 2010 standard for environmentally engineered applications and will fail prematurely when placed in a corrosive environment,” says Cheyne.
Specifications are application specific
The correct specification will always be application specific and in accordance with the anticipated life expectancy. In a marine or river environment, for example, a more corrosionresistant PVC coated wire is recommended. The alternative is a Galfan with PVC-coated Class A galvanised wire.
Where gabion systems do fail – either through negligence or uncontrolled factors like extreme weather or vehicle impacts – the repair solutions are often straightforward, although this doesn’t negate the added cost.
“Often the damage can easily be fixed with some extra rock and mesh panels reattached onto older baskets. In some situations, the structural design can also be modified to serve or counter new problems encountered, like recurring floods spurred on by climate change,” adds Cheyne.
“The magic of gabions is their design and build flexibility, and it’s not unusual for these systems to last 50 years or more with minimal maintenance. That of course depends on best-in-class installation and optimal material selection,” Cheyne concludes.
WHITE RIVER RETAINING WALLS
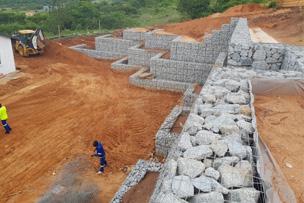
An intricate retaining wall constructed for a new residential development in White River by Gabion Baskets’ local agent, Fanie Joubert. The series of 500 mm wide walls were installed with soil anchor tie-backs to reduce the amount of rock required
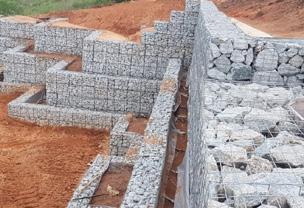
Welded mesh type 50 mm x 100 mm x 3.0 mm was used to form the individual gabion baskets, with some 180 m3 of rock sourced from a nearby quarry. The maximum wall height is 6 m with provision made for the planting of vegetation A rear view of the retaining wall showing the landscaped terraces taking shape
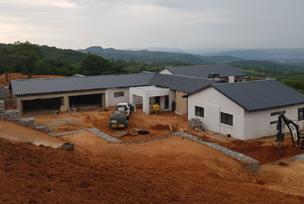
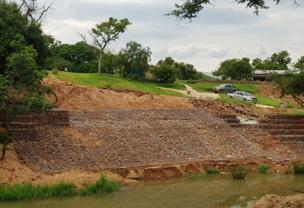
Gabion mattresses were installed to provide riverbank protection on the 1:2 (30-degree slope) bordering the property. These mattresses were formed using 230 mm diameter Class A galvanised double-twisted hexagonal wire mesh
TIPS TO PREVENT GABION FAILURES
Ensuring a durable installation is interdependent on key factors. These include:
Design
Correct design knowledge and a comprehensive understanding of the theory of gabion structures are essential, since they perform in unique ways that differ from structural and precast concrete installations.
Retaining walls
Here there are five modes of failure to note: - overturning - sliding - overall stability - founding bearing pressure capacity of the soil - the internal stress of mesh panels/mesh systems.
Channel lining
- Limiting the water velocity on mattress linings depends on mattress thickness, rock size and type, plus correct packing. It’s important to ensure that there are no small rocks or fines in the mattress, as these will be lost due to hydraulic forces, subsequently undermining mattress performance. - It’s vital that correct cut-offs, which include wing walls, are installed upstream for adequate river undermining and outflanking protection. - Correct specification on mesh type. It’s recommended that designers specify a thicker 2.7 mm diameter wire instead of 2.20 mm mesh on very sandy sites. As an additional protective measure, PVC coating should be specified where there’s a possibility of heavy scouring and/or corrosion.
Keep to the specifications
Gabion wire systems must adhere to the SANS 1580 specifications to make sure they perform optimally.
Installation
Making a design work in practice requires best-in-class installation techniques. Key points to note here include: - Ensuring that the entire project team have the necessary skills and experience. This requirement encompasses the gabion labour/installers, supervisors, and resident engineer. - Certified installation training should be provided where needed. - Adequate site supervision will yield the best results.