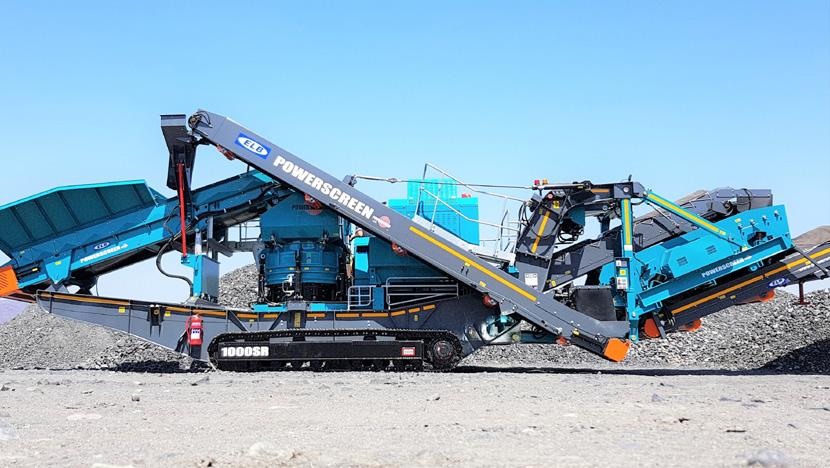
9 minute read
The evolution of a screening legend
from Imiesa February 2022
by 3S Media
While new entrants have come and gone, ELB has stood the test of time as Powerscreen’s dealer since 1994 and Dickson has been part of the team from inception. An OEM with a proud history, Powerscreen was founded in 1966 in Northern Ireland, and is widely regarded as one of the pioneers in crushing and screening mobility – taking the machine to the material in a revolutionary breakthrough to improve efficiencies and productivity.
“The past 28 years has seen significant research and development milestones, as the market shifted from wheel-mounted to self-propelled track-mounted mobile crushing and screening plant,” says Dickson, adding that the Powerscreen series meets niche application requirements in the aggregates, mining, and recycling segments.
Advertisement
In addition to the Powerscreen range, ELB is also the dealer for Terex Minerals Processing Systems Products, which incorporates Terex modular, portable, and static crushing and screening equipment. A more recent development is ELB’s introduction of Powerscreen’s ProStack tracked conveyors.
“Initially, tracked machines were relatively small and compact,” recalls Dickson. “Back in the 1990s, for example, one of the largest mobile twodeck incline screens fielded by Powerscreen was the Chieftain 1400 with its 14-foot hopper and 440 tonne per hour (tph) capacity. Today, it’s one of Powerscreen’s midrange machines, with this class led by the Chieftain 2200 650 tph unit.”
From the onset, ELB achieved major gains in South Africa with the Powerscreen MK 11 mobile screening unit, with hundreds sold locally, many of which are still operational. This was a wheel-mounted machine set up for an approximately 150 tph throughput. Targeted users included contractors looking for a lighterweight machine capable of screening a diverse range of products – from gravel and sand to topsoil.
Forming part of Terex Corporation, Powerscreen is one of the world’s most recognised brands in the evolving field of mobile crushing and screening. It is represented in South Africa by ELB Equipment (ELB).
Alastair Currie speaks to Heath
Dickson, applications manager and product specialist at ELB, about market developments.
Crushing developments
Mobile screens were soon joined by their crushing counterparts following Powerscreen’s acquisition of UK-based OEM Pegson (now Terex Pegson) in 1996. Powerscreen was in turn acquired by Terex Corporation in 1999. Then in 2009, the Pegson and Powerscreen product lines united under the Powerscreen brand. Popular modern-day models include the 400 tph Premiertrak 400X jaw crusher, the 230 tph Maxtrak 1000 SR cone crusher, and the 350 tph XV 350 vertical shaft impact crusher.
“As with the screens, Powerscreen’s mobile jaw, cone and impact crushers have become progressively more advanced and – in some cases – larger to meet the needs of mines and quarries,” Dickson continues.
A prime example is the Trakpactor 550 horizontal shaft impactor (HSI), capable of up to 550 tph, which is being introduced for the first time to the South African market. The first unit will arrive during Q1 2022.
Demolition and recycling
Among other applications, HSIs are ideal for heavy-duty processing of reinforced concrete and building rubble in the demolition market. They provide an excellent mass reduction ratio and are only limited in terms of feed size. Where this is an issue, contractors can run the material through a primary jaw crusher first.
To safeguard against potential belt damage caused by rebar, Powerscreen has developed a deflector plate. The 45-degree angle of the plate is designed to guide rebar onto the conveyor belt and not through it. Specially positioned magnets are then designed to remove the rebar as it passes down the belt.
“The setup will depend on what the downstream material requirement is – in other words, whether the crushed material is being resized for disposal to landfill or being recycled for markets that include G5 sub-base road material. That will in turn influence the type of screen setup required,” Dickson continues.
Application advice
Optimising crushing and screening trains is the key to cost and production efficiency. For this reason, ELB’s application team, headed by Dickson, provides expert advice on machine selection, setup and preventative maintenance based on the material and site conditions. Comprehensive operator training is also provided.
“No two sites are exactly the same since there are unique factors to consider like the moisture content of the material, as well as the size and
type of materials handling equipment being used, such as excavators and wheel loaders,” Dickson explains.
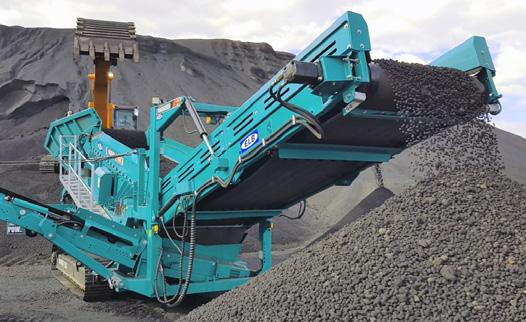
Mobile conveying
One of the biggest challenges facing contractors is managing the materials handling component. Tracked screens and crushers are designed to be compact enough to fit on a low-bed for on-road transport. That invariably means material stacking heights under the belts will be compromised. The main tools to keep production flowing are front-end wheel loaders, constantly moving screened material to nearby stockpiles.
In response, Powerscreen’s ProStack mobile tracked conveyors are masters in materials handling, passing on fuel burn savings of up to 25% when compared to a medium-sized wheel loader. The screen operator controls the diesel-powered operation of the conveyor remotely.
“We have one conveyor unit that can put 7 500 m3 at 180 degrees on the floor,” says Dickson. “What that means in
practice is that plant availability can shoot up from say 60-70% to 95% overnight because crushing and screening plants are not standing idle waiting for loaders to remove full stockpiles.”
Backed by one of the largest branch networks in South Africa, ELB is well placed to support customers nationwide in terms of its crushing and screening equipment offering.
Adds Danie Gerber, director at ELB: “Across the construction, earthmoving, and mining segments, ELB product lines provide integrated solutions for our clients. Our application specialists in all fields proactively engage with customers to ensure that all their questions are answered. In that way, we can provide best-in-class solutions.”
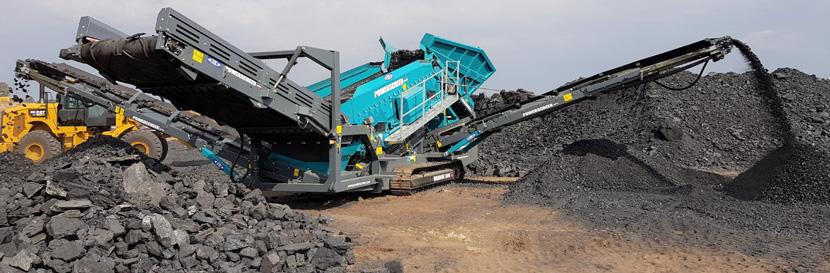
CTRACK LEADS THE WAY WITH CONTINUOUS INNOVATION
Recently celebrating its 35th birthday, Ctrack – South Africa’s leading fleet management and asset monitoring solutions provider – is continuously innovating to provide its customers with the latest technologies in an ever-changing environment.
South Africa’s harsh economic climate, especially over the last two years, has meant that Ctrack’s product development has had to cater for unique business difficulties, while improving efficiencies for owners who must ensure positive cash flows in a highly competitive market.
When developing and refining its operations, Ctrack always considers the five keys of fleet management around which all solutions are developed. Risk, Cost Control, Fleet Utilisation, Operations Control and Asset Control remain at the core of all the solutions that Ctrack offers.
OTR (On the Road) solution
Ctrack’s high-quality, reliable, fleetspecific, in-cab solutions that operate with Ctrack’s On-The-Road (OTR) application are now also available for mobile Android devices, eliminating the need for a second piece of hardware inside vehicles. A basic Android 6 device with 2 GB RAM, an internal GPS and Bluetooth will suffice. The OTR solution combines navigation and fleet experience into a platform that integrates with Ctrack’s software platforms for easy data extraction.
Drivers are a key part of running fleets successfully and efficiently, and Ctrack’s OTR solutions allow drivers to complete their daily tasks as required. Features include driver behaviour monitoring, navigation, driver status, messaging, task management, voice calls and behaviour history. This new development saves operators money while empowering their drivers with a powerful tool in hand.
SMILE script
Ctrack’s unique SMILE script software capability is the perfect solution for challenging operational environments and bespoke solutions. With SMILE script, operators can create unique efficiency and risk outputs that create endless opportunities to measure and solve an operator’s critical KPIs.
For example, in high-risk environments such as cash-in-transit or valuable goods deliveries, integration through SMILE script with risk-reducing technology (such as gunfire detection or foam encapsulation technology) – plus the ability to match various planned delivery addresses and ensure complete control of high-risk packages – leads to unique monitoring and reporting options in the online software platform. This ability creates the option to immediately activate risk mitigation actions, reduce risk and improve customer service levels.
The same system used within agricultural sectors, such as the milk industry, allows fleet managers to set up geo zones with predefined speed limits on certain routes. Speed can be controlled on gravel roads by activating a speed limiter. These simple
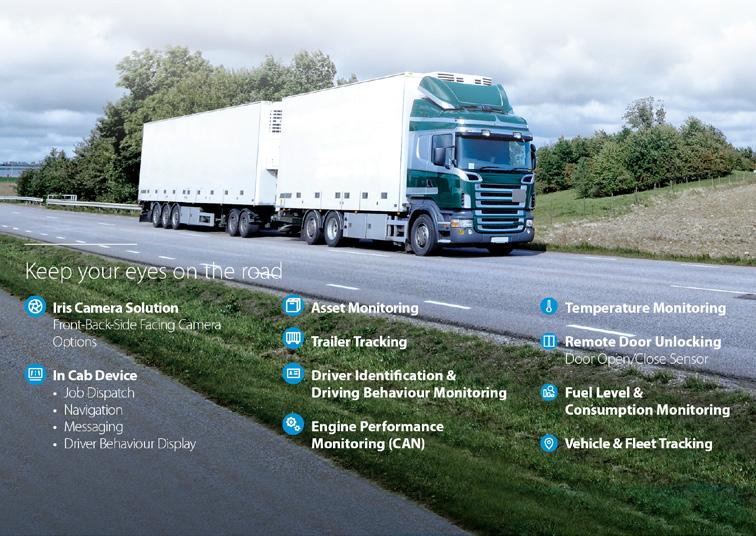
yet effective actions reduce wear and tear on the vehicle, reduce warranty claims and, in essence, mean the vehicle spends less time in workshops. The uptime of the vehicle again brings about improved vehicle efficiency and pushes service levels to the next level within service level agreements for fleet clients.
Fatigue alerts
Driver fatigue is a very serious problem with high demand on production and service delivery. By creating a SMILE script to monitor the driving hours, the Ctrack device can be configured to audibly alert the driver when the driving time limits or distance are reached. If the driver chooses to ignore warnings, the Ctrack technology, through the SMILE script, can put the vehicle into limp mode (reduced speed and engine power) to ensure that the driver takes the required break.
Jamming
A growing threat to the economy and various industries is that of jamming. This unscrupulous practice directly impacts fleets’ risk and not only interferes with the transmission of telematics data – which has become a vital part of successfully running a fleet operation – but can also prevent the tracking of vehicles or assets as part of a stolen vehicle recovery attempt. Ctrack’s jamming detection technology reacts accordingly by implementing several mitigating protocols.
Owning and operating vehicles efficiently, no matter the industry, is reliant on information. Having the correct information in a tangible format is imperative to making the right decisions.
24-hour monitoring
The Live Productivity Dashboard, which forms part of the online software suite, provides a 24-hour timeline of vehicle or asset movement, allowing for the quick and easy dissemination and management of fleets. Users can view the movement, stationary times and driving times in a single graphical view. Stopping locations and operating times allow fleet managers to identify unauthorised usage of vehicles quickly. Ctrack’s Fleet Monitoring Service is a complete outsourcing option of fleet control room activities and a perfect solution for managing larger fleets. Analytics of data while considering highly proficient hindsight, insight and foresight, and concise reporting allows for the streamlining of a fleet operation, enabling business owners to spend more time managing their business.
Real-time support is on hand as dedicated fleet controllers meticulously monitor vehicle movements, route control, incidents, alerts, and alarms. The thorough interrogation and interpretation of data allows for easier decision-making and ultimately reduces costs and improves operations.
Ctrack has industry-specific solutions to monitor, manage and control various assets – including cars, trucks, trailers, containers, generators, packages and confidential deliveries and the software to back it up – which is why the company is a one-stop shop for all your fleet management needs.
