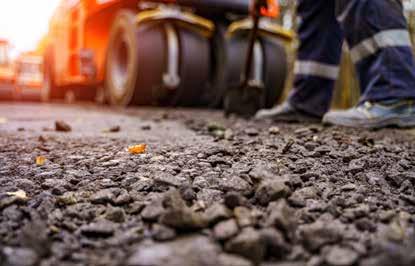
4 minute read
Conforming to COTO specifications
from IMIESA January 2022
by 3S Media
definite demand for this for longer-term projects. At the other end of the spectrum, though, contractors are looking for more rapid deployment, where the entire unit can be moved in one go for on-site commissioning within days, rather than weeks. “Our new trailer system meets this requirement,” Lehman continues.
First mobile retrofits
Advertisement
One of the first plants to be retrofitted by Kenzam was an ACC Countermix mobile plant produced at Ammann’s factory in India. ACC Countermix models in the range extend from 90 to 120 tonnes per hour (tph) with the capability of processing up to a 15% recycled asphalt (RA) mix.
For higher-specification requirements, like Sanral-type projects, where the minimum RA component is 25%, with an average of 30%, Ammann’s ACM Prime 100 tph to 210 tph continuous mix plants fit the bill perfectly. “We’ve redesigned the popular mid-range Prime 140 plant to specifically meet the Sanral RA specification, and South African road-legal towing requirements,” Lehman explains.
Static plant retrofits
Alongside the mobile segment, the Ammann Group is further addressing the needs of customers worldwide looking to extend the life of their static plant investments. Older plants can be retrofitted to keep pace with new environmental codes, as well as more modern mix designs. By modernising at a fraction of the cost of a new static plant, Ammann offers this solution for its own as well as other OEM plants. In some cases, plants older than 30 years can be successfully retrofitted if their condition has been well maintained.
All projects are managed via the Ammann Retrofit Centre in Austria, which relies on proven processes and experienced technicians to troubleshoot any issues and ensure superior results.
“One of the strategic advantages of the Kenzam alliance is their well-established manufacturing arm, which enables us to implement Ammann static plant retrofit services, locally and regionally,” Lehman continues.
Allied to this are the host of ancillary products manufactured by Kenzam that support Ammann’s after-market offering. These include drum decanters, emulsion plants, mobile and static bitumen tanks, and mobile laboratories.
“After a long hiatus on Sanral and provincial projects, our customers are reporting renewed tender activity with good prospects for coastal and inland work. In fact, we could see a situation going into 2022 where immediate demand outstrips supply for mobile plants – something the market hasn’t experienced for many years,” adds Lehman.
In terms of recent cross-border sales, Ammann South Africa supplied and commissioned a ValueTec 180 static plant for a client in the DRC. An ACC Countermix 120 plant was also sold to a contractor in Zimbabwe towards the end of 2021. This will be one of the first to be retrofitted with Ammann’s new road-legal trailer option.
Exclusion clauses used by suppliers of aggregates will no longer be accepted on road construction projects. This follows changes to the new Committee of Transport Officers (COTO) requirements that call for the laboratory certification of loads.
Nico Pienaar, director, ASPASA
The exclusion clauses provided some protection from liability in the event of failure of a road or structure but had become a contentious issue in recent times. The new requirements rather call for testing to be done beforehand by the buyer and seller to ensure that the materials meet specifications. Thereafter, laboratory certification is required, and loads need to be inspected and accepted on-site at the time of delivery.
While requiring the utmost diligence on behalf of the supplier to undertake the correct sampling and testing of the aggregates, it also offers a level of protection by preventing the mishandling and contamination of aggregates stored on-site and tested well after the delivery date. In the past, it was found that aggregates stored incorrectly on-site were often to blame for failures.
According to Nico Pienaar of surface mining industry association ASPASA, the surest way to avoid claims against the supplier of materials is to ensure all procedures are correct when sampling and testing materials, as well as keeping careful record of the tests done before leaving the premises and upon acceptance of the materials.
Quality defined, tested and accepted
“We have pushed the concept that quality must be defined, tested and agreed to at the mine. Thereafter, once it has been delivered and accepted, the mine cannot be held responsible, as it has been found on many cases that the material delivered is misused, left outside or not placed correctly. Then when tested, it is often blamed on the supplier and the quarry,” says Pienaar.
“We highly recommend quarries and suppliers of aggregates undertake training that we offer for on-site laboratories and thereafter participate in our annual quality audit to ensure the aforementioned criteria are met and robust enough to hold up to scrutiny in the event of a claim or subsequent court appearance,” he adds.
“The cost of such an audit is approximately the equivalent of a single load of aggregates and may save millions of rand in compensation in the event of a material failure,” Pienaar concludes.