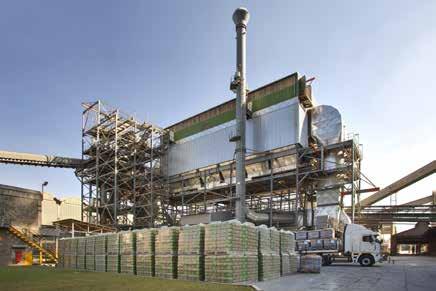
2 minute read
Silo refurbishment at Mamba
from IMIESA July 2020
by 3S Media
As far back as 2000, AfriSam introduced Project Green Cement to actively reduce its CO 2 emissions
Recognising excellence
Advertisement
In addition to taking responsibility for its own actions, AfriSam plays a leading role in creating awareness and establishing open debate about sustainability within the broader context of the industry. One such platform is the AfriSam-SAIA Awards for Sustainable Architecture + Innovation, launched in 2009.
The awarded projects and programmes make a positive contribution to communities and reduce environmental impacts through strategies such as the reuse of existing structures, connection to transit operations at Mamba Cement’s Koedoeskop plant, structural repairs were carried out using Sika Monotop-412
NFG to restore the integrity of concrete sections. Sika says the product is ideal for restoration work, in addition to preserving or restoring passivity to the rebar. In addition, 94 m of cold joints and cracks on the structure were repaired by means of crack injection, using a low-viscosity epoxy, Sikadur-52 ZA.
Our ongoing focus on alternative fuels and resources has allowed us to steadily reduce the amount of coal burnt in our cement kilns.”
systems, low-impact and regenerative site development, energy and water conservation, and the use of sustainable or renewable construction materials.
“AfriSam’s reputation of caring for the planet, people and the environment is evident in the way we manufacture our vast product offering and how we conduct our business,” adds Govender.
“This philosophy is underpinned by the Centre of Product Excellence and applies to all business units to actively measure and manage their impact on the environment, while continuing to produce high-performance products with low carbon
Silo refurbishment at Mamba
Mamba Cement’s operation in Koedoeskop
D
uring silo refurbishment
footprints,” Govender concludes. Key advantages of this product include its shrinkage-free hardening properties, and its suitability for both dry and damp conditions. Sikadur-52 ZA is also solvent free and can be used at low temperatures.
Finally, the top of the silo was waterproofed with Sikalastic-152 and a 4 mm x 4 mm alkali-resistant coated glass mesh fabric to add resistance to moving cracks. According to Sika, Sikalastic-152 affords an extremely easy application process and is a flexible, durable and aesthetically appealing waterproofing product.
This was the first major maintenance project done on this relatively new, oneof-a-kind plant, which is thought to be the first in Africa to possess a waste heat recovery system – an innovative way of reducing its carbon footprint.
The maintenance programme was carried out by Teichmann Contractors and BSM Baker Consulting Engineers.
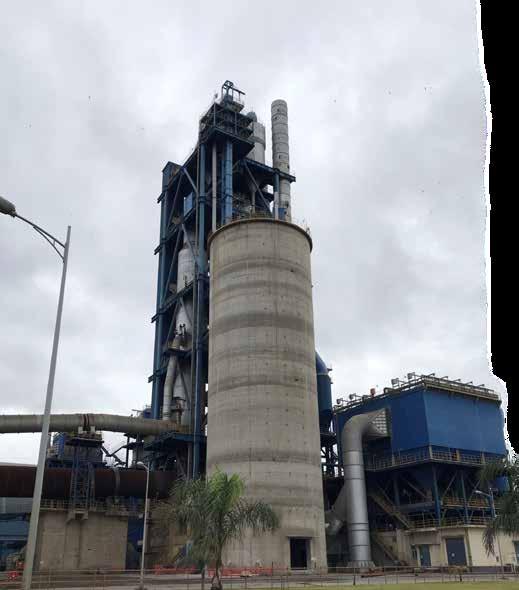