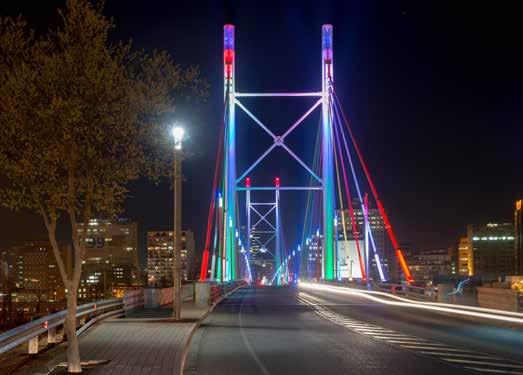
4 minute read
How admixtures influence concrete designs
from IMIESA July 2020
by 3S Media
Over the past three to four decades, admixtures have become increasingly popular. Bryan Perrie outlines the rationale for, and type of, admixtures most commonly found in the mix.
Admixtures are chemicals added to a concrete mix to modify some of its properties; however, they should never be regarded as a substitute for good mix design, sound workmanship, or use of the correct materials.
Advertisement
The most common reasons for using admixtures in concrete are to:
The most common reasons for using admixtures in concrete are to:
• increase workability without changing water content
• reduce water content without changing workability
• achieve a combination of the above
• adjust setting time
• reduce segregation and/or bleeding
• improve pumpability
• accelerate or retard the rate of strength development at early stages
• improve potential durability and reduce permeability gaining an understanding of.
• reduce the total cost of the materials used added to a concrete mix in the concrete to modify some of its •
compensate for poor aggregate properties. properties;
Plasticisers
When added to a concrete mix, plasticisers (water-reducing agents) are absorbed on the surface of the binder particles, causing them to repel each other and de-flocculate. This results in improved workability and provides a more even distribution of the binder particles through the mix. The main types of plasticisers are lignosulfonic acids and their salts, hydroxylated carboxylic acids and their salts, and modifications of both.
Plasticisers usually increase the slump of concrete with a given water content and can reduce the water requirement of a concrete mix for a given workability by about 10%. The addition of a plasticiser makes it possible to achieve a given strength with a lower cement content, and it may also improve pumpability.
However, some plasticisers contain a retarder and can cause problems if overdosed. While some entrain varying amounts of air, others are reasonably consistent in this. Where plasticisers are used to increase workability, shrinkage and creep will invariably be increased.

An admixture played an important part Superplasticisers in the construction of the Nelson Mandela Bridge
Superplasticisers
These admixtures are chemically in Johannesburg. Selfdifferent from normal plasticisers compacting concrete, and their action is more marked. containing a superplasticiser supplied by Chryso SA, was When used to produce flowing used to build the concrete, a rapid loss of workability towering pylons can be expected and, therefore, they should be added just prior to placing.
Superplasticisers are usually chemical are used to the best advantage in areas of congested reinforcement and where a self-levelling consistence facilitates placing. For highstrength concretes, they decrease the watercement ratio by reducing the water content by 15% to 25%.
Special mixes must be designed for superplasticisers and their use carefully controlled. Their effect varies from 30 minutes to six hours, depending on the admixture used.
Air entrainers
An air-entraining agent introduces air in the form of minute bubbles distributed uniformly throughout the cement paste. The main types include salts of wood resins, animal or vegetable fats and oils, and sulfonated hydrocarbons. Uses include improving the resistance of hardened concrete to damage from freezing and thawing; adding workability, especially in harsh or lean mixes; and reducing bleeding and segregation, especially when a mix lacks fines. Air entrainment may reduce the strength of concrete and overdosing can cause a major loss of strength: 1% air may cause a strength loss of 5%, so it is important that the percentage of air entrained during construction be monitored. Because dosages are typically small, special dispensers and accurate monitoring are required.
Different types and sources of cement/ cement extenders may result in the entrainment of different amounts of air for the same dose and mix proportions. A change in cementitious content in the grading or proportions of the fine fractions of sand will normally alter the volume of air entrained.
The amount of air entrained may depend on the source and grading of sand in concrete. Forced-action mixers entrain larger volumes of air than other types, while increased ambient temperatures tend to reduce the volume of air entrained. The use of ground granulated blast furnace slag and fly ash will reduce the amount of air entrained, and the duration of mixing can also affect air content.
Accelerators
These admixtures speed up the chemical reaction of the cement and water, and so accelerate the rate of setting and/or early gain in strength of concrete. Among the main types are chloride-based, non-chloridebased and shotcrete accelerators. Shotcrete accelerators react almost instantaneously, causing stiffening, rapid setting and hardening of the shotcrete.
Accelerators’ uses include: where rapid setting and high early strengths are required (e.g. in shaft sinking); where rapid turnover of moulds or formwork is needed; and where concreting takes place under very cold conditions.
All chloride-based accelerators promote the corrosion of reinforcing steel and should not be used in reinforced concrete, waterretaining structures, prestressed concrete, and steam-cured concrete. Overdosing with these materials can cause instant setting of the concrete, resulting in equipment damage. Accelerators work more effectively at lower temperatures.
Retarders
These admixtures slow the chemical reaction of the cement and water, leading to longer setting times and slower initial strength gain. The most common retarders are hydroxylated carboxylic acids, lignins, sugar and some phosphates. They are mainly used when placing concrete in hot weather, particularly when the concrete is pumped; to prevent cold joints due to the duration of placing; and for concrete that needs to be transported for a long time.
If a mix is overdosed beyond the limit recommended by the supplier, retardation can last for days. Retarders also often increase plastic shrinkage and plastic settlement cracking, and the delayed addition of retarders can cause extended retardation.