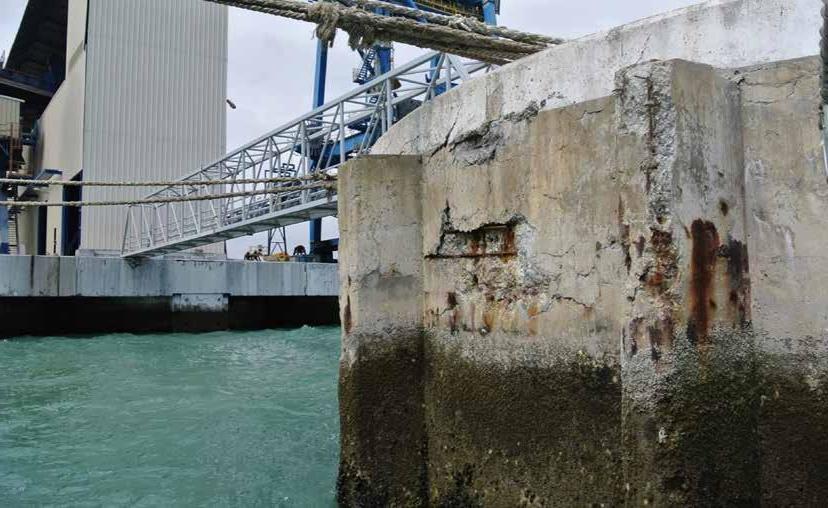
4 minute read
Asset maintenance is a lifelong journey
from IMIESA July 2021
by 3S Media
Routine maintenance of reinforced concrete structures is essential to extend their productive life. Ignoring the warning signs will significantly increase the cost of repair, and may pose a risk in extreme cases in terms of weakened structural integrity, says Wayne Smithers, manager: Technical Services, Sika South Africa.
By Alastair Currie
Advertisement
The first prize is to apply a protective coating on all new reinforced concrete structures – a widespread practice globally, but an uncommon one in South Africa. However, the added upfront cost has been proven to reduce the frequency and extent of future structural repairs and potential failures.
“The most common causes of steel reinforcement corrosion are carbonation and chloride ingress. However, there are a host of other factors that include alkali-silicate reaction, chemicals, electrolysis, dampness and leakage, impurities in the water used to produce the concrete, and internal moisture – or combinations of these. Structural movement and overloading are other contributing factors that can trigger corrosion,” explains Smithers. “That’s why it’s crucial to understand the root causes of corrosion before embarking on any repair solution.”
As a specialty chemicals company, Sika is a market leader in the development and production of corrosion management systems and products. Some of the most widely used products include SikaTop Armatec-110 EpoCem. The latter is a cementitious, epoxy-resin-compensated, three-component coating material with corrosion inhibitor, used as a bonding primer, as well as for reinforcement corrosion protection.
Another key product is Sika MonoTop-412 NFG – a one-component, polymer-modified, fibre-reinforced, low-shrinkage repair mortar with corrosion

INFLUENCES OF STEEL CORROSION IN CONCRETE
inhibitor. ‘NFG’ stands for ‘normal set, with ferroguard’, and can be used as a repair mortar for larger repairs, like a micro concrete application. This makes the product ideal for restoration work, such as the repair of spalled and damaged concrete in buildings, bridges, general infrastructure and superstructure works.
Specialist coatings
Alongside these repair solutions are key coating products like Sikagard-550 W Elastic. The latter is a one-component, plasto-elastic coating based on UV-curing acrylic dispersion with excellent crackbridging properties.
Another popular coating solution is Sika FerroGard-903 Plus, a surface-applied, mixed corrosion inhibitor designed to impregnate steel-reinforced concrete. Essentially, Sika FerroGard-903 Plus penetrates the concrete and forms a protective monomolecular layer on the surface of the reinforcing steel. Smithers says it delays the start of corrosion and reduces the corrosion rate, increasing service and maintenance life cycles by up to 15 years when used as a part of a complete Sika concrete repair and protection system.
Products like Sika FerroGard-903 Plus provide a practical, overall solution because, in most cases, it’s not realistic to expose all the concrete for steel reinforcement repair.
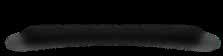
A hidden threat
“The attack on reinforcing is like a cancer and the extent of the internal corrosion damage may not be immediately apparent. Initially, corrosion tends to develop slowly, but then rapidly escalates – so, in a few years of a structure’s life, it can jump from moderate to severe,” says Smithers.
Repairs to extend the service life of reinforced concrete therefore require a total solution. There are cases, for example, where a short-term repair in isolation, like the patching of a spalled section, might inadvertently trigger enhanced corrosion around the repair area itself – a scenario known as insipient anode attack.
“For this reason, corrosion needs to be constantly monitored by property owners and infrastructure asset managers; where it occurs, an industry specialist must be employed to carry out a detailed inspection,” says Smithers.
Typical techniques include the half-cell potential test, as well as core-sample drilling. These techniques help to identify the worst affected areas.
“Aside from the public and private building segment, across South Africa, there are critical structures like bridges, water and wastewater treatment works, and reservoirs that need urgent refurbishment. Over the longer term, this growing maintenance backlog places further pressure on available funds, and impacts on service delivery,” adds Smithers.
INDIRECT INFLUENCES
- Design: joints, cover - Concrete: cement, type and content, water/cement ratio mixed - Application: cracks, gravel nests, curing, surface finishing - Conditions: humidity 50-70%, exposure conditions
DIRECT INFLUENCES
- Mechanical attack: impact, overloading, movement, vibration - Physical attack: freeze-thaw, thermal movement, shrinkage, salt crystal expansion, erosion, abrasion, wearing - Chemical attack: alkali aggregate reaction, aggressive chemicals, bacterial, biological, efflorescence, leaching (Source: Sika)
“In addition to maintenance, more focus needs to be placed on preventative corrosion protection during the construction and commissioning stages. The relatively low cost of applying corrosion protection at inception will greatly extend any maintenance intervals and maximise the return on investment for property and infrastructure asset owners,” Smithers concludes.
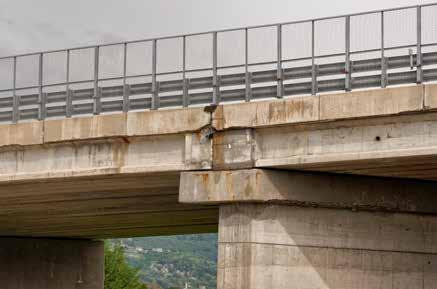