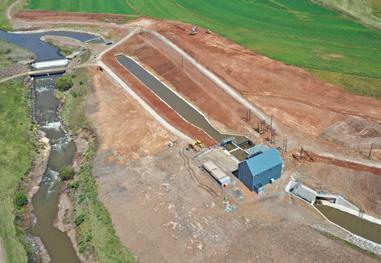
9 minute read
Hydropower on the Ash River
from IMIESA July 2022
by 3S Media
A downstream bird’seye view of the Middle Kruisvallei facility
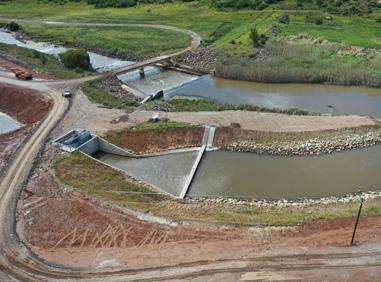
Advertisement
The Lower Kruisvallei powerhouse
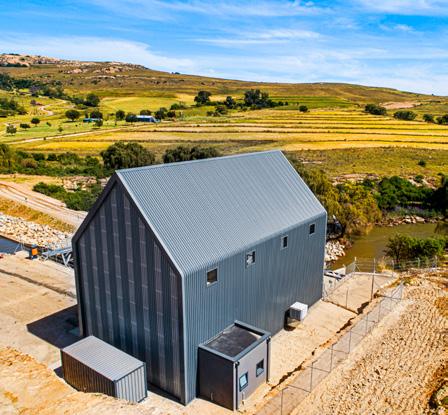
Completed in March 2021, the construction of the Kruisvallei Hydropower Scheme showcases exceptional innovation as well as multidisciplinary engineering and construction management teamwork in delivering a worldclass clean energy solution.
PROJECT TEAM
Middle Kruisvallei abstraction works
Client/Independent Power Producer: Zevobuzz (RF) Civils, Structural & Hydraulic Design Engineers: Zutari EPC Contractor: Red Rocket Civil & Mechanical Contractor: Eigenbau Hydroelectrical Contractor: Scotta SpA Interconnection Contractor: Tractionel Enterprise
Located on the Ash River approximately 13 km north-west of Clarens and 17 km south of Bethlehem in the Free State, the scheme consists of two small run-ofriver hydropower plants – Middle and Lower – generating a combined output up to 4 MW, which cost approximately R260 million to construct within a tight 18-month programme.
The project formed part of Round 4 of South Africa’s Renewable Energy Independent Power Producer Programme (REIPPP), with the power purchase agreement (PPA) awarded to Zevobuzz (RF) as the IPP. Zevobuzz (RF) is majority owned by Red Rocket, with H1 Holdings as a shareholder. Red Rocket is a pan-African IPP with previous experience in wind and solar projects. This is Red Rocket’s first hydropower investment.
Team dynamics
Zevobuzz employed Red Rocket as the EPC (engineering, procurement and construction) contractor, with Eigenbau appointed as the main design and build contractor, and Scotta appointed as the turbine supply contractor (water to wire). Zutari was, in turn, appointed by Eigenbau as the design engineer. Designs were developed in close cooperation with the contractors, with a strong emphasis on constructability.
The Zutari team was responsible for the detail design of all civil and structural works. Another team from Zutari formed part of the management and supervision team of Red Rocket during construction. Zutari also undertook all necessary grid code and network compliance studies, and was responsible for witnessing the factory acceptance tests of electromechanical equipment. Zutari also managed the critical commissioning activities for the EPC.
The project included the fabrication and installation of large radial gates and large active spillway gates, as well as automatic trash rack cleaning machines and switchyards, together with the 13 km transmission line and upgrading an existing Eskom substation to enable the power to be exported to the national grid.
Revisiting the original design proposal
A design proposal had been undertaken for each site at a feasibility level over 10 years before the project was realised, with Zutari appointed to conduct a more detailed technical feasibility study. The results of that study indicated the preferred option for project implementation required single turbines at each site of approximately 2.25 MW and 1.55 MW housed in power stations constructed along the Ash River.
Each of the two standalone, run-of-river systems has an offtake canal tying into the river above the existing Department of Water
and Sanitation (DWS) weirs at each site. The approach channels run through the intake works, consisting of a coarse screen and radial gate. The water is then transferred via a concrete-lined headrace canal to each power station.
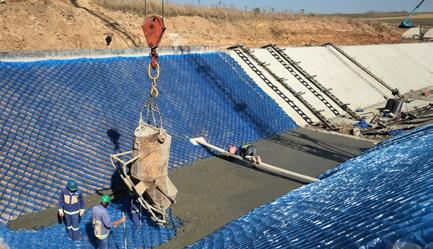
Perfect location
The Ash River is utilised to transfer water from the Lesotho Highlands Water Project (LHWP) to South Africa and provides a reliable, year-round flow, varying between 14 m3/s and 32 m3/s. This was a key consideration for the optimal location of the two power stations. Their location also considers the future completion of Phase 2 of the LHWP, which will increase the flow to approximately 45 m3/s. Extensive computational fluid dynamics analyses were undertaken to optimise waterway designs and to ensure uniform, turbulence-free flow entering the turbines. The use of concrete-lined canals, as opposed to riprap (rock lining), significantly reduced the head losses through the system.
Being a low-head scheme, every centimetre of head loss has an associated value. Consequently, it was imperative to design the scheme to minimise hydraulic losses through the water conveyance.
Optimisation of costs versus returns achieved a maximum hydraulic loss of 0.5 m and 0.7 m respectively at the Middle and Lower Kruisvallei power station sites. The measured hydraulic loss was evidently less than the allowed losses through careful design and construction.
The bypass canals were designed to discharge into the tailrace canals rather than directly back to the river, where energy dissipation structures would have been required, allowing for a more compact site.
Powerhouse construction under way at Middle Kruisvallei

The intake works at Middle Kruisvallei include coarse screens and radial gates Geocell construction of a headrace canal
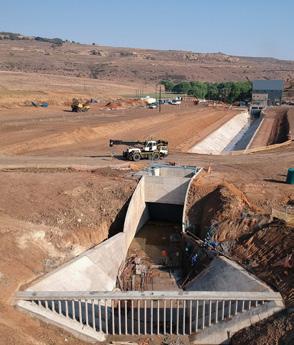
Farmhouse theme
The main powerhouse structure is reminiscent of a typical farm barn, an intentional aesthetic element that blends in well with the surrounding agricultural landscape. These buildings also house the control, switchgear and storage rooms, which are painted to match the outside of the main structure, therefore maintaining a clean and subtle appearance.
Stone, taken locally from the excavation works, was used as riprap along the banks of the canal. While having obvious engineering benefits by stabilising the exposed slopes, it has also been used to afford a natural look as far as possible and to provide natural surfaces for fauna and flora.
Powerhouse configuration
The powerhouse at each site comprises the
main turbine hall. This houses the turbine, generator, gearbox and hydraulic equipment, a chamber housing the dewatering and sump pumps, control and switchgear rooms, a loading bay for assembly, installation and maintenance work, and the structural steel frame building incorporating an overhead crane. Specifying a vertical Kaplan turbine required a significantly deeper excavation than for a horizontal turbine, but resulted in a more efficient scheme overall. In addition, the turbine is fitted with a step-up gearbox, significantly reducing the size, weight and costs of the generator. This solution further minimised the size of the gantry crane and the supporting superstructure. In turn, the hydromechanical equipment design was optimised from a cost and operational flexibility perspective. Instead of the traditional stoplogs at the up- and downstream ends of the waterways, radial gates are employed. Additionally, Active Spillway gates are used to control flow into the bypass channels in the event of an unplanned shutdown.
Canal design and rated flow
Further efficiencies were Kaplan turbine assembly in progress within the Middle achieved in terms of the canal
Kruisvallei powerhouse designs, which are key to the overall success of the plant operations. Here, geocell liners were utilised as a flexible and permeable concrete liner. The use of a concrete liner significantly decreases the friction losses in the canals (compared to an unlined canal), aiding the hydraulic efficiency of the scheme. The plastic layers between the square interlocked concrete cells act as a bond breaker, allowing the slow release of hydrostatic pressure when the canal is emptied, and eliminating the need for a subsurface drainage system. The two separate power stations are each able to operate with a rated flow of 37 m3/s. The existing DWS weirs provide the available head – specifically 7.2 m and 4.9 m for Middle and Lower Kruisvallei, respectively – to ensure sustained downstream power delivery. After passing all necessary tests to be able to connect to the Eskom network, the project achieved commercial operation at the end of February 2021. Now, over the term of the 20-year PPA, the generating capacity will provide electricity to some 2 000 households and the comforting assurance of having power on demand.
6 – 7 SEPTEMBER 2022
EMPERORS PALACE, GAUTENG
PIPES XIII CONFERENCE
The versatility of Plastic Pipe

The Southern African Plastic Pipe Manufacturers Association (SAPPMA) has released an exciting line-up of local and international speakers who will be presenting at the PIPES XIII Conference that will be taking place on 6 &7 September 2022 at Emperors Palace in Gauteng, in collaboration with the Plastic Pipes Conference Association.
Jan Venter, Chief Executive Officer of SAPPMA says they are looking forward to the hybrid conference after a two-year absence owing to the COVID-19 pandemic. Whilst SAPPMA encourages as many people as possible to attend in person, there will also be the opportunity for delegates to log-in virtually.
The theme of PIPES XIII is “The Versatility of Plastic Pipe”. Local industry experts will share the stage with some of the best international papers that were presented at the PPCA’s PIPES XX conference in Amsterdam last year.
“We are very fortunate that our event will take place in collaboration with the Plastic Pipe Conference Association (PPCA) - hosts of the biggest international pipe conference that takes place every second year either in Europe or the USA. A spin-off conference is organised every alternate year and this year it is coming to South Africa!” Jan says.
“Each year, our PIPES conference attracts people from a wide range of different ages, backgrounds and industries who benefit from this valuable learning opportunity. The event is a must for students and academics, engineers, industry representatives, local government, parastatals, pipe fittings and extrusion equipment manufacturers, raw material suppliers and consultants who need to remain at the top of their game. For two days, they will not only have the privilege of being exposed to the latest industry research and best practice, but there will also be ample networking opportunities with fellow professionals,” Jan concluded.
GOLD SPONSOR SILVER SPONSOR SPEAKER LINE-UP
The opening keynote speaker for the event will be popular economist Roelof Botha, followed by various local and international speakers who will be covering all elements relating to pipeline design and installation, standards, testing and certification, extrusion technology, addressing water problems in Southern Africa, infrastructure, raw materials and the rehabilitation of old pipelines.
PRESENTERS INCLUDE: Dr Mike Troughton (TWI LTD), George Diliyannis (Safripol), Dolores Herran (Molecor), Dominique Gueugnaut (GRTgaz), Kirtida Bhana (Plastics SA), Beverley Manikum (Sasol), Antonio Rodolfo Jr (Braskem S/A, Vinyls), Sylvie Famelart (European Council of Vinyl Manufacturers), Albert Vaartjes (Rollepaal), Christian Schalich (SIKORA AG, Corporate Communications), Joerg Wermelinger (Georg Fischer Piping Systems Inc., TEC), Ilija Radeljic (Pipelife Norway), Gunter Dreiling (Borouge Pte. Ltd., Innovation Centre), Peter Sejersen (TEPPFA), Mario Messiha (Polymer Competence Center Leoben GmbH), Prashant D.Nikhade (Borouge Pte Ltd), Sjoerd Jansma (Kiwa Technology), Gregory Vigellis (Union Pipes Industry LLC), Norbert Jansen (PE100+), Lennert Bakker (Suloforce), Simon Thomas (Simon Thomas Consulting), Moshodo Motebele (Department of Water & Sanitation), Jacques van Eck (Avesco), Mike Smart (Genesis Consulting), Alaster Goyns (Pipes CC), Victor Pinedo (Georg Fischer Piping Systems Inc., TEC), Ian Venter (SAPPMA), Bruce Hollands (Uni-Bell PVC Pipe Association), Ricardo Pascual Galan (Aenor) and Kate Kleingeld (Plastic & Chemical Trading).
EXHIBITORS
In addition to listening to this line-up of world-renowned speakers, delegates will also be able to visit exhibitions by leading plastic pipe manufacturers, suppliers and industry partners such as Aenor, Alprene, BSI Group, MacNeil, Molecor, Pipeflo, Plastiweld, Pipestar Africa, SAVA, Zerma etc.
SPONSORS
We would not be able to host this event without the financial support of our sponsors. In particular, we wish to thank Molecor, who has come onboard as a Gold sponsor and Plastic & Chemical Trading, our silver sponsor.
REGISTRATION FEE:
• R4 300 or 300 Euro (excluding VAT) • R3 400 SAPPMA members (excluding VAT) • R3 000 for 5 or more in group (excluding VAT) • R2 200 virtual attendance (excluding VAT)