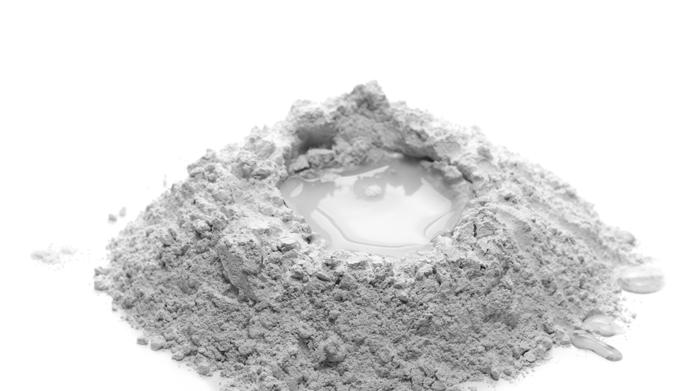
6 minute read
How water influences concrete mix designs
from IMIESA June 2021
by 3S Media
Water is an integral part of any concrete mix design, and not without reason, says John Roxburgh. Here, he explains why the quantity and state of the mixing water are so important.
Concrete mix design usually places significant emphasis on the reduction of the mixing water. By reducing it, less cement can be used, thereby lowering the cost of the concrete. Less water in relation to the cement also increases the strength of the concrete.
Advertisement
A reduction in water will also reduce the overall shrinkage in the plastic and hardened concrete, and will ensure that the hardened concrete is less permeable and consequently more durable.
Furthermore, reducing the amount of mixing water will help reduce settlement in the compacted concrete and thereby reduce the chance of plastic settlement cracks.
But there are some negative concerns about including too little mix water. For example, the plastic concrete could be more susceptible to plastic shrinkage cracking if the surface is allowed to dry out.
So, although there are some very good reasons for reducing the amount of mixing water in concrete, one should always consider the important roles this water plays in the whole concreting process.
Hydration
First, mixing water is needed in the concrete for the hydration of the Portland cement clinker. Water reacts with the clinker to form a cement gel, which is the ‘glue’ that holds the sand and stone together and gives the concrete its strength. Typically, around 28 kg of water is theoretically needed to hydrate 100 kg of Portland cement clinker.
However, during the hydration process, some of the mixing water is ‘trapped’ in the cement gel structure and can never be made available for the hydration process. The result is that richer concrete mixes, with water to cement ratios of below about 0.56, may self-desiccate. This means that all the available mixing water is used up and the concrete would then require additional curing water to continue the hydration process.
Interestingly, most concretes – particularly stronger ones – end up with a proportion of the cement clinker unhydrated. This bodes well for when the concrete is eventually recycled. Crushed, this unhydrated cement then becomes available if the recycled concrete is used as aggregate in new concrete. When fly ash and slag are used as cement extenders, the mixing water will help facilitate the pozzolanic reaction of the fly ash and optimise the slag’s role as a latent hydraulic binder.
Workability
Second, mixing water is also the major lubricant within the plastic concrete mix. Adding more mixing water to a mix will generally increase the workability of the concrete. In the slump test, which is a useful tool in assessing concrete workability, a rule of thumb that often applies is that adding 10 litres of water to a cubic metre of concrete will double its slump, while removing 10 litres of water from a cubic metre of concrete will halve its slump. This shows the critical lubricating effect of mixing water.
Air voids
In modern concrete mix design, admixtures also play an important role in the workability
of a concrete mix. Lubrication and the resulting increased workability are important in concrete to ensure that the concrete fills all parts of the shutters easily and the air in the concrete can be expelled effectively (usually through vibration). Air voids left in the hardened concrete of even 1% can lead to a drop in strength of between 5% and 6%, so it is crucial that the air be expelled from the plastic concrete. Well-lubricated concrete compacts easily by allowing the air to move easily out of it.
Heat energy
Water also has a high specific heat capacity. For the temperature of water to rise by 1°C, it must first absorb a lot of heat energy. This is why hot water geysers are the biggest contributing factor to electricity bills. Water has an enormous capacity to both take in a lot of energy, but also release a lot of it. This is why water is used extensively for both heating and cooling operations, generally. Mixing water in concrete can also be used to heat or cool the concrete.
In massive concrete pours or thick sections, there can be substantial heat buildup in the core of the concrete and if the difference in temperature in the core – compared to other parts of the concrete – becomes too large, the concrete can crack. In concrete practice specifications, the maximum temperature differential is often limited to between 10°C to 15°C.
There are various effective techniques employed to achieve this. One is to lower the temperature of the plastic concrete, which can be done effectively by chilling the mixing water or adding the water into the mix in the form of crushed ice. By casting the concrete at a lower temperature, the peak temperature in the concrete is reduced.
The hydration reaction between cement and water is pushed forward by heat. High ambient and concrete temperatures can result in early stiffening of the concrete, thereby not allowing enough time for transport, placing and compaction. Using the mixing water to cool the concrete will allow more open time for the handling of the plastic concrete and slow the evaporation of water off the surface of the concrete – hopefully mitigating plastic shrinkage cracking.
Heating the mixing water up by around 50°C will raise the concrete temperature by around 10°C. In cold weather, preventing the concrete from freezing, or making sure the concrete has sufficient strength before
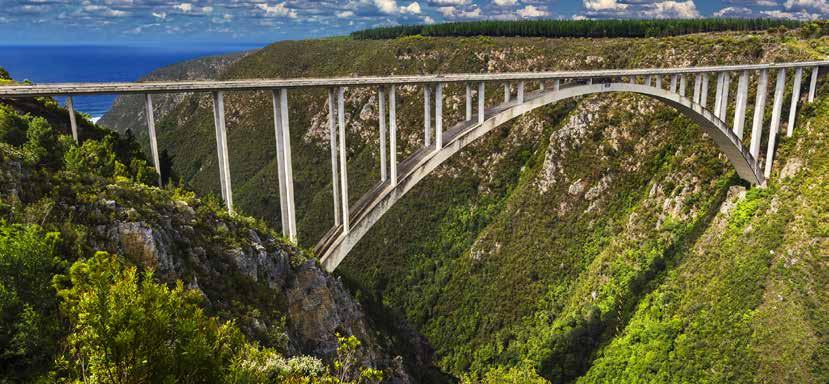
FAR LEFT: Bongani Methula, lab assistant at CCSA, prepares to add mixing water to produce concrete. The important roles this water plays in the concreting process should always be considered LEFT: Methula performs a slump test – a useful tool in assessing concrete workability
John Roxburgh, senior lecturer at Cement & Concrete SA’s School of Concrete Technology
freezing, is important. In such cases, using heated mixing water can help. Casting concrete at an elevated temperature in cold weather and preventing heat from escaping from the concrete through insulation will promote the initial hydration of the cement, which will add further heat to the concrete – a win-win situation.
This is also a useful technique that can be used in precast applications where the economical use of moulds is important. Accelerating the setting times, and the gain in concrete strength, allows for earlier demoulding.
Admixtures
Finally, mixing water can be useful in evenly dispersing admixtures through the mix. Admixtures often have highly charged molecules that will easily attach to cement particles. If an admixture is added to a mix in a concentrated form, these molecules may quickly attach to the cement in the immediate environment and therefore reduce the effectiveness of the admixture. Adding the admixture to the mixing water, and then dispatching the mixing water over time into the mix, will allow for even dispersion of the admixture throughout the concrete.
For further information and details of the School of Concrete Technology’s online training, contact info@cemcon-sa.org.za or phone +27 (0)11 315 0300.