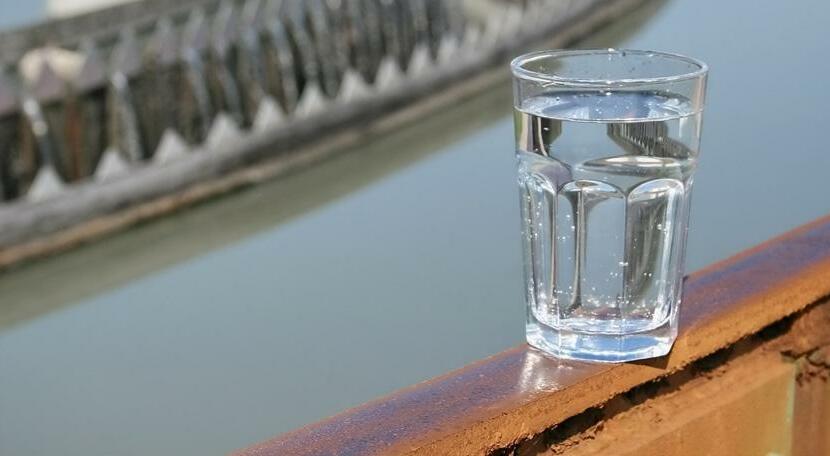
6 minute read
A proactive approach to life-cycle costing
from IMIESA March 2022
by 3S Media
Climate change, population growth and urbanisation are placing increasing pressure on South Africa’s water and wastewater infrastructure. Finding sustainable solutions requires a value-engineered approach that looks beyond conventional design, says Dr Michele Kruger, functional general manager: Water Infrastructure, SMEC South Africa.
By Alastair Currie
Advertisement
The introduction of the UN Sustainable Development Goals (SDGs) marked a turning point for the world by placing the emphasis on people and the environment first, rather than pure economic gain. Participating SDG countries, which include South Africa, as well as member firms, are required to effect meaningful change.
“In many respects, the SDGs are a race against time and, from SMEC’s perspective, our responsibility is to design and execute positive outcomes, based on engineered solutions,” says Kruger, who prior to joining SMEC was an advisor to South Africa’s Minister of Water and Sanitation.
Kruger’s passion for this field has been recognised both at home and abroad. In 2007, she won the Young Engineer of the Year Award at the SAACE Glenrand MIB Engineering
Excellence Awards. Internationally, her doctoral research in water treatment was honoured by the UK’s Federation for Water Research as the best paper by a young South African in the field of water science and technology. “My key mandate is to make practical and implementable connections between water security and life-cycle costing,” Kruger explains. “That’s because our problems and challenges are heavily weighted towards treatment, or the lack thereof, where there’s minimal room for error.”
Dr Michele Kruger, functional general manager: Water Infrastructure, SMEC South Africa
Asset registers, operations and maintenance, cost-reflective tariffs
From previous experience and working as a Green Drop auditor in 2021, Kruger has a clear understanding of the current performance status of South Africa’s water and wastewater treatment plants. As defined by the Department of Water and Sanitation, “The Green Drop process measures and compares the results of the performance of water services authorities and their providers, and subsequently rewards (as incentive-based regulation) the municipality upon evidence of their excellence (or failures) according to the criteria that have been defined.”
One of the key Green Drop audit criteria is an up-to-date asset register with evidence of how effectively this speaks to the municipality’s operations and maintenance (O&M) programme. The asset register – as a status report – forms the basis for a lifecycle costing model, based on a detailed risk analysis that identifies the critical gaps.
“The fact that a higher-than-acceptable percentage of water and wastewater treatment plants are dysfunctional points to poor O&M, which can be improved together with the active management of asset registers,” says Kruger. “Municipalities need to increase their inspection periods and response times, as well as develop realistic maintenance budgets and an action plan that works. Being able to collect cost-reflective tariffs is of course also essential to be able to afford such plans.”
On a positive note, Kruger points out that there are treatment works that have passed their end of life but are still performing optimally. In these instances, this shows that the maintenance plan has worked exceptionally well. This presents opportunities to share success stories with struggling municipalities so they can improve their O&M capabilities.
Needs analysis
Before building or upgrading a treatment plant, Kruger says the first step is scenario planning and risk analysis. The foremost consideration from a potable water perspective is establishing current and future security of supply. From a wastewater perspective, changing raw water quality and the effluent quality discharged to rivers or how the limits for these might change in future becomes a factor.
From there, a risk register can be developed that ranks the likelihood of something happening, like a drought, and its impact, with a recommended contingency response.
“Wastewater plants are designed for a specified treatment strength. In an extreme drought, however, like the situation experienced in Cape Town during the ‘Day Zero’ threat, you can end up receiving half the flow, but twice the contamination,” Kruger explains. “That makes it very challenging to treat to the required quality; however, in Cape Town’s case, they rose and overcame these challenges, thanks to contingency planning and process optimisation.”
Design for efficiencies
When conducting an upfront design, one of the key challenges facing consulting engineers in general is pressure from the client to discount their fees as a perceived saving on the final project. However, these are relatively small upfront costs compared to the longer-term life-cycle costs of a plant.
“Every plant design should be fit for purpose, with sustainability in mind, and that’s the starting point. As consulting engineers, our responsibility is to give the client the best solution based on the capital and operational budget available to them. In a metro, full plant automation with remote monitoring and control may be a requirement, while our recommendation to a rural municipality might be to stick with a manual plant operation model from maintenance cost and practicality perspectives,” says Kruger.
The advent of the Fourth Industrial Revolution (4IR) has introduced a host of exciting new internet of things possibilities when it comes to life-cycle costing. For clients going the automated route, for example, this includes near real-time diagnostics on influent per second, as well as chemical and electricity use. These days, automated plants can also be controlled remotely via smart devices.
“Running in parallel with 4IR is 5IR, which balances the equation by emphasising that technology exists to benefit humanity. In this respect, 4IR uses machine intelligence to perfect life-cycle costing models in response to SDGs,” says Kruger.
Energy savings
Energy efficiency is a core component of SMEC’s life-cycle cost management framework. Sometimes it’s a simple change in process scheduling. For example, treatment works can reschedule pumping, desludging or backwash operations so that they occur during off-peak electricity consumption periods. Then there are technology interventions like variablespeed drive motors on equipment that further reduce energy use during lower demand.
SMEC’s designs also include renewable energy options. “While the upfront cost may be high, the longer-term financial and environmental benefits on a large-scale plant are significant,” she explains. As an aside, Kruger mentions visiting a 400 Mℓ/day water treatment plant in Abuja, Nigeria, which runs entirely on solar power.
Chemical consumption
Another area where plant owners can save costs is on chemical dosing, like the use of disinfectants, precipitation chemicals and polymers, as part of the water and wastewater treatment processes. The objective is not to compromise the system, but again to refine efficiencies.
As one of the first treatment stages, raw water is traditionally dosed with polymer to facilitate the separation of solids during flocculation; however, it’s not uncommon for plants to cut costs by using low-cost polymer, with a subsequent reduction in efficacy. Similarly, the use of polymers in belt presses affects the life-cycle costing if the maximum dosing requirements are not well specified and adhered to during the procurement process.
A holistic process
Going forward and in line with the SDGs, plants need to be designed, constructed or retrofitted to reduce waste and keep the circular economy in mind. This has a bearing on everything from the sustainability of construction materials selected right through to the sludge beneficiation techniques applied. Plants also need to be designed up front for sustainable closure.
Bankability
“Conducting an in-depth risk and life-cycle cost analysis, combined with scenario planning, provides a coherent roadmap for project and service delivery sustainability,” says Kruger. “As consulting engineers, we have so much value to add walking the road together with our clients.”
In parallel, among the interesting developments are the opportunities presented by South Africa’s Infrastructure Fund, with a weighting towards publicprivate partnerships (PPPs) and concession agreements like build-own-operate-transfer models. Water and wastewater plants are already part of the PPP mix, hopefully ramping up speedily; however, getting to financial bankability relies heavily on life-cycle costing and sustainable offtake agreements.
“Public clients stand a far better chance of attracting private investors and making projects bankable if all the feasibility, cost and risk data is in place,” she adds.
“Either way, as the pressure on South Africa’s water and wastewater systems mount, the best route is a collaborative one that brings together public and private stakeholders in a common quest to meet the SDGs and support a resurging economy,” Kruger concludes.
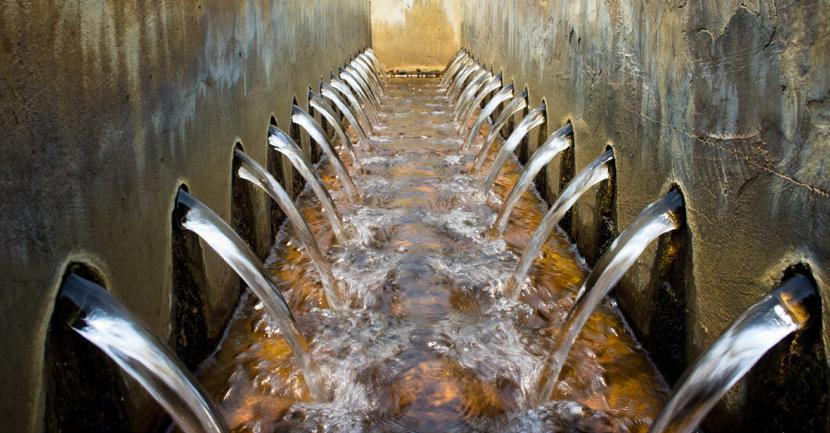