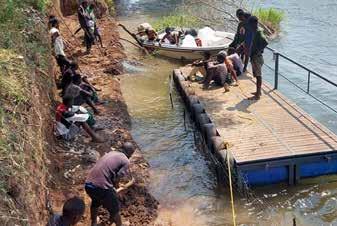
6 minute read
Wire and stone
from IMIESA October 2021
by 3S Media
ZAMBIA RIVERBANK PROTECTION The wall begins to take shape
Workers prepare the bank and foundation. The fence in the river is designed to discourage marine life, including crocodiles, from entering the construction zone
Advertisement
With the gabion mattresses installed, workers begin establishing the wire baskets for the initial 1 m high wall at the base of the retaining structure
A section of the gabion mattress foundation at an advanced stage of completion. Note the steel plate working platform extending out into the river

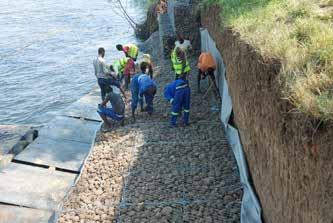
The strength of hightensile steel wire has been used for generations to form seemingly simple cubic boxes filled with rock to form structures commonly referred to as gabions. Modern-day fabrication techniques have significantly extended the design and application boundaries, says Clinton Cheyne, operations manager, Gabion Baskets, citing recent projects.
By Alastair Currie
Derived from the Italian gabbione, gabion structures are designed to create a natural interface that blends in and essentially ‘breathes’ with the environment due to their approximately 75% or higher stone composition. The voids are there to intentionally ensure permeability, which is especially well suited to mass gravity retaining walls that must provide a degree of controlled drainage, whether in a bridge abutment role or for riverbanks or marine installations. Being rock-filled, water can pass through to a greater or lesser extent with the added incorporation of permeable or impermeable membranes, depending on the designer’s intention.
Zambezi River erosion
In a recent riverine example, Gabion Baskets secured an order for the supply of gabion baskets and mattresses for an erosion control protection project on a section of the Zambezi River near Chirundu in southern Zambia. This section borders a private property that extends to the riverbank.
In addition to providing technical drawings and design advice, Gabion Baskets conducted in-depth training for locally employed workers, with a South African trainer deployed on-site during the key construction phases.
“Before the preparation works could begin, though, the contractor first had to install a temporary 2 m high protective fence in the river, boarding the site in case a crocodile came to visit,” says Cheyne. “This was certainly a new take for us on an environmentally engineered solution.” For this project, a combination of gabion systems was installed, depending on
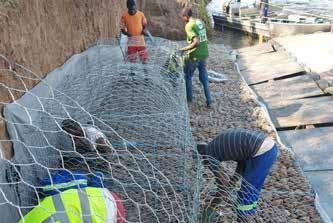
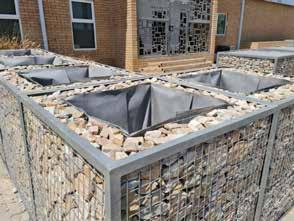
HONEYDEW BUILDING ENTRANCE The perimeter layout incorporates weld mesh gabions with space for planting shrubs The welded mesh gabions complement the company’s mosaic entrance panel design
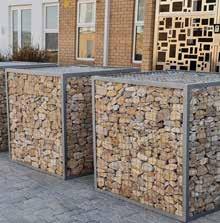
erosion severity at points along the bank. In some cases, up to 3 m of the original bank had been lost to the river.
Interventions include standalone gabion mattresses installed at an angle of some 33 degrees, and gabion wall sections at 1 m or 2 m heights, founded on mattresses. The scope also included the repair of existing gabions installed locally some seven years ago that were in an advanced stage of deterioration. The fact that the contractor at the time didn’t install gabion mattress foundations was a contributing factor.
Temporary working platform
“A key challenge was that the river embankment has a very small toe and the contractor needed to excavate back into the embankment to create a suitable platform wide enough for placing the mattress base,” explains Cheyne.
“The riverbed also slopes steeply away to depth from the toe. Aside from the depth, the installers also couldn’t work in the water due to the crocodile threat. We thus recommended the installation of a temporary 5 mm steel plate working platform extending out into the river on designated sections. The mattresses were built on top of the steel plate. This worked very well. As the mattresses began to fill with rock, they held the steel plate horizontal. Once the applicable mattress sections were completed, the plates were removed.”
Gabion Baskets supplied its standard hexagonal double-twisted mesh panels. The wire specification is Class A galvanised. “It’s not unusual to expect at least a 50-year life from a gabion river retaining wall, but that does depend on a number of criteria,” he explains.
“Beyond correct design and installation procedures, corrosion protection is a must, and although the standard zinc-coated steel wire manufactured is fine for land-based structures, it won’t last beyond a reasonable period in environments that will be submersed and exposed to potential scour, flotsam impact and corrosion. Ideally, a more advanced Galfan coating is recommended, often in conjunction with an additional PVC coating,” he continues.
Gabion islands
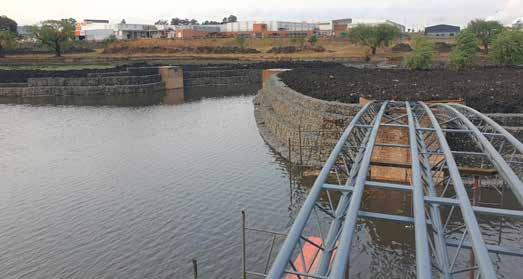
Back in South Africa, work continues on a mixed-use residential and office development in Secunda, Mpumalanga. A key element is a lake, which was drained to enable the construction of an approximately 300 m long gabion retaining wall. For this project, Gabion Baskets completed a detailed site assessment, design proposal and costings, securing the order for the supply of the gabion systems, as well as training. Another interesting element has been the developer’s decision to construct gabion islands.
“The concept of gabion islands is a really innovative adaptation. Simple to construct, and with an earth-filled centre, the aesthetic appeal of these installations is another example of out-of-the-box approaches to traditionally environmentally engineered designs. We’re seeing this increasingly on both civil and building projects, as architects, engineers and developers embrace the beauty and simplicity of wire and stone combinations,” says Cheyne.
Demarcation
A major growth in landscaping and architectural gabion designs underscores the increasing popularity of the natural stone appeal for installations that include building cladding, boundary walls, and barrier structures that delineate between parking spaces and properties. An example of the latter is a welded mesh gabion project recently completed by Gabion Baskets in Honeydew, Johannesburg. “The client wanted to establish a perimeter delineation in front of its entrance, using four free-standing welded mesh gabion baskets as the central design, bordered by L-shaped gabion wing walls – the latter including a central pocket for the planting of scrubs,” Cheyne explains.
The framed boxes were fabricated by Gabion Baskets using 40 mm x 40 mm x 3 mm angle iron sections. The wire mesh panels are placed flush against the inside edges and held in place by the rock infill. Ornamental rock forms the exterior faces, while the interior fill was sourced from building rubble.
“This is a cost-effective way to create attractive effects, while at the same time recycling waste material that would otherwise end up in a landfill,” says Cheyne.
SECUNDA GABION RIVER PROTECTION & ISLANDS This gabion island creates a distinctive feature for a property development in Secunda. The gabions for the island and the retaining wall in the background were supplied by Gabion Baskets
Project management and quality control
Increasingly, Gabion Baskets is being called in to provide design recommendations and installation support. In response, the company has now appointed a full-time project manager to assist clients and contractors with quality execution.
From a throughput perspective, Gabion Baskets also recently upgraded the production lines at its Johannesburg factory to meet rising volume demand. One of the major changes on its welded mesh line is a switch to the use of hog ring guns in place of the more time-consuming hand-lacing technique. The pneumatic gun dispenses a hard wire clip at set intervals to instantly bind panel sections together. These clips are manufactured to Class A galvanised or stainless-steel specification, as specified.
“Each project is unique in terms of shape, size and design. It’s an exciting opportunity to deliver on our out-of-the-box approach by assisting clients to create customised and sustainable engineered solutions,” Cheyne concludes.