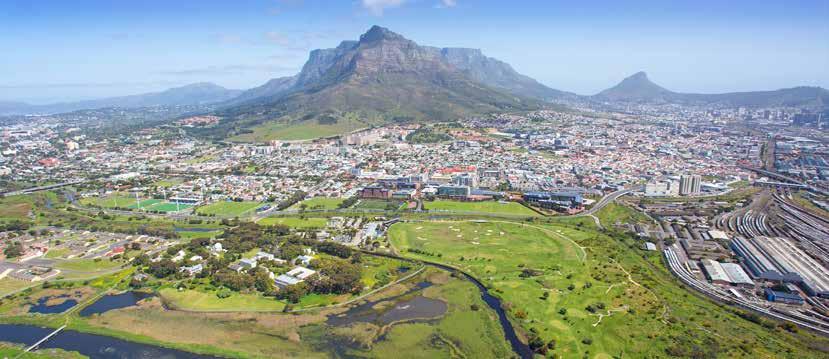
6 minute read
Rehabilitating Cape Flats 1 and 2
by 3S Media
Trenchless technologies will be employed extensively for the refurbishment of one of Cape Town’s largest sewer systems, with all works expected to be completed by 2025. Vuyo James, senior professional officer: Planning, Design and Projects at the City of Cape Town’s Water and Waste Directorate, says the project is the largest undertaken to date in South Africa. By Alastair Currie
The Cape Flats 1 and 2 (CF 1 and 2) sewer lines, each measuring some 14 km in length and running in parallel, were originally installed in 1962 and 1969, respectively, to meet growing demand. Then and now, they perform a vital service, which has become even more crucial given ongoing residential, commercial, and industrial expansion within the City of Cape Town.
Advertisement
This was the motivation for the construction of the new Cape Flats 3 (CF 3) sewer line, completed in 2016, which has significantly reduced the load on the overall system. The additional services provided by CF 3 now make it possible for a systematic and phased refurbishment of CF 1 and 2, without putting service delivery on the line.
As a far more modern system, CF 3 was installed with larger-diameter pipe networks compared to CF 1 and 2 – the latter ranging from 1 050 mm up to 1.8 m. CF 3 also benefits from the latest advances in protective polyurethane lining systems preinstalled by the precast pipe manufacturer that supplied the project. Athlone is the starting point for CF 1 and 2, culminating at the Cape Flats Wastewater Treatment Works (WWTW) in Zeekoevlei. The treated effluent is subsequently discharged into the Zeekoevlei zone, an approximately 258 ha water body that borders the Atlantic Ocean.
Designed to last
The original networks for CF 1 and 2 are composed of precast reinforced concrete pipe in varying diameters along their length – as is typical of a sewer system. However, it’s interesting to note that the City’s design team went a step further by encasing the entire pipeline installation with a concrete outer layer as an added protective measure during their construction.
As was common practice in the 1960s, the manholes are built predominantly of clay brick, incorporating a chamber, or chimney, for inspections.
“Considering that these pipes have been in operation for close on 60 years in a highly corrosive environment, they have stood the test of time exceptionally well,” says James. “From the CCTV inspections undertaken to date, it has been confirmed that there are no pipe collapses on CF 1 and 2. However, there are collapses at the manholes, which can be expected given some six decades of performance. Manhole chambers tend to be subjected to far higher concentrations of hydrogen sulfide (H2S) gas build-ups than the pipes themselves.”
Vuyo James, senior professional officer: Planning, Design and Projects, City of Cape Town Water and Waste Directorate
Trenchless versus opentrench excavation
The City of Cape Town’s engineers have gained extensive experience in the deployment of trenchless technology for new pipeline installations, like CF 3, as well as major bulk line refurbishments. This made going the trenchless route a logical choice.
“A major benefit of trenchless construction is minimal, if any, disruption, which is especially important in urban areas,” James explains. “Plus, the cost of electing for an open-trench
method to replace and re-lay new pipelines would have been prohibitive, and unnecessary, given the refurbishment products available on the market. In any case, space constraints within the pipelines’ servitudes ruled out an open-cut approach.”
Depending on the specific repair intervention required, three products have been specified by the City following in-depth research. These comprise cured-in-place pipe (CIPP) lining systems (either reinforced or unreinforced), a PVC spirally wound pipe liner system, and concrete-on-concrete repair using a proprietary calcium aluminate cement (CAC) and aggregate product. CAC will be employed extensively for the manhole refurbishments.
This will be the first-time application of spirally wound pipe on a City of Cape Town project. The product is installed by launching a spindle machine attached to a PVC liner spool feed. As the spindle travels down the pipe, it systematically installs an approximately 20 mm diameter liner, which incorporates a strip of steel reinforcement. Strips are secured in place by a mechanical locking joint. A further plus is that the spindle machine can be set for a fixed or variable diameter.
The ovality factor
Currently, the appointed contractors are completing detailed profiling inspections that will determine which of the recommended technologies should be employed on affected sections. The ovality of CF 1 and 2 pipelines will be the determining factor.
Pipes start out round, but their shape changes over time due to corrosion and/ or scale build-up. Corrosion is always going to be a key issue within sewer lines unless combatted with protective systems, like HDPE liners, during their original commissioning.
Where calcification occurs, this will reduce the pipe’s diameter; however, corrosion is the main factor. It progressively eats away the concrete. The pipe diameter then starts to increase, exposing the steel reinforcing. This in turn negatively affects the pipe’s hydraulic characteristics, increasing the speed and variability of flow patterns.
Typically, a mushroom effect results at the base of eroded pipes, since this is where most of the flow occurs. However, a reverse mushroom effect can also occur, characterised by scale build-up at the apex of the pipe.
CIPP is not limited in terms of diameter. However, the risk and cost increase exponentially above a certain diameter. It’s also important to note that each CIPP liner is custom-built to meet a specific pipe’s exact dimensions, making allowance for some degree of expansion and contraction. Typically, these liners are blown through the pipe using compressed air and then inflated using either heat, air, or water. They contain a specialist resin that cures and hardens through exposure to air or UV light.
“Generally, CIPP tends to work best on pipe diameters up to 1.2 m. After this, spirally wound liners are the preferred approach,” James explains.
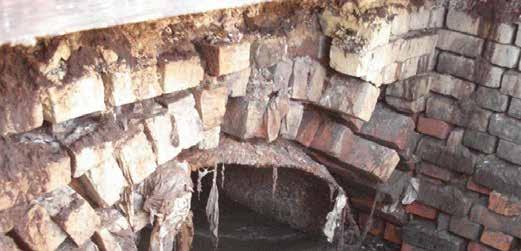
An example of a collapsed brick manhole section
A strategic and phased intervention
The budgeted cost for the refurbishment of CF 1 and 2, which includes the rehabilitation of over 300 manholes, is more than R200 million. Some R100 million has been allocated during the 2021/22 financial year for profiling work and the appointment of consultants.
Once the project enters the refurbishment stage, the first phase will entail repair works on CF 1. In preparation for this, a wall constructed at Manhole 1 (the mixing chamber) will divide the CF 1 and 2 lines. At Manhole 12, sluice gates have also been installed so that flows can be diverted to either pipeline.
James says that the flow to CF 1 will be completely diverted to CF 2 during CF 1’s repair; however, completely shutting off CF 2 during its repair will not be possible since it currently transports higher loads than CF 1. So, some sections of CF 2 must remain operational during its rehabilitation.
“We’ll need to be very strategic. The success of the project will hinge on close teamwork between the City, consultants, contractors and product suppliers,” says James. “Optimal process efficiencies at the Cape Flats WWTW will also be a critical factor.” The scale of the project is certain to place the spotlight on Cape Town from trenchless technology practitioners locally and internationally.
“Our engineering teams take a proactive approach to asset management and infrastructure master planning as part of the City’s longer-term socio-economic vision. Investing in infrastructure creates the enabling framework,” adds James.
“That was clearly well understood by the City’s engineers back in the 1960s, when CF 1 and CF 2 were built. Their visionary design in encasing the pipelines means that we can now use modern-day trenchless techniques to extend their life for at least another 100 years,” James concludes.
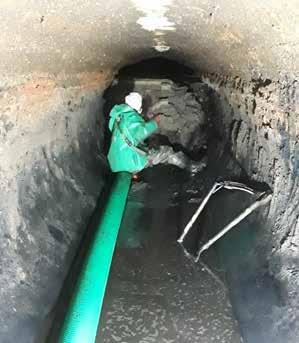
Mining a pipe blockage