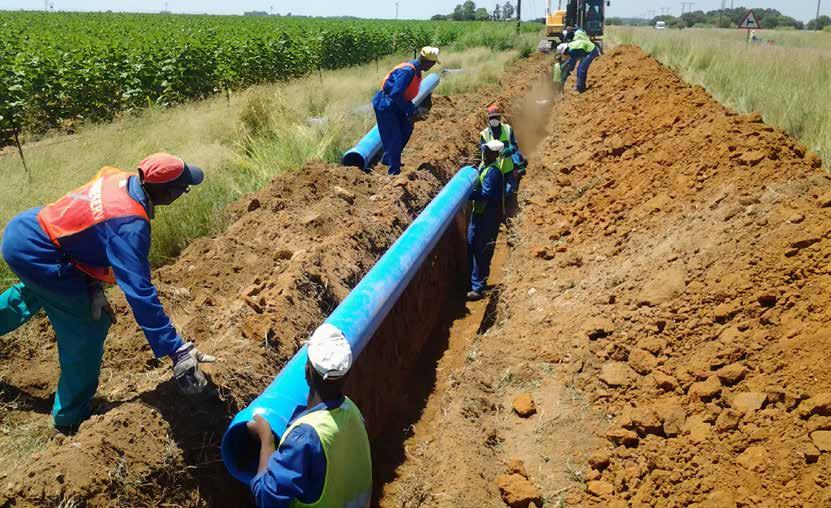
5 minute read
Plastic pipe specifications, design and performance
by 3S Media
The durability of plastic pipe is legendary; the material is used in over 50% of the water and sewage networks installed globally. Optimal performance depends on various factors, especially the strict adherence to product, design and construction standards. A good understanding of pipe/soil interaction adds further benefits. By Alastair Currie
Within the world of thermoplastic pipe, there are a range of material options that can be used to form them, depending on the downstream application requirements. Within the spectrum, polyvinylchloride (PVC) and high-density polyethylene (HDPE) are the best known. Understanding their material characteristics is important from design, specification and installation perspectives.
Advertisement
“Aspects like stress and strain, as well as how the pipe is supported above and in the ground, will have a direct bearing on its performance characteristics. Each site has its own unique conditions, like the depth of excavation, marshy conditions, traffic loads or higher-thannormal groundwater levels, which must be factored in during the design and pipelaying stage,” says Ian Venter, technical manager, Southern African Plastic Pipe Manufacturers Association (SAPPMA).
Venter recently hosted a SAPPMA webinar on the subject (Webinar VII), presented by design and construction management experts. (Visit www.sappma.co.za to download the training material for quick reference and guidance.)
In addition to ensuring quality standards among its members, technical training and industry consultation are core SAPPMA mandates. This was the motivation for the launch of the Installation and Fabrication Plastics Pipe Association (IFPA) – a SAPPMA initiative aimed at ensuring best practice in the sector. Pipe manufacturers belonging to SAPPMA subject their products to extensive testing, supported by ongoing investment in research and development. The same holds true for polymer manufacturers. SAPPMA’s quality assurance programmes, which include unannounced audits at member production facilities, ensure that specifiers can buy with confidence, knowing that key specifications, like wall thickness, and critical dimensions are consistently adhered to.
“The reality is that any type of material system will fail if it’s not properly designed, manufactured, and installed, so it’s vital to take a holistic approach,” Venter explains.
“Where pipe failures do occur, the root causes are often not difficult to find. It’s just a matter of ensuring that products are well understood and that the design and application have been aligned to their unique properties, characteristics, as well as jointing capability. By doing this, it is quite easy to further prevent failures of this type,” he continues.
Construction is a multidisciplinary field, where sharing technical knowledge is vital in achieving the UN’s Sustainable Development Goals
Tougher and more flexible
Research and development advances have been significant over the years, with the industry progressively shifting from rigid to flexible plastic pipes. Tensile strengths have also vastly increased for all plastic pipe materials, such as polyethylene (PE) pipes (12 MPa to 24 MPa) and PVC (45 MPa to 75 MPa), allowing them to enjoy market shares typically occupied by steel and concrete pipe.
One advantage of modern-day plastic pipes is that they offer the designer internal pressure and loadbearing capabilities, while remaining flexible to soil movements
and changes in the native soil conditions. External loads would include the backfilled material, plus any superimposed loads like vehicle traffic.
The degree of elasticity provided by the side support then plays a key role in minimising any pipe deflection imposed by vertical loading. The influence of the water table on the soil properties also needs to be taken into consideration.
There will always be a combination of stress conditions to consider in determining the permissible load. The main ones are internal pressure, deflection, buckling, ring bending and arching.
Where the vertical load is too great, and the side support inadequate, a flexible plastic pipe will eventually buckle, or collapse inwards because its ring stiffness is inadequate. Therefore, a buckling design check must form part of all thermoplastic pipe design approaches. This must also factor in the pipe manufacturer’s recommendations in terms of the diameter over wall thickness ratio.
“Confirming buoyancy resistance of shallow gravity piping systems is always good practice, regardless of the type of material being used to design with,” adds Venter.
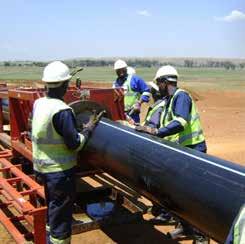
Technical design guidelines
SAPPMA’s Technical Manual for Pipe Manufacturing and Pipeline Design, now in its fifth edition, serves as an invaluable and user-friendly tool for designers, specifiers and installers. The manual provides a set of useful formulas for most types of applications.
Studies show that correctly designed and installed thermoplastic pipe will easily outperform traditional materials, even at extreme depths. In addition, the deeper the pipeline installation, the more dispersed the vertical load. However, to accurately determine this requires a specialist geotechnical investigation, which is especially recommended for larger pipelines.
BENEFITS OF PLASTIC PIPE
• Corrosion resistance • Excellent flow characteristics due to exceptional resistance to chemicals and microbial growth • Virtually leak free due to welded joints • Lightweight and flexible for ease of handling • Ductile and durable • Manufactured under ISO/SANS 4427
Parts 1, 2, 3 and 5
Adhering to the specifications and standards


This underlines the importance of only specifying products manufactured according to applicable industry specifications and specifically those that apply to South Africa. This is crucial since product specifications vary internationally – a case in point being DIN versus ISO pipe stiffness standards, where there’s a variation in how ring stiffness is calculated.
All pipes manufactured by SAPPMA members must comply with the relevant local or international product standard as referenced on the membership certificate. This standard also clearly defines the frequency and parameters for testing and quality control.
Examples of key specifications include the maximum allowable deflection, with a clear distinction between short-term (i.e. immediately after installation) and longterm deflections (typically some 18 months after installation). That will influence the optimum selection of the pipe joints to prevent overloading and potential leaks.
Another important specification is the regulation of recycled materials. For PE pipe systems, the SANS 4427 stipulation is that pipes and components can only be manufactured from virgin compound or unused own in-house reworked compound. This ruling prevents the use of recycled pipe that may have been previously installed or contaminated through contact during its application. All potable water standards follow these principles to ensure a zero possibility of toxicity from previous use and application.
Custom fittings, like bends, also need to be verified to ensure that they match the pipe specification, including the pressure rating.
Long life and sustainability
“When designed and installed correctly, plastic pipe offers a virtually maintenancefree lifespan of well over 100 years, making for an exceptional return on investment for infrastructure asset owners,” adds Venter. “However, like any technology, it requires expert execution.
“End-user benefits are also outweighed by benefits from a construction perspective. Plastic pipes remain highly cost-competitive due to their lightweight properties, which lower transport costs and promote easier handling and installation. Depending on the pipe diameter, this makes plastic pipe the most well suited for labour-intensive and communitybased projects, and SMME contractor development,” Venter concludes.