
4 minute read
Product excellence driven by investment in technology
by 3S Media
An extruded pipe section coming off the production line at Inkulu’s Hammarsdale factory
Established in 2014, Inkulu Plastic Pipe’s team combines years of industry experience with the application of cutting-edge technology to target niche market expansion. The company’s motto, ‘Dare to commit’, underscores its confidence in meeting just-in-time delivery and strict quality assurance standards, says Gabriel Reddy, founder and CEO.
Advertisement

Leading the market, Inkulu Plastic Pipes (Inkulu) is believed to be the first company in South Africa to invest in a new extrusion production line designed to manufacture soldwall 1 200 mm diameter HDPE pipe. The line was commissioned at Inkulu’s Hammarsdale factory in Durban and is set up for pipes in nominal diameters from 500 mm to 1 200 mm. This specialist extrusion line has a maximum output capacity of 1 600 kg/h.
“Setting a new production benchmark for the local and cross-border market, designers, municipalities and utilities now have a highquality and locally manufactured solution for bulk water distribution and sewer lines,” says Reddy.
The company currently operates seven pipe extrusion lines, with an overall monthly production output capacity of more than 1 500 t. Depending on the application, products are supplied in three different materials – namely HDPE, low-density polyethylene (LDPE) and polypropylene (PP).
Extensive product range
HDPE solid-wall pipes are manufactured in a range from 16 mm through to 1 200 mm according to specified pressure ranges to meet small-, medium- and large-bore requirements.
In addition, Inkulu produces spiral-structured wall pipe for applications that include stormwater and sewer systems. Sizes range from 300 mm to 1 500 mm in 4 kN/m² and 8 kN/m² ring stiffness specifications.
The company’s small-bore high-speed extruder lines produce coils in 500 m lengths in diameter sizes from 16 mm to 40 mm. Additionally, Inkulu produces full coil diameters for borehole depths exceeding 100 m. These are supplied as a single coil with no joints.
Latest investment
“Our latest investment in new production technology now means we can extrude corrugated-sleeve pipes in a range from 50 mm to 160 mm, which is an exciting development that will serve key markets like agriculture, roads infrastructure and telecommunications,” says Reddy.
“We invest in the best technology to optimise production throughput and quality. For example, our new high-speed lines are far more efficient, significantly reducing the cost per kilogram to produce plastic pipe. Faster output times make us far more competitive,” he continues.
Alongside its extrusion line acquisitions, Inkulu has responded to client requirements for turnkey solutions by investing in fabricated fittings equipment. A wide range of bends,
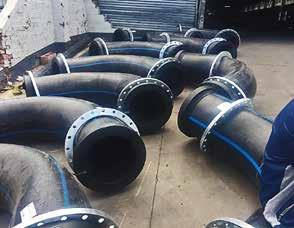
Inkulu’s industry-certified fabricated fittings provide custom connections
QUALITY ASSURANCE
Standard industry material tests are conducted at Inkulu’s on-site laboratory according to SANS ISO 4427/ISO 4437. Inkulu is also ISO 9001, ISO 14001 and ISO 45001 certified, and is a member of the Southern African Plastic Pipe Manufacturers Association.
PRODUCTS
• Coiled: HDPE pipes 16 mm to 110 mm • Lengths: HDPE pipes 125 mm to 1 200 mm • Perforated: HDPE pipes 63 mm to 1 200 mm • Plumbing hot water pipes, manufactured using PP • Telecommunication fibre-optic HDPE ducting • PE100 HDPE gas pipe • Manufactured fittings up to 630 mm • Moulded HDPE butt-welding and electrofusion fittings
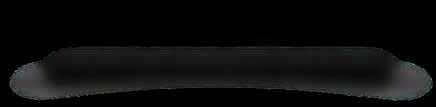
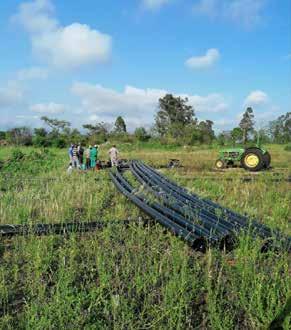
Inkulu’s products serve key markets like agriculture, roads infrastructure and telecommunications
tees, stubs, flanges, and reducers cater for pipe systems up to 630 mm.
Gas market gains
The liquid gas sector is another growth area for Inkulu for HDPE installations typically ranging from 16 mm to 630 mm. Sectors supplied to date include the industrial, mining, municipal and residential markets. “Switching to gas as an alternative energy source holds huge potential,” says Reddy. “In this respect, HDPE lines – combined with electrofusion fittings – are ideally suited to this application.”
Manufactured in accordance with ISO 4437 standards, Inkulu’s gas pipes and fittings are quality tested throughout the entire production process to ensure safety and reliability. Available in coils and lengths, these gas pipes are specifically designed for buried installations and, like all HDPE products, they are maintenance-free over their lifetime, resistant to corrosion, easy to install and flexible, with high-impact strength. A further advantage of HDPE pipe is their suitability for trenchless construction.
The material of choice
In the infrastructure space, Inkulu is experiencing growing demand for water, wastewater and stormwater applications as municipalities recognise the cost benefits of plastic pipe compared to traditional pipeline systems manufactured from ductile iron and concrete.
“Through our ongoing research and development (R&D) programme, we’ve met the need for more complex and costefficient pipeline designs by means of HDPE fabricated fittings to solve installation situations where common fittings fail,” Reddy explains, adding that Inkulu also supplies and manufactures moulded HDPE butt-welding and electrofusion fittings.
Keeping pace with the market, Inkulu’s ongoing R&D initiatives continue to tap into new niche segments. The latest developments include the production of PP plumbing hot water pipes, as well as fibre-optic HDPE ducting.
“Inkulu has established a well-proven track record for supplying quality pipes on time, focusing on establishing and building partnerships with suppliers and customers. Our recent capex investments now place us at the forefront of the plastic pipe manufacturing sector. We’re excited about the possibilities as more infrastructure projects come online,” Reddy concludes.
Inkulu’s truck fleet ensures on-time delivery. Purpose-designed trailers cater for pipe lengths up to 24 m To support its turnkey installation and commissioning services, Inkulu has invested in a wide range of welding technologies
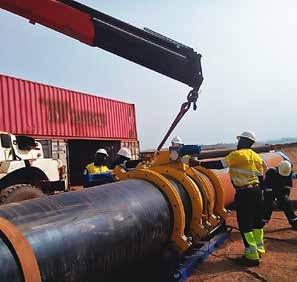
www.inkuluplastics.co.za
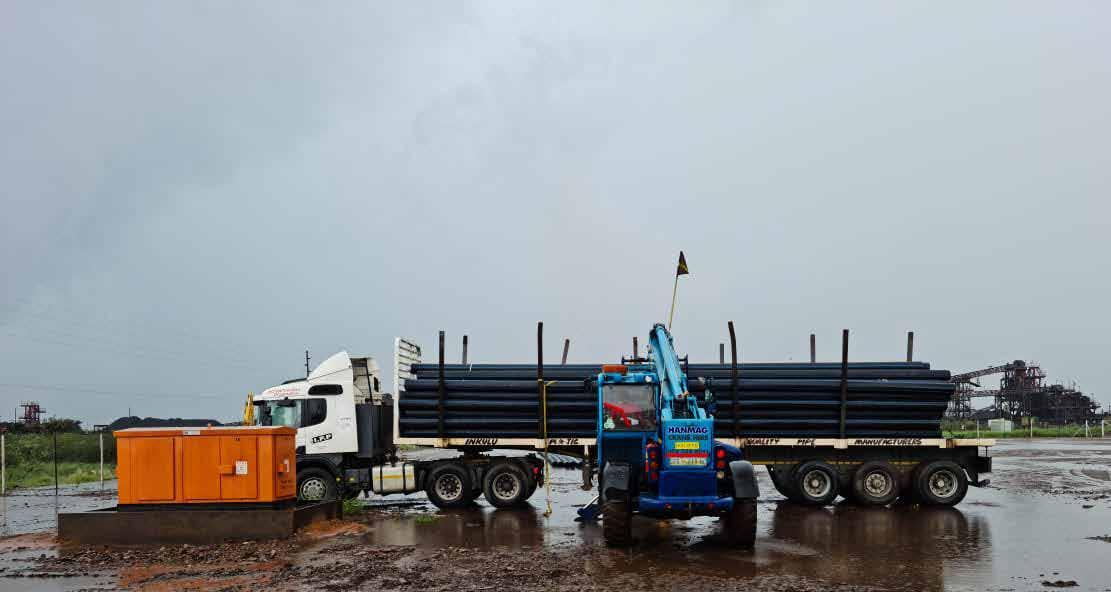