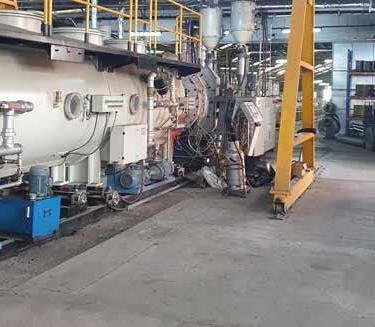
5 minute read
Extr usion line investment adds value
by 3S Media
Established in 2014, Inkulu Plastic Pipes' team combines years of industry experience with the application of cuttingedge technology to target niche market expansion. The company’s motto, ‘Dare to commit’, underscores its confidence in meeting just-in-time delivery and strict quality assurance standards, says Gabriel Reddy, founder and CEO.
Supplied by Zhangjiagang City Yili Machinery, Inkulu’s 38D Series pipe extrusion machine sets a new manufacturing benchmark for the company, as well as the local market, enabling pipes of up to 1 200 mm to be produced
Advertisement
Extrusion line investment adds value
D
uring January 2020, Inkulu commissioned its 1 200 mm pipe extrusion line at its Hammarsdale factory in Durban. Supplied by Zhangjiagang City Yili Machinery (Yili), this 38D Series machine sets a new production benchmark for the company, as well as the local market, for the extrusion of high-density polyethylene (HDPE) solid wall pipe in nominal diameters from 500 mm to 1 200 mm. This specialist extrusion line is set up for a maximum output capacity of 1 600 kg/h.
Yili’s relationship with Inkulu started in 2015, when the company began its initial capex investments. To date, Yili equipment installed at the Hammarsdale facility includes various extrusion machines, shredders, granulators and pelletisers. Virgin-grade materials are used to form all products.
The company currently operates seven pipe extrusion lines, with an overall monthly production output capacity of more than 900 t. Depending on the application,
Installation of an HDPE bulk water line
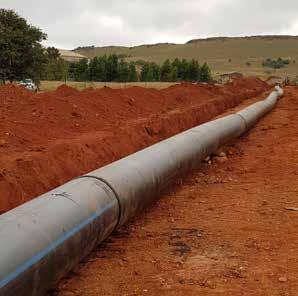
products are supplied in three different materials, namely HDPE, low-density polyethylene (LDPE) and polypropylene (PP).
HDPE solid wall pipes are now manufactured in a range from 16 mm through to 1 200 mm according to specified pressure ranges to meet small-, mediumand large-bore requirements in South Africa, as well as further afield in Africa in countries such as Botswana, the DRC and Zambia. A hose line is also produced in 16 mm to 40 mm diameters in 500 m coils.
In addition, Inkulu produces spiral structured wall pipe from 300 mm to 1500 mm applications that include stormwater and sewer systems.
“Our multimillion-rand investment in this automated 38D Series line has positioned Inkulu as a major player in the bulk water and sewer line segments,” says Reddy, who has more than 30 years’ experience in the HDPE piping industry. Inkulu is a Level 2 BBBEE contributor with a dedicated focus on transformation, technical training and skills transfer.
An extruded pipe section coming off the production line at Inkulu’s Hammarsdale factory

“Prior to the acquisition, our research showed that high-speed machines are far more efficient, significantly reducing the cost per kilogramme to produce plastic pipe. Faster output times now make us more competitive from a price perspective, as well as in terms of our turnkey installation and commissioning services,” he continues.
Standard industry material tests are conducted at Inkulu’s on-site laboratory according to SANS ISO 4427/ISO 4437. Inkulu is also ISO 9001, ISO 14001 and ISO 45001 certified, and is a member of the Southern African Plastic Pipe Manufacturers Association.
Gas market gains
Alongside its focus on the water and wastewater markets, Inkulu has identified growth opportunities for the fluid transfer of
liquid gas in an HDPE pipe range from 16 mm to 630 mm. Sectors supplied to date include the industrial, mining, municipal and residential markets. The latter includes the Steyn City mixed-use precinct in Gauteng, where Inkulu supplied and installed a residential gas reticulation network in 2017.
“Switching to gas as an alternative energy source holds huge potential,” says Reddy. “In this respect, HDPE lines – combined with electrofusion fittings – are ideally suited to this application.”
Manufactured in accordance with ISO 4437 standards, Inkulu’s gas pipe and fittings are quality tested throughout the entire production process to ensure safety and reliability. Available in coils and lengths, these gas pipes are specifically designed for buried installations and, like all HDPE products, they are maintenance free over their lifetime, corrosion resistant, easy to install and flexible, with high impact strength. A further advantage of HDPE pipe is its suitability for trenchless construction.
The material of choice
Within its operating range, plastic pipe has become the preferred material for all industrial sectors, including the rigorous demands of the mining industry, where corrosive fluid transfer is common. Within

Inkulu’s truck fleet ensures on-time delivery. Purpose-designed trailers cater for pipe lengths up to 24 m
PRODUCTION CAPABILITIES
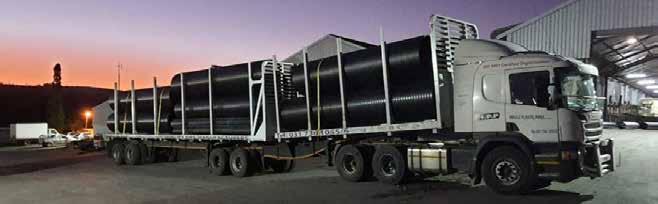
Materials
Depending on the application, pipe products can be supplied in three different materials, namely: • HDPE • LDPE • PP
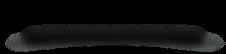
Products
• Coiled: HDPE pipes 16 mm to 110 mm • Lengths: HDPE pipes 125 mm to 1 200 mm • Perforated: HDPE pipes 63 mm to 1 200 mm • Plumbing hot water pipes, manufactured using PP • Telecommunication optic fibre
HDPE ducting • PE100 HDPE gas pipe • Manufactured fittings up to 630 mm • Moulded HDPE butt-welding and electrofusion fittings
the infrastructure space, Inkulu is experiencing growing demand for water, wastewater and stormwater applications as municipalities recognise the cost benefits compared to traditional pipeline systems manufactured from ductile iron and concrete.
Alongside its extrusion line acquisitions, Inkulu has responded to client requirements for turnkey solutions by investing in fabricated fittings equipment. A wide range of bends, tees, stubs, flanges, and reducers cater for pipe systems up to 630 mm.
“Through our ongoing research and development (R&D) programme, we’ve met the need for more complex and costefficient pipeline designs by means of HDPE fabricated fittings to solve installation situations where common fittings fail,” Reddy explains, adding that Inkulu also
To support its turnkey installation and commissioning services, Inkulu has invested in a wide range of welding technologies. These include butt-welding machines, socket fusion machines and electrofusion welding machines

supplies and manufactures moulded HDPE butt-welding and electrofusion fittings.
Keeping pace with the market, Inkulu’s ongoing R&D initiatives continue to tap into new niche markets. The latest developments include the production of PP plumbing hot water pipes, as well as telecommunication optic fibre HDPE ducting.
“Inkulu has established a well-proven track record for supplying quality pipes on time, focusing on establishing and building partnerships with suppliers and customers. Our recent capex investments now place us at the forefront of the plastic pipe manufacturing sector and we’re excited about the possibilities as more infrastructure projects come online in 2021,” Reddy concludes.
