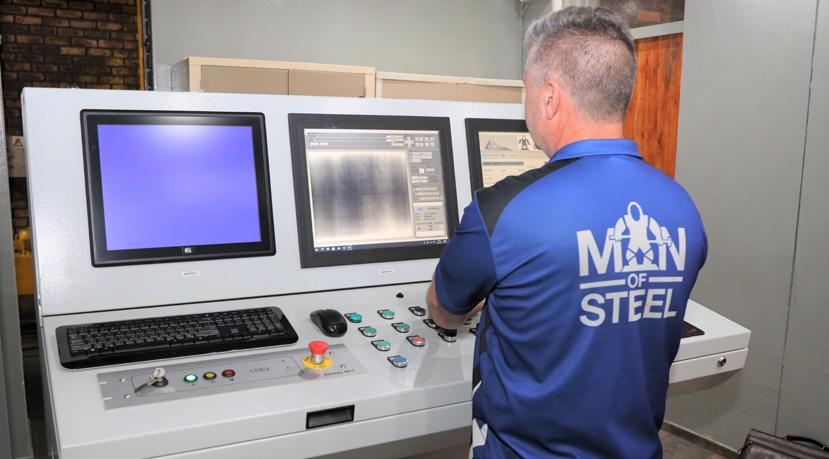
6 minute read
Switching over from analogue to digital radiographic pipe inspection
by 3S Media
A technician manning the new digital RT operator station. The three control screens (from left) show a live view of the pipe in the test bay, enabling the operator to perform a visual inspection for potential weld defects; the middle screen shows the X-ray image; and the third screen is the reporting system
Christo Le Grange, quality control manager, Hall Longmore
Advertisement
SWITCHING OVER FROM ANALOGUE TO DIGITAL
radiographic pipe inspection
Hall Longmore’s growth over close to 10 decades is the result of a concerted focus on product innovation, backed by best-in-class steel pipe manufacturing techniques. IMIESA speaks to quality manager
Christo Le Grange about the company’s latest investment in automated radiographic testing (RT) technology at its
Duncanville factory.
What is Hall Longmore’s current production focus and capabilities?
CLG Hall Longmore has two factories in South Africa, namely our Duncanville plant in Vereeniging, and the Wadeville facility in Germiston. Combined, these plants have the potential to produce around 230 000 tonnes of steel pipe annually.
These state-of-the-art manufacturing facilities feature the most modern pipemaking equipment, as well as specialist coating and lining application processes.
Our two main products are electric resistance welded (ERW) pipe and spiral welded steel pipe employing the submerged arc-welding (SAW) process. ERW pipe is manufactured in Wadeville for the oil and gas markets, as well as the water sector, with a strong export focus. In turn, our Duncanville factory specialises in the production of SAW products, with around 98% of our production serving the bulk water infrastructure market locally and in Africa.
Which pipe specifications are produced at Duncanville?
At Duncanville, we produce SAW pipes up to a maximum length of 19.2 m. Depending on the requirement, diameters range from DN500 to DN2 400 and wall thicknesses from 6 mm up to 20 mm.
What are the key quality control systems in place?
In line with international standards, steel pipe manufacturers globally are required to employ RT technology to performing non-destructive testing (NDT) on each welded pipe section as it comes off the production line. Inspection and fault detection are performed via a specialist fluoroscopic X-ray machine designed for industrial applications.
However, before each pipe reaches the X-ray test bay, there are a series of quality control steps required. For SAW pipe, the first requirement is the correct setup of the steel coil feed to ensure a sound and proper weld in line with specific codes and specifications.
Is RT a compulsory requirement?
RT is a mandatory requirement for SAW pipe in terms of the American Petroleum Institute standards, as is ultrasonic testing for ERW pipe. Locally, RT is also a supplementary requirement stipulated by water utilities for SAW pipe, in addition to hydrostatic pressure testing.
When was the first RT system installed and why opt for an upgraded unit?
Our first RT facility was installed at the Duncanville plant around 1994 and has been in daily use since then. It was cutting-edge technology at the time, back in the days when analogue X-ray systems were the norm. In the ensuing decades, however, the rise of digital electronic technologies has made analogue obsolete.
While our analogue RT unit has stood the test of time, it was clear that we needed to move into the digital world sooner rather than later and to provide our factory technicians with the
current technology; with digital RT, inspection times will drop dramatically.
Being digital, the latest RT systems are designed to integrate into the plant’s IT infrastructure. In the past, X-ray test parameters needed to be inputted manually within the analogue environment. However, thanks to digital RT, the process is now almost 100% automated, which makes it far more accurate in terms of defect detectability. All the operator needs to do is type in the unique pipe ID and the system takes care of the rest.
Who supplied the digital RT system and how much did it cost?
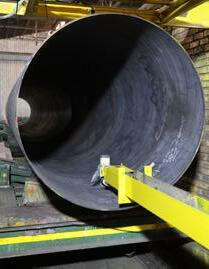
Hall Longmore’s new digital RT system undergoing commissioning trials in the X-ray test bay at the Duncanville factory
All the components for our new inline RT system have been sourced from Balteau, a leading OEM based in Belgium. Locally, the supply and commissioning of this custom solution has been carried out by NDT specialist H. Rohloff, and the overall project cost is estimated at around R5 million.
To protect against radiation, strict safety protocols have been implemented. The operator control room is shielded from the X-ray inspection bay by a specially designed steel door that if opened accidently, automatically shuts everything down immediately.
To the best of our knowledge, this is the first digital RT system installed to date within the South Africa steel pipe manufacturing industry and it is capable of X-raying up to a 40 mm pipe wall thickness. The system has taken around five months to install and commission.
The SAW pipe mill at our Wadeville factory currently has a similar analogue X-ray device to the one now decommissioned in Duncanville. So, once we’ve optimised the new system here, our next project will be to transition Wadeville to digital RT.
How different is analogue versus digital RT technology?
There is a massive technology gain. Ten times faster inspection speeds are now possible without sacrificing quality of testing. We’re proud to say that, even with the old analogue system, we’ve been consistently below this threshold.
The RT system incorporates an uninterrupted power supply backup system, which provides added assurance during load-shedding Additionally, the process is more accurate, fully computerised and delivers enhanced traceability. This time constraint liberation leads to increased quality throughput and costeffective manufacturing.
The operator station on the new system has three screens. The first shows a live view of the pipe in the test bay, enabling the operator to perform a visual inspection for potential weld defects; the middle screen shows the X-ray image; and the third screen is the reporting system.
Information is recorded as raw data in exhaustive detail. This means that at any time – even 10 years later on a possible pipe failure dispute – all the data can be recalled and re-analysed as if you were X-raying the pipe for the first time. That’s in comparison to analogue, where the report only records the once-off findings of the inspector.
Will digital RT make you see things differently?
Over time, digital RT will help us pinpoint further quality improvements that will take Hall Longmore’s reputation for product excellence to new heights due to enhanced weld defect detection. The continuous feedback loop from the digital RT team to the production setup team will also lead to a much higher rate of first-time passes.
Internationally, the accepted norm for pipes that fail the RT test – in other words, where weld defects are detected – is less than 3%, which is also Hall Longmore’s quality target.
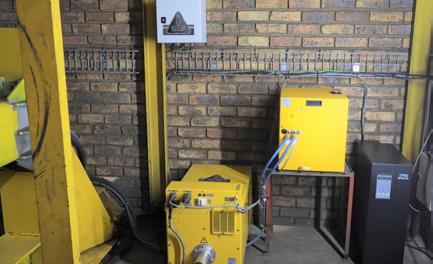
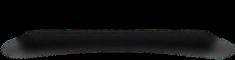

An overview of the RT setup
And in closing?
At Hall Longmore, we strive to be in line with modern and up-to-date inspection and testing solutions, which not only meet but exceed local and international standards. Quality is non-negotiable and we use the best technology available to ensure we supply our customers with world-class products made in South Africa.
KEY BENEFITS OF DIGITAL RT COMPARED TO ANALOGUE
• Increased defect detectability due to higher sensitivity • Significantly lower background noise with digital filtering • Contrast adjustability for fine defect detection • Lower X-ray radiation energy due to enhanced image detectors that require less energy • Fixed X-ray energy for multiple thicknesses due to adjustable contrast settings. (With analogue, varied X-ray energy is required for different thicknesses) • 10 times faster inspection speeds are now possible without sacrificing quality of testing • Instant result storage and reporting • X-ray results are immediately available and transferrable • Automated spraying unit to ID and mark defects