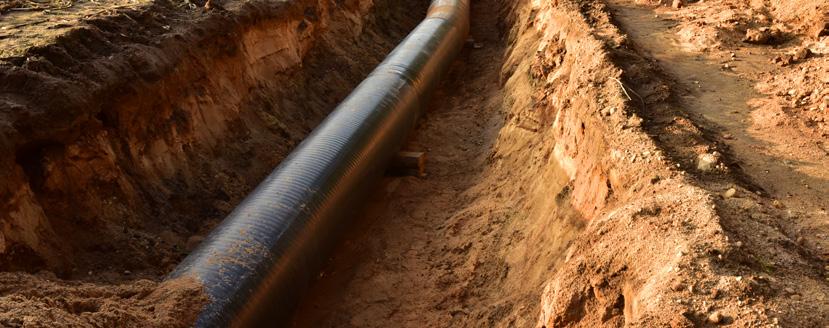
6 minute read
Bedding, embedment, backfill and compaction
by 3S Media
BEDDING, EMBEDMENT,
BACKFILL AND COMPACTION
Advertisement
Engineering soils are produced by the erosion of the earth’s crust. They change in character by being moved from the source. Particle shapes change from angular to rounded, and are then sorted and graded. Water is the most productive of all soil-forming agencies (see Arthur Casagrande’s Soil Classification).
Classification of engineering soils
The classification of engineering soils is a complex and exacting science that requires extensive investigation, testing and analysis to precisely define a given soil (see COLTO classifications G1 to G9).
There are four basic methods of designing a road structure. These methods, based on AASHTO Soil Classification, are not applicable to bedding, embedment and backfill of pipelines: 1. Group Index Method: US Highway Engineers’ empirical quantity calculated from the soil’s grading and Atterberg limits. 2. Shear Strength Method: links it to theoretical stress imposed on pavement and subgrade that ignores repeated loading effects. 3. Californian Bearing Ratio (CBR) Method: subgrade empirical property measured by empirical penetration test. 4. Modulus of Elasticity Method: considers this the critical soil property. However, for the purposes of bedding, embedment and backfill of a pipeline, the broad general classification of soils may be sufficient as follows: • coarse-grained or non-cohesive soils • fine-grained or cohesive soils • organic soils (peat); extremely treacherous and troublesome. The characteristics of coarse-grained (sand) material is preferable for bedding, embedment and backfill for a pipeline – although limited amounts of fine-grained (clay) material, indicted by the PI (Plasticity Index), can be tolerated but must be specified and controlled.
Soils are mixtures of particles of various sizes, but the properties of a soil are, to a great extent, determined by the predominant particle size in its composition – the MIT (Massachusetts Institute of Technology) classification system is based upon particle size.
Results of sieve analyses are plotted as a grading curve; the log-scale abscissae are particle sizes and percentage by weight finer than the given particle size, the ordinates. For engineering purposes, a well-graded material has greater strength and stability.
Two figures provide an approximate description of material as follows: 1. Effective size – maximum particle-size of the smallest 10%. 2. Uniformity coefficient – ratio of the maximum of the smallest 60% to the effective size. A uniformity coefficient approaching 1, the minimum possible, shows a high degree of uniformity.
Two fine-grained soils with similar grading curves may have widely divergent engineering properties and characteristics caused by the varying properties of the clay minerals in the soil and their different effects when the moisture content varies.
Fine-grained soils, formed by slow settlement of particles suspended in water during which consolidation and drying occurs, go through clearly defined stages, the Atterberg limits. Moisture content is the ratio of the weight of water to the weight of solid in a given volume. Everything a civil engineer designs and constructs rests on, or in, the earth. Soil mechanics play a pivotal role in laying pipes.
By Mike Smart*
Thermoplastic pipes
Reinforced concrete pipes have dominated the gravity pipeline market because engineers know that when a reinforced concrete pipe is delivered, the conduit and structure is delivered too. With a thermoplastic structured wall pipe (SWP), only the conduit is delivered and the structure must be constructed on-site. Thermoplastic SWP relies on the ‘soil-pipe’ structure that is constructed in situ with the pipe and its embedment.
Compaction is the expulsion of air, consolidation the gradual expulsion of water, from the pores of saturated cohesive soil. Two common compaction tests, Standard Proctor (25 x 5.5 lb x 12”) and Modified AASHTO (25 x 10 lb x 18”), classify the density of a material.
Thermoplastic pipe standards, thermoplastic pipe literature and TEPPFA specify 95% Standard Proctor compaction but the South African construction standard, SANS 2001-DP1 Earthworks, specifies: - 90% Modified AASHTO for bedding - 93% Modified AASHTO in traffic areas for cohesive soils - 98% Modified AASHTO in traffic areas for noncohesive soils. These road construction specs are potentially detrimental to thermoplastic pipes – because compaction energy goes into soil and pipe alike.
The compactive effort applied to the sample in the Modified Proctor (Mod. AASHTO) test method is over 4.5 times that applied to the same size (1/30 ft³) sample in the Standard Proctor test method. The Modified Proctor, known as ‘heavy’ compaction, was devised by AASHTO (American Association of State Highway Transport Officials) to simulate conditions where heavy compacting equipment is used in highway construction.
TABLE 1 Comparison of Original and Modified Proctor
Method Name Applicable Standard No. of Lifts No. of Blows Mass lbs Drop inches Energy ft-lb/ft³
Standard Proctor ASTM D698 AASHTO T99 3 25 5.5 12 12 375
Modified Proctor ASTM D1557 AASHTO T180 5 25 10 18 56 250
It is imperative that the compaction of the embedment supporting the haunch of the pipe is conforming to enable the compaction of the embedment at the ‘halfpipe level’ to be conforming to enable it to transfer loads on the pipe to the trench walls, to limit the deflection to the predetermined design magnitude.
The ETH’s (Swiss Federal Institute of Technology Zurich) IGT (Institute of Geotechnical Engineering) produced a technical report in December 2004, ‘Correlation between the values of Compaction AASHTO-Standard and AASHTO-Modified’ – the results of which are reproduced in Graph 1.
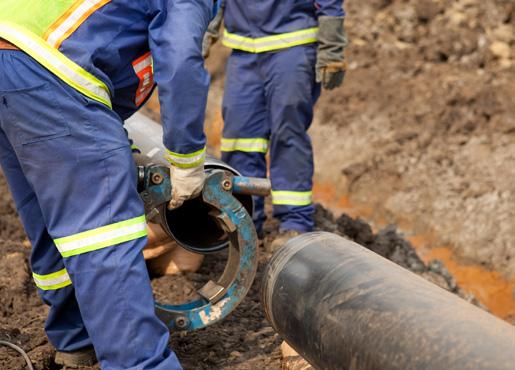
GRAPH 1 Correlation Standard AASHTO and Modified AASHTO

η = 0.95 = SC Well graded sand-clay mixture; excellent binder η = 0.97 = GP Poorly graded gravel/ gravel-sand; little or no fines η = 0.97 = GW Well-graded gravel/gravelsand; little or no fines
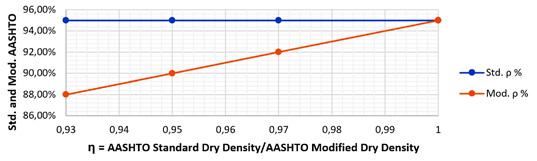
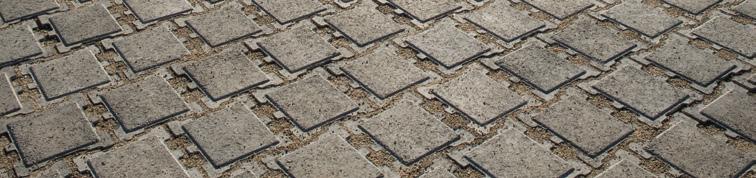
TABLE 2 Standard Proctor and Mod. AASHTO Tests Comparison
Method Name Layers No. Blows No. Mass lbs. Drop inches Compaction ft-lb/ft³
Equivalent energy
Standard Proctor 3 25 5.5 12 12 375 56 per layer Modified AASHTO 5 25 10 18 56 250 25 per layer
Note: Both tests use a cylindrical mould, 4 inches in diameter of 1/30 ft³ volume. Both samples receive equal energy if 56 blows are applied in Standard Proctor
The relationship between the compaction factors is dependent upon the classification of the soil being compacted. A Casagrande Classification SC material will achieve 95% Standard Proctor compaction with 90% Mod. AASHTO compaction. Different classification soils will have different ratios for the two compaction methods. A comparison of the compactive effort of the test methods is shown in Table 2.
Well-graded soils compact better than poorly graded soils. Moisture content in excess of optimum moisture content reduces dry density because the pore water pressure pushes the soil particles apart, increasing the volume between them.
Thermoplastic SWP manufacturers must understand, when the pipe has been manufactured, delivered and joined in the trench, approximately half the work to construct a pipeline has been done. The other half is the construction of the ‘soil-pipe’ structure on-site that must be conforming if the pipeline is to function as designed. The SANS 2001DP1 must be revised to take cognisance of the requirements of thermoplastic pipelines by replacing Modified AASHTO with appropriate Standard Proctor values. The thermoplastic SWP requirement, that a ‘soil-pipe’ structure is constructed, must be explicitly expressed in contract documents to establish its importance to the conformance and performance of the pipeline.
The bedding, embedment and compaction of the pipeline is an integral part of the pipeline’s construction to enable it to deliver its designed service life, of not less than 50 years, as a sustainable buried conduit.
*Owner of Genesis Consulting. References available from the author on request: mike@genesislabour.co.za.
