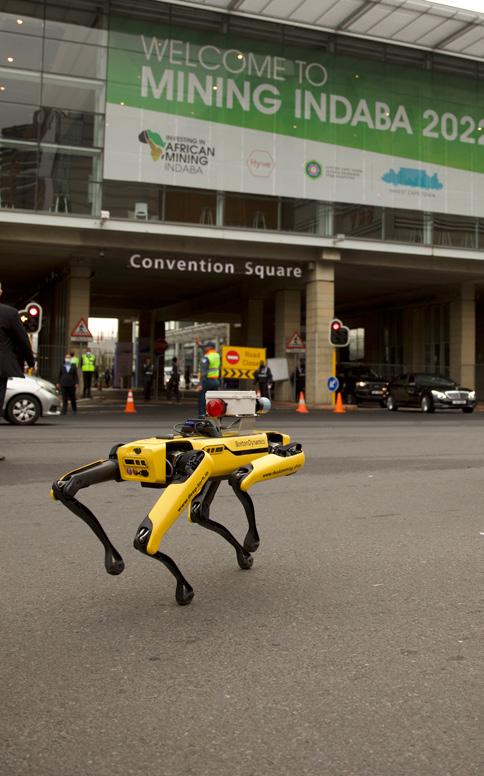
7 minute read
An unusual canine spotted at Mining Indaba
Boston Dynamics’ Spot Enterprise robot stole the show at Mining Indaba 2022, where it illustrated how technology can be used to address various issues in the mining industry.
An unusual canine spotted at
Advertisement
Mining Indaba
The robotic dog was a major attraction at Mining Indaba 2022 S pot Enterprise is an agile mobile robot designed to navigate all types of terrain, allowing organisations to automate routine inspection tasks, capture data securely and safely, and drive streamlined operations in complex and dangerous environments.
This new development is equipped with Maestro’s industrial internet of things (IIoT) gas sensor, which can be operated on mine sites to detect hazardous gases like carbon monoxide, without putting mining and ventilation teams in danger. Teams will easily be able to add different gas sensors on to Maestro’s connected Zephyr Air Quality Station, capturing critical environmental data to proactively identify gas or temperature concerns.
“We are excited to share our new best friend Spot and its amazing capabilities with the delegates of Mining Indaba and the global mining industry. In the spirit of technological collaboration, we have assembled the world’s best mining technologies to be on the stand with us to share and conceptualise end-to-end solutions for maximum impact for our mining clients,” said Jamie van Schoor, CEO of Dwyka Mining Services.
During Mining Indaba, various experiments were done using a series of partner payloads. A number of devices can be attached to Spot to extend the robot’s ability to capture and process data, acting as remote sensing devices that allow Spot to hear, see and smell in a virtual capacity.
As part of Spot’s introduction to the mining fraternity, delegates walked a mile with Spot from the V&A Waterfront to the Cape Town International Convention Centre (CTICC) to benefit the NSPCA. This 1.6 km walk started at Nobel Square in the V&A harbour, where Spot was sent on his way by Nobel prize winners like Nelson Mandela and Desmond Tutu, streaming live content all the way to the CTICC.
On-board processing capabilities Using the Spot Enterprise on-board processing capabilities, the data is shared over Wi-Fi. Gas and temperature sensor readings are captured while the robot is in operation and displayed in real time via the MaestroLink application. With the addition of a SLAM scanning unit sensor, like the Emesent Hovermap, readings can be saved with precise coordinates in a high-fidelity point cloud that can be exported and examined in a variety of mining software packages.
“Spot is an amazing platform with almost unlimited applications. The ability to get live environmental monitoring data ‘on the go’ by extending our remote-sensing capability to ‘smell’ for hazardous
TECHNOLOGY

gas detection from our new robot dog is very exciting,” said Rethabile Letlala, operations director of Dwyka Mining Services.
Hazardous gases that accumulate underground are an invisible threat to mining teams who often don’t know they are in danger until it’s too late. This gas build-up is created through the exposed strata, blasting, daily ‘mucking’ and even runaway battery fires on critical machinery. Traditionally, gas levels are measured by the ventilation system at the return air raises or wearable sensors donned by miners. While this fixed infrastructure has saved countless lives, mobile autonomous inspection by aerial and ground robots of strategic areas before re-entry or in emergency situations is the next step to complete real-time coverage.
With South Africa having many of the world’s deepest and hottest mines, the adoption of innovative solutions for ventilation, occupational health and environmental hazards and the use of proactive visualisation automation platforms are paramount for industry sustainability.
“The established client base of Maestro Digital Mine environmental sensors will allow us to make the technology mobile for broader applications. We’re very excited about this integration with Maestro Digital Mine as a future partner payload for Boston Dynamics’ Spot Enterprise solution and look forward to continually improving worker safety for whole-of-mine deployment with our new best friend Spot,” said Van Schoor.
“Collaborating with our mud-in-boots partner, Dwyka Mining Services – who are always pushing the envelope with technology integration with pioneering brands like Boston Dynamics – is in turn pushing us to innovate and collaborate with our core purpose of enhancing lives by the pursuit of productivity and safety excellence,” said Michael Gribbons, CEO and co-founder of Maestro Digital Mine. “This relationship will open up immediate opportunities to Dwyka Mining Services and Maestro in Africa and extend mobile environmental monitoring to our current installations at over 170 mines in 38 countries globally using our patented, Edge-based IIoT sensor technologies once the solution is fully embedded.”
“We are excited about extracting value from ‘no-go’ and ‘fly-low’ mining areas typical at the majority of narrow reef mining operations in Southern Africa where the use of enterprise GPS-denied drones becomes limited. The Spot Enterprise package allows us to access confined spaces and this information could be used to undertake remote gas inspections so that we can accelerate re-entry
The Spot Enterprise robot dog during the 1.6 km walk from the V&A Waterfront to the CTICC
TECHNOLOGY
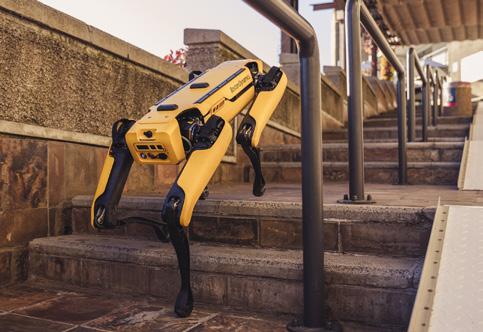
to target, getting ore to surface sooner without comprising safety,” commented Van Schoor.
The adoption of underground mining technology is linked closely with the extent of mine-wide wireless connectivity available up to the working face. Generally referred to as the last mile – the underground section from a level access to the blast face – this area is a complex space in which to deliver robust wireless coverage.
Plexus PowerNet delivers a high-speed, low-latency digital communication network that provides PoE+ power to wireless access points (WAPs), cameras and any other IP-based device. The system eliminates the need for costly outside fibre-optic contractors and can be installed and maintained by any internal tradesperson. With global success as a last-mile solution to connect mission-critical assets, robotic dogs are the next connected device to be connected as we race to the face.
Solving problems beyond human capabilities
Speaking to Inside Mining, Van Schoor explains that a robot dog is a great innovation, as is can solve problems that many humans cannot. “It allows us to access no-go areas. These no-go areas are the kinds of environments that we wouldn’t want to put humans into, either because there are environmental issues like gas and temperature, or because of unsupported areas in an underground mine.” He adds that such areas are common places for incidents resulting in injuries/fatalities. “Spot thrives in these environments because it is able to handle tough conditions in very dark, dusty and dangerous environments.” As a ground robotic platform, Spot Enterprise can be used to send different payloads – devices that can be attached to Spot – to extract mission-critical data from the required location. “These are normally the most challenging environments [from which] to extract data.” The agile robotic dog is able to navigate through different terrain, including loose ground, rocks and slippery underfloor footing.
Additional capabilities
Spot Enterprise has other applications such as gas monitoring on a mobile platform and acoustic sensing devices (in partnership with Fluke) that pick up faint decibels such as the hiss of a compressed-air pipe leak.
There are also opportunities for the robotic dog to contribute to drilling and blasting by reducing the travelling time in this area. Van Schoor explains that travelling to the working area of a deep underground mine can take one to three hours. “Once the blast happens, it takes one to three hours to flush this mine from its blast gases.”
He believes that Spot Enterprise could add value by potentially saving up two hours a day from each blast, which equates to 40 hours a week. “Extracting 40 hours of remote sensing capability to have a better idea of not only the blast performance, but the safer working conditions of the most valuable assets, humans, is something that we should be prioritising.”
There was a lot of excitement around Spot at Mining Indaba, notes Van Schoor. “The team could see how much excitement and happiness it added to the general population of Cape Town.” The team expects that the excitement can transcend into business value through the correct assessment of unique user requirements and ensuring that Spot is equipped to handle and measure the right kinds of data to better navigate accurate decisions in a timely fashion.
“The basis of short-interval control is the practice where mining companies are able to make better decisions faster based on more timely information. We believe Spot is going to be able to address this by being able to auto-walk from underground locations, thereby reducing the downtime of travelling time, as well as equipping it with advanced sensing capabilities to deliver information to humans for more proactive decision-making from the surface,” Van Schoor concludes.
With Spot’s intervention in drilling and blasting, mine workers will not only operate in a safe environment, but also redirect resources to ensure that they can complete the task to avoid instances of a lost blast, which is costly. Be it before, during or after a shift, workers will be able to operate in a safe environment.