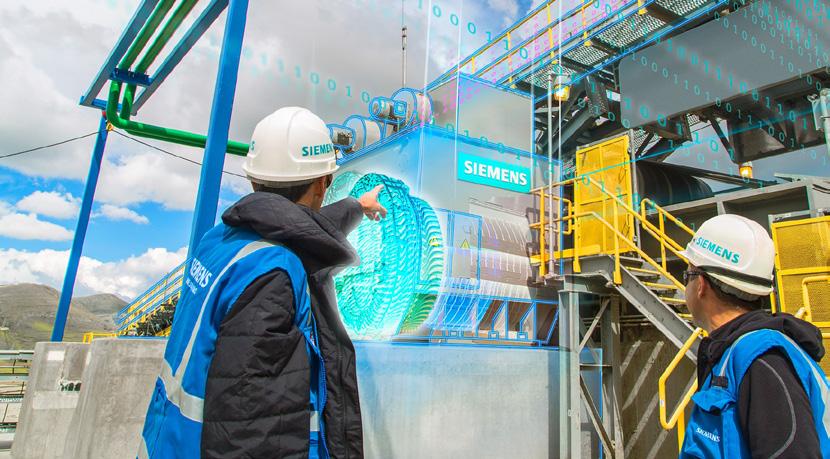
5 minute read
Building capacity and reliability in mining materials handling
Digital insights are delivering step changes in the efficiency of materials handling operations through integrated processes and proactive maintenance services.
Digitalisation will play a major role in the future of materials handling in mining. It will not only be key in delivering mines to the next level of efficiency, but will also initiate changes in the industrial landscape going forward.
Advertisement
Sabine Dall’Omo, CEO at Siemens Southern and Eastern Africa, discussed the trends taking place with materials handling operations. “We already see a clear trend of process integration through applying digital technologies vertically and horizontally,” she says. “This delivers complete integration through all the technical hierarchies, from the field level up to enterprise resource planning (ERP), as well as complete integration in plant life-cycle management, from design up to operations. This improvement will make significant opex and capex savings possible and also open up new ways of production management. For instance, by integrating different kinds of simulation technologies, a beneficiation process can be tested and even fine-tuned before production starts.”
The benefits can also extend across the value chain. For example, using digital insights, production management can be conducted end-to-end based on the market needs and price realisation possibilities; the digitalisation journey in mining is just beginning. Dall’Omo points out that digitalisation also has a critical role to play in decarbonising mining — a key focus for most major and mid-tier miners currently. “Both digitalisation and electrification will be key in creating more sustainable business practices,” she says. “Therefore, for us at Siemens Large Drives Mining, these themes are a central component of our portfolio going forward. We are working with multiple external partners to extend our portfolio and to drive the digitalisation of the mining industry together. It’s an agile and fast developing area of the market, which requires openness and collaboration.”
Siemens: integrated expertise for digital mines
The challenges and opportunities associated with digitalisation are unique to each client and each mine site. Every company has different needs that require appropriate offerings. According to Dall’Omo, Siemens is able to assist customers who are in their infancy with their digital journey, by encouraging them to build a path towards integrated digital solutions. “For customers who are already in the implementation phase, we are able to offer a full suite of products and services, including engineering services based around functional requirements, and architecture design based on our multiple solutions. Complete software development can also be offered on a case by-case basis,” she explains.
Siemens has various solutions for various applications within materials handling. For electrification, there is the innovative SIMINE solutions for mills, conveyors, mobile mining, trolley truck systems and mine hoists. There are also products and solutions for automation systems, which are customised especially for the mining industry.
In partnership with MineSense, Siemens also introduced the latest developments in digitalisation. This enables the determination of ore characteristics in real time along conveying systems as well as material and quality management systems.
SIMINE Digital Twin expands
Among the solutions planned for implementation in 2022 is the Siemens Digital Twin for mining processes. While this has been available for grinding mills for some time, the solution has been extended to incorporate the transportation and crushing portions of the process as well. Dall’Omo explains that the integration of these processes will deliver the next level of operational improvements for mine operators.
Artificial intelligence, simulation and interaction with the user (e.g. in order to store and reuse operational experiences) are just a few of the features that are now included in the SIMINE Digital Twin. Dan-Niculae Fodor, head: Minerals Portfolio Management and R&D, Siemens, is leading the development of the technology.
“This year, we plan to focus on integrating the major mining processes, which are transportation, crushing and grinding,” he says. “This includes the optimisation of complex mining pit-to-stockyard systems or even just simple belt conveyors. The pilot application, which will start being implemented during 2022 at a mine in the Americas, includes trucks for the first stage of transportation from the pit to the primary crusher, as well as a conveyor line with more than 10 conveyors for the further transport to stockyard.”
While grinding mills are complex and their optimisation in isolation can deliver benefits, to realise a step change in production performance and keep downtime to an absolute minimum (both planned and unplanned) requires a process-level approach. “We’re taking the experiences that we gained with our MES manufacturing execution platform that we developed about seven years ago and applying it to build out our Digital Twin offering for mining,” Fodor explains. “IoT-enabled tools, such as asset health analytics for mills, which help mines reduce their costs and improve the reliability of their equipment, are high on our clients’ agenda at the moment, especially given current high metal prices. Remote operating capabilities are also important in tackling personnel access and travel restrictions resulting from the Covid-19 pandemic. These customer requests are some of the major factors that have guided us in developing our latest solutions.”
The beauty of working across multiple sectors – including mining, infrastructure and transport – is that Siemens can draw upon and integrate its own expertise to create enhanced solutions and technologies for clients in each of its divisions.
Dall’Omo further adds that Siemens now has a huge advantage through offering a full range of solutions for mission-critical mining applications like conveyors and grinding mills. “In addition to providing the software and technologies for automation and digitalisation, we also provide the hardware. Combining our know-how in both areas is incredibly powerful,” she concludes.
At Siemens, we want to become a partner to all stakeholders to support them towards a more sustainable economy, by creating sustainable value. It is thereby our highest priority to take leadership towards decarbonisation and responsible business practices as a company and be the technology leader in addressing our customers’ ESG goals and more particular climate change ambitions.
In line with the Siemens Carbon Neutral Programme, we have committed ourselves to turn our operations carbon-neutral by 2030. Our goal is clear: all Siemens production facilities and buildings worldwide are to achieve a net zero-carbon footprint by then. This programme does not only benefit humanity and the environment, but also comes with sustainable economic advantages for our company.
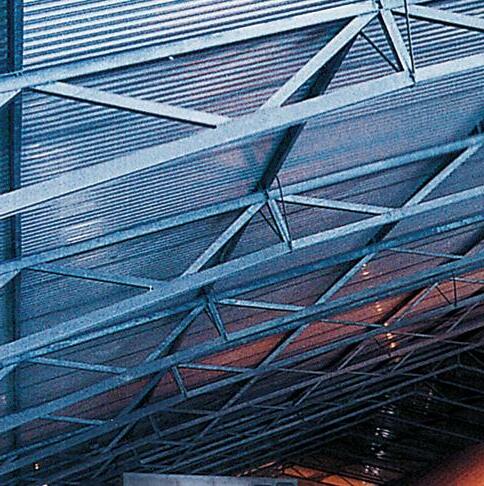
TECHNOLOGY
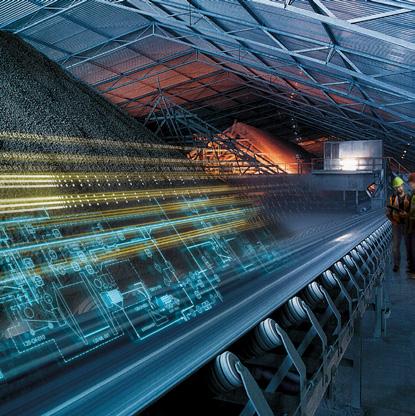

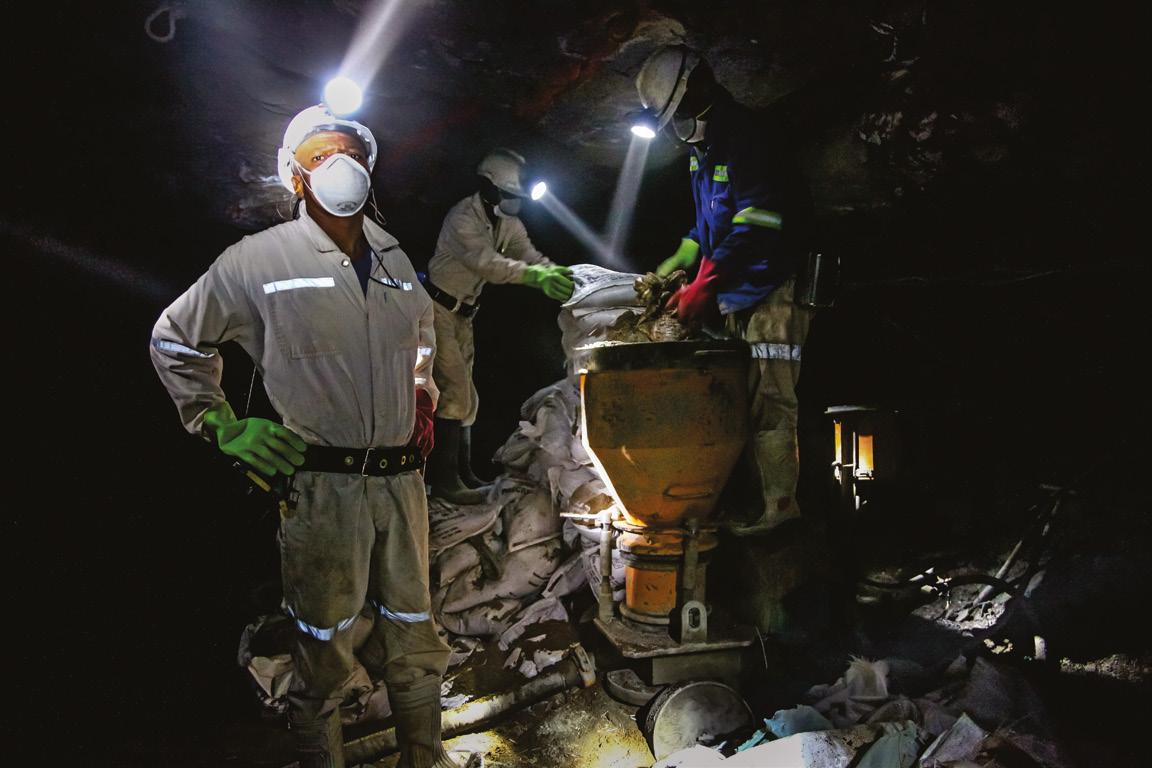