LEADERS WALK THE TALK
Improving mine health & safety

GREEN METALS
A booming market for EVs
THE ENERGY TRANSITION
A growing demand for Africa’s critical minerals
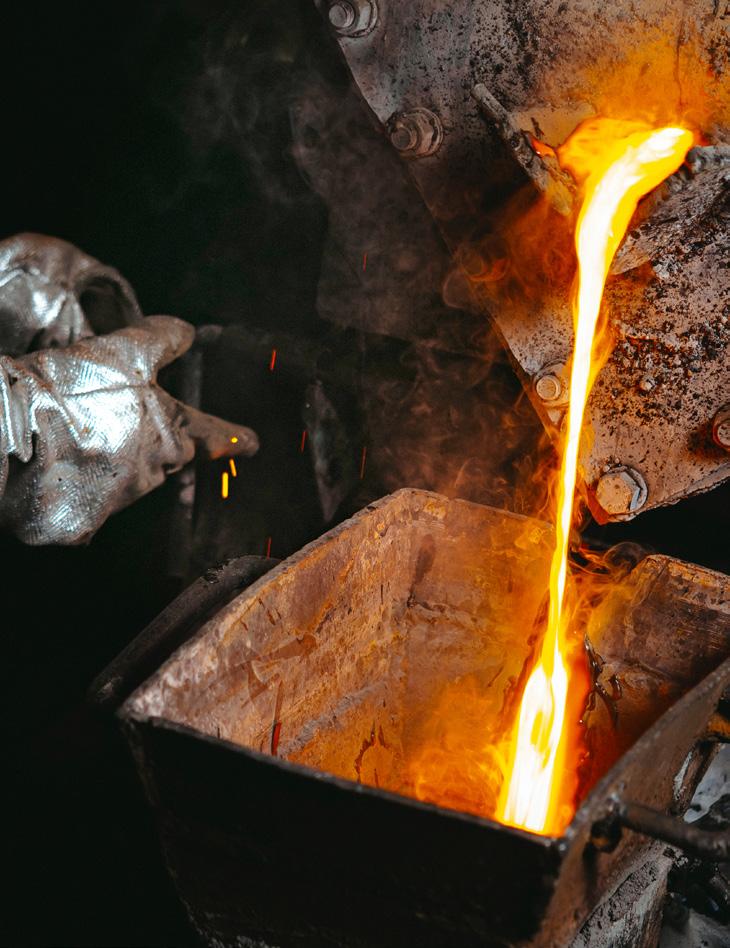
Improving mine health & safety
GREEN METALS
A booming market for EVs
THE ENERGY TRANSITION
A growing demand for Africa’s critical minerals
Through GIW® Slurry Pumps, KSB is an innovative partner that provides you with the best and longest wearing slurry solutions. We are your partner over the entire lifecycle of your GIW® slurry pump
KSB Pumps South Africa is a globally recognized pump solutions provider that manufactures globally recognized products locally to the highest quality standards both internationally and locally.
We not only manufacture and service your slurry pumps, we offer total slurry solutions to your industry.
KSB Pumps and Valves (Pty) Ltd
Tel: +27-11-876-5600
www.ksb.com/en-za
Level 1 B-BBEE Supplier
Get in touch with Inside Mining’s sales team to sponsor the upcoming issue of the magazine. Contact Chilomia Van Wijk (+27 11 233 2627/ Chilomia.VanWijk@3smedia.co.za) or Amanda De Beer (+27 11 233 2612/ Amanda.DeBeer@3smedia.co.za).
It’s not often that one gets to witness a paramount chief deliver a speech at an event, as tribal councils often speak on their behalf. Things were different when I witnessed Her Majesty, Queen Mother Manyaku Thulare of the Bapedi Nation address attendees during Nkwe Platinum’s Social and Labour Plan (SLP) Water Supply Projects handover ceremony.
Nkwe Platinum hosted a ceremony to hand over the SLP Water Supply Projects to Sekhukhune District Municipality in Limpopo. There were many speakers during the ceremony, including representatives of Fetakgomo-Tubatse Local Municipality, tribal councils and Sekhukhune District Municipality.
The Queen Mother was dressed in a colourful pleated dress with Ndebele patterns, draped with traditional leopard-printed skin, which made her stand out. Surrounded by her royal entourage, she spoke with much grace and her aura of authority was evident in the way she captivated the audience.
What was most impressive was what the Queen Mother had to say; unlike the other speakers, her utterances were those of a true leader. After expressing gratitude towards Nkwe Platinum for the SLP water supply projects, she mentioned that the projects brought dignity and hope to the community, adding that community members could stand tall and walk proudly because they now had access to clean drinking water. Affectionally referring to the community as ‘children of Thulare’, the Queen Mother also implored community members to look after and guard the projects as they were now the community’s responsibility.
South Africa’s socio-political factors and challenges such as high unemployment have often led to community-related protests and unrest. The Queen Mother sternly condoned violent protests by community members when they are unhappy about anything. She stressed that violent protests were an old way of doing things and that it was uncivilised. She rather encouraged all stakeholders to normalise a culture of sitting around the table to discuss and resolve any problems and grievances that may arise. She also stressed the importance of communication.
The Queen Mother’s speech hit all the right notes, without creating unrealistic expectations. Her utterances were that of a true leader driving nation-building and collaboration for success. We can only hope that her wise words did not fall on deaf ears.
EDITOR Dineo Phoshoko (dineo.phoshoko@3smedia.co.za)
HEAD OF DESIGN Beren Bauermeister
CHIEF SUB-EDITOR Tristan Snijders
CONTRIBUTORS Sarika Andhee, James Chester, Spencer Eckstein, Anton Fester, Roland Innes, Wynand Marx, Chetan Mistry, Yershen Pillay, Noora Puro, Lani van der Merwe, Louise Woodburn
PRODUCTION
DISTRIBUTION
PUBLISHER
Novus Holdings is a Level 2 Broad-Based Black Economic Empowerment (BBBEE) Contributor, with 125% recognised procurement recognition. View our BBBEE scorecard here: https://novus.holdings/sustainability/transformation ISSN
Rising demand for critical minerals and metals, fuelled by the energy transition, has placed African producers in a strategic position to unlock their vast mineral resource wealth and diversify global supply. By
The global energy transition represents the key to unlocking a bull market for critical minerals and metals in Africa. Boasting commercially significant deposits of the very minerals essential for the development of green technologies – such as electric vehicles, solar and wind installations, batteries and renewable power systems – Africa’s mineral wealth can be leveraged not only to reduce the global carbon footprint, but also create new economic opportunities, build diversified industries and drive sustainable growth across the continent.
As the world progresses towards a low-carbon economy, the ability to transition relies on the stable supply of raw materials like lithium, nickel, cobalt, graphite and manganese. The International Energy Agency (IEA) projects that by 2040, the demand for critical minerals will grow on average by four to six
times, driven largely by the green-tech industry. Reinforcing this point, the World Bank estimates that the production of critical minerals would need to increase by 500% in order to mitigate the worst effects of climate change.
Since 2012, the minerals market has seen its largest jump ever – with lithium production growing by 200%, rare earth elements (REE) growing by 100% and chromium growing by 50%. Yet despite the intensity of such growth, global demand continues to outweigh supply.
As governments continue to put in place green policies aimed at decarbonising national energy matrices, price fluctuations and inconsistent supply have restricted the pace of the transition. According
James believes that Africa’s mineral resource deposits are unparalleled –leading to strategic opportunities in the critical minerals sector
to the IEA, recent price trends have emphasised the need for policy intervention to enhance the stability and resilience of the critical minerals supply chain. China is currently responsible for 60% of the world’s cobalt supply, for example, while Latin America accounts for 40% of copper production, and Chile and Argentina collectively produce 35% of the world’s lithium. As the global economy seeks to diversify its energy supplies in the face of ongoing trade wars, geopolitical conflicts and shifting market realities, a strategic opportunity has emerged for African critical mineral producers.
Africa’s unparalleled mineral resource deposits
So, why Africa and why now? Simply put, the continent’s mineral resource deposits are unparalleled. Nearly half of the world’s gold and a third of all minerals are located in Africa, and already several African countries are making a play for market dominance. South Africa currently produces 60% of the world’s manganese supply, 75% of platinum supply and 40% of palladium supply, while neighboring Zimbabwe and Namibia are close behind in the production of platinum and uranium, respectively.
The African Critical Minerals Summit will take place on 6 and 7 November 2023 in Johannesburg and is hosted by the country’s Department of Mineral Resources and Energy.
Over 2 000 delegates are expected to join the event, with delegations from the US, EU, UK, BRICS and G20 nations
In terms of proven reserves, the Democratic Republic of the Congo contains 70% of the world’s cobalt reserves, while Zimbabwe holds the largest lithium reserves globally, and Namibia is home to significant reserves of REEs such as dysprosium and terbium. The continent’s mineral resources represent a viable solution to powering the global green economy. Now is the time for investors to rally to finance a new era of mineral wealth and security in Africa and around the world.
That being said, foreign investment must go beyond extraction and extend to mineral processing and manufacturing capabilities. For Africa, the export of raw minerals accounts for more than 50% of export earnings for resource-rich countries such as Mali, Mauritania, Mozambique, Namibia, Zambia and Zimbabwe, yet unprocessed mineral exports limit the full value of and revenue generated by these precious commodities.
Currently, China is the dominant player in both the mining and processing of Africa’s critical minerals, accounting for 73% of cobalt processing, 40% of copper,
59% of lithium and 67% of nickel. Notwithstanding international concerns about Chinese interests in Africa, the trend of exporting raw minerals rather than finished products puts the continent at risk of being locked in as a crude supplier rather than as a global manufacturing hub.
Progress has been made to reverse this trend. Zimbabwe, for example, imposed a strict ban on the export of unprocessed lithium to encourage the development of a domestic mineral processing industry. Other countries have imposed similar policies, including Tanzania in 2017 and Uganda in 2013 – since retracted – while Zambia is also considering a ban on unprocessed mineral exports. The efficacy of these policies, however, largely depends on the flow of new foreign investments to support the creation of local mining value chains.
African Critical Minerals Summit
Stepping into this picture, the African Critical Minerals Summit will connect foreign investors with African mineral producers, laying the foundation for new deals to be signed that will alter the trajectory of the African critical minerals market. As the world looks to diversify extractive industry supply chains, untapped minerals and REE reserves, favorable investment policies and strong political drive will not only serve to accelerate the global energy transition, but also ensure that African economies are at the forefront of such developments.
The African Critical Minerals Summit will take place on 6 and 7 November 2023 in Johannesburg and is hosted by the country’s Department of Mineral Resources and Energy (DMRE). Over 2 000 delegates are expected to join the event, with delegations from the US, EU, UK, BRICS and G20 nations.
Minister Gwede Mantashe of the DMRE will discuss his minerals strategy – centred around South Africa’s Just Energy Transition framework policy, vast industrial mineral endowment and substantial manufacturing capacity – while establishing the country’s leadership role in the sector. Other regional heavyweights will showcase their own investment opportunities, while reinforcing the strategic link between African mineral resources and the global energy transition.
As the world mines for the future, Africa will power progress.
April 2023 saw the return of Exxaro’s Sustainability Summit – the first iteration since the outbreak of the global Covid-19 pandemic. Dineo Phoshoko speaks to Mongezi Veti, executive head: Sustainability at Exxaro, about the significance of present leaders for mine health and safety.
What is Exxaro’s approach when it comes to mine health and safety?
MV Health and safety at Exxaro have been part of an integrated strategy in the last 20 or more years. This shift was decisive because, at a particular time, we went through a bad patch. The organisation – year after year – kept on losing colleagues. It reached a point where the organisation decided to have an event like this that is aimed at bringing a representative sample of the entire organisation starting from the chairperson of the board and CEO, right down to the coal face.
This day has become a premier event for the organisation – so much so that it sets the tone for the year going forward in the area of safety and health. We have broadened it over the years into more than just health and safety, to include sustainability. The demand and the changes that the globe presents require us to seriously look at the environment, climate change, the closing of abandoned mines and land use. We have extended and expanded it to include sustainability aspects. We have also now included communities in the areas where we operate.
Over the years, Exxaro has achieved impressive fatality-free milestones across various operations. Please explain how the company managed to achieve this.
One of the key ingredients of a successful safety campaign is the ability to engage all employees in the operation. They begin to feel you and touch you as the leader of the organisation. You can’t manage safety remotely. You’ve got to be there, and people must see you and you must communicate with people. We’ve designed a communications strategy, emanating from this summit. From this summit, there are going to be subsequent indabas that mirror this event from all the business units so that you touch all the employees in the organisation because today is a representative sample of the organisation.
Mongezi has more than 40 successful years in the mining industry
Following this event, every business unit, every shift, will be exposed to this event according to the programme for this year. This has given us an opportunity to engage our people as safety becomes a way of life: ‘Safety always, all the way’ –our slogan. We talk safety literally throughout the year. There is no time when we only refer to safety after an accident. This approach has ultimately led to these phenomenal performances that we have seen. The time of fatality-frees that we have managed to achieve is just more than five years. This unfortunately ended in August last year. But we are up, dusting ourselves off and putting together all the pieces. We have done it before; we know we can do it again going forward.
What is your view of the current state of mine health and safety in South Africa?
There are still lots of pockets of excellence in the mining industry across the board. There are areas of improvement that can be focused on by all of us. First, the opportunity to harness the talent and the knowledge of our partners and also working together with the Department of Mineral Resources and Energy. The officials in that department are always ready and gladly waiting to assist us. Lastly, and most importantly, it
depends on the leadership style and the culture of an organisation.
If you are a leader of an organisation and you have never stood in front of everybody in your organisation and talked about how safety is important for your organisation, then you have not done it well, because then people do not know your thinking and your conviction about issues of health and safety. Most organisations have opened up and gone out to the people, asking them to rally together and become each other’s brothers’ and sisters’ keepers. As they work [together], they tend to work better.
What would you say are the important aspects to consider when it comes to zero harm in the mining industry?
Make it simple for the employees; don’t use complex and complicated language when you are launching a safety campaign. Make it relevant and make sure that people walk the journey with you, and they understand you. Use language that people can understand. Don’t make the drivers of the campaign senior people; make people who are driving the campaign people reachable to the employees. Make sure you use your own workforce for implementation rather than using consultants because consultants come and go – once they leave, everybody has forgotten about safety. But if you use your own internal workforce, you’ve got much better prospects for success because people are the asset of the organisation, and they become part of a process that creates a new culture of resetting safety and talking about safety every day.
For the South African mining industry to move forward in making sure that fatalities are drastically reduced, it is all about sharing the details of all accidents. We must all move away from the paradigm of thinking that if I fully disclose how this accident actually happened, I might be taking myself to the courts or jail. We must create a neutral space for people to be able to give full disclosure of what exactly happened in an accident without fear of retribution. If we do that, then we have more likelihood to be a better industry in South Africa, and across the world.
I must also state that if one looks back at the last 20 to 25 years, we’ve had a remarkable improvement. Last year, we had 49 fatalities in South Africa’s mining industry; the year before that, it was 71. We have a measurable improvement, but one fatality is still one too many. So, there is still more room for improvement in the industry.
Mining is notorious for being one of the most dangerous working environments in the world. As a result, it's imperative to understand the associated risks – not only the environmental hazards but the behavioural tendencies of the individuals working on-site. By
Consider a ‘workplace’ created by Mother Nature in all her beauty and brutality, coupled with heavy machinery, an often-autocratic leadership style and unrelenting target-chasing, and it’s unsurprising that we’ve seen so many fatalities in the past.
Yet, over the last few years, the public and private sectors have poured enormous energy into promoting health and safety within mines, with new safety controls developed and rolled out far and wide.
This approach is showing dividends, and the number of fatalities has dropped significantly compared to a few decades ago. However, sometimes rigorous checks and balances – while necessary – can be a double-edged sword should people become complacent, unduly confident in thinking that these controls alone will protect them.
In our line of work, as behavioural change consultants within the mining industry, we’re still seeing avoidable incidents in our mines. Research has indicated that between 80% and 90% of all accidents are caused by direct violations of safety rules, which can be in large part attributed to an individual’s underlying mindset and propensity to indulge in risky behaviour.
When we enter a mine, we typically conduct an assessment that measures an individual’s propensity to take risks.
This assessment, conducted in the form of a 3D game, helps us understand their risk tendencies. The game takes individuals through a series of risky scenarios that offer the potential for loss or gain, requiring them to make certain decisions. The assessment studies their decision-making in
these situations, and groups their behaviour into one of two distinct categories: Risk-seeking decision-making behaviour – an individual is confronted with a risky situation and displays a tendency to overestimate the probability of gain relative to the probability of loss.
Risk-averse decision-making behaviour – an individual is confronted with a risky situation and displays a tendency to overestimate the probability of loss relative to the probability of gain. By assessing these individual risk patterns, we’re able to understand the workforce’s general risk-taking tendency, which we categorise according to a Risk Propensity Matrix with four main risk profiles: Consistent Risk Averse (cautious and predictable);
Consistent Risk Taking (predictable in taking risks); Erratic Risk
Averse (cautious and unpredictable); and Erratic Risk Taking (takes risks but is unpredictable) – with Consistent Risk Averse being the least concerning from a safety perspective, and Erratic Risk Taking being the most concerning.
Once we have identified the workforce’s generalised risk profile according to the Risk Propensity Matrix, we take our subjects through various scenarios to help them understand the factors that might influence their behaviour. These include overestimating capability (“my strong body and work experience will keep me safe”), familiarity with task (“these everyday
Lani van der Merwe*
tasks are safe, I can do them without thinking”), the potential for profit (“if I finish this job quickly I will reach target, which means I will be rewarded with a bonus”), confidence in protection and rescue (“the rescue team will ensure my safety if I get into trouble”), and role models accepting risky behaviour (“my leaders take small risks so it’s okay”), among others. These can all influence one’s tendency to take risk.
Once we understand the workforce’s risk propensity, we work with them to change their behaviour by focusing on situational awareness, which involves making people stop and think – in real time – what constitutes an unsafe act that might lead to injury or fatality. We help them evaluate their own behaviour and the possible consequences.
A control, in itself, cannot keep you safe. Just like with Swiss cheese, any safeguard or control has certain ‘holes’. These holes could be organisational factors, unsafe supervision, preconditions or an unsafe act. Then suddenly, an initiating event occurs – such as the fall of ground – and multiple holes line up, creating a clear pathway for disaster. In other words, while an individual might indulge in risky behaviour 9 times out of 10 with no repercussions, all it takes is once for a perfect storm to occur.
For us to enhance the efficacy of our safety controls or regulations, we need to nurture a safety mindset in our workforce. This will protect individuals in the event that all ‘holes’ line up, helping them make better decisions.
A safety mindset is a mentality: a way of thinking and acting; a tendency or frame of mind; an intention and will to protect yourself and others; to control risk, and share safety values.
It is a set of underlying assumptions, beliefs and attitudes that result in an equal emphasis on a caring and controlling approach to safety. Our mindset influences our choices, actions and the way we respond to challenges and changes. It encompasses how we respond to rules and regulations.
Therefore, we teach our workforce how to apply situational awareness in their day-today work environment. We work with them to see the potential risk (risk identification), understand the risk (risk comprehension), and then think about how they respond to that situation (risk projection). We work with individuals to put together an action
plan to address their behaviours, which we reinforce through coaching.
Coaching can foster and reinforce a mindset that allows for deeper situational awareness, important for environments where a great deal of work is repetitive. Embedding this behaviour can help prevent someone from operating on ‘autopilot’ or becoming complacent. OIM Consulting’s Supervisory Development Programme, for example, is one such programme that develops and reinforces a safety mindset. Through our coaching, leaders and supervisors learn that by applying the right behaviours or social processes around certain technical levers, our behaviours can positively impact our performance and keep us safe. The safety controls and regulations that have come to the fore over the past few years are vital controls in promoting safety and should be adhered to. But we cannot become complacent or overly reliant on these
The core business of mines is to extract ore safely in line with market demand and forecasts, stockpile levels, processing capacity, transport and hoisting capacity, as well as the life-of-mine production profile. This requires certain enablers, such as adequate ventilation systems, to be in place to make this possible; however, many mines often consider these enablers to be a constraint to their operations and business plan, instead of a support.
Mine ventilation provides a flow of surface air to the underground mine workings of sufficient volume to dilute and remove dust as well as noxious blasting and diesel machine exhaust gases, typically nitric oxide, sulfur dioxide, methane and carbon dioxide, while also regulating the temperature.
Ventilation systems are also central to ensuring the optimal physical and cognitive ability of the workforce for maximum productivity without any health impact. These systems must also provide favourable operating conditions for equipment by removing heat and dust.
Unacceptable workplace conditions can result in ventilation related work stoppages when blast fumes are not cleared within the re-entry period, or when temperatures or noxious gas levels exceed defined limits. These are constraints that could prevent mining sites from achieving their production targets, resulting in mines rightfully placing the blame on the limitations of the ventilation system.
In addition, a mine ventilation system is an expensive enabler, especially from an electricity cost point of view, as it can account for up to a third of a mine’s operating cost.
At the same time, the ventilation system is significant to manage and maintain, and could potentially hamper the core business of ore extraction when it is underdesigned or fails. It requires a considerable engineering team effort to design, build, manage and maintain the
ventilation systems; if under-designed, there is often no quick fix.
To avoid ventilation constraints and balance productivity and ventilation, mines should ensure that the ventilation design function is fully integrated with the mine planning and design process. Ventilation can influence mining parameters such as concentration of mining, schedule, production, excavation layouts and sizing, as well as diesel fleet limits.
In the past, ventilation teams faced the challenge of not being fully involved in an iterative mine design process. They were typically given a mine design and tasked to ventilate it, potentially putting the ventilation team on the back foot.
In recent times, mine designs have increasingly had to prioritise ventilation considerations, mainly due to mines producing at higher rates and/or from deeper orebodies. Ultimately, if the mine planning and management processes embrace ventilation as an enabler, the mine will reap the benefits; equally, if ventilation is not adequately planned, integrated and managed, it remains a constraint. The benefits of a well-designed mine ventilation system by far outweigh the effort and cost of designing, installing and managing it.
By engaging a ventilation specialist with the adequate experience and knowledge, a mine can have a ventilation system designed that enables unconstrained mining as planned. Mining ventilation specialists have ample experience from around the globe and can leverage it to help mines design effective and efficient ventilation systems for the life-of-mine.
Mine ventilation is critical, as it provides a flow of surface air to the underground mine workings
Wynand also manages and contributes specialist technical input to a variety of ventilation and cooling projects
Ventilation is key to ensuring a safe and healthy working environment that promotes the wellness of the workforce, while minimising the risk of mining-related illnesses such as heat stress and silicosis. By Wynand Marx*
By using emerging technologies and trends, companies can also equip employees with training and knowledge retention strategies that empower them to effectively handle safety concerns and uphold a safe working environment. To successfully shift employee behaviour and gear their mindsets towards safety, organisations must adopt a topdown approach. This involves ensuring that the leadership group is aligned with the thinking and committed to promoting a culture of safety. This requires continuous learning at all levels and is much easier for businesses to achieve when they partner with an experienced, reliable occupational health and safety (OHS) service provider.
Continuous learning is critical to ensure that workers develop a sustainable habit of awareness in their roles and responsibilities to maintain a job safely. When frequent training is involved, it becomes habitual to work safely. Given human nature, if safety becomes habitual, it becomes easier to create a safe production environment, instead of an environment in which safety conflicts with production. Organisations that invest in facilitating the ongoing growth of their employees through continuous learning, fuel their enterprise’s ability to dynamically transform as necessary, to anticipate and exploit opportunities as they arise. Safety creates a competitive advantage in that the business can move forward confidently, knowing its risks are minimised.
Technology can be used to enhance the employee’s awareness of the dangers in the work environment while increasing the speed of communication between teams. Technology also brings safety into environments that were previously hard to access, thanks to remote working capabilities. Consider the virtual safety officer (VSO), who allows teams to access advisory services without needing a person physically on-site. Technology also takes continuous learning outside the training classroom, extending the learning environment through digital formats – from online training and virtual assessments with a facilitator to accessing contextual hazard guides and safety refreshers within the working environment by scanning a QR code, for example.
Louise has extensive
The most important thing for businesses to come to grips with is the fact that safety matters. It must not be an afterthought. If management and employees fail to understand that safety matters, then instead of prioritising safe production, their workplace devolves into a conflict zone that pits production against safety. As such, it is essential for any business with a health and safety risk to keep reminding their people of the dangers faced in the workplace regularly, and the importance of acting to ensure that everyone returns to their loved ones at the end of each day. For this messaging to be effective, we must utilise different strategies and consider different individual learning styles when delivering the initial information and following up with refreshers. By ensuring that the message of safety catches the attention of every person, at every turn, we can make safety an immersive part of that workplace culture.
By focusing on the upskilling of managers, the
Promoting a workplace attitude that prioritises safety requires a commitment to continuous learning. By fostering a culture of ongoing education, businesses can proactively address their safety risks.
skills and expertise in safety, health, environment, risk and quality
company can ensure that its managers appreciate the importance of safety and make it a social component of the business itself. When people keep learning, they keep growing. While there is room for mistakes in such a continuous learning cycle, mistakes must become lessons and be used for growth and improvement.
Communication, collaboration and feedback on all levels are non-negotiable within continuous learning environments. Additionally, we must increase our awareness of safety, while narrowing our focus on relevance and cooperation. Instead of having a checklist for production and a checklist for safety, it is more effective to find ways to combine the two so that it becomes part of the same culture. Ensuring relevance at all times is highly critical – there is no need for reams of documentation with endless rules that are not industry-specific or pertinent to the risks at hand. This necessitates a tailored approach to documentation that covers the right personal protective equipment (PPE) in the right processes with
the right training, which is the only way to guarantee that the safety system is relevant to those people in that business.
A positive safety culture is invaluable. It cannot be emphasised enough that a company with a safety-first work culture is a company that has fewer incidents and accidents because people are more aware of the risks they are encountering daily. Shifting the risk perception of people is hugely beneficial and an experienced OHS service provider can make all the difference in achieving this shift with relevant, customised safety training programmes. The more prepared people are to address risk, the more adaptable they are to change. Adaptability is the key ingredient for innovation and productivity, which in turn unlocks greater profitability through safety.
Mining and heavy-duty industry fatalities are, of course, a reality all over the world and it would be naïve to think it can be wished away overnight, especially in industries where risks are higher than those pushing paper, for instance. But the advent of serious technological advances are
changing the picture and shifting the needle to a world where these occurrences become the exception, rather than the norm. When we recently celebrated a fatality-free January, my biggest wish was for this to continue for many more months. However, there is
Technologies are now being integrated into PPE to achieve zero harm in mining Anton believes that collaboration is critical in achieving a working world with zero harmThe tragic death of a miner in a rigging-related incident in the Free State highlights the ongoing need for enhanced safety to ensure such tragedies are rooted out before they affect lives and families. They also come at substantial cost to businesses and the economy.
nothing stopping us repeating these successes with a broader roll-out of innovative, smart digital solutions, which continue to evolve.
The biggest problem at the moment, however, is there are very few solutions that offer an integrated approach, which allows the marrying of best of breed solutions – this is where we need to get, and fast. Another problem is complacency and the key now is for companies to get a move on and harness better tech for the safety of workers. A little bit of competition will go a long way to ensure entire sectors work harder and faster at adopting safe digital solutions.
A seminal study by Deloitte, On the road to zero harm , says conditions are now in place to move the dial toward a goal of zero harm through the use of predictive analytics and wearables. The tech making waves right now includes an array of
hard hats, watches, clothing, eyeglasses and more, designed to deliver various benefits – from collision avoidance and environmental monitoring to fatigue management and personal injury reduction.
In doing so, however, companies will likely need to integrate different data pools and systems, while more proactively driving industry collaboration. And the report is quite right to note that if this does not happen, we may still be highlighting the potential for improvement a few years from now, without having seen much progress.
Sedna Industrial IT Solutions has made strides on the integration through an alliance with Guard Hat, which helps us move away from becoming a hardware ecosystem and a platform provider to becoming a platform integrator. This model essentially gives specialists the space to do their thing – they can manage their development cycle and other elements – as long as the system delivers the best solution. I recently travelled to Silicon Valley
to look for other specialists in safety to partner with in a symbiosis, where we add the connectivity layer and integrate it to the safety system, tailored to specific industry needs, for a powerful, collaborative answer to managing risk.
We want to operate in any industries that require a hard hat, safety glasses and risk assessments in operational areas. The future will truly be an integration of platforms where you integrate all hardware components (video, VoIP mechanism, environmental monitoring and location services like geofencing) into a hazardous environment.
It continues to amaze me that connected worker functionality can be achieved with something the size of a cigarette box – a device that sits in a pocket, connects to a network and other devices like a gas monitor, which would in turn connect with an integration hub (IoT hub which connects to the network). You can then add a bioband around the arm, which also connects to the device and network. That is true integration in action, but with outsized benefits in terms of safety, efficiency and operational excellence. Simply put, quite apart from injuries or tragedies, there is no business out there that can afford downtime caused by safety-related emergencies and shutdowns.
This technology knows no bounds as, it can for instance, be used to geolocate and track workers to such a degree that you will know when someone not trained on a certain machine has approached and is within 3 m of it. It is also great at tagging visitors to make sure they remain in designated areas. With adverse weather events on the rise, you can even assimilate data to issue warnings that can save lives –e.g. should a dam wall collapse or by providing time to get masks and other equipment in the event of a gas leak. In fact, AI will be a force for good in this space as a guardian of safety, as it will advance to such an extent it will help pre-
empt certain events that could or are likely to take place, before they happen.
There are already increasingly better solutions to enable a lone worker who, a few kilometres underground, can be tracked, checked and kept safe. These systems may even have algorithms to detect physical stress and fatigue by monitoring the core body temperature of workers and heart rates. We are not far off from seeing solutions such as vibration detection to preempt any possible weaknesses in underground structures, detect abnormal seismic activity and prevent dreaded fall-of-ground incidents well before anything happens. These sensory networks will run through mines like veins in a body, creating an entire view of what’s happening in and around production areas.
The proliferation of private wireless networks will in turn drive greater advances in automation, enabling greater productivity and efficiency on sites and in factories.
Sedna installed Africa’s first licensed spectrum LTE private wireless network in South Africa. We also deployed Africa’s first underground leaky feeder licensed spectrum LTE private wireless. Partnerships with Nokia and Globalstar continue to provide opportunities for growth, access and an ability to extend the reach of these solutions to more people.
All of this is leading to a sea change in the connected worker and safety space. Let’s join forces as we work towards a working world with zero harm.
The market dynamics around this are important to consider: the source of these metals and minerals is generally not found in the countries where EVs are manufactured and/or where battery and energy storage technology supply chains are located. Consumers and manufacturers in Europe, China and the US are the key purchasers of EVs, with lithium being a crucial battery component.
All roads lead to…
Perhaps it is not surprising that China has the lion’s share of the EV market in terms of sales per unit: it subsidises EV sales. Not only does the country have a grip on lithiumion battery production, but it also boasts the largest concentration of lithium processing assets.
From a US perspective, the Infrastructure Relations Act has had a significant impact on the EV industry. This legislation underpins the Biden administration’s efforts to create tax incentives for car manufacturers and other industries in the US to go green. Tesla, for example, is looking to create a lithium refinery in Texas to the value of US$375 million (R7.38 billion).
Despite the ongoing conflict in Ukraine and the resulting energy crisis, car manufacturers in the EU, including Volkswagen and Volvo, have taken the lead in producing hybrids and EVs. As anticipated, the pressure to shift towards EV production has largely come from this region’s climate-conscious consumers.
Same parts, new model
Zimbabwe boasts the largest lithium deposit in Africa and fifth largest in the world. South Africa is home to 80% of the world’s PGMs, which includes nickel, while the global EV market mostly relies on Zambia and the DRC for its cobalt supply. South Africa has relatively low lithium reserves. The bulk of the globe’s lithium supply is contained within what is known as the ‘lithium triangle’ in South America. Here, large deposits can be found in Bolivia, Chile and Argentina. Australia also has significant lithium reserves and the US and China to a much lesser extent. These six countries possess more than 80% of the world’s lithium resources.
The road ahead?
The demand for lithium will, over the next decade, most
likely surpass supply. According to a January 2023 report by McKinsey, the demand for lithium is projected to increase by over 30% compounded annually from 2020 to 2030. To address this, some companies, such as Glencore, have already started prioritising recycling. In conjunction with its JV partner, Li-Cycle from Canada, they intend to produce a definitive feasibility study for its battery hub in Portovesme, Italy, by mid-2024. Mergers and acquisitions are also a consideration when it comes to enhancing the security of supply, with Australia’s Allkem and Livent’s $10.6 billion (R208.7 billion) merger being a prime example of how consolidation may occur in the sector. South Africa, unfortunately, has simply not focused sufficiently on exploration and may well miss out on the lithium boom.
Drew Watson, global product manager:
Volvo R60 at Volvo CE, says, “The Volvo R60 offers a 55 t payload and body volume of 36 m 3, enabled by a V-shaped body ensuring optimum load retention and minimal material carry-back.
He adds that the rigid hauler is a perfect match for a 90 t excavator and meets the industry standard of 10/10/20, where it can take 10% overload for 10% of the time but should not exceed 20%. “To help operators haul the optimum amount of material, an optional on-board weighing system provides real-time payload insight to the hauler
operator via the on-board display, and can predict the 10/10/20 payload.”
Contributing to speedy cycle times, the drivetrain combines high torque capability and high drive axle multiplication to deliver the traction force needed to take on the steepest site gradients.
Not only is it productive, but the Volvo R60 is also fuel efficient. Thanks to Volvo Dynamic Shift Control, gear selection automatically adapts to varying conditions, while Eco mode enables the hauler to default to the most efficient gear shifting schedule. In addition, auto engine-idle shutdown eliminates unnecessary fuel consumption and engine wear.
The new Volvo R60 rigid hauler from Volvo Construction Equipment (Volvo CE) has been designed to get the most out of every working day – moving more for less with a higher payload and greater uptime.
The rigid hauler is available with the Volvo CareTrack telematics system to enable remote machine monitoring and help boost efficiency even further. What’s more, customers can gain recommendations on the optimum fleet configuration and site setup from their Volvo dealer, with the support of Volvo Site Simulation.
Designed to deliver high uptime and low operating costs, the R60 is built to last with a 60 000-hour life frame and a list of features that contribute to longlasting performance and component life, including:
• a low centre of gravity and balanced weight distribution to provide rock-solid stability and spread the impact of loads and stresses across the machine
• a high-strength, flexible chassis and responsive MacPherson strut with lower wishbone connection to absorb shocks and vibrations and improve the operator ride
• a V-shaped body, manufactured from high impact and high abrasion resistant steel, with minimal number of panels and welds
• neutral coast inhibitor and engine overspeed protection to further minimise wear.
Servicing of the R60 is required every 500 hours and can be completed swiftly thanks to a straightforward machine design that includes grouped maintenance points located within easy reach either from the ground or the service platform, as well as commonsized bearings throughout. On-board diagnostics provide insights into system pressures and
temperatures, and fault reporting to facilitate and speed up troubleshooting.
The Volvo R60 is built with operator comfort and safety top of mind. Operators can enter the cab from both sides using anti-slip steps and walkways. The cab is now pressurised, Roll-/Fall-Over Protective Structure (ROPS/FOPS) certified, and features a leftpositioned operator station to aid safe passing. Volvo Smart View is an added option to improve visibility even further with a 360-degree bird’s-eye view of the work zone.
Ergonomically positioned displays, responsive fingertip controls and low-effort steering combine to make operation effortless. The adjustable airsuspended seat and a Bluetooth-enabled audio system add to operator comfort.
The Volvo R60 is equipped with two retardation systems to keep a steady speed and facilitate machine navigation when going downhill, reducing the need for operator input. When manually selected, the transmission retarder slows the drivetrain to limit wheel lock-up, particularly useful on steep declines or in wet conditions. The modulating braking retarder can be automatically activated when the operator’s foot is off the accelerator to maintain a gear-selected constant engine speed. What’s more, fail-safe braking and secondary steering systems add to jobsite safety. Customers wanting to lower their total cost of ownership in quarry and mining applications should look no further than the Volvo R60 rigid hauler.
to operations and the difficulty of properly maintaining and updating the electrical systems documentation.
It’s virtually real
Digital twin technology allows facility management teams to overcome the limitation of static representation by gaining deeper insights using dynamic, real-time simulation that is enhanced by intelligent data.
Also, a digital twin isn’t only limited to modelling real-time conditions; it can also run predictive simulations. For example, it can demonstrate the effect of adding an additional motor/load to the existing electrical reticulation and model the effects of that modification.
This is immensely valuable to maintenance teams who are responsible for staying one step ahead of any equipment problems and failures. Not only does it improve uptime, but it also aids external service providers’ role in providing maintenance and support to facilities.
Digital twins provide the following important benefits to maintenance teams:
‘What if’ scenarios allow teams to simulate different situations and gain insight into the impact of a facility’s performance without the risk of downtime and potentially injury to personnel.
Research group Gartner has identified digital twin technology as one of the top trends shaping industrial equipment and process manufacturing industry. But, to contextualise digital twin technology’s importance in facility maintenance, it’s important that we take one step back.
Neglected maintenance of facilities increases safety and financial risks, often causing unplanned outages that can lead to equipment damage and, worse yet, injuries to personnel.
Equipment downtime and electrical outages cost organisations such as manufacturing plants hundreds of thousands, if not millions, of rand. South Africa’s current volatile grid continues to re-emphasise this bleak picture.
Unfortunately, in their efforts to mitigate downtime, equipment failure and outages, many engineers such as those working in the power systems domain, are limited to working with static paper or PDF-based electrical single-line diagrams (SLDs), which are often outdated. These limitations increase the risk
Facility personnel have an updated reference for their electrical single line diagram. This is critical because it can pose both equipment damage and injury to personnel operating the equipment. Having this single source of truth is necessary to ensure optimal performance.
Having an interactive, digital SLD offers great value to maintenance teams as they can easily gain access to equipment documentation and datasheets. The analysis of new equipment and changes can help to identify what impact these will have on a facility’s overall performance, helping teams to streamline diagnostics and make informed decisions on upgrades and modifications.
Next-generation, predictive solutions such as digital twins that use real-time and archived data to act as a simulation platform are undoubtedly becoming an essential tool for maintenance teams.
When provided with reliable, high-quality data, digital twins offer invaluable, real-time insights that enhance the quality, performance and efficiency of facilities, while adapting to ever-changing conditions and constraints. This technology is fast becoming an effective way to maintain a facility’s assets and reduce equipment and personnel risk.
Digital twin technology is emerging as the unsung hero of facility maintenance and service, enabling organisations, their internal teams and external partners to truly stay one step ahead of potential downtime and even catastrophic failure.
By Sarika Andhee*
Dating as far back as the 1980s, APE Pumps has played a crucial role in Zambia’s Copperbelt mining industry.
Beyond being involved in the refurbishment of most of Zambia’s major Copperbelt mines, APE Pumps is also the biggest carrier of multistage dewatering pumps in the Southern African nation. The company has a big stock of spares for the various multistage dewatering pumps that are used in the mines across Konkola, Kitwe and large parts of the Copperbelt area.
Pump applications and features
APE Pumps’ multistage high-pressure pumps can be used in various applications such as water supply systems, pressure boosting, boiler feed, irrigation installations, cooling water and hot water circulation, as well as pressurisation in chemical, process and allied industries. The pumps have unique features that make them a perfect fit for the desired application, such as a multistage ring section pump of robust construction with an extralarge shaft section for vibration-free running. For high output pressures, additional axial thrust balancing is provided by a balance valve mounted on the pump shaft. All wearing parts are renewable without additional work on the casing parts. Shaft sealing is achieved through stuffing box packing or mechanical seal. Bearing housings are protected against the ingress of spray water utilising lip seals. The pumps also have special coatings on the impellers, which give the pumps a longer lifespan –providing customers with greater value for money.
Under difficult suction conditions – such as low NPSH (net positive suction head) available – the pump can be provided with an axial inlet for cavitation-reducing flow entry pattern into the first-stage impeller.
In pumps with a small number of stages, the ball bearings absorb the axial thrust. In pumps with a larger number, the axial thrust is equalised through a balance valve mounted on the shaft in the area of the delivery housing.
Over the years, the Zambian mining industry has experienced various challenges. These include Covid-19, issues of taxation, and mine closures. Despite these and many other challenges, APE has managed to establish a trusted reputation with Zambia’s mining industry, via PSV Zambia (which is majority owned by APE).
Although various mines were being decommissioned, there was still an obligation on mining companies to keep the water levels down to avoid mine water contaminating the groundwater. Because of its reputation, APE Pumps became the pump supplier of choice to maintain the required mine water levels in the decommissioned mines. During his speech at the 2022 Mining Indaba, President Hakainde Hichilema of Zambia acknowledged that mining played a crucial role in his country’s economy, and further emphasised that the government was determined to reinvigorate economic growth. He also welcomed Canada-listed First Quantum Minerals’ announcement of a US$1.35 billion (R26.5 billion) investment over 20 years in Kansanshi Mine.
President Hichilema’s comments and First Quantum’s announcements are an indication that APE Pumps’ product and service offerings will continue to be in demand in Zambia’s mining industry.
APE Pumps’ multistage high-pressure pumps can be used in various applications such as water supply systems, pressure boosting, boiler feed, irrigation installations, cooling water and hot water circulation, as well as pressurisation in chemical, process and allied industries
www.apepumps.co.za www.matherandplatt.com
The leaching vats each weigh 220 t, measure 39 m in length, 7 m in height and 7.6 m in width, presenting some challenges with workshop handling, transport and site erection.
Christo Marais, managing director of C.I.S Engineering, says that the creation of this focused division has been extremely successful and has already resulted in the completion of several major projects.
The division specialises in steel structures in the following broad categories:
Building structures: C.I.S Industrial Structures has successfully manufactured a variety of building structures, which include: • wide-span large warehousing • factory buildings and extensions, including crane support structures.
Process support structures: Mining and chemical process plants inevitably require steel supporting structures. The division has successfully completed several such projects recently, including a covering structure installed at a vanadium mine.
Process vats and tanks: The division has successfully manufactured welded steel tanks and bins for the mineral beneficiation industry. It recently completed a megaproject together with Turnmill Proquip Engineering for the manufacturing of four leach vats for a vanadium mine.
Each module consisted of a structural steel ‘ribcage’ and was manufactured and supplied by C.I.S Engineering. These individual modules could easily be steered by workshop overhead cranes. The special cut and formed plates were then fitted into the ‘ribcage’ and were welded together to form a module. Each vat consists of four modules.
The four vats, totalling 880 t, took approximately nine months to complete, from raw material to the final complete painted product – all taking place under the roof at C.I.S Engineering and Turnmill Proquip Engineering respectively.
Mechanical equipment structures: C.I.S Industrial Structures manufactures a variety of mechanical equipment structures such as crane beams, sieves and shaker structures, and conveyor structures.
Piping and ducting: The division has successfully manufactured non-pressurised, large-diameter piping and ducting to typical high welding requirements such as AWS D1.1.
The division operates under the C.I.S Engineering Quality system, which is certified to ISO 9001:2015. It is housed in the C.I.S Engineering complex, which consists of 10 000 m2 of factory space under the roof and crane, laydown and despatch areas of some 15 000 m2 as well as administration and engineering offices.
The plant houses modern automated and semiautomated steel processing equipment, and the division has full access to the laser and plasma cutting facilities of sister company Structa Profile, which is housed in the same complex.
The division can offer a full complement of associated design services, which include draughting, CAD modelling and structural analysis. “We can truly offer smooth product development from sketch to product,” concludes Marais.
Critical incidents at mine sites and disputes with local stakeholders are examples of issues that can compromise an organisation’s social licence to operate. The term, which denotes the acceptance of organisations and their operations by local communities, is essential to sustainable mining – but takes time and effort to cultivate. After all, building trust is not just about making a promise, it is about following through. Ensuring that mineral wealth brings real and long-term gains to communities is a multifaceted challenge that requires persistence and excellence across all dimensions of sustainability, including transparency about the impacts mining operations have on the
groups affected by mineral extraction. The proposed GRI Sector Standard for Mining was out for public comment until 30 April 2023 and invited stakeholders to provide input on this critical issue – alongside wider environmental and economic topics – to develop a holistic sustainability reporting standard that will improve accountability on the sector’s impacts. The range of stakeholders who can potentially be affected by mining includes not only residents near or downstream from mining operations, but also the farmers, artisanal miners, employees, contractors or migrants who live and work in the wider vicinity. The rights of indigenous peoples are of particular concern, especially given the prevalence of mining that occurs on protected
Noora has been with the GRI since 2017, and previously worked on the Sector Standards for coal, and oil and gas
A delicate balancing act has been playing out across the mining sector: while minerals are intrinsic to global development and can pave the way for a lowcarbon economy, the impacts of their extraction are disproportionately felt by communities living in the vicinity of operations.
By Noora Puro*
land, and the history of conflict between mining firms and such communities. In many cases, these groups can gain financial benefits from mining activities, but also bear the brunt of its negative impacts.
Achieving a balance of impacts and opportunities
“Mining can provide employment, opportunities for local suppliers, taxes, community development, infrastructure and investment,” Judy Kuszewski, outgoing chair of GRI’s Global Sustainability Standards Board, recently stated. “And yet, at the same time, mining activities can have an adverse effect on communities and their livelihoods through biodiversity loss, pollution, lack of access to freshwater, noise, displacement, and health and safety threats.”
Yet if relations with local communities are managed with an eye towards transparency and shared
benefits – with vigilance to avoid, mitigate and remediate negative impacts – mining operations can be a source of positive change. They can bring a much-needed inflow of capital and employment, providing prosperity and decent work. They can also support community development and infrastructure investments with lasting benefits, such as renewable energy, transportation networks or water infrastructure. Proactive and continuous consultation with local stakeholders throughout the mine life can also prepare communities for a diverse and resilient post-mining economy, helping mitigate the sometimes drastic impacts mine closure can have.
“Through the development of the GRI Standard, this juxtaposition has really been front and centre,” explained Kuszewski. “Having that kind of balance in mind the whole time is a foundational principle to the work that’s been done here.”
In the process of drafting the Mining Standard, the importance of meaningful community engagement by mining organisations has been consistently raised by the expert working group and peer reviewers. Disclosing information in local languages is seen as essential, taking into consideration vulnerabilities and sufficient representation of the affected communities themselves. Being transparent about environmental and social monitoring on mine-site-level impacts can signal an openness by organisations about their actual impact and their management on local communities.
Due to the salience of communities in this sector, GRI has organised consultation sessions aimed at community and civil society groups specifically. These engagements in Africa and Latin America made it abundantly clear: community is key.
Stakeholders in the sector expect transparency from start to finish, and they increasingly demand information that the community can understand and engage with.
Stakeholder input received through in-person sessions during GRI’s public comment period has highlighted that the dialogue must occur on an equal footing. Providing capacity-building for local groups on participation, ensuring consultations are democratic and inclusive, with transparency about who was consulted and at what stage, is a way mining companies can mitigate corruption risks while helping communities regain trust.
Unlike reporting that focuses only on financially material issues, the GRI Sector Standard for Mining will consider a wider range of concerns directly related to the challenges faced by communities. This includes whether they are consulted on post-mining land use, approaches to employment, procurement and training opportunities, as well as the framework for providing remediation to individuals subjected to involuntary resettlement. The draft standard also gives attention to the programmes to enhance positive or mitigate negative impacts involving artisanal and small-scale mining. Rather than looking at risks that communities or vulnerable groups might pose to the mining company as a potential trigger for conflict or operational delays, the proposed standard focuses on to how organisations are creating value for the people whose lands they are using to extract resources from.
The mining sector is increasingly under a magnifying glass due to its essential role in enabling a low-carbon transition – to ensure that impacts of extracting minerals are well managed and benefits equitably distributed. Sustainable mining can be a boon for everyone: resource-rich economies can achieve long-term stability, while mining companies can develop positive relations and a social licence to operate – with communities reaping benefits from their land and labour.
To that end, the GRI Mining Standard will be a crucial step toward accountability for a sector deeply involved both in the significant sustainability challenges facing the global society, as well as the potential solutions to overcome them.
*Noora Puro is a manager at the GRI Standards Sector programme, leading the project to develop a sustainability reporting standard for mining organisations.
The GRI Sector Standard for Mining also focuses on programmes to mitigate negative impacts involving artisanal and small-scale mining
Engagements in Africa and Latin America made it abundantly clear: community is key
KSB Pumps and Valves, a leading manufacturer of pumps and valves, has been at the forefront of this movement, designing and manufacturing pumps specifically built to meet the needs of the mining industry. With a focus on sustainability, KSB is leading the charge when it comes to providing equipment that can handle a variety of mining conditions, is easy to maintain, and can provide a long wear life.
“In addition to our focus on sustainability, KSB also dedicates time and energy to minimising downtime on our mining pumps, which is achieved through a range of measures, including the use of high-quality materials and manufacturing processes, as well as extensive testing and quality control procedures,” says Rob Bond, area manager: Mining in Southern Africa, KSB Pumps and Valves. This in turn ensures that KSB pumps are built to last, with minimal need for maintenance or repairs.
But when issues do arise, KSB’s after-sales service is there to provide support and assistance. With a global network of service centres and technicians, “KSB can provide rapid response times and quick repairs, minimising downtime and ensuring equipment is up and running as quickly as possible,” says Bond. This commitment to after-sales service
is a key part of KSB’s approach to sustainability, as it helps to extend the life of their pumps and reduce the need for replacement or disposal.
“One of the biggest challenges facing the mining industry is the need to operate in a sustainable and environmentally friendly manner. To meet this challenge, we have focused on developing pumps and valves that are designed to reduce energy consumption and minimise the environmental impact,” Bond adds.
By using the latest technology and materials, KSB has been able to produce pumps that are more energy-efficient, while still delivering the level of performance the mining industry demands. KSB’s after-sales service is also focused on preventative maintenance, with a range of services available to help customers keep their pumps and valves in top condition.
From regular inspections and maintenance schedules to training and technical support, KSB’s after-sales service is designed to help customers get the most out of their equipment, while also reducing the environmental impact of their operations.
“We have 37 production sites in 18 countries and nine foundries on three continents. Plus, we have over 3 500 worldwide service staff ready to assist you wherever you may be. KSB Mining has proven it is well equipped to offer our partners a complete package of products and services. We use our expertise to make our customers’ experience easy and successful. We provide exceptional and unparalleled customer service,” he concludes.
As the mining industry in Southern Africa continues to grow, there is an increasing need for pumps and valves that are bigger, more energy-efficient and sustainable.KSB Guard ensures pumps operate optimally
Resources 4 Africa is pleased to announce the 9th edition of its annual Junior Indaba, a popular meeting place for junior miners which is enjoyed by all for its incisive, informative and frank discussions tackling the challenges and opportunities for exploration and junior mining companies in South Africa and elsewhere in Africa. Discussion topics this year include:
• What will it take for junior mining in South Africa to succeed?
• What is needed to create a conducive policy and regulatory framework for junior miners in South Africa?
• How are commodity prices faring in 2023 and what will this mean for juniors?
• Do we have the geological endowment to support junior mining in South Africa?
• What lessons can be learned from successful junior miners who are already operating in SA and beyond?
• The battery hype: should miners go beyond mining?
• Experiences of juniors in South Africa, Botswana, Zambia, Zimbabwe, Namibia, Côte d'Ivoire, Burkina Faso and Tanzania
• And much more…
We will feature a number of junior mining success stories, as well as our regular features - Myth Busters and a showcase of presentations from junior miners across the continent. Early confirmed speakers include representatives from: Minerals Council South Africa, DMRE, Council for Geoscience, Wood Mackenzie, DRA Global, Afrimat, Orion Minerals, Osino Resources, Andrada Mining, Botswana Diamonds, Cape 360, Manganese Metal Company and more…..
Mining Industry Partners: Gold Sponsor: Sponsors: Lead Sponsor: Contact us about sponsorship opportunities: sponsorship@resources4africa.com
For more information please contact,
Carina Willemse: Tel: +27 (0) 61 421 9492 Email: carina@resources4africa.com or Stuart Alderson-Smith: Email: stuart@resources4africa.com
Chances are you've heard of ChatGPT –the artificial intelligence chatbot taking the world by storm. It’s an impressive showcase of what we can achieve with today’s technology. But ChatGPT is also a warning that major changes are coming to our world. Africa needs to be prepared – not just for digital technology but all the pieces that create a 21st
century society. This is why we need more women in the STEM fields.
STEM is the foundation of modern society. Let’s put that into perspective by defining a spectrum. On the leading side are breakthroughs such as ChatGPT that define what the next century will look like. On the other side is infrastructure – the physical foundations that empower progress and innovation.
According to Unesco, girls and women are underrepresented in science, technology, engineering and mathematics (STEM) education and, consequently, in STEM careers. Women make up more than half of the world’s population and therefore need to be actively involved in STEM fields. By Chetan Mistry*
Sub-Saharan Africa (SSA) is still at the low end of this spectrum. We struggle with delivering electricity, connecting our populations to the internet, and reliably offering essential services. Water scarcity impacts one out of three Africans. Many Africans are unemployed, especially in South Africa. Less than half of people in SSA have access to modern healthcare. And only 22% of primary schools in the region have access to electricity. SSA is still behind the curve when it comes to modern infrastructure and offering the fundamentals of a 21st century society.
STEM is how we will close that gap. Countries such as South Africa boast slightly above-average STEM rates. In the first decade of this century, SSA countries doubled the amount of research they produce. But these figures come from a low base: the region still produces less than 1% of global research. The World Economic Forum is concerned about Africa’s low number of engineers and scientists, and the New York Academy of Sciences has estimated that SSA requires 2.5 million more engineers to address our fundamental challenges.
The world is moving ahead. So, how do we catch up? How do we supercharge STEM? Women are the answer. Much has been written about getting more women into STEM careers. But why specifically women? They are a massive untapped opportunity. Even though they represent half the population,
women are still a rarity in STEM careers. Only 7% of female students enrol in engineering and construction courses compared with 22% of male students. Fewer than a third of researchers in SSA are women; 32% of graduates in South Africa are women.
Why are these numbers so lopsided? It’s not that women don’t want to become engineers, IT specialists, mathematicians or researchers. Africa has many prominent woman engineers and technical leaders – but we need to encourage and support more women to pursue these careers.
At Xylem Africa, we fund the tertiary education of aspirant STEM professionals, primarily women. And we represent a very engineer-focused industry. When you talk to these future engineers, they all say the same thing: they want to solve problems for their communities and see a STEM career as the best way to do that.
They are completely correct. While we should encourage all types of people to join the STEM ranks, there is a particular advantage and opportunity to bring more women into that world. We can achieve this goal through several actions. We can elevate female role models, create more inclusive learning resources, equip and support teachers, and spread the narrative that a prosperous Africa will stand on innovation, technology and engineering.
Our world will change faster than before, even during the rapid 20th century. Artificially intelligent software is just the start of a massive step forward for humanity. Yet while we call this Africa’s century, Africa is not prepared. We still need to tackle our fundamental needs, such as water, energy, healthcare and education.
With more women in STEM, we can quickly move ahead on the spectrum and start joining the pack in the front.
As of January 2023, the Mine Engineer’s Certificate of Competency requires a mentor to possess certification from an accredited institution, and proof that at least five engineers in training are being mentored, among other requirements.
By Roland Innes*While this may be viewed as another hurdle in achieving certification, it can be hugely beneficial – not just for engineers themselves but for mines as well. Embracing this new requirement as a positive can make all the difference in shifting mindsets and can help mining engineers further their careers and mines to improve efficiency, productivity and safety in the long term.
While mentorship has now become one of the criteria for competency certification, many engineers remain reluctant to pursue mentorship skills. Reasons for this include a lack of time for additional responsibilities like mentoring, as well as a lack of incentive or reward for pursuing these goals. There is also a lack of training to contend with, as mining engineers may not have received formal
mentoring training, leaving them feeling ill-equipped to take on the role. This shift represents a change in the way things have always been done, so resistance to this change as well as fear of making mistakes or giving bad advice could hold them back.
Addressing these challenges requires mining organisations to get on board with incentives and recognition for mentors, as well as training and support for mentoring skills development. The goal should be to create a culture that values mentoring and encourages engineers to take on a mentorship role. This will not only aid in achieving the requirements for certification, but will also create an environment that encourages learning and development, which will benefit both the organisation and its employees.
Mentoring is a critical element in effective skills transfer, helping the next generation of mining professionals to benefit from the knowledge and experience that exists within the organisation. This helps mines to develop a pipeline of talent to improve business continuity. It also assists with enhancing job performance all around, as mentoring can identify areas for improvement and
then goals can be set and plans developed to achieve these goals.
Effective mentors are empowered to provide guidance and support to help engineers overcome challenges, learn new skills, and achieve their full potential. But these skills can also help mining engineers themselves by developing leadership skills, including communication, listening and problemsolving, which are essential management skills and important for job progression. Having effective skills in these areas can enhance job satisfaction as well as both personal and professional growth.
Mentoring can expose mining engineers to different perspectives and ways of thinking, which can broaden their horizons and enhance their creativity and innovation, ultimately benefiting their careers as well as the productivity of the mines. These skills also help build professional networks and relationships that can provide valuable insights, advice and opportunities for career advancement.
Accredited providers can simplify training processes
Having the right skills around mentoring can help mining engineers become more effective, resulting in satisfied employees – but the fact remains that a certificate of competency is now also a requirement for the Mine Engineer Certificate of Competency. This must also be awarded by an accredited provider.
By seeking out accredited mentorship training programmes offered by reputable institutions, mines will empower their engineers with the guidance they need to complete the certification quickly. This simplifies the training process and in turn will help them to mentor effectively, add value to their resumes and demonstrate their commitment to their professional development and the success of their mine.
In 2021, the International Energy Agency (IEA) declared that hydrogen would be an essential source of energy for reducing carbon emissions.
By Yershen Pillay*During 2016, South Africa signed the Paris Agreement on climate change at the UN in New York. Signing the agreement meant that the country is committed to reducing greenhouse gas emissions and collaborating with the global community to reduce global temperatures to below 2°C. The problem that the country faces is how best to accelerate the reduction of carbon emissions to meet its commitments to the Paris agreement.
One way of accelerating the reduction of carbon emissions is the use of green hydrogen as a zeroemissions energy carrier. According to a recent report by the Hydrogen Council in collaboration with McKinsey & Company, 40 countries have developed national hydrogen strategies to tap into hydrogen’s potential to decarbonise and the industry has announced 680 hydrogen projects proposals as at the end of May 2022.
The emerging green hydrogen industry is facing a multitude of challenges. One significant challenge is the skills and training needed for a hydrogen-ready workforce. This pertains to both current and future skills needs and training requirements. A recent study on reskilling the green hydrogen economy found that 80% of industry employees would require new hydrogen skills and further education about electrolysers, fuel cells, hydrogen storage, and future refuelling stations.
The lack of skills development and training is the biggest challenge to growing South Africa’s hydrogen economy. It’s not just accessibility to hydrogen training that poses a challenge, but actually receiving the education and skills to meet industry needs.
The main barriers to closing the hydrogen skills gap in South Africa are a lack of expertise and funding, as well as an absence of training facilities and equipment such as electrolyser simulators. For this reason, more needs to be done to develop South Africa’s education infrastructure and physical infrastructure to support both current and future demand. If we are unable to develop this infrastructure in the next five years, we may miss the opportunity to be a leader in this rapidly growing industry. We need to plan now for the future growth and expansion of hydrogen energy.
In the future, a more comprehensive assessment of skill requirements will be needed. The current desktop modelling places a greater emphasis on engineering qualifications with extraordinarily little attention paid to occupational qualifications. Hydrogen safety training has been less of a priority, yet safety skills programmes will be a vital part of hydrogen education. Hydrogen can be
an extremely dangerous gas to work with, as it is highly flammable and hence appropriate training is essential.
Closing the hydrogen skills and training gaps
In attempting to close the hydrogen skills and training gaps in South Africa, research by the Chemical Industries Education and Training Authority (CHIETA) has identified 17 specific training and skills requirements. Approximately 14 000 jobs are likely to be created, including hydrogen systems engineers, technicians, gas fitters, and other associated trades and services. The technical and regulatory uncertainties in South Africa provide a major challenge for effective skills planning. For this reason, leadership needs to be provided for enabling policy and regulatory changes. The education sector needs to work more closely with industry for joint skills planning and the co-creation of future training courses and learning materials. What is needed is more cross-sector collaboration and research development by engaging with industries such as transport, mining, manufacturing, energy, infrastructure and agriculture.
South Africa lacks the cross-sector collaboration to support skills development and training on green hydrogen. Cross-sector collaboration and joint skills planning between government, the private sector and training authorities should be an apex priority for a hydrogen-ready workforce. Without cross-sector collaboration, a fragmented and piecemeal training landscape may evolve in which hydrogen training is expensive, exclusive and inaccessible to all. Digital skills are the foundation for hydrogen skills. For this reason, South Africa needs to prioritise digital literacy skills programmes. A coherent digital literacy
skills curriculum is required for hydrogen education. To this end, CHIETA has prioritised digital literacy skills by launching SMART Skills Centres across the country. CHIETA SMART Skills Centres provide free
digital literacy skills programmes, including experiential learning using virtual reality technology for certain occupations. This first-of-its-kind SMART Skills Centre in Saldanha Bay has been opened to the public since 1 February 2023. Eight new centres are planned over the next two years.
The biggest risk facing South Africa is the inability to seize the moment and implement green hydrogen at scale because of the lack of adequate skills and appropriate expertise. Mitigating this risk and closing the hydrogen skills gap in South Africa requires a multipronged strategy that includes better coordination from government, cross-sector collaboration with industry, digital literacy programmes, and specialised training on electrolysers, fuel cells and hydrogen systems. The relevant expertise will have to be sourced to develop and deliver the training required by the industry. The country needs an explosion of training to become a leader in the global hydrogen economy.
19 July 2023 | The Country Club Johannesburg, Auckland Park
Resources 4 Africa is pleased to announce the 3rd edition of its annual Hydrogen Economy Discussion, which brings together all the key players, including mining companies, OEMs, investors, industry associations, hydrogen equipment suppliers, infrastructure providers and independent advisers, to debate the potential of the green hydrogen economy and its implications and opportunities for Southern Africa and the mining industry. This year discussions will centre around developments in hydrogen policy, what specific measures and regulations are needed, hydrogen infrastructure and distribution, the role of PGMs in the creation of a local hydrogen economy, timeframes for the scaling up of renewable energy, where demand will come from and much more.
Hydrogen Economy Discussion 2023 is proudly sponsored by:
Mining Industry Partners
Sponsors